Разработка комбинированной энергетической установки




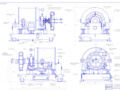
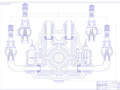
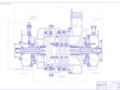
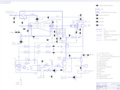
- Добавлен: 25.10.2022
- Размер: 8 MB
- Закачек: 0
Описание
Состав проекта
![]() |
![]() |
![]() ![]() |
![]() ![]() |
![]() ![]() |
![]() ![]() ![]() ![]() |
![]() ![]() |
![]() ![]() |
![]() ![]() |
![]() ![]() ![]() ![]() |
![]() ![]() ![]() ![]() |
![]() ![]() ![]() ![]() |
![]() ![]() |
![]() ![]() ![]() ![]() |
![]() ![]() ![]() ![]() |
![]() ![]() |
![]() ![]() |
![]() ![]() ![]() ![]() |
![]() ![]() |
![]() ![]() |
![]() ![]() |
![]() ![]() ![]() ![]() |
![]() ![]() ![]() ![]() |
![]() ![]() ![]() ![]() |
![]() ![]() |
![]() ![]() ![]() ![]() |
![]() ![]() ![]() ![]() |
![]() ![]() ![]() ![]() |
![]() |
![]() |
![]() |
![]() |
![]() |
![]() |
![]() |
![]() ![]() ![]() |
![]() |
![]() |
![]() ![]() ![]() |
Дополнительная информация
12 А1 Схема измерений.dwg

-электромагнитный клапан перепуска
-измерение перемещения ротора
КН-конденсатный насос
ЭРС-электронный регулятор скорости
ЭУ-эжектор уплотнений
МКП- масляный клапан перепускной
КС-конденсатосборник
- технлологические трубопроводы
ХОВ- химически очищенная вода
ЭГ - эжектор главный
ЭУ - эжектор уплотнений
СД - система дожигания взрывоопасных газов
СК - стопорный клапан
01 А1 Тепловая схема (полузависимая, с водородом).dwg

ПТУ (Режим 1) и режима работы по парогазовому
циклу (Режим 2) через дробь соответственно.
производительности мембранного реактора
08 А2 Исследовательская часть (Параллельная тепловая схема) .dwg

ПТУ (Режим 1) и режима работы по парогазовому
циклу (Режим 2) через дробь соответственно.
Комбинированная установка
с параллельной схемой работы
13 А1 Выбор тепловой схемы.dwg

ПГУ-У (с котлом утилизатором)
ПГУ с низконапорным ПГ
дополнит. оборудования
не используется из-за
низких параметров для ГТУ
ПГУ с параллельной схемой
ПГУ с полузависимой схемой
ПГУ с полузависимой схемой работы
ПГУ с параллельной схемой работы
ПГУ с высоконапорным парогенератором
ПГУ с низконапорным парогенератором
ПГУ утилизационного типа
09 А0 Исследовательская часть (графики).dwg

б). Параллельная работа ПГУ
Характеристики паротурбинной установки в составе ПГУ
с полузависимой схемой работы
с параллельной схемой работы
ТАБЛИЦА РАСХОДОВ на входе и выходе из цилиндров
7 - КПД с учетом газификатора
4 - КПД с учетом газификатора
Расход при автономной работе ПТУ
Расход в режиме работы по парогазвому циклу.
03 А1 поперечный разрез.dwg

11 А1 Продольный разрез водородной ПТ.dwg

06 А2 Наладка сверлильная.dwg

07 А2 Кондуктор для сверления.dwg

02 А0х2 продольный разрез.dwg

Номинальная мощность
Давление пара на входе
Температура пара на входе
Температура пара после пром.прегрева
05 А2 Наладка токарная.dwg

выдержав 30 мм от торца
выполнив закругление R16
Операция 65-токарная
Неуказанные предельные отклонения размеров
04 А2 Полумуфта.dwg

* Сверление отверстий произвести с припуском 0
** Размеры для справок
обозначают припуск на
обработку при сборке ротора
Риска длиной 10мм для установки кондуктора.
Маркировать шрифтом 4-Пр3 ГОСТ 26.020-80.
10 А0 Общий вид стенда испытаний.dwg

испытательной установки
Подвод циркуляционной
Преобразователь термоэлектрический
Отвод циркуляционной
для охлаждения масла
Преобразователь давления АИР-20
Преобразователь термо-
электрический ТПК ХА-054
Труба к расходомерному
К предохранительному
Р Е Ч Ь.doc
Планируется покрыть нехватку в электроэнергии за счет строительства новых эффективных ПГУ которые придут на смену мощным ПТУ ТЭС.
В рамках дипломного проекта была поставлена задача: Разработать энергетическую установку эффективную удовлетворяющую требованиям предъявленным в Генеральной схеме и работающую с пониженным уровнем вредных выбросов. Дополнительно необходимо обеспечить возможность независимого функционирования газотурбинной и паротурбинной её частей. Это условия ставилось с той целью чтобы таким образом добиться более широкого диапазона нагрузок без снижения эффективности работы. Т.к. держать в горячем или холодном резерве ПТУ большой мощности экономически не эффективно. Также в виду политики перехода на твердое ископаемое топливо такое как каменный уголь в качестве топлива был выбран синтез-газ получаемый при газификации угля на месте работы энергетической установки. Часть получаемого синтез-газа планируется перерабатывать с целью получения из него в реакторах конверсии водорода необходимого в водородной энергетике. Об установке использующей водородное топливо пойдет речь во втором разделе ИЧ ДП.
Выбор оптимальной тепловой схемы проектируемой энергетической установки является предметом первого раздела ИЧ ДП. Были рассмотрены схемы комбинированных установок реализованные в современной электроэнергетике. Среди всех схем были отобраны 2 как наиболее полно удовлетворяющие представленным требования к независимой работе ПТУ и ГТУ. Был произведен подробный тепловой и газодинамический расчет ПТУ работающей в составе этих схем. Результаты исследования приведены на листе Х из них видно что Как видим предпочтение той или другой схеме необходимо отдавать в зависимости от условий в которых работает ПГУ. Мной как более приоритетные были приняты условия частой смены нагрузки энергоблока что приводит к одинаковому по времени %-му соотношению автономной работы ПТУ и работы её по ПГ-циклу. Поэтому предпочтение было отдано полузависимой схеме работы.
В конструкторской части кроме теплового предварительного и проектировочный расчет ПТУ работающей на двух режимах был произведен расчет на прочность лопатки ЦСД и корпуса ЦВД на нераскрытие стыка.
Результатом КЧ является следующая предлагаемая конструкция ПТУ. В качестве прототипа была выбрана новая турбина ЛМЗ К-330-240. Среди конструктивных особенностей можно выделить следующие:
Ротор ЦВД выполнен цельнокованым с реактивным облопачиванием что позволяет обеспечить высокую эффективность работы установки на переменных режимах.
За прототип ЦНД был выбран хорошо зарекомендовавший себя на турбинах К-1200-240 и К-1000-553000 цилиндр низкого давления производства ЛМЗ с высотой последней лопатки 1200мм и площадью выхлопа в конденсатор 14м2.
Все лопатки направляющие и рабочие имеют Т-образный хвост применена специальная конструкция замкового соединения.
Турбина снабжена паровыми лабиринтными уплотнениями. Новые усовершенствованные уплотнения имеют меньший зазор и работают на витых отжимных пружинах. Также предусмотрены специальные отверстия в обоймах уплотнений для циркуляции пара и их охлаждения. Из концевых каминных камер уплотнений всех цилиндров паровоздушная смесь отсасывается водоструйным эжектором через вакуумный охладитель. В качестве уплотнений на последних ступенях ЦНД используются сотовые уплотнения.
литые диафрагмы ЦНД заменены на сварную конструкцию
применение рабочих лопаток с цельнофрезерованными бандажами в том числе и в последних ступенях ЦНД
В технологической части рассматривалось производство левой полумуфты соединяющей вал турбины с валом генератора. Разработан технологический процесс и выполнены чертежи следующих наладок.. Также для выполнения отверстий под соединительные болты был спроектирован кондуктор для сверления.
Как известно существует два принципиальных метода повышения эффективности паротурбинных установок. Это увеличение термического к.п.д. за счет повышения начальных и понижения конечных параметров пара и второй – развитая система регенерации тепла. Считается оптимальным если два этих метода удается совместить на практике.
В предыдущем разделе исследовательской части речь шла о современном типе парогазовых установок с развитой системой регенерации тепла. Но если поставить целью дальнейшее повышение к.п.д. турбины то решение этой задачи может быть найдено только в применении высокотемпературных циклов. Реализация таких циклов связана с применением новых высокотемпературных технологий и спец. техники.
Второй раздел исследовательской части посвящен разработке программы испытаний такой высокотемпературной ПТУ работающей на водородном топливе.
Объектом испытаний является высокотемпературная паротурбинная установка (ВПТУ-100) изображенная на листе Х с водородным пароперегревателем. Продольный разрез самой турбины – на листе Х. Номинальная мощность снимаемая с вала турбины составляет 100кВт. Роль нагружающего устройства выполняет воздушный тормоз.
Предварительные испытания включают в себя проверку систем охлаждения масла конденсата; систему подачи масла на уплотнения; систему прокачки конденсата. Подробная методика проверки всех этих систем изложена в ИЧ. После проверки всех вспомогательных систем а также работы измерительного оборудования и автоматики выполняется запуск турбины.
Рабочее тело – пар нужных параметров (3 МПа 800ºС) поступает из парогенерирующего узла. Температура пара не меняется при изменении режима испытаний. Для построения диаграммы режимов необходимо проверить работу турбины при частичных нагрузках по мощности и при различном числе оборотов.
Частичные по мощности режимы работы турбины достигаются дросселированием пара на входе в турбину с помощь элементов регулирующей арматуры. Испытания проводятся при изменении давления на входе в турбину от 2 до 3 МПа с интервалом в 0.2 МПа.
Изменение частоты вращения при неизменных параметрах на входе в турбину достигается изменением степени дросселирования воздушного тракта нагружающего устройства – воздушного тормоза (ВТ).
Для каждой степени дросселирования ВТ производится установление ряда режимов по частоте вращения от 10000 до 24000 обмин с интервалом 500 обмин. начиная с минимальной. Изменение частоты вращения производится за счет изменения давления на входе в турбину (изменения степени открытия регулирующего вентиля).
Практический интерес представляет такие характеристики когда а) давление расход и мощность меняются при фиксированной частоте вращения; б) частота вращения меняется при неизменных температуре и давлении на входе. По выполненным измерениям для каждого варианта дросселирования воздушного тормоза строятся графики характеристик турбины в параметрах подобия.
Результаты анализируются по ним выпускается технический отчет.
Экспериментальные данные по работоспособности проточной части турбины при высоких температурах полученные в ходе данных испытаний будут приняты за основу для дальнейших разработок высокотемпературных паровых турбин с начальными параметрами пара до Т = 1500°С и Р = 35МПа.
Теоретически применение энергетических установок подобного типа позволит достичь термодинамического КПД до 70% что значительно выше существующего на сегодняшний день для тепловых машин.
Экология: расчет освещения и теплоизоляции
Экономика: расчет срока окупаемости доп.кап. влож.
ЗАПИСКА вся.doc
Выбор основных параметров5
Предварительный термодинамический расчет турбины8
Расчет режима №1 (автономная работа ПТУ)12
Расчет газовой турбины и реактора газификации27
Расчет режима №2 (комбинированная работа ГТУ и ПТУ)29
Расчет проточной части40
Расчеты на прочность 44
Описание спроектированной турбоустановки53
ТЕХНОЛОГИЧЕСКАЯ ЧАСТЬ56
ИССЛЕДОВАТЕЛЬСКАЯ ЧАСТЬ85
Выбор тепловой схемы ПГУ86
Разработка программы и методики предварительных испытаний опытного образца высокотемпературной водородной турбины
мощностью 100 кВт 109
ОРГАНИЗАЦИОННО-ЭКОНОМИЧЕСКАЯ ЧАСТЬ132
ПРОМЫШЛЕННАЯ ЭКОЛОГИЯ И БЕЗОПАСНОСТЬ ТРУДА141
Список литературы 159
Анализ развития энергетики и промышленности России за последние несколько десятков лет показал что хотя принятая Правительством Программа развития энергетики до 2020 года ()и предусматривает поступление больших инвестиций в строительство новых энергоблоков (более 11000 млрд. руб. в ценах соответствующих лет) нехватка энергетических и тепловых мощностей все ещё серьезно сказывается на развитии экономики страны в целом. Во многих регионах строительство различных промышленных предприятий замораживается т.к. наблюдается острый дефицит электроэнергии а тарифы на подключаемую мощность для промышленных предприятий возросли в десять раз за последние несколько лет.
Все это говорит о том что новые мощные энергоблоки не только должны вводиться по всем регионам России с энергоемким производством но и строительство их должно быть как можно быстрее а срок окупаемости – как можно короче.
В рамках дипломного проекта была поставлена задача: разработать такую энергетическую установку которая способна удовлетворить более коротким срокам окупаемости обладать повышенным ресурсом и большим коэффициентом полезного действия. Также учитывая стратегические планы разработки дешевого угольного топлива и технологий по его экологически чистому использованию было принято решение в качестве основного энергоносителя использовать каменный уголь добываемый в районах Сибири.
Целью дипломного проекта является разработка комбинированной энергетической установки способной обеспечить независимое функционирование газотурбинной и паротурбинной её частей работающей на синтез-газе получаемом при газификации угля. Главным объектом проектирования является паровая турбина мощностью 330 МВт работающая в составе такой установки. Особенностью такой схемы является способность работать в двух различных режимах (с включенной ГТУ и с выключенной) практически не снижая своей эффективности. Предполагается что ГТУ будет включаться в параллельную схему работы во время дневного пика нагрузки в сети а ночью и в выходные дни ПТУ будет работать автономно. Таким образом мы получаем большой регулируемый диапазон мощности практически без потери в производительности. Также значительным преимуществом такой энергоустановки является её способность работать в составе электростанции с внутрицикловой газификацией угля с применением таких передовых технологий как мембранные реакторы конверсии для извлечения водорода из синтез газа и системой улавливания и удержания СО2 – CCS.
Получение водорода рассматривается как попутное производство при обработке синтез газа после газификации угля и занимает второстепенную позицию. Но если в регионе где планируется устанавливать такой энергоблок высокий спрос на водородное топливо то установленную мощность газовой турбины можно уменьшить или исключить её как компонент из цикла вообще что позволит производить больше водорода без снижения мощности паровой турбины.
КОНСТРУКТОРСКАЯ ЧАСТЬ
Выбор основных параметров
В соответствии с поставленной задачей на дипломное проектирование и номенклатурой паротурбинных установок выпускаемых машиностроительными предприятиями а также анализом технической литературы задаемся следующими основными параметрами паротурбинной установки работающей в составе комбинированной парогазовой установки:
Номинальная мощность турбогенератора:
Начальные параметры пара выбраны сверхкритические:
Р0=235 МПа; t0 =540C;
Давление в конденсаторе:
Температура и давление промежуточного перегрева пара:
Рпп=408 МПа tпп=565С
В качестве прототипа выбираем паровую турбину К-330-240 производства ЛМЗ. Паровая турбина К-330-240 номинальной мощностью 330 МВт с начальным абсолютным давлением 235 МПа предназначена для привода двухполюсного генератора переменного тока ТВВ-330-2 для работы в блоке с прямоточным котлом использующим органическое топливо. В тепловой схеме предложенной в данной работе паровой котел работает на синтез газе получаемом при газификации угля.
Предусмотрено два режима работы турбоустановки один из которых принимается за расчетный (базовый) а другой – должен не слишком отклоняться от расчетного так чтобы не происходило существенного спада в эффективности энергоблока. Первый рассчитываемый режим – это параллельная работа ГТУ и ПТУ причем регенерация тепла и подогрев питательной воды осуществляется в газо-водяных подогревателях. При этом из самой паротурбинной установки планируется производить отборы пара на деаэратор привод турбонасоса и два ПНД в которые производится слив дренажей. Также в связи с включением дополнительного газификатора производящего синтез-газ для ГТУ планируется производить отбор пар из цикла ПТУ с давлением превышающем давление в газификаторе (35 МПа).
На втором режиме работы (автономном с отключенной газотурбинной частью) ПТУ должна обходится без тепла регенерируемом в газо-водяных подогревателях. Для этого в схему включены ряд ПВД и два дополнительных ПНД. Таким образом мы рассчитываем получить установку способную работать как совместно с газотурбинной установкой так и независимо от неё с хорошими характеристиками.
Выбор оптимальной тепловой схемы для выполнения задач поставленных в дипломном проекте является предметом исследовательской части. В работе рассматриваются пять принципиальных тепловых схем по двум из которых приводится тепловой расчет и расчет паротурбинной установки. В параллельной схеме приоритет отдается более полному использованию тепла газов уходящих из газотурбинной установки при этом часть пара для паротурбинной установки генерируется в котле-утилизаторе и подается в голову ЦСД для обеспечения выхода на заданную мощность при комбинированном режиме работы. В другой схеме (полузависимая схема работы) приоритетным является достижение наивысшей эффективности в работе паротурбинной установки т.е. расход пара в отдельных частях турбины должен быть практически одинаковым на автономном режиме работы и при работе по парогазовому циклу.
В результате расчетов проведенных в исследовательской части за исходную схему для проектирования заданной паротурбинной установки принимаем ПГУ с полузависимой схемой работы приведенную на рис. 1.1.
Рис. 1.1. Расчетная тепловая схема
Предварительный термодинамический расчет турбины
При выполнении расчетов использовалась программа MathCAD 14. Результаты расчета приведены из интерфейса программы с некоторыми пояснениями.
Начальные параметры пара перед турбиной :
Промежуточный перегрев :
Конечное давление за турбиной :
Давление питательной воды после ПН
Расход пара на турбопривод питательных насосов:
- мощность турбопривода
- теплоперепад на приводных турбинах
Предварительный тепловой расчет турбины
Потери давления на паровпуске
Давление в промежуточном перегреве определяется из условия максимальной экономичности по рис. 1.18 в [1]
Потери давления в тракте пром. перегрева составляют
Конечная температура :
Энтальпия в конце процесса адиабатного расширения :
Энтальпия на выходе из конденсатора
Учет промежуточного перегрева пара
Предварительно задаемся КПД :
По i-s диаграмме находим:
Энтальпия пара в конце процесса расширения в ЦВД (перед пром. перегревом):
Энтальпия пара в конце процесса расширения в ЦНД (перед конденсатором):
- без пром. перегрева
Учет регенеративного подогрева питательной воды
Температуру питательной воды определяется как
- температура насыщения при
Но т.к. в данном проекте параметры пара сверхкритические и при давлении 24 МПа вода
сразу переходит в перегретый пар минуя двухфазное состояние то по рекомендациям выбираем:
КПД цикла с бесконечным числом отборов на регенерацию :
Определим термический КПД цикла без регенерации
Прирост КПД в идеальном регенеративном цикле составит:
Найдем абсолютный внутренний КПД цикла с промежуточным перегревом и регенеративным подогревом
Для числа отборов на регенерацию равного z по рисунку 1.25 в [1] находим реальный выигрыш
в КПД в цикле с регенерацией:
В ходе предварительного расчета были найдены значения располагаемого теплоперепада в турбине внутренний и термический к.п.д. а также построен процесс расширения пара в турбине в I-S координатах.
Выполненный предварительный термодинамический расчет турбины позволяет произвести более детальные вычисления.
Сперва проведем тепловой расчет паровой турбины при её автономной работе т.е. с отключенной газотурбинной частью (Режим №1). В таком режиме задействованы все регенеративные подогреватели и соответственно все отборы пара открыты.
Затем выполнив вычисление необходимых входных и выходных параметров для газовой турбины и реактора газификации проведем расчет паровой турбины при её работе по парогазовому циклу (Режим №2).
В заключении произведем распределение теплоперепадов по отсекам (между отборами) и ступеням турбины оценим изменение характерных параметров эффективности работы турбины таких как отношение скоростей UCф степени реактивности и внутреннего к.п.д. каждой ступени.
Расчет режима №1 (автономная работа
паротурбинной установки Nэ=330 МВт)
Мощность энергетической установки :
Газовая турбина отключена
- КПД электрогенератора
Тогда расход пара на входе в турбину будет равен:
Рис.1.2. Процесс расширения пара в турбине в H-S координатах
Расчет тепловой схемы
Давление в парогенераторе
Давление в деаэраторе
Схема установки: 2 ПВД + Д + 4 ПНД
Коэффициент регенерации.
Предварительный расход питательной воды.
Расход пара на собственные нужды котельного оборудования
Расход питательной воды
Расход химически очищенной воды (ХОВ) подаваемой в деаэратор.
- утечки из деаэратора
Энтальпия химически очищенной воды поступающей в деаэратор из подогревателя ХОВ.
Мощность питательного насоса.
Количество пара поступившего из концевых уплотнений турбины в конденсатор.
Количество пара поступившего из передних концевых уплотнений в деаэратор.
Энтальпия питательной воды после повышения давления в ПН.
энтальпия питательной воды за деаэратором:
Потери давления пара в линиях отборов составляют 8%
Потери тепла в теплообменниках составляют 2% от величины отбираемой теплоты
Разность энтальпий конденсата греющего пара и воды на выходе из ПВД - 84 ; для ПНД - 21 кДжкг
Энтальпия дренажа из ПВД на 418 кДжкг выше чем энтальпия воды на входе в этот подогреватель.
Энтальпия дренажа из ПНД принимается равной энтальпии конденсата греющего пара.
Расчет расходов пара на ПВД
Давление в подогревателе
Т.к. отбор №1 производится на выхлопе из ЦВД то
Энтальпия греющего пара
Энтальпия конденсата греющего пара
Энтальпия воды на выходе из ПВД
- подогрев воды в каждом ПВД
Температура и энтальпия воды на входе в теплообменники
Энтальпия дреажа пара из ПВД
Использованный теплоперепад
В точке пересечения изобары и линии процесса находим
Энтальпия воды на входе в ПВД
Энтальпия дреажа пара из подогревателя
- кпд теплообменника
Из отбора 1 на ПВД 6:
Из отбора 2 на ПВД 5:
Давление пара в отборе
Энтальпия воды на выходе из деаэратора
- средний подогрев воды в ПНД
Давление конденсатного насоса :
Энергетический баланс деаэратора :
Расход основного конденсата :
- расход в отборе на деаэратор
Расчет расходов пара на ПНД.
Энтальпия воды на выходе из ПНД
Энтальпия дренажа пара из подогревателя
Расходы пара на ПНД :
Из отбора 4 на ПНД 4:
Из отбора 5 на ПНД 3:
Из отбора 6 на ПНД 2:
Из отбора 7 на ПНД 1:
Расход пара в конденсатор через последнюю ступень турбины.
Мощность турбины с учетом отборов пара на регенерацию:
Электрическая мощность турбины.
Требуемый дополнительный расход пара на турбину.
Уточненный расход пара на турбоустановку.
Уточненный коэффициент регенерации.
Расчет ПТС с уточненным коэффициентм регенерации.
Расчет расходов пара на ПВД.
Коеффициенты отбираемого пара.
Регулирующая ступень:
Для одновенечной регулирующей ступенни:
Параметры за регулирующей ступенью и перед первым отсеком ЦВД :
Параметры за первым отсеком :
Параметры перед вторым отсеком :
Параметры за вторым отсеком :
Теплоперепад от пром. перегрева до конденсатора делим пополам между цсд и цнд
Параметры пара перед ЦСД :
Параметры пара за ЦСД :
Потери в ресивере приняты 2 %
Вычисляем потери с выходной скоростью для чего принимаем для последней ступени:
Кольцевая площадь последних лопаток :
- теплоперепад приходящийся на область влажного пара
Максимальный расход пара на ЦНД принимаем по оценке из условия 100 кгс на один поток :
- предварительоное значение общего выха в конденсатор
Вычисляем потери от влажности на последних ступенях :
- к-т учитывающий эффективность влагоудаления
Параметры пара на выходе из ЦНД :
Разбивка теплоперепадов по цилиндрам и отсекам турбины
Отборы разбивают проточную часть турбины на 8 отсеков :
Используемые теплоперепады отсеков находятся через вычисленные используемые теплоперепады цилиндров :
Использованные теплоперепады:
Находим приведенный теплоперепад турбины:
Уточняем значение расхода пара:
- общий выход в конденсатор
Мощност отсеков составляет :
Электрический КПД установки составляет :
Уточняем количество отбираемого пара :
Рис. 6. График изменения параметров пара при его расширении в турбине
Расчет газовой турбины
Для расчета газотурбинной части за основу возьмем хорошо зарекомендовавшую себя турбину Siemens SGT5-2000E (модернизированная ГТУ v.94.2 которая успешно эксплуатируется на ПГУ в России и за рубежом).
Основные технические характеристики заявленные производителем этой ГТУ таковы :
Мощность номинальная
Коэффициент полезного действия
Степень сжатия в компрессоре
Температура газов после ГТ
Для расчета зададимся некоторыми величинами а некоторые примем из прототипа :
Определение температуры воздуха после компрессора К
Определение температуры газов после газовой турбины К
- термический КПД цикла Брайтона
Удельная работа ГТУ кДжкг
Массовый расход рабочего газа кгс
Количество энергии подводимое к ГТУ при сжигании синтез-газа в камере сгорания кВт
В реакторе предполагается аллотермический процесс паровой газификации угля (с подводом тепла в реакционную зону извне) согласно уравнению реакции :
Расчет реактора газификации
Уравнение энергобаланса на 1 кг угля :
- теплоты сгорания углерода окиси углерода и водорода соответственно МДжкг
- энтальпия пара подаваемого в реактор для процесса газификации
Молекулярные массы соответствующих веществ :
- изобарная теплоемкость синтез-газа
- массовая доля углерода в угле
Определяем физическое тепло синтез-газа МДжкг.угля :
Теплота аллометрического процесса МДжкг.угля :
Теплота сгорания синтез-газа при высокой золоочистке МДжкг :
Удельный расход синтез-газа на реактор :
Удельный расход синтез-газа на ГТУ :
- удельный расход синтез-газа потребителю (20%)
Количество синтез-газа на ГТУ кгс :
Количество синтез-газа на ПТУ кгс :
Количество угля на реактор
Расчет режима №2 (работа энергоустановки
по парогазовому циклу Nэ=190+330 МВт)
Мощность паротурбинной установки :
- расход в головную часть турбины
Расход пара в конденсатор
Схема установки: ГВП ВД + Д + ГВП НД + 2 ПНД
Давление питательного насоса.
температура газов перед ГВП ВД
Количество теплоты переданное воде в газо-водяном подогревателе высокого давления :
- удельная изобарная теплоемкость продуктов сгорания находится по таблицам теплофизических свойств газов
температура газов на выходе из КУ
Количество теплоты переданное воде в газо-водяном подогревателе низкого давления :
Отборы 4 5 закрыты. ПНД4 и ПНД3 отключены
Расчет ПТС с уточненным коэффициентом регенерации.
Коэффициенты отбираемого пара.
- расход пара на реактор конверсии
Проведем более точную оценку к.п.д. отсеков турбины с использованием эмпирических формул
Для одновенечной регулирующей ступени:
Теплоперепад от пром. перегрева до конденсатора делим пополам между ЦСД и ЦНД
Максимальный расход пара на ЦНД принимаем по оценке из условия 180 кгс на один поток :
- предварительное значение общего выхода в конденсатор
Мощность отсеков составляет :
- с учетом расхода теплоты на газификатор и
расхода синтез-газа потребителю.
Расчет проточной части
Задаемся числом ступеней в отсеке средним диаметром первой ступени. Теплоперепад отсека известен. Варьируя степенью реактивности добиваемся лучшего отношения скоростей UCф
За расчетный режим для ЦВД принимаем режим работы с большим расходом пара т.е режим №1.
- расход в головную часть турбины на режиме №2
- расход в головную часть турбины на режиме №1
Принимаем количество ступеней
Задаемся средним диаметром первой ступени отсека :
Задаемся постоянным корневым диаметром для отсека :
Задаемся средним диаметром регулирующей ступени :
Определяем средний располагаемый теплоперепад на ступень
Расчет проточной части произведен в специальном программном приложении модернизированной программе RTPT разработанном студентами К-1 КФ МГТУ при содействии их научных руководителей. Результаты расчета приведены на рисунках 789.
За расчетный режим для ЦCД принимаем режим работы с большим расходом пара т.е режим №2.
Задаемся повышенным теплоперепадом на последнюю ступень - 200 кДжкг
По итогам расчета проточной части паровой турбины в программе RTPT получили следующие значения для мощности и к.п.д.:
Мощность представлена при автономном и комбинированном режиме работы соответственно. С учетом допустимой погрешности в расчетах данные значение можно считать приемлемыми.
Расчеты на прочность
Для расчета на прочность и исследования напряженного состояния были выбраны рабочая лопатка последней ступени ЦСД и внешний корпус ЦВД. Указанная ступень работает при высоких параметрах рабочего тела поэтому напряжения в отдельных сечениях деталей и узлов её конструкции представляют определённый интерес у конструктора. Корпус цилиндра высокого давления имеет продольный горизонтальный разъем. Две части корпуса скрепляются шпильками диаметр которых предстоит рассчитать.
Значения параметров на среднем диаметре последней ступени :
Располагаемый теплоперепад на ступень :
Реактивность рабочей решетки в среднем сечении :
в корневом сечении :
Критический перепад давлений для перегретого пара :
К-ты скорости для сопловой и рабочей решеток соответственно :
К-т расхода для сопловой решетки :
для рабочей решетки :
). Расчет пера лопатки на растяжение центробежными силами
Рабочие лопатки всех ступеней выполняются из стали ЭИ802 (15Х12ВМФ)
Плотность стали ЭИ802
Окружная скорость посередине длины лопатки
Отношение среднего диаметра к длине лопатки
Разбиваем лопатку по высоте на элементарные участки :
Площадь стандартного профиля (из атласа турбинных решеток) находим для каждого сечения
Центробежные силы растяжения :
Напряжение растяжения в пере лопатки :
). Расчет пера лопатки на изгиб силами пара
- число лопаток на рабочем колесе
Угол установки находим по атласу профилей :
- плотность пара за рабочей решеткой
). Расчет на прочность хвостовика лопатки
- высота рабочей части хвостовика
- площадь хвостовика
- радиус среднего сечения хвостовика
- сила действующая на каждую площадку хвостовика
Расчет разъема внешнего корпуса ЦВД на нераскрытие
-расчетное давление действующее на стык
Расчет производится по условию герметичности соединения. Полная сила растягивающая шпильки при действии расчетного давления складывается из силы действия среды на крышку и остаточной силы потребной для сжатия прокладки:
- внутренний диаметр корпуса
Вертикальную силу действующую на крышку можно с малой погрешностью определить по
Принимаем число шпилек равным:
(H)-осевая сила действующая на один болт.
(по рекомендациям Л.[2])
Расчетная сила действующая на шпильку
Определим расчетный диаметр шпильки:
(Па) - допускаемое напряжение при растяжении.
(Па)-предел прочности.
(Па)-предел текучести.
-запас по пределу прочности.
-запас по пределу текучести.
(Па) - допускаемое напряжение по пределу прочности.
(Па) - допускаемое напряжение по пределу текучести.
Дальнейший расчет ведем по меньшему значению :
Принимаем диаметр шпильки
Описание спроектированной паротурбинной установки
Таким образом в результате выполненных конструкторских тепловых и прочностных расчетов была спроектирована паровая турбина удовлетворяющая предъявленным требованиям.
Турбина имеет 7 нерегулируемых отборов пара предназначенных для подогрева питательной воды в ПВД основного конденсата – в ПНД деаэраторе до температуры 274°С при номинальной нагрузке турбины. Кроме регенеративных отборов допускаются отборы пара без снижения номинальной мощности на подогрев сетевой воды и на собственные нужды станции. В модернизированной схеме предлагается производить отбор пара после ЦВД на нужды газифигатора.
Турбина представляет собой одновальный трехцилиндровый агрегат выполненный по схеме 1ПВД+1ЦСД+1ЦНДх2.
ЦВД имеет внутренний корпус в патрубки которого вварены сопловые коробки. Паропроводящие штуцера имеют сварные соединения с наружным корпусом цилиндра и подвижные – с горловинами сопловых коробок.
Ротор ЦВД выполнен цельнокованым с реактивным облопачиванием что позволяет обеспечить высокую эффективность работы установки на переменных режимах. Передние и задние уплотнения в ЦВД выполнены блочно с обоймами на витых пружинах применение которых приводит к меньшему изнашиванию зубчиков в отличие от плоских пружин используемых в паротурбиностроении.
После промежуточного перегрева пар по двум паропроводам подводится к двум стопорным клапанам ЦСД. Стопорные клапаны совмещены с регулирующими и вынесены отдельно от корпуса ЦСД. Из выхлопных патрубков ЦСД пар по двум паропроводам подводится к ЦНД.
ЦНД – двухпоточный по пять ступеней в каждом потоке. За прототип был выбран хорошо зарекомендовавший себя на турбинах К-1200-240 и К-1000-553000 цилиндр низкого давления производства ЛМЗ с высотой последней лопатки 1200мм и площадью выхлопа в конденсатор 14 м2. Средний диаметр последней ступени ЦНД – 3000 мм. Из двух выхлопов после ЦНД отработавший пар поступает в общий конденсатор. Расход охлаждающей воды через конденсатор 36000 м3ч. Номинальная температура охлаждающей воды 26 °С.
Роторы частей высокого и среднего давления – цельнокованые ротор ЦНД – сварной. Все роторы имеют жесткие соединительные муфты и по две опоры. Упорный подшипник расположен между ЦВД и ЦСД. Фикспунт турбины находится на стыке выхлопа из ЦНД и входа в конденсатор.
Рабочие лопатки всех ступеней кроме регулирующей выполнены из профилей переменного сечения с цельнофрезерованными бандажами. Направляющие лопатки 1-16 ступеней выполнены из профилей постоянного сечения направляющие лопатки 17-20 ступеней выполнены с тангенциальным навалом что способствует более равномерному полю скоростей по высоте рабочих лопаток. Направляющие лопатки 18-20 ступеней выполнены переменного сечения что способствует хорошему совпадению поточных и скелетных углов сечений профилей. Все лопатки направляющие и рабочие имеют Т-образный хвост применена специальная конструкция замкового соединения.
Турбина снабжена паровыми лабиринтными уплотнениями. Новые усовершенствованные уплотнения имеют меньший зазор и работают на витых отжимных пружинах. Также предусмотрены специальные отверстия в обоймах уплотнений для циркуляции пара и их охлаждения. Из концевых каминных камер уплотнений всех цилиндров паровоздушная смесь отсасывается водоструйным эжектором через вакуумный охладитель. В качестве уплотнений на последних ступенях ЦНД используются сотовые уплотнения.
Максимальный расход пара при указанных начальных параметрах спроектированной турбины составляет 280 кгс. При этом турбоагрегат может развивать мощность измеряемую на зажимах генератора равную 350 МВт. Эксплуатировать паротурбинную установку при частичных нагрузках (до 40% от номинальной мощности) разрешено не более 24 часов. При нагрузке генератора меньше чем 40% от номинальной мощности эксплуатация установки запрещена.
Модернизация проточной части ЦНД содержит:
улучшение верхних и прикорневых обводов проточной части;
литые диафрагмы заменены на сварную конструкцию;
применение рабочих лопаток с цельнофрезерованными бандажами в том числе и в последних ступенях;
вынесение во всех ступенях кроме последних демпферных проволок из проточной части в тело бандажа;
применение новых профилей направляющих и рабочих лопаток учитывающих согласование поточных и скелетных углов профилей в том числе направляющих лопаток с тангенциальным навалом.
Предложенная в результате проведенных в исследовательской части расчетов полузависимая схема работы установки обеспечивает практически абсолютное равенство расходов на обоих режимах (кроме последних ступеней ЦНД которые на автономном режиме будут несколько недогружены из-за отбора на регенеративный подогрев питательной воды и первых ступеней ЦСД).
Предложенный способ выравнивания расходов – это включение дополнительного отбора пара после ЦВД. Этот отбор будет работать на комбинированном режиме и при останове газовой турбины будет закрываться. Пар с параметрами 4МПа и 330°С может быть использован в газификаторах питающих синтез газом ГТУ.
ТЕХНОЛОГИЧЕСКАЯ ЧАСТЬ
Соединительные муфты связывают отдельные роторы цилиндров турбины и генератора в единое целое – валопровод.
Муфты – очень ответственные элементы валопровода в значительной степени определяющие надежность работы всей турбины. Они передают крутящий момент с ротора на ротор и не должны разрушаться даже при его кратковременном повышении в 4-6 раз например при коротком замыкании в генераторе.
Различают муфты жесткие полужесткие и подвижные. В турбоагрегате рассматриваемом в дипломном проекте все валы ротора соединены жесткими муфтами. В технологической части диплома описывается техпроцесс выполнения левой полумуфты соединяющей валопровод турбины с валом генератора.
Жесткие муфты для обеспечения отсутствия вибрации требуют почти абсолютной центровки не допуская ни смещения ни излома осей соединяемых роторов.
Центровка полумуфт обеспечивается с помощью кольцевого выступа на одной полумуфте и впадины – на другой. Полумуфты стягиваются призонными болтами устанавливаемыми в строго соосные тщательно обработанные отверстия в полумуфтах с зазором 0001 – 0025 мм. Болты затягивают равномерно контролируя их удлинения. Крутящий момент в полумуфтах передается за счет сил трения между торцами полумуфт возникающих из-за сжатия призонными болтами.
Концы валов турбины и генератора на которые насаживаются полумуфты выполняют с небольшой конусностью (примерно 05%) а их посадочные поверхности пригоняются друг к другу по краске на длине 80-90% посадочного участка. Затем полумуфту нагревают в кипящей воде или ацетиленовой горелкой до 100-130 °С и насаживают на вал до упорного буртика следя за точным совпадением шпоночных пазов полумуфте и вале. Затем вставляют составные шпонки состоящие из двух клинообразных частей. Повторяемость сборки обеспечивается 4-мя отжимными болтами.
Выбор типа производства.
Серийность производства в машиностроении определяется номенклатурой и повторяемостью изготовляемых изделий их количеством в годовой программе выпуска с учетом весовой характеристики изделий сложности конструкции и трудоемкости их изготовления.
Полумуфта изготавливается небольшими партиями. На протяжении длительного промежутка времени производство не повторяется следовательно можно сделать вывод о том что целесообразно единичное его производство.
Для данного типа производства характерна широкая номенклатура выпускаемых изделий предметная специализация участков оснащенных универсальным оборудованием высокая квалификация рабочих.
Выбор типа заготовки.
ЛМЗ для своих турбин большой мощности применяет стали марок 35ХМА и 34ХН1М по пятой категории прочности с пределом текучести 50-60 кГмм2 пределом прочности не менее 70 кГмм2 относительным удлинением не менее 16% относительным сужением не менее 45% и ударной вязкостью не менее 6 кГммм2 . Видом заготовки для деталей соединительных муфт являтся поковки изготовленные методом свободной ковки. Они не должны иметь флокенов а также видимых невооруженным глазом плен трещин песочин волосовин усадочной рыхлости и прочих дефектов Наружные пороки допускаются только при условии что они могут быть выведены при последующей механической обработке. Испытание механических свойств производится от каждой поковки.
Анализ технологичности детали.
Технологичность конструкции изделия – это степень соответствия детали заданным условиям производства которые обеспечивают минимальную трудоемкость и себестоимость изготовления.
ГОСТ 14.201 - ГОСТ 14.204-83 посвящен анализу технологичности изделия сборочных единиц деталей заготовки. По этому ГОСТу существует два вида показателей технологичности: качественные и количественные.
На этапе технологической подготовки производства все детали должны быть подвергнуты тщательному анализу на технологичность в целях повышения степени конструкторской и технологической преемственности элементов детали.
Полумуфта имеет ряд ответственных посадочных и центровочных поверхностей. Достаточно жесткие допуски размерной точности ( ) точности формы (допуск формы 002) и требования предъявляемые к шероховатости поверхностей (Ra08 Ra16 Ra32) выдвигают довольно высокие требования к тому оборудованию и оснастке которая используется при изготовлении данной детали.
Материал заготовок отвечает требованиям технологии изготовления: при изготовлении нет необходимости применять сложные технологические процессы. Для хранения материала нет необходимости создавать определенные условия хранения и транспортирования.
Шероховатость базовых поверхностей удовлетворяет требованиям точности установки его обработки и контроля.
Конструкция деталей обеспечивает свободный подвод и выход режущего инструмента (резца фрезы) при обработке наружных поверхностей.
Исходя из приведенных расчетов и аргументов можно сделать вывод о том что вкладыш отвечает всем условиям технологичности.
Конструкция детали позволяет исключить количественную оценку технологичности полумуфты.
Количество поверхностей 14 квалитета точности существенно превышает количество поверхностей требующих более точную обработку. Это позволяет однозначно утверждать что к детали нет излишних требований по точности обработки а следовательно коэффициент точности обработки Кт>08 удовлетворяет условиям технологичности.
Средняя шероховатость поверхностей превышает Ra 3 следовательно полумуфта удовлетворяет требованиям технологичности по коэффициенту шероховатости.
Требования к механической обработке.
Муфта является проверочной базой при центровке роторов по полумуфтам; отступления допущенные при её изготовлении и сборке ухудшают работу турбины в эксплуатации. Поэтому при механической обработке к деталям соединительных муфт предъявляются высокие требования независимо от их конструкции. Для жестких муфт с насадными полумуфтами эти требования следующие:
) торцевое биение всех отдельных деталей муфты не более 003 мм;
) радиальное биение по отношению к оси деталей по наружному диаметру фланцевых соединений муфты 002 мм по прочим диаметрам не более 005-006 мм;
) точность выполнения наружного диаметра фланцев муфты и отверстий под соединительные болты по второму классу;
) чистота обработки цилиндрических поверхностей – 6;
) отклонения по шагу отверстий во фланцах под соединительные болты ±015 мм суммарное отклонение на 5-6 шагов не более ±02 мм;
) после посадки полумуфты на вал ротора проверка правильности посадки её на токарном станке (на биение);
) динамическая балансировка ротора должна проводиться с собранной на нем полумуфтой;
) при конусной посадке полумуфты на вал ротора для конусности в 05% допустимое отклонение конусности ±005% и чистота обработки конца вала 7-8 (пригонка конусной части производится по краске);
) шпоночные соединения выполняются в части ширины паза по 3-му классу точности непараллельность граней паза между собой и по отношению к оси допускается до 01 мм;
) натяг при посадке полумуфты на конусный конец вала 025-036 мм.
Приведенные выше требования к механической обработке деталей наборных муфт определяют и выбор технологических баз. В качестве радиальной базы выбирается центральное отверстие насаживаемых на вал полумуфт которое является и конструктивной базой а для соединительных частей к полумуфтам – центрирующие выступы на фланцах. Так как осевое положение полумуфт на валу определяется торцевой поверхностью их то за осевую технологическую базу принимают торцы полумуфт и соединительных частей которые должны быть при этом обработаны строго перепендикулярно к оси отверстия.
Маршрутная карта изготовления левой полумуфты.
Наименование содержание операции
Технический контроль: проверить по размерам заготовительного чертежа внешнему виду клеймение сверить с паспортом.
Токарная: обработать кругом на карусельном станке до размеров обдирочного чертежа с припуском от чистовых размеров по 5 мм на сторону
Термическая: провести снятие напряжений.
Токарная: на карусельном станке вырезать кольца А (рис.1) для определения остаточных напряжений и механических свойств материала поковки.
Токарная: срезать остатки припусков для пробы материала
Токарная: обработать кругом на карусельном станке с припуском по 2 мм на сторону
Токарная: точить внешнюю сторону фланца выдержав 20мм до цилиндрической поверхности.
Токарная: подрезать торец фланца до размера 240±02 мм.
Токарная: проточить фланец по окружности диаметром 920 мм
Токарная: расточить центральное отверстие на конус 1:200 (05%) по калибру с проверкой по краске.
Установочная: перекантовать проверить установки по индикатору с точностью до 002 мм
Токарная: подрезать второй торец до размера 510±04 мм.
Токарная: проточить цилиндрическую поверхность по диаметру 750 мм с соответствующими радиусами переходов по чертежу.
Контрольная: сдать токарную обработку ОТК клеймо пробы сохраняется.
Разметочная: разметить два шпоночных паза шириной 502мм.
Долбежная: тщательно проверить установку полумуфты на столе для получения необходимой параллельности граней пазов оси центрального отверстия полумуфты на долбежном станке произвести долбление размеченных пазов.
Сверлильная: установить полумуфту на столе радиально-сверлильного станка (соединительным фланцем вверх) установить по осевым рискам кондуктор как показано на чертеже произвести сверление зенкерование и развертывание 18 отверстий 55 мм под болты. Взаимное положение деталей фиксируется.
Сборочная: произвести насадку полумуфты на вал ротора.
Слесарная: добиться требуемой концентричности фланца полумуфты с осью ротора и перпендикулярности его торца той же оси шабрением.
Технический контроль: проверить выполнение всех контрольных операций отсутствие заусенцев трещин правильность маркировки.
Технический контроль: проверить правильность посадки полумуфты на вал на токарном станке (на биение).
Расчет общих припусков аналитическим методом.
Данный расчет произведем для основных поверхностей показанных на рис. 1 чтобы определить потребные размеры заготовки.
Рис. 2.1. Заготовка.
Для обрабатываемых поверхностей определяем следующие операции:
Токарную черновую обработку
Токарную получистовую обработку
Токарную чистовую обработку
Определение составляющих минимального припуска:
Высота микронеровностей и глубина дефектного слоя:
Черновое точение: мкм мкм;
Получистовое точение: мкм мкм;
Чистовое точение: мкм мкм;
Тонкое точение: мкм мкм;
Поверхность D: мкм; мкм; мкм.
Поверхность H: мкм; мкм; мкм.
Поверхность d: мкм; мкм; мкм; мкм.
Суммарные пространственные отклонения:
Поверхность D: мкм; мкм; мкм; мкм
Поверхность H: мкм; мкм; мкм: мкм
Поверхность d: мкм; мкм; мкм; мкм; мкм
Определение минимальных припусков :
Определение промежуточных размеров:
Предельные фактические (округленные) значения припусков:
Определение общих припусков на механическую обработку:
Проверка правильности расчётов:
– проверка выполняется;
Проверка показала что расчет произведен правильно.
Чертёжный размер заготовки:
Произведенный расчет позволяет изготовить деталь с минимальным коэффициентом использования материала а значит повысить технологичность детали. Чертеж заготовки показан на листе № графической части дипломного проекта.
Описание приспособления.
Сверлильная операция 085 производится с использованием приспособления - кондуктора чертеж которого представлен на листе № графической части диплома. Приспособление устанавливается на торец полумуфты с предварительно продолбленными пазами для шпонок и центруется по этим пазам. Кондуктор позволяет сократить время выполнения операции исключив из неё время на дополнительные промеры. Втулки установленные в отверстиях плиты кондуктора являются направляющими для сверла и способствуют повышению точности обработки.
Расчет режимов резания.
Подробно рассмотрим операцию 65 получистового точения полумуфты на токарном станке а также операцию 85 сверления сквозных отверстий под соединительные болты на вертикально-сверлильном станке.
Подбор оборудования.
Для выполнения токарно-винторезных работ выбираем станок 1Н65-5.
Станок токарно-винторезный модель 1Н65-5 (РМЦ=5000 мм) предназначен для выполнения разнообразных токарных работ включая точение конусов и нарезание резьб: метрических дюймовых модульных питчевых. Высокая мощность привода и жесткость станка широкий диапазон частоты вращения шпинделя и подач позволяют полностью использовать возможности прогрессивных инструментов при обработке различных материалов.
Стандартный комплект поставки:
- люнет неподвижный (диам. 70-780 мм);
- люнет подвижный (диам. 70-750 мм);
- патрон восьми кулачковый диам.1500 мм.
Табл. 2.1. Технические характеристики токарно-винторезного станка
Наибольший диаметр устанавливаемой заготовки мм:
Наибольший диаметр обрабатываемой заготовки мм:
Наибольшая длина обрабатываемой заготовки мм
Наибольший вес устанавливаемой заготовки кг
Высота резца устанавливаемого в резцедержателе мм
Размер конца шпинделя передней бабки по DIN
Внутренний конус в шпинделе бабки шпиндельной (метрический)
Количество ступеней частот вращения шпинделя
Диаметр цилиндрического отверстия в шпинделе мм
Пределы частот вращения шпинделя обмин
Пределы рабочих подач ммоб:
Наибольшее усилие резания кН
Наибольший крутящий момент на шпинделе кНм
Мощность главного привода кВт
Габаритные размеры мм:
Для выполнения сверлильных работ выбираем станок универсальный вертикально-сверлильный станок 2С132.
Универсальный вертикально-сверлильный станок предназначен для выполнения операций сверления зенкерования развёртывания и резьбонарезания в различных материалах. Наличие откидного стола позволяет обрабатывать на станке детали крупных габаритов. Позволяет использовать различные приспособления и инструменты расширяющие его технологические возможности. Станок может использоваться в мелкосерийном производстве на малых предприятиях в ремонтных мастерских.
Табл. 2.2. Технические характеристики вертикально-сверлильного станка
Диаметр сверления мм
Размер внутреннего конуса шпинделя мм
Наибольшее перемещение шпинделя мм
Расстояние от оси шпинделя до колонны мм
Наибольший ход подъёмного стола мм
Количество частот вращения шпинделя
Частота вращения шпинделя мин
Размеры рабочей поверхности стола не менее мм: длина
Размеры рабочей поверхности плиты мм: длина
Количество Т-образных пазов на столе (плите)
Ширина крепёжных Т-образных пазов мм
Расстояние между Т-образными пазами мм
Мощность электродвигателя кВт
Габариты станка мм: длина
ширина (без рукоятки подъёма стола)
Расчет режимов резания для токарной операции 65.
Полумуфта устанавливается в восьми кулачковый патрон станка 1Н65-5 согласно чертежу наладки приведенной на листе № графической части дипломного проекта. Инструменты при помощи которых производится обработка детали – резцы Т10К5(проходной для обтачивания наружной цилиндрической поверхности; подрезной для обтачивания плоской торцовой поверхности; расточной для растачивания сквозного отверстия).
Для этой операции рассчитываются режимы резания по трем переходам по методике описанной в [1] .
А) Скорость резания ммин при наружном продольном и поперечном точении и растачивании рассчитывается по эмпирической формуле:
а при отрезании прорезании – по формуле:
t – глубина резания мм.
Среднее значение стойкости Т при одно инструментальной обработке – 30 – 60 мин. Значение коэффициента Сv показателей степени xym приведены в таблице № 17 справочника технолога – машиностроителя [1].
- общий поправочный коэффициент на скорость резания учитывающий фактические условия резания;
kmv – коэффициент учитывающий влияние материала заготовки;
kГ – коэффициент учитывающий группу стали по обрабатываемости;
sВ – предел прочности стали 30;
knv – коэффициент учитывающий состояние поверхности;
kиv – коэффициент учитывающий влияние материала инструмента.
Б) Сила резания Н раскладывается на составляющие направленные по осям координат станка (тангенциальную Рzрадиальную Рy осевую Рx) и рассчитывается по формуле:
Постоянная Ср и показатели xyn для конкретных условий обработки для каждой из составляющих силы резания находятся по таблицам № 22 справочника технолога – машиностроителя [1].
- поправочный коэффициент учитывающий фактические условия резания.
в) Мощность резания кВт рассчитывается по формуле :
г) Частота вращения детали обмин рассчитывается по формуле :
D – наибольший диаметр детали.
Переход №1. Подрезать торец в 510±04 мм.
Для этого перехода используется резец подрезной ГОСТ 18880-73. Материал резца – Т5К10.
По формуле (2) находим скорость резания:
S=0.37 ммобsВ=500 МПА
По формуле (3) находим силу резания:
По формуле (4) находим мощность резания:
По формуле (5)находим частоту вращения детали обмин:
Переход №2. Точить 760 мм.
Для этого перехода используется резец проходной ГОСТ 18879-73. Материал резца – Т5К10.
По формуле (1) находим скорость резания:
S=0.36 ммобsВ=500МПА
Переход №3. Точить 750 мм с соответствующими радиусами переходов по чертежу.
S=0.35 ммобsВ=420МПА
Расчет режимов резания для сверлильной операции 85.
На полумуфту устанавливается специальное приспособление для сверления – кондуктор (см. лист № дипломного проекта) где производится сверление отверстий на станке 2С132 сверлами из быстрорежущей стали Р6М5.
Для этой операции рассчитываются режимы резания по двум переходам по методике описанной в [1].
А) Скорость резания ммин при сверлении рассчитывается по эмпирической формуле:
а при рассверливании зенкеровании развертывании – по формуле:
Т – среднее значение периода стойкости. Значение коэффициента Сv показателей степени xym приведены в таблице № 28 29 справочника технолога – машиностроителя[1].
kГ – коэффициент учитывающий группу стали по обрабатываемости.
sВ – предел прочности стали 20.
kиv – коэффициент учитывающий влияние материала инструмента;
б) Крутящий момент Нм и осевая сила Н рассчитывается по формуле :
при рассверливании и зенкеровании
Постоянная Ср и показатели xyq для конкретных условий обработки находятся по таблицам № 32 справочника технолога – машиностроителя [1].
- поправочный коэффициент учитывающий фактические условия обработки.
в) Мощность резания кВт рассчитывается по формуле (5):
частота вращения детали n обмин рассчитывается по формуле (6):
D – диаметр инструмента.
Переход №1. Сверлить 18 отверстий 8 мм по окружности с помощью кондуктора.
Для этого перехода используется сверло из быстрорежущей стали Р6М5.
S=0.28 ммобsВ=500МПА
По формуле (3) находим осевую силу и крутящий момент:
По формуле (6)находим частоту вращения инструмента обмин:
По формуле (5) находим мощность резания:
Переход №2. Рассверлить 18 отверстий 45 мм .
Для этого перехода используется сверло из быстрорежущей стали Р6М5 .
t=(D-d)2=22.5 ммkГ=1.0
S=0.45 ммоб sВ=500МПА
По формуле (4) находим осевую силу и крутящий момент:
Расчет норм времени на выполнение операций.
Расчет выполнен по методике указанной в [3]
а) на токарную операцию № 65:
- норма времени на станочную операцию мин;
- оперативное время мин;
- основное (машинное) время мин;
- вспомогательное время мин;
- число проходов при обработке поверхностей;
- припуск на обработку мм;
- глубина резания мм;
- расчетная длина обработки в направлении подачи;
- длина обработки по чертежу мм ;
- доп. длина на врезание и перебег инструмента мм;
- доп. длина на взятие пробных стружек резания мм;
- скорость обработки мммин
Расчет основного времени проводим полагая величину подачи постоянной.
б) на сверлильную операцию № 85
- длина обработки по чертежу м;
- доп. длина на врезание и перебег инструмента м;
- доп. длина на взятие пробных стружек резания м;
ИССЛЕДОВАТЕЛЬСКАЯ ЧАСТЬ
Выбор тепловой схемы ПГУ
В энергетике реализован ряд тепловых схем ПГУ имеющих свои особенности и различия в технологическом процессе. Были рассмотрены различные варианты реализации ПГУ с возможностью независимой работы газотурбинной и паротурбинной частей. Все они обладают существенными недостатками заключающимися по большей части в том что увеличение эффективности ПТУ (развитая регенерация тепла промежуточный перегрев пара) отрицательно сказывается на эффективности утилизации тепла отработавшего в ГТУ газа. И наоборот если мы используем более полную регенерацию тепла в котле утилизаторе то это приводит к снижению начальных параметров ПТУ (со сверхкритических до критических) и её КПД упрощению схемы регенерации ПТУ.
Перечислим преимущества и недостатки возможных вариантов ПГУ.
Лучшие показатели экономичности среди всех типов ПГУ имеют газопаровые установки с котлом утилизатором (рис. 3.1). При работе на природном газе синтез газе или водородном топливе они обеспечивают производство электроэнергии с КПД нетто до 60%. Вместе с тем для их работы необходимо бесперебойное круглогодичное снабжение газообразным топливом высокого давления (4МПа). Эти установки также могут работать и с применением синтез газа и водородного топлива в камере сгорания газовой турбины. Газопаровые комбинированные установки утилизационного типа имеют неоспоримые преимущества перед другими видами комбинированных установок но чтобы реализовать работу энергоблока по такой схеме необходимо соблюсти следующие условия:
По крайней мере 23 мощности энергоблока должно приходиться на газотурбинную часть. Это условие связанно с тем что только такое отношение мощностей газотурбинной и паротурбинной частей способно гарантировать выход утилизируемого газа из ГТУ в количестве достаточном для генерации пара в утилизационном паровом котле. Установки такого типа успешно работают на площадках многих электростанций. Максимальная мощность энергоблока составляет 500 МВт (две газовые турбины работают на одну паровую) но применение столь мощных газовых турбин сопряжено со значительными техническими и экологическими проблемами.
Рис. 3.1. Газопаровая комбинированная установка с котлом-утилизатором
Для работы паровой турбины необходимо чтобы обе газовые турбины тоже работали. Для установок у которых не предусмотрена возможность автономной работы газотурбинной части с выхлопом в атмосферу эксплуатация котла-утилизатора запрещена при остановленной паровой турбине.
Различие в ресурсах работы оборудования паровой и газовой частей приводит к тому что капитальный ремонт должен проводиться с большей частотой и при нем не соблюдается принцип комплексности. Ещё пока не накоплено достаточное количество статистических данных по работе комбинированных установок такого типа поэтому точно прогнозировать их надежность и ремонтопригодность пока что можно только при помощи методов математического моделирования.
В утилизационных комбинированных установках стараются не применять паровые турбины на сверхкритические параметры. Это обусловлено уменьшающимся сроком службы утилизационного котла и тем что паровые турбины средней мощности (до 220 МВт) которые целесообразно применять на установках такого типа не изготавливаются на сверхкритические параметры.
В исследовательской части не производился расчет тепловой схемы утилизационной комбинированной газопаровой установки в виду того что в ней не соблюдено главное условие проекта т.е. возможность обеспечить автономную работу паротурбинной и газотурбинной частей.
В схемах ПГУ сбросного типа (с низконапорным парогенератором) (рис. 3.2) существует возможность отказаться от воздухоподогревателя котла и от дутьевых вентиляторов. Автономный режим работы газовой и паровой частей возможен но в этом случае приходится производить дополнительную модернизацию схемы что сводит на нет большинство её преимуществ. А именно приходится вводить значительное количество резервного теплообменного оборудования а так же дополнительный автономный дутьевой вентилятор.
Рис. 3.2. ПГУ сбросного типа
Было принято решение отказаться от подробного расчета такой схемы в рамках данной исследовательской работы т.к. она теряет свои преимущества в сравнении с параллельной и полузависимой схемами работы парогазовых установок.
ПГУ с параллельной схемой работы (рис. 3.3) где большая часть мощности приходится на ПТУ дают высокие показатели экономичности лишь в том случае если ПТУ работает на сверхкритических параметрах пара. Это требует использования прямоточного котла утилизатора стоимость изготовления которого больше чем КУ барабанного типа. В такой схеме переключение между режимами работы происходит сравнительно просто т.к. паротурбинный и газотурбинный контуры связаны между собой только промежуточными трубопроводами но общая стоимость такой установки значительно выше чем у ПГУ с полузависимой схемой работы и ПГУ сбросного типа.
Рис. 3.3. ПГУ с параллельной схемой работы
Как вариант такой схемы в рамках исследовательской работы рассматривалась ПГУ с параллельной схемой работы с котлом утилизатором двух давлений где пар вырабатываемый в КУ попадает в ЦСД. Основная же часть пара подаваемого в голову ЦВД паровой турбины вырабатывается в паровом котле куда подается уже подогретая до температуры близкой к температуре кипения питательная вода. Подогрев воды осуществляется параллельно в газо-водяных утилизационных подогревателях и в регенеративных подогревателях питаемых из отборов турбины. Эта схема обеспечивает более полное использование высокопотенциального тепла уходящих газов. Расчет такой схемы был выполнен по той же методике что и в конструкторской части дипломного проекта для установки с полузависимой схемой работы. Результаты расчета приводятся ниже. Сама схема приведена на рис. 3.5.
Тепловая схема ПГУ с полузависимой схемой работы (рис. 3.4) отличается от тепловой схемы ПГУ с параллельной работой тем что теплота выходных газов ГТУ используется в ГВТО (газо-водяном теплообменнике) для нагрева конденсата и питательной воды. Это значительно упрощает технологический процесс и конструкцию котла а также обслуживание паросилового энергоблока. Его нагрузка не связана с работой энергетической ГТУ а тип и характеристика этой установки выбираются таким образом чтобы в КУ обеспечивалась достаточно полная утилизация выходных газов.
Существуют ограничения в отношении ПТУ. Увеличение расхода пара через отдельные отсеки проточной части вследствие уменьшения отбора пара на регенеративные подогреватели не должно приводить к повышению допустимых значений расхода пара в конденсатор и нагрузки электрогенератора.
Рис. 3.4. ПГУ с полузависимой схемой работы
При проектировании и строительстве ПГУ с полузависимой схемой желательно использовать модернизированные ПТУ например с реактивным облопачиванием ЦВД и ЦСД позволяющие пропустить повышенное количество пара через проточную часть в режимах работы по парогазовому циклу с меньшей потерей в эффективности.
Расчет комбинированной парогазовой установки с полузависимой схемой работы приведен в конструкторской части дипломного проекта т.к. эта схема была принята за расчетную для проектируемой турбины.
В рамках исследования ставилась задача сравнить характеристики работы паровой турбины работающей в составе комбинированной установки с параллельной и полузависимой схемами работы. В принципе эти схемы являются конкурирующими и выбор между ними при проектировании энергоблока должен производиться в зависимости от потребности в электрической тепловой энергии и графика сетевой нагрузки в регионе где планируется строительство. В параллельной схеме приоритет отдается более полному использованию тепла газов уходящих из газотурбинной установки при этом часть пара для паротурбинной установки генерируется в котле-утилизаторе и подается в голову ЦСД для обеспечения выхода на заданную мощность при комбинированном режиме работы. В другой полузависимой схеме приоритетным является достижение наивысшей эффективности в работе паротурбинной установки т.е. расход пара в отдельных частях турбины должен быть практически одинаковым на автономном режиме работы и при работе по парогазовому циклу. Более полным использованием регенерируемого тепла при этом пренебрегаем.
Рис. 3.5. Расчетная схема ПГУ с параллельной работой ГТ и ПТ частей
Расчет газовой турбины
Отметим что температура отработавших газов на выходе из ГТ должна быть достаточно высокой чтобы возможно было получать пар с температурой 565 С. Для этого возможно понадобится увеличить температуру в камере сгорания ГТ на 100 С и довести её до 1470 С
Теплота аллотермического процесса МДжкг.угля :
- удельный расход синтез-газа потребителю (20 %)
- расход в обвод ЦВД из пароперегревателя КУ
Расчет параллельной тепловой схемы
Предполагается что на регенерацию идет тот пар который подается в головную часть турбины.
Давление в барабане КУ
Схема установки: ГВП ВД 2 ПВД + Д + ГВП НД 2ПНД+ 2 ПНД
Расчет перегревателя КУ :
температура газов после газовой турбины
температура газов перед перегревателем
Температура пароводяной смеси при давлении в барабане :
Энтальпия пара в барабане
Энтальпия воды в барабане
температура газов перед испарителем
Расход газа на перегреватель КУ:
Количество теплоты переданное пару в перегревателе :
Расчет испарителя КУ :
Расход газа на испаритель КУ:
Количество теплоты переданное пароводяной смеси в испарителе :
температура газов перед ГВП НД
Для добавочного расхода :
Для основного расхода :
Энтальпия дренажа пара из ПВД на 418 кДжкг выше чем энтальпия воды на входе в этот подогреватель.
Энтальпия дренажа пара из ПНД принимается равной энтальпии конденсата греющего пара.
% питательной воды подогревается в ПВД а остальные 70% - в ГВП
Давление пара в отборе
Электрическая мощность турбины без дополнительного расхода пара.
Разбивка теплоперепадов по отсекам турбины:
Расчеты производились аналогичным образом как и в конструкторской части дипломного проекта
За расчетный режим для ЦCД принимаем режим работы с большим расходом пара т.е рижим №2.
За расчетный режим для ЦНД принимаем режим работы с большим расходом пара т.е рижим №2.
Характеристики работы паровой турбины на автономном и комбинированном режимах приведены на рис. 3.6-3.9. Расчет проточной части выполненный в программе RTPT дает следующие значения для мощности и к.п.д. турбины:
В результате проведенных расчетов решено было остановиться на варианте тепловой схемы ПГУ с полузависимой схемой работы где доминирующей по мощности является паротурбинная установка. За номинальный режим принят режим комбинированной работы ПГУ. Таким образом ПГУ данного типа можно рассматривать как ПТУ с высокотемпературной надстройкой в виде ГТУ. Повышение экономичности такого энергоблока при переходе к работе по парогазовому циклу составляет в среднем 2-3%.
Что касается эффективности использования теплоты сгораемого топлива то установка с параллельной схемой работы в этом отношении превосходит выбранную для проектирования. Отсюда можно сделать вывод что если основную часть времени эксплуатировать энергоблок в режиме работы по парогазовому циклу то использования параллельной схемы работы более целесообразно. В нашем же случае ввиду частой смены нагрузки предпочтение было отдано энергоблоку с полузависимой схемой работы которая обеспечивает меньшее изменение в расходах через проточную часть паровой турбины при переходе на автономный режим работы.
РАЗРАБОТКА ПРОГРАММЫ И МЕТОДИКИ ПРЕДВАРИТЕЛЬНЫХ ИСПЫТАНИЙ ОПЫТНОГО ОБРАЗЦА ВЫСОКОТЕМПЕРАТУРНОЙ ПАРОВОЙ ТУРБИНЫ С ВОДОРОДНЫМ ПЕРЕГРЕВОМ ПАРА МОЩНОСТЬЮ 100кВт
Существует два принципиальных метода повышения эффективности паротурбинных установок. Это увеличение термического к.п.д. за счет повышения начальных и понижения конечных параметров пара и второй – развитая система регенерации тепла. Считается оптимальным если два этих метода удается совместить на практике.
В предыдущем разделе исследовательской части речь шла о современном типе парогазовых установок с развитой системой регенерации тепла. Но если поставить целью дальнейшее повышение к.п.д. турбины то решение этой задачи может быть найдено только в применении высокотемпературных циклов. Реализация таких циклов связана с применением новых высокотемпературных технологий. Это и технологии охлаждения лопаточного аппарата высокотемпературной части турбины и методы снижения количества окислов азота образующихся в процессе высокотемпературного сгорания топлива и применение водородного топлива.
В рамках исследовательской части дипломного проекта была разработана программа и методика предварительных испытаний опытного образца высокотемпературной паровой турбины мощностью 100 кВт с применением водородного топлива.
Объектом испытаний является высокотемпературная паротурбинная установка (ВПТУ-100) с водородным пароперегревателем. Номинальная мощность снимаемая с вала турбины составляет 100кВт. Роль нагружающего устройства выполняет воздушный тормоз. Турбоустановка препарируется по рабочему тракту: устанавливаются термопары и датчики давления устанавливается динамометр измеряющий осевые нагрузки на подшипник а также виброметры для отслеживания критических частот ротора. Препарируется система электролиза обеспечивающая стенд реагентами и системы водо- и маслоснабжения.
Разработанная программа испытаний предусматривает следующие разделы:
· Проверка и подтверждение соответствия технических и эксплуатационных характеристик изделия требованиям технического задания. Определение основных параметров характеризующих работу ВПТУ-100 (КПД; расход пара расходы H2 и мощности снимаемой с вала; удельные расходы пара охлаждающей воды в конденсаторе и масла в системе смазки).
· Оценка показателей работы установки и указание путей повышения её экономичности. Выдача рекомендаций о возможности постановки изделия на производство и установки его в объекты.
Испытания планируется проводить при различных режимах нагружения турбоагрегата. При одном режиме производится измерение параметров при постоянном числе оборотов турбины и переменном расходе пара (изменяется снимаемая мощность). При другом – изменяется число оборотов ротора турбины при изменении момента сопротивления на валу воздушного тормоза (регулируется расход воздуха РМУ). Возможен также режим испытаний когда все параметры определяющие мощность турбоустановки изменяются динамически.
Рабочее тело – пар нужных параметров (3 МПа 800ºС) поступает из парогенерирующего узла. Температура пара не меняется при изменении режима испытаний. Частичные по мощности режимы работы турбины достигаются дросселированием пара на входе в турбину с помощь элементов регулирующей арматуры. Испытания проводятся при изменении давления на входе в турбину от 2 до 3 МПа с интервалом в 0.2 МПа.
Изменение частоты вращения при неизменных параметрах на входе в турбину достигается изменением степени дросселирования воздушного тракта нагружающего устройства – воздушного тормоза (ВТ). Дросселирование может осуществляться за счет установки дросселирующих шайб (5-10 типоразмеров) как по входу в ВТ так и по выходу из него. Максимально допустимая степень дросселирования определяется появлением неустойчивых режимов работы воздушного тормоза.
Для каждой степени дросселирования ВТ производится установление ряда режимов по частоте вращения от 10000 до 24000 обмин с интервалом 500 обмин. начиная с минимальной. Изменение частоты вращения производится за счет изменения давления на входе в турбину (изменения степени открытия регулирующего вентиля).
Измерение параметров согласно перечню указанному в табл. 3.1 выполняется автоматизированной системой измерений разрабатываемой специализированным предприятием. Разработанная система измерений включает в себя набор термопар и датчиков давления с унифицированным выходом по току или напряжению. Данные с датчиков и средств измерения передаются через контроллер ТРМ-138 и АС-3 фильтр к СОМ-порту ПЭВМ для отслеживания данных с параллельной записью их в память компьютера. Испытательный стенд оснащается системой аварийного пожаротушения и на нем ведется постоянный визуальный контроль над исправностью работающего оборудования.
Измерения выполняются непрерывно с частотой записи 01 Гц. Измерение на заданных режимах выполняется после выдержки 5-10 минут для достижения установившегося по температурам режима.
Примечание: Режим считается установившимся если скорость изменения температур не превышает 3°мин а частоты вращения ротора – не более 50 (обмин)мин.
Частота записи на режимах измерения при необходимости может быть увеличена до 0001 Гц. Измерения в виде совокупности записей на диске должны быть идентифицированы по времени начала и конца с номером точки в журнале испытаний. За время измерения должно быть выполнено до 100 но не менее 15 20 записей. Время опроса датчиков должно быть менее времени между двумя соседними записями.
А. Допустимые величины скоростей изменения параметров и частоты записей уточняются в процессе проведения испытаний.
Б. На стадии отладки системы измерений допускается использование показывающих приборов с ручной записью визуальных результатов измерений в журнал испытаний. В этом случае число записей каждого измерения может быть уменьшено до 1.
Табл. 3.1. Замеряемые параметры
Наименование единицы измерения
Параметры для определения к.п.д. и мощности турбины
Барометрическое давление КПа
Частота вращения ротора обмин
Температура на входе в турбину ºС
Избыточное давление на входе в турбину МПа
Избыточное статическое давление на выходе из турбины кПа
Избыточное статическое давление на входе в конденсатор кПа
Температура торможения на выходе из турбины ºС
Параметры для измерения расхода пара на турбину
Избыточное давление перед расходомерным устройством (РМУ) МПа
перепад давлений на РМУ кПа
температура пара перед РМУ ºС
Параметры для измерения тепловых потерь в уплотнении
Избыточное давление воды перед эжектором уплотнения МПа
Температура воды на входе в эжектор ºС
Температура воды на выходе из эжектора ºС
Параметры для определения тепловых и механических потерь в опорах
Избыточное давление масла на входе МПа
Температура масла на входе ºС
Температура масла на выходе ºС
Параметры для измерения мощности ВТ*
Параметры для измерения расхода воздуха:
избыточное давление перед расходомерным (по воздуху) устройством (ВРМУ) МПа
перепад давлений на ВРМУ кПа
температура воздуха перед ВРМУ ºС
Температура торможения на выходе из ВТ ºС
Осевое перемещение ротора мкм
Температуры корпусов в точках препарирования ºС (16 точек)
Осевая сила на ротор (по градуировочной характеристике) Н
Запуск установки осуществляется на исходном перегретом паре с температурой 560°С с выходом на режим холостого хода. Затем производится розжиг водородного пароперегревателя после чего турбина развивает номинальную мощность и работает на перегретом паре при Т=800°С.
Цели предварительных испытаний опытного образца:
- проверка правильности и качества сборки;
- проверка габаритов и массы;
- проверка работоспособности и параметров маслосистемы;
- проверка работоспособности и параметров системы откачки конденсата;
- проверка функционирования системы маслоохлаждения;
- проверка функционирования системы охлаждения конденсатора;
- проверка функционирования электрооборудования;
- проверка функционирования устройства измерения осевой силы;
- проверка функционирования датчика осевого перемещения ротора;
- проверочный запуск установки с выходом на номинальную мощность;
- построение характеристик турбины по результатам испытаний
Требования к условиям проведения испытаний:
- температура окружающего воздуха °С20±10
- относительная влажность воздуха % от 45 до 80
- атмосферное давление мм рт.ст.от 630 до 800
Табл. 3.2. Программа предварительных испытаний
Пункт программы испытаний
Наименование показателя
Номинальное значение
Предельные отклонения или пределы измерения
Проверка на соответствие комплектности и оценка качества технической документации предъявляемой на испытании
Проверка комплектности объекта испытаний его соответствия спецификациям сборочным чертежа и общим схемам
Проверка показателей назначения
Проверка правильности и качества сборки
(длина ×ширина ×высота)
Проверка работоспособности и параметров маслосистемы:
а) Проверка чистоты маслопроводов и каналов подводящих масло к подшипникам турбины
б) Определение расхода масла через форсунки
- давление (избыточное)
- расход (секундомер мерная емкость)
в)определение герметичности масляных стыков
г) проверка работы сигнализации уровня масла в маслобаке
Проверка работоспособности и параметров системы откачки конденсата:
а) Определение расходов конденсата на режимах соответствующих мощности 0 50 % Nном; 100% Nном (секундомер мерная емкость)
б) Отладка работы системы поддержания подпора
КН - уровня воды в конденсатосборнике
Проверка функционирования системы маслоохлаждения – определение гидравлических характеристик
(секундомер мерная емкость).
Давление на входе (избыточное) Ром
Проверка функционирования системы охлаждения конденсатора – определение гидравлических характеристик:
Давление на входе (избыточное) Рок
Проверка функционирования электрооборудования электрических преобразователей давления и температуры и вторичных приборов (указатели компьютер)
Проверка функционирования устройства измерения осевой силы
Проверка функционирования штатного датчика осевого перемещения ротора
Проверка функционирования средств измерения
* Настраивается масляным клапаном перепуска (МКП).
** Давление уточняется технологией.
Табл. 3.3. Параметры контролируемые в процессе испытаний
точнос-ти или погре-шность
Температура пара перед турбиной
точки на подводящем паропроводе
Избыточное давление пара перед турбиной
точки на подводящем паропроводе
Температура пара за турбиной
Давление пара за турбиной
Частота вращения ротора турбины
Избыточное давление масла на выходе из маслонасоса
Температура масла на выходе из маслонасоса
Температура масла на выходе из опор турбины
по1 точке на сливе из каждой опоры
Уровень масла в баке и конденсата в конденсатосборнике
Между рисками «мало» и «много»
Определяется визуально
Электрический сигнал минимального уровня масла в баке
Ниже риски «мало» 3 5 мм
Замыкается электрический сигнал в маслобаке
Избыточное давление воды на входе в охладитель масла в баке
Температура конденсата в конденсатосборнике
Температура воды на входе в охладитель масла в баке
Температура воды на выходе из охладителя масла в баке
Устанавли-вается в ходе испытаний
Осевое перемещение ротора относительно корпуса
Температура паровоздушной смеси перед эжектором отсоса из конденсатора.
Избыточное давление циркуляционной воды перед шайбой РМУ – расходомерного устройства
Перепад давления на шайбе РМУ
Температура циркуляционной воды перед шайбой РМУ
Температура циркуляционной воды за шайбой РМУ
Температура химочищенной воды
Давление химочищенной воды
Температура химочищенной воды на входе в ЭГ
Давление химочищенной воды на входе в ЭГ
Температура на выходе из ЭГ
Давление на выходе из ЭГ
Методика предварительных испытаний
Проверка по п. 1 Программы выполняется следующим образом.
Проверяется соответствие комплектности и качества предъявленных технических документов требованиям приведенным в п. 1 Программы.
Комплект считается выдержавшим испытаниям если комиссия признает комплектность и качество документов соответствующими требованиям п.1 Программы.
Проверка по п. 2 Программы выполняется следующим образом.
Проверяется соответствие комплектности объекта испытаний требованиям п. 2 программы.
Объект испытаний считается выдержавшим проверку если его комплектность соответствует требованиям п. 2 Программы сам он – спецификациям сборочным чертежам и общим схемам предусмотренных КД.
Проверка по п. 3.1 Программы выполняется следующим образом.
Проверяется внешний вид объекта испытаний на соответствие требованиям КД. Проверяется легкость вращения:
а) Ротора турбины соединенного с воздушным тормозом – без постороннего звука задеваний наличие выбега без подачи масла и с подачей масла при испытании маслосистемы;
Примечание: Роторы проворачиваются спецключем за свободные шлицы ротора турбины.
б) Электродвигателей маслонасоса и конденсатного насоса – коротким пуском ("толчком"). Одновременно определяется правильность направления вращения.
Объект испытаний считается выдержавшим проверку если его внешний вид соответствует требованиям КД легкость вращения и направление обеспечены.
Проверка по п. 3.2 Программы выполняется следующим образом.
Измеряются габариты и масса объекта испытаний.
Объект испытаний считается выдержавшим испытания если его габариты и масса соответствуют значениям указанным в п. 3.2 Программы.
Проверка по п. 3.3 Программы выполняется следующим образом.
1. Производится проверка чистоты маслопроводов и каналов подводящих масло к подшипникам турбины для чего:
а) Не снимается технологическая заглушка и не присоединяется маслопровод турбины к маслопроводу рамы вместо него подключается технологический шланг который направляется в технологическую мерную емкость;
б) В маслобак заливается горячее 70 80°С турбинное масло ТП 46 (50 литров);
в) Включается маслонасос производится прокачка маслопроводов с проверкой чистоты «на батист» с включением поочередно первого и второго масляного фильтра;
г) Определяется расход масла поочередно через первый и второй маслофильтры при различных давлениях (избыточных) масла: фиксируется давление Р'м и температура масла t'м. Давление регулируется клапаном до фильтра (35; 40; 45кгсм2).
2. Определяется расход масла через форсунки:
а) Подключается маслопровод турбины к маслопроводу рамы;
б) Слив масла из турбины подключается к технологической мерной емкости;
в) Определяется расход масла поочередно через передний и задний (вместе с подшипниками воздушного тормоза) подшипники турбины при различных давлениях Рм (избыточных) масла: фиксируется давление и температура масла t'м и t''м. Давление регулируется клапаном до фильтра (35; 40; 45 кгсм2).
3. Проводится проверка работы сигнализации уровня масла фиксацией уровня при срабатывании сигнализатора на соответствие градуировке мерного стекла.
4. Определяется герметичность маслосистемы:
а) подключаются все элементы маслосистемы визуально определяется герметичность масляных стыков при давлении Р'м = 4кгсм2 (избыточном) масла и установившейся температуре (факультативно).
5. По завершении работ по п. 5.1 5.4 заменяются фильтроэлементы на новые из маслобака сливается масло и заливается свежее.
6. Маслосистема объекта испытаний считается выдержавшей испытания если:
а) При проверке чистоты маслопроводов и каналов «на батист» на последнем нет следов грязи и посторонних механических частиц;
б) Расход масла через форсунки составляет 8 10 лмин при давлении 4 кгсм2;
в) Сигнализатор уровня масла срабатывает при достижении минимального и максимального уровня по градуировке мерного стекла;
г) При визуальном осмотре негерметичность не обнаружена – допускается отпотевание без каплепадения.
Проверка по п. 3.4 Программы выполняется следующим образом.
1. Определяется расход воды на режимах соответствующих мощности ВПТУ-100: 0; 50% Nном; 100%Nном и гидравлические характеристики системы откачки конденсата для чего:
а) Подключается технологическая мерная емкость к выходному штуцеру клапана Кк и подводится технологический водопровод с клапаном Кв1 к штуцеру Главного эжектора. Клапан Кэм блокируется в открытом положении. Открывается крышка заливной горловины конденсатосборника (КС) закрывается клапан Кк и заливается вода в КС до заливной горловины через клапан Кв1.
б) Открывается клапан Кк включается конденсатный насос (КН). Регулировкой открытия клапана Кв1 устанавливается примерно постоянный уровень воды в КС по оси штуцера перепуска. В ходе эксперимента не допускается увеличение уровня воды и допускается некоторое его снижение.
Измеряется расход воды (секундомер мерная емкость) и давление Ркн.
в) Закрывается клапан Кэм (разблокируется клапан и снимается электропитание) регулируется открытие клапана Кв1 для поддержания уровня воды.
Измеряется расход воды и давление Ркн.
г) Регулируя открытие клапанов Ккн и Кв1 производится измерения расхода в пределах 18 53 лмин и давления Ркн при каждом измерении расхода. Останавливается КН закрывается клапан Кк.
2. Проверяется работа концевых выключателей управляющих работой линии перепуска: включение – выключение клапана Кэм для чего:
а) Заливается вода в КС (п. 6.2) и закрывается клапан Кв1. Подается питание на клапан Кэм открывается клапан Кк и включается КН. Измеряется расход воды и давление Ркн. Фиксируется срабатывание клапана Кэм останавливается КН и закрывается клапан Кк. Определяется минимальный уровень воды в КС.
б) Открывается клапан Кв1 фиксируется срабатывание клапана Кэн и закрывается клапан Кв1.
Определяется максимальный уровень воды в КС.
По результатам определения уровней принимается решение по регулировке положения поплавков сигнализатора уровня.
3 Система откачки конденсата объекта испытаний считается выдержавшей испытания если:
а) Зависимость G=f(Pкн) где G – расход воды согласуется с характеристикой КН.
б) Концевые выключатели обеспечивают в заданные в п. 3.4 программы минимальный и максимальный уровни воды в КС.
Проверка по п. 3.5 Программы выполняется следующим образом.
Подключается технологический водопровод с клапаном Кв2 и манометром Ром к одному штуцеру маслоохладителя от водопроводной сети. Ко второму штуцеру подключается технологический трубопровод к технологической мерной емкости.
Измеряются расход воды (секундомер мерная емкость) при давлениях (избыточных) воды от 0 до 1 кгсм2 на входе в маслоохладитель.
Система маслоохлаждения считается выдержавшей проверку если расход воды составит 54 лмин при давлении (избыточном) на входе в маслоохладитель 1 кгсм2.
Допускается работа на отдельно взятом маслоохладителе.
Проверка по п. 3.6 Программы выполняется следующим образом.
Подключается технологический водопровод с клапаном Кв3 и манометром Рок к одному фланцу конденсатора от водопроводной сети. Ко второму фланцу подключается технологический трубопровод к технологической мерной емкости.
Измеряется расход воды (секундомер мерная емкость) при установившемся давлении сети на входе в конденсатор.
Допускается работа на отдельно взятом конденсаторе.
Проверка по п. 3.7 Программы выполняется следующим образом.
Электрооборудование: электродвигатели привода маслонасоса конденсатного насоса; электромагнитный клапан перепуска конденсата; концевые выключатели – контроль уровня в маслобаке и конденсаторосборнике преобразователи давления и температуры.
Электрические сигналы от преобразователей коммутируются в сигналы для компьютера которые выводятся на последний. Проверяется прохождение сигналов. Проверка функционирования электрооборудования может совмещаться с проверкой систем маслоохлаждения и откачки конденсата.
Электрооборудование считается выдержавшим испытания если работают электродвигатели электромагнитный клапан концевые выключатели и компьютер фиксирует заведенные на него параметры.
Проверка по п. 3.8 Программы выполняется следующим образом.
Выводы тензодатчиков и термопар через коммутирующее устройство заводятся на компьютер.
При воздействии на ротор турбины в осевом направлении (воздушный тормоз не устанавливается) измеряется перемещение ротора индикатором и фиксируются показания компьютера. Проверяется прохождение сигнала от термопар на компьютер.
Устройство измерения осевой силы считается выдержавшем испытания если показания перемещения ротора и компьютера совпадают с тарировочной кривой А=f() где: А – осевая сила в кг;
– осевое перемещение тензометрированной «балочки» т.е. ротора турбины в мм а также компьютер фиксирует показания термопар.
Проверка по п. 3.9 выполняется следующим образом.
Закрепляется датчик осевого перемещения ротора на специальном кронштейне и фиксировано перемещается относительно ротора сигнал измерения зазора через коммутирующее устройство на компьютер.
Датчик осевого перемещения ротора турбины считается выдержавшим испытания если показания на компьютере соответствуют реальному перемещению.
Проверка по пункту 3.10 выполняется следующим образом.
Средства измерения подключаются через контроллер ТРМ-138 и АС-3 фильтр к СОМ-порту ПЭВМ. Показания датчиков фиксируются и сохраняются на твердотельном носителе информации.
Средства измерений считаются выдержавшими испытания если их испытания соответствуют паспортным характеристикам.
Методика обработки результатов измерений
Обработка данных испытаний должна выполняться в темпе эксперимента по заранее записанной в компьютер программе реализующий приведенный ниже алгоритм и выводиться на экран в цифровом и графическом виде. Должна быть предусмотрена процедура исключения из обработки заведомо некондиционных измерений по указанию руководителя испытаний. По каждому датчику в обработку принимаются среднеарифметические величины по всем записям выполненным за время измерения на назначенном режиме:
В дальнейшем индекс «cp» опускается.
Для дублированных измерений кроме того производится аналогичное осреднение и по всем измеряющим один и тот же параметр датчикам.
При обработке данных испытаний параметры воды и водяного пара должны определяться с использованием библиотеки программ «WaterSteamPro» для чего на компьютер обработки и накопления данных производится запись этой библиотеки и устанавливается специальный ключ.
Алгоритм обработки данных.
Для построения характеристик турбины в обработку берутся данные указанные в табл. 3.1.
Измерение расхода воздуха производится устройствами двух типов: а) лемнискатного типа на входе в ВТ; б) с помощью критического сопла на выходе из ВТ.
Методика обработки данных.
1. Вычисление абсолютных давлений и температур выполняется по формулам:
2. Массовый расход пара Gвх поступающего в турбину.
Определяется в соответствии с методическими указаниями для стандартных сужающих устройств РД 50-213-80 и для специальных РД 50-411-83. Тип устройства выбирается на этапе разработки РКД стенда.
Вычисление массового расхода выполняется по формуле:
здесь - коэффициент расхода зависящий от типа и размеров сужающего устройства определяемый в соответствии с РД 50-213-80 и РД 50-411-83;
- коэффициент сжимаемости ;
d – диаметр узкого сечения сужающего устройства м ;
р – перепад давлений на РМУ;
r - плотность кгм3 определяется согласно разд. 6 РД 50-213-80.
После измерения фактических размеров рабочей части РМУ рабочая формула приобретает вид
и в таком виде записывается в программу обработки данных.
Мощность турбины определяется двумя способами:
а) с использованием измерений расхода пара и температур на входе и выходе из турбины;
б) с использованием аналогичных измерений по воздушному тракту нагружающего устройства – воздушного тормоза.
Табл. 3.4. Перечень измеряемых параметров для определения расхода пара через турбоагрегат и контроля загрузки его воздушным тормозом
Класс точности или погреш-ность
Параметры пара в расходомерном устройстве (РМУ) турбоагрегата
Температура пара перед шайбой РМУ
Избыточное давление пара перед шайбой РМУ
Перепад давления пара на шайбе РМУ
Параметры воздуха в РМУ воздушного тормоза
Давление на входе в мерный коллектор
точек равнорасполо-женные
Температура на входе в мерный коллектор
Перепад давления на мерном коллекторе
3.1. Внутренняя и эффективная мощности по измерениям в турбине
Внутренняя мощность
здесь hвх и hвых – энтальпия соответственно на входе в турбину и на выходе из нее
потеря мощности из-за утечек в уплотнениях определяется по подогреву воды в водоструйном эжекторе отсоса пара из рассечек уплотнений с учетом схемы уплотнений Газ ПТ 070-800-1 следующим образом:
а) расход пара удаляемый из системы уплотнений эжектором
- энтальпия воды эжектора соответственно по выходу и входу определяется по измеренным температурам воды;
- энтальпия пара турбины в месте его утечки в уплотнение (в данном случае от выхода из ступени Кертиса определяется по измеренным температуре и давлению пара турбины на выходе из ступени Кертиса) ;
- расход воды в эжекторе определяется в зависимости от давления воды перед соплом по экспериментальным данным проливки сопла или расчетом по площади сопла;
б) потеря мощности из-за утечек
hвых – энтальпия пара на выходе из турбины;
- полный расход пара отбираемый от выхода из ступени Кертиса в систему уплотнений.
где К – коэффициент определяемый опытным или расчетным способом.
Эффективная мощность
- потери на трение в опорах определяются по расходу масла и температурам масла на входе в турбину и выходе из нее. Для этого при проливке форсунок должна быть снята их расходная характеристика - по которой и определяется GМ. Тогда
). Вычисленная таким образом величина строго говоря является суммой механических и тепловых потерь однако поскольку разделить их не представляется возможным все потери условно относятся к механическим.
). Допускается определять по подогреву воды в водомасляном теплообменнике (ТО) предусмотрев для этого замер расхода и температур воды и масла на входе и выходе из ТО. Окончательный выбор методики определения - на этапе отладки измерений.
3.2. Располагаемая мощность
- энтальпия изоэнтропического расширения от параметров входа в турбину до давления выхода из нее определяется в следующем порядке:
а) удельная энтропия по параметрам входа
- с обр. к библиотеке
3.3. Мощность по измерениям на воздушном тормозе
– определяется по температуре барометрическому давлению на входе в ВРМУ и перепаду давлений (разрежению) в мерном сопле согласно ГОСТ 10921-90 по расчетным зависимостям;
- удельная теплоемкость воздуха; в расчет принимается среднеинтегральная величина для диапазона температур ;
- определяется по подогреву масла аналогично описанному в п.2.3.1.
Примечание: При отсутствии измерений позволяющих разделить механические потери в опорах турбины и ВТ это разделение осуществляется расчетным способом.
внутренний относительный ;
эффективный по измерениям на ВТ = .
5. Параметр нагрузки
Средний диаметр турбины ;
средняя окружная скорость
6. Проверка энергетического баланса.
Допустимый мощностной баланс составляет 0.03 (уточняется по результатам расчета погрешности эксперимента).
Построение характеристики турбины
Полученные по описанной выше технологии данные представляют собой зависимости в которых при постепенном уменьшении степени дросселирования в регулирующей арматуре на входе в турбину одновременно увеличивается частота вращения мощность расход пара и перепад давления на турбине. В то же время практический интерес представляет такие характеристики когда а) давление расход и мощность меняются при фиксированной частоте вращения; б) частота вращения меняется при неизменных температуре и давлении на входе. Сделать это можно следующим образом.
По выполненным измерениям для каждого варианта дросселирования воздушного тормоза простраиваются графики характеристик турбины в параметрах подобия:
Набор параметров может быть расширен в зависимости от конкретных целей. На каждом из этих графиков находят значения всех из указанных параметров при одном и том же значении . По полученным данным строятся зависимости всех параметров от например. Повторяют это при нескольких значениях . Тем самым получают зависимость каждого параметра от при =const.
Можно эти построения аналогично выполнить для другой из наиболее употребляемых пар параметров подобия: и .
Полученные данные с использованием построенных в безразмерной форме характеристик могут переноситься на другие режимы отличающиеся от режимов испытаний по физическим температурам и давлениям при условии равенства параметров подобия. В частности это позволит выполнить испытания на приведенных к расчетным условиям режимах и получить достоверные оценки параметров и эффективности турбины на них по испытаниям при пониженных температурах и частотах вращения что важно для сохранения математической части.
Результаты анализируются по ним выпускается технический отчет.
Проводимые испытания должны обеспечить возможность расчета параметров управления и регулирования ВПТУ-100 а также освоить на практике совместную работу электролизера для получения H2 и O2 из воды и водородного перегревателя где будет происходить реакция горения водорода с кислородом в паровой среде. Также экспериментальные данные по работоспособности проточной части турбины при высоких температурах полученные в ходе данных испытаний будут приняты за основу для дальнейших разработок высокотемпературных паровых турбин с начальными параметрами пара до Т = 1500°С и Р = 35МПа.
Свойства водяного пара при таких термодинамических параметрах ещё не достаточно изучены. В расчетах применяют методику разработанную МЭИ и оформленную в виде программного продукта “WaterSteamPro”. Но при переходе на суперсверхкритические параметры пара аппроксимация заложенная в основу этой методики обнаруживает значительные расхождения с теорией. Поэтому испытаний подобного рода необходимы для исследования свойств высокотемпературного водяного пара и дальнейшего развития паротурбостроения.
Теоретически применение энергетических установок подобного типа позволит достичь термодинамического КПД до 70% что значительно выше существующего на сегодняшний день для тепловых машин.
ОРГАНИЗАЦИОННО-ЭКОНОМИЧЕСКАЯ ЧАСТЬ
Для подобранной конструкции были установлены следующие удельные данные: себестоимость цена и трудоемкость одного килограмма массы турбины а также структура себестоимости и цены по статьям затрат; вид цены и коэффициенты использования материалов; структура материальных затрат перечень комплектующих изделий нормы их расхода и оптовые цены; вид и стоимость полуфабрикатов собственного производства; состав работ в процессе изготовления турбины и структура её трудоёмкости. Эти данные важны не только как детальная характеристика экономичности изготовления конструкции-базы сравнения они необходимы для последующих расчетов технико-экономических показателей по проектируемой турбине и сравнительного анализа. Перечисленные данные будут использованы для ориентировочной оценки себестоимости проектируемой турбины по методу удельного веса статей затрат.
Идея данного метода основана на том что близкие в конструктивном технологическом и функциональном отношениях изделия изготовляющиеся в аналогичных условиях производства имеют сходную структуру себестоимости по статьям затрат. Используя это обстоятельство необходимо рассчитать величину затрат по одной из статей затрат проектируемой турбины ("Основные материалы") и в соответствии со структурой себестоимости изделия-аналога определить величину затрат по остальным статьям себестоимости. Так будет ориентировочно определена себестоимость проектируемой конструкции.
Расчет затрат на основные материалы
Вес основных материалов в составе массы турбины – 343000 кг.
Вид и наименование материала
Уд. вес вес вида материала в составе осн. материалов
Уд. вес вес наимен-я материала в матер-ах дан. вида
а. крупносортная сталь
б. мелкосортная сталь
а. сталь углеродистая
б. сталь легированная
в. нержавеющая сталь
г. углеродистая листовая сталь
д. легированная листовая сталь
е. нержавеющая листовая сталь
Изделия дальнейшего передела
а. калиброванная сортовая сталь
б. легированная сортовая сталь
а. катаные высокого давления
г. тянутые высок. давл.
е. сварные больш. диам.
е. проволока константановая
ж. лента нейзильберовая
Для определения размера затрат по статье «Основные материалы» необходимо исключить стоимость реализуемых отходов учесть транспортно-заготовительные расходы и расходы на прочие материалы.
Стоимость основных материалов за вычетом реализуемых отходов определяется зависимостью:
где - стоимость черной массы основных материалов руб.;
- стоимость реализуемых отходов %; .
Стоимость основных материалов с учетом реализуемых отходов определяется:
где - коэффициент транспортно-заготовительные расходы %; .
Общая стоимость основных материалов определяется соотношением:
где - стоимость прочих основных материалов в процентах от стоимости ведущей группы основных материалов %; .
Полученная в результате расчета стоимость основных материалов используется для вычисления всех остальных статей затрат себестоимости проектируемой турбины и определения её полной себестоимости.
Используя структуру затрат полной себестоимости изделия-аналога вычислим себестоимость проектируемой турбины воспользовавшись величиной удельного веса затрат на сырье и основные материалы в данной структуре.
Структура затрат полной себестоимости
Вес статей затрат в полной себестоимости турбины
Сырье и основные материалы
Покупные и комплектующие изделия полуфабрикаты и услуги кооперирования
Полуфабрикаты своего производства
Итого материальные затраты:
Реализуемые отходы (вычитаются)
Материальные затраты за вычетом отходов:
Топливо и энергия на технологические нужды
Основная зарплата производственных рабочих
Расходы на подготовку в том числе:
а. отчисления в фонд новой техники
б. отчисления в фонд премирования в за освоение новой техники
Расходы на спецоснастку
Отчисления на НИР и ОКР
Итого условно-прямых затрат:
Общезаводские расходы
Итого производственная себестоимость:
Внепроизводственные расходы
Итого полная себестоимость:
Плановый уровень полной себестоимости проектируемой турбины используется для определения её цены:
где - средний уровень рентабельности продукции предприятий турбиностроительной промышленности; .
Выводы об экономической эффективности
проектируемого варианта турбины
После расчета себестоимости и оптовой цены турбины необходимо провести сравнительный технико-экономический анализ разработанного варианта конструкции. Для этого определяются и сопоставляются капитальные и эксплуатационные затраты по проектируемому и базовому вариантам.
Единовременные капитальные затраты:
б. транспортировка и строительно-монтажные работы (5% от цены)
Число часов использования установленной мощности
Годовая выработка электрической энергии
Эксплуатационные затраты:
б. стоимость годового расхода пара:
- удельный расход пара
- годовой расход пара
- стоим-ть 1т. пара – 100 руб.
Эксплуатационные затраты в расчете на 1000 кВт×час выработанной энергии
Амортизация рассчитывается линейным способом. Заявленный ресурс эксплуатации составляет 20 лет для базового варианта турбины и 30 лет – для проектируемого.
Сравнительный анализ ведется на базе показателей сравнительной экономической эффективности.
Годовой экономический эффект:
где - соответственно эксплуатационные затраты по базовой и проектируемой конструкциях;
- соответственно капитальные затраты по базовой и проектируемой конструкции.
- нормативный коэффициент эффективности дополнительных капитальных вложений
Коэффициент эффективности дополнительных капительных вложений:
- годовая экономия эксплуатационных затрат. Определяется разностью эксплуатационных затрат по базовой и проектируемой конструкции:
- дополнительные капитальные вложения. Определяются разностью капитальных вложений по проектируемой и базовой конструкции:
Срок окупаемости дополнительных капитальных вложений:
Общие данные о технико-экономическом преимуществе
усовершенствованного варианта конструкции
Технико-экономические показатели
Себестоимость 1000 кВт выработанной энергии
Срок окупаемости дополнительных капитальных вложений
Коэффициент эффективности дополнительных капиталовложений
Годовой экономический эффект
Вывод: технико-экономичекий анализ проектируемой турбины и базовой конструкции К-300-170 ЛМЗ показал что ее производство по сравнению с аналогом ведет к незначительному увеличению капитальных затрат но приводит к снижению эксплуатационных затрат. Спроектированная турбина по сравнению с турбиной-аналогом имеет более высокий КПД меньшие потери в цикле увеличенный на 50% ресурс полезного использования а также более низкую себестоимость вырабатываемой электроэнергии что позволяет судить об эффективности внедряемой конструкции и ее экономической целесообразности для производителя. Эффективность внесенных конструктивных изменений в базовый вариант изделия очевидна и изменения оправданы.
ПРОМЫШЛЕННАЯ ЭКОЛОГИЯ И БЕЗОПАСНОСТЬ ТРУДА
ОБЕСПЕЧЕНИЕ БЕЗОПАСНОСТИ ТРУДА ПРИ МЕХАНИЧЕСКОЙ ОБРАБОТКЕ ПОЛУМУФТЫ ВАЛОПРОВОДА ПАРОВОЙ ТУРБИНЫ
Оценка безопасности и условий труда
Технологический процесс включающий токарную фрезерную и шлифовальную обработку полумуфты осуществляется в условиях механического цеха с железобетонным полом. В цехе имеется водяное отопление цеховая магистраль сжатого воздуха осветительные и вентиляционные установки. Цеховой транспорт представлен тралью на монорельсе электрокранами и электропогрузчиками.
Эргономические характеристики трудовой деятельности оператора определяются спецификой системы «человек – станок – производственная среда» для оптимизации которой необходимо обеспечение эргономических требований.
На данном этапе производства можно выделить следующий ряд вредных производственных факторов:
- механические опасные факторы;
- повышенное напряжение в электрической цепи замыкание которой может произойти через человека;
- повышенная концентрация аэрозолей СОЖ;
- повышенный уровень шума;
- опасные факторы пожара (в случае его возникновения);
- психофизиологические вредные факторы возникающие в процессе труда (перенапряжение зрительного анализатора умственная и эмоциональная перегрузка неудобные рабочие позы).
Оценка механической безопасности
Механическим опасные факторы создают движущиеся части машин и механизмов. При работе на обрабатывающих станках источниками опасных факторов могут быть: резец стружка обрабатываемая деталь приспособление.
При воздействии на человека они вызывают травмы как легкие так и тяжелые. Во избежание травмирования применяют следующие меры защиты:
Блокировочные устройства препятствующие проникновению человека в опасную зону или устраняющие опасный фактор на время пребывания человека в опасной зоне (защитные кожухи и т.д.);
Сигнализирующие устройства информирующие о работе оборудования (световые и звуковые сигналы);
Дистанционное оборудование с помощью которого осуществляют контроль и регулирование оборудования с участков удаленных от опасной зоны.
Оградительные устройства (стационарные подвижные и переносные);
Различные предохранительные средства которые отключают оборудование при отклонении какого-либо параметра характеризующего работу оборудования;
Для удаления металлической стружки применяют специальные инструменты.
Оценка безопасности токарных работ при повышенной концентрации вредных аэрозолей СОЖ
Производственный процесс характеризуется повышенным содержанием пыли в воздушной среде рабочей зоны. Пыль образующаяся в процессе абразивной обработки состоит на 30-40% из материалов абразивного круга на 60-70% из материала обрабатываемого изделия. При обработке резанием повышается температура поверхности оборудования и материала и следует охлаждать зону резания с помощью подачи СОЖ а это является источником выделения в воздухе аэрозолей и паров воды.
Повышенное содержание паров газов и пыли вызывают затруднение дыхания головокружение и негативно сказывается на здоровье человека.
Для создания комфортного климата в рабочей зоне применяется общеобменная вентиляция.
Оценка электробезопасности
К факторам вызывающим опасность травмирования электрическим током относятся:
Повышенное напряжение в электрической цепи замыкание которой может произойти через тело человека вызывая электротравмы;
Аварийные режимы работы оборудования возникает при повреждением изоляции и замыканием фазы на корпус электрифицированного оборудования или на землю;
Для защиты в соответствии с ГОСТ 12.1.019-81 предусматривает зануление. Помимо этого для защиты от повышенного напряжения применяют:
Изоляцию токоведущих частей оборудования размещение их на недоступной высоте сооружение ограждений от случайного прикосновения;
Изолирующие подставки — применяются в качестве изолирующего основания (диэлектрические коврики).
Оценка акустической безопасности
Повышенный уровень шума на рабочем месте возникает при обработке резанием. Источники шума можно разделить на конструкторские и технологические.
Конструкторские источники шума связаны с работой станка на холостых режимах связанные с неточностью проектирования станка.
Технологические источники связаны с самим производственным процессом истечением струи сжатого воздуха из пневматической системы.
Длительное нахождение человека в шумном помещении приводит к снижению слуха нервно-психическим перегрузкам (эмоциональные перегрузки). Октавные уровни звукового давления и уровни шума на рабочем месте не должны превышать значений указанных в ГОСТе 12.1.003-83
Для снижения уровня шума и его вредного воздействия следует принимать меры. Такие как ограждение особо шумного оборудования звукопоглощающей перегородкой или звукоизолировать (звукоизолирующие кабины).
Оценка вибробезопасности
На станках возможно возникновение повышенного уровня вибрации связанного с движением режущего инструмента и работой двигателя то эта вибрация оказывает воздействие на рабочего обслуживающего станок. Повышенный уровень вибрации в резонансной или околорезонансной зоне может быть причиной вибрационной болезни – стойких нарушений физиологических функций организма обусловленных воздействием вибраций на центральную нервную систему.
Следовательно необходимо применение мер подавления вибраций и ограничения времени воздействия на человека. К таким мерам относятся:
Подкладывание под станок специальных ковриков;
Длительность рабочей смены не более 8 часов;
Установление 2 регламентированных перерыва учитываемых при установлении нормы выработки длительностью 20 минут через 1-2 часа после начала смены и длительностью 30 минут примерно через 2 часа после обеденного перерыва;
Обеденный перерыв длительностью не менее 40 минут примерно в середине смены.
Оценка климатических условий в рабочем помещении
Повышенная или пониженная температура рабочей зоны повышенная или пониженная влажность воздуха повышенная или пониженная подвижность воздух являются факторами недопустимыми в рабочем помещении. Эти факторы могут привести к появлению дискомфортного состояния рабочих.
Допустимые параметры микроклимата должны соблюдаться в соответствии с ГОСТом 12.1.005 - 88.
Для нормализации температурного режима и влажности воздуха в помещении используется общеобменная вентиляция. В холодное время года используется отопление а в теплое кондиционирование воздуха.
Оценка взрывопожарной безопасности механического цеха
Возможными источниками возгорания в отделении цеха является: электрическая искра электрическая дуга при коротком замыкании нагретая стружка.
Воздействие на человека открытого огня вызывает ожоги различных степеней тяжести. Выделение угарного газа при горение вызывает затруднение дыхание.
Пожарная безопасность при обработке металлов резанием обеспечивается:
Системой предотвращения пожара;
Системой пожаротушения;
Противопожарной защитой и организационно-техническими мероприятиями в соответствии с ГОСТом 12.1.004 - 91 «ССБТ. Пожарная безопасность. Общие требования».
В соответствии с НПБ 105-95 здание относится к категории «Д». К этой категории относятся производства в которых обращаются негорючие вещества и материалы в холодном состоянии (цеха холодной обработки материалов).
Обеспечение нормативных параметров освещенности
Различают следующие виды производственного освещения: естественное искусственное и совмещенное. При освещении производственных помещений используют естественное освещение создаваемое прямыми солнечными лучами рассеянным светом небосвода и меняющемся в зависимости от географической широты времени года и суток степени облачности и прозрачности атмосферы; искусственное освещение создается в основном электрическими источниками света и совмещенное освещение при котором недостаточное по нормам естественное освещение дополняют искусственным.
Система общего освещения представляет собой совокупность светильников расположенных над рабочими местами и питающимися от сети переменного тока 220В. Она дополняет естественное освещение и заменяет его в темное время суток. Система оказывает психофизиологическое воздействие на рабочих способствует высокой эффективности и безопасности труда снижает утомляемость и травматизм сохраняет высокую работоспособность продолжительное время.
Естественное и искусственное освещение в помещениях регламентируется нормами СНиП 23-05-95 в зависимости от характера зрительной работы системы и вида освещения фона контраста объекта с фоном.
Расчет искусственного освещения в механическом цехе
Задачей расчета является определение потребной мощности электрической осветительной установки для создания в помещении заданной освещенности.
Принимаем лампы типа ДРЛ светильники типа С35ДРЛ. Длина цеха А = 60 м. Ширина цеха В = 48 м.
Расчет числа и мощности ламп светильников
Установка и расположение светильников определяется параметрами:
h – расчетная высота
L – расстояние между соседними светильниками
l – расстояние от крайних светильников до стен.
Распределение освещенности по площади поля существенно зависит от типа светильника и отношения:
Для заданного типа светильника С35ДРЛ величина λ = ( 06 ÷ 10 ).
Расстояние между лампами выбираем кратным расстоянию между колоннами.
В соответствии с размерами цеха предварительно выбираем расстояние между светильниками L м:
L = λ h = ( 06 ÷ 10 ) 7
Принимая во внимание расстояние между колоннами и учитывая что расстояние светильников от стен или рядов колонн принимается в пределах 03 ÷ 05 L выбираем L = 6 м и подсчитываем количество светильников в одном пролете: N = 18 св. А затем количество светильников в цехе N = 78.
Определяем индекс помещения i:
Определяем коэффициент использования :
для этого необходим индекс помещения i и коэффициенты отражения поверхностей помещения. Для упрощения используем таблицу 2 для наиболее распространенных коэффициентов отражения.
Определим необходимый световой поток ламп:
где: Е – заданная минимальная освещенность; z – отношение
k – коэффициент запаса; – коэффициент использования;
S – освещаемая площадь.
Коэффициент запаса k можно принять равным 11; z для ламп типа ДРЛ принять равным 115.
S = 60 48 = 2880 м ;
По световому потоку выбираем ближайшую стандартную лампу из табл.3. Световой поток не должен отличаться от расчетного в пределах минус 10 и плюс 20 %.
Для заданных пролетов размещение светильников производим по углам площадки со сторонами L× L = 6 × 6 м.
Определение расчетной нагрузки
Расчетная нагрузка – это нагрузка по которой производим расчет электрической сети. Для осветительных установок расчетная нагрузка примерно равна установленной мощности:
N – количество светильников;
р – мощность лампы одного светильника;
– коэффициент спроса.
Для производственных зданий состоящих из отдельных крупных пролетов коэффициент спроса принимаем равным 095.
= 72 400 095 = 27360 Вт.
Рис. 5.1. План размещения светильников в механическом цехе
Таким образом для обеспечения оптимальной освещенности на рабочем месте необходимо установить 72 лампы светильника типа С35ДРЛ общей мощностью 27360 Вт.
ОБЕСПЕЧЕНИЕ ЭКОЛОГИЧЕСКОЙ БЕЗОПАСНОСТИ ПРИ ЭКСПЛУАТАЦИИ ПГУ-500
В ходе эксплуатации паротурбинный блок как известно оказывает серьезное воздействие на окружающую среду. К таким воздействиям следует отнести:
Выбросы вредных веществ в атмосферу
Сброс сточных вод ТЭС
Загрязнение твердыми отходами
Тепловая электростанция с установленной на ней спроектированной турбиной оказывает существенное влияние на воздушный бассейн в районе расположения. В результате сгорания органического топлива в дымовых газах образуются углекислый газ СО2 водяные пары Н2О азот N2 сера в виде окислов SO2 (сернистый газ) и SO3 (серный ангидрид) и летучая зола. К числу токсичных составляющих относятся окислы серы SО3 и SO2 оксид углерода СО и летучая зола. Около 99% в окислах серы составляет SO2.
Кроме указанных компонентов при высоких температурах в топочной камере образуется некоторое количество токсичных окислов азота в виде NO NO2 N2O4 N2O5 и др.
Основное количество углерода выбрасывается в форме СО2 и не относится к числу токсичных компонентов но в глобальном масштабе может оказывать некоторое влияние на состояние атмосферы и даже климат планеты. Оксид углерода СО является токсичным компонентом однако при рационально построенном процессе горения он выбрасывается в незначительном количестве.
Согласно ГОСТ 17.2.1.01 – 76 выбросы в атмосферу классифицируют:
)по агрегатному состоянию вредных веществ в выбросах. Это газообразные и парообразные (SO2 СО Ох углеводороды и др.); жидкие (кислоты щёлочи органические соединения растворы солей и жидких металлов); твёрдые (свинец и его соединения органическая и неорганическая пыль сажа смолистые вещества и др.);
)по массовому выбросу выделяют 6 групп тсут:
– не менее 001;2 – 001 ÷ 01;3 – 01 ÷ 10;
– 10 ÷ 10;5 – 10 ÷ 100;6 – свыше 100.
При неполном сгорании топлива в продуктах сгорания могут содержаться также углеводороды окись углерода СО и некоторые другие компоненты. Зола ряда органических топлив может иметь повышенную токсичность и содержать мышьяк свободную двуокись кремния свободную окись кальция. Зола мазутов содержит в частности окисел ванадия V2O5.
Для уменьшения выбросов золы применяются различные золоуловители которые классифицируются следующим образом:
)Механические золоуловители (циклон)
)Мокрые золоуловители (скруббер)
В качестве меры борьбы с выбросами с окислами серы и азота применяется предварительное обессеривание топлива и переработка сернистых топлив сжиганием на ТЭС(газификация).
Даже после очистки содержание вредных веществ в сотни раз превышает ПДК. Для снижения концентрации до приемлемых величин применяют рассеивание из высотных труб за счет турбулентного перемешивания с огромной массой воздуха концентрация снижается до норм ПДК.
В дипломной работе предлагается использовать для рассматриваемой энергетической установки современную технологию CCS (CO2 Capture and Storage) которая заключается в удержании углекислого газа из топлива до его непосредственного использования в камере сгорания газовой турбины и его последующем захоронении. Технология CCS широко применяется в ряде современных энергоблоков в США и Европе на установках с внутрицикловой газификацией угля (IGCC – Integration Gasification Combined Cycle). Принципиальная схема такого энергоблока приведена на рис. 2.
Рис. 5.2. Базовая схема IGCC электростанции с получением Н2 и захоронением СО2. Использование мембран удерживающих СО2
Существует два принципиальных варианта реализации такой схемы. Первый изображенный на рисунке выше представляет собой парогазовую установку с внутрицикловой газификацией угля и мембранным реактором конверсии с мембранами извлекающими СО2 из очищенного синтез-газа. Второй вариант заключается в использовании реактора конверсии с мембранами удерживающими водород. Для доставки водорода в цикл ПГУ и контроля его стехиометрической температуры горения применяется продувка азотом той части реактора куда попадает адсорбированный водород. Остальная часть очищенного синтез-газа подвергается дополнительному процессу рафинирования и все удержанные горючие элементы возвращаются в цикл а СО2 подвергается ожижению и захоронению. Принципиальная схема такой установки приведена на рис. 3.
Рис. 5.3. Базовая схема IGCC электростанции с получением Н2 и захоронением СО2. Использование мембран удерживающих Н2
Газификаторы угля делают возможным получение водорода достаточно высокого давления чтобы его можно было использовать в мембранных реакторах конверсии. В отличие от электростанций использующих реформинг природного газа для получения Н2 где применение Н2-мембран более целесообразно мембраны извлекающие СО2 могут составить конкуренцию Н2-мембранам на электростанциях с газификацией угля т.к. они обеспечивают дополнительную конверсию СО.
Использование энергетических установок с удержанием и захоронением СО2 может значительно сократить загрязнение окружающей среды и предотвратить опасность глобального потепления.
Одним из факторов взаимодействия ТЭС с водной средой является
потребление воды системами технического водоснабжения в т.ч. безвозвратное потребление воды. Основная часть расхода воды в этих системах идёт на конденсацию пара в конденсаторах паровых турбин. Остальные потребители технической воды (системы золо- и шлакоудаления химводоочистки охлаждения и промывки оборудования) потребляют около 7% общего расхода воды. В тоже время именно они являются основными источниками примесного загрязнения. Например при промывке поверхностей нагрева котлоагрегатов серийных блоков ТЭС мощностью
0 МВт образуется до 10 000 м3 разбавленных растворов соляной кислоты едкого натра аммиака солей аммония.
Кроме того сточные воды ТЭС содержат ванадий никель фтор фенолы и нефтепродукты. На крупных электростанции расход воды загрязнённой нефтепродуктами (масла и мазут) доходит до 10-15 м3ч при среднем содержании нефтепродуктов 1-30 мгкг (после очистки). При сбросе их в водоёмы они оказывают пагубное влияние на качество воды водные организмы.
Сжигание на электростанциях многозольного топлива с невысокой теплотой сгорания приводит к выходу большого количества золошлаковых материалов требующих утилизации и минимизации их вредного воздействия на окружающую среду. На большинстве ныне существующих тепловых электростанциях зола и шлак удаляются гидравлическим способом. Для этого требуется выделение значительных площадей земли под золоотвалы. Территория золоотвалов абсолютно не пригодна для эффективного использования в сельском хозяйстве и в промышленности. Основной путь решения проблемы создание системы отпуска золошлаковых материалов потребителям для различных нужд.
В решении общей проблемы снижение вредных воздействий энергоустановок на окружающую среду существенное значение приобретают вопросы борьбы с шумом. Основное и вспомогательное оборудование ТЭС является как правило источником шума. Это оборудование расположенное внутри главного корпуса воздействует только на обслуживающий персонал ТЭС и борьба с шумом от такого оборудования относится к вопросам охраны труда. Однако имеются источники шума которые могут воздействовать на район расположенный за пределами территории ТЭС. Эта проблема имеет особое значение для ТЭЦ расположенных в районе жилой застройки больших городов где нормы допустимого уровня шума приняты значительно более жесткими чем в цехах электростанции. Остро стоит проблема борьбы шумами от тягодутьевых устройств на ТЭС большой мощности. Несмотря на то что дымососы и дутьевые вентиляторы установлены на уровне земли звук от них распространяется по газо- и воздухопроводам как по волноводам к месту забора воздуха вентиляторов и устью дымовых труб у дымососов а оттуда по воздуху в окружающий район. Поскольку звук распространяется прямолинейно то исключительное значение имеет высота расположения источника над уровнем земной поверхности. Чем выше расположен источник звука тем на больший район вокруг ТЭЦ он может оказывать воздействие.
Для борьбы с шумом из высотных источников используют шумоглушитель. Так в газоходах между дымососом и дымовой трубой устанавливают плоский шумоглушитель. Дымовые газы двигаясь в каналах в которых размещены плиты с шумопоглощающим материалом снижают свою звуковую мощность до необходимого уровня.
Снижение звуковой мощности достигается использованием труб с газоотводящим стволом конической формы с прижимной кирпичной футеровкой или вентилируемым зазором.
На ТЭС наблюдается выделение огромного количества тепла в окружающую среду. Тепловые потери происходят:
)с охлаждающей водой;
)с уходящими газами;
)потери от горячих частей турбины паропроводов котла
Количество охлаждающей конденсаторы воды превышает количество конденсирующегося пара примерно в 40—70 раз. Температура охлаждающей воды при этом повышается по крайней мере на 8-10°С т. е. имеет место тепловое загрязнение водоемов. В настоящее время еще нет четких и единых технических и экологических решений полезного использования «тепловых сбросов» в связи с чем на большинстве электростанций создаются оборотные системы охлаждения конденсаторов турбин.
Температура уходящих газов составляет 120-170°С. Тепло выноситься в окружающую среду с частицами золы сбрасываемых из дымовой трубы. В настоящее время происходит развитие различных способов использование низкопотенциального тепла. Постоянно снижается температура уходящих газов и как следствие снижаются тепловые выбросы.
Паропроводы паровпуск корпус турбины имеют температуру примерно равную температуре острого пара которая составляет 540°С. Методом борьбы с тепловыми потерями в данном случае является теплоизоляция горячих частей турбины.
Расчёт теплоизоляционного покрытия паропровода острого пара
В спроектированной паротурбинной установке максимальную температуру будет иметь поверхность паропровода острого пара. В качестве теплоизоляционного покрытия паропровода выбраны известково-кремнистые сегменты.
В связи с необходимостью создания запаса толщины слоя изоляции пренебрегаем в расчёте сопротивлением теплоотдачи теплоносителя к стенке паропровода.
Коэффициент теплопроводности материала изоляции
- средняя температура слоя изоляции
t н. из. - наружная температура изоляции tmeпл - температура теплоносителя.
Полное термическое сопротивление:
Удельные линейные потери:
Рис. 5.4. Толщина теплоизоляции трубопровода
Рассчитанная система освещения обеспечивает требуемый уровень освещенности токарного цеха.
Для снижения тепловых выбросов применена тепловая изоляция. Для обеспечения температуры наружной изоляции tн.из.=20°С необходимо и достаточно изоляция толщиной 248мм.
Соблюдение приведенных выше норм по охране труда обеспечивает безопасные условия труда работникам и существенно снижает загрязнение окружающей среды.
А.В. Щегляев Паровые турбины. М.: Энергоатомиздат 1993.
В.И. Кирюхин Н.М. Тараненко Е.П. Огурцова и др. Паровые турбины малой мощности КТЗ. М.: Энергоатомиздат 1987.
А.И. Занин А.С. Соколов Паровые турбины. М.: Высшая школа 1988.
А.Г. Костюк В.В. Фролов Турбины тепловых и атомных электрических станций М.: Издательство МЭИ 2001.
Г.А. Зальф В.В. Звягинцев Тепловой расчет паровых турбин. М.: МАШГИЗ 1961.
Г.М. Кочетов Тепловой расчет паровой турбины М.: МВТУ 1979.
А.А. Жинов Методические указания к курсовому и дипломному проектированию «Комплекс программ для расчета осевой турбины по радиусу». Калуга 1997.
Г.С. Жирицкий В.А. Стрункин Конструкция и расчет на прочность деталей паровых и газовых турбин. М.: Машиностроение 1968.
Рекомендуемые чертежи
- 10.05.2023
- 25.01.2023
- 25.01.2023