Редуктор цилиндрический 2




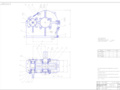
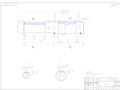
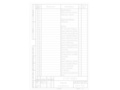
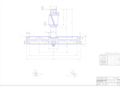
- Добавлен: 25.10.2022
- Размер: 2 MB
- Закачек: 1
Описание
Состав проекта
![]() |
![]() ![]() |
![]() ![]() ![]() ![]() |
![]() ![]() |
![]() |
![]() ![]() |
![]() ![]() ![]() ![]() |
![]() |
![]() ![]() ![]() |
![]() ![]() |
![]() |
![]() ![]() ![]() |
![]() ![]() ![]() ![]() |
![]() |
![]() |
![]() |
![]() ![]() ![]() ![]() |
![]() ![]() |
![]() ![]() ![]() ![]() |
![]() ![]() ![]() ![]() |
![]() ![]() |
Дополнительная информация
Спецификац Клинорем+Редуктор Л1.dwg

Вал шестерня ведущий
Крышка подшипника сквозная
Прокладка регулировочная
Кольцо мазеудерживающее
Крышка подшипника глухая
Кольцо уплотнительное
Крышка корпуса редуктора
Крышка смотрового окна
Маслоуказатель жезловый
Клинорем +редуктор цилиндрический.dwg

Общее передаточное число i
Скорость вращения тихоходного вала
Мощность на тихоходном валу Р
Число зубьев: шестерни
Ширина колеса: шестерни
Валы собранного редуктора должны проворачиваться от руки плавно
Сопряженные поверхности корпуса и крышек покрыть тонким слоем герметика
ВГК-18 N2 МРТУ 07-6012-63.
Необработанные наружные поверхности редуктора покрыть серой эмалью:
Редуктор обкатать без нагрузки при частоте вращения быстроходного вала
Титульник, содержание, задание.docx
Федеральное государственное бюджетное образовательное учреждение высшего профессионального образования
АМУРСКИЙ ГОСУДАРСТВЕННЫЙ УНЕВЕРСИТЕТ
Факультет Энергетический
Кафедра Автоматизации производственных процессов и электротехники
Специальность 160803 – «Стартовые и технические комплексы ракет и космических аппаратов»
на тему: Расчет и конструирование привода общего назначения.
по дисциплине «Детали машин»
К курсовому проекту студента Седых Егора Валерьевича
Тема курсового проекта: «Расчет и конструирование привода общего назначения».
Исходные данные к курсовому проекту: мощность на ведущем валу Р3 = 2 кВт; угловая скорость ведущего вала 3 = 2.
Содержание пояснительной записки: Расчет и конструирование цилиндрического редуктора
Перечень материалов приложения:
: Первый этап компоновки
: Второй этап компоновки
: Общий вид редуктора
выдачи задания: 10 сентября 2011 г.
Руководитель курсового проекта: Доценко С.М. профессор доктор техн. наук.
Курсовой проект содержит 41 с. 5 рисунков 4 таблицы 5 источников 3 приложения.
МЕХАНИЗМ ВАЛ РЕДУКТОР ШПОНКА КОЛЕСО ПОДШИПНИК.
В данном проекте изучается работа механизма редуктора и проводится его проектирование.
Расчет и конструирование привода 6
1 Выбор электродвигателя и кинематический расчет 6
2 Расчет клиноременной передачи 8
3 Расчет зубчатых колес редуктора 12
4 Предварительный расчет валов редуктора и выбор подшипников 18
5 Конструктивные размеры шестерни и колеса 20
6 Конструктивные размеры корпуса редуктора 20
7 Первый этап компоновки 21
8 Выбор муфты для соединения концов валов редуктора и приводного
9 Проверка долговечности подшипника 24
10 Проверка долговечности подшипников на ведущем валу 25
11 Проверка долговечности подшипников на ведомом валу 26
12 Второй этап компоновки редуктора 27
13 Проверка прочности шпоночных соединений 29
14 Уточненный расчет валов 30
14.1 Расчет ведущего вала 31
14.2 Расчет ведомого вала 32
15 Посадки зубчатого колеса шкива полумуфты подшипников 37
16 Смазочные системы и устройства. Выбор сорта масла 37
Библиографический список 41
Приложение А. Первый этап компоновки
Приложение Б. Второй этап компоновки
Приложение В. Спецификация
Курсовая.docx
Создание машин отвечающих потребностям народного хозяйства должно предусматривать их наибольший экономический эффект и высокие тактико-технические и эксплуатационные показатели.
Основные требования предъявляемые к создаваемой машине: высокая производительность надёжность технологичность ремонтопригодность минимальные габариты и масса удобство эксплуатации экономичность техническая эстетика. Все эти требования учитываются в процессе проектирования и конструирования.
Объектом данного курсового проекта является привод ленточного конвейера который состоит из:
- электродвигателя с мощностью 22 кВт частотой вращения 1000 обмин.
-одноступенчатого цилиндрического редуктора
Принцип работы привода следующий: крутящий момент с вала двигателя передается на приводной вал рабочей машины через ременную передачу и цилиндрический редуктор. Редуктор состоит из двух валов: быстроходного и тихоходного установленных в корпус редуктора на роликовых конических однорядных подшипниках. Смазка зубчатых колес осуществляется погружением колеса в масляную ванну подшипники смазываются за счёт разбрызгивания масла. Для герметизации мест выхода из корпуса валов применены уплотнения с помощью мазеудерживающих колец. Для предохранения от перегрузки используется ременная передача.
РАСЧЕТ И КОНСТРУИРОВАНИЕ ПРИВОДА
В данном курсовом проекте мы рассматриваем одноступенчатый горизонтальный цилиндрический косозубый редуктор и клиноременную передачу для привода к ленточному конвейеру (рисунок 1).
– электродвигатель; 2 – клиноременная передача; 3 – одноступенчатый цилиндрический редуктор; 4 – муфта
Рисунок 1- Привод ленточного конвейера с цилиндрическим редуктором и клиноременной передачей
1 Выбор электродвигателя и кинематический расчет
Коэффициент полезного действия пары цилиндрических зубчатых колес 1 = 098; коэффициент учитывающий потери пары подшипников качения 2 = 099; КПД клиноременной передачи 3 = 095; коэффициент учитывающий потери в опорах приводного барабана 4=099 [1; c.238 ].
-коэффициент полезного действия (КПД) привода равный произведению КПД передач входящих в кинематическую схему:
= 1 2 3 4 = 098 0992 095 099 099 = 090. (1)
Требуемая мощность электродвигателя:
Ртр = =2136 кВт. (3)
Рекомендуемые значения передаточного отношения (i ) для зубчатых передач равны 2–6 [1 c. 58 ] и [2 c. 7 ] для ременных 2-4 [2 c. 7 ]. Таким образом передаточное отношение привода следующее:
Выбираем электродвигатель с таким числом оборотов чтобы передаточное отношение привода было не меньше 4 и не больше 24.
При выборе электродвигателя мы видим что мощность по паспорту отличается от требуемой. В этом случае надо учитывать два обстоятельства: большой запас мощности электродвигателя приводит к повышению расхода электроэнергии перегрузка – к перегреву двигателя (допускается перегрузка не более 5 %). Поэтому следует применять электродвигатель с ближайшим большим значением мощности [3 с. 24].
По ГОСТ19523 – 81 по требуемой мощности Ртр = 2136 кВт выбираем электродвигатель трехфазный асинхронный короткозамкнутый серии 4А закрытый обдуваемый с синхронной частотой вращения 1000 обмин 4А100L6УЗ с параметрами Рдв = 22 кВт и скольжением 51 %.
Проверим общее передаточное отношение:
что можно признать приемлемым так как оно находится между 9 и 36 (большее значение принимать не рекомендуют)
Частные передаточные числа (они равны передаточным отношения) можно принять: для редуктора по ГОСТ 2185 – 66 u=5. Для клиноременной находим по формуле:
Угловая скорость и частота вращения ведущего вала редуктора:
= 3 · u = 2 · 314 · 5 = 314 радс; (8)
n1 = n3 · u = 60 · 5 = 300 радс; (9)
Запишем полученные данные в таблицу 1:
Таблица 1 – Частоты вращения и угловые скорости валов
2 Расчет клиноременной передачи
Исходные данные для расчета: передаваемая мощность Ртр = 2136 кВт; частота вращения (меньшего) шкива nдв = 1000 обмин; передаточное отношение скольжение ремня = 0015.
По номограмме на рисунке 2 в зависимости от частоты вращения меньшего шкива n1 = nдв = 1000 обмин и передаваемой мощности Р = Ртр = 2136 кВт принимаем сечение клинового ремня А.
Рисунок 2 – Номограмма для выбора сечения клинового ремня
где Р = 2136 · 103 Вт.
Диаметр меньшего шкива определяем по формуле:
Согласно таблице 7.8 [1; с.132] с учетом того что диаметр шкива для ремней сечения А не должен быть меньше 100 мм принимаем d1 = 100 мм.
Диаметр большого шкива определяем по формуле:
Примем d2 = 355 по таблице 7.8 [1; с.132].
Уточняем передаточное отношение:
При этом угловая скорость вала В будет:
Расхождение с тем что было получено по первоначальному расчету составит:
что менее допускаемого на .
Следовательно окончательно принимаем диаметры шкивов d1 = 100 мм и d2 = 335 мм.
Межосевое расстояние ар следует принять в интервале:
аmax = 100 + 355 = 455 мм (25)
где Т0 = 8 мм (высота сечения ремня по таблице 7.7) [1; с.131].
Принимаем предварительно близкое значение ар = 500 мм.
Расчетная длина ремня определяется по формуле:
Ближайшее значение по стандарту L = 1800 [1; таблица 7.7; с.131].
Уточняем значение межосевого расстояния аР с учетом стандартной длины ремня L
где w = 05(d1 + d2) = 05 · 314(100 + 355) = 71435 мм;
y = (d2 – d1)2 = (355 – 100)2 = 65025 (29)
При монтаже передачи необходимо обеспечить возможность уменьшения межосевого расстояния на 001 L = 001 · 1800 = 18 мм для облегчения надевания ремней на шкивы и возможность увеличения его на 0025 L = 0025 · 1800 = 45 мм для увеличения натяжения ремней.
Угол обхвата меньшего шкива находим по формуле:
Коэффициент режима работы учитывающий условия эксплуатации передачи смотрим по таблице 7.10 [1; с.136]. Для привода к ленточному конвейеру при односменной работе он равен СР = 10.
Коэффициент учитывающий влияние длины ремня смотрим по таблице 7.9 [1; с.135]. Для ремня сечения А при длине L = 1800 мм коэффициент равен СL = 101.
Коэффициент учитывающий влияние угла обхвата [1; с.135]: при α1 = 152440 коэффициент Сα = 093.
Коэффициент учитывающий число ремней в передачи [1; с.135]: предполагая что число ремней в передаче будет от 4 до 6 примем коэффициент СZ = 090.
Число ремней в передаче рассчитаем по следующей формуле:
где Р0 – мощность передаваемая одним клиновым ремнем кВт [1; таблица 7.8]; для ремня сечения А при длине L = 1800 мм работе на шкиве
Натяжение ветви клинового ремня рассчитаем по формуле:
где скорость v = 05ДВd1 = 05 · 104667 · 100 · 10-3 = 5233 мс;
– коэффициент учитывающий влияние центробежных сил [1; с.136]; для ремня сечения А коэффициент = 01 .
Вш = (z – 1) e + 2f (39)
Вш = (3 – 1) 15 + 2 · 10 = 50 мм. (40)
3 Расчет зубчатых колес редуктора
Для начала выбираем материалы для зубчатых колес[1; таблица 3.3; с.34]. Для шестерни сталь 45 термообработка – улучшение твердость НВ 230; для колеса сталь 45 термообработка – улучшение твердость НВ 200.
Допускаемое контактное напряжение для косозубых колес из указанных материалов [Н] = 410 МПа.
Примем коэффициент ширины венца ba = 04.
Коэффициент КН учитывающий неравномерность распределения нагрузки по ширине венца примем по таблице 3.1 [1; с.32]. Несмотря на симметричное расположение колес относительно опор примем значение этого коэффициента как в случае несимметричного расположения колес так как со стороны клиноременной передачи действует сила давления на ведущий вал вызывающая его деформацию и ухудшающая контакт зубьев: КН = 125.
Мощность на валу барабана (он же ведомый вал редуктора) Р3 = Р2 = 2 кВт.
Найдем вращающий момент на этом валу:
Межосевое расстояние из условия контактной выносливости активных поверхностей зубьев находим по формуле:
где Ка = 43 – для косозубых колес;
u = 5 – принято ранее для рассматриваемого редуктора.
Ближайшее значение межосевого расстояния по ГОСТ 2185 – 66 аw = 160 мм.
mn = (001 ÷ 002) aw (45)
mn = (001 ÷ 002) 160 = 16 ÷ 32; (46)
принимаем по ГОСТ 9563 – 60 mn = 25 мм.
Примем предварительно угол наклона зубьев = 100.
Число зубьев шестерни рассчитаем с помощью формулы:
принимаем z1 = 21. Тогда z2 = z1 · u = 25· 5 = 105.
Уточняем значения угла наклона зубьев:
3.1 Основные размеры шестерни и колеса
Диаметры делительные:
Диаметры вершин зубьев:
da1 = 535 + 2 · 225 = 585 мм; (58)
da2 = 2676 + 2 · 25 = 2726 мм. (60)
b2 = 04 · 160 = 64 мм. (62)
b1 = 64 + 5 = 69 мм. (64)
Коэффициент ширины шестерни по диаметру:
Окружная скорость колес:
Степень точности передачи: для косозубых колес при скорости до 10 мс следует принять 8-ю степень точности.
Коэффициент нагрузки:
KH = KH KHα KHV (69)
По таблице 3.5 [1; с.39] при bd = 129 твердости НВ 350 и несимметричном расположении колес (учет напряжения клиноременной передачи) коэффициент КН 1165.
По таблице 3.4 [1; с.39] при v = 084 мс и 8-й степенью точности коэффициент KHα 106.
По таблице 3.6 [1; с.40] для косозубых колес при скорости менее 5 мс коэффициент KHV 10.
KH = 1165 · 106 · 1 = 1234. (70)
Проверяем контактные напряжения:
что менее [Н] = 410 МПа. Условие прочности выполнено.
Силы действующие в зацеплении:
Fa = 882 · tg 10260 = 160 H. (78)
Проверим зубья на выносливость по напряжениям изгиба:
Коэффициент нагрузки KF = KF KF [1; с.42].
По таблице 3.7 [1; с.43] при bd = 129 твердости НВ 350 и несимметричном расположении зубчатых колес относительно опор коэффициент KF 132.
По таблице 3.8 [1; с.43] для косозубых колес 8-й степени точности и скорости до 3 мс коэффициент KF = 11.
KF = 132 · 11 = 1145. (80)
Коэффициент учитывающий форму зуба YF зависит от эквивалентного числа зубьев z [1; с.46];
Коэффициенты YF1 = 42 и YF2 = 360 [1; с.42].
Определяем коэффициент Y и KFα [1; с.46]:
где средние значения коэффициента торцового перекрытия α = 15; степень точности n = 8.
Допускаемое напряжение при проверке на изгиб определяют по формуле:
По таблице 3.9 [1; с.44] для стали 45 улучшенной предел выносливости при отнулевом цикле изгиба НВ.
Коэффициент безопасности [SF] = [SF]’ [SF]’’ [1; с.43].
По таблице 3.9 [1; с.44] [SF]’ = 175 для стали 45 улучшенной; коэффициент [SF]’’ = 1 для поковок и штамповок. Следовательно:
[SF] = 175 · 1 = 175. (90)
Допускаемые напряжения:
Проверку на изгиб следует проводить для того зубчатого колеса для которого отношение меньше. Найдем эти отношения:
Проверку на изгиб проводим для шестерни:
F1 = МПа 206 МПа. (96)
Условие прочности выполнено.
4 Предварительный расчет валов редуктора и выбор подшипни- ков
Предварительный расчет валов проводят на кручение принимая пониженные допускаемые напряжения.
Допускаемое напряжение на кручение примем [К] = 20 МПа. Это невысокое значение принято с учетом того что ведущий вал испытывает изгиб от напряжения клиноременной передачи.
Определим диаметр выходного конца вала:
Примем ближайшее большее значение из стандартного ряда [1; с.161] dB1 = 26.
Диаметр вала под подшипниками принимаем dп1 = 35 мм.
Конструкция ведущего вала приведена на рисунке 3.
Рисунок 3 – Конструкция ведущего вала
Вращающий момент Т2 = 318 Н·м.
Допускаемое напряжение на кручение [К] = 25 МПа [1; с.161-162].
Определяем диаметр выходного конца вала:
Диаметр вала под подшипниками принимаем dп2 = 55 мм.
Примем радиальные шарикоподшипники особо легкой серии; габариты подшипников выбираем по диаметру вала в месте посадки подшипников dп1 = 35 мм и dп2 = 55 мм. По таблице 2 имеем следующее [1; с.393]:
Таблица 2 – Шарикоподшипники радиальные однорядные
Условное обозначение подшипника
Конструкция ведомого вала приведена на рисунке 4.
Рисунок 4 - Конструкция ведомого вала приведена
5 Конструктивные размеры шестерни и колеса
Шестерню выполняем за одно целое с валом.
dст = 16 · 55 = 88 мм. (104)
lст = (12 ÷ 15) dk2 (105)
lст = (12 ÷ 15) · 55 = 66 ÷ 825 мм (106)
принимаем lст = 70 мм.
= (25 ÷ 4) · 25 = 625 ÷ 10 мм (108)
принимаем 0 = 10 мм.
С = 03 · 64 = 192 мм (110)
6 Конструктивные размеры корпуса редуктора
Толщина стенок корпуса и крышки:
= 0025 · 160 + 1 = 5 мм (112)
= 002 · 160 + 1 = 42 (114)
Толщина фланцев поясов корпуса и крышки:
верхнего пояса корпуса и пояса крышки
b = 15 · 8 = 12 мм; (116)
b1 = 15 · 8 = 12 мм; (118)
нижнего пояса крышки
р = 235 · 8 = 19 мм (120)
d1 = (003 ÷ 0036) аw + 12 (121)
d1 = (003 ÷ 0036) · 160 + 12 = 168 ÷ 1776 мм (122)
примем болты с резьбой: М18;
крепящих крышку к корпусу у подшипников
d2 = (07 ÷ 075) d1 (123)
d2 = (07 ÷ 075)18 = 126 ÷ 135 мм (124)
принимаем болты с резьбой: М14;
соединяющих крышку с корпусом
d3 = (05 ÷ 06) d1 (125)
d3 = (05 ÷ 06) · 18 = 9 ÷ 108 (126)
принимаем болты с резьбой: М10.
7 Первый этап компоновки
Компоновку обычно проводят в два этапа. Первый этап служит для приближенного определения положения зубчатых колес относительно опор для последующего определения опорных реакций и подбора подшипников.
Компоновочный чертеж выполняем в одной проекции – разрез по осям валов при снятой крышке редуктора; масштаб принимаем 1:1 чертим тонкими линиями.
Примерно посередине листа параллельно его длинной стороне проводим горизонтальную осевую линию; затем две вертикальный линии – оси валов на расстоянии аw = 160 мм.
Вычерчиваем упрощенно шестерню и колесо в виде прямоугольников; шестерня выполнена за одно целое с валом; длина ступицы колеса равна ширине венца и не выступает за пределы прямоугольника.
Очерчиваем внутреннюю стенку корпуса:
а) принимаем зазор между торцом шестерни и внутренней стенкой корпуса
А1 = 12 · 8 = 96 мм; (128)
при наличии ступицы зазор берется от торца ступицы.
б) принимаем зазор от окружности вершин зубьев колеса до внутренней стенки корпуса
в) принимаем расстояние между наружным кольцом подшипника ведущего вала и внутренней стенкой корпуса
если диаметр окружности вершин зубьев шестерни окажется больше наружного диаметра подшипника то расстояние А надо брать от шестерни.
Предварительно намечаем радиальные шарикоподшипники особо легкой серии; габариты подшипников выбираем по диаметру вала вместе посадки подшипников dп1 = 35 мм и dп2 = 55 мм.
В таблице 3 приведены подшипники особолегкой серии и их размеры.
Таблица 3 – Подшипники особолегкой серии
Решаем вопрос о смазывании подшипников. Принимаем для подшипников пластичный смазочный материал. Для предотвращения вытекания смазки внутрь корпуса и вымывания пластичного смазочного материала жидким маслом из зоны зацепления устанавливаем мазеудерживающие кольца. Их ширина определяет размер у = 8 ÷ 12 мм.
Измерениями находим расстояния на ведущем валу l1 = 62 мм и на ведомом l2 = 65 мм.
Примем окончательно l1 = l2 = 65 мм.
Предварительная компоновка редуктора показана на рисунке 5.
Рисунок 5 – Предварительная компоновка редуктора
8 Выбор муфты для соединения концов валов редуктора и при- водного вала конвейера
Муфта соединяющая быстроходные валы (вал электродвигателя) в целях уменьшения пусковых моментов должна иметь малый момент инерции.
К муфтам которые соединяют сравнительно тихоходные валы (например редуктор и приводной вал конвейера) не предъявляют повышенных требований в отношении малого момента инерции. В то же время если исполнительный механизм и привод не располагаются на общей раме то от муфты требуются сравнительно высокие компенсирующие свойства.
Основной паспортной характеристикой муфты является допускаемый вращающий момент на передачу которого она рассчитана. По этому моменту и подбирают стандартные муфты:
где Т – номинальный длительно действующий момент на соединяемых валах Н·м;
К – коэффициент динамичности нагрузки; для ленточных конвейеров К= 125 15; цепных скребковых К=15 20.
ТK=125 · 338 = 4225 (134)
следовательно 4225 ≤ [630].
По таблице 11.1 [1; с.268] подбираем размеры для фланцевой муфты:
d = 50 мм; D = 170 мм; L = 170 мм.
9 Поверка долговечности подшипника
Из предыдущих расчетов имеем: Ft = 2377 H Fa = 160 H Fr = 882 H
FВ = 374 Н; из первого этапа компоновки: l1 = 82 мм l0 = 130 см.
Реакции опор в плоскости xz:
(Rx1 + Rx2) – (Ft + FB) = 0 (139)
(19365 + 8145) – (2377 + 374) = 0. (140)
Реакции опор в плоскости yz:
Ry1 + Ry2 – Fr = 0 (145)
4 + 408 – 882 = 0. (146)
10 Проверка долговечности подшипников на ведущем валу
Проверяем подшипники № 107.
Эквивалентная нагрузка:
Рэ = (Х · V · Pr1 + Y · Pa)Kб · КТ (151)
в которой радиальная нагрузка Pr1 = 1994 H; осевая нагрузка Ра = Fa = 160 Н; V = 1; коэффициент безопасности для приводов ленточных конвейеров Kб = 1[1; таблица 9.19]; КТ = 1 [1; таблица 9.20].
Отношение ; этой величине соответствует е 020 [1; таблица 9.18].
Отношение е; тогда Х = 1 Y = 0.
Рэ = (1 · 1 · 1280 + 0 · 160)1 · 1 = 1280 Н. (152)
Расчет долговечности млн. об:
Расчет долговечности ч:
что больше установленный ГОСТ 16162 – 82.
11 Проверка долговечности подшипников на ведомом валу
Находим опорные реакции вала от нагрузки в зацеплении.
Rx3 = Rx4 = H. (158)
Ry3 + Ry4 – Fr = 0 (163)
4 + 438 – 882 = 0. (164)
Суммарные радиальные реакции подшипников для опоры 3:
Pr3 = (R2x3 + R2y3)05 (165)
Pr3 = (11892 + 4442)05 = 1269 H. (166)
Суммарные радиальные реакции подшипников для опоры 4:
Pr4 = (R2x4 + R2y4)05 (167)
Pr4 = (11892 + 4382)05 = 1267 Н. (168)
Расчитываем долговечность для подшипников № 111.
Рэ = Pr3 · V · Кб · КТ (169)
Рэ = 1267 · 1 · 1 · 1 = 1267 Н. (170)
Расчет долговечности млн.об:
12 Второй этап компоновки редуктора
Второй этап компоновки имеет целью конструктивно оформить зубчатые колеса валы корпус подшипниковые узлы и подготовить данные для проверки прочности валов и некоторых других деталей.
Примерный порядок выполнения следующий.
Вычерчиваем шестерню и колесо по конструктивным размерам найденным ранее. Шестерню выполняем за одно целое с валом.
Конструируем узел ведущего вала:
а) наносим осевые линии удаленные от середины редуктора на расстояние
б) между торцами подшипников и внутренней поверхностью стенки корпуса вычерчиваем мазеудерживающие кольца. Их торцы должны выступать внутрь корпуса на 1 – 2 мм от внутренне стенки. Тогда эти кольца будут выполнять одновременно роль маслоотбрасывающих колец. Для уменьшения числа ступеней вала кольца устанавливаем на тот же диаметр что и подшипники ( = 35 мм). Фиксация их в осевом направлении осуществляется заплечиками вала и торцами внутренних колец подшипников;
в) вычерчиваем крышки подшипников с уплотнительными прокладками (толщиной примерно 1 мм) и болтами. Болт условно заводится в плоскость чертежа о чем свидетельствует вырыв на плоскости разъема.
Войлочные и фетровые уплотнения применяют главным образом в узлах заполненных пластичной смазкой. Уплотнения манжетного типа широко используют как при пластичных так и при жидких смазочных материалах.
г) переход вала от 35 к присоединительному концу вала 26 мм выполняют на расстоянии 10 – 15 мм от торца крышки подшипника так что бы ступица муфты не задевала за головки болтов крепления крышки.
Длина присоединительного конца вала 26 мм определяется длиной ступицы муфты.
Аналогично конструируем узел ведомого вала. Стоит обратить внимание на следующие особенности:
а) для фиксации зубчатого колеса в осевом направлении предусматриваем утолщение вала с одной стороны и установку распорной втулки – с другой; место перехода вала от 60 мм к 55 мм смещаем на 2 – 3 мм внутрь распорной втулки с тем чтобы гарантировать прижатие мазеудерживающего кольца к торцу втулки (а не к заплечику вала);
б) отложив от середины редуктора расстояние
в) вычерчиваем мазеудерживающие кольца крышки подшипников с прокладками и болтами;
г) переход от 55 мм к 50 мм смещаем на 2 – 3 мм внутрь подшипника с тем. чтобы гарантировать прижатие кольца к внутреннему кольцу подшипника (а не к валу);
На ведущем и ведомых валах применяем шпонки призматические со скругленными торцами по ГОСТ 23360 – 78. Вычерчиваем шпонки принимая их длины на 5 – 10 мм меньше длин ступиц.
13 Проверка прочности шпоночных соединений
Шпонки призматические со скругленными торцами. Размеры сечений шпонок и пазов и длины шпонок – по ГОСТ 23360 – 78 [1; таблица 8.9].
Материал шпонок – сталь 45 нормализованная.
Напряжения смятия и условие прочности
Допускаемые напряжения смятия при стальной ступице [см] = 100 ÷ 120 МПа.
Проверяем шпонку на конце вала на котором закреплен шкив ременной передачи.
Имеем следующие размеры: d = 26 мм; b t1 = 40 мм; дли шпонки момент на ведущем валу Т1 = 64 Н·м;
(материал полумуфты МУВП – чугун марки СЧ 20).
Проверяем шпонку на конце вала соединенном с муфтой: d = 50 мм; b t1 = 60; длина шпонки момент Т2 = 318 Н·м;
см = МПа [см]. (177)
Проверяем шпонку под зубчатым колесом: d = 60 мм; b t1 = 70 мм; длина ступицы момент Т2 = 318 Н·м;
см = МПа [см]. (178)
Условие см [см] выполнено.
14 Уточненный расчет валов
Уточненный расчет валов состоит в определении коэффициентов запаса прочности S для опасных сечений и сравнении их с требуемыми значениями S.
Условие прочности соблюдено при S S = 25.
Коэффициент запаса прочности по нормальным напряжениям
S = -1 (K v + m ) (179)
где -1 – предел выносливости стали при симметричном цикле изгиба;
K – эффективный коэффициент концентрации нормальных напряжений;
– масштабный фактор для нормальных напряжений;
v – амплитуда цикла нормальных напряжений;
– коэффициент чувствительности материала к асимметрии цикла нормальных напряжений для углеродистых сталей = 02 для легированных = 025 – 030 [2 c.163];
m – среднее напряжение цикла нормальных напряжений.
Коэффициент запаса прочности по касательным напряжениям
S= -1 (K v + m) (180)
где -1 – предел выносливости стали при симметричном цикле кручения;
K – эффективный коэффициент концентрации касательных напряжений;
– масштабный фактор для касательных напряжений;
v – амплитуда цикла касательных напряжений;
– коэффициент чувствительности материала к асимметрии цикла касательных напряжений = 01 [2 c.166];
m – среднее напряжение цикла касательных напряжений.
v = m =05 max = 05ТWк. (181)
Результирующий коэффициент запаса прочности
S= SS (S 2 + S2 )12 . (182)
Нормальные напряжения от изгиба изменяются по симметричному циклу а касательные от кручения — по отнулевому (пульсирующему) циклу.
14.1 Расчет ведущего вала
Поскольку шестерня выполнена заодно с валом материал вала тот же что и для шестерни: сталь 45 термическая обработка — улучшение.
При диаметре заготовки до 90 мм среднее значение в= 780 МПа [1; таблица 3.3].
Предел выносливости при симметричном цикле изгиба:
-1 = 043в = 043 780 = 3354 МПа. (183)
Предел выносливости при симметричном цикле касательных напряжений:
-1 058 -1=058 3354 = 194 МПа. (184)
Это сечение при передаче вращающего момента от электродвигателя через муфту рассчитываем на кручение. Концентрацию напряжений вызывает наличие шпоночной канавки. Коэффициент запаса прочности:
S = S = -1 (K v + m ) (185)
где амплитуда и среднее напряжение от нулевого цикла:
v=m =max2=T12 Wк нетто (186)
здесь Wк нетто – момент сопротивления сечения кручению.
При d = 26 мм; b t1 = 4 мм:
Wк нетто = мм3; (188)
Принимаем K= 168; = 090; =01 [1; с.166].
14.2 Расчет ведомого вала
Материал вала — сталь 45 нормализованная.
Пределы выносливости:
-1 =043 570=245 МПа (193)
-1=058 245=142 МПа. (194)
Диаметр вала в этом сечении
Концентрация напряжения обусловлена наличием шпоночной канавки:
K=159; K=149; = 082; = 070; =015; =01.
М = 1269 · 65 = 82485 Н · м. (196)
Момент сопротивления кручению:
d= 70 мм; b= 20 мм; t1= 75 мм;
Wк нетто = мм3. (198)
Момент сопротивлению изгибу:
Амплитуда и среднее напряжение цикла касательных напряжений:
Амплитуда нормальных напряжений:
среднее напряжение m=0.
Коэффициенты запаса прочности по нормальным напряжениям находим по формуле (179):
Коэффициенты запаса прочности по касательным напряжения определяется по формуле (180)
Результирующий коэффициент запаса прочности для сечения А – А
Концентрация напряжений обусловлена посадкой подшипника с гарантированным натягом (для диаметра вала 55 мм):
K = 340 K= 244 =015 =01.
М4 = Fм l3=1445 · 86=124270 Н·м (209)
Осевой момент сопротивления:
Полярный момент сопротивления кручению:
Wk = 2 · 163255 = 32651 мм3. (215)
Коэффициент запаса прочности по радиальным напряжениям:
Коэффициент запаса прочности по касательным напряжениям:
Результирующий коэффициент запаса прочности для сечения К – К находим по формуле (207)
Концентрация напряжения обусловлена переходом от 55 к 50.
При ; : K=1.65 K= 1.19 =0.80 =0.68.
Крутящий момент тот же что и в сечении К–К.
МL-L= Fм · XL-L (223)
МL-L =1445 · 60=8652 Н·м. (224)
v = max = МПа. (228)
Полярный момент сопротивления при кручении:
WK = 2 · 122656 = 245312 мм3. (230)
Коэффициент запаса прочности по нормальным напряжениям по формуле (218)
Коэффициент запаса прочности по касательным напряжениям по формуле (220)
Результирующий коэффициент запаса прочности для сечения Л – Л находим по формуле (207)
Концентрация напряжения обусловлена наличием шпоночной канавки:
K= 159; =079 K=149 =069.
Изгибающий момент (XБ-Б = 40 мм)
МБ-Б = Fм · XБ-Б =1445*40=57800 (236)
Момент сопротивления сечения нетто при b = 18; t1 = 70:
Амплитуда нормальных напряжений изгиба:
Момент сопротивления кручению сечения нетто:
Wк нетто = мм3. (242)
Коэффициент запаса прочности по нормальным напряжениям по формуле (218):
Коэффициент запаса прочности по касательным напряжениям по формуле (220):
Результирующий коэффициент запаса прочности для сечения Б – Б находим по формуле (207)
Сведем результату проверки в таблицу 4.
Таблица 4 – Результаты проверки
Коэффициент запаса S
Во всех сечениях S > S= 25.
15 Посадки зубчатого колеса шкива полумуфты подшипников
В соответствии с рекомендациями [2 с.263] назначаем:
– посадку зубчатого колеса на вал Н7
– посадку шкива на вал Н7
– посадку полумуфты на вал Н7p6.
В редукторе используем подшипники класса точности 0 [3 c. 179 – 182].
Предельные отклонения размеров посадочных поверхностей подшипников регламентированы ГОСТ 520-89. Посадки подшипников отличаются от обычных расположением и величинами полей допусков на посадочные поверхности колец.
С учетом вида нагружения колец назначаем следующие посадки:
наружные кольца подшипников качения в корпусе H7
внутренние кольца подшипников качения на валу L0k6 [3 c. 179 – 182].
16 Смазочные системы и устройства. Выбор сорта масла
Для смазки зубчатых колес выбираем способ смазывания погружением зубчатых колес в масло залитое в картер редуктора. Данный способ используют при окружных скоростях менее 15 мс.Уровень масла в картере редуктора должен обеспечить погружение венца колеса на глубину до двух высот зубьев но не менее 10 мм [3 c. 223].
Объем масляной ванны принимают таким чтобы обеспечить отвод выделяющейся в зацеплении теплоты к стенкам корпуса. Для одноступенчатых цилиндрических редукторов объем масляной ванны рекомендуется принимать таким чтобы на 1 кВт мощности приходилось 035 07 л масла. [3 c. 224]. Учитывая что длина масляной ванны 430 мм ширина 125 мм а количество масла при мощности 22 кВт должно быть 29 37 л глубина масляной ванны должна быть 35 70 мм.
В спроектированном редукторе доступ масляных брызг к подшипникам качения затруднен и смазку подшипников масляными брызгами осуществить нельзя. Поэтому полость подшипника отделяем от внутренней части корпуса мазеудерживающим кольцом. Свободное пространство внутри подшипникового узла заполняем на 13 объема пластичной мазью. Для подачи в подшипниковую полость смазочного материала без снятия крышки используем пресс-масленки.
Для наблюдения за уровнем масла в картере редуктора используем жезловый маслоуказатель.
Во время работы в связи с нагревом воздуха и масла повышается давление внутри редуктора. Это приводит к выбрасыванию масляного тумана из корпуса через уплотнения и стыки. Чтобы избежать этого внутреннюю полость корпуса сообщают с внешней средой установкой отдушины в верхней части корпуса.
При работе передачи масло постепенно загрязняется продуктами износа. С течением времени оно стареет свойства его ухудшаются. Поэтому масло налитое в корпус редуктора периодически меняют. Отработанное масло нужно слить таким образом чтобы не производить разборку механизмов привода. Для этой цели в нижней части корпуса редуктора предусматриваем сливное отверстие закрываемое пробкой.
В соответствии с рекомендациями [2 c. 253] для имеющих место в нашем случае контактных напряжений н = 388 МПа и скорости V = 084 мс.
Рекомендуемая вязкость масла 34·10-6м2с. Принимаем масло индустриальное И-40А по ГОСТ 20799-75 [2 c. 253].
БИБЛИОГРАФИЧЕСКИЙ СПИСОК
Дунаев П.Ф. Конструирование узлов и деталей машин. – М.: Издательский центр «Академия» 2004.-496 с.
Жуков К. П. Атлас конструкций механизмов узлов и деталей
машин. – М.: Машиностроение 2000.-386 с.
Комаров С.Б. Расчет и проектирование привода с клиноременной передачей и одноступенчатым цилиндрическим косозубым редуктором. – Екатеринбург: ГОУ ВПО УГТУ–УПИ. 2006.-76 с.
Чернавский С. А. Курсовое проектирование деталей машин. – М. : Машиностроение 2005.-416 с.
Чернилевский Д.В. Основы проектирования машин. – М. : УМ и
«Учебная литература» 1998.-472 с.
вал.dwg

Крышка подшипника с отверстием.dwg

Узел А1.dwg

Спецификац Клинорем+Редуктор Л2.dwg

Кольцо уплотнительное
Болт М10x30 ГОСТ7808-70
Шайба пружинная 10 ГОСТ 6402-70
Болт М6x20 ГОСТ7798-70
Болт М16x120 ГОСТ7798-70
Шайба пружинная 16 ГОСТ 6402-70
Болт М12x40 ГОСТ7808-70
Шайба пружинная 12 ГОСТ 6402-70
Болт М16x140 ГОСТ7808-70
Болт М12x30 ГОСТ7808-70
Гайка М16 ГОСТ 5915-70
Гайка М12 ГОСТ 5915-70
Шпонка 18x11x65 ГОСТ 2336-78
Шпонка 10x8x36 ГОСТ 2336-78
Подшипник 308 ГОСТ 8338-75
Подшипник 312 ГОСТ 8338-75
Штифт 10x35 СТС ЗВ 240
Рекомендуемые чертежи
Свободное скачивание на сегодня
Другие проекты
- 24.01.2023