Расчет цилиндрического двухступенчатого редуктора




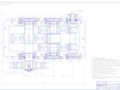
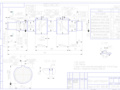

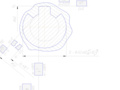
- Добавлен: 25.10.2022
- Размер: 2 MB
- Закачек: 0
Описание
Состав проекта
![]() |
![]() ![]() |
![]() ![]() ![]() |
![]() ![]() |
![]() ![]() ![]() ![]() |
![]() ![]() |
![]() ![]() |
![]() ![]() |
![]() ![]() ![]() ![]() |
![]() ![]() |
![]() ![]() ![]() ![]() |
![]() ![]() |
![]() ![]() ![]() ![]() |
![]() ![]() ![]() ![]() |
![]() ![]() |
![]() ![]() ![]() ![]() |
Дополнительная информация
ryirssrresrrsrrs-rrryiresryer.doc
Донбасская государственная машиностроительная академия
Расчетно-пояснительная записка к курсовой работе по дисциплине
«Взаимозаменяемость стандартизация и технические измерения»
Проект проверил:Абрамова Л.Н.
Чертежных форматовА1 – 1
Анализ конструкции и назначения сборочной единицы5
Допуски и посадки подшипников качения7
Допуски и посадки гладких цилиндрических соединений8
1 Выбор системы образования посадок .8
2 Обоснование посадок в гладких цилиндрических соединениях ..8
3 Выбор посадки с натягом расчетным путем 9
4 Выбор переходной посадки расчетным путем 12
Посадки шпоночных шлицевых и резьбовых соединений15
Выбор и обоснование метода достижения точности сборки узла17
Выбор расчет и обоснование средств и методов контроля точности деталей20
1 Выбор и обоснование средств измерения зубчатого колеса 20
2 Выбор и обоснование универсальных средств измерения для контроля
точности и шероховатости вала22
Обоснование допусков и технических требований к изготовлению деталей26
Расчетно-пояснительная записка содержит: 28 страниц 6 рисунков 4 таблиц
Объект проектирования – цилиндрический редуктор.
Цель работы – выбор и обоснование точностных параметров деталей и соединений обеспечивающих служебное назначение и качественные показатели изделий.
С учетом служебного назначения составлены и обоснованы технические требования предъявляемые к точности изготовления основных деталей и соединений цилиндрического редуктора. Принята система отверстия назначения посадок расчетным методом выбрана посадка с натягом соединения зубчатого колеса с валом. С учетом класса точности выбраны посадки подшипников качения шпоночных шлицевых и резьбовых соединений. Обоснована методика достижения точности сборки узла. Назначен и обоснован комплекс измерительных средств для контроля зубчатого колеса и вала.
Разработан сборочный чертеж узла схемы расположения полей допусков соединений рабочие чертежи вала и зубчатого колеса.
ТЕХНИЧЕСКИЕ ТРЕБОВАНИЯ ДОПУСК ПОСАДКА ПРЕДЕЛЬНЫЕ КАЛИБРЫ ПОДШИПНИК РАЗМЕРНЫЕ ЦЕПИ МЕТОД ДОСТИЖЕНИЯ ТОЧНОСТИ ЗАМЫКАЮЩЕГО ЗВЕНА ПРЕДЕЛЬНЫЕ ОТКЛОНЕНИЯ РАЗМЕРА ОТКЛОНЕНИЯ РАСПОЛОЖЕНИЯ ПОВЕРХНОСТИ.
В рыночных условиях основной задачей конструкторов и технологов является разработка и изготовление принципиально новых изделий высокого качества которые обеспечили бы их конкурентоспособность и получение прибыли.
К сожалению планово-распределительная система в бывшем СССР в полной мере не стимулировала работников к достижению высокого качества поскольку в достаточной мере не была направлена на запросы потребителей и отсутствовала конкуренция.
Зачастую это проявлялось в некоторой небрежности при размерной отработке чертежей изделий в части обоснованного назначении технических требований к изготовлению деталей и сборки узлов и соединений.
Между тем именно разработка чертежей и технологической документации связанная с выбором необходимой точности поверхностей и шероховатости. обоснованием посадок с учетом технологических особенностей обработки выбором контрольно-измерительных средств расчетом размерных цепей и особенно с обоснованным нормированием отклонений формы и расположения в первую очередь формирует качественные показатели машиностроительных изделий.
Большое значение для развития машиностроения имеет организация производства машин и других изделий на основе взаимозаменяемости создание и применение надежных средств технических измерений и контроля деталей.
Наиболее широко применяется полная взаимозаменяемость которая обеспечивает возможность беспригонной сборки любых независимо одна от другой изготовленных деталей в сборочные единицы а последних в машины. Взаимозаменяемыми могут быть как отдельные детали так и сборочные узлы и изделия в целом.
При полной взаимозаменяемости сборку выполняют без доработки деталей и сборочных единиц.
В курсовой работе обоснованы технические требования к изготовлению деталей и сборки изделия установлен комплекс измерительных средств для контроля вала и зубчатого колеса.
Анализ конструкции и назначения сборочной единицы
В курсовой работе рассмотрен цилиндрический двухступенчатый редуктор. Опоры валов образованы подшипниками качения (радиальными шариковыми однорядными):
- быстроходный вал № 324 (поз. 25);
- промежуточный вал № 320 (поз. 24);
- тихоходный вал № 315 (поз. 20).
Быстроходный вал редуктора получает вращательное движение от электродвигателя через ременную передачу. На тихоходном валу находится звёздочка посредством которой сообщается крутящий момент исполнительным механизмам. Кроме того часть мощности отбирается с промежуточного вала.
При сборке редуктора валы собираются за пределами корпуса и в собранном виде устанавливаются в корпус.
Быстроходный и промежуточный валы – вал-шестерня которые находятся в зацеплении с шевронными колёсами. Вследствие того что валы выполнены ступенчатыми и за счет распорных втулок колеса удерживаются от осевого смещения.
Подшипники крепятся в корпусе с помощью накладных крышек которые крепятся винтами. Для уплотнения предусмотрены манжеты и прокладки.
Зубчатое колесо 5 установлено на валу посредствам шпоночного соединения 6 и 7 установлены на валах по посадке с натягом. Шкив установлен с помощью шпонки. Тихоходный вал на конце с шлицевым соединением на нём установлена звёздочка цепной передачи.
Крепление крышки корпуса к корпусу редуктора осуществляется болтами смещение ее при сборке предотвращается с помощью штифтов.
Редуктор силовой корпус чугунный температура нагрева корпуса - 40°С; температура нагрева зубчатых колес - 70°С.
Требования к точности вращения вала
Радиальная нагрузка кН
Эксплуатационные параметры и технологические возможности сборки соединений с натягом
Крутящий момент Т Н·м
Имеется оборудование для сборки
Стабильность технологических режимов
Требуемая точность центрирования - относительно высокая твердость втулки 260 285 HВ.
Скорость вращения мс
Требования к точностным параметрам
Обозначение параметра на эскизе
Предельные значения мм
Риск выхода значений параметра за установочные пределы не более %
Допуски и посадки подшипников качения
Устанавливаем тип и номинальные размеры подшипников по справочнику исходя из их номеров указанных в спецификации сборочной единицы. Затем с учетом служебного назначения изделия определяем класс точности.
Определяем вид нагружения колец подшипников качения: внутреннее кольцо вращается- циркуляционное; наружное кольцо неподвижно - местное.
Выбор посадок колец подшипников осуществляем по ГОСТ 3325-85. Для этого воспользуемся таблицами рекомендуемых посадок учитывая класс точности подшипников. Посадки наружного кольца подшипника (имеющего местное нагружение) с корпусом назначаем с зазором чтобы при работе нагрузка распределялась по периметру кольца равномерно вследствие периодического проворачивания кольца внутреннего кольца (имеющего циркуляционное нагружение) с валом - с натягом.
Требования к точности вращения вала – нормальные назначается 0 класс точности подшипников. Сведенья об подшипниках качения приводим в таблице.
Таблица 2.1 – Сведенья об подшипниках качения
корпус-наружное кольцо
внутреннее кольцо-вал
Рисунок 2.1 – Схема расположения полей допусков подшипника узла 1242
Допуски и посадки гладких цилиндрических соединений
1Выбор системы образования посадок
Выбор системы отверстия или вала для той или иной посадки определяется конструктивными технологическими и экономическими соображениями.
В большинстве случаев отдается предпочтение системе отверстия так как она обуславливает значительное уменьшение номенклатуры режущего и измерительного инструмента вследствие чего является более экономичной чем система вала.
В некоторых случаях более предпочтительна система вала: для шпоночных соединений и соединений наружного кольца с корпусом.
Но в некоторых случаях назначают и внесистемную посадку для соединений: распорное кольцо с валом или втулка с валом это связано с изготовлением деталей.
Важно также правильно выбрать квалитеты (допуски) сопрягаемых размеров соединения поскольку от этого зависят – качество и долговечность работы соединения стоимость и производительность изготовления деталей.
В курсовой работе для соединения 62 с гарантированным натягом производят выбор стандартной посадки на основе расчётов с помощью ЭВМ. Выбор всех остальных посадок в соединениях осуществляется используя рекомендации в литературе.
2 Обоснование посадок в гладких цилиндрических соединениях
В соединениях редуктора применены наиболее предпочтительные посадки применимые для всех узлов общемашиностроительного применения. В редукторе используются посадки с зазором с натягом и переходные. Посадки с зазором используют для посадки крышек в корпус распорных втулок на валах в шпоночных соединениях.
Для гладкого соединения (корпус-глухая крышка) назначаем посадку 260 (поз. 111) 215 (поз. 110) 215 (поз. 113) 160 (поз. 114) где Н7 - поле допуска отверстия под подшипник d11 - назначаем исходя из того что точное центрирование таких крышек по отверстию корпуса не требуется.
Для гладкого соединения (корпус - проходная крышка) назначаем посадку 160 (поз. 19) 260 (поз. 112). Соединение корпуса с крышкой должно быть подвижным и разъемным (с зазором). Поле допуска отверстия принято Н7 из условия посадки подшипника качения. В проходной крышке расположено уплотнение манжетного типа. Для надёжной работы уплотнения манжета должна быть соосна оси вращения вала. Отклонения от соосности вызывают следующие причины: радиальное смещение крышки при сборке относительно отверстия корпуса в пределах посадочного зазора отклонение от соосности посадочной поверхности под манжету в крышке и оси центрирующей поверхности. Чтобы ограничить радиальное смещение проходной крышки поле допуска центрирующей поверхности по ГОСТ 18512 - 73 задают h9.
Для соединений 163 и 152 (втулка - вал) назначаем посадку D9m6 и A11u8. Посадки втулок должны иметь минимальный зазор или минимальный натяг. При большом зазоре втулка превращается в кольцо. При большом натяге усложняется сборка деталей.
Для соединения 72 и 62 (зубчатое колесо - вал) назначаем посадку H8u8 - c натягом чтобы при действии на колесо внешней нагрузки не нарушалось касание сопрягаемых поверхностей то есть не происходило раскрытие стыка.
Для соединений 53 193 и 84 назначаем соответствующие посадки из ряда рекомендуемых H7k6 H7n6 H7m6 . Для надежной передачи крутящего момента назначаем переходную посадку. При этом с назначением переходной посадки в соединении возможен зазор или недостаточный натяг вследствии чего возникает фрейтинг - корозия поэтому посадку следует назначать с меньшей вероятностью зазора.
Для соединений 274 и 263 (вал - манжет) назначаем поле допуска на вал d9.
3Выбор посадки с натягом расчетным путем
Посадки с натягом предназначены для неподвижных неразъёмных (или разбираемых лишь в отдельных случаях при ремонте) соединений деталей как правило без дополнительного крепления винтами штифтами шпонками и т.п.
В отличие от других способов обеспечения неподвижности деталей в соединении при передаче нагрузок посадки с натягом позволяют упростить конструкцию и сборку деталей и обеспечивают высокую степень их центрирования.
Рассчитываем посадку с натягом при сборке соединения с нагревом зубчатого колеса на вал и нагрузке осевой силой и крутящим моментом (позиция на эскизе 62).
При запрессовке деталей произойдёт растяжение втулки на величину NA и одновременное сжатие вала на величину NВ причём
Из задачи определения напряжений и деформаций в толстостенных цилиндрах известны зависимости:
где p - давление на поверхности контакта вала и втулки Па; D - номинальный диаметр соединения мм; - модуль упругости материала вала и втулки Па; - коэффициенты Ляме определяемые по формулам:
где - размеры деталей соединения мм (см. рис. 3.3.1); - коэффициенты Пуассона.
Из вышеприведенных уравнений следует:
где рэ – эксплуатационное давление на контактных поверхностях соединения Па;
D - номинальный диаметр соединения м; и - модуль упругости материала вала и втулки Па; и - коэффициенты Ляме.
Контактное эксплуатационное давление: при сдвигающем усилии Р (в Н)
где - длина контакта сопрягаемых поверхностей м; - коэффициент трения при установившемся процессе распрессовки или провертывания; n – 12 2- коэффициент запаса.
Прежде чем приступать к выбору посадки следует проверить обеспечение прочности соединения. Для этого на основе теории наибольших касательных напряжений определяют максимально допустимое давление pmax при котором отсутствует пластическая деформация на контактных поверхностях деталей.
где и - пределы текучести материалов охватываемой и охватывающей деталей; - коэффициент зависящий из отношения и выбираемый по графику.
Наибольший расчётный натяг при котором возникает наибольшее допустимое давление pдоп находим по формуле
Стандартную посадку выбирают таким образом чтобы детали не провертывались одна относительно другой поэтому
где и- табличные значения выбранной стандартной посадки с натягом.
В процессе запрессовки неровности на контактных поверхностях деталей сминаются и в соединении создается меньший натяг что уменьшает прочность соединения. Смятие неровностей зависит от их величины метода и условий сборки соединения механических свойств материала деталей и др. факторов. Эту правку необходимо определять по формуле:
где и - средние арифметические отклонения профилей сопрягаемых поверхностей по ГОСТ 2789-73.
В сборки с нагревом охватываемой детали температура до которой она должна быть нагрета:
где - температура помещения сборки; - минимально необходимый зазор (мм) при сборке зависящий от массы размеров деталей и применяемых приспособлений; - коэффициент линейного расширения при нагреве.
Рисунок 3.3.1 - Расчетная схема посадки с натягом
Выбор и обоснование посадки с натягом
конструктивных и технологических параметров соединения.
Диаметр соединения мм d=12000
Диаметр отверстия охватываемой детали мм d1=000
Принятый диаметр наружной поверхности охватывающей детали мм d2=19000
Длина соединения мм l=9500
Материал деталей: охватываемой – Сталь 45 охватывающей – Сталь 45
Предполагаемый вид сборки - С предварительным нагревом
Нагрузка в соединении:
Крутящий момент Нм T=500000
Осевая сила Н P(Fa)=250000
Шероховатость поверхностей мкм: Raв=320; Raо=080
Коэффициент трения f=014
Коэффициенты учитывающие смятие микронеровностей: kв=050; kо=050
Коэффициенты Пуассона: Mв=030; Mо=030
Коэффициенты линейного расширения: Aв=11500E-005; Aо=11500E-005
Модули упругости материалов Па: Eв=20600E+011; Eо=20600E+011
Пределы текучести материалов Па: Sтв=34000E+008; Sто=34000E+008
Температуры соединения град С: рабочая tраб=50; сборки tсб=20
Основные данные расчета предельных натягов
Коэффициенты Ляме: Св=070; Со=263
Необходимое минимальное давление в соединении Па pmin=1662766778
Необходимый минимальный натяг мкм Nmin=3223
Допустимое минимальное давление на поверхности Па
охватываемой детали pma охватывающей детали pmaxo=11853850416
Допустимый максимальный натяг в соединении мкм Nmax=22975
Поправки мкм: на смятие неровностей (шероховатости) Nш=2000
на различие рабочей и сборочной температур деталей Nt=000
Минимальный расчетный натяг мкм Nmin расч=5223
Максимальный расчетный натяг мкм Nmax расч=24975
Характеристики расчетных посадок
Рекомендуемая посадка 12000 H8u8
Назначена посадка - 12000 H8u8
Аргументы в пользу выбранной посадки
Стабильность технологического режима не обеспечена.
Данные для разработки рабочих чертежей деталей
Основные технологические параметры
Вид сборки соединения - С предварительным нагревом
Температура нагрева град С - 172
Используемое оборудование - ТПЧ
Вид контроля качества сборки – по температуре нагрева
Предполагаемые технологические процессы обработки
охватываемой детали - шлифование
охватывающей детали - шлифование
Предполагаемые виды контроля точности обработки
охватываемой детали – активный контроль
охватывающей детали – активный контроль
Допуск формы (допуск круглости и допуск профиля продольного сечения) принят с учетом нормальной относительной геометрической точности за рекомендациями стандарта по 7 степени точности.
4Выбор переходной посадки с применением ЭВМ
Трудоемкость сборки и разборки соединений с переходными посадками равно как и характер этих посадок во многом определяется достоверностью получения в них натягов и зазоров. Для предварительно выбранной посадки определяются допуски отверстия и вала по формулам:
а также максимально возможный минимально возможный и средний натяги по формулам:
Определяется среднее квадратичное отклонение натяга (зазора) по формуле:
Определяется предел интеграции ровный (при Ni = 0):
Из таблиц по найденному значению z определяется функция Ф(z). Рассчитывается достоверность натяга (или процент натяга) и достоверность зазоров (или процент зазоров):
– процент натягов (процент соединений с натягом):
– достоверность зазоров
– процент зазоров (процент соединений с зазором):
Результаты расчетов с помощью ЭВМ представлены ниже.
Вимоги до вибраної посадки
- зручнiсть складання – розкладання
- нормальне центрування при більшiй iмовірностi натягу
Вывод: для соединения 53 назначается посадка 140 H7m6.
- нормальне центрування при приблизно рівних ймовірностях зазорів та натягів
Вывод: для соединения 223 назначается посадка 120 H7k6.
Посадки шпоночных шлицевых и резьбовых соединений
1Шпоночное соединение
С учетом конструктивно-технологических особенностей и служебного назначения сборочной единицы определяем вид шпоночного соединения - поз. 5213 и соответствующую ему посадку. Для обеспечения неподвижности соединения в узлах не требующих частых разборов в эксплуатации - нормальное соединение.
Для нормального соединения установлены поля допусков:
- поле допуска паза втулки:
- поле допуска паза вала – N9.
Принятые посадки указывают на рисунке предварительно определив номинальные размеры шпоночного соединения по ГОСТ 23360-78 в зависимости от 140 - диаметра вала который в свою очередь назначают из основных рядов нормальных линейных размеров.
Параметры шпоночного соединения:
Для шпоночного соединения позиция 5213 строим схему полей допусков:
Рисунок 4.1 – Схема расположения полей допусков шпоночного соединения - поз. 5213
2Шлицевое соединение
Исходя из конструктивно-технологических особенностей узла для определения оптимальной посадки прямобочного шлицевого соединения 84 назначим вид центрирования: центрирование по наружному диаметру (D). Т.к. втулка имеет невысокую твердость (260 285 HB) и ее можно обработать протяжкой а вал по наружному диаметру – на обычном круглошлифовальном станке.
Принятый способ центрирования обеспечивает высокую точность просто и экономично в изготовлении и обычно применяется для неподвижных соединений или в подвижных соединениях с небольшими нагрузками.
В соответствии с выбранным видом центрирования по таблицам ГОСТ 1139-80 определяют поля допусков центрирующих и нецентрирующих размеров вала и втулки на основании чего указывают посадки и допуски на рисунке предварительно установив номинальные размеры и число шлицев соединения по ГОСТ 1139-80:
Для шлицевого соединения 8×52×60×10 позиция которого 84 строим схему полей допусков:
Рисунок 4.2 – Схема расположения полей допусков шлицевого соединения - поз. 84
3Резьбовое соединение
Исходя из конструктивно-технологических соображений в резьбовом соединении 131 назначаем вид резьбы - метрическая с наружным диаметром 20 мм шаг резьбы крупный Р=2.5 мм.
По наружному диаметру d(D)=20 мм определяем параметры резьбы:
- средний диаметр =18376 мм;
- внутренний диаметр d1(D1)=17294 мм;
- высота профиля H1=1353 мм.
Назначаем поля допусков для наружного и внутреннего диаметров резьбы из таблиц ГОСТа 16093-81 взависимости от длины свинчивания и класса точности резьбы длина свинчивания – нормальная класс точности – средний:
Выбор и обоснование метода достижения точности сборки узла
При проектировании и изготовлении изделий одним из главных вопросов есть распределение и достижение точности установленных параметров качества при сборке. Такая задача решается при разработке чертежей и технологических процессов изготовления.
Основной целью является нахождение метода достижения точности который позволит иметь самые низкие расходы. Эта задача развязывается на основе размерных цепей.
Различают шесть видов сборки по методу достижения требуемой точности замыкающего звена:
- сборка с полной взаимозаменяемостью;
- сборка с неполной взаимозаменяемостью;
- сборка с групповой взаимозаменяемостью;
- сборка с пригонкой;
- сборка с регулированием;
- сборка с компенсирующими материалами.
При составлении данного узла необходимо обеспечить зазор между торцами крышки 33 и подшипником 20 который необходим для компенсации температурных деформаций и погрешностей при изготовлении. Проанализируем возможность обеспечения зазора = 01– 08 мм (p не больше 05%) между торцами подшипника и крышки методами полной и неполной взаимозаменяемости. Метод полной взаимозаменяемости (max min) целесообразно применять для расчета если в дальнейшем будет выбран квалитет 8 или 9 в противном случае расчёт методом max min вести нецелесообразно экономично и нужно решать размерную цепь вероятностным методом.
- номинальный размер замыкающего звена
- предельные отклонения замыкающего звена =+800 мкм; =+100 мкм;
- допуск замыкающего звена =800 - 100=700 мкм;
- среднее отклонение замыкающего звена = = +045 мм.
Выявляем схему размерной цепи определяющую точность этого зазора. Схема размерной цепи имеет следующий вид:
Рисунок 5.1 - Схема размерной цепи
Как видно из сборочного чертежа в размерную цепь входят следующие размеры деталей:
А1 = мм (ширина кольца подшипника);
А2 = 500 мм (ширина вала);
А3 = мм (ширина кольца подшипника);
А4 = 10 мм (ширина выступа крышки);
А5 = 610 мм (ширина корпуса);
А6 = 10 мм (ширина выступа крышки);
Где A5 - увеличивающее звено (1);
A1 A2 A3 A4 A6 - уменьшающие звенья (1);
Проверим замкнутость размерной цепи:
- передаточное отношение j-ого элемента размерной цепи
- номинальный размер звена j-ого элемента размерной цепи.
Для обеспечения равенства назначаем А5 = 594 мм. Расчёт будем вести вместо 610:
Находим среднее число единиц допуска:
ij – единица допуска j-ого звена
- допуск замыкающего звена
- допуск на номинальный раз мер j-ого подшипника.
Назначаем допуски по 8-му квалитету для которого
Расчетное значение допуска замыкающего звена в этом случае:
Назначаем поля допусков для составляющих звеньев:
для звеньев А6 и А4 – назначаем симметричное поле допуска;
для звеньев А5 и А2 – назначаем поле допуска от 0 в «-» как для основного вала.
Назначаем предельные отклонения составных звеньев предварительно определив расположение полей допусков составных звеньев:
Для обеспечения равенства принимаем
Для звена определяем предельные отклонения:
Проверка: = = ()=97 мкм.
Для обеспечения точности замыкающего звена на чертеже необходимо проследить простановку следующих размеров:
Выбор расчет и обоснование средств и методов контроля точности деталей
1Выбор и обоснование средств измерения зубчатых колес
Для каждой степени точности зубчатых колес и передач устанавливаются нормы кинематической точности плавности работы контакта зубьев а также гарантированного бокового зазора который не зависит от степени точности.
Определим геометрические параметры зубчатого колеса (поз. 6).
Межосевое расстояние: =315 мм.
Передаточное отношение по чертежу:
Ориентировочный угол наклона зуба =30°.
Для шевронной передачи
Уточняем угол наклона зуба
= = 302890° = 30°16'54''.
Находим число зубьев на колесе
Определяем делительные диаметры для колес:
Уточняем межосевое расстояние:
Геометрические параметры зубчатых колес приведены в таблице 6.1.1.
Определим степень точности по кинематической точности плавности работы и контакта зубьев. При заданной скорости V = 15 мс выбираем 6 степень точности по плавности работы. Передача в силовой и высокой кинематической точности не нуждаются назначаем точность на единицу степени грубее нормы плавности – 7 а норма контакта зубьев имеет такую же степень точности что и норма плавности работы – 6.
Вид сопряжения определяем по значению бокового зазора который рассчитываем по формуле:
α1 – коэффициент линейного расширения стали α1 = 115·10-6 с-1;
α2 – коэффициент линейного расширения чугуна α2 = 105·10-6 с-1.
Δt1 Δt2 – отклонение температур колеса и корпуса от +20°С Δt1 = 50°С Δt2 = 20°С;
α = 20° – угол профиля исходного контуру колес передачи.
Принимая коэффициент перед mn равным 20 (считаем передачу среднескоростной) получим а также:
С учетом межосевого расстояния и значения назначаем вид сопряжения – A для которого при заданном межосевом расстоянии гарантированный зазор равняется 320 мкм.
Обозначение зубчатого колеса: 7-6-6-А ГОСТ 1643-81.
Предельное отклонение межосевого расстояния: far=[10 табл. Б.7]
Для данных степеней точности назначаем показатели которые нормируются за данным степенем точности. За ним происходит контроль зубчатого колеса.
Кинематическая норма точности за 7 степенью точности:
= 112 мкм (колебание измерительного межосевого расстояния за оборот колеса) [10 табл. Б.1];
= 60 мкм (колебание длины общей нормали).
Норма плавности работы - по 6 степени точности:
= 17 мкм (отклонение шага зацепления) [10 табл. Б.3];
= 16 мкм (погрешность профиля зуба).
Норма контакта зубьев - по 6 степени точности:
Ширина зубчатого венца В=100 мм.
= 12 мкм (погрешность направления зуба) [10 табл. Б.5].
Норма бокового зазора - по 6 степени точности:
= 400 мкм (наименьшее дополнительное смещение исходного контура) [10 табл. Б.8];
= 250 мкм (допуск на смещение исходного контура) [10 табл. Б.9].
Для данных показателей нормируемых в комплексе выбираем измерительные средства и заносим в таблицу 6.1.2.
Прибор для измерения
Допускаемая погрешность
Шагомер полуавтоматический переносной ТУ 2-022-1197-011-84
Для контроля крупногабаритных зубчатих колёс по
ГОСТ 5368-81 ТУ 2-034-542-80
Зубомер смещения по ГОСТ 4446-81
Определим диаметры выступов для колеса:
где - коэффициент высоты головки зуба для стандартного исходного контура - коэффициент смещения исходного контура для колес без смещения .
Определим отклонение диаметра вершин зубьев внешнего цилиндра заготовки и допуск на радиальное биение (внешний цилиндр используется в качестве базы при контроле размера зубьев):
За таблицей допусков устанавливаем что ближайший допуск (110 мкм) относится до 8 квалитетa. Устанавливаем отклонение диаметра .
Определим данные для контроля зубчатого колеса:
Постоянная хорда [13 табл.9 стр. 406]
Высота постоянной хорды [13 табл.9]
Определим предельные отклонения постоянной хорды и наименьшее отклонение толщины зуба:
(наименьшее отклонение толщины зуба для зубчатых колес с внешними зубьями) [10 табл. Б14].
Допуск на толщину зуба:
Нижнее отклонение постоянной хорды определяем как:
Таким образом в таблицу чертежа зубчатого колеса должно быть занесено для постоянной хорды:
Определим допуск на торцевое биение базового торца:
мм где мм [10 табл. Б16].
Рассчитаем величину максимального гарантированного бокового зазора:
2 Выбор и обоснование универсальных средств измерения для контроля точности и шероховатости вала
Для детали вал (поз. 4) выбираем измерительные средства необходимые для контроля всех линейных и узловых размеров и шероховатостей поверхностей.
Для контроля шероховатости подшипниковых шеек выполняемых по 6 квалитету принимаем профилометр (ГОСТ 19300-73) типа AII модели 296 для контроля шероховатости остальных поверхностей вала применяем образцы сравнения параметров шероховатости.
Возможность применения того или иного измерительного прибора определяется суммарной погрешностью с помощью этого прибора включаются все составляющие самого прибора установочных мер базирования температурных погрешностей и т.д.
Сведения о выбранных средствах измерения приведены в таблице 6.2.1.
Таблица 6.2.1 - Измерительные средства
Допускаемая погрешность измерения
Диапазон измерениймм
Осн. погрешн. изм. средстваПогрешность измерения мм
Микрометр гладкий ГОСТ 6507-78
(класс точности m по ДСТУ 2768 -1 -2001)
Индикаторы многооборотные
Шероховатость поверхности
Набор образцов шероховатости ГОСТ 9378-93
Проилометр цеховый переносной
Определив межосевое расстояния и значения назначив вид сопряжения – A для которого при заданном межосевом расстоянии гарантированный зазор равняется 320 мкм.
Получаем степень точности: 7-6-6-А ГОСТ 1643-81.
Определим диаметры выступов для вала-шестерни:
За таблицей допусков устанавливаем что ближайший допуск (100 мкм) относится до 9 квалитетa. Устанавливаем отклонение диаметра .
Определим данные для контроля вала-шестерни:
Таким образом в таблицу чертежа вала-шестерни должно быть занесено для постоянной хорды:
Измерение отклонений от круглости
Отклонение от круглости наиболее полно контролируется на специальных приборах - кругломерах на которых реальный профиль сравнивается с траекторией точного вращения осуществляемого шпинделем прибора.
Приближенно отклонение от круглости может быть измерено двухконтактным или трехконтактным способами.
Двухконтактный способ позволяет выявить овальность и огранку с четным числом граней. При измерении по этому способу отклонение от круглости будет равно половине разности между наибольшим и наименьшим диаметрами поперечного сечения которые определяет при поворачивании детали I между измерительное головкой 3 и узкой опорой 2 установленной на поверочной плите 5 (рис. 6.2.1 а). Для удобства и в этом случае рекомендуется пользоваться боковым упором 4.
Если характер отклонения от круглости соответствует огранке с нечетным числом граней применяют трехконтактный способ. Для этого можно использовать базирование на призмах (рис. 6.2.1 б). В этом случае показания прибора делят на поправочный коэффициент (приводится в таблицах) который зависит от числа граней огранки и угла призмы.
Так как не при всяком угле призмы α можно выявить огранку с любым числом граней а число граней заранее как правило неизвестно то обычно производят измерения на призмах с различными углами α например 60° 90° 120° и др.
Рис. 6.2.1 – Измерение отклонений от круглости
Обоснование допусков и технических требований к изготовлению деталей
Допуск на круглость и профиль продольного сечения посадочных поверхностей подшипников 75 выбираем по ГОСТ 3325-85 в зависимости от класса точности подшипников и номинального диаметра = 0005 мм.
Допуск на соосность посадочных поверхностей вала относительно общей оси поверхностей в диаметральном выражении по ГОСТ 3325-85 [5 стр. 359]
мкм (принимаем 16 мкм)
где В - ширина подшипника В=37 мм.
Допуск непостоянства диаметра шеек 75 k6 в продольном и поперечном сечении не более 0016 мм.
Допуск торцевого биения заплечиков вала о подшипник = 0030 мм в зависимости от степени точности подшипников [6 стр. 27].
Шероховатость посадочной поверхности под подшипники Rа=125 мкм [6 стр. 29];
Шероховатость опорных торцов заплечиков вала и подшипников Rа=250 мкм [6 стр. 29];
Шероховатость шлицов Rа=32мкм [11 стр. 525].
Для зубчатого колеса (поз. 6)
Допуск параллельности шпоночного паза [5 стр. 363]
Допуск симметричности шпоночного паза =[5 стр. 363]
Отклонение диаметра вершин зубьев внешнего цилиндра заготовки и допуск на радиальное биение:
Допуск на торцевое биение базового торца:
Шероховатость поверхностей колеса назначаем по таблице 2.68 [11 стр. 525]. Шероховатость рабочей поверхности зубьев в зависимости от степени точности по ГОСТ 1643-81.
В ходе выполнения курсовой работы составлены и обоснованы технические требования которые предъявляются к точности изготовления основных деталей и соединений цилиндрического редуктора с учетом его служебного назначения. Выполнены расчеты размерных цепей и назначены посадки с натягом.
Определен комплекс измерительных средств для контроля деталей в
Разработаны сборочные чертежи узла рабочие чертежи вала и зубчатого колеса (листы I и 2 графической части работы).
Технические требования назначены в соответствии с учётом мировых тенденций повышения качества и конкурентоспособности изделий. Для этого из рекомендуемых в справочной литературе пределов точности выбирались нижние значения значительное внимание уделено дифференциации степеней точности зубчатой передачи (по нормам кинематической точности плавности и контакту зубьев) выбор контрольно-измерительных средств осуществлён с учетом влияния их погрешностей на результаты контроля.
В целях совершенствования работы считаем целесообразным при назначении технических требований к точности вала вместо рекомендуемых литературой допусков цилиндричности шеек под зубчатые колёса назначать допуски круглости и профиля продольного сечения (по аналогии с подшипниковыми шейками). Это позволит унифицировать и упростить контроль при изготовлении вала.
Результаты работы будут использованы при курсовом и дипломном проектировании.
Методические указания к выполнению раздела курсовой работы «Расчёт посадок с натягом с испоьзованием ЭВМ» по дисциплине «Взаимозаменяемость стандартизация и технические измерения» (для студентов всех специальностей) Сост. В.М. Кислов Л.П. Субботина. – Краматорск: КИИ 1988. - 24 с.
Методические указания к курсовой работе «Выбор и обоснование точностных параметров и соединений изделия» по дисциплине «ВМС и управление качеством»Сост. А.П. Мартынов. – Краматорск: КИИ 1991. – 31с.
Допуски и посадки: Справочник В24ВД Минов М.А. А.Б.Романов. – М. Машиностроение - 1982.
Допуски и посадки: Обоснование выбора Д83П.Ф. Дунаев О.П. Леликов – М.1984-Высшая школа - 112с.
Конструирование узлов и деталей машин П.Ф. Дунаев О.П. Леликов. Высшая школа. 2001 - 447с.
Методические указания по курсовому и дипломному проектированию. Раздел «Выбор и обозначение посадок подшипников качения и технических требований к сопрягаемым поверхностям».Сост. А.П.Мартынов. – Краматорск: КИИ 1990. – 32с.
Методические указания к курсовому и дипломному проектированию «Расчеты размерных цепей для обеспечения точности изготовления и сборки по методам полной и неполной взаимозаменяемости». Сост. А.П.Мартынов. – Краматорск: ДГМА 2000. – 45с.
Методические указания к курсовому и дипломному проектированию «Допускаемые погрешности измерения и выбор универсальных измерительных средств». Сост. А.П.Мартынов.- Краматорск : ККИ 1993.- 13с.
Выбор и обоснование допускаемых отклонений геометрических поверхностей деталей при проектировании изделий Методическое пособие к курсовому проектированию (для студентов всех специальностей направления «Инженерная механика»).Сост. Мартынов А.П. – Краматорск: ДГМА 2001. – 132 с.
Методические указания к курсовому и дипломному проектированию (для студентов всех специальностей). «Выбор точности средств контроля и оформление чертежей зубчатых колес и валов-шестерен» Сост.: А.П. Мартынов Л.Н. Абрамова. – Краматорск: ДГМА 2005. – 100с.
Допуски и посадки: Справочник. В 2 чВ.Д.Мягков М.А.Палей А.Б.Романов. – Г.:Машиностроение1982.-ч.1-543с.
Допуски и посадки: Справочник. В 2 ч.В.Д.Мягков М.А.Палей А.Б.Романов. – Г.:Машиностроение1983.-ч.2-448с.
rrr.dwg

Нормальный исходный контур
Коэффициент смещения
Степень точности по ГОСТ 1643-81
Высота до постоянной хорды
Допуск непостоянства диаметров шеек
дольном и поперечном сечениях 0
Сталь 45 ГОСТ 1050-88
rrrrsr.dwg

Нормальный исходный контур
Коэффициент смещения
Степень точности по ГОСТ 1643-81
Высота до постоянной хорды
Штамповочные уклоны 5 7
Сталь 45 ГОСТ 1050-88
rerress.dwg

rrrsreryirrerye.dwg

reryirrryer.dwg

r-rrsryesrs-rrr.dwg

Внутреннюю поверхность покрыть грунтом
ОЛ-03К-коричневый ГОСТ 9100-80
наружную поверхность
красить эмалью ХВ-124 серый ГОСТ 1044-89
Сборка узлов подшипников качения по ГОСТ 3325-85
В собранном редукторе валы должны проворачиваться
Боковой зазор в зацеплении зубьев
по степени точности 7-6-6-А ГОСТ 1643-81
В редуктор заливать масло индустриальное
И-20-А ГОСТ 20799-88
Плоскость разъёма при сборке уплотнить
После сборки произвести обкатку и испытание редуктора
под рабочей нагрузкой.
Редуктор цилиндрический
Рекомендуемые чертежи
- 17.04.2018