Пневматическая система электролизера для выплавки алюминия




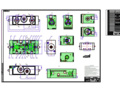
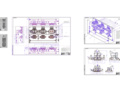
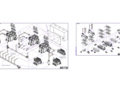
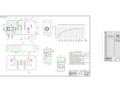
- Добавлен: 25.10.2022
- Размер: 17 MB
- Закачек: 0
Описание
Состав проекта
![]() |
![]() ![]() ![]() ![]() |
![]() ![]() ![]() ![]() |
![]() |
![]() ![]() ![]() ![]() |
![]() ![]() ![]() ![]() |
![]() ![]() ![]() ![]() |
![]() ![]() ![]() ![]() |
![]() ![]() ![]() ![]() |
![]() ![]() ![]() |
![]() ![]() ![]() ![]() |
![]() ![]() ![]() ![]() |
![]() ![]() ![]() ![]() |
Дополнительная информация
л. 4-5. Шкаф управления.dwg

л. 7 Распределитель.dwg

DIMENSIONS ARE IN MILLIMETERS
Распределитель 32 c пневматическим управлением
Кольцо ХостаформC9021
Втулка ХостаформC9021
Манжета золотника NBR
Толкатель ХостаформC9021
Уплотнение крышки TPE
Сегмент ХостаформC9021
Винт М6 ГОСТ 11738 -72
Кольцо запорное 40 МН 470-61
Уплотнительное кольцо 45
Уплотнительное кольцо 40
Уплотнительное кольцо 36
Уплотнительное кольцо 7
Уплотнительное кольцо 38
Условия сборки: 1. Сборка производится вручную. 2. Покупные детали вынуть из упаковки
провести визуальный осмотр. 3. Изготавливаемые детали промыть в уайт-спирите
продуть сжатым воздухом 4. Установить сборочную единицу поз 9. в корпус поз. 4 с помощью специального интсрумента для исключения повреждения фигурной манжеты острыми кромками проточек в корпусе. 6. Резьбовые соединения поз. 12 перед сборкой покрыть герметиком по ТУ предприятия 6. На отверстия под штуцера установить после сборки установить колпачки защитные из полиэтилена. 7. Плоскости X
Y защитить картонной прокладкой.
л. 9. Мат.модель.dwg

Приведение системы уравнений к виду Коши
Решение уравнения при отсутствии демпфирования и усилия от пробития корки (=0
Решение уравнения при отсутвии усилия от пробития корки (=0
Решение уравнения с усилием от пробития корки
л. 12.Экономика 1.dwg

Капитальные вложения на разработку технической документации
Себестоимость основных материалов
Стоимость покупных изделий
Полная себестоимость изделия
Эксплуатационные издержки
Прибыль от реализации основной продукции
Чистый дисконтированный доход за 5 лет
л. 3. Пневмосхема.dwg

ул. Энгельса - ул. Красной Армии
Автоматизация и диспетчеризация инженерных систем
Фильтр с очисткой 40 мкм
Фильтр с очисткой 1 мкм
Фильтр с очисткой 0.01 мкм
электролизера для выплавки
Компрессорная станция
с электроуправлением
Адсорбционный осушитель
Дроссель регулируемый
л. 6. Дроссель регулируемый.dwg

DIMENSIONS ARE IN MILLIMETERS
Уплотнительное кольцо 16
Дроссель регулируемый
РЕГУЛИРОВОЧНАЯ ХАРАКТЕРИСТИКА ДРОССЕЛЯ
Условия сборки: 1. Сборка производится вручную. 2. Детали промыть в уайт-спирите
продуть сжатым воздухом. 3. Запорно-регулирующий элемент поз. 2 довести до контакта с поверхностью седла поз. 3. После контакта органолептическим способом
отвернуть на 1 оборот. Окончательная регулировка производится на объекте. 4. После окончательной сборки на поверхности Y и Z разместить прокладки из картона. 5. Поместить в полиэтиленовый пакет с последующим ваккумированием. 6. На объекте после проведения установки и отладочных работ
отверстие Х залить герметиком и пломбировать. Работы производятся представителем организации - поставщика
л. 8 Крепление распределителей.dwg

провести визуальный осмотр. 3. Изготавливаемые детали промыть в уайт-спирите
продуть сжатым воздухом. 4. Гибкие шланги поз. 22 продуть сжатым воздухом. 5. К аппаратуре поз. 2
присоединить фитинги. 6. Прикрепить аппаратуру поз. 2
к крепежным элементам поз. 3
и установить на монтажной плите поз. 1. 7. В штуцера вставить гибкие трубопроводы поз. 22. 8. Проверить блок резервирования на работоспособность.
Плита монтажная Ст45
Планка монтажная ДА16
Болт пустотелый ДА16
Болт М5х10 ГОСТ 7805-70
Болт М12х10 ГОСТ 7805-70
Гайка М5 ГОСТ 11871-80
Гайка М12 ГОСТ 11871-80
Шайба 5 ГОСТ 6402-70
Шайба 12 ГОСТ 6402-70
Штуцер 14х6ГОСТ 6172-72
Штуцер 12х6ГОСТ 6172-72
Записка.doc
Государственное образовательное учреждение
высшего профессионального образования
(технический университет)
Кафедра гидромеханики и гидравлических машин
Расчетно-пояснительная записка
Тема дипломного проекта:
ПНЕВМАТИЧЕСКАЯ СИСТЕМА ЭЛЕКТРОЛИЗЕРА ДЛЯ ВЫПЛАВКИ АЛЮМИНИЯ.
Студентка: Задорожная
Руководитель проекта: Зуев Ю.Ю.
(ТЕХНИЧЕСКИЙ УНИВЕРСИТЕТ)
З А Д А Н И Е Н А Д И П Л О М Н Ы Й П Р О Е К Т (работу)
Пневматическая система электролизера для выплавки алюминия.
Фамилия И.О. группа подпись
должность звание Фамилия И.О подпись
Руководитель от предприятия
Содержание задания и исходные данные к проекту (работе)
Современная система электролизера для выплавки алюминия включает в себя пневмопробойник с оптической обратной связью и датчиком касания расплава систему подготовки сжатого воздуха и шкаф управления. Все составляющие системы рассчитаны на тяжелые условия эксплуатации. При этом система нуждается в повышении надежности ресурса работы точности определения положения штока и понижения стоимостных показателей.
Для решения поставленных задач необходимо рассмотреть и выполнить анализ существующих схемо-технических решений систем. Разработать конкурентоспособную систему подготовки воздуха очистки сжатого воздуха до необходимого класса с учетом внешних вредных факторов. Рассмотреть способ позволяющий определять положения штока.
Исходные данные таковы: в электролизер устанавливается 6 цилиндров пробойников. Диаметр поршня 200 мм ход поршня 400 мм рабочее давление 2-10 бар. Максимальное давение 10 бар. Температурное исполнение пневмоцилиндров пробойника -40 +120 С (кратковременное до +150 С). Сжатый воздух для пневмоцилиндров не грубее 5.7 класса(по DIN ISO 8573). Пневмораспределители и управляющую аппратуру пробойников размесить в металлическом шкафу. Температурное исполнение шкафа -40 +120 С.
Необходимо предложить несколько вариантов структур данных систем (пневматические схемы способы компоновки) выполнить необходимые расчеты. разработать необходимые чертежи составить математическую модель выполнить расчет экономической эффективности проекта. Рассмотреть экологическую безопасность использования пневмоситемы.
(специализированная часть проекта)
График работы по разделам дипломного проекта (работы)
Анализ исходного задания. Подбор и систематизация информации о системе подготовки воздуха цилиндра-пробойника и шкафе управления. Формирование массивов показателей работоспособности конкурентособности входных ресурсов и дестабилизирующих факторов. Анализ ПК на конфликтность
Написание реферативной главы проекта. Формирование технического задания на проект
Составление матрицы структурных решений по компоновке и системам пневмопривода. Разработка обобщенных критериев эффективности схемных и конструкционных решений. Выбор предпочтительной структуры системы подготовки воздуха.
Разработка принципиальных вариантов пневматических схем для предпочтительной структуры. Оценка схем и выбор выигрышного решения по совокупности ПК и ПР. Оформление структурного синтеза.
Разработка математической модели. Расчет основных характеристик. Параметрическая оптимизация. Подбор пневматических устройств. Формирование спецификации.
Разработка устройства. Выполнение необходимых расчетов.
Оформление конструкторских листов проекта и главы параметрического синтеза.
Выполнение технологической части проекта
Выполнение экономической части проекта
Выполнение главы раздела по экологической чистоте охране труда и безопасности жизнедеятельности
Написание заключения по выполненной работе
Оформление графической части проекта и расчетно-пояснительной записки
Поучение отзыва на проект у рецензента
Написание текста выступления. Подготовка к защите
Перечень графического материала
Лист 1 – Анализ ИЗ для выполнения дипломного проекта; лист 2 – Таблица выбора оборудования для подготовки сжатого воздуха; лист 3 –Принципиальная пневматическая схема; листы 4–8 – Сборочные чертежи лист 9–Математическая модель; листы 10–11 – технологическая часть проекта; лист 12 – экономическая часть проекта;
Половинкин А.И. Основы инженерного творчества. – М.: Машиностроение 1988.
Слюсарев А.Н. Гидравлические пневматические элементы и приводы промышленных роботов: Учебник. – М.: Машиностроение 1989.
Гидроприводы и гидропневмоавтоматика станков В.А. Федорец М.Н. Педченко А.Ф. Пичко Ю.В. Пересадько В.О. Лысенко; Под ред. В.А. Федорца. – Киев: Вища школа. Головное изд-во 1987.
Башта Т.М. Объёмные насосы и гидравлические двигатели: Учебник. – М.: Машиностроение 1989.
Герц Е.В. Крейнин Г.В. Расчёт пневмоприводов: Справ. Пособие. – М.: Машиностроение 1975.
Дмитриев В.Н. Градецкий В.Г. Основы пневмоавтоматики. – М.: Машиностроение 1973.
Моль Р. Гидропневмоавтматика: пер. с фр. – М.: Машиностроение 1975.
Пневматические устройства и системы в машиностроении: справочник Под ред. Е.В. Герц. – М.: Машиностроение 1981.
Элементы и устройства пневмоавтоматики высокого давления: Каталог Под ред. А.И. Кудрявцева и А.Я. Оксененко. – М.: НИИМАШ 1982.
Пневмопривод систем управления летательных аппаратов В.А. Чащин О.Г. Камладзе А.Б. Кондратьев и др. – М.: Машиностроение 1987.
Гликман Б.Ф. Математические модели пневмогидравлических систем. – М.: Наука. Гл. ред. физ.-мат. лит. 1986.
Иринг Ю. Проектирование гидравлическихи пневматических систем. – Л.: Машиностроение. Ленингр. отд-ние 1983.
Пневмогидравлические системы. Расчёт и проектирование: Учеб. пособие Н.М. Беляев Е.И. Уваров Ю.М. Степанчук; Под ред. Н.М. беляева. – М.: Высш. шк. 1988.
Монтаж наладка и эксплуатация пневматических приводов и устройств А.И. Кудрявцев А.П. Пятидверный Е.А. Рагулин. – М.: Машиностроение 1990.
Краткие сведения о дипломнике:
Реферативный обзор16
1.Особенности подготовки сжатого воздуха в настоящее время16
2.Особенности оборудования для пневматической системы электролизера17
Формирование пневматической схемы работы электролизера22
1.Формирование показателей качества – функциональной пригодности и конкурентоспособности22
2.Морфологический метод25
3.Определение класса загрязнения сжатого воздуха26
4.Расчет расхода системы26
5.Структурный анализ системы подготовки сжатого воздуха29
6.Рассмотрение способов определения положения штока49
7.Описание пневматической схемы50
Определение параметров системы52
1.Определение производительности компрессора. Выбор52
компрессора на рассчитанные параметры52
2.Выбор оборудования на рассчитанные параметры55
Математическое моделирование движения штока цилиндра пробойника58
1.Основные периоды в работе пневмоцилиндра.58
2.Описание работы пневмоцилиндра при прямом ходе60
3.Математическая модель движения штока пневмоцилиндра.61
4.Численное решение математической модели движения пневмоцилиндра67
4.1.Решение математической модели при отсутствии68
4.2.Решение математической модели при существовании алюминиевой корки79
Описание и расчеты конструкции82
1.Распределитель с пневматическим и ручным управлением82
2.Регулируемый дроссель85
Оценка экономической эффективности применения пневматической системы электролизера для выплавки алюминия88
1.Технико-экономическое обоснование применения способа88
определения положения штока88
2.Расчеты затрат на проектирование способа89
определения положения штока89
3.Расчет затрат на изготовление устройств92
для определения положения штока.92
4.Расчет затрат на эксплуатацию пневмосистемы.97
5.Расчет экономической эффективности.99
Экологичность и безопасность102
1.Общие положения102
2.Метеорологические условия производственной среды103
(температура воздуха относительная влажность воздуха скорость движения воздуха интенсивность103
теплового излучения)103
3.Вредные химические вещества в производстве105
4.Шум на производстве106
5.Вибрация в производстве108
6.Электромагнитные электрические и магнитные поля в производстве110
7.Пожаробезопасность на предприятии112
9.Действие электрического тока на работу человека на промышленных предприятиях115
10.Очистка отходящих газов от электролизера117
11.Техника безопасности работы с компрессорами высокого давления121
Технология сборки шкафа управления130
Список литературы142
Список основных обозначений
Число допустимых циклов вклвыкл
Термодинамический эквивалент работы
Скорость распространения звука в воздухе
Диаметр дросселя во входной линии
Диаметр дросселя в выходной линии
Диаметр трубопровода
Площадь поршневой полости
Площадь штоковой полости
Площадь сечения трубы
Расход сжатого воздуха
Ускорение свободного падения
Вводимый коэффициент
Показатель политропы
Удельный массовый расход воздуха
Удельная масса воздуха
Сила сопротивления давлению
Циклический дифференциал давления
Гидравлический радиус сечения канала
Удельное количество тепла
Производительность компрессора
Удельная газовая постоянная
Оцениваемый размер резервов
Абсолютная температура по Кельвину
Внутренняя энергия идеального воздуха
Удельная внутренняя энергия идеального воздуха
Удельный объем воздуха
Оцениваемый размер утечек
Скоростной поток газа
Скорость течения воздуха в резервуаре
Координата сечения трубы или цилиндра
Координата минимального
поступающего в полость воздуха
вытекающего из полости воздуха
Удельный вес воздуха
Коэффициент сопротивления
Коэффициент трения в трубе
Коэффициент рассхода
Отношение давления среды
Критическое отношение
Коэффициент относительно
Коэффициент демфирования
Нет ни одной отрасли промышленности которая которая бы так или иначе не пользовалась алюминием и его сплавами. Основные достоинства алюминия в качестве конструкционного материала — лёгкость податливость штамповке коррозионная стойкость (на воздухе алюминий мгновенно покрывается прочной плёнкой Al2O3 которая препятствует его дальнейшему окислению) высокая теплопроводность неядовитость его соединений[25]. Благодаря всем этим свойствам алюминий широко применяется в аэрокосмической индустрии в машиностроении при производстве автомобилей вагонов скоростного метро морских судов в современном строительстве при производстве посуды банок для напитков и т.д.[26].
Датой рождения алюминиевой промышленности России считается 14 мая 1932 года когда на Волховском заводе в Ленинградской области была получена первая партия алюминия. После этого в течение 7 лет были введены в эксплуатацию Днепровский алюминиевый Тихвинский глиноземный завод и Уральский алюминиевый завод [27].
Во время Великой Отечественная войны основное оборудование Волховского и Тихвинского заводов было демонтировано и вывезено на Урал и в Западную Сибирь где его использовали для строительства Богословского и Новокузнецкого алюминиевых заводов которые были запущены соответственно в 1945 и 1943 годах.
В послевоенные годы потребности советской экономики в стратегической металлопродукции продолжали расти что способствовало интенсивному развитию алюминиевой промышленности. В 50-е годы были введены в эксплуатацию Кандалакшский (1951 г.) Надвоицкий (1954 г.) и Волгоградский (1959 г.) алюминиевые заводы а также Белокалитвинское металлургическое производственное объединение (БКМПО 1954 г.) специализирующееся на выпуске различной продукции из алюминиевых сплавов. В 1960 г. состоялся пуск Самарского металлургического завода – крупнейшего в Европе производителя полуфабрикатов и готовых изделий из алюминия.
В 60-е и 70-е годы XX века в непосредственной близости от крупнейших ГЭС – источников дешевой электроэнергии – были построены Иркутский Красноярский и Братский алюминиевые заводы. В этот же период были введены в эксплуатацию Красноярский металлургический завод Павлодарский алюминиевый завод и Дмитровский опытный завод алюминиевой консервной ленты.
В 1985 году вступил в строй Саяногорский алюминиевый завод оснащенный современными технологиями и оборудованием. В 1995 году начал работать завод «Саянская фольга» – крупнейший в России производитель алюминиевой фольги и упаковочных материалов на ее основе.
В 1996 году Создана Сибирско-Уральская алюминиевая компания в результате объединения акционерных капиталов Иркутского и Уральского алюминиевых заводов. С 1996 – 2006 года компания РУСАЛ начала объединение алюминиевых заводов страны. В 2006 году подписано соглашение о создании Объединенной компании United Сompany RUSAL путем слияния алюминиевых и глиноземных активов Компании РУСАЛ занимавшей третье место в мире по производству алюминия группы СУАЛ входившей в десятку ведущих мировых производителей алюминия и швейцарской компании Glencore. (Все заводы принадлежащие United Сompany RUSAL см. в прилож. 1) [27]. На сегодняшний день United Сompany RUSAL производится 415 млн. т. алюминия в год что составляет 12% мирового рынкаалюминия (см. прилож. 1).
В настоящее время ведутся подготовительные работы по возведению алюминиевого завода в Иркутской области (Тайшетского Алюминевого завода). Запланированный срок завершения строительства – 2011 год. В мае 2006 года компании РУСАЛ и «ГидроОГК» подписали соглашение о сотрудничестве в совместной реализации проекта по созданию Богучанского энергометаллургического объединения (БЭМО). Проект БЭМО включает в себя завершение строительства Богучанской ГЭС установленной мощностью 3000 МВт на реке Ангаре и сооружение алюминиевого завода мощностью 600 тыс. т. в год [27].
Алюминиевая промышленность развивается и основной задачей является модернизация оборудования и автоматизация технологических процессов получения алюминия.
Алюминий получают электролитическим восстановлением окиси алюминия растворенной в расплаве на основе криолита (редкий минерал из группы природных фторидов химический состав Na3AlF6.). Процесс проходит при температуре 950-970°С. Электролизер (см. рис. 1.1) состоит из футерованной углеродистыми блоками ванны к подине (нижней части горизонтального ограждения печи формирующей ванну для жидкого металла) которой подводится электрический ток. Выделившийся на подине служащей катодом жидкий алюминий тяжелее расплава соли электролита поэтому он собирается на угольном основании откуда его периодически откачивают.
Криолитоглиноземный расплав
Ванна из стального листа
Рис.1.1. Схема электролизной ванны
Сверху в электролит погружены угольные аноды которые сгорают в атмосфере выделяющегося из окиси алюминия кислорода выделяя окись углерода (CO) или двуокись углерода (CO2).
В результате происходящего процесса на поверхности электролита образуется оксидная корка разрушение которой осуществляется с помощью специального пробойника приводимого в действие пневмоприводом. Питание пневмосистемы осущестляется осушенным сжатым воздухом. Глинозем добавляется в образовавшееся отверстие с помощью цилиндров дозаторов (рис. 1.2 рис. 13).
Рис.1.2. Схема применения пробойников
При пробитии корки пробойник опускается в электролит вследствие чего происходят два нежелательных явления: попадание примесей в расплав и образование так называемой «слоновьей ноги» (нароста металла напробойнике) (см. рис. 1.4)
Рис. 1.3. – Цилиндр-пробойник Рис. 1.4. – Образование слоновьей ноги.
Существует два способа подачи глинозема: ручной и автоматический. Ручная подача глинозема питания алюминиевых электролизёров основана на растворении глинозёма в объёме электролита при поточно регламентированных обработках ванны с периодичностью колеблющейся на разных заводах от 6 до 12 раз в сутки. При этом после каждой обработки на длительное время нарушается тепло- и массообмен в электролизёре что приводит к значительному снижению эффективности электролиза. При периодичности обработки 6-12 раз в сутки электролизёр фактически 3-6 часов в сутки работает в нестабилизированном режиме с низкими технико-экономическими показателями. Технология автоматического питания электролизёров глинозёмом (АПГ) также основана на его растворении в объёме электролита. Однако объём порции глинозёма погружаемой в электролит с помощью специальных питателей сведён до минимума а частота подачи существенно увеличина. Глинозём в электролит поступает за счёт растворения его порции погружаемой в электролит[28].
Для обеспечения современного процесса получения алюминия необходимо переходить к АПГ но совершенствование системы связано с решением различных задач: обеспечение бесперебойной работы электролитных ванн увеличение производительности металла уменьшение выбросов вредных соединений в атмосферу и время нахождения обслуживающего персонала в цехах. При внедрении системы АПГ требуется использовать для пробития корки цилиндры – пробойники а для добавления солей – цилиндры дозаторы. Необходимо автоматизировать работу системы что позволит определять положение расплава уменьшать эффект «слоновьей ноги» а также обеспечивать бесперебойный подвод сжатого воздуха очищенного до требуемого класса к цилиндрам за счет введения системы резервирования и диагностики.
По этим причинам темой дипломной дипломного проекта была выбрана: «Пневматическая система электролизера для выплавки алюминия»
в которой предполагается рассмотреть систему подготовки сжатого воздуха и способ определения положения штока по параметрам системы (составление математической модели) подобрать необходимую аппаратуру и укомплектовать ей шкаф управления. Цилиндр дозатор в дипломном проекте не рассматривается.
При рассмотрении системы подготовки воздуха необходимо обеспечить бесперебойную подачу сжатого воздуха отвечающего требованиям работы цилиндров. Рассмотреть возможность применения индивидуальной системы питания электролитных ванн.
Дипломный проект состоит из глав: реферативный обзор формирование пневматической схемы электролизера определение параметров системы математическое моделирование движения штока цилиндра пробойника описание и расчеты конструкции экономическая часть экологическая часть и технологическая часть.
1. Особенности подготовки сжатого воздуха в настоящее время
Подготовка сжатого воздуха заключается в доведении качественного сжатого воздуха поставляемого компрессорной станцией до уровня требуемого его потребителями. Подготовку можно разделить на три стадии: предварительная фильтрация осушка и окончательная фильтрация [21].
При использовании нескольких уровней качества воздуха экономически целесообразнее готовить «лучший» воздух перед соответствующим потребителем. При необходимости в разных давлениях обычно используют локальные усилители давления. Присоединение устройств осуществляют используя технику защелкивания с фиксаций. При проектировании необходимо рассматривать диагностику системы с помощью которой возможно избежать простоев оборудования [7].
В систему подготовки сжатого воздуха входят следующие элементы:
компрессор (машина для повышения давления и перемещения газа) или компрессорная установка (совокупность компрессора привода и вспомогательного оборудования);
охладитель (необходим для понижения температуры сжатого воздуха);
ресивер (устройство обеспечивающее постоянство питания пневматического оборудования);
кондесатоотводчик (служат для удаления влаги);
осушитель (предназначены для понижения точки росы путем изменения давления давления или темперауры);
фильтры (элемент пневмосистемы для очистки воздуха).
Очищенный воздух поступает к цилиндрам пробойникам.
2.Особенности оборудования для пневматической системы электролизера
Для пробития корки в электролитных ваннах должно использоваться оборудование которое функционирует при сочетании неблагоприятных факторов к числу которых относятся:
Широкие диапазоны рабочих температур -40+120 C (кратковременно до +150 C);
Сильное магнитное поле;
Загрязненная окружающая среда (оксид углерода пыль а также различные фтористые соединения).
Для таких условий работы целесообразным является применение пневмосистем [2].
На современном рынке установкой этих систем занимаются следующие фирмы: Festo SMC и Parker. Каждая фирма использует различные пневмоцилиндры и устройства для системы подготовки воздуха. Рассмотрим основные особенности данных конструкций:
Фирмой SMC используются цилиндры пробойники серии CS1(см. прилож. 2) подвижные поверхности которых спроектированы так чтобы снизить износ трущихся частей до минимума. Все пневматические комплектующие предварительно смазаны специальной консистентной фторсодержащей смазкой для высоких температур. Она предохраняет поверхности трения от износа и не требует замены в течение нескольких лет [28]. Применяются пневмораспределители серии VS (см. прилож. 2). Данные распределители имеют прямое управление без пилотного клапана (золотник перемещается непосредственно мощным электромагнитом). Такая особенность конструкции в сочетании со стальным уплотнением золотника который притерт к гильзе обеспечивает надежную работу даже в тяжелых условиях эксплуатации. Для очистки воздуха используется фильтры серии АFF с увеличенным ресурсом работы. (см. прилож. 2). Магистральный фильтр серии AFF обеспечивает комплексную очистку сжатого воздуха удаляя 99% водяного конденсата 97% компрессорного масла и твердые частицы размером более 3 мкм. За счет увеличенной эффективной фильтрующей поверхности многослойный картридж фильтра AFF создает минимальные потери давления даже на сжатом воздухе с высокой степенью загрязнения. Он применяется для предварительной очистки воздуха в магистрали электролизного корпуса (пропускная способность до 42 м3мин) а также в качестве фильтра окончательной очистки на электролизере [20].
В цилиндрах фирмы Parker также используются специальные смазки для пар трения уменьшающие износ трущихся частей. Пневмоцилиндры не нуждающиеся в дополнительном смазывании имеют эффективную защиту против пыли (глинозема) и рассчитаны на срок службы около 20 лет. Поршень и пробойник сделаны из укрепленного самосмазочного материала PTFE с графитом (см. прилож. 7) [29].
При установки оборудования на алюминиевых заводах фирмой Festo используются пневмоцилиндры-пробойники DI-200-400-PPV-SA (см. прилож. 4). В этих цилиндрах применяется материал PTFE с добавками графита не требующий смазки (из такого материала делается направляющая втулка) применяются комбинационные манжеты из витона (см. прилож. 7) для надежной работы в условиях высоких температур и запыленности также используются специальные уплотнения для обеспечения увеличенного пути регулирования демфирования в конце хода (см. прилож. 2) [20]. Применяют распределители типа МD-52 в которых система уплотнений представляет собой притертую стальную пару (уплотнение металл-металл). Распределители имеют мощное прямое электромагнитное управление и температурный диапазон применения от -40 до +120С. Возможен вариант с пневматическим управлением с температурным диапазоном -40 +150 С.
На российских заводах в основном применяется оборудование фирмы Festо. Особенности пневмосистем производимых этой фирмой описаны ниже в хронологическом порядке:
Изначально требовалось пробитие алюминиевой корки осуществляемое за счет пневмоцилиндра. Для этого использовались стандартные цилиндры-пробойники и распределитель (исполнение такого цилиндра показано на рис. 1 прилож. 5). Для предотвращения опускания штока вниз в аварийной ситуации в систему был введен обратный клапан позволяющий удерживать шток в поднятом состоянии (исполнение цилиндра рис. 2 в прилож. 5). Для оптимизации работы пневмосистемы (определение крайних положений штока) в передней и задней крышках были встроены пневмо-механические концевые выключатели. Встроенные датчики не чувствительные к магнитным полям и высоким температурам позволяют надежно определить положение поршня в конечном положении (исполнение цилиндра см. рис. 3 в прилож. 5). Так же были пущены в эксплуатацию пневмосистемы с электро-механическим концевым выключателем (24230 В) (исполнение цилиндра см. рис. 4 в прилож. 5).
Для устранения нежелательных последствий возникающих из-за попадания пробойника в расплав и точного определения разрушения корки был поставлен электрический датчик. Система с этим датчиком имеет следующий принцип работы: как только шток с пробойником коснется расплава сигнал в 350 мВ через интегральный контакт подается на контроллер системы и происходит возврат поршня в исходное положение.
Для уменьшения потребляемого воздуха устанавливаются блоки экономии воздуха (исполнение цилиндра см. рис. 56 в прилож. 5). Работа которых основана на возникновении высокого давления в момент пробития корки и в период вытягивания штока из расплава. При отсутствии нагрузок движение происходит при пониженном давлении.
По технологическим требованиям появилась необходимость определять положение расплава электролита. Сделать это можно с помощью цилиндра пробойника при применении системы позиционирования. В настоящее время запатентован (см. прилож. 6) и внедряется в эксплуатацию пневмоцилиндр с обратным датчиком обратной связи (исполнение цилиндра см. рис. 7 в приложение 2). Встроенный датчик обратной связи по положению поршня не чувствительный к магнитным полям и высоким температурам позволяет определять положение поршня в любой момент времени.
В настоящее время цилиндры-пробойники востребованы в промышленности но нуждаются в доработке способы определения положения штока цилиндра. В системе подготовки воздуха необходимо вводить диагностику и резервирование (избежание простоя оборудования при смене фильтра). Исходя из этих выводов основными задачами при проектировании системы управления пневмоцилндров-пробойников являются:
Гарантировать поступление к потребителям воздуха требуемого класса необходимого по количеству и требуемому давлению.
Обеспечить бесперебойную подачу сжатого воздуха за счет внедрения системы резервирования.
Рассмотреть применение индивидуального питания электролизеров.
Разработать способ определения положения штока с наименьшими затратами и небольшой погрешностью.
Выбрать шкаф управления и обеспечить размещение в нем оборудования.
В соответствии с поставленными задачами необходимо:
Выбрать по критериям качества и работоспособности оптимальную схему подготовки воздуха рассмотрев возможные варианты. Для данного решения следует произвести необходимые расчеты и подобрать соответствующее оборудование. При необходимости - сконструировать модифицированные детали и узлы.
Сформировать математическую модель с помощью которой возможно получать информацию изменения хода от времени изменение давления в поршневой и штоковой полости от времени.
Разместить оборудование в шкафу управления.
Описать технологию сборки шкафа управления.
Определить экономическую эффективность метода определения положения штока по косвенным показателям.
Описать экологические факторы влияющие на здоровье людей при работе с пневматической системой на алюминиевом заводе. Описать безопасную эксплуатацию компрессоров высокого давления.
ФОРМИРОВАНИЕ ПНЕВМАТИЧЕСКОЙ СХЕМЫ РАБОТЫ ЭЛЕКТРОЛИЗЕРА
При рассмотрении системы подготовки сжатого воздуха для правильного выбора оборудования необходимо рассчитать потребляемый расход определить требуемое давление и обеспечить заданный класс загрязненности сжатого воздуха.
В цехе может быть установлено до 100 электролизеров. Питание оборудования обычно осуществляется централизованно за счет компрессорных установок. В случае аварийной ситуации из строя может выйти весь цех. Если же установить индивидуальное питание электролизеров то таких последствий можно избежать. При индивидуальном питании компрессорное оборудование проще в настройке и более ремонтопригодно. Поэтому в дипломном проекте рассмотрим питание электролитной установки индивидуальной компрессорной станцией. Связи с изменением типа питания электролизера изменяется компоновка оборудования для очистки сжатого воздуха. Поэтому необходимо рассмотреть подготовку сжатого воздуха с момента засасывания компрессором до подачи к пробойникам.
1.Формирование показателей качества – функциональной пригодности и конкурентоспособности
При выполнении работы воспользуемся системно-креативным подходом который является эффективным методом определения конкурентоспособности изделия. Базовые исходные положения данного подхода заключаются в следующем:
Любая техническая система существующая в жизненной среде на протяжении своего жизненного цикла характеризуется ресурсным (энергетическим и (или) информационным и (или) вещественным) обменом с жизненной средой что представляется устойчивой и инвариантной к конкретной ТС совокупностью трёх многомерных массивов [23]:
G – массив входных регламентированных (ресурсных или условно полезных факторов) имеющий вид G = g1 g2
F – массив входных (внешних) нерегламентированных (дестабилизирующих) факторов определяемых как F = f1 f2
Y – массив выходных показателей (показателей качества) имеющий вид Y = y1 y2 yn
Компоненты массива Y можно разделить на 3 группы: показатели работоспособности Yр (определяют функциональную пригодность системы для выполнения требуемых жизненной средой «обязанностей» на протяжении заявленного жизненного цикла [15]) показатели конкурентоспосбности Yк (характеризуют степень совершенства обеспечения технической системой компонента подмассива Yр [15]) и побочные показатели Yп (незаявленный факторы воспринимающиеся как вредные [15]).
Факторы G и F существуют в окружающей среде вне зависимости от существования технической системы показатели Y возникают в среде потому что в ней появилась ТС. Схематически это изображено на рис. 3.1.
Рассмотрим систему подготовки воздуха как сложную техническую систему содержащую ряд элементов взаимосвязанных структурно и функционально.
Рис. 3.1. Факторы действующие на систему
Исходя из требований к системам описанным в п. 2.2 введем показатели работоспособности конкурентоспособности и побочные показатели.
Показатели работоспособности:
yр1 – содержание твердых частиц;
yр2 – содержание масла;
yр3 – значение точки росы;
yр4 – способность автоматического отвода конденсата;
Показатели конкурентоспособности:
yк1 – надежность (является интегративным показателя включающим в себя четыре составляющие: долговечность безотказность ремонтопригодность сохраняемость. При надежной работе устройство должно выполнять все заданные функции сохраняя во времени значения установленных показателей в заданных пределах соответствующих заданным режимам и условиям использования технического обслуживания ремонтов и транспортирования.)
yк1б – безотказность
yк1р – ремонтопригодность
yк3 – осуществление диагностики системы;
yк4 – резервирование системы;
yк5 – необходимость дополнительного охладителя;
yк7 – простота констукции;
yк8 – простота обслуживания;
yк9 – самовостановимость расходного материала(показатель используется для осушителей см. далее).
Побочные выходные показатели:
Внешние возмущающие факторы:
f1 – сильное магнитное поле
f2 – большой перепад температур
f3 – высокая запыленность
По показателям конкурентоспособности выбирается наилучшее решении.
2.Морфологический метод
Один из способов выбрать из множества различных вариантов наиболее подходящий – морфологический метод (метод Ф. Цвикки). Данный метод применяется когда известны принципиальные способы сочетания частей целого и возможные исполнения данных частей. Данные исполнения частей должны быть функционально равноценными (или почти равноценными) т.е. принципиально взаимозаменяемыми но могут различаться какими либо существенными по отношению к целому характеристиками оценивающими степень совершенства выполнения частями требуемых функций [23]. При поиске новых технических решений формируются морфологические таблицы. Преимуществом метода является то что он позволяет образовывать и рассматривать все множества возможных решений и при этом работать с числовыми значениями что увеличивает точность оценки решения [24].
3.Определение класса загрязнения сжатого воздуха
По техническому заданию необходимо обеспечить 10 класс загрязненности по ГОСТ 17433-80 (см. прилож. 8) и не грубее 5.7 класса загрязненности ISO 554 (см. прилож. 8). Очищенный воздух должен иметь степень фильтрации 5 мкм влагоотделение должно составлять 99% точка росы -40 С.
4.Расчет расхода системы
Расход воздуха необходимый для питания пробойников определяется следующим образом. Учитывается что стандартная температура воздуха составляет 20°С атмосферное давление 1 атм. и относительная влажность 36%. Расчет возможных объемов подачи проводится на стандартные условия. Повышение температуры воздуха на 5-6°С влечет снижение подачи примерно на 2%. Например в летнее время или в помещении при температуре воздуха 37 °С объем подаваемого воздуха уменьшается на 6% по сравнению с расчетной производительностью. Поэтому компрессор должен быть установлен в холодном помещении или у окна где существует хорошая циркуляция воздуха вокруг установки.
При расчете вводится понятие удельного потребления воздуха которое представляет массу воздуха которую необходимо подать чтобы поршень совершил ход 1 мм. Это величина зависит от рабочего давления и диаметра цилиндра и ее можно получить по диаграмме рис. 3.2 [21]. Удельная масса воздуха показана там в функции рабочего давления и диаметра поршня. Для двойного хода поршня :
где - ход - удельный массовый расход воздуха.
После того как определена масса потребляемого воздуха можно посчитать стандартный объем воздуха :
где – стандартный объем - плотность воздуха.
Рис. 3.2. Диаграмма для определения потребления воздуха
пневматическими цилиндрами
Цилиндр пробойник. По техническому заданию диаметр поршня цилиндра составляет 200 мм ход H=400 мм. Максимальное давление 10 бар. Общее время перемещения равно 55 с.
Используя эти исходные данные по диаграмме определяется удельное потребление воздуха рассчитывается удельный массовый расход воздуха по формуле (3.1) и стандартный объем по формуле (3.2):
Пропускная способность устройств рассчитывается по следующей формуле:
Расход компрессора (из условия что в минуту пробойник совершает один двойной ход) определяется исходя из объема потребляемого одним пробойником за двойной ход и числа пробойников (см. формулу (3.3)):
где - количество пробойников тогда
Цилиндр дозатор. По условию диаметр поршня данного цилиндра равен 100 мм рабочее давление цилиндра составляет 10 бар ход поршня 125 мм.
По диаграмме рис. 3.2. определяется удельное потребление воздуха кгмм хода рассчитывается потребление воздуха за двойной ход по формуле (3.1) и по (3.2) определяется стандартный объем:
Рассчитаем расход компрессора (из условия что в минуту цилиндр совершает один двойной ход а число пробойников равно 9):
Общий расход определяется следующим образом:
5.Структурный анализ системы подготовки сжатого воздуха
Работа системы начинается с засасывания воздуха в компрессор где он нагревается до 65-260°С в зависимости от типа компрессора и рабочего давления. На основании результатов п. 3.4. и учитывая что максимальное давление потребителя 10 бар используя таблицу 12.1 в прилож. 12 выбираем походящий тип компрессора. Для заданных условий подходят винтовые и поршневые(плунжерный и крейцкопфный) компрессоры. Детальное сравнивание выбранных типов компрессоров и результаты анализа сведены в табл. 3.1.
Поршневой компрессор
Низкая стоимость. По сравнению с винтовым той же производительностью ниже на 20-40%. Дополнительные затраты на монтаж. (Необходим специальный фундамент)
поршневых. Установка проста.
Низкий КПД. Высокие затраты
Имеет высокий КПД (сжатие воздуха
происходит непрерывно температура
нагнетаемого воздуха
меняется незначительно характеристика процесса сжатия максимально
к изотерме). За счет этого экономия
производительности за счет чего вырабатывается
необходимое количество сжатого воздуха
Расходные материалы. Ремонт и техническое обслуживание
Частая замена клапанов поршневых колец и т.д.
Механическая часть не содержит быстро
давления что приводит к необходимости
установления ресиверов больших размеров
Не создает пульсаций давления
Содержание масла в воздухе
В сжатом воздухе масло не содержится
Необходимы перерывы в работе
Остановы нежелательны
Низкая срок службы до капитального ремонта 12500 часов
Высокая срок службы около 40000 часов
Конструктивное исполнение
Воспользовавшись данными в табл. 3.1 с помощью метода морфологического анализа сопоставим поршневой и винтовой компрессоры. Сравнение основано на том что каждому показателю качества выставляется соответствующее число в пределах от 0 до 1 при этом 0 – это лучшее решение а 1 – худшее.
Надежность поршневого компрессора низкая и поэтому она соответствует –1. Винтовой компрессор имеет более высокую надежность и показателю качества данного свойства этой машины присваивается значение 0.
При оценке стоимостного показателя необходимо учитывать закупочную стоимость затраты на установку и дальнейшее обслуживание. По совокупности этих показателей целесообразней устанавливать винтовые компрессоры.
В обслуживании более просты поршневые компрессоры т.к. винтовые содержат более сложную систему смазки и охлаждения.
Условимся что значимость всех показателей равноценна и поэтому весовые коэффициенты не вводятся. Полученные решения сведем в табл. 3.2.
В результате проведенного анализа получили что целесообразней использовать винтовой компрессор.
После компрессора воздух необходимо охладить для этого используются холодильники.
Охладители применяются для первичного удаления (60-70%) влаги из сжатого воздуха и понижения температуры (до 30-50 С). Их делят на две группы по типу охлаждения: воздушного и водяного.
В охладителях водяного типа понижение температуры достигается за счет циркуляции холодной воды. Охладитель обычно устроен по принципу "труба в трубе". Внутри большой трубы расположены маленькие трубки по которым проходит сжатый воздух а по большой трубе подается холодная вода. Собравшийся конденсат отводится автоматически с помощью поплавковой системы. Несмотря на довольно простую конструкцию охладители водяного типа менее популярны так как болеегромоздки и требуют подвода воды.
На основании этих соображений присвоим показателям качества соответствующие значения и покажем в табл. 3.3.
Просуммировав значения показателей получаем что лучшим вариантом является воздушный охладитель.
После холодильника для правильной работы постоянного питания устанавливается ресивер. Он выполняет следующие функции:
компенсации колебаний давления на выходе компрессора;
компенсации колебаний расхода и кратковременных пиков потребления;
аварийного питание в случае потери энергии;
экономии энергии за счет сокращения числа включений компрессоров и усилителей давления.
В ресивере происходит охлаждение сжатого воздуха. Образовавшийся вследствие этого конденсат необходимо отводить с помощью конденсатоотводчиков [21].
Ручные дренажные краны - это простейшее устройство для слива конденсата. Обычно ручные дренажные краны выполнены в виде шаровых кранов размещенных в точке слива конденсата. Предполагается что обслуживающий персонал регулярно проверяет уровень конденсата и сливает его вручную открывая кран.
Поплавковое устройство отвода. Отвод управляется уровнем конденсата (см. рис. 3.3). При всплывании сферического поплавка открывается клапан давления и конденсат вытесняется наружу.
Рис.3.3. Поплавковый конденсотооводчик
Клапан с ручным управлением
Клапан с коническим седлом
Отвод с электронным управлением. При таком способе отвода емкостной датчик подает сигнал когда уровень конденсата достигает максимальной отметки. Клапан открывается с помощью электроуправления. Конденсат выдувается в трубу давлением воздуха (см. рис. 3.4).
Диафрагменный клапан
Рис.3.4 Отвод конденсата с электронным управлением
Отвод с помощью электромагнитного клапана и реле времени. При таким способе отвода конденсата клапан открывается через определенные промежутки времени которые настраиваются с помощью реле давления.
Основные особенности преимущества и недостатки конденсатоотводчиков сведем в табл. 3.4.
количество конденсата
конденсатосборник имеет значительный объем.
Невысокая стоимость;
Максимально простая конструкция;
Самый надежный тип устройств для отвода конденсата;
Необходимо вручную сливать конденсат;
Отсутствие функции подачи сигнала
Применим для случая когда количество конденсата немного
Поплавковое устройство отвода
Работают автоматически без вмешательства
Надежность их работы
зависит от кострукции и качества исполнения т.к. заклинивание поплавка в нижнем положении влечет за собой прекращение
отвода конденсата а в верхнем положении
постоянное стравливание сжатого воздуха;
Нуждаются в регулярных инспекциях и в случае
Максимально простая конструкция;
Высокая потребность в контроле за работой;
Отсутствие функции подачи сигнала
Отвод с электронным управлением
Надежный отказоустойчивый принцип работы;
Совмещают в себе надежность слива конденсата контроль за уровнем конденсата и исключение потерь сжатого воздуха.
Отсутствие потерь сжатого воздуха;
удаленной его передачи.
Требуют наличия электропитания;
При вязком а также сильно загрязненном твердыми частицами конденсате
существует опасность заклинивания
твод с помощью электромагн. клапана и реле времени.
надежными изо всех видов автоматических
конденсатоотводчиков.
Самые надежные автоматические
конденсатоотводчики;
Простая конструкция;
Существуют версии на высокие давления (до 350 бар)
На основании табл. 3.4 введем значения показателей качества. При рассмотрении надежности из-за отсутствия сложности в конструкции и безотказной работы лучим решением является ручные дренажные клапана. Наихудшим решением является поплавковое устройство отвода (см. особенности применения в табл. 3.4). Стоимость определяется по каталогам.
Рассматривая простоту конструкции необходимо отметить что наиболее простая конструкция у ручных дренажных кранов. Далее по простоте можно поставить поплавковое устройство отвода. Наиболее сложной конструкцией является отвод электронным управлением. Эти данные внесем в табл. 3.5.
Ручные дренажные краны
Отвод с помощью электромагнитного клапана и реле времени
По табл. 3.5. лучшими вариантами являются: ручные дренажные клапаны и отвод с электронным управлением. При автоматизированной системе управления подготовкой воздуха будем использовать отвод конденсата с электронным управлением.
После прохождения ресивера воздух нуждается в осушении. Осушители бывают рефрижераторные мембранные адсорбционные и абсорбционные.
Рефрижераторный осушитель. Принцип работы осушителя заключается в том что воздух охлаждается противоположным потоком хладагента в несколько этапов (предварительный: воздух-воздух; главный: воздух-хладагент). Образовавшийся при этом конденсат отводится (см. рис. 3.5).
Вход сжатого воздуха
Возвратный трубопровод
Выход сжатого воздуха
Сепаратор конденсата
Предварительный осушитель
Рис.3.5. Принцип работы рефрижераторного осушителя
Осушение избыточным сжатием. При таком виде осушения воздух сначала сжимается до давления значительно превышающего нужное а затем расширяется до требуемого давления.
При растущем давлении и значит уменьшающемся объеме воздух может содержать в себе меньшее количество влаги. Сначала воздух сжимается до высокого давления что сопровождается выделением значительного количества конденсата.
p=0бар p=35бар p=3бара
Абсолютная влажность сжатого воздуха падает (при этом относительная по-прежнему составляет 100%). Выделившийся конденсат удаляется и затем воздух расширяется до нужного давления как показано на рис. 3.6. При расширении относительная влажность а значит и точка росы падают.
Мембранный осушитель. Осушитель состоит из пучка полых волокон которые открыты для водяных паров. Осушиваемый воздух обтекает эти волокна (см. рис. 3.7). Осушка происходит за счет разницы давлений между влажным воздухом внутри волокон и сухого воздуха протекающего в обратном направлении [21].
Рис.3.7. Принцип работы мембранного осушителя
Абсорбционные осушитель. Действие осушителя абсорбционного типа основано на способности таких веществ как силикагель и хлорид лития поглощать влагу из воздуха (см. рис. 3.8) [21].
Осушенный сжатый воздух
Воздух от компрессора
Рис 3.8. Принцип работы абсорбционного осушителя
Адсорбционные осушитель. В процессе адсорбции молекулы воды прикрепляются к десиканту (адсорбенту) под воздействием адгизии (неравномерного межмолекулярного притяжения) (см. рис. 3.9). Влага остается на поверхности и внутри пор адсорбента [21].
Рис.3.9. Принцип работы адсорбционного осушителя
Занесем все особенности осушителей в табл. 3.6 и 3.7.
конденсации охлаждением.
Высокая экономичность;
удаления твердых частиц и масла;
частиц и компрессорное масло.
Падение давления на рефрижераторных
осушителях составляет от 02 до 04 бар.
Осушение избыто- чным сжатием
используется крайне редко главным образом из-за своей абсолютной неэкономичности.
Приемлемо только при крайне небольших
Продолжение табл. 3.6
Мембранный осушитель
Применяется достаточно редко
из-за ограниченного диапазона пропускных способностей
осушителей этого типа.
Простота контрукции;
Отсутствие потребности во внешних источниках энергии;
Необходимо обеспечить предварительную
очистку сжатого воздуха от твердых частиц и масла
абсорбционный осушитель
Потери сжатого воздуха Для осушителей
давлениях (до 16 бар) эти потери могут
составлять от 14 до
небольших и средних расходах
Простота конструкции
энергопотребление (близкое к нулю)
Потери сжатого воздуха
Рефрижераторный осушитель
Осушение избыточным давлением
в зависимости от компрессора
в зависимоти от компрессора
Абсорбционный осушитель
Адсорбционный осушитель
По п. 3.3 рефрижераторный осушитель осушение избыточным давлением и мембранный осушитель не подходят под заданные параметры. Следовательно в дальнейшем рассмотрим абсорбционный и адсорбционные осушители см. табл. 3.8.
Способ удаления влаги
Химический адсорбционный. Сорбент поглощает и
удерживает влагу насвоей
поверхности иотдает ее во время регенерации.
Химический абсорбционный. Сорент поглощает влагу ипостепенно растворяется. Сорбент неподлежит
Две вертикальные колонны емкости-адсорберы
соединенные трубопроводами склапанами дляуправления потоком воздуха.
Обе емкости заполняются
Одна вертикальная емкость
находящаяся поддавлением.
Опорная сетка располагается надвходным отверстием иудерживает абсорбент
Первая колонна пропускает поступающий внее влажный воздух через слой
находящегося вней адсорбента который отбирает
накапливает влагу. Вто же время адсорбент второй
колонны регенерируется.
Накопленная влага удаляется при помощи электрического или парового подогрева или продувкой частью сухого воздуха после первой колонны.
центральную нижнюю часть колонны где механически
отделяются крупнодисперсные
жидкие итвердые частицы.
Помере прохождения воздуха снизу вверх влага поглощается гранулами абсорбента.
Конденсат ирастворяемый помере насыщения абсорбент стекают внижнюю часть
колонны откуда могут
удаляться автоматически или вручную.
Алюмогель или молекулярные сита.
гранулированный абсорбент.
управления потоками иэнергия длярегенерации
Крупные частички масла
удаляются механически.
фильтрации воздуха навходе
Фильтрование необходимо
дляпредотвращения контакта адсорбента находящегося вколоннах осушителя смаслом иводой во
избежание его разрушения.
Фильтрование рекомендуется вслучае высокой
насыщенности сжатого
воздуха маслом воизбежание обволакивания ивыхода из
строя гранул абсорбента.
Продолжение табл. 3.8
дляисключения уноса из
осушителя впневмосистему пыли адсорбента.
дляисключения уноса из
осушителя впневмосистему пыли абсорбента.
Требования кэксплуатации
Замена адсорбента каждые 2÷3 года. Настройка системы управления. Замена или восстановление
Удалять конденсат вручную
одновременно сзаменой
абсорбента один раз в3÷4
обслуживающий персонал.
персонал нетребуется.
На основании данных указанных в таблице 3.8 составим таблицу 3.9.
По таблице полученным данным табл. 3.9 выгодно устанавливать адсорбционный осушитель. При этом очистка воздуха должна проходить до и после адсорбционного осушителя. Рассмотрим виды фильтров и выберем подходящие для нашей системы.
Циклонный сепаратор предназначен для первичной очистки воздуха. Внутри сепаратора установлен завихритель который придает входящему в сепаратор сжатому воздуху вращательное движение (см. рис. 3.10). При соударении потока сжатого воздуха со стенками сепаратора значительная часть более тяжелых твердых и жидких частиц выделяются из потока и продолжая свое движение проникают в конденсатосборник которым служит нижняя часть циклонного сепаратора. Экран предотвращает возврат отделенного конденсата в основной поток сжатого воздуха[25].
Рис.3.10. Циклонный сепаратор
Поверхностные фильтры. Это фильтры фильтрующие элементы которых задерживают частицы примесей на своей поверхности (см. рис. 3.11 и рис. 3.12). и выступают в роли предварительных фильтров защищая фильтры более тонкой очистки а также осушители от чрезмерной конденсатной нагрузки. [25].
Рис.3.12. Фильтроэлемент
Рис.3.11. Поверхностная фильтрация
Глубинно-коалесцентные фильтры. Это фильтры фильтрующие элементы которых задерживают частицы примесей поверхности и в глубине фильтрующего материала (см. рис. 3.13 и 3.14) [30].
Рис.3.13. Глубиннокоалесцентная
Рис.3.14. Фильтроэлемент
Адсорбирующие фильтры. Адсорбирующие фильтры снабжены фильтрующимим элементами задерживающими летучие примеси: пары компрессорного масла а также иные пахучие и обладаюшие вкусом соединения.
Угольные колонны. Угольные колонны представляют собой емкости заполненные активированным углем в зернах. Служат для удаления паров компрессорного масла и запахов. Фильтрующим материалом угольных колонн служит зерна активированного угля [30].
Фильтры с насыпным углем. В таких фильтрах в качестве сменного фильтроэлемента которых служит картридж наполненный зернами активированного угля[25].
Все данные о фильтрах сведем в табл. 3.10 и 3.11.
Удаление крупных частиц конденсата
Недорогое и простое устройство;
дифференциальное давление
Обеспечивает только
фильтроматериала меньше размера частиц находящихся в воздухе
Обеспечивают только грубую предварительную очистку
Глубинно-коалесцентные
полхаотично переплетенных волокон
Тонкой очистка сжатого воздуха или иного газа.
Адсорбирующие фильтры.
Угольные фильтры позволяют избавиться от паров компрессорного масла и пахучих примесей.
Небольшой срок службы фильтроэлемента
Фильтры с насыпным углем
Большая надежность и более долгий срок службы
Относительно высокая по сравнению
с угольными фильтрами стоимость
Дифференциальное давление бар
Остаточное содержание
Поверхностные фильтры.
Глубинно-коалесцентные фильтры.
В системе устанавливается регулятор давления который служит для обеспечения постоянного давления (вторичного давления) при колебаниях давления в сети (первичное давление) Если не обеспечивать такое постоянное давление в системе могут происходить нежелательные отклонения во временах переключения и срабатывания устройств управления приводом.
Результаты полученные в данном пункте представим графически (см. рис. 3.15 и рис. 3.16). На этих двух рисунках представлены две возможные схемы подготовки воздуха. Первый вариант предполагает использование масляного компрессора второй вариант – применение безмаслянного компрессора. На заданные параметры системы имеет смысл использовать схему изображенную на рис. 3.15 но при этом необходимо обеспечить более глубокую очистку воздуха.
Рис 3.15. Вариант системы подготовки воздуха с использованием масляного компрессора
Рис 3.16. Вариант системы подготовки воздуха с использованием безмаслянного компрессора
Используя оборудование выбранное в результате структурного синтеза возможно получить сжатый воздух со степенью фильтрации 001мкм влагоотделением 99999% точкой росы до – 70 эти показатели удовлетворяют требования технического задания.
6.Рассмотрение способов определения положения штока
Одной из задач при автоматизации производства является определение положения оксидной корки. Как было показано в п. 2.2 в настоящее время существует оптический метод определения положения корки но кроме эффекта отражения и испускания света существуют и другие физические эффекты на основании которых возможно определять положение (краткое описание принципа действия каждого физ. эффекта см. прилож. 9)[23]:
Отражение и испускание света
Изменение электрических и магнитных полей
Электрические разряды
По косвенным показателям
Магнитострикционный метод
Отбросим методы которые не подходят хотя бы по одному показателю работоспособности (см. таб.3.12).
В результате получилось четыре метода определения положения штока. Но методы отражения и испускания света эффект Доплера сопло заслонка требуют дополнительного оборудования что приводит к удорожанию конструкции к тому же все конструкции довольно сложны в исполнении. В данной работе предлагается рассмотреть метод по косвенным показателям заключающийся в составлении динамической модели движения штока. Предлагаемый способ не требует дополнительного дорогостоящего оборудования и является более надежным и дешевым.
По косвенным параметрам
7.Описание пневматической схемы
Составим схему пневматической системы электролизера для выплавки алюминия включающую себя систему подготовки сжатого воздуха и систему управления движением пневмоцилиндра.
Оборудование для управления работы 6 цилиндров пробойников и 9 цилиндров дозаторов. Для возможности монтажа пневмооборудования в шкафу установлены краны КШ.
Рассмотрим движение штока при прямом ходе. В первый момент времени поршень находится в поднятом положении. Как только на Y2 подается сигнал воздух проходит через ДР1 попадает в поршневую полость и выходя из штоковой полости проходит через управляемый клапан (пневмозамок) КОУ (клапан служит для блокировки штока в случае отсутствия питания). Далее движение происходит через распределитель и дроссель ДР2
При обратном ходе сигнал с катушки Y2 снимают. Распределитель возвращается в исходное положение. Воздух проходит через ДР1 далее проходит через дроссель ДР2 и КОУ и происходит поднятие штока. Принцип работы всех цилиндров пробойников аналогичен.
ОПРЕДЕЛЕНИЕ ПАРАМЕТРОВ СИСТЕМЫ
1.Определение производительности компрессора. Выбор
компрессора на рассчитанные параметры
В п. 3.4. были рассчитаны потребление воздуха пневмоцилиндрами пропускная способность устройств а также производительность компрессора. При выборе компрессора необходимо предусмотреть возможные утечки в пневмосети и резервы на увеличение потребления сжатого воздуха.
Утечки [%]. Утечки могут иметь место в самых разных частях системы сжатого воздуха. В новых пневмосетях они обычно невелики и не превашают 5% от общего расхода сжатого воздуха. Однако в старых обширных сетях сжатого воздуха по мере износа трубопроводов а также потребляющего оборудования объем утечек может достигать 25%.
Резервы [%]. Резервы следует предусматривать в двух основных случаях:
при наличии обоснованных предположений о последующем увеличении потребления сжатого воздуха которое может вызвать появление новых потребителей или увеличение среднего времени работы;
если требуется полностью исключить уменьшение объема производимого сжатого воздуха которое может быть вызвано например выходом из строя одного или нескольких компрессоров. Необходимо помнить о том что любой компрессор нуждается и в плановых остановках для проведения технического обслуживания - пусть обычно и непродолжительных. В случае если снабжаемое оборудование безостановочно и круглосуточно нуждается в сжатом воздухе нужно принимать это во внимание при формировании компрессорной системы.
Ошибки при расчетах [%]. Обычно при расчетах появляются ошибки обусловленные неизвестными значениями расхода сжатого воздуха отдельными потребителями и другими факторами [30]. Обычно разумной поправкой на всевозможные ошибки является 5-15%.
Рассчитаем необходимую производительность компрессора с учетом поправок на утечки резервы и ошибки при расчетах по следующей формуле:
- необходимая производительность компрессора м³мин; - расчетное общее потребление м³мин; - оцениваемый объем утечек%; - оцениваемый объем резервов %; - поправка на ошибки в расчетах %.
По указаниям [30] целесообразней принимать утечки резервы и ошибки равными соответственно и . По формуле (4.1) рассчитаем необходимую производительность компрессора:
Далее следует определить на какое максимальное рабочее давление должен быть рассчитан подбираемый компрессор при этом необходимо учесть следующие факторы:
Давление в воздушном ресивере (или вообще в трубопроводе на выходе компрессора) которое колеблется между максимальным давлением и давлением перехода под нагрузку всегда должно быть выше чем то давление которое необходимо для работы потребляющих сжатый воздух агрегатов.
Обстоятельство которое нужно принимать во внимание при выборе максимального рабочего давления компрессора - это возможное падение давления в пневмосети. Типичными являются следующие падения давления в сетях сжатого воздуха вообще и на отдельных устройствах в частности:
Для простой неразветвленной сети принято принимать расчетное падение давления на трубопроводах за 01 бар. Для большой и разветвленной сети сжатого воздуха принять падение давление можно за 05 бар [30].
На осушителях сжатого воздуха давление также падает. На адсорбционных осушителях большинства производителей давление падает на 03 08 бар.
Магистральные фильтры: перепад давления на магистральных фильтрах сжатого воздуха растет по мере загрязнения их фильтрующих элементов. Принимаем падение давление на фильтре 03 бар.
На циклонных сепараторах падение давления составляет обычно 006 008 бар и является постоянным.
Рассчитаем необходимое давление. Максимальное давление работы цилиндров равно 10 барам. Сеть небольшая и при этом устанавливаются новые пневмолинии Тем самым допустимо принимать падение давления на падение давления в пневмосети равным 01 бар. В сети установлен адсорбционный осушитель перепад давления на котором можно принять 04 бар. Также в сети установлено 4 фильтра падение давление на каждом принимаем 03 бара. Общий перепад давления на воздухоподготовительном оборудовании составляет 17 бара. При использовании винтового компрессора циклический дифференциал (см. приложение 7) (то есть разница между и ) компрессора составляет 1 бар. В результате получаем максимальное давление компрессора 127 бар.
На данные параметры системы нам подходят маслозаполненные винтовые компрессоры. По каталогам выбираем компрессор на максимальное давление 13 бар производительностью 19 м³мин и мощностью 15 кВт [30].
2. Выбор оборудования на рассчитанные параметры
По расчетам в п. 3.4. и 4.1. подберем оборудование для пневмосистемы.
Для выбора ресивера необходимо рассчитать его объем по формуле (4.2):
где - эффективная производительность компрессора м³мин; - объем воздушного ресивера м³.
При выборе ресивера необходимо учитывать что винтовые компрессоры приспособлены для непрерывной работы имеют возможность переходить на холостой ход поэтому для них достаточно меньшего объема ресивера. При расчете также необходимо учесть что компрессоры с меньшим объемом ресивера включаются и выключаются чаще чем компрессоры с относительно большим объемом ресивера. Кроме того каждое включение электродвигателя - это дополнительная нагрузка на агрегат которую по возможности следует избегать.
Винтовые компрессоры которые имеют возможность переходить в режим холостого хода могут работать без выключения электродвигателя (непрерывный режим работы). Однако частые переходы из режима холостого хода в режим работы под нагрузкой и обратно также нежелательны пусть и в гораздо меньшей степени чем пускиостановки электродвигателя. При частых переходах между холостым ходом и нагрузкой увеличивается износ сальников и подшипников винтового блока а также и некоторых других компонентов компрессора.
Существуют упрощенные формулы расчета объема воздушного ресивера для винтовых компрессоров. В эти формулы уже заложена проверка максимально допустимой цикличности включениявыключения[30].
где - объем воздушного ресивера м³; - эффективная производительность компрессора м³мин; 5 - поправочный коэффициент; - число допустимых циклов вклвыкл двигателя ч-1; Δp - циклический дифференциал давления (см. прилож. 7) бар.
Максимально допустимое число включенийвыключений электродвигателя определяется по табл. 4.1 с учетом мощности электродвигателя[30].
Мощность электродвигателя кВт
Максимально допустимое количество
По формуле (4.3) рассчитаем объем ресивера.
Подбор оборудования для подготовки воздуха и пневмоаппаратуры осуществляется на давление от 13 бар и пропускную способность 3456 лмин для системы подготовки воздуха и на давление от 10 бар и пропускной способностью 3270 лмин и 190 лмин для пневмоаппаратуры цилиндров пробойников и цилиндров дозаторов соответственно (см. п. 3.4). Все данные сведены в спецификацию.
Рассчитаем диаметр медных трубопроводов расположенных в шкафу управления:
Внутренний диаметр трубопровода определяется по следующей формуле [30]:
где – объемный расход системы м³с; – длина трубы м; – падение давления Па; – рабочее давление Па.
Выбираем диаметр трубопровода равным 18 мм.
МАТЕМАТИЧЕСКОЕ МОДЕЛИРОВАНИЕ ДВИЖЕНИЯ ШТОКА ЦИЛИНДРА ПРОБОЙНИКА
Для автоматизации работы электролизера необходимо иметь данные о положении оксидной корки. А как было указано в п.п. 2.2 на пробойнике установлен датчик касания расплава обеспечивающий поднятие штока в случае соприкосновения штока с жидким алюминием. Таким образом зная пройденное штоком расстояние можно определить положение оксидной корки.
Для определения положения штока цилиндра необходимо провести динамический расчет движения входного звена с помощью которого возможно определить действующие скорости и ускорения при движении рабочих органов закона движения характера изменения давлений а полостях пневмодвигателя.
1. Основные периоды в работе пневмоцилиндра.
Динамический расчет проводится для двухстороннего цилиндра. Движение цилиндра можно разделить на два периода (см. рис. 5.1.): прямой ход и обратный ход (не рассматривается).
При прямом и обратном ходе различают три периода:
подготовительный интервал времени от момента подачи сигнала на переключение распределителя до начала движения поршня. Для упрощения задачи принимаем что процессы наполнения рабочей полости и опорожнения полости выхлопа начинаются после полного переключения распределителя и прохождения волны давления по соответствующим пневмолиниям. Тогда:
где – время переключения распределителя (для серийной пневмоаппаратуры приводится в технической характеристики); – время распространения волны давления; – время изменения давлений в полостях пневмоцилиндра до момента страгивания поршня с места;
Рис. 5.1. Диаграмма перемещения (x) пневмоцилиндра
двустороннего действия
период движения – период движения поршня в течение времени является сложным как по характеру протекающих процессов так и по расчету. Процесс движения описывается системой дифференциальных уравнений в которую входят уравнение движения поршня и два уравнения энергетического баланса характеризующие изменение давлений в полостях цилиндра во время движения;
заключительный период – интервал времени втечение которого давление в полостях пневмоцилиндра после остановки поршня в конце движения стабилизируется: в рабочей полости до магистрального а в полости выхлопа до атмосферного.
2.Описание работы пневмоцилиндра при прямом ходе
В исходном положении поршень находится вверху. Его положение определяется координатой x (см. рис. 5.2). В начальном положении но между поршнем и крышкой цилиндра имеется некоторый небольшой объем называемый вредным объемом цилиндра (на расчетной схеме рис. 5.2 характеризуется координатой ). К штоковой полости подводится магистральное давление в поршневой полости давление является атмосферным. При подаче сигнала на блок управления распределителя он переключается и воздух начинать поступать в поршневую полость цилиндра. После достижения давления равного давлению страгивания поршня начинается движение поршня пневмоцилиндра. Движение происходит со скоростью при этом преодолевая возникающую силу сопротивления. Каждому моменту времени соответствует определенное состояние воздуха в полостях цилиндра характеризуемое параметрами и и .
Рис. 4.2 Принципиальная схема
пневмоцилиндра с распределителем 52
Рабочая полость во время движения поршня связана с источником питания пневмолиний подвода с эффективной площадью а полость выхлопа – с атмосферой через пневмолинию выхлопа с эффективной площадью сечения . Как только «датчик касания расплава» расположенный на штоке поршня касается алюминия подается сигнал на распределитель и поршень начинает перемещаться вверх.
3.Математическая модель движения штока пневмоцилиндра.
При формировании математической модели используются уравнения термодинамики которые общеизвестны и приведены в прилож. 11. Математическую модель можно условно разделить на два интервала времени для которых расчеты ведутся отдельно. Это интервал времени соответствующий подготовительному периоду и интервал времени движения поршня.
Подготовительный период движения: В период переключения распределителя и распространения волны давления изменения давления не происходит. Время переключения определяется по каталогу время распространения волны определяется по следующей формуле [4]:
где – длина трубопровода – скорость распространения звука в воздухе.
Для определения времени изменения даления в полостях пневмоцилиндра можно воспользоваться уравнениями описывающими наполнение газом постоянного объема (формула (1.65) см. в прилож.11):
где – давление при котором поршень начинает движение – минимальный расчетный объем рабочей полости – эффективная площадь линий подвода – функция давления (см. рис. 5.5).
где – вредный объема – расчетный объем трубопровода.
Определить расчетный объем трубопровода можно формуле (5.4)
где – коэффициент приведения распределенного объема к сосредоточенному – длина трубопровода на участке от рабочей полости до распределителя – внутренний диаметр трубопровода на участке от рабочей полости до распределителя.
Коэффициент приведения распределенного объема к сосредоточенному определяется по формуле (5.5):
где – коэффициент расхода подводящей пневмолинии – коэффициент расхода участка подводящей пневмолинии от ее начала до середины наполняемой части трубопровода для которой определяется объем. Сопротивление участка пневмолинии всегда меньше ее полного сопротивлении и следовательно коэффициент т.е. расчетный объем трубопровода всегда меньше фактического.
Эффективная площадь линий подвода определяется по формуле (5.6)
где – эффективная площадь трубопровода – эффективная площадь сечения дросселя.
Эффективные площади определяются из уравнений (5.7) и (5.8)
где – коэффициент расхода трубопровода – площадь трубопровода.
где – коэффициент расхода дросселя – площадь дросселя.
Коэффициенты расхода определяются по рис. 5.4 – коэффициент сопротивления пневмолинии определяемый по формулам:
где – коэффициент трения в трубе принимает значения в пределах от 001-004 в зависимости от шероховатости стенок диаметра и материала трубы – длина трубопровода – диаметр трубопровода.
где – коэффициент местных потерь на входе в дроссель определяемы по графикам (см. рис. 5.6) – коэффициент сопротивления характеризующий потери на трение при движении жидкости.
При турбулентном течении можно пренебречь т.к. преобладающее значение имеет сопротивление на входе в дроссель.
Рис. 5.4 Зависимость коэффициента расхода от коэффициента трубопровода соответственно.
Рис. 5.5 Функция давления при наполнении полости
и при истечении из полости
Рис. 5.6 Значение коэффициента
После достижения давления страгивания начинается движение поршня вниз. Будем полагать что процесс происходит без теплообмена с окружающей средой а т.е. является адиабатическим. Полость пневмоцилиндра наполняется воздухом с постоянными параметрами давления и температуры . Тем самым для описания процессов происходящих в поршневой полости можно воспользоваться уравнениями энергетического баланса для наполняющейся полости переменного объема (вывод формулы - см. уравнение (11.62) в прилож. 11):
Уравнение (5.11) показывает что энергия подводимая массой газа тратится на внутреннюю энергию и работу затраченную на вытеснение газа их пневмополости.
При опорожнении полости переменного объема уравнение энергетического баланса принимает вид:
где и – переменные расчетные объемы рабочей и выхлопной полостей.
Подводимая и отводимая масса газа может быть получена из уравнений для истечения газа из неограниченного объема для случая равномерного установившегося течения (вывод уравнения см. п.1.4 прилож. 11):
где в уравнениях (5.13) и (5.14) и – расход сжатого воздуха определяемы по формуле (11.52) в прилож. 11 где и – эквивалентные площади определяемые как и в подготовительном периоде – вводимый коэффициент .
Записав процессы происходящие в полостях пневмоцилиндра также необходимо учесть уравнение движения поршня двухстороннего типа. На поршень действует сила сопротивления давления которая включает в себя силу внутреннего трения цилиндра силу внешнего трения силу пробития корки и вес подвижных частей. Исходя из этого уравнение приобретает вид:
где – сосредоточенная масса и – давление и площадь поршневой полости; и – давление и площадь штоковой полости; – сила сопротиления давлению:
где – сила трения; – сила пробития корки; – вес подвижных частей – поправка вызванная тем что в уравнении (5.22) учитывается не избыточное а абсолютное давление.
После преобразований уравнений (5.13) (5.14) и (5.21) получим систему решив которую возможно построить зависимости изменения давления скорости и перемещения в каждый момент времени:
4.Численное решение математической модели движения пневмоцилиндра
Для решения математической модели запишем основные исходные величины:
Условное обозначение
распространения звука
в воздухе (при T=290К)
Атмосферное давление
4.1.Решение математической модели при отсутствии
По экспериментальным данным цилиндр пробивает алюминиевую корку только в 10% случаев опускания штока. Поэтому сначала рассмотрим общий случай движения штока без образования корки.
Подготовительный период движения:
Время переключения распределителя MN1H–52–D–3–C по каталогу [24] равно:
Время распространения волны давления определяется по формуле [5.1]:
Время изменения давлений в полостях пневмоцилиндра до момента страгивания поршня с места определяется по формуле [5.2]:
Опередим все составляющие уравнения:
по рис. 5.5 определим функцию давления при наполнении полости пневмоцилидра: .
По рис. 5.5. определим функцию давления при наполнении полости пневмоцилидра:
Определим коэффициент трения в трубопроводе (5.9):
По рис. 5.4. определим коэффициент расхода для трубы:
Определим коэффициент трения в трубопроводе для половины длины:
По рис. 5.4 определим коэффициент расхода: .
Коэффициент приведения распределенного объема к сосредоточенному определим по формуле (5.5):
Объем трубопровода определяется по формуле (5.4):
Принимаем что вредный объем цилиндра равен 5% полного объема цилиндра тогда:
Тогда минимальный расчетный объем рабочей полости определяется по формуле (5.3):
Эквивалентная площадь трубопровода рассчитывается по формуле (5.7):
Эквивалентная площадь дросселя определяется по коэффициенту (см. рис. 5.6) (см. рис. 5.4) и площади дросселя:
Расчет эффективной эквивалентной площади производится по формуле (5.6):
По формуле (5.2) время изменения давлений в полостях пневмоцилиндра с момента подачи сигнала до момента страгивания поршня с места:
Общее время подготовительного периода определяется по формуле:
Для определение изменения параметров в период движение необходимо решить уравнения (5.23) (5.24) (5.25):
Уравнение (5.23) описывает динамику поршня В него входят сила трения сила пробития корки вес подвижных частей и силы давлений действующих на поршневую и штоковую полость.
Силу трения можно разделить на силу трения в цилиндре (определяется по данным каталога (см. формулу (5.26)) и задается графически см. рис. 5.7) и силой трения в опорах пробойника (определяется экспериментально и задается формулой см. - (5.27) и рис. 5.8).
Рис. 5.7 Сила трения в цилиндре
Рис. 5.8. Сила трения в опорах пробоника
Сила веса определяется исходя из массы пробойника и массы штока: .
Сила пробития корки (задается для данного случая)
Сила сопротивления давлению рассчитывается по уравнению (5.22) вид нагрузки показан на рис. (5.9):
Рис. 5.9. Сила сопротивления давлению
В уравнениях (5.24) (5.25) описывается изменение давления в поршневой и штоковой полостях. Определим составляющие входящие в эти уравнения:
Эквивалентные площади входной () и выхлопной линии ():
(определяется в п. 3 подготовительно периода);
считается аналогично только для выхлопной линии
Эквивалентная площадь выхлопного трубопровода рассчитывается по формуле (5.7):
Эквивалентная площадь дросселя в выхлопной линии определяется по коэффициенту (см. рис. 5.6) (см. рис. 5.4) и площади дросселя (диаметр дросселя определяется итерационным путем в ходе решения математической модели.):
Расчет эффективной эквивалентной площади в выхлопной линии производится по формуле (5.6):
В уравнениях (5.24) (5.25) вводится коэффициент К определяемый по формуле:
Начальные координаты и определяется по формулам:
После определения всех параметров входящих в уравнения мы получили три дифференциальных уравнения два из которых второго порядка и три неизвестных члена – :
Решить систему уравнений второго порядка возможно с помощью численного метода Рунге – Кутта. Для этого необходимо уравнения записать в стандартной форме (форме Коши) а потом с помощью встроенных функций программы Mathcad решить уравнения. Кроме того для решения уравнений необходимо задать начальные условия т.е. значение функции в некоторой точке.
Приведение системы уравнений к стандартной форме.
Запишем начальный условия в момент времени :
где – давление в поршневой полости в момент страгивания поршня (); – давление в штоковой полости в момент страгивания поршня ().
Используя уравнения (5.28) – (5.35) перепишем уравнения (5.23) – (5.25):
Уравнения такого вида решаются с помощью встроенной функции rkfixed. Полученное решение представим в графическом виде рис. 5.10 рис. 511:
Рис. 5.10. Изменение хода поршня и скорости от времен.
Рис. 5.11. Изменение давления в поршневой и штоковой
полостях от времени.
На рафиках показанных на рис. 5.10 5.11 видны сильные колебания системы Устранить колебания возможно введением в пневмоцилиндр демпфирующего элемента. Отразим введение этого элемента в уравнением коэффициентом демпфирования. В результате получаем уравнения (5.23) – (5.25) с учетом введения коэффициента в форме Коши:
После введение коэффициента демпфирования ( и проведения расчетов получаем следующие результаты (см. рис. 5.12 и рис. 5.13):
Рис. 5.12. Изменение перемещения и скорости от времени при введении коэффициента демпфирования равного 5000 кгм
Из полученных графиков видно что при введении коэффициента демпфирования колебания в системе исчезают. Коэффициент демпфирования можно менять изменяя проходное сечение демпфера.
Рис. 5.13. Изменение давления в поршневой и штоковой полости от времени. при введении коэффициента демпфирования равного 5000 кгм
По полученным графикам видно что 400 мм цилиндр проходит за 31 секунду.
4.2.Решение математической модели при существовании алюминиевой корки
Этот случай отличается от предыдущего введением значения силы - пробития корки. Сила вводится на основании экспериментальных данных для конкретного случая записывается уравнением (5.36) график силы показан на рис. 5.14.
Рис. 5.14. Усилие пробития корки
Остальными параметрами система не отличается от случая рассмотренного в п. 5.4.1. В результате решения системы уравнений получаем графики показанные на рис. 5.15 и на рис 5.16:
Рис. 5.16. Изменение хода и скорости поршня
при наличии оксидной корки.
Рис. 5.16. Изменение давления в поршневой и штоковой полости
При введения усилия пробития корки скорость при подходе к корки уменьшается и резко возрастает при прохождении корки. Давление в поршневой полости увеличивается за счет введения сопротивления а в штоковой уменьшается.
ОПИСАНИЕ И РАСЧЕТЫ КОНСТРУКЦИИ
1. Распределитель с пневматическим и ручным управлением
В п. 2 говорилось о введении системы резервировании и диагностики системы.
Одним из способов резервирования системы подготовки воздуха является автоматическая смена работающих фильтров при загрязнении фильтроэлемента. Осуществляется это с помощью пневматического распределителя. За основу разработки был взят пневмораспределитель фирмы FESTO JH-5. Распределитель 52 с пневматическим и вспомогательным ручным управлением. Переключение распределителя осуществляется подачей сигнала на канал управления (12) либо (14) см. рис. 6.1.
Рис. 6.1. Внешний вид распределителя JH – 5
На основании этого распределителя пользуясь принципом максимальной унификации деталей (все детали выпускаются серийно) необходимо спроектировать распределить 32 работающий на перепаде давлений т.е. как только дифференциальное давление на фильтре достигнет заданного значения распределитель должен переключиться. Принципиальная схема показана на рис. 6.2.
Рис. 6.2. Принципиальная схема установки распределителя.
Опишем принцип работы пневматического распределителя 32 (см. рис 6.3).
Рис. 6.3. Распределитель пневматический 32
Отверстие 1 – питание 23 – управляющий сигнал 45 – выход на аппаратуру. На рис. 6.3 показан случай когда воздух выходит в отверстие 5 которое с помощью сверлений в корпусе соединено с полостью 6 в которой создается давление перед фильтром (см. рис. 6.2). К отверстию 2 подводится давление равное давлению . Это давление попадает в полость 7. В результате на крышку золотника действует сила создаваемая давлением с одной стороны и сила создаваемая от давления и сила пружины с другой стороны. Как только падение давление на фильтроэлементе достигнет предельного значения давление уменьшится и пружина перейдет в новое устойчивое положение золотник переместится и воздух будет проходить через отверстие 4.
Произведем расчет сил учитываем что переключение должно произойти при .
Давление действует на площадь с диаметром (см. рис. 6.3.):
Давление сопротивления пружины определяется по рис. 6.4. из условия что давление перед фильтром равняется 63 бара
Определим по этому давлению усилие переключения пружины:
Определим усилие переключения исходя из сил давления:
Рис. 6.4. Распределитель.
2. Регулируемый дроссель
При проектировании регулируемого дросселя необходимо построить регулировочную характеристику. Регулировочная характеристика строится исходя из геометрии дросселя 2 и седла 3
Рис. 6.5. Регулируемый дроссель.
Рис. 6.6. Геометрический расчет золотника
По рис. 6.5 рассчитаем площадь проходного сечения:
Исходя из конструкционно-технологических соображений принимаем . Построим график зависимости проходной площади от перемещения (см. рис. 6.7). Регулирование продолжается до площади равной после этого значения происходит процесс насыщения. Для удобства работы с дросселем шаг резьбы принимаем равным 1 мм и поворот дросселя на 90 соответсвует перемещению на 025 мм. Построим зависимость диаметра условного сечения от перемещения (см. рис. 6.8).
Рис. 6.7. Зависимость площади проходного сечения от перемещения
Рис. 6.8. Диаметра проходного сечения от перемещения
ОЦЕНКА ЭКОНОМИЧЕСКОЙ ЭФФЕКТИВНОСТИ ПРИМЕНЕНИЯ ПНЕВМАТИЧЕСКОЙ СИСТЕМЫ ЭЛЕКТРОЛИЗЕРА ДЛЯ ВЫПЛАВКИ АЛЮМИНИЯ
1. Технико-экономическое обоснование применения способа
определения положения штока
В дипломном проекте «Пневматическая система электролизера для выплавки алюминия» рассматриваются система подготовки сжатого воздуха для цилиндров пробойников и цилиндров дозаторов и способ определения положения штока пневмопробойника по косвенным показателям. Для рассмотрения остановимся на способе определения положения штока.
Пневматическая система является составной частью автоматической подачи глинозема внедряемой в настоящее время на алюминиевых заводах.
За счет введения системы определения положения шока а следовательно и оксидной корки повышается производительность электролизера.
Проведем оценку экономической эффективности и на основании полученных данных сделаем вывод о целесообразности использования данной разработки.
Все расчеты проводятся для 1 электролитной ванны.
Экономическая эффективность – результативность экономической системы выражающаяся в отношении полезных конечных результатов ее функционирования к затраченным ресурсам [39]. Определять экономическую эффективность можно с помощью четырех показателей:
Обобщающих показателей экономической эффективности производства.
Показателей эффективности использования труда.
Показателей эффективности использования основных фондов оборотных средств и капитальных вложений.
Показателей эффективности использования материальных ресурсов.
Будем рассматривать экономическую эффективность применения пневматической системы в течение жизненного цикла который включает в себя: проектирование и разработку технической документации изготовление освоение и испытание эксплуатацию и утилизацию
Длительность жизненного цикла примем равной сроку годности цилиндра пробойника:
Рассмотрим затраты на каждом периоде жизненного цикла.
2.Расчеты затрат на проектирование способа
К затратам на проектирование отнесем затраты на оплату труда исполнителей.
Исходной базой для установления размера заработной платы работнику выступает тарифная ставка (оклад). Оклад это элемент тарифной системы оплаты труда определяющий фиксированный размер оплаты труда выраженный в денежной форме различных квалификационных групп и категорий работников за выполнение нормы труда в который не включаются доплаты надбавки премии и другие поощрительные выплаты.
Размер тарифной ставки (оклада) конкретного работника определяется в зависимости от его квалификации и сложности выполняемой работы.
Часовая ставка работника определяется по формуле:
где – оклад работника в месяц руб.; – эффективный месячный фонд времени ч.
Эффективный месячный фонд времени при 8 часовом рабочем дне и 22 днях в месяц составляет 176 часов. Ставки работников для выполнения проектной документации представлены в табл. 7.1.
Сроки исполнения и затраты на каждой стадии проектирования приведены в табл.7.2.
Научно-исследовательская работа
Технологическая проработка
Зарплата исполнителей с начислениями по формуле (7.2):
где – основная заработная плата исполнителей по табл. 7.1 – дополнительная заработная плата (оплата отпусков премии доплаты надбавки) составляет 30% от основной заработной платы –отчисления в фонд социального страхования составляют 26% от основной заработной платы.
К затратам на проектирование необходимо отнести затраты на расходные материалы:
Прочие расходы связанные с затратами на обслуживание организацию и управление во время проведения проекта. Накладные расходы могут включать в себя затраты на амортизацию ремонт оргтехники содержание офиса аренду заработную плату административного сектора хозяйственные расходы рекламу и.т.д. В данном случае накладные расходы принимаем пропорционально основной заработной плате в размере не превышающем 70%. Расчет накладных расходов можно произвести по формуле:
Сложив накладные расходы затраты на расходные материалы и расходы на зарплату получим капитальные вложения на разработку технической документации:
После разработки изделия следует его производство. Средства потраченные на производство изделий включаются в себестоимость изделия.
3.Расчет затрат на изготовление устройств
для определения положения штока.
Себестоимость пневмосистемы определяется по формуле (7.5):
Рассмотрим методику определения каждой из статей себестоимости. Себестоимость основных материалов:
где – количество деталей (для рассматриваемой конструкции число проектируемых деталей ) – коэффициент учитывающий транспортно-заготовительные расходы предприятия (3-5% от стоимости материалов); n – число наименований материалов (дроссель управляемы и неуправляемый изготавливаются из алюминия n = 1); – черновой вес материалов израсходованных на производство комплектующих привода кг; Цм – цена единицы материала (стоимость 1 кг. алюминия равна 70 руб.кг); – стоимость реализуемых расходов;
Черновой вес по каждому виду материала:
где – чистый вес материалов расходуемый на изделие (); Кисп –коэффициент использования материала (принимаем коэффициент использования материала Кисп = 08). Тогда по формуле (7.7):
Стоимость отходов определяется по следующей формуле:
где – реализационная цена отходов (примем реализационную стоимость отходов ).
Рассчитаем значение стоимости отходов по формуле (7.8):
По формуле (7.6) рассчитаем себестоимость основных материалов:
Стоимость покупных изделий:
где с – число наименовании покупных изделии; - число покупных изделий каждого наименования шт; - цена покупного изделия определяемая как:
где – цена покупного изделия приведённая к 1 кг массы этого изделия; - масса покупного изделия; - число покупных изделий каждого наименования.
Составим таблицу 7.3. с помощью которой рассмотрим стоимость покупных изделий:
Наименование покупного изделия
Монтажные плиты (iso 1)
Монтажные плиты (iso 3)
Распределители (iso 1)
Распределители (iso 3)
Запорно-регулирующая арматура
Зарплата производственных рабочих с начислениями:
где – прямая зарплата производственных рабочих; – коэффициенты учитывающие доплаты и отчисления на дополнительную зарплату и в соцстрах ().
Прямая зарплата производственных рабочих:
где – количество исполнителей для производства изделия; – количество часов; - средняя часовая тарифная ставка по каждому виду работ.
Количество чел. час.
Ведущий инженер (координация работ)
Оператор станков с ЧПУ
ИТОГО: Прямая заработная плата
По формуле (7.11) рассчитаем заработную плату производственных рабочих с начислениями:
Рассмотрим затраты на возмещение износа инструментов и приспособлений целевого назначения. В данном случае затраты по этой статье себестоимости проектируемого изделия будут определяться стоимостью для изготовления дросселей.
Расходы по содержанию и эксплуатации оборудования определим косвенным путём:
где – процент расходов по содержанию оборудования по отношению к прямой зарплате производственных рабочих(.
Цеховые расходы включают затраты на содержание цехового персонала (ИТР служащих младшего обслуживающего персонала) амортизации текущего ремонта и содержанию зданий цеха сооружений инвентаря общецехового назначения и т.п.:
где – процент цеховых расходов по отношению к прямой зарплате производственных рабочих и расходам по содержанию и эксплуатации оборудования ().
В составе общезаводских расходов учитываются затраты по общему управлению предприятием: зарплата с начислениями персоналу заводоуправления амортизация содержание и текущий ремонт зданий сооружений и инвентаря общезаводского назначения конторские типографские и другие расходы.
При различном уровне механизации и автоматизации процессов изготовления отдельных изделий общезаводские расходы на единицу продукции:
где – процент общезаводских расходов по отношению к зарплате производственных рабочих и расходам по содержанию и эксплуатации оборудования ().
Для определения производственной себестоимости необходимо определить затраты на электроэнергию расходуемую на технологические цели:
где – средняя мощность оборудования кВт (); – общая сумма трудозатрат ч (); – тариф руб.кВт.ч ().
По формуле 7.6. почитаем себестоимость пневмосистемы:
Внепроизводственные расходы учитывают затраты связанные с реализацией готовой продукции:
где – производственная себестоимость пневмосистемы руб.; – внепроизводственные расходы по сравнению к производственно себестоимости изделия .
Полная себестоимость изделия:
Задавшись коэффициентом прибыльности 40 % оценим стоимость пневматической системы электролизера:
4. Расчет затрат на эксплуатацию пневмосистемы.
Затраты покупателя на покупку пневмосистемы определяется по формуле:
где – стоимость пневматической системы руб.; – сопутствующие затраты на транспортировку и установку ( – затраты на ввод в эксплуатацию ().
Система подготовки воздуха эксплуатируется 24 часа в сутки и 365 дней в году. Исходя из этого определим затраты на электроэнергию:
где – продолжительность эксплуатации (); – мощность компрессора (); – цена электроэнергии ()
Зарплата обслуживающего персонала рассчитывается по следующей формуле:
где – трудоемкость обслуживания ч в год () – тарифная ставка обслуживающего персонала (); – коэффициенты учитывающие доплаты и отчисления на дополнительную зарплату и в фонд социального страхования ().
Амортизационные отчисления за один год определяются по формуле:
Эксплуатационные затраты за год составляют:
Полные издержки определяются по формуле (7.22):
где – прочие издержки.
Благодаря внедрению новой системы производительность электролизера увеличивается на 15 процента. [27] С учетом что электролизер производит 2500 кгсутки а стоимость первичного алюминия 50 руб. Следовательно выручка с установки новой пневматической системы составит 684 357 руб.
5.Расчет экономической эффективности.
При оценке эффективности инвестиционного проекта соизмерение разновременных показателей осуществляется путем дисконтирования (приведения) их к ценности в начальном периоде. Для приведения разновременных затрат результатов и эффекта используется норма дисконта (Е) равная приемлемой для инвестора норме дохода на капитал. Для дисконтирования разновременные затраты результаты и эффект умножаются на коэффициент дисконтирования определяемый для постоянной нормы дисконта Е как:
где – номер шага расчета (t = 0 1 2 . T) Т – горизонт расчета.
Величина ЧДД для постоянной нормы дисконта вычисляется по формуле:
где – результаты достигаемые на t-ом шаге расчета - затраты осуществляемые на t-ом шаге расчета – горизонт расчета.
Если ЧДД инвестиционного проекта (за расчетный период) положителен проект является эффективным (при данной норме дисконта) и может рассматриваться вопрос об его принятии. Чем больше ЧДД тем эффективнее проект.
На практике часто пользуются модифицированной формулой для определения ЧДД. Для этого из состава исключаются капитальные вложения:
где – капитальные вложения на t-ом шаге К – сумма дисконтированных капиталовложений
Тогда формула ЧДД записывается в виде:
где - затраты на t-ом шаге расчета при условии что в них не входят капиталовложения.
Данные расчетов сведем в таблицу 7.5 и представим на рис. 7.1
Рис. 7.1. Дисконтирование нарастающим итогом
-ой период (до начала эксплуатации)
Норма дисконтирования
ставка рефинансирования (12)+инфляция (8) +риск (5)
Коэффициент дисконтирования
Эксплуатационные издержки
Выручка от реализации
Прибыль от реализации осн. продукции
Дисконтированный доход
Дисконтированное наростающим итогом
Чистый дисконтированный доход
ЭКОЛОГИЧНОСТЬ И БЕЗОПАСНОСТЬ
На человека в процессе его трудовой деятельности могут воздействовать опасные (вызывающие травмы) и вредные (вызывающие заболевания) производственные факторы. Опасные и вредные производственные факторы (ГОСТ 12.0.003-74) подразделяются на четыре группы: физические химические биологические и психофизиологические.
К опасным физическим факторам относятся: движущиеся машины и механизмы; различные подъемно-транспортные устройства и перемещаемые грузы; незащищенные подвижные элементы производственного оборудования (приводные и передаточные механизмы режущие инструменты вращающиеся и перемещающиеся приспособления и др.); отлетающие частицы обрабатываемого материала и инструмента электрический ток повышенная температура поверхностей оборудования и обрабатываемых материалов и т.д.
Вредными для здоровья физическими факторами являются: повышенная или пониженная температура воздуха рабочей зоны; высокие влажность и скорость движения воздуха; повышенные уровни шума вибрации ультразвука и различных излучений - тепловых ионизирующих электромагнитных инфракрасных и др. К вредным физическим факторам относятся также запыленность и загазованность воздуха рабочей зоны; недостаточная освещенность рабочих мест проходов и проездов; повышенная яркость света и пульсация светового потока.
Химические опасные и вредные производственные факторы по характеру действия на организм человека подразделяются на следующие подгруппы: общетоксические раздражающие сенсибилизирующие (вызывающие аллергические заболевания) канцерогенные (вызывающие развитие опухолей) мутогенные (действующие на половые клетки организма).
К биологическим опасным и вредным производственным факторам относятся: микроорганизмы (бактерии вирусы и др.) и макроорганизмы (растения и животные) воздействие которых на работающих вызывает травмы или заболевания.
К психофизиологическим опасным и вредным производственным факторам относятся: физические перегрузки (статические и динамические) и нервно-психические перегрузки (умственное перенапряжение перенапряжение анализаторов слуха зрения и др.).
Уровни воздействия на работающих вредных производственных факторов нормированы предельно-допустимыми уровнями значения которых указаны в соответствующих стандартах системы стандартов безопасности труда и санитарно-гигиенических правилах.
2.Метеорологические условия производственной среды
(температура воздуха относительная влажность воздуха скорость движения воздуха интенсивность
теплового излучения)
Микроклимат производственных помещений определяется сочетанием температуры влажности подвижности воздуха температуры окружающих поверхностей и их тепловым излучением. Параметры микроклимата определяют теплообмен организма человека и оказывают существенное влияние на функциональное состояние различных систем организма самочувствие работоспособность и здоровье.
Температура в производственных помещениях является одним из ведущих факторов определяющих метеорологические условия производственной среды.
Параметры микроклимата производственных помещений зависят от теплофизических особенностей технологического процесса климата сезона года условий отопления и вентиляции.
Тепловое излучение (инфракрасное излучение) представляет собой невидимое электромагнитное излучение с длиной волны от 076 до 540 нм обладающее волновыми квантовыми свойствами. Интенсивность теплоизлучения измеряется в Втм2. Инфракрасные лучи проходя через воздух его не нагревают но поглотившись твердыми телами лучистая энергия переходит в тепловую вызывая их нагревание. Источником инфракрасного излучения является любое нагретое тело.
Метеорологические условия для рабочей зоны производственных помещений регламентируются ГОСТ 12.1.005-88 "Общие санитарно-гигиенические требования к воздуху рабочей зоны" и Санитарными нормами микроклимата производственных помещений (СН 4088-86).
Получение алюминия характеризуется далеко неполной механизацией и автоматизацией производственных процессов и сопровождается выделением лучистого и конвекционного тепла.
Метеорологические условия в "старых" корпусах при использовании самообжигающихся анодов так и в современных корпусах оборудованных электролизерами с предварительно обожженными анодами выступают на первый план. Рабочие при обслуживании анодов и электролизных ванн постоянно подвергаются воздействию теплового облучения от открытой поверхности расплава и вторично нагретых предметов интенсивностью от 800 до 7000 ккалм2 ч. В летний период особенно на заводах расположенных в южных широтах микроклимат носит перегревающий характер. На рабочих местах температура воздуха достигает 40 - 45°С а в проходах цеха превышает наружную на 5 - 10°С.
Микроклимат в холодный период года (преимущественно на сибирских заводах) вследствие больших воздухообменов характеризуется низкими температурами воздуха и ограждений и повышенной подвижностью его в проходах. В холодные дни температура приточного воздуха поступающего через вентиляционные решетки в полу обычно отрицательная и превышает наружную всего на 8 - 9°С. Между рабочими местами и проходами наблюдается температурный перепад до 30°С.
При проектировании пневматической системы электролизера выборе оборудования важным фактором являлось плохие метрологические условия в которых должно работать оборудование. При этом сами пневматические устройства не влияют на микроклимат помещений.
3.Вредные химические вещества в производстве
Под вредным понимается вещество которое при контакте с организмом человека вызывает производственные травмы профессиональные заболевания или отклонения в состоянии здоровья. Классификация вредных веществ и общие требования безопасности введены ГОСТ 12.1.007-76.
Вредные вещества попадают в организм через органы дыхания желудочно-кишечный тракт и через кожный покров. Наиболее вероятно проникновение в организм веществ в виде газа пара и пыли через органы дыхания (около 95 % всех отравлений).
Выделение вредных веществ в воздушную среду возможно при проведении технологических процессов и производстве работ связанных с применением хранением транспортированием химически веществ и материалов их добычею и изготовлением.
Основой проведения мероприятий по борьбе с вредными веществами является гигиеническое нормирование.
Предельно допустимые концентрации (ПДК) вредных веществ в воздухе рабочей зоны установлены ГОСТ 12.1.005-88.
Снижение уровня воздействия не работающих вредных веществ или его полное устранение достигается путем проведения технологических санитарно-технических лечебно-профилактических мероприятий и применением средств индивидуальной защиты.
Алюминиевое производство характерно поступлением в воздушную среду фтористых соединений в виде пыли и газа глиноземосодержащей пыли окиси углерода возгонов каменноугольного пека. Что учитывается при проектировании пневмооборудования.
4.Шум на производстве
В производственных условиях источниками шума являются работающие станки и механизмы ручные механизированные инструменты электрические машины компрессоры кузнечно-прессовое подъемно-транспортное вспомогательное оборудование (вентиляционные установки кондиционеры) и т.д.
Допустимые шумовые характеристики рабочих мест регламентируются ГОСТ 12.1.003-83 "Шум общие требования безопасности" (изменение I.III.89) и Санитарными нормами допустимых уровней шума на рабочих местах (СН 3223-85) с изменениями и дополнениями от 29.03.1988 года №122-6245-1.
По характеру спектра шумы подразделяются на широкополосные и тональные.
По временным характеристикам шумы подразделяются на постоянные и непостоянные. В свою очередь непостоянные шумы подразделяются на колеблющиеся во времени прерывистые и импульсные.
Основные мероприятия по борьбе с шумом - это технические мероприятия которые проводятся по трем главным направлениям:
устранение причин возникновения шума или снижение его в источнике;
ослабление шума на путях передачи;
непосредственная защита работающих.
Наиболее эффективным средством снижения шума является замена шумных технологических операций на малошумные или полностью бесшумные однако этот путь борьбы не всегда возможен поэтому большое значение имеет снижение его в источнике. Снижение шума в источнике достигается путем совершенствования конструкции или схемы той части оборудования которая производит шум использования в конструкции материалов с пониженными акустическими свойствами оборудования на источнике шума дополнительного звукоизолирующего устройства или ограждения расположенного по возможности ближе к источнику.
Одним из наиболее простых технических средств борьбы с шумом на путях передачи является звукоизолирующий кожух который может закрывать отдельный шумный узел машины.
Значительный эффект снижения шума от оборудования дает применение акустических экранов отгораживающих шумный механизм от рабочего места или зоны обслуживания машины.
Применение звукопоглощающих облицовок для отделки потолка и стен шумных помещений приводит к изменению спектра шума в сторону более низких частот что даже при относительно небольшом снижении уровня существенно улучшает условия труда.
По нормам на алюминиевом заводе ПДУ уровень звука должен достигать 75 дбА при этом продолжительность воздействия составляет 92% от рабочей смены. Пневмооборудование при работе создает шум. Но как раз внедрение АПГ уменьшает время нахождения человека в электролитном цеху.
5.Вибрация в производстве
Вибрация - это механическое колебательное движение системы с упругими связями.
Вибрацию по способу передачи на человека (в зависимости от характера контакта с источниками вибрации) условно подразделяют на:
местную (локальную) передающуюся на руки работающего
общую передающуюся через опорные поверхности на тело человека в положении сидя (ягодицы) или стоя (подошвы ног). Общая вибрация в практике гигиенического нормирования обозначается как вибрация рабочих мест. В производственных условиях нередко имеет место сочетанное действие местной и общей вибрации.
Производственная вибрация по своим физическим характеристикам имеет довольно сложную классификацию.
По характеру спектра вибрация подразделяется на узкополосную и широкополосную; по частотному составу - на низкочастотную с преобладанием максимальных уровней в октавных полосах 8 и 16 Гц среднечастотную - 315 и 63 Гц высокочастотную - 125 250 500 1000 Гц - для локальной вибрации;для вибрации рабочих мест - соответственно 1 и 4 Гц 8 и 16 Гц 315 и 63 Гц.
По временным характеристикам рассматривают вибрацию: постоянную для которой величина виброскорости изменяется не более чем в 2 раза (на 6 дБ) за время наблюдения не менее 1 мин; непостоянную для которой величина виброскорости изменяется не менее чем в 2 раза (на 6 дБ) за время наблюдения не менее 1 мин.
Непостоянная вибрация в свою очередь подразделяется на колеблющуюся во времени для которой уровень виброскорости непрерывно изменяется во времени; прерывистую когда контакт оператора с вибрацией в процессе работы прерывается причем длительность интервалов в течение которых имеет место контакт составляет более 1 с; импульсную состоящую из одного или нескольких вибрационных воздействий (например ударов) каждый длительностью менее 1 с при частоте их следования менее 5 6 Гц.
Производственными источниками локальной вибрации являются ручные механизированные машины ударного ударно-вращательного и вращательного действия с пневматическим или электрическим приводом.
Инструменты ударного действия основаны на принципе вибрации. К ним относятся клепальные рубильные отбойные молотки пневмотрамбовки.
Основными нормативными правовыми актами регламентирующими параметры производственных вибраций являются: "Санитарные нормы и правила при работе с машинами и оборудованием создающими локальную вибрацию передающуюся на руки работающих" № 3041 -84 и "Санитарные нормы вибрации рабочих мест" № 3044-84.
Наиболее действенным средством защиты человека от вибрации является устранение непосредственно его контакта с вибрирующим оборудованием. Осуществляется это путем применения дистанционного управления промышленных роботов автоматизации и замены технологических операций.
По нормам локальная вибрации в электролитном цеху должна достигать не 126 дБ. Продолжительность воздействия 92 % от рабочей смены. Как и в случае с шумовым воздействием внедрение АПГ уменьшает нахождение человека на рабочем месте а установка винтовых компрессоров а не плунжерных введет к уменьшению вибрации.
6.Электромагнитные электрические и магнитные поля в производстве
Опасное воздействие на работающих могут оказывать электромагнитные поля радиочастот (60 кГц-300 ГГц) и электрические поля промышленной частоты (50 Гц).
Источником электрических полей промышленной частоты являются токоведущие части действующих электроустановок (линии электропередач индукторы конденсаторы термических установок фидерные линии генераторы трансформаторы электромагниты соленоиды импульсные установки полупериодного или конденсаторного типа литые и металлокерамические магниты и др.). Длительное воздействие электрического поля на организм человека может вызвать нарушение функционального состояния нервной и сердечно-сосудистой систем. Это выражается в повышенной утомляемости снижении качества выполнения рабочих операций болях в области сердца изменении кровяного давления и пульса.
Основными видами средств коллективной защиты от воздействия электрического поля токов промышленной частоты являются экранирующие устройства - составная часть электрической установки предназначенная для защиты персонала в открытых распределительных устройствах и на воздушных линиях электропередач.
Источником электромагнитных полей радиочастот являются:
в диапазоне 60 кГц - 3 МГц - неэкранированные элементы оборудования для индукционной обработки металла(закалка отжиг плавка пайка сварка и т.д.) и других материалов а также оборудования и приборов применяемых в радиосвязи и радиовещании;
Длительное воздействие радиоволн на различные системы организма человека по последствиям имеют многообразные проявления.
Наиболее характерными при воздействии радиоволн всех диапазонов являются отклонения от нормального состояния центральной нервной системы и сердечно-сосудистой системы человека. Субъективными ощущениями облучаемого персонала являются жалобы на частую головную боль сонливость или общую бессонницу утомляемость слабость повышенную потливость снижение памяти рассеянность головокружение потемнение в глазах беспричинное чувство тревоги страха и др.
Для обеспечения безопасности работ с источниками электромагнитных волн производится систематический контроль фактических нормируемых параметров на рабочих местах и в местах возможного нахождения персонала. Контроль осуществляется измерением напряженности электрического и магнитного поля а также измерением плотности потока энергии по утвержденным методикам Министерства здравоохранения.
Важное профилактическое мероприятие по защите от электромагнитного облучения - это выполнение требований для размещения оборудования и для создания помещений в которых находятся источники электромагнитного излучения.
Защита персонала от переоблучения может быть достигнута за счет размещения генераторов ВЧ УВЧ и СВЧ а также радиопередатчиков в специально предназначенных помещениях.
Экраны источников излучения и рабочих мест блокируются с отключающими устройствами что позволяет исключить работу излучающего оборудования при открытом экране.
Допустимые уровни воздействия на работников и требования к проведению контроля на рабочих местах для электрических полей промышленной частоты изложены в ГОСТ 12.1.002-84 а для электромагнитных полей радиочастот - в ГОСТ 12.1.006-84.
Электролитные цехи характеризуются наличием постоянных электромагнитных полей различной напряженности. Что оказывает неблагоприятное воздействие не только на человека но и на пневмооборудование правильный правильный подбор пневмосистем работающих в таких условиях позволяет уменьшить время нахождения человека в цеху.
7.Пожаробезопасность на предприятии
Пожар – неконтролируемое горение приводящее к ущербу и возможным человеческим жертвам. Опасными факторами пожара воздействующими на людей являются:
повышенная температура окружающей среды
токсичные продукты горения дым
пониженная концентрация кислорода
падающие части строительных конструкций станков агрегатов.
Основными причинами пожаров от электрического тока является короткое замыкание перегрузки электрических установок переходные сопротивления и искрения.
Причинами короткого замыкания могут неправильный выбор сечения и марки кабелей приводов износ и различные механические повреждения изоляций. Перегрузка электрических цепей вызывает нагрев электрических установок снижение диэлектрических свойств изоляции и ее воспламенение. Большие переходные сопротивления вызывают нарушения диэлектрических свойств изоляции и ее возгорание. Они как правило возникают когда проводники состоят из проводов разного сечения и разнородного материала а также плохого контакта между собой и коммуникационными аппаратами. Искрение происходит в момент разъединения находящихся под напряжением проводов включателей предохранителей и т.п.
Большую опасность представляет искрение в помещениях в которых имеется пожароопасная пыль. Пары легковоспламеняющихся жидкостей и горючие газы образующие с газом взрывоопасные концентрации а так же твердые легковоспламеняющиеся материалы (дерево бумага).
Во избежание пожаров от электрического тока необходимо чтобы электрические сети и электрооборудование отвечали требованиям правил технической эксплуатации электроустановок потребителей и правил ТБ.
Согласно с правилами устройства электроустановок не допускается прохождение воздушных линий электропередачи и электропроводов над сгораемыми кровлями навесами и т.д.
Причинами пожаров могут быть так же курение в неположенном месте. Несоблюдение норм техники безопасности при появлении на рабочем месте в нетрезвом состоянии.
Освещение – использование световой энергии солнца и искусственных источников света для обеспечения зрительного восприятия окружающего мира.
Свет имеет различные физические характеристики: световой поток (мощность лучистой энергии по производимому ею зрительному ощущению измеряется в люменах [лм] –световой поток испускаемый точечным источником в телесном угле в 1стерадиан (телесный угол вырезающий на поверхности сферы площадь равную квадрату ее радиуса) при силе света 1кандела (единица силы света)).
Сила света: световой поток распространяющийся внутри телесного угла равного 1 стерадиану [кд - кандела].
Освещенность (Е): распределение светового потока (Ф) на поверхности площадью S. Освещенность (Е) измеряют в люксах лк – это освещенность поверхности S=1м световым потоком Ф=1лм.
С точки зрения гигиены труда освещенность имеет существенное значение т.к. по ней нормируются условия освещения в производственных помещениях и рассчитываются осветительные установки. В физиологии зрительного восприятия важен также уровень яркости освещаемых производственных и других объектов которая отражается от освещаемой поверхности в направлении глаза. Яркость зависит от их световых свойств степени освещенности и угла под которым поверхность рассматривается измеряется в нитах [нт]. Частые изменения уровней яркости приводят к снижению зрительных функций развитию переутомления вследствие переадаптации глаза а зрительное утомление приводит к снижению зрительной и общей работоспособности (Адаптации: световые – при повышении яркостей в поле зрения происходит быстро в течение 5-10 мин.; темновые – приспосбление глаза к низким уровням яркости в течение 05-2часов).
В помещениях с электролизными установками со взрывоопасными зонами для электрического освещения как правило должны применяться комплектные осветительные устройства со щелевыми световодами (КОУ). Источники света в этих устройствах помещаются в камеры входящие в состав КОУ. Сочленение камер со световодами должно обеспечивать степень защиты световодов со стороны камер не ниже IP 54. Камеры КОУ должны размещаться вне взрывоопасной среды в стене граничащей с соседним невзрывоопасным помещением или в наружной стене.
Помимо КОУ рекомендуется использование светильников общего назначения устанавливаемых:
за неоткрывающимися окнами с двойным остеклением без фрамуг и форточек;
в специальных нишах с двойным остеклением в стене;
в специальных фонарях с двойным остеклением в потолочном перекрытии;
в остекленных коробах.
Ниши и фонари должны иметь вентиляцию наружным воздухом с естественным побуждением.
Остекленные короба должны продуваться под избыточным давлением чистым воздухом. В местах где возможны поломки стекол в коробе для остекления следует применять небьющееся стекло.
Стационарное местное освещение в цехах (корпусах залах) электролиза как правило не требуется
9.Действие электрического тока на работу человека на промышленных предприятиях
Действие электрического тока на живую ткань в отличие от других материальных факторов носит своеобразный и разносторонний характер. Проходя через организм электрический ток оказывает термическое электролитическое и биологическое действие.
Термическое воздействие заключается в нагреве тканей и биологических сред организма что ведет к перегреву всего организма и как следствие нарушению обменных процессов и связанных с ним отклонений.
Электролитическое воздействие заключается в разложении крови плазмы и прочих физиологических растворов организма после чего они уже не могут выполнять свои функции.
Биологическое воздействие связано с раздражением и возбуждением нервных волокон и других органов.
Любое из этих действий тока может привести к электрической травме т.е. к повреждению организма вызванному воздействием электрического тока или электрической дуги.
К помещениям с повышенной опасностью относятся помещения с повышенной влажностью (более 75%) или высокой температурой (выше 35oС). При наличии токопроводящих пыли и полов а также при наличии возможности одновременного прикосновения к элементам соединенным с землей и металлическим корпусам электрооборудования помещение относится к классу повышенной опасности.
Помещения с высокой относительной влажностью (близкой к 100%) химически активной средой или одновременным наличием двух и более условий соответствующих помещениям с повышенной опасностью называют особо опасными.
Средства и способы защиты человека от поражения электрическим током сводятся к следующему:
уменьшению рабочего напряжения электроустановок;
выравниванию потенциалов (заземление зануление);
электрическому разделению цепей высоких и низких напряжений;
увеличению сопротивления изоляции токоведущих частей (рабочей усиленной дополнительной двойной и т. п.);
применению устройств защитного отключения и средств коллективной защиты (оградительных блокировочных сигнализирующих устройств знаков безопасности и т. п.) а также изолирующих средств защиты.
Электролизные установки работают на постоянном токе который получают от преобразовательных подстанций выпрямляющих трехфазный переменный ток. Электролитные ванны относятся к электроприемникам I категории по степени надежности электроснабжения. По опасности поражения людей электрическим током помещения электролиза относятся к помещениям с повышенной опасностью.
10.Очистка отходящих газов от электролизера
При производстве алюминия очистке промышленных выделений уделяют первостепенное значение. В выборе типа и конструкции электролизера решающими факторами являются минимальное количество выделяемых при электролизе вредных веществ и возможность улавливания их в максимально концентрированном виде. Отходящие от электролизера газы захватывают частицы порошкообразного сырья в основном мелкие фракции глинозема.
Назначение газоочистки — отделить вредные составляющие и пыль от основной массы газов.
Применяют различные системы газоочистки состоящие из одной двух и более ступеней. Назначение и аппаратурное оформление ступеней системы газоочистки различно. Па первой ступени газовая смесь очищается от механических включений (пыли) и смолистых составляющих образующихся в результате коксования пека. Затем от газообразной части отделяются вредные составляющие. Для улавливания и выделения ценных фтористых соединений чаще всего применяют содовый раствор который по мере обогащения фтористыми солями поступает в специальные отделения и цехи для регенерации фтора. При взаимодействии соединений фтора с алюминатным раствором фтор переходит в твердое состояние; образующееся соединение отвечает но составу формуле криолита Na3AlF6.
Для улавливания пыли и смолистых составляющих применяют электрофильтры специальной конструкции охлаждающие электроды которых оборудованы гидросмывом. Уловленная в электрофильтрах пыль в виде шламов поступает на дальнейшую переработку для извлечения из нее ценных составляющих. Для улавливания пыли могут быть применены и мультициклоны.
Для очистки газов от фторсодсржащих компонентов применяют различные аппараты мокрой очистки в которых фтористые соединения переводятся в раствор. Наиболее часто применяют скрубберы и цепные аппараты работающие по принципу противотока. Раствор в виде распыленной взвеси или пены постепенно обогащаясь фтористыми соединениями движется сверху вниз а газы—снизу вверх и по мере очистки выбрасываются через вентиляционные трубы.
Системы газоочистки объединяют с системами вытяжной вентиляции располагают как правило между вентиляторами создающими разрежение в системе вытяжной вентиляции и вентиляционными трубами. Аппараты газоочистки располагают последовательно на свободном пространстве между корпусами электролиза.
Рис. 9.1 Расположение газоочистных аппаратов
Число аппаратов для очистки газов или число секций в аппарате входящих в один блок подбирают по производительности с таким
расчетом чтобы обеспечить постоянную очистку всего объема поступающих газов. Перед остановкой на чистку или ремонт одной
секции пли одного аппарата к работе подключают резервные чем и достигается непрерывность очистки газов. В отечественной практике наибольшее распространение получило расположение газоочнстных аппаратов приведенное на рис.9.1.
Системы газоочистки корпусов оборудованных непрерывными самообжигающимися анодами с верхним подводом тока состоят
как правило из трех ступеней. В первой ступени (в “горелке” газосборного колокола) сгорают уловленные смолистые составляющие коксования анода и дожигается угарный газ до углекислого.
Во второй ступени (обычно в электрофильтре) улавливается пыль и несгоревшие в “горелках” остатки продуктов коксования.
В третьей ступени улавливаются фторсодержащие и серосодержащие составляющие газа. Для этого широкое распространение получили пенные аппараты различных конструкций.
Избирательное действие отдельных ступеней газоочистки позволяет повысить общую степень очистки газов и снизить трудовые затраты на обслуживание системы. Например при очистке газов в одну ступень только на аппаратах “мокрой” очистки эти аппараты быстро забиваются пылью что резко снижает степень очистки и приводит к частым остановкам для извлечения накопившейся твердой фазы. Эта операция очень трудоемка и практически не поддается механизации.
В последнее время все большее распространение получают системы так называемой сухой очистки газов. Принцип действия таких систем основывается на избирательной способности некоторых твердых реагентов улавливать (адсорбировать) фторсодержащие составляющие промышленного газа. Наиболее эффективно применение таких систем для очистки газов не содержащих смолистых составляющих. Такие газы улавливают газосборными устройствами электролизеров с предварительно обожженными анодами.
В качестве улавливающего реагента как правило применяют специально приготовленный глинозем с относительно малым содержанием составляющей α и разветвленной поверхностью зерен.
Перечисленными выше способами осуществляется очистка достаточно концентрированных газов организованного газоотсоса.
При высоких темпах роста производства алюминия для надежной охраны окружающей среды в последнее время все чаще стали применять системы сводящие до минимума выделение вредных составляющих промышленных газов в атмосферу через аэрационные фонари корпусов электролиза алюминия. Такие системы получили название “фонарной” газоочистки (рис.9.2). Принцип улавливания вредных составляющих газа в системах такого типа заключается в пропускании всего объема выходящих из корпуса газов через газопоглощающий раствор подаваемый в аэрационный фонарь форсунками специальной конструкции в виде мелкодисперсной взвеси. Соприкасаясь с частицами раствора фтористые соединения растворяются в нем. Для увеличения контактной поверхности и сокращения брызгоуноса на пути газа устанавливают несколько рядов решеток.
Рис. 9.2. Фонарная газоочистка
Когда фонарь корпуса используют для улавливания вредных составляющих газа его выполняют герметичным. Для создания необходимого разрежения применяют вентиляторы которые устанавливают либо на строительных конструкциях фонаря корпуса либо в специальных помещениях между корпусами. В первом случае устанавливают много вентиляторов малых размеров во втором — высокопроизводительные вентиляторы больших размеров вес которых не лимитируется прочностью несущих конструкций здания корпуса. Число таких вентиляторов выбирают на основании их производительности с учетом обеспечения непрерывного отсоса из корпуса требуемого объема газа.
При установке вентиляторов на здании корпуса вся система по очистке газов располагается около фонаря. При установке вентиляторов между корпусами очистку газов можно организовать как под фонарем корпуса так и после вентиляторов в специальных гaзоочистных аппаратах с применением различных схем их компоновки. В зимнее время и газоулавливающие растворы таких систем добавляют различные антифризные добавки (препятствующие замерзанию раствора). Насыщенные фтористыми соединениями растворы направляют на регенерацию.
Основным недостатком систем “фонарной” газоочистки кроме сложности изготовления и больших капитальных и эксплуатационных затрат на сооружение и обслуживание является ограничение кратности обмена воздуха внутри корпуса что приводит к ухудшению условий труда. Перспективными для “фонарной” газоочистки могут оказаться сухие способы улавливания газа.
11.Техника безопасности работы с компрессорами высокого давления
Одним из главных элементов пневмосистемы электролизера является компрессорная установка. Для безопасного использования установки необходимо выполнение некоторых правил.
Установка и подготовка к работе. Уровень шума компрессора измеренный в открытом пространстве может оказаться более высоким если место где установлен компрессор окружено стенами которые отражают звук. Это необходимо учесть при выборе места установления компрессора.
Воздух забираемый в компрессором должен быть сухим и прохладным. Необходимо избегать забора загрязненного воздуха из окружающей среды либо уже раннее проциркулированного воздуха так же окружающий воздух не должен содержать взрывоопасных газов.
Особое внимание должно быть уделено пневматическим соединениям. Излишне свободное или неправильное подсоединение шлангов может стать причиной повреждения компрессора. Перед отсоединением шлангов необходимо сбросить избыточное давление. Ресиверы должны соответствовать местным нормам для емкостей работающих под давлением. Электрические соединения должны быть выполнены сертифицированными квалифицированными специалистами. Во время проведения работ по подсоединению следуйте инструкциям по технике безопасности.
В водном конденсате может содержаться небольшое количество масла.
Направление потока сжатого воздуха на кожу.
Работы компрессора при открытых съемных панелях. Используйте исключительно рекомендованные виды масел.
Смешивания различные виды масел без согласования с заводом изготовителя.
Компрессоры работающие при использовании пульта дистанционного управления должны быть снабжены специальными информационно-предупредительными табличками в которых должен быть указан метод запуска.
Техническое поддержание. Все работы по техническому поддержанию компрессора должны выполняться только после обесточивания и отсоединения компрессора от линии сжатого воздуха. Прежде чем начать работы по техническому поддержанию необходимо убедиться что фильтр сепаратора не находится под давлением. Все вносимые изменения должны согласовываться с заводом изготовителем и соответствовать нормам разработанных для агрегатов работающих под давлением.
Во время проведения работ по техническому поддержанию особое внимание должно уделяться пульту дистанционного управления при использовании мультикомпрессорной системы. Нельзя пренебрегать регулярными проверками и работами по техническому поддержанию компрессора.
Подъем компрессора. При подъеме компрессора следует учитывать центр тяжести. Тросы используемые для подъема не должны давить на корпус компрессора.
Передвижение компрессора форклифтом. Необходимо соблюдать особую предосторожность во время подъема и транспортировки.
Вилообразные держатели должны подводиться под компрессор как показано на рисунке.
Компрессор должен быть установлен на ровной поверхности принимая во внимание вес агрегата.
Помещение где устанавливается компрессор должно хорошо вентилироваться.
Электрическое подсоединение. Электрическое подсоединение должно выполняться в соответствии с международными нормами (IEC). Кроме того должны соблюдаться все местные нормы безопасности.
Необходимо чтобы напряжение электрической сети соответствовало необходимому. Колебания напряжения не должны превышать 5%.
Необходимо использовать отдельный автоматический распределительном щите.
Особенно важно правильно произвести заземление.
Работы по электрическому подключению могут выполняться только сертифицированными специалистами.
Первый запуск компрессора. Если компрессор не использовался в течении длительного периода времени необходимо проверить масло и натяжение приводных ремней.
Уровень масла в фильтре-сепараторе должен находится в обозначенных предеделах.
Необходимо кратковременно включить компрессор для проверки направления вращения роторов (держать включенным не более 2 секунд). Для немедленного отключения агрегата воспользоваться кнопкой аварийной остановки. Правильное направление вращения обозначено стрелкой на кожухе приводных ремней. Неверное направление вращения может вызвать поломку компрессора. Направление вращения необходимо проверять при любом переподключении компрессора к системе электроснабжения.
Закрыть съемные панели компрессора.
Включить главный выключатель компрессора. Если компрессор не включается выяснить причину (см. возможные неисправности).Не открывайте съемные панели во время работы компрессора.
Необходимо отрегулировать давление на выходе установив давления включения и остановки компрессора в соответствии с допустимым давлением модели.
Проверить уровень масла
Включить главный выключатель
Открыть запорный клапан на выходе из компрессора
Нажать на кнопку включения «I»
Нажать на кнопку выключения «0»
Подождать 1 минуту до полной остановки компрессора
Закрыть запорный клапан
Отключить главный выключатель
Экстренная остановка
Компрессор остановится немедленно после нажатия кнопки аварийной остановки
Для повторного включения компрессора поверните кнопку аварийной остановки по часовой стрелке. Снимите аварийный сигнал на контрольной панели. Затем запустите компрессор в обычном порядке.
Техническое обслуживание. Меры предосторожности при проведении технического обслуживания
Остановить компрессор и убедиться что фильтр-сепаратор не находится под давлением. Функция разгрузки позволяет снизить давление в ресивере до атмосферного. После остановки подождать не менее 2-х минут.
Отключить подачу электричества посредством главного выключателя и убедитесь что компрессор не может быть включен случайно.
Компрессоры управляемые пультом дистанционного управления должны быть снабжены соответствующей табличкой «НЕ ВКЛЮЧАТЬ РАБОТАЮТ ЛЮДИ»
Закрыть запорный клапан на выходе из компрессора.
Откройте заливную горловину на фильтре сепараторе.
Процедуры после проведения работ по техническому поддержанию
Закрыть заливную горловину.
Открыть запорный клапан.
Включить компрессор.
Возможные неисправности и их способы устранения см. в табл. 8.2[30].
Компрессор не пускается
Нажата кнопка аварийного выключения
аварийной остановки по часовой стрелке для включения.
недостаточное напряжение электросети.
электроподключение и плавкие вставки.
Компрессор остановился из-за перегрузки из-за высокой температуре масла
Высокая температура в помещении
Неправильно подобрано масло или низкий уровень масла
Продолжение табл. 8.2.
Проверить соединения
Проверить контакты пускателей
Проверить электронную контрольную панель
Компрессор остановился из-за перегрузки по высокому давлению
Не работает управляющий клапан впускного клапана. Заменить.
Проверить открытие запорного клапана на воздушной магистрали
Повреждение уплотнения впускного клапана. Заменить
Сломана пружина впускного клапана. Заменить
Загрязнён воздухо-масляный сепаратор. Заменить
Неисправен прессостат. Заменить.
Компрессор включается но не загружается
Давление в системе выше давления запуска
Неисправность системы управления впускным
Проверить соединения. Заменить при
Сообщить в сервисную службу
минимального давления
загружается срабатывает предохранительный
Неисправность системы управления впускным
Проверить соединения. Заменить при
Неисправность прессостата
Недостаточная производитель-
Неправильно подобран компрессор. Требуется более мощный.
Загрязнён воздушный фильтр
Недостаточное натяжение ремней.
отрегулировать механизм натяжения ремней
разгрузочного предохранительного или дренажного клапана
Прочистить или заменить
Проверить систему на предмет протечек
Неправильная настройка дренажного клапана
Проверить настройки на электронной контрольной панели
Высокая температура
Обеспечить циркуляцию воздуха
Не допускать попадания холодного охлаждающего воздуха в компрессор
Высокая температура масла на выходе из винтового блока.
Большой расход масла
Неисправен винтовой блок
Высокая температура в
Обеспечить вентиляцию помещения
Низкий уровень масла
Неподходящий тип масла в компрессоре
рекомендованный тип масла
Загрязнён охладитель масла
Загрязнен масляный фильтр
Неисправен сепаратор масла
Засорена трубка возврата масла
Низкое рабочее давление
давление в соответствии с указаниями в паспорте
Высокий уровень масла
Неподходящий тип масла
рекомендуемый тип масла
Окончание табл. 8.2.
уплотнения винтового блока
Высокая температура масла на выходе из винтового блока
Выяснить и устранить причины
Течь масла из воздушного фильтра после остановки компрессора
Не герметичность впускного клапана
Заменить воздушный фильтр
Компрессор пускается слишком медленно
находится в открытом
Недостаточное напряжение в электросети
Устранить неполадки в сети
Компрессор слишком много работает вхолостую
Система сжатого воздуха мала
Изменить систему при
необходимости. (добавить дополнительно
Установлен слишком узкий диапазон давления
ТЕХНОЛОГИЯ СБОРКИ ШКАФА УПРАВЛЕНИЯ
Оборудование для управления пневмоцилиндрами устанавливается в шкафе управления. Расмотрим последовательность установки оборудования:
На первом этапе набираются монтажные плиты требуемого типоразмера и количества согласно пневмосхеме. Для цилиндров-пробойников используются плиты NAV-12-3-ISO см. рис. 9.1 для цилиндров дозаторов NAV-14-1-ISO см. рис. 9.2
Рис. 9.1. Соединение монтажных плит NAV-12-3-ISO
Рис. 9.2. Соединение монтажных плит NAV-14-1-ISO
Соединение плит NAV-12-3-ISO и NAV-14-1-ISO происходит с помощью болтов М8х1х30 и М5х08х20 соответственно при этом между плитами вставляются заглушки для отделения потока воздуха (см. рис. 9.3 и рис. 9.4).
Рис. 9.3. Скресление монтажных плит NAV-12-3-ISО
Рис. 9.4. Скрепление монтажных плит NAV-14-3-ISO
Соединив плиты в них вворачиваются штуцера с предварительно надетыми резиновыми кольцами и заглушки так же с кольцами. Обозначение элементов (см. на рис. 9.5 и на рис. 9.6).
Рис. 9.5. Установка штуцеров и заглушек на монтажные плиты
Рис. 9.6. Установка штуцеров и заглушек на монтажные плиты
На плиты устанавливается аппаратура указанная на принципиальной схеме. После установки все блоки скрепляются болтами (см. рис. 9.7 и 9.8).
Рис. 9.7.Установка аппаратуры на монтажные плиты
Рис. 9.8.Установка аппаратуры на монтажные плиты
Собранные блоки устанавливается на плиту в которой по чертежам просверливают отверстия диаметром 12 мм и 10 мм для блоков типа ISO3 отверстия диаметром 6 и 8 мм для блоков ISO 1 и отверстия диаметром 14 мм для крепления плиты в шкаф (см. рис. 9.9). На плиту устанавливается аппаратура и крепится болтами М10х15х80 (для ISO 3) и М8х1х40 (для ISO 3) и М6х1х60 (для ISO 3) и М5х08х30 (для ISO 3) (см. рис. 9.10)
Рис. 9.9. Отверстия в плите
Рис. 9.10. Установка блоков на плите
Медные трубы для подсоединения к блокам ISO 3 соединяются пайкой и с помощью фитингов. Рассмотрим особенности пайки.
Пайка — технологическая операция применяемая для получения неразъёмного соединения деталей из различных материалов путем введения между этими деталями расплавленного материала (припоя) имеющего более низкую температуру плавления чем материал (материалы) соединяемых деталей.
Спаиваемые элементы деталей а также припой и флюс (вещества (чаще смесь) органического и неорганического происхождения предназначенные для удаления окислов с поверхности под пайку иили защиты от вредного влияния атмосферы) вводятся в соприкосновение и подвергаются нагреву с температурой выше температуры плавления припоя но ниже температуры плавления спаиваемых деталей. В результате припой переходит в жидкое состояние и смачивает поверхности деталей. После этого нагрев прекращается и припой переходит в твёрдую фазу образуя соединение. Прочность соединения во многом зависит от зазора между соединяемыми деталями (от 003 до 2 мм) чистоты поверхности и равномерности нагрева элементов. Для удаления оксидной плёнки и защиты от влияния атмосферы применяют флюсы.
Технология процесса пайки.
Очистить соединяемые детали
Подвергнуть детали процессу лужения
Закрепить детали с соблюдением требуемого зазора и нахлеста
Нагреть детали факелом пламени. Нагревание происходит в зоне 25—30 мм от центра спайки. Больше нагревать надо детали имеющие большую (по сравнению с другой соединяемой деталью) толщину и теплопроводность.
Когда место спая нагрето факелом горелки до температуры растекания припоя нанести флюс.
Припой разогреть и тоже окунуть во флюс. Когда флюс на припое расплавился ввести припой в место спая и расплавлять его путем касания разогретых ранее деталей но ни в коем случае не плавить припой в пламени горелки. Высокотемпературная пайка производится газовым пламенем нормального состава. Возможен небольшой избыток горючего. Удельная мощность пламени (по ацетилену) принимается [л(ч мм)]: для углеродистой стали — 100—200 нержавеющей стали не более 70 меди— 150—200 латуни—100—120.
Закончив пайку пламя надо отвести в сторону и дать соединенным деталям остыть естественным путем не пытаясь ускорить процесс охлаждения. Затем надо очистить шов от флюса ветошью с использованием теплой воды.
Соединение фитингами осуществляется по следующее технологии:
Рис. 9.11. Удаление грязи и заусенцев
Рис. 9.12. Одевание на трубу гайки и нипеля
Рис. 9.13. Труба вставляется в ответную часть фитинга и затягивается до упора
В результате пайки и соединением фитингами получаем напорный и выхлопной трубопровод для блоков ISO3(см рис.9.14). Смонтированные трубопроводы крепятся с помощью гайки и ниппеля к штуцерам. Уплотнение обеспечивается за счет герметика. В шкафу высверливаются отверстия для подвода отвода воздуха и для подачи его к пневмоцилиндрам и в него вставляется собранная плита которая крепится к шкафу с помощью четырех болтов М12х125х30. В шкаф крепится датчик давления (см. рис 9.15).
Рис. 9.14. Напорный и выхлопной трубопровод
Рис. 9.15. Шкаф в сборе
После установки аппаратуры в шкаф монтируются гибкие шланги PAN-8х15-SI.
Штуцер установленный в монтажные плиты типа ISO1 имеет вид показаны на рис. 9.16. Монтаж происходит следующим образом: Шланг 2 вставляется в разъем нажимного соединения соединение самозажимается.
Рис. 9.16. Напорный и выхлопной трубопровод
Шланги нужно располагать и соединять таким образом чтобы избежать резких перегибов которые могут привести к разрыву. В прилож. 14 показаны правильные и неправильные примеры соединения шлангов.
После установки пневматического оборудования производится установка электрического оборудования и разводка и маркировка кабелей.
Когда шкаф полностью собран необходимо проверить герметизацию оборудования. Существует несколько способов определения герметичности один из них метки флюорицентной радиацией. Он заключается в следующем: система заполняется сжатым воздухом который содержит газообразный люминофор. В шкафу устанавливают ультрафиолетовое излучение. В местах негерметичности происходят утечки воздуха а за счет содержания в сжатом воздухе частиц люминофора происходит свечение. Таким образом определяются места утечек.
После окончательной проверки шкафа и устранения всех неисправностей на шкаф наклеивается табличка с номером проекта и пневматической схемой.
В проекте была рассмотрена пневматическая система электролизера пробойника.
При анализе системы были рассмотрены существующие пневматические устройства применяемые для алюминиевой промышленности у различных производителей. Показаны особенности аппаратуры применяемой на фирме Festo и эволюция в определении положения штока.
На этапе выбора схемы системы подготовки воздуха были рассмотрены необходимые составные части системы и по показателям качества и конкурентоспособности были выбраны устройства обеспечивающие требования технического задания. В результате были предложены 2 схемы основанные на применении винтового компрессора. Особенностями и преимуществами данных схем является: индивидуальное питание электролитных ванн уменьшение шума работы системы повышение качества воздуха уменьшение эксплуатационных расходов. Для случая индивидуального питания были рассчитаны параметры системы: давление компрессора 13 бар производительностью 19 м³мин и мощностью 15 кВт пропускная способность пневматических устройств подготовки воздуха 3456лмин пропускная способность равная 3270 лмин и 190 лмин для пневмоаппаратуры цилиндров пробойников и цилиндров дозаторов соответственно.
Для повышения надежности системы подготовки сжатого воздуха был введен блок состоящий из пневматического распределителя и двух фильтров. Введение такого элемента в систему позволяет сократить простои в производстве и уменьшить убытки.
В дипломном проекте была построена математическая модель описывающая изменение хода от времени давления в поршневой и штоковой полости. В результате решения были получено что опускание происходит за 31 в случае отсутствия алюминиевой корки и за 32 с при образовании корки. Используя эту модель возможно определять положение корки не использую сложных и дорогостоящих устройств.
Пневматическое оборудование управления пневмоцилиндрами было размещено в 1 шкафе управления. Для системы определения положения штока был сконструирован регулируемый дроссель имеющий простую конструкцию и позволяющий менять пределы регулирования проходного сечения в широких пределах.
В экономической части была рассмотрена экономическая эффективность применения пневматической системы. По полученным данным система окупится в течении одного года а чистый дисконтированный доход достигнет 1127077 у.е. на 5 году использования системы.
В части по безопасности и экологичности были рассмотрены основные факторы влияющие на здоровье человека на предприятии. Описаны способы очистки отходящих газов от электролизера. Необходимо отметить что система подготовки воздуха не наносит вред здоровью. Описана техника безопасности работы с компрессорами высокого давления.
В технологической части были описаны особенности сборки шкафа управления. Так же были рассмотрены особенности пайки и проверки шкафа на герметичность.
В дипломном проекте были рассмотрены все поставленные задачи.
Монтаж наладка и эксплуатация пневматических приводов и устройств А.И. Кудрявцев А.П.
Гидроприводы. Гидро – пневмоавтоматика станков. В.А. Федорец. М.Н. Педченко. А.Ф. Пичко – Вица. Школа 1973
Зуев Ю.Ю. Основы создания конкурентоспособной техники и выработки эффективных решений – М.: Издательский дом МЭИ 2006
Гессе С. Сжатый воздух как носитель энергии. Подготовка и распределение. – ДП «Фесто» 2004
Охрана труда. Учебник для электротехнических специальностей вузов Ред. Б. А. Князевский . - 2-е изд. перераб. и доп. - М. : Высшая школа 1982 . - 311 с.
Инженерная экология. Учебник для вузов по электротехническим и электроэнергетическим специальностям Ред. В. Т. Медведев . - М. : Гардарики 2002 . - 687 с.
Евтушенко Н.Г. Кузьмин А.П. «Безопасность жизнедеятельности в условиях чрезвычайных ситуаций» М. 94.
«Анализ несчастных случаев на производстве. Охрана труда. практикум» 982 М
Тенденции в автоматизации. № 3. Январь 2007. Пневматика в Алюминиевой промышленности.
Паспорт пневмопробойника
Общие сведения о компании Объединенная компания
«Российский алюминий».
Заводы принадлежащие «Российскому алюминию»
Производство алюминия
Производство глинозема
Производство тары упаковки и проката
Десятка компании-мировых лидеров по производству алюминия
Оборудование фирмы SMC
Пневматический цилиндр
Применяется в качестве привода с усилием до 68500Н
В стандартном исполнении предусмотрено воздушное демпфирование конечных положений
Возможно исполнение с двусторонним штоком
Прочная конструкция корпуса
Потери на трение не более 5%
Пнемо-гидро исполнение
Технические характеристика см. в табл. 2.1
Резьба поршневого штока
Допуски по длине хода (мм)
До 25+1.00. до 1000 +1.4-0. до 1500 +1.80. до 2000 +2.2-0. до 2400 +2.6-0
Очищенный сжатый воздух с содержанием масла или без него
Температура окружающей среды (°С)
Скорость хода поршня (ммс)
Продолжение прилож. 2
Максимально возможная длина хода цилиндра (мм) см табл. 2.2.
пневмораспределитель с прямым управлением
Притертый стальной золотник
Высокая надежность долгий срок службы
Сохранение работоспособности в тяжелых условиях: при сильной загрязненности рабочей окружающей среды; при повышенной и пониженной температуре
Высокая пропускная способность
Быстрое срабатывание благодаря низкому трению и короткомуходу золотника
Технические характеристики см. табл. 2.3
Рабочее давление (МПа)
Рабочая температура (°С)
Вспомогательноеручное управление
Электрический подвод
В пост. тока 220 В переменного тока
В или эквивалентный (130°С)
Макс. частота 220VAC
Срабатывания (Гц) 24 VDC
Индикатор рабочего состояния
Стандартное исполнение
Магистральный фильтр
Предназначен для удаления из сжатого воздуха твердых частиц а также водяного и масляного конденсата. Принцип действия основан на эффекте слияния мелких капель в более крупные в фильтрующем элементе (явление коалесценции). Образовавшиеся крупные капли оседают на стенках фильтрующего элемента и стекают на дно резервуара.
Продолжительный срок службы
Создает минимальный перепад давления
Легкая замена фильтрующего элемента
Большой объем резервуара
Оборудование фирмы Festo
Конструкция цилиндра
на пневмоцилиндры-пробойники корки для алюминиевой
промышленности типа D SA .
по ГОСТ 12.2.101 ГОСТ 12.3.001 ГОСТ 12.2.003
DIN ISO 6431 VDMA 24562 NFE 49003.1
Назначение и номенклатура
Пневмоцилиндры-пробойники предназначены для работы на очищенном при необходимости осушенном сжатом воздухе не содержащем распыленное масло.
Базовая версия пневмоцилиндра – пробойника имеющая специальный индекс в наименовании (D 200- -SA-27060 и D 160- -SA 210414 для диаметра штока 40мм D 200- -S1-SA 27087 для диаметра штока 50мм) определяет неизменными основные геометрические размеры и технические характеристики пневмоцилиндра как приводного механизма и является основой для производных версий с интегрированным управляющим распределителем различными датчиками определения положения поршня автоматической системой энергосбережения и пр. Каждой перечисленной версии присваивается свой специальный индекс SA.
По желанию пользователей могут производится изменения существующих и создание новых версий пневмоцилиндров-пробойников.
Каждый пневмоцилиндр-пробойник снабжается идентификационным шильдом содержащим официальный номер для заказа точное номенклатурное наименование изделия и идентификационный номер характеризующий дату производства согласно нижеследующим принципам (см. табл. 4.1 и см. табл. 4.2):
-год производства – первая буква латинского алфавита в номере
-месяц производства – цифра от 1 до 9 или буква латинского алфавита после идентификации года производства
Продолжение прилож. 4
Пневмоцилиндры-пробойники разработаны и используются в качестве приводов механизмов пробивающих оксидную корку на электролизерах производств первичного алюминия различных типов. Могут использоваться в качестве элемента толкающего тянущего или удерживающего усилия для любых других промышленных применений требующих долговременной устойчивости к высокой температуре химической и абразивной агрессивности окружающей среды повышенного уровня допустимых механических нагрузок.
Правила эксплуатации
Качество очистки сжатого воздуха задается по DIN ISO8573-1 при этом сжатый воздух должен быть очищен не грубее класса загрязненности 5.3.4 для возможного присутствия минеральных и синтетических масел и класса 5.3.2 для возможного присутствия эфирных масел.
Пневмоцилиндры типа D -SA обеспечены заводской смазкой на весь срок службы пневмоцилиндра и не требуют дополнительной смазки при условии выполнения требований к питающему воздуху а также при условии что в рабочее тело в процессе эксплуатации не проникают посторонние смазочные материалы (например масло из компрессора) которые способны вымывать заводскую смазку.
Для регулирования скорости движения поршня пневмоцилиндра применяются пневматические дроссельные клапаны устанавливаемые на линиях подвода к пневмоцилиндру. Минимальная величина равномерной скорости движения составляет 15 20 ммсек а максимальная – 05 мс.
Пневмоцилиндры-пробойники типа D -SA оснащены механизмами регулируемого демпфирования поршня в конечных положения о чем свидетельствует индекс PPV в наименовании. Регулировка демпфирования осуществляется вращением дроссельных винтов размещенных в передней и задней крышках пневмоцилиндра при условии что последний смонтирован в нужном положении и движется под рабочей нагрузкой до достижения ситуации при которой приход поршня в конечное положение не сопровождается ударом.
Рабочее положение пневмоцилиндра-пробойника – вертикальное положение штока при отсутствии регулярных срабатываний или хранении – полностью втянутое. В случае монтажа под углом к вертикали пользователь должен обеспечить соответствие реальной величины радиальной нагрузки на оконечность штока значению не превышающему указанное в табл. 2.
При монтаже пневмоцилиндра необходимо обеспечить совпадение направления действия силы с осью штока на всем пути движения или применять специальные компенсационные устройства. В любом случае следует иметь ввиду что несмотря на усиленную по сравнению со стандартной конструкцию опорного подшипника скольжения передней крышки максимально допустимая радиальная нагрузка на шток цилиндра имеет ограничения указанные в нижеследующей табл. 2.
Передняя крышка пневмоцилиндра-пробойника оснащена плавающим грязесъемным кольцом обеспечивающим совместно с внутренним грязесъемным кольцом второй ступени очистку движущегося в подшипнике штока от глиноземной пыли и прочих загрязнений. Однако значительные механические и прочие (например электросварка)
воздействия на шток пневмоцилиндра ведущие к серьезным нарушениям чистоты его зеркала (раковины задиры глубокие царапины) будут значительно сокращать ресурс подшипника грязесъемника и уплотнений передней крышки.
Случайное проникновение во внутренние полости цилиндра глиноземной пыли окалины прочих абразивов и инородных предметов не допускается. В том случае если это произошло пневмоцилиндр-пробойник должен быть разобран его детали очищены промыты и заново смазаны специальной температуростойкой смазкой (пришедшие в негодность заменены). Любые операции по сборкеразборке пневмоцилиндров-пробойников находящихся под действием условий коммерческой гарантии допускаются только в присутствии под руководством или по согласованию со специалистами Фесто.
Такие же операции по отношению к цилиндрам не находящимся под действием условий коммерческой гарантии рекомендуется проводить по возможности под наблюдением специалистов Фесто.
Требования безопасности при эксплуатации должны соответствовать ГОСТ 12.3.001 раздел 4.
Нормы утечек из полостей пневмоцилиндра при максимальном давлении соответствуют ГОСТ 18460-91 и приведены в табл. 4.3.
В табл. 4.4 приведены основные технические характеристики условия эксплуатации и структура обозначения для заказа пневмоцилиндров-пробойников D -SA .
Обозначение для заказа
№ для заказа + D + D поршня(мм) + ход(мм) + PPV+ (S1)+S6+SA
Пример заказа: поршень D 200 мм ход 400мм
базовая версия: D-200-400-PPV-S1-S6-SA-27087
(информацию по номерам для заказа и модификациям можно получить у специалистов Фесто)
Очищеный сжатый воздух без наличия масла. Необходимая степень осушки от -20 до –40oС
точки росы но не менее чем на 5oС ниже температуры окружающей среды.
Максимально допустимое содержание примесей в окружающей среде
Продолжение Таблица 4.4
Максимально допустимая радиальная нагрузка на оконечность полностью выдвинутого штока
до 650 Н (для диаметра штока 50 мм ход 300мм)
Диапазон температур окружающей среды
-40 + 150oС кратковременно до 200 oС
Фиксация максимального положительного значения температуры обеспечивается встроенным регистратором
Наименование деталей и узлов
) Передняя и задняя крышки
C45 твердохромированный
) Уплотнения поршневые
) Уплотнения PPV опорная втулка подшипника
) Грязесъемное кольцо
Статистический ресурс эксплуатации пневмоцилиндра-пробойника составляет ~1500000 двойных ходов при условии соблюдения пользователем вышеизложенных Правил эксплуатации включая условия табл. 4.4.
Нарушения пользователем вышеизложенных «Правил эксплуатации» пневмоцилиндров-пробойников типа D -SA отсутствие на них идентификационных шильдов или датчиков-регистраторов температуры равно как и нарушение «Правил транспортировки и хранения» может являться причиной для отказа в приеме возможных гарантийных претензий.
Для наиболее полного использования технического ресурса по истечении срока коммерческой гарантии пневмоцилиндр-пробойник следует демонтировать разобрать и произвести дефектовку желательно с участием специалистов Фесто.
В том случае если результат дефектовки будет признан положительным возможно повторное использование пневмоцилиндра-пробойника после замены быстроизнашиваемых уплотнений поставляемых Фесто в рамках ремкомплекта (или отдельно по деталям) совместно со специальной температуростойкой консистентной смазкой и клеем для резьбовых соединений.
При сборке пневмоцилиндра после обслуживания необходимо смазать все трущиеся части кроме штока подшипника передней крышки и уплотнений камер торможения PPV специальной высокотемпературной консистентной смазкой поставляемой Фесто.
Правила транспортировки и хранения
Складское помещение предназначенное для хранения пневмоцилиндров-пробойников должно быть прохладным сухим не запыленным и умеренно проветриваемым.
Хранение и транспортировка пневмоцилиндров-пробойников могут производиться только в фирменной транспортной упаковке не более семи рядов на паллете. Хранение и транспортировка на открытом воздухе даже с защитой от погодных воздействий и в фирменной транспортной упаковке недопустимы.
Температура внешней среды при хранении и транспортировке не должна быть ниже –10С и выше + 40С при относительной влажности воздуха 65%. Оптимальная температура хранения и транспортировки от +15С до +24С. В процессе хранения и транспортировки источники тепла должны располагаться на расстоянии не менее 2 метров от упаковок пневмоцилиндров-пробойников.
По завершении хранения или транспортировки при отрицательных температурах перед вводом в эксплуатацию пневмоцилиндры-пробойники должны быть медленно в течении 15-2 часов доведены до температуры +20С.
Варианты исполнения цилиндров - пробойникв
Стандартное исполнение цилиндров пробойников
Исполнение с управляемым обратным клапаном
Продолжение прилож. 5
Исполнение с пневмо-механическим концевым выключателем в передней и задней крышках.
Исполнение с электро-механическим концевым выключателем (24230 В)
Цилиндр с блоком экономии воздуха. Распределитель с электромагнитным управлением. Пневмомеханические концевые выключатели нижнего и верхнего положения поршня. Реле давления.
Цилиндр блоком экономии воздуха. Распределитель с электромагнитным управлением. Пневмомеханические концевые выключатели нижнего и верхнего положения поршня. Реле давления
Пневмоцилиндр с датчиком обратной связи
Патент на цилиндр - пробойник
Основные понятия и определения
PTFE - Фторопласт-4PTFE (ГОСТ10007-80) - кристаллический полимер с температурой плавления кристаллитов (мелких кристаллов не имеющих ясно выраженной огранённой формы (БСЭ)) 327°С и температурой стеклования аморфных участков от -100 до -120°С.
Фторопласт-4 (Ф-4) обладает исключительной химической инертностью по отношению практически ко всем агрессивным средам (за исключением расплавов щелочных металлов и трифторида хлора). Это качество фторопласта-4 используется при эксплуатации трубопроводов для транспортировки высоко агрессивных сред футеровке реакторов аппаратов колонного типа запорной арматуры насосов ёмкостей для хранения химически активных сред прокладочно-уплотнительных деталей контактирующих с агрессивными средами и др.
Самый низкий среди конструкционных материалов коэффициент трения а также равенство статического и динамического коэффициентов трения фторопласта-4 и композиций на его основе обуславливают широкое применение их в машиностроении - в узлах трения механизмов машин и приборов в качестве подшипников и опор скольжения подвижных уплотнителей - поршневых колец манжет. Использование фторопластов в узлах трения повышает надежность и долговечность механизмов обеспечивает стабильную эксплуатацию в условиях агрессивных сред глубокого вакуума и при сверхнизких температурах.
Фторопласт-4 является самым стойким из всех известных материалов - пластмасс металлов стекол эмалей сплавов и т.п. На него совершенно не действуют кислоты окислители щелочи растворители. На фторопласт-4 действуют только расплавленные щелочные металлы и их комплексные соединения с аммиаком нафталином пиридином а также трехфтористых хлор и элементный фтор при повышенных температурах.
Витон– Аналог Фторопласт-4PTFE
Дифференциальное давление на фильтре (перепад или падение давления на фильтре) – это величина измеряемая как разница между давлением Δp на входе и выходе фильтра и характеризующая сопротивление фильтра потоку сжатого воздуха. По мере загрязнения фильтроэлементов дифференциальное давление растет [10].
Степень очистки фильтра сжатого воздуха (фильтрующая способность и эффективность фильтрации - ) - разница между концентрацией определенного размера частих в сжатом воздухе до и после фильтра.
Циклический дифференциал компрессора – колебания давления на выходе из компрессорной станции. Для винтовых компрессоров циклический дифференциал составляет обычно 05 10 бар.
Классы загрязненности воздуха
Классы загрязненности сжатого воздуха по ГОСТ 17433-80
Размер твердой частицы мкм не более
Содержание посторонних примесей мгм3 не более
(в жидком состоянии)
Классы чистоты по DIN ISO 8573-1:2000
Содержание твердых примесей штм³ не более
Класс 0 зарезервирован под более высокие требования оговаривается специально
Размер 5 мкм концентрация 5 мгм³
Установлены также требования к воздуху классов 7 8 и 9. Содержание влаги для этих классов оговаривается применительно к жидкой конденсированной влаге.
Краткое описание основных физических эффектов с помощью которых возможно получать данные о перемещении
Квантовая система (атом молекула) находящаяся в возбужденном состоянии излучает излишнюю энергию в виде порции электромагнитного излучения. Атомы каждого вещества имеют сбою структуру излучательных переходов которые можно зарегистрировать оптическими методами
На фотоэффекте основано превращение светового сигнала в электрический. Электрическое сопротивление полупроводника падает при освещении; это используется для устройства фотосопротивлений. При освещении области контакта различных полупроводников возникает фото-эдс что позволяет преобразовывать световую энергию в электрическую.
Обратимое или необратимое (упругая или пластическая деформация) изменение взаимного положения точек тела под действием механических сил электрических магнитных гравитационных и тепловых полей сопровождающееся выделением тепла звука света
Электризация возникает при соприкосновении двух разнородных веществ из-за различия атомных и молекулярных сил на их поверхности. При этом происходит перераспределение электронов (в жидкостях и газах ещё и ионов) с образованием на соприкасающихся поверхностях электрических слоёв с противоположными знаками электрических зарядов. Фактически атомы и молекулы одного вещества отрывают электроны от другого вещества.
Полученная разность потенциалов соприкасающихся поверхностей зависит от ряда факторов – диэлектрических свойств материалов значения их взаимного давления при соприкосновении влажности и температуры поверхностей этих тел климатических условий. При последующем разделении этих тел каждое из них сохраняет свой электрический заряд а с увеличением расстояния между ними за счет совершаемой работы по разделению зарядов разность потенциалов возрастает и может достигнуть десятков и сотен киловольт. Электрические разряды могут взаимно нейтрализовываться вследствие некоторой электропроводности влажного воздуха. При влажности воздуха более 85% статическое электричество практически не возникает.
Эффект основан на изменении частоты и длины волн регистрируемых приёмником вызванным движением их источника или приёмника.
Для волн распространяющихся в какой-либо среде (например звука) нужно принимать во внимание движение как источника так и приёмника волн относительно этой среды.
Потенциал течения. Сопло - заслонка
Возникновение разности потенциала между концами капилляров а так же между противоположными поверхностями диафрагмы мембраны или другой пористой поверхности при продавливании через них жидкости.
Используется закон Менделеева – Клаперона. Составляется математическая модель решение которой позволяет получить зависимость перемещения скорости и давлений в поршневой и штоковой полости от времени.
Магнитострикция - явление изменения формы и размеров тела при намагничивании; характерна для ферромагнитных веществ и измеряется относительной величиной удлинения ферромагнетика при намагничивании его до насыщения.
Магнитострикционные преобразователи преобразуют энергию магнитного поля в механическую (звуковую или ультразвуковую) энергию. Их действие основано на магнитоупругом эффекте т.е. на том что некоторые металлы (железо никель кобальт) и их сплавы деформируются в магнитном поле. Если магнитоупругий стержень расположить вдоль переменного магнитного поля то этот стержень станет попеременно сокращаться и удлиняться т.е. испытывать механические колебания с частотой переменного магнитного поля и амплитудой пропорциональной его индукции. Вибрации преобразователя возбуждают в твердой или жидкой среде с которой он соприкасается волны ультразвука той же частоты. Обычно такие преобразователи работают на собственной частоте механических колебаний так как на ней наиболее эффективно преобразование энергии из одной формы в другую.
Компрессорная станция
Продолжение прилож. 10
Винтовые компрессоры BOGE серии S всасывают атмосферный воздух через предварительный панельный фильтр в корпусе и фильтр всасывания с бумажным сменным микрофильтром (1) установленный перед многофункциональным динамическим регулятором всасывания (2). Очищенный воздух поступает в компрессорную ступень которая приводится в движение от электродвигателя. Постоянно охлаждаемое компрессорное масло DOGE впрыскивается в компрессорную ступень в точно дозированных количествах (3).
Масло выполняет три функции:
Оно поглощает и удаляет тепло возникающее в процессе сжатия воздуха. Оно герметизирует зазор между вращающимися навстречу друг другу роторами и поверхностью рабочей камеры компрессорной ступени смазывая в то же время подшипники роторов.
Сжатый воздух с маслом из компрессорной ступени (4) через фланцевое соединение поступает в горизонтальный резервуар отделение масла (5) без потери давления. Здесь происходит механическое отделение масла за счет соударения со стенкой резервуара и быстрого снижения скорости потока с эффективностью не менее 99%. Потери давления при этом равны нулю.
После того как сжатый воздух проходит через внешний быстросменный масляный сепаратор (6) содержание масла в сжатом воздухе составляет всего лишь 1-3 мгм3 при любом режиме работы. Пройдя сепарацию сжатый воздух через клапан минимального давления (7) поступает в охладитель (9) где охлаждается до значения превышающего температуру всасываемого воздуха приблизительно на 8°С. Здесь осаждается большой процент конденсата содержащегося в сжатом воздухе. Сжатый воздух поступает в систему через стандартный нагнетательный канал.
Масло отделяемое в резервуаре сепарирования быстро деаэрируется и прекращает пениться. Далее оно поступает в масляный теплообменник большого размера (8) где охлаждается до оптимальной температуры для впрыскивания в компрессорную ступень. Масляный микрофильтр позволяет осуществлять рециркуляцию масла без загрязнения механизмов. Термоститический клапан (11) позволяет винтовым компрессорам BOGE работать при любом режиме с оптимальной температурой.
Общие сведения по термодинамике необходимые для построения
математичкой модели движения поршня пневмоцилиндра
1. Базовые понятия термодинимаки
Введем основные понятия термодинамики которые понадобятся для составления математической модели. Используемый материал взят из [32].
Рабочим телом в пневмоустройствах является сжатый воздух. Обычно воздух рассматривается как идеальный газ. Под идеальным понимают такой газ у которого отсутствуют силы сцепления между молекулами а молекулы являются материальными точками не имеющими объема. Эти допущения позволяют упростить расчеты сохранив точность достаточной для решения поставленной задачи. Состояние сжатого воздуха описывается уравнением Клапейрона. Это уравнение выведено с помощью методов кинетической теории в предположении что молекулы газа представляют собой материальные точки взаимное притяжение между которыми отсутствует.
Состояние газа характеризуется тремя параметрами: абсолютным давлением удельным объемом (удельным весом) и абсолютной температурой (В дальнейшем во все расчетные уравнения и во все термодинамические зависимости входит только абсолютное давление).
Удельным объемом называют объем занимаемый единицей веса газа
где - вес газа в объеме
Плотностью называется масса газа в единице объема
где - ускорение свободного падения
Абсолютная температура измеряется по абсолютной шкале Кельвина которая связана с температурой t по шкале Цельсия зависимостью:
Параметры идеального газа связаны между собой уравнением состояния.
Уравнение Клапейрона имеет следующий вид:
где – удельная газовая постоянная представляющая собой работу выполняемую одним килограммом газа при изменении его температуры на один градус при постоянном давлении. Для сухого воздуха
Уравнение (11.6) можно переписать с учетом уравнения (11.1)
В термодинамических зависимостях пользуются физической величиной называемой теплоемкостью. Под теплоемкостью понимают количество тепла необходимое для нагрева тела на 1 градус. Удельная теплоемкость это теплоемкость единицы веса или объема вещества. Удельная теплоемкость зависит от условий протекания процесса. Если объем газа постоянен она равна теплоемкости при постоянном объеме ; если процесс протекает при то т.е. теплоемкости при постоянном давлении.
Продолжение прилож. 11
Внутренняя энергия идеального газа складывается из кинетической энергии внутримолекулярных колебаний. Удельная внутренняя энергия представляет собой внутреннюю энергию единицы веса вещества[29]
Изменение внутренней энергии зависит только от температуры т.е. она является функцией температуры:
Первый закон термодинамики (закон сохранения и превращения энергии) имеет формулируется следующим образом. Подведенное к системе тепло расходуется на изменение внутренней энергии системы и на совершение работы. Тепло подведенное к системе считается положительным а отведенное от системы – отрицательным; работа произведенная системой – положительная а работа совершаемая над системой – отрицательная.
Уравнение первого закона термодинамики записывается в дифференциальной форме:
где – количество тепла подведенного к системе – термический эквивалент работы - работа совершаемая системой.
Если все члены уравнения поделить (11.10) поделить на количества газа в полости это уравнение можно записать для удельных величин.
где – количество тепла подведенное к 1 Па газа; – работа совершаемая 1 Па газа.
Работа затрачиваемая на перемещение поршня нагруженного силой P которую совершает 1 Па газа равна
где - площадь поршня
Подставив (11.12) в (11.11) получим уравнение первого закона термодинамики в более удобном для расчетов виде.
2. Термодинамические процессы
Термодинамический процесс – процесс при котором параметры воздуха при переходе его от одного состояния к другому изменяется. Существуют следующие простейшие термодинамические процессы при постоянном количестве воздуха:
Изохорический – процесс при постоянном объеме
Изобарический – процесс при постоянном давлении
Изотермический – процесс при постоянной температуре
Адиабатический – процесс без внешнего теплообмена
Политропный процесс где - показатель политропы который может принимать различные численные значения. Рассмотрим некоторые из этих процессов подробнее.
Изобарический процесс
При изобарический уравнение (11.11) принимает следующий вид:
В этом процессе часть подведенного тепла затрачивается на совершение внешней работы а часть на изменение внутренней энергии. Уравнение (11.6) при для начала и конца процесса и . Из соотношений этих величин получаем
Из уравнения (11.14) следует что при изобарическом процессе изменения состояния газа его объем прямо пропорционален температуре.
Выразим в уравнении (11.13) через теплоемкость при постоянном давлении:
Записав уравнение (11.6) в дифференциальной форме для изобарического процесса и воспользовавшись формулой (11.12) выразим удельную работу в следующем виде
Подставив (11.16) (11.15) (11.9) в выражение (11.13) получим:
Введем так же показатель адиабаты - для воздуха
Из совместного решения уравнений (11.18) и (11.19) получим соотношения:
Коэффициент относительного теплообмена - выражает отношение между подведенным теплом и полученной внешней работой газа
По формулам (11.15) (11.16) (11.21) в изобарическом процессе
Процесс в котором коэффициент относительного теплообмена всегда постоянен и может принимать все значения в пределах от нуля до бесконечности называют политропическим. Процесс протекает при постоянной теплоемкости.
Политропический процесс
Политропический процесс характеризуется постоянным показателем политропы равным
где – теплоемкость в политропическом процессе.
Коэффициент относительного теплообмена в политропическом процессе
Адиабатический процесс
Процесс протекающий без теплообмена с окружающей средой называют адиабатическим. В этом случае в уравнение (11.11) записывают следующим образом:
Т.е. внешняя работа совершается за счет внутренней энергии газа. При расширении газа и совершении им работы температура его снижается а при сжатии повышается. В первом случае работа положительна а во втором отрицательна.
Энтальпия – удельное теплосодержание газа:
В дифференциальной форме:
Если в уравнении (11.13) значение внутренней энергии согласно формуле (11.27) выразить через теплосодержание то можно получить уравнение первого закона термодинамики выраженное в другой форме
Если процесс протекает при постоянном давлении (p=const) то из уравнения (11.29) можно получить
3. Термодинамические процессы при переменной массе газа
Масса газа в приводе постоянно меняется вследствие того что одни полости привода соединены с магистралью а остальные с атмосферой или с другими полостями. Особенностью этих процессов является то что во-первых при их рассмотрении необходимо учитывать переменную массу газа а во-вторых энергию которая подводится с поступающим газом или отводится с вытекающим. Характерной особенностью процессов при переменной массе газа является то что они зависят от времени так как количество поступившего (или отведенного) газа.
В уравнении (11.10) под необходимо понимать не только тепло вносимое из окружающей среды но и абсолютно все подведенное (и отведенное) тепло в том числе и тепло поступившего (или вытекающего) газа. Процесс теплообмена системы с окружающей средой целесообразно отделить от других тепловых процессов. Поэтому под по-прежнему понимаем количество тепла поступающего (или отводимого) из окружающей среды а количество тепла подведенного вместе с газом учтем дополнительными членами в уравнении (11.10).
где – количество энергии содержащиеся в 1 Па поступающего в полость газа и вытекающего из него
– количество газа поступающего в полость из магистрали и вытекающего из нее.
Члены учитывающие в уравнении (11.31) энергию поступившего и отведенного в систему газа являются функциями времени. А значит и все остальные члены уравнения зависят от времени.
Для получения адиабатического процесса в уравнении (11.31) необходимо принять и :
Уравнение (1.32) характеризует процесс истечения сжатого воздуха из полости переменного объема. Найдем и удельной энергии газа в уравнении (11.31). Рассмотрим процесс истечения газа из резервуара неограниченного объема параметры которого постоянны в среду с более низким давлением. Энергия вытекающего газа складывается из его внутренней энергии и работы затраченной на вытеснение газа из резервуара:
Работа сил давления при перемещении выделенной поверхности на расстояние
Подставляя значение в уравнение (1.33) и заменяя получим уравнение
Разделим уравнение (11.35) на и с учетом что получим уравнение:
По выражению (2.14) для энтальпии и из формулы (11.36) получим окончательную величину удельной энергии газа вытекающей из резервуара.
4.Истечение газа из неограниченного объема
Истечение газа из резервуара который имеет практически постоянные параметры сжатого воздуха в общем случае является неустановившемся процессом. Для упрощения задачи истечение газа из резервуара можно рассматривать как частный случай установившегося движения потока газа. Установившееся движение потока газа называют такое движение газа когда его скорость в каждой точке потока определяется только ее координатами и не зависит от времени. Это идеализированный процесс т.к. в действительности скорость при движении газа зависит от перепада давлений а величина давления зависит от времени наполнения газом объема полости или трубопровода от инерционности столба газа от количества поступающего газа которое является функцией времени и других факторов. Но для упрощения расчетов примем движение установившимся подчиняющееся уравнению Бернулли:
В дифференциальной форме оно принимает вид:
где – скоростной поток газа - ускорение свободного падения - член учитывающий потери на трение.
Потери на трение можно рассчитывать по следующим формулам:
где - коэффициент трения газа в трубе; - координата сечения трубы; - диаметр трубы. Подставим (11.40) в (11.39) и получим
Перепишем уравнение (1.41) в следующем виде:
где - коэффициент сопротивления.
Для того что бы установить зависимость между параметрами газа и скоростью потока газа уравнение уравнение движения (11.41) необходимо решить совместно с уравнением состояния (11.3) уравнением (11.11) сохранения энергии которое с учетом работы сил трения имеет вид
Из уравнения неразрывности потока газа для средних значений параметров газа по сечению трубы:
где – расход сжатого воздуха – площадь сечения трубы
Рассмотрим процесс истечения газа из неограниченного объема в среду с меньшим давлением параметры газа поддерживаются постоянными. Примем процесс истечения политропическим и в уравнении (11.42) значение выразим через показатель политропы
Проинтегрировав данное уравнение принимая за начальные условия параметры резервуара а за конечные - параметры произвольного сечения и выражая через в соответствии с политропическим законом истечения получим значение для скорости течения газа:
где - скорость течения газа в резервуаре – показатель политропы в ппоцессе истечения газа - отношение давления среды в которую поступает газ к давлению среды из которой он вытекает. Так как объем резервуара принимается бесконечно большим то скорость течения газа в нем можно пренебречь (). Тогда получим следующее выражение для скорости истечения:
Расход газа возьмем из уравнения неразрывности (11.44) подставив в него значения из выражения (11.47) и из уравнения политропы:
В уравнении (11.48) потери на трение при истечении учтены показателем политропы. При расчетах процесс истечения рассматривают как адиабатический а потери на трение и другие потери давления учитывают коэффициентом расхода . Под коэффициентом расхода в термодинамике понимают произведение коэффициента скорости учитывающего потери на трение и коэффициента сжатия учитывающие уменьшение
поперечного сечения струи при истечении. Но на практике под коэффициентм расхода понимают отношение действительного расхода при истечении к теоретическому. Таким же образом с помощью коэффициента расхода учитываются многие факторы не всегда поддающиеся точному расчету например скорость подхода газа к отверстию потери на трение а также допущения которые прияты при выводе уравнения расхода.
Заменив в формуле (11.48) и введя коэффициент расхода получаем формулу расхода:
Из формулы (11.49) видно что является функцией отношений давлений . Для того что бы найти при каком значении эта функция имеет максимум надо найти производную от подкоренного выражения и приравнять ее к нулю. Получим выражение:
где - критическое отношение давлений. Если то
При подстановке (1.50) в уравнение (1.49) получаем критический расход:
При постоянном давлении в ресивере и значениях давлений меньше расход остается постоянным и равным критическому.
Так как при одном диапазоне отношений давлений расход является постоянным различают два режима истечения: первый – надкритичный когда расход воздуха определяется формулой (1.51) и второй – подкритичный при котором применяют формулу (1.49). Для удобства расчетов представим формулу в другом виде
где - расходная функция она является переменной величиной от нее зависит изменение расхода.
Для надкритичного режима формула (1.52) принимает вид
5.Наполнение газом постоянного объема
Рассмотрим процесс наполнения объема сжатым воздухом из магистрали с постоянными параметрами . Этот процесс протекает без теплообмена с окружающей средой и его можно описать с помощью уравнения (1.31) в котором принимаем
(по формуле (1.37)) (11.60)
Проведем преобразования:
(после подстановки (11.56) и (11.57)) (11.61)
Чтобы определить время наполнения постоянного объема из магистрали подставим в уравнение (11.62) из выражений (1.52) и (1.53). После интегрирования полученных выражений получим следующие расчетные значения для надкритического режима:
для подкритического режима
В уравнениях (11.63) и (11.64) и соответствующие начальным и конечным давлениям причем первое уравнение используется тогда когда и меньше критического отношения давлений . Если значения и больше критического то используют уравнение (11.64). Когда наполнение начинается при давлении меньше критического (например при атмосферном давлении ) а заканчивается при давлении больше кртического т.е то используются совместно обе формулы. За конечное значение давления в первой формуле и за начальное значение во второй принимаем критическое значение давлений .
Для упрощения расчетов обе формулы заменяются одной полученной при условии равенства температур и магистрали и окружающей среды:
Окончание прилож. 11
6.Истечение газа из ограниченного объема
Процесс истечения газа из ограниченного объемапротекает без теплообмена с окружающей средой. Считаем что газ вытекает в атмосферу ( ). Кроме того параметры ограниченного объема будут переменными в то время как параметры остаются постоянными. Подставим в уравнение (11.32) значение составляющих
Получаем следующие значения:
Учтем что получим выражение которое подтверждает собой уравнение адиабаты .
Что бы определить время опорожнения постоянного объема подставим в формулу (1.71) и значение расхода определяем по формулам (1.49) и (1.51) . После интегрирования полученного выражения в пределах от начального состояния газа (параметры ) до некоторого состояния характеризуемого параметрами получим следующие уравнения расчетные уравнения для надкритичного режима:
для подкритичного режима
В уравнениях (11.73) и (11.73) под понимают отношение давления среды куда поступает газ к давлению среды откуда он вытекает
Значения и соответствуют начальному и конечному давлению. Если оба значения меньше критического отношения давлений определяемого из выражения (11.50) то применяют формулу (11.72) а если они больше то формулу (11.73).
Так как в данном случае истечение происходит в атмосферу давление которой принимают постоянной то критическое давление соответствующее критическому отношению так же постоянно и равно
Таким образом процесс истечения в диапазоне изменения давления в объеме от его начального значения до критического протекает в надкртичном режиме а при давлении ниже - в подкритичном режиме.
Для удобства расчетов обе формулы (11.72) и (11.73) заменяем одной зависимостью которую применяем независимо от режима истечения:
Принципиальные схемы компрессоров
Продолжение прилож. 12
Продолжение табл. 12.1
л. 10-11. Технология.dwg

DIMENSIONS ARE IN MILLIMETERS
Распределители условно сняты
Напорный трубопровод
Выхлопной трубопровод
л. 1.Исходные данные.dwg

Исходные данные: в электролизер устанавливается 6 цилиндров пробойников. Диаметр поршня 200 мм
рабочее давление 2-10 бар. Максимальное давление 10 бар. Температурное исполнение пневмоцилиндров пробойника -40 +120 С (кратковременное до +150 С). Сжатый воздух для пневмоцилиндров не грубее 5.7 класса (по DIN ISO 8573). Пневмораспределители и управляющую аппратуру пробойников размесить в металлическом шкафу. Необходимо предложить несколько вариантов структур данных систем (пневматические схемы
выполнить необходимые расчеты
разработать необходимые чертежи
составить математическую модель
выполнить расчет экономической эффективности проекта. Рассмотреть экологическую безопасность использования пневмоситемы.
Пневматическая система электролизера
Сильное магнитное поле
Большой перепад температур
Высокая запыленность
Простота системы управления
Простота конструкции
Стоимость обслуживания
л. 2.Выбор оборудования.dwg

Выбор оборудования для подготовки сжатого воздуха
Конденсото- отводчик
Глубинно-коалесцентный