Привод ленточного конвейера




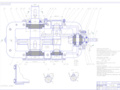
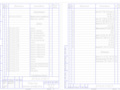
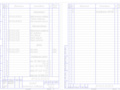
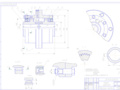
- Добавлен: 25.10.2022
- Размер: 1 MB
- Закачек: 1
Описание
Состав проекта
![]() |
![]() |
![]() ![]() |
![]() ![]() |
![]() ![]() |
![]() ![]() |
![]() ![]() |
![]() ![]() |
![]() ![]() |
![]() ![]() |
![]() ![]() |
![]() ![]() |
![]() ![]() |
![]() |
![]() ![]() ![]() ![]() |
![]() ![]() ![]() ![]() |
![]() ![]() ![]() ![]() |
![]() |
![]() ![]() ![]() ![]() |
![]() ![]() ![]() ![]() |
![]() ![]() ![]() ![]() |
![]() ![]() ![]() ![]() |
![]() ![]() ![]() ![]() |
![]() ![]() ![]() ![]() |
![]() ![]() ![]() ![]() |
![]() ![]() ![]() ![]() |
![]() ![]() ![]() |
Дополнительная информация
приводной вал.dwg

Обоб - лист толщиной 8мм по ГОСТ 5681-57
Диски - лист толщиной 6мм по ГОСТ 103-57
На виде А вал и подшипник условно не показаны.
Подшипниковые камеры при окончательной сборке
заполнить пластичной смазкой УТ-1
сверлить и развернуть
совместно с основанием
муфта.dwg

Допускаемые смещения
Залить масло ИТП-300 ТУ 38.101292-78
Спецификация муфта.dwg

Винт ГОСТ 11738-84 М6-8g
Гайка ГОСТ 15521-70 М8
Манжета ГОСТ 8752-79 1.1.-70
ШайбаГОСТ 6402-70 10
дмкурсовой.dwg

ТЕХНИЧЕСКАЯ ХАРАКТЕРИСТИКА:
Общее передаточное число
Номинальный вращающий момент на выходном валу Т=725
Число оборотов быстроходного вала
Число оборотов тихоходного вала
Коэффициент полезного действия
ХАРАКТЕРИСТИКА ЗАЦЕПЛЕНИЯ:
Число зубьев шестерни
Ширина шестерен расчетная
Степень точности 7-С
ТЕХНИЧЕСКИЕ ТРЕБОВАНИЯ:
Плоскость разъема покрыть герметиком при окончательной
сборке ГОСТ 10584-75
Необработанные поверхности красить внутри редуктора
маслостойкой краской ГОСТ 10144-75
снаружи серой нитроэмалью ГОСТ 10354-75
В редуктор залить масло индустриальное И-Г-А-32 ГОСТ 1707-90
После сборки валы редукторов должны поворачиваться свободно
без стуков и заедания
Спецификация приводной вал.dwg

Болт ГОСТ 7796-70 М10-6gx65
Гайка ГОСТ 15521-70 М10
Манжета ГОСТ 8752-791.1.-70х92-2
Подшипник ГОСТ 28428-90 1212
Шайба ГОСТ 6402-70 10
Штифт ГОСТ 3128-70 2.6x24
колесо.dwg

Радиусы скруглений 1
Общие допуски по ГОСТ 30893
Направление линии зуба
Коэффициент смещения
Спецификация 1 алена.dwg

Редуктор коническо-цилиндрический
Кольцо маслоотрожательное
Прокладка уплотительная
Болт ГОСТ 17796-70 М14-8g
Винт ГОСТ 11738-84 М14-8g
Гайка ГОСТ 11871-88 М27х1
Манжета ГОСТ 8752-79 1.1.-22
Подшипник конический ГОСТ 27365-87 7307А
Шайба Н.27.01.05 ГОСТ 11872-89
Шпонка ГОСТ 23360-78 14
ШтифтГОСТ 3129-70 2.10
Масло И-Г-А-32 ГОСТ 1707-09
Маслостойкая краска ГОСТ 10144-75
Нитроэмаль ГОСТ 10354-75
курсач 2 лист.dwg

вал.dwg

* Размер обеспеч. инстр.
Общие допуски по ГОСТ 30893.2 - mK
общий вид перв.dwg

под фундаментные болты
Осевое смещение валов элекродвмгателя и редуктора
Радиальное смещение валов электродвигателя и редуктора
Перекос валов элетродвигателя и редуктора
Техническая характеристика
Окружное усилие на барабане 3150Н
Частота вращения приводного вала 48 мин
Привод: электродвигатель АИР112МВ6
редуктор коническо-цилиндрический U=19
Осевое смещение валов редуктора и вала приводного
Радиальное смещение валов редуктора и вала приводного
Перекос валов редуктора и вала приводного
Позиция 3 не показана
Спецификация привод.dwg

Привод ленточного конвейера
Пояснительная записка
Редуктор коническо-цилиндрический
Болт ГОСТ 15589-70 М16 х 70
Гайка ГОСТ 15526-70 М16
Шайба ГОСТ 6402-70 16 Н
Шайба косая ГОСТ10906-78 16
Электродвигфтель АИР112МВ6
записка.doc
и ордена Трудового Красного Знамени
Государственный Технический Университет имени Н. Э. Баумана
Кафедра «Детали машин»
Расчётно-пояснительная записка
к курсовому проекту на тему:
Проектирование привода ленточного конвейера
Студент: Феденкова А.Ю.
Руководитель проекта: Витушкина Е.А.
ТЕХНИЧЕСКОЕ ЗАДАНИЕ . . . . . . . . . . . . . . . . . . . . . . . . . . . . . . . . . . . . . . . . . . . . . . . . . . . . . . . . . . . . . . . . . .3
КИНЕМАТИЧЕСКАЯ СХЕМА ПРИВОДА ЛЕНТОЧНОГО КОНВЕЙЕРА . . . . . . . . . . . . . . . . . . . . 3
ВЫБОР ЭЛЕКТРОДВИГАТЕЛЯ . . . . . . . . . . . . . . . . . . . . . . . . . . . . . . . . . . . . . . . . . . . . . . . . . . . . . . . . . . . . . .4
ОПРЕДЕЛЕНИЕ ОБЩЕГО ПЕРЕДАТОЧНОГО ЧИСЛА И РАЗБИВКА ЕГО ПО СТУПЕНЯМ . . . . . .5
ОПРЕДЕЛЕНИЕ МОЩНОСТИ КРУТЯЩЕГО МОМЕНТА И ЧАСТОТЫ ВРАЩЕНИЯ КАЖДОГО ВАЛА ПРИВОДА . . . . . . . . . . . . . . . . . . . . . . . . . . . . . . . . . . . . . . . . . . . . . . . . . . . . . . . . . . . . . . . . . . . . . . . . . . . .6
ПРОЕКТНЫЙ И ПРОВЕРОЧНЫЙ РАСЧЁТ ЗУБЧАТЫХ ПЕРЕДАЧ . . . . . . . . . . . . . . . . . . . . . . . . . . . . .8
ОПРЕДЕЛЕНИЕ ДИАМЕТРОВ ВАЛОВ . . . . . . . . . . . . . . . . . . . . . . . . . . . . . . . . . . . . . . . . . . . . . . . . . . . . . . 18
ВЫБОР И ПРОВЕРКА ПОДШИПНИКОВ КАЧЕНИЯ ПО ДИНАМИЧЕСКОЙ ГРУЗОПОДЪЁМНОСТИ . . . . . . . . . . . . . . . . . . . . . . . . . . . . . . . . . . . . . . . . . . . . . . . . . . . . . . . . . . . . . . . . . . . .20
ПРОВЕРОЧНЫЙ РАСЧЁТ НАИБОЛЕЕ НАГРУЖЕННОГО ВАЛА НА УСТАЛОСТНУЮ ПРОЧНОСТЬ И ЖЁСТКОСТЬ . . . . . . . . . . . . . . . . . . . . . . . . . . . . . . . . . . . . . . . . . . . . . . . . . . . . . . . . . . . . . . 23
ВЫБОР И РАСЧЁТ ШПОНОЧНЫХ И ШЛИЦЕВЫХ СОЕДИНЕНИЙ . . . . . . . . . . . . . . . . . . . . . . . . . . .26
СМАЗКА ЗУБЧАТЫХ ЗАЦЕПЛЕНИЙ И ПОДШИПНИКОВ . . . . . . . . . . . . . . . . . . . . . . . . . . . . . . . . . . . .28
СБОРКА ПРИВОДА . . . . . . . . . . . . . . . . . . . . . . . . . . . . . . . . . . . . . . . . . . . . . . . . . . . . . . . . . . . . . . . . . . . . . . . . 29
СПИСОК ИСПОЛЬЗОВАННОЙ ЛИТЕРАТУРЫ . . . . . . . . . . . . . . . . . . . . . . . . . . . . . . . . . . . . . . . . . . . . . . 30
Выбор электродвигателя
Для выбора электродвигателя определим мощность на приводном
валу и число оборотов необходимое ему:
Требуемая мощность электродвигателя:
Предварительная частота вращения выходного вала редуктора:
Требуемая частота вращения вала электродвигателя:
где – окружное усилие на барабане; – скорость ленты барабана;
Принимаем электродвигатель АИР112МВ6 мощностью с
Определение общего передаточного числа и разбивка его по ступеням
Общее передаточное число привода где – передаточное число редуктора и – частота вращения вала электродвигателя и приводного вала соответственно и – передаточные числа быстроходной и тихоходной ступеней редуктора.
По таблице 2.2 методички 1 определяем что .
Определение мощности крутящего момента и частоты вращения каждого вала привода
Определим мощности: ;
где – мощность на валах двигателя редуктора и приводного вала.
Определим частоту вращения: ;
где вала – передаточное число быстроходной и тихоходной ступеней редуктора соответственно.
Определим крутящие моменты: ;
где – крутящие моменты на валах двигателя редуктора и приводного вала.
Результаты расчётов занесём в таблицу 1.
Проектный и проверочный расчёт зубчатых передач
I. Расчёт тихоходной ступени редуктора.
Материал колеса – сталь 40Х а шестерни – 40ХН. Таким образом учитывая что термообработка зубчатых колёс колеса – улучшение а шестерни – закалка ТВЧ по таблице 3.1 методички1 имеем:
где – твёрдость рабочей поверхности зубьев и – предел прочности материала на растяжение и предел текучести материала.
Определим коэффициенты приведения на контактную выносливость и на изгибную выносливость по таблице 4.1 мет.1 учитывая режим работы II: ; .
Определим число циклов перемены напряжений. Числа циклов перемены напряжений соответствуют длительному пределу выносливости. По графику 4.3 мет. 1 определяем числа циклов на контактную и изгибную выносливость соответственно: .
Определим суммарное число циклов перемены напряжений для шестерни и колеса соответственно: где –ресурс передачи; – частота вращения колеса; и – число вхождений в зацепление зубьев шестерни и колеса соответственно за один его оборот; - передаточное число тихоходной ступени.
Получим эквивалентное число циклов перемены напряжений для расчёта на контактную выносливость: где – коэффициенты приведения на контактную выносливость; – суммарное число циклов перемены напряжений для шестерни или колеса.
Так как то принимаем и то принимаем.
Найдём эквивалентное число циклов перемены напряжений для расчёта на изгибную выносливость: где – коэффициенты приведения на изгибную выносливость; – суммарное число циклов перемены напряжений для шестерни или колеса.
Так как то принимаем и то принимаем .
Определим допускаемые напряжения для расчётов на прочность при действии пиковых нагрузок. По таблице 4.3 мет. 1 находим что
контактная прочность:
Определим напряжения для расчета на контактную выносливость:
где и - коэффициенты безопасности
– предел текучести материала колеса или шестерни;
Определим допускаемые напряжения для расчета на изгибную выносливость:
где и – длительный предел контактной выносливости и коэффициент безопасности; и – длительный предел изгибной выносливости и коэффициент безопасности.
Определим коэффициенты нагрузки на контактную и изгибную выносливость по формулам: и где и – коэффициенты концентрации нагрузки по ширине зубчатого венца; и – коэффициенты динамической нагрузки (учитывают внутреннюю динамику передачи).
Относительная ширина шестерни находится по формуле здесь – коэффициент ширины шестерни определяется по таблице 6.1 мет. 1; – передаточное число данной ступени редуктора. где значение ( и соответственно) выбираем по таблицам 5.2 и 5.3 мет. 1: ; – коэффициент режима учитывающий влияние режима работы передачи на приработку зубчатых колёс находим по таблице 5.1 мет. 1.
. Значения определяются по табл.5.6 и 5.7 мет. 1 по известной окружной скорости: где – частота вращения быстроходного вала – крутящий момент на тихоходном валу – передаточное число данной ступени редуктора коэффициент определяется по табл. 5.4 мет. 1 в зависимости от вида передачи . Находим что и . Теперь находим значения коэффициентов нагрузки и .
Определим предварительное значение межосевого расстояния: где – передаточное число данной ступени редуктора; – допускаемое контактное напряжение; – коэффициент учитывающий распределение нагрузки между зубьями определяем по рис. 6.2 метт. 1; – крутящий момент на валу зубчатого колеса; – коэффициент ширины зубчатых колёс передачи.
Из стандартного ряда выбираем по ГОСТ 6636–69 ближайшее стандартное значение межосевого расстояния .
Определяем рабочую ширину колеса: . Ширина шестерни: .
Вычислим модуль передачи по формуле где – изгибное напряжение на колесе; .
Тогда . Из стандартного ряда значений по ГОСТ 9563–60 выбираем значение .
Определим минимально возможный угол наклона зуба .
Рассчитываем предварительное суммарное число зубьев: . Округляем это число в меньшую сторону и получаем .
Определяем действительное значение угла и сравниваем его с минимальным значением: .
Найдём число зубьев шестерни и колеса ; .
Найдём фактическое передаточное число передачи: .
Проверим зубья колёс на изгибную выносливость. Для колеса получим:
где – крутящий момент на валу колеса; – коэффициент нагрузки при расчёте на изгибную выносливость; – коэффициент учитывающий распределение нагрузки между зубьями выбираем по табл.6.4 мет.1; – коэффициент учитывающий форму зуба находится по табл.6.2 мет.1; – коэффициент учитывающий наклон зуба. Сравниваем полученное значение напряжения с допускаемым напряжением при расчёте на изгиб зубьев колеса: т.е. не выполняется условие.
т.е. выполняется условие.
Для шестерни: где и – коэффициенты учитывающие форму зуба определяются по табл. 6.2 мет. 1. Сравним полученное значение напряжения с допускаемым напряжением при расчёте на изгиб зубьев шестерни: но не превышает 10%.
Определим диаметры делительных окружностей шестерни и колеса соответственно:
где – модуль зубчатых колёс; – угол наклона зуба; – число зубьев шестерни или колеса.
Проверим что ; – верное равенство.
Вычислим диаметры окружностей вершин зубьев и впадин зубьев ;
Определим силы действующие на валы зубчатых колёс.
Окружную силу находим по формуле: где – крутящий момент на валу колеса; – диаметр делительной окружности колеса.
Радиальная сила: где – угол зацепления; – угол наклона зуба.
II. Расчёт быстроходной ступени редуктора.
Материал колеса и шестерни – сталь 40Х. Таким образом учитывая что термообработка зубчатых колёс – улучшение по таблице 3.1 мет.1 имеем:
Определим среднюю твёрдость зубьев шестерни и колеса: .
Ресурс передачи т.е. суммарное время работы: .
Определим суммарное число циклов перемены напряжений для шестерни и колеса соответственно: где –ресурс передачи; и – частота вращения шестерни и колеса соответственно; и – число вхождений в зацепление зубьев шестерни или колеса соответственно за один его оборот.
Так как то принимаем и то
Так как и то принимаем .
Найдём предельные допускаемые контактные и изгибные напряжения:
где – предел текучести материала колеса или шестерни; – средняя твёрдость зубьев шестерни или колеса.
Определим допускаемые контактные напряжения и напряжения изгиба при неограниченном ресурсе передачи:
Проверим передачу на контактную выносливость и изгибную выносливость: .
Коэффициенты нагрузки:
Коэффициенты нагрузки находят из выражения:
при расчете на контактную выносливость: ;
при расчете на изгибную выносливость: где
зубчатого венца; - коэффициенты динамической нагрузки.
Относительная ширина шестерни:
где значения выбирают по таблице 5.2 и 5.3 мет 1
где х – коэффициент режима учитывающий влияние режима работы передачи на приработку зубчатых колес.
Окружная скорость: где выбирают из табл.5.4 мет 1.
По табл. 5.6 и 5.7 мет.1 выбираем значения коэффициентов
Проектный расчет закрытой конической передачи:
Предварительное значение диаметра внешней делительной окружности колеса из мет. 1:
где номинальный крутящий момент на валу колеса; - заданное передаточное число; - допускаемое напряжение; - коэффициент нагрузки; - коэффициент выбирают из таблицы 7.1 мет. 1
Предварительное значение диаметра внешней делительной окружности шестерни (мет.1):
Число зубьев шестерни определяют по графику 7.2 мет. 1:
Число зубьев колеса:
Окончательное значение передаточного числа:
Углы делительных конусов:
Внешний окружной модуль:
Внешнее конусное расстояние:
Ширина зубчатых венцов колес:
Значение коэффициента смещения инструмента для шестерни находят по 8815числа зубчатой пары:
Коэффициент смещения для колес:
Проверка зубьев колеса на изгибную прочность:
Расчетное напряжение в опасном сечении зуба колеса:
где коэффициент выбирают по таб. 7.1 мет. 1: ; коэффициент учитывающий форму зуба колеса выбирают по табл.6.2 мет. 1;
Окончательное значение диаметра внешней делительной окружности шестерни:
Внешние диаметры вершин зубьев:
Средний нормальный модуль:
Проверка возможности получения требуемых механических характеристик материала при термической обработке заготовок зубчатых колес:
Силы действующие на валы зубчатых колес:
Окружная сила на среднем диаметре:
Коэффициент осевого усилия:
Коэффициент радиального усилия:
Осевая сила на шестерне:
Радиальная сила на шестерне:
Осевая сила на колесе:
Радиальная сила на колесе:
Определение диаметров валов
Диаметр быстроходного вала шестерни: Принимаем . Для найденного диаметра вала выбираем значения: – приблизительная высота буртика – максимальный радиус фаски подшипника – размер фасок вала. Определим диаметр посадочной поверхности подшипника: . Так как стандартные подшипники имеют посадочный диаметр кратный -ти то принимаем . Рассчитаем диаметр буртика для упора подшипника: . Пусть .
Определим диаметр промежуточного вала: где – момент на промежуточном валу. Принимаем . Для найденного диаметра вала выбираем значения: – приблизительная высота буртика – максимальный радиус фаски подшипника – размер фасок вала. Определим диаметр посадочной поверхности подшипника: . Так как стандартные подшипники имеют посадочный диаметр кратный -ти то принимаем . Диаметр буртика колеса . Принимаем . Рассчитаем диаметр буртика для упора подшипника: . Пусть .
Определим диаметр тихоходного вала: где – момент на тихоходном валу. Принимаем . Для найденного диаметра вала выбираем значения: – приблизительная высота буртика – максимальный радиус фаски подшипника – размер фасок вала. Определим диаметр посадочной поверхности подшипника: . Так как стандартные подшипники имеют посадочный диаметр кратный -ти то принимаем . Расчитаем диаметр буртика для упора подшипника: . Пусть .
Диаметр приводного вала нагружен моментом и его диаметр можно взять таким же как и у тихоходного вала: . Посадочный диаметр внутреннего кольца подшипника можно принять а посадочный диаметр барабана .
Выбор и проверка подшипников качения по динамической грузоподъёмности
I. Для быстроходного вала редуктора выберем роликовые конические однорядные средней серии серии . Для него имеем: – диаметр внутреннего кольца – диаметр наружного кольца – ширина подшипника – динамическая грузоподъёмность – статическая грузоподъёмность – предельная частота вращения при пластичной смазке. На подшипник действуют: – осевая сила – радиальная сила. Частота оборотов . Требуемый ресурс работы .
Найдём: – коэффициент безопасности (табл.1 мет.2); – температурный коэффициент (стр. 12 мет. 2); – коэффициент вращения (стр. 10 мет. 2).
Определяем эквивалентную нагрузку . По табл.3 мет.2 находим коэффициент осевого нагружения . Проверим условие что : . По табл. 3 мет. 2 определяем значение коэффициента радиальной динамической нагрузки и коэффициента осевой динамической нагрузки .
Определяем эквивалентную радиальную динамическую нагрузку .
Рассчитаем ресурс принятого подшипника: или что удовлетворяет требованиям.
II. Для промежуточного вала редуктора выберем роликовые конические однорядные средней серии . Для него имеем: – диаметр внутреннего кольца – диаметр наружного кольца – ширина подшипника – динамическая грузоподъёмность – статическая грузоподъёмность – предельная частота вращения при пластичной смазке. На подшипник действуют: – осевая сила – радиальная сила. Частота оборотов . Требуемый ресурс работы .
Найдём: – коэффициент безопасности (табл.1 лит.2); – температурный коэффициент (стр. 12 лит. 2); – коэффициент вращения (стр. 10 лит. 2).
Определяем эквивалентную нагрузку . По табл.3 лит.2 находим коэффициент осевого нагружения . Проверим условие что : . По табл. 3 лит. 2 определяем значение коэффициента радиальной динамической нагрузки и коэффициента осевой динамической нагрузки .
III. Для тихоходного вала редуктора выберем радиальные однорядные шарикоподшипники лёгкой серии . Для него имеем: – диаметр внутреннего кольца – диаметр наружного кольца – ширина подшипника – динамическая грузоподъёмность – статическая грузоподъёмность – предельная частота вращения при пластичной смазке. На подшипник действуют: – осевая сила – радиальная сила. Частота оборотов . Требуемый ресурс работы .
IV. Для приводного вала редуктора возьмём шарикоподшипники радиальные двухрядные сферические . Для него имеем – диаметр внутреннего кольца подшипника – диаметр наружного кольца подшипника – ширина подшипника – номинальный угол контакта подшипников – динамическая грузоподъёмность – статическая грузоподъёмность.
Проверочный расчёт наиболее нагруженного вала на усталостную прочность и жёсткость
Проведём расчёт тихоходного вала.
Действующие силы: – окружная – осевая – радиаль-ная – крутящий момент.
Определим реакции опор в вертикальной плоскости.
. Отсюда находим что .
Выполним проверку: . Следовательно вертикальные реакции найдены верно.
Определим реакции опор в горизонтальной плоскости.
Проверим правильность нахождения горизонтальных реакций: – верно.
По эпюре видно что самое опасное сечение вала находится в точке причём моменты здесь будут иметь значения: .
Расчёт производим в форме проверки коэффициента запаса прочности значение которого можно принять . При этом должно выполняться условие что где – расчётный коэффициент запаса прочности и – коэффициенты запаса по нормальным и касательным напряжениям которые определим ниже.
Найдём результирующий изгибающий момент как .
Определим механические характеристики материала вала (Сталь 40Х) по табл. 10.2 лит. 3: – временное сопротивление (предел прочности при растяжении); и – пределы выносливости гладких образцов при симметричном цикле изгиба и кручении; – коэффициент чувствительности материала к асимметрии цикла напряжений.
Определим отношение следующих величин (табл. 10.9 лит. 3): где и – эффективные коэффициенты концентрации напряжений – коэффициент влияния абсолютных размеров поперечного сечения. Также по табл. 10.4 лит. 3 найдём значение коэффициента влияния шероховатости и по табл. 10.5 лит. 3 коэффициент влияния поверхностного упрочнения .
Вычислим значения коэффициентов концентрации напряжений и для данного сечения вала: .
Определим пределы выносливости вала в рассматриваемом сечении: .
Рассчитаем осевой и полярный моменты сопротивления сечения вала: где – расчётный диаметр вала.
Вычислим изгибное и касательное напряжение в опасном сечении по формулам: .
Определим коэффициент запаса прочности по нормальным напряжениям: .
Для нахождения коэффициента запаса прочности по касательным напряжениям определим следующие величины. Коэффициент влияния асимметрии цикла напряжений для данного сечения . Среднее напряжение цикла . Вычислим коэффициент запаса .
Найдём расчётное значение коэффициента запаса прочности и сравним его с допускаемым: – условие выполняется.
Выбор и расчёт шпоночных и шлицевых соединений
Расчёт шпоночных соединений заключается в проверке условия прочности материала шпонки на смятие.
Соединение быстроходного вала с муфтой электродвигателя. Имеем: – крутящий момент на валу – диаметр вала – длина шпонки – её ширина – высота шпонки – глубина паза вала – глубина паза ступицы – допускаемое напряжение на смятие материала шпонки – временное сопротивление материала шпонки (предел прочности при растяжении). Условие прочности: – верно.
Соединение промежуточного вала с зубчатым колесом. Имеем: – крутящий момент на валу – диаметр вала – длина шпонки – её ширина – высота шпонки – глубина паза вала – глубина паза ступицы – допускаемое напряжение на смятие – временное сопротивление (предел прочности при растяжении). Условие прочности: – верно.
Соединение тихоходного вала с колесом зубчатым. Имеем: – крутящий момент на валу – диаметр вала – длина шпонки – её ширина – высота шпонки – глубина паза вала – глубина паза ступицы – допускаемое напряжение на смятие материала шпонки – временное сопротивление материала шпонки (предел прочности при растяжении). Условие прочности: – верно.
Соединение тихоходного и приводного валов с муфтой. Имеем: – крутящий момент на валу – диаметр вала – длина шпонки – её ширина – высота шпонки – глубина паза вала – глубина паза ступицы – допускаемое напряжение на смятие материала шпонки – временное сопротивление материала шпонки (предел прочности при растяжении). Условие прочности: – верно.
Рассчитаем прямобочное шлицевое соединение торсионного вала и промежуточного полого вала. Средняя серия: – внутренний диаметр – наружный диаметр – число зубьев – ширина зубьев – статический момент площади смятия соединения длиной 1 мм. Длина соединения крутящий момент . Расчёт производится исходя из условия износостойкости по напряжению смятия: здесь – допускаемое напряжение на смятие материалов валов (Сталь 40Х) – временное сопротивление этих материалов (предел прочности при растяжении).
Смазка зубчатых зацеплений и подшипников
Для смазывания передачи применена картерная система.
Определим окружную скорость вершин зубьев колеса: – для тихоходной ступени здесь – частота вращения вала тихоходной ступени – диаметр окружности вершин колеса тихоходной ступени; – для быстроходной ступени здесь – частота вращения вала быстроходной ступени – диаметр окружности вершин колеса быстроходной ступени.
Расчитаем предельно допустимый уровень погружения зубчатого колеса тихоходной ступени редуктора в масляную ванну: здесь – диаметр окружностей вершин зубьев колеса тихоходной ступени.
Определим необходимый объём масла по формуле: где – высота области заполнения маслом и – соответственно длина и ширина масляной ванны.
Выберем марку масла по табл. 11.1 лит. 3 в соответствии с окружной скоростью колеса быстроходной ступени: И–20А. Его кинематическая вязкость для зубчатых колёс при температуре .
Смазывание подшипников происходит тем же маслом за счёт разбрызгивания. При сборке редуктора подшипники необходимо предварительно промаслить.
Сборку привода ленточного транспортёра рекомендуется производить следующим образом.
Установить плиту позиции 6 закрепив её фундаментными болтами поз. 9 с гайками поз. 11 и шайбами поз. 12.
На валах электродвигателя поз. 1 редуктора поз. 2 приводного вала поз. 3 закрепить соответствующие полумуфты.
Установить электродвигатель поз. 1 и редуктор поз. 2 на плиту поз.6 и закрепить соответствующими элементами.
Установить приводной вал поз. 3 и закрепить его болтами поз. 8 с шайбами поз. 13.
Соединить соответствующие части полумуфт в муфты поз. 4 и поз.5.
Список использованной литературы
А.В. Буланже Н.В.Палочкина Л.Д. Часовников методические указания по расчёту зубчатых передач редукторов и коробок скоростей по курсу “Детали машин” часть 1 Москва МГТУ им. Н.Э. Баумана 1980г.
В.Н. Иванов В.С. Баринова “Выбор и расчёты подшипников качения” методические указания по курсовому проектированию Москва МГТУ им.Н.Э. Баумана 1981 г.
П.Ф. Дунаев О.П. Леликов “Конструирование узлов и деталей машин” Москва “Высшая школа” 1985 г.
Д.Н. Решетов “Детали машин” Москва “Машиностроение” 1989г.
Р.И. Гжиров “Краткий справочник конструктора” “Машиностроение” Ленинград 1983 г.
Атлас конструкций “Детали машин” Москва “Машиностроение” 1980 г.
Л.Я. Перель А.А. Филатов справочник “Подшипники качения” Москва “Машиностроение” 1992 г.