Привод ленточного конвейера 4




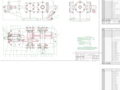
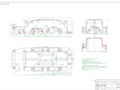
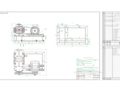
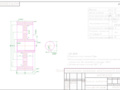
- Добавлен: 25.10.2022
- Размер: 7 MB
- Закачек: 0
Описание
Состав проекта
![]() |
![]() |
![]() ![]() ![]() |
![]() ![]() ![]() ![]() |
![]() ![]() ![]() ![]() |
![]() ![]() ![]() |
![]() ![]() ![]() ![]() |
![]() ![]() ![]() |
![]() ![]() |
![]() ![]() |
![]() ![]() ![]() |
![]() ![]() ![]() |
![]() ![]() ![]() |
![]() ![]() ![]() |
![]() ![]() |
![]() ![]() ![]() ![]() |
![]() |
![]() ![]() ![]() |
![]() ![]() ![]() |
![]() ![]() ![]() |
![]() ![]() ![]() |
![]() ![]() ![]() ![]() |
![]() ![]() ![]() |
![]() ![]() ![]() |
![]() ![]() |
![]() ![]() ![]() ![]() |
![]() ![]() ![]() |
![]() ![]() ![]() |
![]() ![]() ![]() |
![]() ![]() ![]() |
![]() ![]() |
![]() ![]() ![]() |
![]() ![]() |
![]() ![]() ![]() |
![]() ![]() |
![]() ![]() |
![]() ![]() |
![]() ![]() ![]() |
![]() ![]() ![]() ![]() |
![]() ![]() ![]() |
Дополнительная информация
01 Введение.doc
Редуктор состоит из корпуса в котором размещают элементы передачи - зубчатые колеса валы подшипники и т.д. В отдельных случаях в корпусе размещают также устройства для смазывания или устройства для охлаждения.
Редуктор проектируют либо для привода определенной машины либо по заданной нагрузке и передаточному числу без указания конкретного назначения. Наиболее распространены горизонтальные редукторы. Как горизонтальные так и вертикальные редукторы могут иметь колеса с прямыми косыми и круговыми зубьями. Корпус чаще всего выполняют литым чугуном реже сварным стальным. Валы монтируются на подшипниках качения или скольжения. Выбор горизонтальной или вертикальной схемы для редукторов всех типов обусловлен удобством общей компоновки привода (относительным расположением двигателя и рабочего вала приводимой в движение машины и т.д.). Для контроля за уровнем масла в корпусе редуктора установлен маслоуказатель.
В нашем случае схема привода состоит из
)одноступенчатого конического редуктора
Принцип работы: при вращении электродвигателя вращающий момент с вала электродвигателя передается на быстроходный вал редуктора через упругую муфту. Коническая вал-шестерня вращает зубчатое колесо и следовательно тихоходный вал. Ведущая звездочка цепной передачи жестко закрепленная на тихоходном валу начинает вращаться одновременно с тихоходным валом передавая вращающий момент на вал рабочей машины.
Конические зубчатые колеса применяют в передачах у которых оси валов пересекаются под некоторым углом Σ в основном Σ=90о. В коническом зацеплении действуют осевые силы в связи с чем конструкция опор усложнена.
Цепные передачи применяют для понижения частоты вращения приводного вала. В основном-это приводные роликовые цепи однорядные и двухрядные. Передача состоит из двух звездочек соединяемых цепью. Цепные передачи компактнее ременных работают при больших нагрузках меньше нагружают валы.
Вал.dwg

Радиусы скруглений не более 3мм. 2.Неуказанные предельные отклонения размеров: отверстия-по вала-по остальные-±.
Графический материал111.dwg

Техническая характеристика 1 Передаваемая мощность
; 2 Частота вращения тихоходного вала
; 3 Вращающий момент на тихоходном валу
; 4 Передаточное число редуктора 4; 5 Расчетный суммарный срок службы
Звездочка поз.7 и муфта поз.37 условно сняты
Шпонка ГОСТ 23360-78 46 8x7x32 1 47 10x8x32 1 48 14x9x28 1
Штифт ГОСТ 3129-70 i-78.2
Шайба ГОСТ 14734-69 41 7019-6024 1
Шайба ГОСТ 6402-70 42 5.65Г.029 4 43 6.65Г.029 5 44 8.65Г.029 12 45 10.65Г.029 10
Гайка ГОСТ 5916-70 33 М10-6H.5 10
Болт ГОСТ 7798-70 26 М5-8gх14.58.029 4 27 М6-8gх16.58.029 5
М8-8gх25.58.029 8 29 М8-8gх30.58.029 4
М10-8gх35.58.029 2 31 М10-8gх110.58.029 8
Винт ГОСТ 1476-93 32 В.М6-6gх10.14Н 1
Гайка ГОСТ 11871-88 34 М33х1
Манжета ГОСТ 8752-79 35 1.1-30x52-1 1 36 1.1-40x60-1 1
Подшипник ГОСТ 333-79 38 7207 2 39 7208 2
Шайба ГОСТ 11872-80 40 33.01.05 1
ПЛК-7.5-9.01.00.000 СБ Сборочный чертеж
ПЛК-7.5-9.01.00.000 ПЗ Пояснительная записка
ПЛК-7.5-9.01.00.001 Маслоуказатель 1
Масло индустриальное И-Г-А-32 ГОСТ 20799-88 2
Муфта ГОСТ 14084-93 37 63-28-1-25-1-У3 1
Штифт ГОСТ 3128-70 i-78.2
Вертикальная плоскость
Эквивалентный момент
Изгибающие моменты в вертикальной плоскости
Суммарные изгибающие моменты
Горизонтальная плоскость
Изгибающие моменты в горизонтальной плоскости
Рисунок 7.1-Схема нагружения быстроходного вала
Рисунок 7.2-Схема нагружения тихоходного вала
Технические требования 1 * Размеры для справок. 2 Плоскость разъема при окончательной сборке покрыть герметиком УЗОМ ГОСТ 13489-79. 3 Редуктор залить индустриальным маслом И-Г-А-32 ГОСТ 20799-88 в объеме 2
литра. Уровень масла контролировать при помощи маслоуказателя поз.1. 4 Течь масла в местах неподвижных соединений не допускается. Требования к манжетным уплотнениям по ГОСТ 8752-79. 5 Редуктор обкатать по 10-15 мин на всех режимах нагрузки. 6 После обкатки редуктор осмотреть
при необходимости подтянуть подшипники
болтовые соединения. 7 Грунтовку наружных поверхностей
кроме выходных концов валов
произвести грунтом ВА-03К коричневый ГОСТ 19024-73. 8 Окраску редуктора произвести: внутри- маслостойкой краской красного цвета
снаружи- серой нитроэмалью. 9 Остальные технические требования по СТБ 1022-96.
Сталь 40Х ГОСТ 1050-88
173 241 НВ кроме места
Общие допуски по СТБ 1022-96.
* Размер обеспечивает инструмент;
Отв. центр.FM6 ГОСТ 14034-74
Модуль средний нормальный
Нормальный исходящий
Коэффициент смещения х 0
Коэф. изм. толщ. зуба х
Угол делительного конуса
Степень точности - 8-C
Межосевой угол передачи
Модуль внешний окружной m
Внешнее конусное расстояние
Среднее конусное расстояние
Средний делительный диаметр d
Внешняя высота зуба h
Неуказанные радиусы закруглений 6мм
Точность зубчатого колеса- в соответствии с ГОСТ 1758-81;
Сталь 40Х ГОСТ 4543-71
ПЛК-7.5-9.01.00.012 Кольцо 13 ПЛК-7.5-9.01.00.013 Кольцо 14 ПЛК-7.5-9.01.00.014 Кольцо 15 ПЛК-7.5-9.01.00.015 Кольцо
ПЛК-7.5-9.01.00.008 Крышка подшипника
ПЛК-7.5-9.01.00.018 Шайба мазеудерживающая
ПЛК-7.5-9.01.00.009 Крышка подшипника
ПЛК-7.5-9.01.00.019 Пробка 1 20 ПЛК-7.5-9.01.00.020 Пробка-отдушина 1
ПЛК-7.5-9.01.00.005 Вал
ПЛК-7.5-9.01.00.004 Вал-шестерня
ПЛК-7.5-9.01.00.002 Основание корпуса 3 ПЛК-7.5-9.01.00.003 Крышка корпуса
ПЛК-7.5-9.01.00.007 Звездочка
ПЛК-7.5-9.01.00.011 Стакан
ПЛК-7.5-9.01.00.016 Прокладка 2компл. 17 ПЛК-7.5-9.01.00.017 Прокладка 2компл.
ПЛК-7.5-9.01.00.025 Прокладка 1
ПЛК-7.5-9.01.00.022 Прокладка 1 23 ПЛК-7.5-9.01.00.023 Прокладка 1 24 ПЛК-7.5-9.01.00.024 Прокладка 1
ПЛК-7.5-9.01.00.006 Колесо зубчатое
ПЛК-7.5-9.01.00.021 Крышка люка 1
ПЛК-7.5-9.01.00.000 ПЗ
Общие допуски по ГОСТ 30893.1-mk.
ПЛК-7.5-9.01.00.010 Крышка подшипника
ПРИВОД СПЕЦ.doc
ПЛК-14-1.02.00.000 СБ
ПЛК-14-1.03.00.000 СБ
ПЛК-14-1.04.00.000 СБ
Электродвигатель 4А160S8У3
Муфта 1-6300-80-1 У2
Штифт 4×18 ГОСТ 3128-70
ПЛК-14-1.01.00.000 ВО
Графический материал1.dwg

Техническая характеристика 1 Передаваемая мощность
; 2 Частота вращения тихоходного вала
; 3 Вращающий момент на тихоходном валу
; 4 Передаточное число редуктора 4; 5 Расчетный суммарный срок службы
ПЛК-14-1.02.00.000 СБ
Шпонка ГОСТ 23360-78 46 8x7x32 1 47 10x8x32 1 48 14x9x28 1
Штифт ГОСТ 3129-70 i-78.2
Шайба ГОСТ 14734-69 41 7019-6024 1
Шайба ГОСТ 6402-70 42 5.65Г.029 4 43 6.65Г.029 5 44 8.65Г.029 12 45 10.65Г.029 10
Гайка ГОСТ 5916-70 33 М10-6H.5 10
Болт ГОСТ 7798-70 26 М5-8gх14.58.029 4 27 М6-8gх16.58.029 5
М8-8gх25.58.029 8 29 М8-8gх30.58.029 4
М10-8gх35.58.029 2 31 М10-8gх110.58.029 8
Винт ГОСТ 1476-93 32 В.М6-6gх10.14Н 1
Гайка ГОСТ 11871-88 34 М33х1
Манжета ГОСТ 8752-79 35 1.1-30x52-1 1 36 1.1-40x60-1 1
Подшипник ГОСТ 333-79 38 7207 2 39 7208 2
Шайба ГОСТ 11872-80 40 33.01.05 1
ПЛК-14-1.02.00.000 СБ Сборочный чертеж
ПЛК-14-1.00.00.000 ПЗ Пояснительная записка
ПЛК-14-1.02.00.001 Маслоуказатель 1
Масло индустриальное И-Г-А-32 ГОСТ 20799-88 2
Муфта ГОСТ 14084-93 37 63-28-1-25-1-У3 1
Штифт ГОСТ 3128-70 i-78.2
Вертикальная плоскость
Эквивалентный момент
Изгибающие моменты в вертикальной плоскости
Суммарные изгибающие моменты
Горизонтальная плоскость
Изгибающие моменты в горизонтальной плоскости
Рисунок 7.1-Схема нагружения быстроходного вала
Рисунок 7.2-Схема нагружения тихоходного вала
Технические требования 1 * Размеры для справок. 2 Плоскость разъема при окончательной сборке покрыть герметиком УЗОМ ГОСТ 13489-79. 3 Редуктор залить индустриальным маслом И-Г-А-32 ГОСТ 20799-88 в объеме 2
литра. Уровень масла контролировать при помощи маслоуказателя поз.1. 4 Течь масла в местах неподвижных соединений не допускается. Требования к манжетным уплотнениям по ГОСТ 8752-79. 5 Редуктор обкатать по 10-15 мин на всех режимах нагрузки. 6 После обкатки редуктор осмотреть
при необходимости подтянуть подшипники
болтовые соединения. 7 Грунтовку наружных поверхностей
кроме выходных концов валов
произвести грунтом ВА-03К коричневый ГОСТ 19024-73. 8 Окраску редуктора произвести: внутри- маслостойкой краской красного цвета
снаружи- серой нитроэмалью. 9 Остальные технические требования по СТБ 1022-96.
173 241 НВ кроме места
Общие допуски по СТБ 1022-96.
* Размер обеспечивает инструмент;
Отв. центр.FM6 ГОСТ 14034-74
Модуль средний нормальный
Нормальный исходящий
Коэффициент смещения х 0
Коэф. изм. толщ. зуба х
Угол делительного конуса
Степень точности - 8-C
Межосевой угол передачи
Модуль внешний окружной m
Внешнее конусное расстояние
Среднее конусное расстояние
Средний делительный диаметр d
Внешняя высота зуба h
Неуказанные радиусы закруглений 6мм
Точность зубчатого колеса- в соответствии с ГОСТ 1758-81;
ПЛК-14-1.02.00.012 Кольцо 13 ПЛК-14-1.02.00.013 Кольцо 14 ПЛК-14-1.02.00.014 Кольцо 15 ПЛК-14-1.02.00.015 Кольцо
ПЛК-14-1.02.00.008 Крышка подшипника
ПЛК-14-1.02.00.018 Шайба мазеудерживающая
ПЛК-14-1.02.00.009 Крышка подшипника
ПЛК-14-1.02.00.019 Пробка 1 20 ПЛК-14-1.02.00.020 Пробка-отдушина 1
ПЛК-14-1.02.00.005 Вал
ПЛК-14-1.02.00.004 Вал-шестерня
ПЛК-14-1.02.00.002 Основание корпуса 3 ПЛК-14-1.02.00.003 Крышка корпуса
ПЛК-14-1.02.00.007 Звездочка
ПЛК-14-1.02.00.011 Стакан
ПЛК-14-1.02.00.016 Прокладка 2компл. 17 ПЛК-14-1.02.00.017 Прокладка 2компл.
ПЛК-14-1.02.00.025 Прокладка 1
ПЛК-14-1.02.00.022 Прокладка 1 23 ПЛК-14-1.02.00.023 Прокладка 1 24 ПЛК-14-1.02.00.024 Прокладка 1
ПЛК-14-1.02.00.006 Колесо зубчатое
ПЛК-14-1.02.00.021 Крышка люка 1
ПЛК-14-1.00.00.000 ПЗ
ПЛК-7.5-9.02.00.000 СБ
Общие допуски по ГОСТ 30893.1-mk.
ПЛК-14-1.02.00.010 Крышка подшипника
Сталь 40Х ГОСТ 1050-88
6.2 проверочный расчет вала редуктора.doc
Опорные реакции в горизонтальной плоскости:
Опорные реакции в вертикальной плоскости:
Суммарные изгибающие моменты:
Эквивалентные моменты:
Намечаем опасное сечение на валу: посадка подшипника на вал.
Действующий в сечении эквивалентный момент
Расчетный диаметр вала в опасном сечении:
Принятый диаметр вала удовлетворяет условию .
00_Soderzhanie.doc
Проектный расчет передач редуктора 7
Проверочный расчет передач редуктора 13
Расчет открытой цепной передачи 16
Проектный расчет валов привода 22
Проверочный расчет вала редуктора . ..25
Выбор и расчет шпоночных соединений привода 31
Выбор и расчет подшипников привода 33
Выбор соединительных муфт .. 37
Обоснование и выбор смазочных материалов .38
Техника безопасности и экологичность проекта .40
Список использованных источников 42
Приложение А(обязательное). Спецификации
12 заключение.doc
Целью данного проекта является проектирование привода конвейера который состоит как из стандартных (двигатель муфта болты барабан подшипники и т.д.) деталей так и из деталей форма и размеры которых определяются на основе конструктивных технологических экономических и других нормативов (корпус и крышка редуктора валы и др.).
В ходе решения поставленные передо мной задач была основана методика выбора элементов привода получены навыки проектирования позволяющие обеспечить необходимый технический уровень надёжность и долгий срок службы механизма.
Опыт и навыки полученные в ходе выполнения курсового проекта будут востребованы при выполнении как курсовых проектов по специальным дисциплинам так и при выполнении дипломного проекта.
9 Выбор соединительных муфт.doc
Для соединения быстроходного вала редуктора с валом электродвигателя используем муфту зубчатую по ГОСТ 50895-96.
Работоспособность муфты определяется по напряжениям смятия рабочих поверхностей зубьев:
где [sсм]=12 15 МПа;
Do – делительный диаметр зубьев;
K=1 – коэффициент режима работы.
Условие прочности соблюдается.
10 Обоснование и выбор смазочных материалов.doc
Для уменьшения потерь на трение в зацеплении предотвращения заедания зубьев охлаждения зубчатых колес удаления продуктов износа и предохранения от коррозии применяются два способа смазывания: картерная (окунанием) и циркуляционная. Для окружной скорости 12 мс применяется картерная смазка являющаяся простым и надежным способом.
Принимаем масло И-Г-А-32 ГОСТ 20799-88
Коническое колесо погружаем в масло на всю длину зуба:
Принимаем расстояние от вершины колеса до дна редуктора
Корректируем высоту расположения оси h редуктора:
Согласно ГОСТ 24386-91 принимаем
В таком случаем объем масла заливаемого в редуктор составит:
где расстояния между стенками (по компоновке).
Контроль уровня масла осуществляется при помощи фонарного маслоуказателя. Для замены масла в корпусе предусмотрено сливное отверстие закрываемое пробкой с цилиндрической резьбой. Внутренняя полость корпуса сообщается с внешней средой посредством установленной на крышку отдушины. Заливка масла осуществляется путем снятия крышки корпуса.
Подшипники быстроходного вала смазываются пластическим материалом типа Литол-24 ГОСТ 21150-87 поскольку смазывание дальнего от зацепления подшипника брызгами масла затруднено. Для предотвращения вымывания смазки маслом заливаемым в редуктор а также предотвращения попадания на дорожки качения продуктов износа устанавливаем мазеудерживающую шайбу.
Рисунок 10.1 – Мазеудерживающая шайба.
Подшипники тихоходного вала смазываются тем же маслом что и зубчатые
колеса поскольку окружная скорость колес больше 2 мс. Брызгами масла покрыты все детали передач и внутренние поверхности стенок корпуса редуктора. Стекающее с колес валов и со стенок корпуса масло попадает в подшипник.
Спецификация.dwg

Вращающий момент на тихоходном валу
Частота вращения тихоходного вала
Техническая характеристика:
Общее передаточное число
Технические требования:
Необработанные поверхности литых деталей
находящихся в масляной
красить маслостойкой красной эмалью.
Наружные поверхности корпуса красить серой эмалью
Плоскость разъема покрыть тонким слоем герметика
ГОСТ 24285 - 80 при окончательной сборке.
Техническая характеристика.
Технические требования.
Регулировку подшипников производить прокладками поз. 17
При окончательной сборке плоскость разъема покрыть герметиком.
Наружные необработанные поверхности покрыть ЭМНЦ-246 серой
Номинальная мощность на выходном валу P=4 кВт.
Частота вращения выходного вала n=47
Общее передаточное отношение U=12.1 в том числе:
а) быстроходной ступени Uб=3.66;
б) тихоходной ступени Uт=3
Объем заливаемой смазки -10 л.
двухступенчатый соосный
АА ДТМ 32.2.5.00.000
АА ДТМ 32.2.5.00.000СБ
АА ДТМ 32.2.5.01.100
Крышка смотрового окна
АА ДТМ 32.2.5.02.200
АА ДТМ 32.2.5.00.013
АА ДТМ 32.2.5.00.004
АА ДТМ 32.2.5.00.014
АА ДТМ 32.2.5.00.005
АА ДТМ 32.2.5.00.003
АА ДТМ 32.2.5.00.010
АА ДТМ 32.2.5.00.011
АА ДТМ 32.2.5.00.016
АА ДТМ 32.2.5.00.017
АА ДТМ 32.2.5.00.018
АА ДТМ 32.2.5.00.019
АА ДТМ 32.2.5.00.015
АА ДТМ 32.2.5.00.006
АА ДТМ 32.2.5.00.007
АА ДТМ 32.2.5.00.023
Прокладки регулировочные
АА ДТМ 32.2.5.00.024
АА ДТМ 32.2.5.00.025
АА ДТМ 32.2.5.00.026
АА ДТМ 32.2.5.00.022
АА ДТМ 32.2.5.00.027
АА ДТМ 32.2.5.00.008
АА ДТМ 32.2.5.00.020
АА ДТМ 32.2.5.00.012
АА ДТМ 32.2.5.00.009
АА ДТМ 32.2.5.00.031
АА ДТМ 32.2.5.00.041
АА ДТМ 32.2.5.00.029
АА ДТМ 32.2.5.00.028
АА ДТМ 32.2.5.00.043
АА ДТМ 32.2.5.00.032
АА ДТМ 32.2.5.00.021
АА ДТМ 32.2.5.00.046
АА ДТМ 32.2.5.00.048
АА ДТМ 32.2.5.00.047
АА ДТМ 32.2.5.00.045
АА ДТМ 32.2.5.00.049
АА ДТМ 32.2.5.00.034
Кольцо 039-050-36-2-4
АА ДТМ 32.2.5.00.035
Кольцо 055-063-30-2-4
АА ДТМ 32.2.5.00.036
АА ДТМ 32.2.5.00.037
АА ДТМ 32.2.5.00.033
АА ДТМ 32.2.5.00.044
АА ДТМ 32.2.5.00.040
АА ДТМ 32.2.5.00.039
АА ДТМ 32.2.5.00.038
АА ДТМ 32.2.5.00.030
АА ДТМ 32.2.5.00.042
Редуктор коническо-цилиндрический
Пояснительная записка
АА ДТМ 32.2.5.02000ПЗ
АА ДТМ 32.2.5.01.000
АА ДТМ 32.2.5.02.000
АА ДТМ 32.2.5.03.000
l=1700 мм ГОСТ 19700-74
6.1 проверочный расчет вала редуктора.doc
Расчет производится в следующей последовательности:
) Определяются окружные радиальные и осевые силы действующие на вал от зубчатых ременных цепных и других передач;
) Определяют положение опор и деталей закрепленных на валу;
) Раскладывают силы в двух взаимно перпендикулярных плоскостях zoy и zo
) Строят эпюры изгибающих моментов и в плоскостях zoy и zo
) Находят наибольшее значение суммарного изгибающего момента;
) Определяют эквивалентный момент;
) Определяют диаметр вала в рассчитываемом сечении;
При необходимости производят корректировку размеров.
Коническая передача:
Делительные диаметры колес
Сила давления на вал со стороны муфты согласно ГОСТ 16162-85:
Расчет быстроходного вала:
Опорные реакции в горизонтальной плоскости:
Опорные реакции в вертикальной плоскости:
Суммарные изгибающие моменты:
Эквивалентные моменты:
Намечаем опасное сечение на валу - посадка подшипника на вал.
Действующий в сечении эквивалентный момент
Расчетный диаметр вала в опасном сечении:
где допускаемое напряжение при изгибе.
Принятый диаметр вала удовлетворяет условию .
2 3 расчет конической прямозубой передачи.docx
крутящий момент на быстроходном валу;
крутящий момент на тихоходном валу;
частота вращения быстроходного вала;
частота вращения тихоходного вала;
передаточное число конической передачи;
Принимаемый ресурс работы передачи
Для изготовления колеса и шестерни в качестве материала выбираем сталь 40Х для шестерни HB1 = 345 HB (термообработка улучшение) для колеса HB2 = 295 HB (термообработка улучшение).
Определим допускаемые контактные напряжения
где Н lim b – предел контактной выносливости материала соответствующий базе испытаний и зависящий от средней твердости поверхностных слоев зубьев.
Коэффициент запаса прочности
Коэффициент долговечности :
где NHlim – базовое число циклов перемены напряжений соответствующее пределу выносливости принимается по графику или рассчитывается по формуле:
NК - число циклов перемены напряжений соответствующее заданному сроку службы передачи при постоянной нагрузке определяется по формуле где – срок службы привода; n – частота вращения рассчитываемого зубчатого колеса;
показатель степени:
Базовое число циклов напряжений :
Эквивалентное число циклов нагружений:
Коэффициент долговечности :
Допускаемое контактное напряжение МПа :
Для рассматриваемой конической передачи в качестве расчетного принимаем
Допускаемые напряжения изгиба при расчете на выносливость FP
где предел выносливости зубьев :
YA - коэффициент учитывающий влияние двустороннего приложения нагрузки при одностороннем приложении нагрузки (передача нереверсивная) YA = 1;
YR – коэффициент учитывающий шероховатость переходной поверхности: при полировании переходной поверхности YR = 12; в остальных случаях можно принимать YR = 10 принимаем YR = 10;
SF - коэффициент безопасности SF = 14 17 = 17 причем чем меньше твердость тем больше должна быть величина коэффициента безопасности;
-Коэффициент долговечности (не менее 1):
при HB350 при HB>350.
Базовое число циклов напряжений изгиба
Допускаемое напряжение изгиба:
Определяем внешний делительный диаметр колеса:
где Kd – вспомогательный коэффициент учитывающий тип передачи;
Kd = 99 - для прямозубых передач Kd = 86 - для косозубых передач; Kh – коэффициент неравномерности распределения нагрузки по ширине
зубчатого венца; выбирается по значению
коэффициент ширины зубчатого венца относительно внешнего конусного расстояния рекомендуется Принимаем
коэффициент ширины зубчатого венца при проектировании редукторов со стандартными параметрами принимается
Согласно рекомендациям число зубьев шестерни .
Число зубьев колеса:
Фактическое передаточное число:
Внешний окружной модуль прямозубых колес:
Внешний делительный диаметр шестерни:
Углы делительных конусов:
Внешнее конусное расстояние:
Принимаем рабочую ширину зацепления
Условия выполняются.
Среднее конусное расстояние:
Средний окружной модуль :
Средний делительный диаметр шестерни:
Средний делительный диаметр колеса:
Коэффициент смещения:
где так как передача прямозубая
Коэффициент расчетной толщины зуба исходного контура:
Внешняя высота головки зуба:
Внешняя высота ножки зуба:
Внешняя высота зуба:
Внешняя окружная толщина зуба шестерни:
Внешняя окружная толщина зуба колеса:
Угол конуса вершин зубьев :
Угол конуса впадин зубьев :
Внешний диаметр вершин зубьев :
Проверим коэффициенты ширины венца :
условие выполняется.
Средняя окружная скорость колес :
Принимаем степень точности
Рис. 2.1 – Схема действия сил в прямозубом коническом зацеплении.
Окружная сила на шестерне и колесе :
где dwm2 – средний начальный диаметр колеса :
Радиальная сила на шестерне численно равная осевой силе на колесе:
Осевая сила на шестерне численно равная радиальной на колесе:
Проверочный расчет конической прямозубой передачи
Контактная выносливость устанавливается сопоставлением расчетного и допускаемого контактных напряжений:
где коэффициент учитывающий механические свойства материала сопряженных зубчатых колес;
коэффициент учитывающий форму сопряженных поверхностей зубьев в полюсе зацепления:
- коэффициент суммарной длины контактных линий:
коэффициент торцового перекрытия:
коэффициент учитывающий динамическую нагрузку возникающую в зацеплении до зоны резонанса :
где -удельная окружная динамическая сила:
где коэффициент учитывающий влияние вида зубчатой передачи и модификацию профиля головок зубьев;
коэффициент учитывающий влияние разности шагов зацеплении зубьев шестерни и колеса;
Недогрузка составляет:
Допускаются отклонения (перегрузка) и (недогрузка).
Проверяем зубья на выносливость по напряжениям изгиба:.
Расчетное напряжение изгиба :
гдекоэффициент нагрузки :
гдекоэффициент учитывающий внешнюю динамическую нагрузку
коэффициент динамической нагрузки в зацеплении:
где удельная окружная динамическая сила :
где коэффициент учитывающего влияние вида зубчатой передачи и модификации профиля зубьев;
коэффициент учитывающий неравномерность распределения нагрузки по длине контактных линий;
коэффициент учитывающий распределение нагрузки между зубьями:
коэффициент учитывающий форму зуба и концентрацию напряжений принимается в зависимости от эквивалентного числа зубьев и коэффициента смещения x:
Число зубьев эквивалентного колеса:
Находим отношение и дальнейший расчет ведем для того колеса у которого это отношение меньше :
Расчет ведем по колесу.
коэффициент учитывающий наклон зуба ;
коэффициент учитывающий перекрытие зубьев ;
Условие прочности по напряжениям изгиба выполняется.
8 Выбор и расчет подшипников привода.doc
Подшипники качения - это опоры вращающихся деталей использующие элементы качения ролики и работающие на основе трения качения. Подшипниковые узлы кроме собственно подшипников качения имеют корпус с крышкой устройства для крепления колец подшипников защитные и смазочные устройства. Подшипники качения разделяют по форме тел качения.
Конические колеса должны быть точно и жестко зафиксированы в осевом направлении. Шариковые радиальные подшипники характеризует малая осевая жесткость. Поэтому в силовых передачах для опор валов конических колес применяют конические роликовые подшипники. Первоначально выбирают легкую серию.
Обычно используют подшипники класса точности 0. Подшипники более высокой точности применяют для опор валов требующих повышенной точности вращения или работающие при особо высоких частотах вращения.
Подшипники быстроходного вала:
Применяем конические роликовые подшипники легкой серии.
Подбираем dп=35 мм №7207 ГОСТ 333-79.
Подшипники тихоходного вала:
Подбираем dп=40 мм №7308 ГОСТ 333-79.
Рисунок 8.1-Геометрические размеры подшипника.
Сведем параметры выбранных подшипников в таблицу 8.1.
Таблица 8.1- Параметры конических роликовых подшипников.
Выбор схемы установки подшипников.
Применяем установку подшипников по схеме «врастяжку».
– расстояние между подшипниками.
Рисунок 8.2-Схема установки подшипников «врастяжку»
Применяем установку по схеме «враспор» как наиболее простую.
Рисунок 8.3-Схема установки подшипников «враспор».
Расчет подшипников быстроходного вала.
Рассчитываем подшипник с параметрами:
базовая динамическая грузоподъемность;
коэффициент радиальной нагрузки;
коэффициент влияния осевого нагружения;
коэффициент осевой нагрузки;
коэффициент вращения;
коэффициент безопасности;
температурный коэффициент.
осевая сила в зацеплении;
частота вращения вала.
Требуемая долговечность
Осевые составляющие радиальных нагрузок:
Определяем осевые нагрузки подшипников. Т.к.
Определяем отношения:
Для заданных условий
Эквивалентная динамическая нагрузка:
Расчет производим для наиболее нагруженной опоры.
Номинальная долговечность:
где показатель степени для роликовых подшипников.
Следовательно окончательно принимаем подшипник .
Расчет подшипников тихоходного вала.
Колесо.dwg

компоновочная схема и выбор способа смазывания передач и подшипников.doc
1 Расчет элементов корпуса.
Корпуса редукторов выполняют из чугуна СЧ15. В корпусе размещаются детали передач подшипники и смазочные устройства. Корпуса редукторов чаще всего разъемные и состоят из крышки и основания корпуса.
Положение основания и крышки фиксируется двумя коническими штифтами устанавливаемыми без зазора до расточки гнезд под подшипники. Основание и крышку корпуса соединяют болтами для обеспечения герметичности. Ориентировочно принимают расстояние между осями болтов . Для создания герметичности корпуса плоскости его разъема перед сборкой покрываются спиртовым лаком или жидким стеклом. Применение уплотнительных прокладок недопустимо.
Для снятия крышки на ней делают проушины или рым- болты. Крюки на корпусе редуктора выполняют для транспортировки. Для заливки масла и осмотра деталей передач в крышке корпуса имеется смотровое окно закрываемое крышкой.
В редукторах с большим выделением тепла предусматривают отдушину соединяющую внутреннюю полость редуктора с атмосферой. Для удаления загрязненного масла и для промывки редуктора в нижней части корпуса делают отверстие под пробку с цилиндрической резьбой. Под цилиндрическую пробку ставят уплотняющую прокладку. Маслоспускное отверстие выполняют на уровне днища. Желательно чтобы днище имело наклон в сторону маслоспускного отверстия.
Подшипники закрывают крышками глухими и сквозными через которые проходят концы валов.
Расчет производим согласно [7 табл.10.2 стр.241].
Толщина стенки корпуса редуктора ():
где внешнее конусное расстояние;
Толщина крышки редуктора:
Толщина фланца корпуса редуктора:
Толщина фланца крышки редуктора:
Толщина фундаментных лап редуктора:
Толщина ребер жесткости корпуса редуктора:
Толщина ребер жесткости крышки редуктора:
Диаметр фундаментных болтов():
Количество фундаментных болтов Принимаем
Размеры определяющие положение болтов :
диаметр болта крышки подшипника [1 табл.12.1.1. стр. 157].
Диаметр болтов соединяющих основание корпуса с крышкой:
Диаметр конического штифта:. Длина штифта
Размеры элементов зубчатых колес [4 стр.163 табл. 10.3]:
Рисунок 7.1 – Конструктивные элементы корпуса.
Ступица зубчатого колеса (см. рис.7.2):
Рисунок 7.2- Конструкция зубчатого колеса.
Конструкция крышек подшипников согласно [1 стр.180 п.12.10].
Рисунок 7.3- Конструкция крышки подшипника.
Диаметр установки болтов:
Наружный диаметр фланца:
Толщина фланца крышки:
Конструирование стакана:
Толщина фланца h2=h1=8 мм.
Толщина стакана h3=8 мм.
Длина L – принимается конструктивно;
D1=D+25d5=72+16+25*8=108мм;
D2=D1+2d5=108+2*8=124 мм;
Принимаем D2=124 мм.
Диаметр отверстий dотв5 во фланце под болты d5 = 8 мм.
Конструкция звездочки цепной передачи [4 стр. 233].
Рисунок 7.4- Конструкция звездочки.
Наружный диаметр ступицы:
где радиус закругления при шаге t35мм.
2 Эскизная компоновка редуктора
Изображение конической зубчатой передачи (рис. 7.1) начинают с нанесения двух взаимно перпендикулярных линий.
Рисунок 7.5 – Эскизная компоновка конической пары.
От точки О пересечения этих линий откладывают по осям: вверх и вниз- отрезки ОА равные 05d1 а вправо и влево- ОВ равные 05d2. Через точки А проводят горизонтальные линии а через точки В- вертикальные линии до взаимного пересечения в точке С. Точки С соединяют с точкой О линиями которые представляют собой образующие делительных конусов шестерни и колеса. В точках С к образующим делительных конусов восстанавливают перпендикуляры на которых откладывают высоту головки зуба и высоту ножки . Концы отложенных отрезков соединяют с точкой О линиями которые представляют собой образующие конусов вершин и впадин зубьев. Вдоль образующих делительных конусов от точек С по направлению к точке О откладывают ширину зуба b и проводят границу зуба. Толщину обода шестерни и колеса назначают одинаковыми
Согласно данным предварительного расчета диаметров валов на эскизную компоновку наносят габариты валов.
При проектировании вала-шестерни с целью уменьшения консольной части вала первый подшипник располагают как можно ближе к шестерне.
Согласно данным предварительного подбора подшипников на эскизную компоновку наносят габариты подшипников.
Перед размещением подшипников необходимо решить вопрос о их смазывании. При достаточно большой скорости вращения зубчатых колес возможно смазывание разбрызгиванием. При небольшой скорости вращения зубчатых колес не происходит смазывания подшипников. В этом случае принимают раздельную систему смазывания зубчатых колес и подшипников. Для подшипников используют консистентную смазку. С целью предотвращения вытекания разжиженной (за счет нагрева редуктора) консистентной смазки из подшипникового узла на валах устанавливают мазеудерживающие шайбы. В этом случае подшипник должен входить в корпус на величину определяемую толщиной мазеудерживающего кольца. Если подшипники будут смазываться разбрызгиванием масла в картере редуктора то их следует располагать сразу от внутренней стенки корпуса
По результатам предварительной компоновки строят расчетные схемы валов и определяют реакции в опорах. При этом валы рассматривают как двухопорные балки нагруженные силами в зацеплении. Расстояния между точками приложения сил и опорами принимают из эскизной компоновки.
Перечисленные ранее размеры окончательно определяют после конструирования крышек подшипников выбора типа уплотнения и конструирования корпусной детали.
Рисунок 7.6 – Эскизная компоновка вала-шестерни конической передачи.
3 Смазывание зацепления.
Для уменьшения потерь на трение в зацеплении предотвращения заедания зубьев охлаждения зубчатых колес удаления продуктов износа и предохранения от коррозии применяются два способа смазывания: картерная (окунанием) и циркуляционная. Для окружной скорости 12 мс применяется картерная смазка являющаяся простым и надежным способом.
Устанавливаем вязкость масла.
По контактным напряжениям и окружной скорости вязкость масла должна быть приблизительно равна [5 табл.11.1 стр.173].
Принимаем масло И-Г-А-32 ГОСТ 20799-88 [5 табл.11.2 стр.173].
Коническое колесо погружаем в масло на всю длину зуба [5 стр. 174]:
Принимаем расстояние от вершины колеса до дна редуктора
Корректируем высоту расположения оси h редуктора:
Согласно ГОСТ 24386-91 [1 табл. 12.8.3] принимаем
В таком случаем объем масла заливаемого в редуктор составит:
где расстояния между стенками (по компоновке).
Контроль уровня масла осуществляется при помощи фонарного маслоуказателя. Для замены масла в корпусе предусмотрено сливное отверстие закрываемое пробкой с цилиндрической резьбой. Внутренняя полость корпуса сообщается с внешней средой посредством установленной на крышку отдушины. Заливка масла осуществляется путем снятия крышки корпуса.
3 Смазывание подшипников.
Подшипники быстроходного вала смазываются пластическим материалом типа Литол-24 ГОСТ 21150-87 поскольку смазывание дальнего от зацепления подшипника брызгами масла затруднено. Для предотвращения вымывания смазки маслом заливаемым в редуктор а также предотвращения попадания на дорожки качения продуктов износа устанавливаем мазеудерживающую шайбу [7 рис. 9.39 стр.207].
Рисунок 7.7 – Мазеудерживающая шайба.
Подшипники тихоходного вала смазываются тем же маслом что и зубчатые колеса поскольку окружная скорость колес больше 2 мс [8 стр. 31]. Брызгами масла покрыты все детали передач и внутренние поверхности стенок корпуса редуктора. Стекающее с колес валов и со стенок корпуса масло попадает в подшипник.
13 Литература.doc
А. Т. Скойбеда А. В. Кузьмин Н. Н. Макейчик «Детали машин и основы конструирования». 2-е изд. перераб.-Минск: Вышэйшая школа 2006-560 с.: ил.
С. Н. Ничипорчик М. И. Корженцевский В. Ф. Калачев и др. «Детали машин в примерах и задачах». Минск: Вышэйшая школа 1981-432 с. ил.
А.Е. Шейнблит «Курсовое проектирование деталей машин»: Учебное пособие для техникумов. -М.: Высшая школа 1991.-432 с.: ил.
П.Ф. Дунаев О.П. Леликов «Конструирование узлов и деталей машин». Учеб. пособие для техн. спец. вузов.-5-е изд. перераб. и доп.-М.: Высшая школа 1998.-447 с. ил.
А.В. Кузьмин И.М. Чернин Б.С. Козинцов «Расчеты деталей машин» Справочное пособие. Минск: Вышэйшая школа 1986 г.
С.А. Чернавский К.Н. Боков И.М.Чернин и др. Курсовое проектирование деталей машин: Учеб. Пособие для учащихся машиностроительных специальностей техникумов -2-е изд. перераб. и доп.-М.: Машиностроение 1988.-416 с.; ил.
В. Л. Николаенко В. И. Шпилевский А. А. Калина В. М. Анохин. Прикладная механика: Курсовое проектирование: учебное пособие под ред. А. Т. Скойбеды. – Минск: БНТУ 2010.-177 с.
П. П. Капуста. Расчеты на сопротивление усталости: Методические рекомендации по технической механике для преподавателей средних специальных заведений.- Минск: Вышэйшая школа 1989-90 с.
С.А. Чернавский Г.А. Снесарев Б.С. Козинцов и др. Проектирование механических передач: Учебно-справочное пособие для втузов - 5-е изд. перераб. и доп. –М.: Машиностроение 1984.-560 с. ил.
Привод.dwg

Вращающий момент на тихоходном валу
Частота вращения тихоходного вала
Техническая характеристика:
Общее передаточное число
Технические требования:
Необработанные поверхности литых деталей
находящихся в масляной
красить маслостойкой красной эмалью.
Наружные поверхности корпуса красить серой эмалью
Плоскость разъема покрыть тонким слоем герметика
ГОСТ 24285 - 80 при окончательной сборке.
Техническая характеристика.
Технические требования.
Регулировку подшипников производить прокладками поз. 17
При окончательной сборке плоскость разъема покрыть герметиком.
Наружные необработанные поверхности покрыть ЭМНЦ-246 серой
Номинальная мощность на выходном валу P=4 кВт.
Частота вращения выходного вала n=47
Общее передаточное отношение U=12.1 в том числе:
а) быстроходной ступени Uб=3.66;
б) тихоходной ступени Uт=3
Объем заливаемой смазки -10 л.
двухступенчатый соосный
Неуказанные литейные радиусы 3 5 мм. 2. Формовочные уклоны 5° 8°. 3. Отливку отжечь. 4. Обработку по размерам в квадратных скобках проводить совместно с корпусом и крышкой люка. 5. Неуказанные предельные отклонения размеров механической обработки: отверстий H14
остальные ±T142. 6. Смещение осей Б
Г относительно плоскости А не более 0
мм. 7. Покрытие необработанных поверхностей эмаль НЦ-5123 серой ГОСТ 7462-73. 8. ** Обработать на глубину неровносит литья. 9. * Размеры для справок
серая НЦ -246 по МРТУ 6-10-609-66.
Покрытие нерабочих поверхностей-эмаль
Смещение канавок шкивов не более 0
Допуск параллельности осей шкивов 1 мм
на 100 мм ширины шкива.
АДТМ 31 00.00.000.СБ
Пояснительная записка
Технические условия 1. Тип редуктора коническо-цилиндрический 2. Передаточное число 10
3. Крутящий момент ны выходном валу
Нм 724 4. Частота вращения выходного вала
6 5. КПД рудуктора 0
Технические требования 1. Допуск параллельности осей шкивов 1 мм на 100 мм ширины шкива 2. Смещение канавок шкивов не более 0
мм 3. Покрытие нерабочих поверхностей - эмаль серая НЦ-246 по МРТУ 6-10-609-66
АА ДТМ 32.2.5.00.000
АА ДТМ 32.2.5.00.000СБ
Редуктор коническо-цилиндрический
АА ДТМ 32.2.5.02000ПЗ
АА ДТМ 32.2.5.01.000
АА ДТМ 32.2.5.02.000
АА ДТМ 32.2.5.03.000
АА ДТМ 32.2.5.00.004
АА ДТМ 32.2.5.00.005
l=1700 мм ГОСТ 19700-74
5 проектный расчет диаметров валов.docx
Вал редуктора представляет собой ступенчатое цилиндрическое тело количество и размеры ступеней которого зависят от количества и размеров установленных на вал деталей.
Для облегчения монтажа зубчатых колес подшипников и других деталей применяют ступенчатые валы.
Диаметр выходного конца вала исходя из условия прочности определяется по формуле:
где условное допустимое напряжение кручения
Принимаем для быстроходного и для тихоходного валов.
Для облегчения монтажа подшипников зубчатых колес и других деталей применяют ступенчатую конструкцию вала.
Диаметр входного и выходного концов валов необходимо согласовать с посадочными диаметрами муфт и электродвигателей или с ГОСТ 12081-72 и ГОСТ 12080-66 на конические и цилиндрические концы валов.
Для удобства соединения вала редуктора с валом электродвигателя стандартной муфтой соблюдают условие чтобы диаметры соединяемых валов имели размеры отличающиеся не более чем на 20%.
Под манжетные уплотнения с учетом ГОСТа на них:
Под подшипники с учетом ГОСТа на них:
Под зубчатое колесо с учетом ГОСТа на нормальные линейные размеры:
Для буртика удерживающего зубчатое колесо в осевом направлении с учетом ГОСТа на нормальные линейные размеры:
Длины указанных участков валов определяются конструктивно в процессе выполнения эскизной компоновки редуктора (передачи).
Размеры быстроходного вала:
Ступень под ступицу упругой муфты:
Ступень под манжетное уплотнение крышки с отверстием:
принимаем под резьбу шлицевой гайки.
Ступень под подшипник:
Рассмотрим соотношение внешнего диаметра зубьев шестерни и диаметра вала под подшипником :
Следовательно принимаем решение об изготовлении вала-шестерни.
Ступень под буртик для подшипника:
Размеры тихоходного вала:
Ступень под ступицу звездочки цепной передачи:
Ступень под буртик для колеса:
Диаметр приводного вала рассчитаем по формуле:
Окончательно диаметр вала в месте посадки барабана d = 85 мм.
Разрабатываем конструкцию вала и по чертежу оцениваем его размеры:
- диаметр вала под барабан;
- диаметр выходного конца вала;
- диаметр выходного под манжету;
- длина выходного конца вала;
- длина шейки под подшипник;
- длина вала под барабан.
Пояснительная записка.doc
ХАРЬКОВСКИЙ НАЦИОНАЛЬНЫЙ АВТОМОБИЛЬНО-ДОРОЖНЫЙ
Кафедра деталей машин и ТММ
ПОЯСНИТЕЛЬНАЯ ЗАПИСКА
к курсовому проекту по деталям машин
на тему: "Проектирование привода конвейера
Энерго-кинематический расчет . .5
Расчет клиноременной передачи 7
Расчет цилиндрической косозубой передачи тихоходной ступени .10
Расчет конической прямозубой передачи быстроходной ступени 22
Расчет выходного вала редуктора 27 8. Выбор муфты .32
Выбор подшипников .33
Расчет шпоночных соединений ..35
Спроектировать привод конвейера
Окружная сила Ft = 4 Н×м
Окружная скорость V = 125 мс
Диаметр барабана D = 035 м
Ременная передача клиновая
Редуктор двухступенчатый
Срок службы Lh = 15000 ч
Рисунок 1 – Кинематическая схема привода
– электродвигатель 2 – клиноременная передача 3 – редуктор 4 – муфта
Редуктором называют механизм выполненный в виде отдельного агрегата служащий для понижения угловой скорости и соответственно повышения крутящих моментов.
Редуктор - неотъемлемая часть современного оборудования. В приводах общемашиностроительного назначения разрабатываемых при курсовом проектировании редуктор является основным и наиболее трудоемким узлом.
Краткая характеристика коническо-цилиндрических двухступенчатых редукторов развернутой схемы:
Коническо-цилиндрических двухступенчатые редукторы развернутой схемы применяются обычно в интервале передаточных чисел u = 8 40. Простота конструкции обусловила широкое их применение в промышленности. Несимметричное расположение колес относительно опор вызывает концентрацию нагрузки по длине зуба поэтому такие редукторы требуют жестких валов.
ЭНЕРГО-КИНЕМАТИЧЕСКИЙ РАСЧЕТ
Выбор электродвигателя
) Мощность на выходном валу привода:
) Расчетная мощность электродвигателя:
где – КПД привода [ 1 стр.15]
где – КПД ременной передачи;
– КПД тихоходной ступени;
– КПД быстроходно ступени.
) Частота вращения выходного вала:
) Принимаем электродвигатель по ГОСТ 19523-81 [1 табл.2 табл.3]:
тип двигателя 4A132S4У3
Выбор передаточных чисел
) Передаточное число привода:
) Производим разбивку по передачам:
Принимаем для клиноременной передачи: [1 стр. 15]
Передаточное число редуктора:
Для тихоходной ступени [1 стр.56]:
Для быстроходной ступени:
Мощности крутящие моменты на валах привода и угловые скорости их вращения.
Результаты расчетов сводим в таблицу 1.
Таблица 1 – Мощности крутящие моменты на валах и их угловые скорости и частоты вращения
РАСЧЕТ КЛИНОРЕМЕННОЙ ПЕРЕДАЧИ
Крутящий момент на быстроходном валу:
При данном моменте по [1 табл.2.12] принимаем сечение ремня «Б» с размерами: bp = 14 мм h = 105 мм b0 = 17 мм y0 =4 мм F1 = 138 см2.
Диаметр меньшего шкива в соответствии с рекомендациями [1 табл.2.12] dp min = 125 мм но так как в рассматриваемом случае нет жестких ограничений к габаритам передачи то для повышения долговечности ремня принимаем dp следующий за минимальным [1 табл.2.12] (таблица 2.21) т.е. dp1 = 140 мм.
Диаметр большего шкива:
Стандартный размер по ГОСТ 17383-17 [1 табл.2.12] dp2 = 280 мм.
Фактическое передаточное число:
Частота вращения ведомого вала:
Межосевое расстояние согласно рекомендациям [1 табл.2.14]:
Расчетная длина ремня:
Расчетная длина ремня L = 1700 мм.
По стандартной длине L уточняем действительное межосевое расстояние:
Минимальное межосевое расстояние для удобства монтажа и снятия ремней:
Максимальное межосевое расстояние для создания натяжения и подтягивания ремня при вытяжке:
Угол обхвата на меньшем шкиве:
Исходная длина ремня [1 табл. 2.15] Lо = 2240 мм. Относительная длина
L Lо = 17002240 = 0759 мм.
Коэффициент длины [1 табл. 2.19] СL = 092.
Исходная мощность при dp1 = 140 мм и v = 1066 мс [1 табл. 2.15]
Коэффициент угла обхвата [1 табл. 2.18] Ca = 096.
Поправка к крутящему моменту на передаточное число [1 табл. 2.20]:
Поправка к мощности:
Коэффициент режима работы при указанной нагрузке [1 табл. 2.8]:
Допускаемая мощность на один ремень:
Расчетное число ремней:
Коэффициент учитывающий неравномерность нагрузки:
Действительное число ремней в передаче:
Сила начального натяжения одного клинового ремня:
Усилие действующее на валы передачи:
Размеры обода шкивов:
lp = 14 мм h1min = 8 мм
Наружные диаметры шкивов:
Ширина обода шкивов:
РАСЧЕТ ЦИЛИНДРИЧЕСКОЙ КОСОЗУБОЙ ПЕРЕДАЧИ ТИХОХОДНОЙ СТУПЕНИ
Передаточное число u34 = 355
На шестерне N3I = 5233 кВт
Обороты n3 = 234677 мин-1
Срок службы t = 15000 ч
Выбор материала и допускаемых напряжений для шестерни и колеса:
По [1 табл. 3.12] назначаем материал для шестерни и колеса сталь 40ХН (поковка); термообработка - улучшение. Для шестерни при радиусе заготовки до 100 мм sв = 850 МПа sт = 600 МПа НВ = 240 для колеса НВ = 265.
Определяем допускаемое напряжение изгиба для шестерни [1ф.3.51]:
Предварительно находим предел выносливости зубьев при изгибе соответствующий эквивалентному числу циклов перемены напряжений [1ф.3.52]
где предел выносливости при изгибе соответствующий базовому числу циклов нагружений [1 табл.3.19]
Коэффициент учитывающий влияние двухстороннего приложения нагрузки [1 табл.3.20] при одностороннем приложении нагрузки КFC = 1 коэффициент долговечности [1 ф.3.53]
при HB 350 [1стр.77] mF = 6; базовое число циклов перемены напряжений [1 с.77] NFO = 4×106 эквивалентное (суммарное) число циклов перемены напряжений [1 ф. 3.54]
принимаем NFL1 = 10. Соответственно sF lim 1 = 477×1×1 = 477 МПа
Коэффициент безопасности [1ф.356]
где [1 табл.3.19] [1 табл.3.21]
Коэффициент учитывающий чувствительность материала к концентрации напряжений [1ф.3.57] Ys = 1. Коэффициент учитывающий шероховатость переходной поверхности зуба [1ф.3.58] YR = 1.
Допускаемое напряжение изгиба для зубьев шестерни
Допускаемые напряжения изгиба для зубьев колеса:
где предел выносливости при изгибе соответствующий базовому числу циклов перемены напряжений [1 табл.3.19]
Коэффициент учитывающий влияние двухстороннего приложения нагрузки [1 табл.3.20] KFC = 1; коэффициент долговечности [1ф. 3.53]
При HB 350 [1c.77] mF = 6; базовое число циклов перемены напряжений [1с.77] NFO = 4 × 106; эквивалентное (суммарное) число циклов перемены напряжений [1ф. 3.54]:
Предел выносливости
sF lim2 = 434 × 1 × 1 = 434 МПа
Коэффициент безопасности [1ф. 3.56]
SF = S=×175 × 10 = 175.
где SF=175 [1 табл.3.19] SF=10 [1 табл.3.21]
Коэффициент учитывающий чувствительность материала к концентрации напряжений [1ф.3.57] Ys = 1. Коэффициент учитывающий шероховатость переходной поверхности зуба [1ф.3.58] YR = 10. Допускаемое напряжение изгиба для колеса
Допускаемое напряжение изгиба при расчете на действие максимальной нагрузки [1ф.3.62] для шестерни:
Предварительно находим предельное напряжение не вызывающее остаточных деформаций или хрупкого излома зуба [1табл.3.19]:
sF limМ1 = 48 ×НВ1 = 48 × 265 = 1272 МПа
Коэффициент безопасности [1с.76]:
SFM1 = S’FM1 × S’’FM1 =175 × 1=175
здесь S’FM1 = 175 [1c.80]; S’’FM1= S’’F1 = 1 [1табл.3.21]
Коэффициент учитывающий чувствительность материала к концентрации напряжений [1ф.3.57] YS=1. Следовательно
Допускаемое напряжение изгиба при действии максимальной нагрузки для колеса:
где предельное напряжение не вызывающие остаточных деформаций или хрупкого излома зуба [1табл.3.19]
sF limМ2 = 48 ×НВ2 = 48 × 241 = 1157 МПа
Коэффициент безопасности [1с.80]
SFM2 = S’FM2 × S’’FM2 =175 × 10=175
здесь S’FM2 = 175 [1c.80]; S’’FM2= S’’F2 = 10[1табл.3.21]
Коэффициент учитывающий чувствительность материала к концентрации напряжений YS=10. Следовательно
Допускаемое контактное напряжение для шестерни [1ф.3.33]
Предварительно находим предел контактной выносливости поверхностей зубьев соответствующих эквивалентному числу циклов перемены нагружений [1ф.3.34]
sН lim1 =sН lim в1 × KHL1
здесь предел контактной выносливости соответствующий базовому числу циклов перемены напряжений [1табл.3.17]
sН lim в1 =2 ×НВ1 +70 = 2× 265 + 70 = 600 МПа
Коэффициент долговечности [1ф.3.35]
где базовое число циклов перемены напряжений [1рис.3.16]
эквивалентное (суммарное) число циклов перемены напряжений
NHЕ1= N1 = 60× n3× t=60×234677×1500=2112 × 108
Отношение NHЕ1 NHO1= > 1 поэтому коэффициент долговечности определяем по формуле [1ф.3.38]
Предел контактной выносливости
sН lim1 = 600 ×09 =540 Мпа. Коэффициент безопасности для зубьев с однородной структурой материала [1с.75] SH1=11
Коэффициент учитывающий шероховатость сопряженных поверхностей [1табл.3.18] ZR=095.
Коэффициент учитывающий окружную скорость [1с.75] ZV=1. Допускаемое контактное напряжение для шестерни:
Допускаемое контактное напряжение для колеса
Предварительно находим предел контактной выносливости поверхностей зубьев соответствующий эквивалентному числу циклов перемены напряжений
sН lim2 =sН lim в2 × КHL2
где предел контактной выносливости соответствующий базовому числу циклов перемены напряжений [1табл.3.17]
sН lim в2 =2 ×НВ2 +70 = 2× 241 + 70 = 552 МПа
коэффициент долговечности [1ф.3.35]
здесь базовое число циклов перемены напряжений [1рис.3.16]
NHЕ2= N2 = 60·n3·t=60×234677×15000=21× 108
Отношение NHЕ2 NHO2= =12424 > 1 поэтому коэффициент долговечности определяем по формуле [1ф.3.38]
sН lim2 = 552 ×09 =497 Мпа. Коэффициент безопасности для зубьев с однородной структурой материала [1с.75] SH2=11
Коэффициент учитывающий окружную скорость [1с.75] ZV=1. Допускаемое контактное напряжение для шестерни
Допускаемое контактное напряжение передачи [1ф.3.41]
[sН ] =045([sН1 ]+ [sН 2]) =045(466364 + 429) = 403 МПа
Проверяем условие [1ф.3.42]
[sН ]=403 МПа 123[sНmin ]=1.23·429 = 528 МПа.
т.е условие выполнено поэтому принимаем допускаемое контактное напряжение передачи [sН ]=403 МПа.
Допускаемое контактное напряжение при расчете на действие максимальной нагрузки (см. с.80):
[sНM1 ]=28 ·sТш = 28 ·600 = 1680 МПа
[sНM2 ]=28 ·sТк = 28 ·sТк = 28 ·580 = 1624 МПа
Расчет передачи на контактную выносливость. Вычисляем начальный диаметр шестерни (табл. 3.13формула 3.16):
Предварительно определяем величины необходимые для расчета. Номинальный крутящий момент на шестерне (формула 3.12)
Ориентировочная окружная скорость (формула 3.27):
При данной скорости требуемая степень точности зубчатых колес (табл. 3.33)-9-я. Коэффициент учитывающий распределение нагрузки между зубьями (рис. 3.13)
Коэффициент ширины зубчатого венца при симметричном расположении опор (табл. 3.15)
Проверяем условие (3.26) Принимаем (см.с.71) K = 2 угол наклона (см.с.60) = 16
расчетное число зубьев шестерни (см.с.58)
Коэффициент учитывающий распределение нагрузки по ширине венца (рис.3.14б) Коэффициент учитывающий динамическую нагрузку (табл.3.16) (определяется интерполированием). Коэффициент учитывающий форму сопряженных поверхностей (формула 3.28`) Коэффициент учитывающий механические свойства материалов сопряженных колес (формула 3.29) Коэффициент учитывающий суммарную длину когтактных линий (формула 3.31)
где коэффициент торцового перекрытия (формула 3.3)
Начальный диаметр шестерни
Модуль зацепления [1 ф.3.46]
Полученный модуль округляем до стандартного значения [1 прил.табл.9]
m=45 мм. По стандартному модулю пересчитываем начальный диаметр
Проверочный расчет передачи на контактную выносливость. Определяем расчетную окружность (формула 3.47) при начальном диаметре шестерни
При данной скорости требуемая степень точности передачи (табл.3.33) - 9-ая что соответствует принятой ранее степени точности. Уточняем по скорости коэффициенты входящие в формулу (3.48): (табл.3.16) (рис 3.13) (рис. 3.17).
Уточняем начальный диаметр шестерни (формула 3.48):
По уточненному начальному диаметру dW1 находим модуль зацепления
Полученный модуль вновь округляем до стандартного значения мм что совпадает с ранее принятой величиной модуля; следовательно диаметр начальной окружности шестерни мм. Ширина зубчатого венца при
Проверочный расчет зубьев на контактную прочность при действии максимальной нагрузки[1 ф.3.60] .
где действующее напряжение при расчете на контактную выносливость
[1 табл.3.13 ф.3.15]
Отклонение действующих контактных напряжений от допускаемых составляет
что допустимо. Расчетное контактное напряжение от максимальной нагрузки
Проверочный расчет зубьев на выносливость по напряжениям згиба. Расчетное напряжение изгиба (табл. 3.13 формула 3.17)
Предварительно определяем величины необходимые для расчета. Эквивалентное число зубьев шестерни и колеса (см. с. 76)
Коэффициенты учитывающие форму зуба шестерни и колеса (рис. 3.18) Коэффициент учитывающий влияние наклона зуба на его напряженное состояние (формула 3.50)
Расчетная удельная нагрузка (формула 3.25`)
где коэффициент учитывающий распределение нагрузки между зубьями (формула 3.49)
Коэффициент учитывающий распределение нагрузки по ширине венца (рис. 3.14 г) коэффициент учитывающий динамическую нагрузку (табл. 3.16) (определяется интерполированием). Соответственно
Напряжение изгиба в зубьях шестерни
в зубьях колеса (табл. 3.13 формула 3.17`)
Проверочный расчет при изгибе максимальной нагрузкой. Расчетное напряжение от максимальной нагрузки (формула 3.61)
Напряжения изгиба при расчете на выносливость:
для зубьев шестерни
Расчетное напряжение изгиба от максимальной нагрузки:
Принимаем окончательно параметры передачи
Определяем межосевое расстояние
Проверяем межосевое расстояние
При необходимости округления межосевого расстояния до целого числа пересчитываем угол наклона (формула 3.2`). Принимаем межосевое расстояние
соответственно угол наклона и
Пересчитываем начальные диаметры шестерни
РАСЧЕТ КОНИЧЕСКОЙ ПРЯМОЗУБОЙ ПЕРЕДАЧИ БЫСТРОХОДНОЙ СТУПЕНИ
Передаточное число u23 = 31
На шестерне N2 = 5506 кВт
Обороты n2 =7275 мин-1
Выбор материала и допускаемых напряжений для шестерни и колеса. Материал и термообработку зубчатых колес сохраняем. При этом сохраняются и допускаемые напряжения.
Расчет передачи на контактную выносливость. Согласно рекомендациям (см. с. 61) принимаем пропорционально понижающиеся зубья (форма I). Вычисляем начальный диаметр шестерни по большому торцу (табл. 3.14 формула 3.20):
Предварительно определяем величины необходимые для расчета (из примера цилиндрической передачи). Ориентировочная скорость зубчатых колес (формула 3.27) При данной скорости требуемая степень точности передачи (табл. 3.33) - 8-я. Коэффициент учитывающий распределение нагрузки между зубьями для прямозубых передач (см. с. 82) Коэффициент ширины венца (формула 3.63) Для улучшения условий работы зацепления и уменьшения длины редуктора коническую шестерню устанавливаем между опорами (см. рис. 3.20 схему II). Коэффициент учитывающий распределение нагрузки по ширине венца (рис.3.20а) при отношении
Коэффициент динамической нагрузки (табл. 3.16) для степени точности зубчатых колес на единицу грубее установленной (см.с.80) т.е. для 9-й степени точности (определяется интерполированием). Коэффициент учитывающий форму сопряженных поверхностей (формула 3.28`) Коэффициент учитывающий механические свойства материалов сопряженных колес (формула 3.29) .
По таблице 3.11 выбираем чмсло зубьев шестерни и коэффициент торцового пееркрытия Коэффициент учитывающий суммарную длину контактных линий (формула 3.30)
Начальный диаметр шестерни по большему торцу
Внешний окружной модуль
Полученный модуль округляем по стандарту (см. приложение табл. 9)
Пересчитываем начальный диаметр
Число зубьев плоского колеса (табл. 3.9)
Внешнее конусное расстояние (табл. 3.9)
Рабочая ширина зубчатого венца (табл.3.1) при принимаем Проверяем условие (формула 3.64) т.е. следовательно условие удовлетворяется.
Проверочный расчет зубьев на контактную выносливость. Вычисляем средний нормальный модуль зацепления (формула 3.4)
Средний начальный диаметр шестерни (см. с.80)
Определяем расчетную окружную скорость на среднем начальном диаметре шестерни (формула 3.47):
При данной скорости по табл. 3.33 требуемая степень точности передачи - 8-я что совпадает с ранее принятой степенью точности. Коэффициент учитывающий окружную скорость передачи (рис. 3.17) Уточняем коэффициент динамический нагрузки (табл. 3.16)
Начальный диаметр шестерни по большему торцу (формула 3.48)
Вновь определяем окружной модуль
Полученный модуль округляем по стандарту Диаметр начальный окружности по большему торцу соответствующий стандартному модулю
Проверочный расчет передачи на контактную прочность при действии максимальной нагрузки. Фактическое напряжение при расчете на контактную выносливость (табл. 3.14 формула 3.19)
Отклонение действующих контактных напряжений от допускаемых составляет менее 4% что допустимо. Расчетное напряжение от максимальной нагрузки (формула 3.60)
Проверочный расчет зубьев на выносливость по напряжениям изгиба. Изгибающее напряжение для зуба шестерни (табл. 3.14 формула 3.22)
Предварительно определяем величины необходимые для расчета. Находим эквивалентное число зубьев для шестерни и колеса (формула 3.7):
Здесь (см. табл. 3.9) Соответственно Следовательно
Определяем коэффициенты учитывающие форму зуба (рис. 3.21): Коэффициент учитывающий влияние наклона зуба на его напряженное состояние для прямозубых колес (см. с. 77) Расчетная удельная нагрузка (формула 3.25`)
где коэффициент учитывающий распределение нагрузки между зубьями (см. с. 82) коэффициент учитывающий распределение нагрузки по ширине венца (рис. 3.20 б) при отношении Коэффициент учитывающий динамическую нагрузку (табл. 3.16) при скорости
Средний нормальный модуль Напряжение изгиба для зуба шестерни
Для зуба колеса (таблица 3.14 формула 3.22`)
Проверочный расчет зубьев при изгибе максимальной нагрузкой. Расчетное напряжение от максимальной нагрузки (формула 3.61)
соответственно расчетное напряжение для зуба шестерни
Окончательно принимаем параметры передачи.
РАСЧЕТ ВЫХОДНОГО ВАЛА РЕДУКТОРА
Так как на настоящем этапе расчета расстояния между опорами неизвестные ориентировочно диаметр вала в опасном сечении определяется из условий прочности при кручении в случае пониженных допускаемых напряжений
где Т3 = 213 - крутящий момент Н.м;
[t] – допускаемое напряжение на кручение для редукторных валов.
хвостовик вала: 50 мм
под подшипник: 55 мм
Расчет на сложное сопротивление:
Окружная сила [1 табл.5.2]
Радиальная сила [1 табл.5.2]
Осевая сила [1 табл.5.2]
Вертикальная плоскость:
Горизонтальная плоскость:
– коэффициент учитывающий различия в характерах цикла и кручения.
Расчетные эпюры промежуточного вала приведены на рисунке 2.
Рисунок 2 – Расчетные эпюры промежуточного вала
Диаметр вала в опасном сечении принятый при конструировании удовлетворяет условию:
Расчет на выносливость.
Коэффициенты чувствительности материала и асимметрии цикла напряжений при изгибе и кручении ys = yt =0.
МИ = 299817 Н. мм; Т = 723000 Н. мм
Вал работает в нереверсивном режиме. Допускаемый запас выносливости [1 с.185] [n] = 18
)Эффективные коэффициенты концентрации напряжений для вала со шпоночным пазом выполненным пальцевой фрезой Ks = 181; Kt =161 [1 табл.5.12]
Масштабный коэффициент при изгибе и кручении для вала [1 табл.5.16]
Кds = 079; Kdt = 069.
Коэффициент состояния поверхности при шероховатости [1 табл.5.14]
Эффективные коэффициенты концентрации напряжений для данного сечения вала при изгибе и кручении в случае отсутствия технологического упрочнения [1 ф.5.15]
)Определяем эффективные коэффициенты концентрации напряжений при изгибе и кручении вала.
)По [1 табл.5.15] КsD = 262; KtD = 208.
Поскольку в проверяемом сечении два концентратора напряжений то при расчете учитываем один из них – тот для которого КsD и KtD наибольшие т.е. принимаем
КsD = 262; KtD = 25.
) Определяем запас прочности для нормальных напряжений [1 ф.5.4]
где амплитуда номинальных напряжений изгиба [1 5.7 5.10]
где W0 = 15290мм3 – осевой момент сопротивления [1 табл.5.9]
) Напряжение кручения [1 ф.5.10]
Амплитуда и среднее значение номинальных напряжений [1 ф.5.8]
Запас прочности для касательных напряжений [1 ф.5.4]
) Запас прочности в сечении [1 ф.5.5]
Расчетный крутящий момент на муфте [1 с.211]
где ТР- расчетный крутящий момент.
КК – коэффициент запаса [1 табл.7.1];
ТНОМ – номинальный крутящий момент на валу.
ТР = 15 . 723 = 10845 Н. м
Применим муфту зубчатую общего назначения типа M3 ГОСТ 5006-55
Посадочный диаметр 50 мм
Длина посадочной поверхности 70 мм
Дано: подшипник № 311;
динамическая грузоподъемность С=56000 Н;
статическая грузоподъемность С0 = 42600 Н;
радиальная сила Fr = 3893728 H;
осевая сила Fа = 2025592 Н;
Отношение по [1 табл.6.1] Этому соответствует е = 0247
то Х=056; У=18 [1 табл.6.1]
Определяем эквивалентную нагрузку [1 табл.6.5 п.1]
Р=(X .V .Fr + Y. Fa) . Ks . KТ = (056 . 3893728 + 18 . 2025592 ) = 5826553 Н
По [1 приложение табл.21]
СР = 571 следовательно потребная динамическая грузоподъемность
С=571 . Р = 571 . 5826553 = 33269 Н
Выбранные подшипники выходного вала по динамической грузоподъемности проходят.
Выбираем для зубчатых передач смазку И-40А ГОСТ 20799-75 объемом
РАСЧЕТ ШПОНОЧНЫХ СОЕДИНЕНИЙ
)Шпонка на хвостовике входного вала
где lP – рабочая длина шпонки
t1 – глубина шпоночного паза
[sсм] – допускаемое напряжение смятия [1 с.191]
)Шпонка на промежуточном валу
)Шпонка на выходном валу
Н. Ф. Киркач Р. А. Баласанян. “Расчет и проектирование деталей машин.”
М. Н. Иванов “Детали машин.” Москва – 1991 г.
Редуктор.dwg

АА ДТМ 32.2.5.00.000
АА ДТМ 32.2.5.00.000СБ
АА ДТМ 32.2.5.01.100
Крышка смотрового окна
АА ДТМ 32.2.5.02.200
АА ДТМ 32.2.5.00.013
АА ДТМ 32.2.5.00.004
АА ДТМ 32.2.5.00.014
АА ДТМ 32.2.5.00.005
АА ДТМ 32.2.5.00.003
АА ДТМ 32.2.5.00.010
АА ДТМ 32.2.5.00.011
АА ДТМ 32.2.5.00.016
АА ДТМ 32.2.5.00.017
АА ДТМ 32.2.5.00.018
АА ДТМ 32.2.5.00.019
АА ДТМ 32.2.5.00.015
АА ДТМ 32.2.5.00.006
АА ДТМ 32.2.5.00.007
АА ДТМ 32.2.5.00.023
Прокладки регулировочные
АА ДТМ 32.2.5.00.024
АА ДТМ 32.2.5.00.025
АА ДТМ 32.2.5.00.026
АА ДТМ 32.2.5.00.022
АА ДТМ 32.2.5.00.027
АА ДТМ 32.2.5.00.008
АА ДТМ 32.2.5.00.020
АА ДТМ 32.2.5.00.012
АА ДТМ 32.2.5.00.009
АА ДТМ 32.2.5.00.031
АА ДТМ 32.2.5.00.041
АА ДТМ 32.2.5.00.029
АА ДТМ 32.2.5.00.028
АА ДТМ 32.2.5.00.043
АА ДТМ 32.2.5.00.032
АА ДТМ 32.2.5.00.021
АА ДТМ 32.2.5.00.046
АА ДТМ 32.2.5.00.048
АА ДТМ 32.2.5.00.047
АА ДТМ 32.2.5.00.045
АА ДТМ 32.2.5.00.049
АА ДТМ 32.2.5.00.034
Кольцо 039-050-36-2-4
АА ДТМ 32.2.5.00.035
Кольцо 055-063-30-2-4
АА ДТМ 32.2.5.00.036
АА ДТМ 32.2.5.00.037
АА ДТМ 32.2.5.00.033
АА ДТМ 32.2.5.00.044
АА ДТМ 32.2.5.00.040
АА ДТМ 32.2.5.00.039
АА ДТМ 32.2.5.00.038
АА ДТМ 32.2.5.00.030
АА ДТМ 32.2.5.00.042
Вращающий момент на тихоходном валу
Частота вращения тихоходного вала
Техническая характеристика:
Общее передаточное число
Технические требования:
Необработанные поверхности литых деталей
находящихся в масляной
красить маслостойкой красной эмалью.
Наружные поверхности корпуса красить серой эмалью
Плоскость разъема покрыть тонким слоем герметика
ГОСТ 24285 - 80 при окончательной сборке.
Техническая характеристика.
Технические требования.
Регулировку подшипников производить прокладками поз. 17
При окончательной сборке плоскость разъема покрыть герметиком.
Наружные необработанные поверхности покрыть ЭМНЦ-246 серой
Номинальная мощность на выходном валу P=4 кВт.
Частота вращения выходного вала n=47
Общее передаточное отношение U=12.1 в том числе:
а) быстроходной ступени Uб=3.66;
б) тихоходной ступени Uт=3
Объем заливаемой смазки -10 л.
двухступенчатый соосный
Технические условия 1. Тип редуктора коническо-цилиндрический 2. Передаточное число 10
3. Крутящий момент ны выходном валу
Нм 724 4. Частота вращения выходного вала
6 5. КПД рудуктора 0
мм: первой ступени mte 5 второй ступени m 4
7. Число зубьев шестерни и колеса Z1Z2: первой ступени 1856 второй ступени 1864 Технические требования 1. Регулировку зацепления производить прокладками поз. 21-26 2. Плоскости розъемов покрыть пастой "Герметик" Ч-ЗОМ ГОСТ 13489-79 3. Масло в редуктор залить до верхней метки маслоуказателя 4. Смазка зубчатых передач И-40А ГОСТ 20799-75 объем 2
7 подбор и проверочный расчет шпоночных соединений.doc
Элемент соединения шпонка препятствует относительному повороту вала и установленной на нем детали и предназначен для передачи вращающего момента. Призматические шпонки создают ненапряженные соединения ступицы детали с валом сборка которых обычно производится с натягом.
Размеры шпонки и пазов выбирают в зависимости от диаметра вала длина шпонки выбирается исходя из длины ступицы (примерно на 5-10 мм меньше).
Для всех шпоночных соединений принимаем призматические шпонки со скругленными концами ГОСТ 23360-78 (см. рис. 10.1).
Материал шпонки- Cталь 45 ГОСТ 1050-88.
Рисунок 7.1- Шпонка призматическая.
Расчет производим на смятие боковых граней шпонки:
где высота шпонки мм;
высота шпонки в пазу вала мм.
- рабочая длина шпонки мм;
допускаемое напряжение смятия при стальной ступице;
допускаемое напряжение смятия при чугунной ступице;
Подставив в формулу 10.1 значение допускаемого напряжения смятия определим минимально необходимую длину шпонки .
Шпонка под муфту быстроходного вала:
Таблица 7.1- Параметры шпонки
Согласно ГОСТ 12080-66 принимаем
Полная длина шпонки:
Согласно стандартному ряду принимаем
Проверим данную шпонку на смятие:
Условие прочности шпонки на смятие выполняется.
Шпонка под звездочку тихоходного вала:
Таблица 7.2- Параметры шпонки
Шпонка под коническое колесо тихоходного вала:
Таблица 7.3- Параметры шпонки
11. безопасность.docx
Для предупреждения преждевременной поломки редуктора а также для его правильной эксплуатации на протяжении всего срока работы необходимо соблюдать следующие требования техники безопасности:
- не допускать длительной нагрузки по сравнению с номинальным значением;
- не включать без смазки;
- не нарушать графики замены масла;
- соединительные муфты должны быть надежно закреплены и защищены предохранительными кожухами;
- температура корпуса работающего редуктора может достигать 90С поэтому нельзя прикасаться к нему при работе (если позволяют условия корпус редуктора должен быть защищен сетчатым кожухом);
- запрещается снимать крышки закрывающие смотровые окна при работающем редукторе во избежание разбрызгивания горячего масла;
- проверку уровня масла заливку свежего и слив отработанного масла следует производить только при полной остановке привода;
- не рекомендуется подтягивать сливные пробки на работающем редукторе так как в случае срыва резьбы горячее масло может вызвать ожоги;
- при ремонтных работах необходимо отключать электрические источники питания от сети проверить заземление и снять внешние нагрузки на валы;
- если приводы окрашены то при ремонте с использованием сварки требуется принять меры предотвращающие возгорание краски;
- при монтаже крупногабаритных редукторов следует соблюдать общие правила безопасности предусмотренные для монтажных и погрузочно-разгрузочных работ;
- транспортировать редукторы следует закрепив их за специальные грузозахватные устройства.
1 выбор электродвигателя и кинематический расчет привода +.docx
Мощность потребляемую рабочим органом кВт вычисляют по формуле
Определяем общий КПД привода
КПД конической закрытой передачи;
КПД цепной открытой передачи;
КПД одной пары подшипников качения.
Уточняем значения коэффициентов:
Мощность потребляемая рабочим органом
Частота вращения рабочего органа вычисляется по формуле
Желаемая частота вращения электродвигателя
где ориентировочное передаточное число привода.
Исходя из вычисленных значений и по таблице выбираем электродвигатель мощностью кВт ближайшей большей и частотой вращения . Выбираем электродвигатель асинхронный 4А160S8У3 с частотой вращения
Определим передаточное число привода
По рекомендации для конической передачи передаточное число принимаем 4 а для цепной передачи рассчитаем передаточное число по формуле
Рассчитаем частоты вращения валов мин-1
Угловые скорости валов привода с-1
Мощности передаваемые валами привода кВт
Крутящие моменты на валах привода Нм
Таблица 1.1 – Значения параметров элементов привода
Передаточное число u
Число часов работы привода за расчетный срок службы равно
0 титульник.doc
БЕЛОРУССКИЙ НАЦИОНАЛЬНЫЙ ТЕХНИЧЕСКИЙ
Кафедра: «Детали машин ПТМ и М»
По дисциплине «Прикладная механика»
Тема: «Рассчитать и спроектировать привод конвейера»
Исполнитель:студент группы 102522
Руководитель проекта: старший преподаватель
Куранова Ольга Витальевна
ПОЯСНИТЕЛЬНАЯ ЗАПИСКА
к курсовому проекту
Исполнитель: Подгорный Юрий
студент 3 курса группы 102522
Руководитель проекта: старший преподаватель Куранова Ольга Витальевна
Крышка.dwg

Вращающий момент на тихоходном валу
Частота вращения тихоходного вала
Техническая характеристика:
Общее передаточное число
Технические требования:
Необработанные поверхности литых деталей
находящихся в масляной
красить маслостойкой красной эмалью.
Наружные поверхности корпуса красить серой эмалью
Плоскость разъема покрыть тонким слоем герметика
ГОСТ 24285 - 80 при окончательной сборке.
Техническая характеристика.
Технические требования.
Регулировку подшипников производить прокладками поз. 17
При окончательной сборке плоскость разъема покрыть герметиком.
Наружные необработанные поверхности покрыть ЭМНЦ-246 серой
Номинальная мощность на выходном валу P=4 кВт.
Частота вращения выходного вала n=47
Общее передаточное отношение U=12.1 в том числе:
а) быстроходной ступени Uб=3.66;
б) тихоходной ступени Uт=3
Объем заливаемой смазки -10 л.
двухступенчатый соосный
Неуказанные литейные радиусы 3 5 мм. 2. Формовочные уклоны 5° 8°. 3. Отливку отжечь. 4. Обработку по размерам в квадратных скобках проводить совместно с корпусом и крышкой люка. 5. Неуказанные предельные отклонения размеров механической обработки: отверстий H14
остальные ±T142. 6. Смещение осей Б
Г относительно плоскости А не более 0
мм. 7. Покрытие необработанных поверхностей эмаль НЦ-5123 серой ГОСТ 7462-73. 8. ** Обработать на глубину неровносит литья. 9. * Размеры для справок"
4 5 расчет цепной передачи.docx
вращающий момент на тихоходном валу;
вращающий момент на валу рабочей машины;
частота вращения тихоходного вала;
частота вращения вала рабочей машины;
передаточное число цепной передачи;
Индекс 1 относится к ведущей звездочке индекс 2 – к ведомой.
Выбираем приводную роликовую однорядную цепь.
Рисунок 4.1 – Схема цепной передачи.
По передаточному числу принимаем число зубьев меньшей звездочки
Число зубьев ведомой звездочки:
Фактическое передаточное число:
Отклонение от исходного передаточного числа:
Определяем коэффициент учитывающий условия эксплуатации:
где коэффициент динамичности нагрузки; при спокойной нагрузке ;
коэффициент учитывающий влияние межосевого расстояния; при межосевом расстоянии принимают ;
коэффициент регулирования натяжения цепи; при регулировке оси одной из звездочек ;
коэффициент учитывающий способ смазывания цепи; при периодической смазке принимают ;
коэффициент периодичности работы передачи;
При работе в одну смену принимают ;
коэффициент учитывающий влияние наклона цепи;
При наклоне до 600 принимают ;
Ориентировочно допускаемое давление в шарнирах определим в зависимости от частоты вращения меньшей звездочки.
Определим ориентировочное значение шага цепи принимая число рядов цепи m = 1:
Зададимся двумя смежными шагами цепи по ГОСТ 13568-75 и рассчитаем оба варианта.
Определяемые величины и
Разрушающая нагрузка Q Н
Ширина внутреннего звена Ввн мм
Диаметр ролика Dц мм
Проекция опорной поверхности шарнира
Средняя скорость цепи
Оптимальное межосевое расстояние
Длина цепи выраженная в шагах
Максимальная частота вращения меньшей звездочки n
Условие n[n] выполняется
Давление в шарнирах
Допускаемое среднее давление цепи [p] МПа
Условие выполняется для обеих цепей
Натяжение от центробежных сил
Натяжение от провисания цепи
где коэффициент учитывающий расположение цепи.
Расчетный коэффициент запаса прочности для первого шага цепи:
нормативный коэффициент запаса прочности.
условие не выполняется.
Расчетный коэффициент запаса прочности для второго шага цепи:
условие выполняется.
Принимаем роликовую однорядную цепь
Диаметры делительных окружностей звездочек:
Геометрическая характеристика зацепления :
Диаметры окружностей выступов по:
где коэффициент высоты зуба;
Диаметры окружностей впадин:
Наибольшая хорда необходимая для контроля звездочек :
Угол поворота звеньев цепи на звездочке:
Продольный угол зубьев:
Длина прямого участка профиля:
Расстояние от центра дуги впадины до центра дуги головки:
Радиус головки зуба :
Координаты точки О2:
Диаметр обода (наибольший):
Радиус закругления у основания зуба при
Радиус закругления зуба (наименьший):
Расстояние от вершины зуба до линии центров дуг закругления:
Ширина зуба звездочки:
Рисунок 4.2 – Основные размеры зуба звездочки.
Рекомендуемые чертежи
Свободное скачивание на сегодня
Другие проекты
- 29.08.2014