Мостовой кран г/п 5т




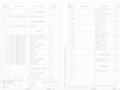
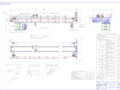
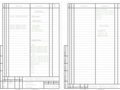
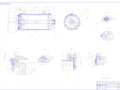
- Добавлен: 25.10.2022
- Размер: 3 MB
- Закачек: 0
Описание
Состав проекта
![]() |
![]() ![]() ![]() |
![]() |
![]() |
![]() ![]() ![]() ![]() |
![]() ![]() |
![]() ![]() |
![]() |
![]() |
![]() ![]() |
![]() ![]() |
![]() ![]() ![]() ![]() |
![]() |
![]() ![]() |
![]() ![]() |
![]() |
![]() |
![]() ![]() ![]() ![]() |
![]() ![]() ![]() ![]() |
![]() ![]() |
![]() ![]() |
![]() |
![]() |
![]() ![]() |
![]() |
![]() ![]() |
![]() ![]() |
![]() ![]() ![]() ![]() |
![]() |
![]() |
![]() |
![]() ![]() |
![]() ![]() ![]() ![]() |
Дополнительная информация
курсовой проект гпм.doc
Расчет металлоконструкции 6
Расчет механизма подъема 9
1 Выбор полиспастной системы расчет и выбор типа каната . .10
2 Определение основных размеров и числа оборотов барабана . .13
3Расчет и выбор электродвигателя . 16
4 Расчет и выбор редуктора ..18
6 Выбор тормоза . ..23
7 Расчет параметров неустановившегося движения . 25
8 Компоновка механизма подъема .27
Расчет механизма передвижения тележки .. 30
1 Сопротивление передвижению тележки .. 31
2 Расчет и выбор электродвигателя . 32
3 Расчет и выбор редуктора . .34
4 Выбор муфт .. ..35
6 Компоновка механизма передвижения тележки 48
Расчет механизма передвижения крана . . 49
1 Определение сопротивлений передвижению крана .. 50
2 Расчет и выбор электродвигателя 51
3 Расчет и выбор редуктора . 53
6 Компоновка механизма передвижения крана .68
Расчет на прочность элементов установки барабана . 69
1 Толщина цилиндрической стенки .. .69
2 Устойчивость цилиндрической стенки барабана ..70
3 Крепление каната к барабану ..71
4 Расчет болтов соединяющих зубчатый венец с барабаном 73
5 Расчет оси барабана . 75
6 Расчет подшипников на статическую грузоподъемность 77
Список используемых источников 79
Техническое задание было выдано на кафедре "Подъёмно-транспортные машины и роботы". На основании этого задания был разработан курсовой проект по теме "Мостовой кран". В ходе разработки проекта были выполнены пояснительная записка чертежи (общий вид крана сборочный чертеж установки барабана общий вид механизма подъема а также чертёж общего вида механизма передвижения крана). Цель проекта - учебная.
Назначение область применения и техническая характеристика крана
Мостовые краны являются основными грузоподъемным оборудованием производственных цехов закрытых и открытых складов. В качестве грузозахватного органа кранов служат: крюки грейферы электромагниты захваты и другие специальные устройства. Кабина управления располагается на мосту крана в месте обеспечивающем наилучший обзор и безопасность работы крановщика а при необходимости – на тележке или имеет возможность автономно перемещаться вдоль пролета крана. На мосту крана могут располагаться две грузовые тележки на одном или двух путях. На рисунке 1.1 представлена схема мостового крана.
-кабина машиниста; 2-крановые рельсы; 3-ходовые колеса; 4-концевая балка; 5-кабель токоподвода; 7-механизм подъема; 8-крановая тележка; 9-струна для подвески гибкого кабеля; 10-площадка для обслуживания крана; 11-главная балка; 12-механизм передвижения тележки; 13-механизм передвижения моста.
Рисунок 1.1 - Схема мостового крана
масса поднимаемого груза - Q = 5000 кг;
высота подъёма груза - Н = 12 м;
скорость передвижения тележки т=03 мс;
скорость подъёма груза г=04 мс;
скорость передвижения крана к=06 мс
Расчет металлоконструкции
Расчет главной балки кранового моста начинается с определения геометрических параметров сечения. Пролетная балка коробчатого сечения состоит из двух вертикальных стенок и двух горизонтальных поясов соединенных между собой при помощи автоматической сварки односторонними швами без разделки.
Выбираем сталь обыкновенного качества - Ст3.
При проектировании крановых мостов рекомендуется выдерживать следующие соотношения между размерами главных балок:
Высота балки на максимальной длине крана:
Определим расстояние между стенками балки:
Определяем свес полки со стенок b1:
При автоматической сварке из-за технологических особенностей b1≥20мм примем b1=40мм.
Определим толщину полки:
B=055+2(0006+004)=064 м
Принимаем ширину полки B=065 м.
Полученное значение должно удовлетворяться условию:
Условие выполняется значит окончательно принимаем:
Определяем толщину верхней полки:
Определяем толщину нижней полки:
На рисунке 2.2 представлено сечение балки.
Рисунок 2.2 – Сечение балки
Расчет механизма подъема
Общий расчет механизма подъема груза включает выбор крюка с подвеской полиспаста двигателя редуктора муфт тормоза выбор каната расчет барабана.
Необходимо рассчитать механизм подъема груза электрического мостового крана грузоподъемностью Q=5000кг для механизации перегрузочных работ в цехах машиностроительных предприятий. Скорость подъема груза г=04 мс. Высота подъема H=12 м. Группа классификации механизма 3М в соответствии с ИСО43011-86 в соответствии с ГОСТ 25835-83. Кинематическая схема привода механизма подъема показана на рисунке 3.1.
- электродвигатель; 2 - муфта 3 - промежуточный вал; 4 - муфта; 5 - тормоз; 6 - редуктор; 7 – барабан 8 - муфта.
Рисунок 3.1 – Кинематическая схема привода механизма подъема
Механизм подъема приводится в движение от кранового электродвигателя 1 соединяемого с цилиндрическим двухступенчатым редуктором 6 с помощью зубчатых муфт 2 и 3. Последняя муфта снабжена тормозным шкивом с которым взаимодействует колодочный электромагнитный тормоз 5. Барабан 7 закреплен на оси опирающейся на два роликовых сферических подшипника позволяющих компенсировать перекосы оси относительно выходного вала редуктора 6. Барабан с редуктором соединяется с помощью зубчатой муфты.
1 Выбор полиспастной системы расчет и выбор типа каната
Кратность полиспаста механизма подъема выбирается в зависимости от типа полиспаста и грузоподъемности механизма 1 с.55. Принимаем сдвоенный двукратный полиспаст. Схема запасовки каната показана на Рисунке 3.2.
- барабан; 2 - канат; 3 - крюковая подвеска; 4 - уравнительный блок.
Рисунок 3.2 - Схема запасовки каната
КПД полиспаста и отклоняющего блока:
где =097 – КПД блока установленного на подшипниках качения 1 с.54;
a=2 – кратность полиспаста;
t=2 – число отклоняющих блоков;
Наибольшее натяжение ветви каната:
где Q=5000 - масса поднимаемого груза кг;
Gз=003Q=150 – масса крюковой подвески кг
Выбор стального каната производится в соответствии с Правилами Ростехнадзора. Расчетное разрывное усилие в канате:
где zp=56 -минимальный коэффициент использования каната для группы классификации механизма М3 по ИСО 43011;
S=135672 - наибольшее натяжение ветви каната Н
Выбираем по ГОСТ 2688-80 канат двойной свивки типа ЛК-Р конструкции 619(1+6+66+1о.с.) диаметром d=13 мм имеющий при маркировочной группе проволок 1470 МПа разрывное усилие F=76190 H.
Канат грузовой (Г) первой марки (1) из проволоки без покрытия (-) правой крестовой свивки (-) нераскручивающийся (Н) обозначается: 130-Г-I-H-1470-ГОСТ 2688-80.
Фактический коэффициент использования каната:
где F=76190 – Разрывное усилие каната Н;
S=135672 - наибольшее натяжение ветви каната Н;
z=56 – минимальный коэффициент использования каната
В соответствии с проведенными расчетами выбранный канат удовлетворяет условиям нагружения механизма.
При выборе стандартного крюка по грузоподъемности не требуется расчет его прочности. Параметры кованых и штампованных однорогих крюков выбирают по ГОСТ 6627-74. Выберем для крюка заготовку – 14А для группы классификации М3 3 с.336.
По 1 с.298 выбираем подвеску крюковую типа 1 грузоподъемностью 5 тонн имеющую блоки диаметром 400 мм с расстоянием между блоками b=225 мм. Укороченная крюковая подвеска состоит из: двух блоков 1 траверсы 2 грузового крюка 3 и упорного подшипника 4. Конструктивная схема крюковой подвески представлена на рисунке 3.3.
- блок 2 - траверса 3 - крюк 4 - упорный подшипник
Рисунок 3.3 - Конструктивная схема крюковой подвески
Определяем размеры блоков минимальный диаметр блока:
где d=13 - диаметр каната мм;
h2=224 - коэффициент выбора диаметра блока 4
В соответствии с рядом предпочтительных чисел размеров выбираем блок диаметром Dбл=400 мм.
2 Определение основных размеров и числа оборотов барабана
Барабаны выполняют литыми из чугуна или стали и сварными стальными. На рисунке 3.4 представлена схема размеров барабана.
Рисунок 3.4 - Схема размеров барабана
Минимальный диаметр барабана по дну канавки:
h1=25 - коэффициент выбора диаметра барабана 4
В соответствии с рядом предпочтительных чисел размеров выбираем барабан диаметром Dб=400 мм=04 м.
t =(11..12)13=15 мм.
Толщина стенки литого чугунного барабана:
Для уменьшения металлоемкости барабана принимаем толщину его стенки =10 мм.
Принимаем в качестве материала барабана чугун марки СЧ 15 ( []=130 МПа) найдем напряжение сжатия в стенке барабана:
где S=135672 - усилие в канате Н;
t=15 - шаг нарезки мм;
[] - допускаемое напряжение сжатия для материала барабана МПа
Действующие напряжения меньше допускаемого поэтому выбранная толщина стенки обеспечивает требуемую прочность.
Длина барабана при сдвоенном полиспасте и намотке обеих ветвей каната на один барабан (см. рисунок 2.2) определяется по формуле:
LБ=2(lр+lраз+lг)+l0 (3.10)
l0- длина свободной (не нарезанной) части барабана.
Длина рабочей части барабана:
где Н=12 - высота подъема м;
DБ=04 – диаметр барабана м;
d=0013 – диаметр каната м;
t=0015 - шаг нарезки м
Длина части барабана на которой размещаются разгружающие витки:
Определяем длину гладкой части барабана:
Приняв расстояние между правой и левой нарезками на барабане (длина не нарезанной части) равными расстоянию между ручьями блоков в крюковой обойме l0=0225м найдем полную длину барабана (см. формулу 3.9):
LБ=2(027+003+0045)+0225=0885м
При расчете длины барабана должно выполняться условие:
Данное условие выполняется оставляем ранее выбранный размер.
Определяем частоту вращения барабана:
где г=04 - скорость подъема груза мс;
DБ=035 – диаметр барабана м
Определяем требуемую угловую скорость барабана:
где nБ=1909 - частота вращения барабана обмин
3 Расчет и выбор электродвигателя
Находим КПД механизма:
где р=096 – расчетный КПД редуктора;
п=093 – КПД полиспаста
Находим требуемую статическую мощность электродвигателя:
где г=04 -скорость подъема груза мс;
м=089 - КПД механизма;
Q=5000 - масса поднимаемого груза кг;
Gз=150 – масса крюковой подвески кг
Номинальная мощность электродвигателя принимается равной или несколько большей статической мощности. С учетом этих указаний из 2 с.241 выбираем крановый электродвигатель с фазным ротором MTF 411-6 имеющим для группы классификации механизма М3 номинальную мощность Nд=27 кВт; частоту вращения n=955 мин-1; угловую скорость д=100 сек-1; Момент инерции ротора Ip=09 кгм2; максимальный пусковой момент двигателя Mп=638 Нм. Габаритная схема электродвигателя представлена на рисунке 3.5.
Рис 3.5 Габаритная схема электродвигателя MTF 411-6 и его размеры
Основные габаритные и установочные размеры представлены в таблице 3.1
Таблица 3.1 - Основные габаритные и установочные размеры
4 Расчет и выбор редуктора
Передаточное число привода от двигателя до барабана:
где Б=199 – угловая скорость барабана сек-1;
Д=100 – угловая скорость двигателя сек-1
В соответствии со стандартным рядом принимаем передаточное число привода округляя его в меньшую сторону i=25.
Расчетная мощность редуктора при kр=17 – коэффициент 1 с.40 учитывающий условия работы редуктора и мощности электродвигателя Nд=27 кВт:
Из 3 с.218 по передаточному числу и мощности выбираем редуктор цилиндрический двухступенчатый горизонтальный крановый имеющий тихоходный вал с зубчатым венцом типоразмера Ц2-400 с передаточным числом ip=50 и мощностью на быстроходном валу для группы классификации механизма 3М - Np=422 кВт.редуктора 315 кг. Габаритная схема редуктора Ц2-400 показана на рисунке 3.6.
Рисунок 3.6 Габаритная схема редуктора Ц2-400 и его размеры
Основные размеры редуктора представлены в таблице 3.2
Таблица 3.2 - Основные размеры редуктора
Фактическая частота вращения барабана:
где nб=955 – частота вращения барабана обмин;
iр=50 – передаточное число редуктора.
Определяем фактическую скорость подъема груза которая не должна отличаться от заданной более чем на 5%:
гдеDБ=04 – диаметр барабана м;
- фактическая частота вращения барабана мин-1;
a=2 – кратность полиспаста
Эта скорость отличается от заданной на 025%. Условие выполняется
Момент статического сопротивления на валу двигателя в период пуска с учетом того что на барабан навиваются две ветви каната:
где Sб=135672 - усилие в канате набегающем на барабан Н;
б=094 - КПД барабана 1 с.23;
пр=096 - КПД привода барабана 1 с.127;
z=2 - число ветвей каната закрепленных на барабане;
Dб=04 - диаметр барабана м.
-при опускании груза:
Момент передаваемый муфтой принимается равным моменту статических сопротивлений :
Номинальный момент на валу двигателя :
где Nд=27 -мощность электродвигателя кВт;
n=955 – частота вращения электродвигателя обмин.
Расчетный момент для выбора зубчатой муфты:
гдеk1=13 -коэффициент учитывающий степень ответственности механизма по 1 с.42;
k2=12 -коэффициент учитывающий режим работы механизма по 1 с.42
Из 1 с.339 выберем ближайшую по требуемому крутящему моменту зубчатую муфту №3 с тормозным шкивом диаметром Dт=300мм шириной с Bт=145 мм и наибольшим передаваемым крутящим моментом 3150 Нм. Момент инерции муфты Iм=06 кгм2.муфты 30 кг. На рисунке 3.7 представлена конструктивная схема муфты типа МЗ с тормозным шкивом.
Рисунок 3.7 Конструктивная схема зубчатой муфты с тормозным шкивом
Так как в механизме присутствует промежуточный вал выбираем по ГОСТ 5006-83 вторую зубчатую муфту №1 с наибольшим передаваемым крутящим моментом 1000 Нм и моментом инерции муфты Iм=005 кгм2. На рисунке 3.8 представлена конструктивная схема зубчатой муфты.
Рис. 3.8 Конструктивная схема зубчатой муфты
Основные размеры муфты представлены в таблице 3.3
Таблица 3.3 – основные размеры муфты
Максимальн. момент Нм
Расчет муфты соединяющей редуктор с барабаном не проводят т.к. конец тихоходного вала редуктора выполнен в виде зубчатого венца.
Механизмы подъема груза должны быть снабжены тормозами нормально закрытого типа автоматически размыкающимися при включении привода.
Статический момент от груза приведенный на быстроходный вал:
гдеобр – КПД при обратном движении (движение механизма под действием груза при отключенном приводе) для зубчатого редуктора обр=095;
м=089 -КПД механизма;
d=0013 – диаметр каната м
КПД при подъеме груза:
гдеп=093 – КПД полиспаста;
м – КПД муфты для зубчатых муфт м=099;
s=2 – число муфт в приводе;
обр=095 – КПД при обратном движении
По полученным данным находим момент от груза на валу тормозного шкива:
Необходимый по нормам Ростехнадзора момент создаваемый тормозом выбирается из условия:
гдеkт - коэффициент запаса торможения. Тормоз механизма подъема груза должен обеспечивать тормозной момент с коэффициентом запаса торможения не менее 15 и не более 25; примем =21.
Из 1 с.341 выбираем тормоз ТКГ-300 с тормозным моментом 800 Нм диаметром тормозного шкива DT=300 мм.тормоза 100 кг. Регулировкой можно получить требуемый тормозной момент МТ=300 Нм. На рисунке 3.9 представлена конструктивная схема двухколодочного тормоза с электрогидравлическим толкателем ТКГ.
Рис. 3.9 Габаритная схема тормоза типа ТКГ.
Основные размеры тормоза типа ТКГ-300 представлены в таблице 3.4
Таблица 3.4 - основные размеры тормоза типа ТКГ-300
7 Расчет параметров неустановившегося движения
Мн=1000NД=100027100=270;
Мсп=155Мн=4185 - среднепусковой момент двигателя Нм;
=1007 - момент статический при подъеме Нм;
=82 – момент статический при торможении Нм;
Мт=300 - момент тормозной Нм;
=100 - номинальная угловая скорость двигателя с-1;
Ip=2 - момент инерции ротора кгм2;
Iм=005 - момент инерции зубчатой муфты кгм2;
Iм=01 - момент инерции зубчатой муфты с тормозным шкивом шкивом кгм2.
Момент инерции вращающихся масс:
где Ip=2 -момент инерции ротора кгм2;
Iм=005 и Iм=01 - моменты инерции муфт кгм2
Параметр uв приведения поступательно движущих масс к валу двигателя:
где DБ=04 – диаметр барабана м;
Момент инерции поступательно движущих и вращательно движущих масс приведенных к быстроходному валу по формуле:
где Iв=318 -момент инерции вращающихся масс кгм2;
uв=0002 - параметр приведения направления движения полиспаста к валу двигателя м
Расчет времени неустановившегося движения t ускорения a и пути перемещения . Определяем время разгона при подъеме груза:
где I=32 - момент инерции всех движущихся масс кгм2;
Мсп=4185 - среднепусковой момент двигателя Нм;
=1007 - момент статический при подъеме Нм
Время разгона при опускании груза:
Время торможения при опускании груза:
Время торможения при подъеме крюковой подвески без груза:
где Мт=300 - тормозной момент Нм
Расчетные значения ускорения и пути перемещения определяются соответственно по формулам и =05t где =04 мс –заданная скорость подъема груза.
Расчетные значения ускорения и пути перемещения представлены в таблице 3.5.
Таблица 3.5 - Расчетные значения ускорения и пути перемещения
Разгон при подъем груза
Разгон при опускание груза
Торможение при опускании груза
Торможение при подъеме подвески без груза
Компоновка механизма подъема груза
На основе рассчитанных параметров и выбранных элементов механизма подъема производим компоновку всех его составных частей их взаимное расположение в масштабе представлено на рис. 3.10.
– двигатель; 2 – зубчатая муфта; 3 – зубчатая муфта с тормозным шкивом; 4 – тормоз; 5 – редуктор; 6 – барабан; 7– уравнительный блок.
Рис. 3.10 Компоновка механизма подъема
Механизм подъема приводится в движение от кранового электродвигателя 1 соединяемого с цилиндрическим двухступенчатым редуктором 5 с помощью зубчатых муфт 2 и 3. Последняя муфта снабжена тормозным шкивом с которым взаимодействует колодочный электромагнитный тормоз 4. Барабан 6 закреплен на оси опирающейся на один роликовый сферический подшипник позволяющих компенсировать перекосы оси относительно выходного вала редуктора.
Расчет механизма передвижения тележки
Расчет механизма передвижения тележки заключается в подборе и расчете ходовых колес определении сопротивлений передвижению выборе электродвигателей редукторов муфт и тормозов. Необходимо рассчитать механизм передвижения тележки электрического мостового крана грузоподъемностью Q=5000 кг. Скорость передвижения тележки т=03 мс. Группа классификации механизма 3М в соответствии с ИСО43011-86 в соответствии с ГОСТ 25835.
Выбранная кинематическая схема механизма передвижения тележки с центральным приводом и тихоходным трансмиссионным валом показана на рисунке 4.1. Механизм имеет привод к валу ходового колеса - 1 от электродвигателя - 8 переменного тока через вертикальный цилиндрический редуктор - 5 типа ВК широко применяемый в механизмах передвижения крановых тележек. Двухколодочный тормоз с электрогидравлическим одноштоковым гидротолкателем - 7 установлен на валу двигателя. В механизме используются три типа муфт: упругая втулочно-пальцевая муфта с тормозным шкивом – 6 зубчатая муфта - 2 с промежуточным валом - 3 и зубчатая – 4.
- ходовое колесо; 2 - муфта зубчатая с промежуточным валом; 3 - пормежуточный вал; 4 - муфта зубчатая;5 - редуктор; 6 - муфта упругая втулочно-пальцевая с тормозным шкивом; 7 - тормоз; 8 - электродвигатель.
Рисунок 4.1 - Кинематическая схема механизма передвижения тележки
1 Сопротивление передвижению тележки
Сопротивление передвижению тележки с номинальным грузом приведенное к ободу ходового колеса:
где Q=5000 – масса номинального груза кг;
m=2000 – масса тележки по 5 с.269 кг;
=00004 – коэффициент трения качения ходовых колес по рельсам с плоской головкой 1 с.33 м;
f=002 - коэффициент трения в подшипниках качения ходовых колес (подшипники конические) по 1 с.33;
Dк = 025 – диаметр ходового колеса 1 с.33 м;
dк= (02..025)Dк=80 – диаметр цапфы м;
kp=22 – коэффициент учитывающий сопротивление трения реборд ходовых колес и торцов ступиц колеса 1 с.33
Сопротивление передвижению тележки без груза:
2 Расчет и выбор электродвигателя
Выбор электродвигателя для механизма передвижения крановых тележек производят по максимально допустимому пусковому моменту двигателя при котором обеспечивается надлежащий запас сцепления ходового колеса с рельсом исключающий возможность буксования при передвижении тележки без груза в процессе пуска.
Определим статическую мощность электродвигателя:
где т=03 - скорость передвижения тележки мс;
=085 - КПД механизма 1 с.23;
Fпер=20688 - сопротивление передвижению тележки Н
Номинальная мощность электродвигателя принимается равной или несколько большей статической мощности. С учетом этих указаний из 6 с.45 выбираем крановый электродвигатель с фазным ротором MTF 011-6 имеющим для группы классификации механизма 3М номинальную мощность Nд=17 кВт; частоту вращения n=850 обмин; Момент инерции ротора Ip=0085 кгм2; максимальный пусковой момент двигателя Mп=39 Нм и массой 51 кг. На рисунке 4.2 показана конструктивная схема электродвигателя MTF 011-6.
Номинальный момент двигателя:
гдеNд=17 – номинальная мощность электродвигателя кВт;
n=850– частота вращения мин-1
Рисунок 4.2 Габаритная схема электродвигателя MTF 011-6 и его размеры
Основные габаритные и установочные размеры представлены в таблице 4.1.
Таблица 4.1 - Основные габаритные и установочные размеры
3 Расчет и выбор редуктора
Частота вращения ходового колеса:
Требуемое передаточное число привода:
Расчетная мощность редуктора:
гдеNс=143 - статическая мощность электродвигателя кВт;
kp=22 – коэффициент учитывающий условия работы редуктора 1 с.40
Исходя из этой мощности и требуемого передаточного числа из 5 с.426 выбираем для группы классификации механизма 3М редуктор типа ВК-400 имеющим номинальную мощность Nр=44 кВт частоту вращения nр=750 обмин и передаточным числом ip=20. Конструктивная схема редуктора ВК-400 представлена на рисунке 4.3.
Рисунок 4.3 Конструктивная схема редуктора ВК-400 и его размеры
Основные размеры редуктора представлены в таблице 4.2.
Таблица 4.2 - Основные размеры редуктора
Всего в данном механизме передвижения тележки исходя из выбранной кинематической схемы используется три муфты одна из которых упругая втулочно-пальцевая с тормозным шкивом установленная на быстроходном валу редуктора и две зубчатые муфты установленная на тихоходном валу.
4.1 Муфта соединяющая электродвигатель с редуктором:
Номинальный момент передаваемый муфтой электродвигателя:
где Fпер=20688 - сопротивление передвижению тележки с номинальным грузом Н;
Dк = 025 – диаметр ходового колеса м;
Расчетный момент для выбора муфты:
гдеk1=12 - коэффициент учитывающий степень ответственности механизма по 1 с.42;
k2=12 - коэффициент учитывающий режим работы механизма по по 1 с.42
Выбираем упругую втулочно-пальцевую муфту с крутящим моментом 250 Нм. Диаметр муфты D=200 мм момент инерции Iм=024 кгм2 и масса 135 кг. Конструктивная схема упругой втулочно-пальцевой муфты с тормозным шкивом показана на рисунке 4.4.
Рис 4.4 Габаритная схема упругой втулочно-пальцевой муфты с тормозным шкивом
Основные размеры муфты представлены в таблице 4.3
Таблица 4.3 - Основные размеры муфты
4.2 Муфты соединяющие редуктор с колесом:
Номинальный момент двигателя приведенный к тихоходному валу редуктора :
Расчетный момент для выбора муфт:
Выбираем по ГОСТ 5006 зубчатую муфту №2 с наибольшим передаваемым крутящим моментом 1600Нм и моментом инерции муфты Iм=006 кгм2 и массой 92 кг. Конструктивная схема зубчатой муфты представлена на рисунке 4.5.
Рисунок 4.5 Конструктивная схема зубчатой муфты
Основные размеры муфты представлены в таблице 4.4
Таблица 4.4 - Основные размеры муфты
Также выбираем по ГОСТ 5006 зубчатую муфту с промежуточным валом №1 для передачи крутящего момента между колесами с наибольшим передаваемым крутящим моментом 710 Нм и моментом инерции муфты Iм=024 кгм2 и массой 205 кг.
Габаритная схема зубчатой муфты с промежуточным валом представлена на рисунке 4.6.
Рисунок 4.6 - Габаритная схема зубчатой муфты с промежуточным валом
Основные размеры муфты МЗП представлены в таблице 4.5
Таблица 4.5 - Основные размеры муфты МЗП
Фактическая скорость передвижения тележки:
отличается от ближайшего значения 02 мс по 1 с.6 из стандартного ряда на 3% что допустимо.
Максимально допустимое ускорение крана при пуске:
где z=4 – общее число ходовых колес;
zпр=2 - число приводных колес;
φ=015 – коэффициент сцепления ходовых колес с рельсами (при работе в помещении) 1 с.33;
kφ=12 – коэффициент запаса сцепления 1 с.32;
f=002 – коэффициент трения в конических подшипниках опор вала ходового колеса;
dk=008 – диаметр цапфы вала м;
kp=22 – коэффициент учитывающий сопротивление трения реборд ходовых колес и торцов ступиц колеса 1 с.23;
=00004 – коэффициент трения качения ходовых колес по рельсам с плоской головкой м;
Dk=025 – диаметр ходового колеса м
Наименьшее допускаемое время пуска:
Средний пусковой момент электродвигателя:
min=11..14 - минимальная кратность пускового момента электродвигателя примем min=11
Момент статических сопротивлений при работе крана без груза:
гдеF’пер=59196 - сопротивление передвижению тележки без груза Н;
ip=4123 – передаточное число редуктора
Суммарный момент инерции вращающихся масс:
гдеIp=0085 – момент инерции ротора электродвигателя кгм2;
Iбм=024 – момент инерции муфты на быстроходном валу кгм2;
Фактическое время пуска механизма передвижения без груза:
где=1.2 – коэффициент учитывающий влияние вращающихся масс привода механизма (кроме ротора двигателя и муфт) 1 с.25;
I=0325 - суммарный момент инерции вращающихся масс кгм2;
n=850– число оборотов электродвигателя обмин;
Мср.п.=3056 - средний пусковой момент электродвигателя Нм;
Мс=297 - момент статических сопротивлений при работе крана без груза Нм;
m=2000 – масса тележки кг;
ф=02 - фактическая скорость передвижения тележки мс;
что согласуется с данными 1 с.28.
Фактическое ускорение крана без груза при пуске:
гдефпер=02– фактическая скорость передвижения мс;
tфп=157 - фактическое время пуска механизма передвижения без груза с;
amax=044– максимально допустимое ускорение тележки мс2
условие выполняется aФamax или 013 мс2 044 мс2.
Проверяем фактический запас сцепления. Для этого найдем суммарную нагрузку на приводные колеса без груза:
m=2000 – масса тележки кг
Найдем фактический запас сцепления:
где=9820– суммарная нагрузка на приводные колеса Н;
=59196 – полное сопротивление передвижению без груза Н;
φ=015 – коэффициент сцепления ходовых колес с рельсами;
z=4 – общее число ходовых колес;
zпр=2 – число приводных колес;
f=002 – коэффициент трения в подшипниках опор вала ходового колеса (для конических).
Максимальное допустимое замедление тележки при торможении:
где φ=0.15 – коэффициент сцепления ходовых колес с рельсами (при работе в помещении);
kφ=1.2 – коэффициент запаса сцепления;
f=0.02 – коэффициент трения в подшипниках опор вала ходового колеса (для конических);
=0.0004 – коэффициент трения качения ходовых колес по рельсам с плоской головкой м
по 1 с.32 принимаем =015мс2.
Время торможения тележки без груза:
где=015 - максимальное допустимое замедление тележки при торможении мс2;
=02 – фактическая скорость передвижения тележки мс
Сопротивление при торможении тележки без груза:
гдеm=2000 – масса тележки кг;
dk=008 – диаметр цапфы вала;
Dk=025 – диаметр ходового колеса м;
f=002 – коэффициент трения в подшипниках опор вала ходового колеса (для конических)
Момент статических сопротивлений на тормозном валу при торможении тележки:
где =1884 - сопротивление при торможении тележки без груза Н;
Момент сил инерции при торможении тележки без груза:
где=12 – коэффициент учитывающий влияние вращающихся масс привода механизма (кроме ротора электродвигателя и муфт быстроходного вала);
n=850– число оборотов электродвигателя мин-1;
tТ=133 - время торможения тележки без груза с
Расчетный тормозной момент на валу тормоза:
где=159 – момент сил инерции при торможении тележки без груза Нм;
=096 – момент статических сопротивлений на тормозном валу при торможении тележки Нм
Из 1 с.341 выбираем тормоз ТКГ-200 с тормозным моментом 250 Нм диаметром тормозного шкива DT=200 мм.тормоза 38 кг. Регулировкой можно получить требуемый тормозной момент =921 Нм. На рисунке 4.7 представлена конструктивная схема тормоза типа ТКГ.
Рисунок 4.7 Конструктивная схема тормоза типа ТКГ
Основные размеры тормоза типа ТКГ-200 представлены в таблице 4.5
Таблица 4.6 - Основные размеры тормоза типа ТКГ-200
Минимальная длина пути торможения:
гдеф=02 - фактическая скорость передвижения тележки мс;
k=15 – коэффициент по 1 с.31
Фактическая длина пути:
гдеtТ=133 - время торможения тележки без груза с
Условие выполняется или 025>0027 м.
6 Компоновка механизма передвижения тележки
На основе рассчитанных параметров и выбранных элементов механизма передвижения тележки производим компоновку всех его составных частей их взаимное расположение в масштабе представлено на рисунке 4.8.
Механизм передвижения рассчитываемой тележки выполнен по схеме приведенной на рисунке 4.1. B этой схеме ходовые колеса - 1 укреплены на осях подшипники которых обычно помещаются в специальные буксы. Муфтами - 2 типа МЗП и - 4 типа МЗ оси связаны с выходным валом редуктора - 5; Первый вал редуктора связан с выходным валом двигателя - 8 муфтой - 6 половина этой муфты укрепленная на валу редуктора одновременно служит тормозным шкивом на котором находится тормоз - 7. Наличие полностью закрытых передач в данном случае позволяет лучше предохранить зубья колес от загрязнения и уменьшить их износ. Одновременно такая схема позволяет использовать стандартные редукторы что значительно упрощает изготовление и сборку механизма в условиях специализированных заводов которыми она широко и используется в данное время. Недостатками схемы является необходимость в более квалифицированной сборке механизма.
- ходовое колесо; 2 - муфта зубчатая с промежуточным валом; 3 - пормежуточный вал; 4 - муфта зубчатая; 5 - редуктор; 6 - муфта упругая втулочно-пальцевая с тормозным шкивом; 7 - тормоз; 8 - электродвигатель.
Рисунок 4.8 - Компоновка механизма передвижения тележки
Расчет механизма передвижения крана
Общий расчет механизма передвижения крана заключается в подборе и расчете ходовых колес определении сопротивлений передвижению выборе электродвигателей редукторов муфт и тормозов.
Необходимо рассчитать механизм передвижения мостового крана грузоподъемностью Q=5000кг. Скорость передвижения крана к=06 мс. Группа классификации механизма 3М в соответствии с ИСО43011-86 в соответствии с ГОСТ 25835-83.
Выбранная габаритная схема механизма передвижения тележки с центральным приводом показана на рисунке 5.1. Механизм имеет привод к валу ходового колеса - 1 от электродвигателя - 6 переменного тока через вертикальный цилиндрический редуктор - 3 типа ВК широко применяемый в механизмах передвижения кранов. Двухколодочный электрогидравлический тормоз - 4 с одноштоковым гидротолкателем установлен на валу двигателя. В механизме используются два типа муфт: упругая втулочно-пальцевая муфта с тормозным шкивом – 5 и зубчатая муфта – 2.
Рисунок 5.1 Габаритная схема передвижения крана с раздельным приводом
- ходовое колесо; 2- зубчатая муфта; 3- редуктор; 4- тормоз; 5- упругая втулочно-пальцевая муфта с тормозным шкивом; 6 - электродвигатель
1 Определение сопротивления передвижению крана
Ориентировочная масса мостового крана по 1 с.13:
гдеQ=5000кг - масса номинального груза;
L=24м – пролет крана
Сопротивление передвижению крана с номинальным грузом приведенное к ободу ходового колеса:
гдеQ=5000 – масса номинального груза кг;
m=24800 – масса крана кг;
=00005 – коэффициент трения качения ходовых колес по рельсам с плоской головкой 1 с.33 м;
f=0.02 - коэффициент трения в подшипниках качения ходовых колес (подшипники конические) по 1 с.33;
Dк = 05 – диаметр ходового колеса 1 с.33 м;
dк= 02Dк=01 – диаметр цапфы м;
Сопротивление передвижению крана без груза:
Статическая мощность электродвигателя:
где т=06 -скорость передвижения крана мс;
Fпер=554858 - сопротивление передвижению крана Н
Поскольку в приводе механизма передвижения должно быть установлено два одинаковых электродвигателя на каждый из них приходится (05..06)Nc т.е. 43..52 кВт. Примем статическую мощность электродвигателя Nc=48 кВт.
Номинальная мощность электродвигателя принимается равной или несколько большей статической мощности. С учетом этих указаний из 6 с.45 выбираем крановый электродвигатель с фазным ротором MTF 112-6 имеющим для группы классификации механизма М3 номинальную мощность Nд=58кВт; частоту вращения n=915 мин-1; Момент инерции ротора Ip=027 кгм2. На рисунке 5.2 показана конструктивная схема электродвигателя MTF 112-6.
Рисунок 5.2 Конструктивная схема электродвигателя MTF 112-6 и его размеры
Таблица 5.1 - Основные габаритные и установочные размеры
Номинальный момент электродвигателя:
гдеNд=58 – номинальная мощность электродвигателя кВт;
n=915 – частота вращения мин-1
гдеNc=58 - статическая мощность электродвигателя кВт;
kp=22 – коэффициент учитывающий сопротивление трения реборд ходовых колес и торцов ступиц колеса 1 с.23
Исходя из этой мощности и требуемого передаточного числа выбираем для группы классификации механизма 3М редуктор типа ВК-600 5 с.426 имеющий номинальную мощность Nр=184 кВт частоту вращения nр=750 обмин и передаточным числом ip=1774. Габаритная схема редуктора ВК-600 представлена на рисунке 5.3.
Основные размеры редуктора представлены в таблице 5.2.
Таблица 5.2 - Основные размеры редуктора
Рисунок 5.3 - Габаритная схема редуктора ВК-600 и его размеры
Муфта соединяющая электродвигатель с редуктором:
где Fпер=554858 - сопротивление передвижению крана с номинальным грузом Н;
Dк = 05 – диаметр ходового колеса м;
Выбираем упругую втулочно-пальцевую муфту с крутящим моментом 250 Нм. Диаметр муфты D=200 мм момент инерции Iм=024 кгм2 и масса 135 кг. Конструктивная схема упругой втулочно-пальцевой муфты с тормозным шкивом показана на рисунке 5.4.
Рис 5.4 Габаритная схема упругой втулочно-пальцевой муфты с тормозным шкивом
Основные размеры муфты представлены в таблице 5.3
Таблица 5.3 - Основные размеры муфты
Муфты соединяющие редуктор с колесом:
Номинальный момент на тихоходном валу редуктора :
где Nр=27 -мощность редуктора кВт;
nр=1000– частота вращения редукторамин-1
где Fпер= - сопротивление передвижению крана с номинальным грузом Н;
Dк =05 – диаметр ходового колеса м;
Выбираем по ГОСТ 5006 зубчатую муфту с наибольшим передаваемым крутящим моментом 6300 Нм и моментом инерции муфты Iм=025 кгм2 и массой 226 кг. Конструктивная схема зубчатой муфты представлена на рисунке 5.5.
Рисунок 5.5 Габаритная схема муфты типа МЗ
Основные размеры муфты представлены в таблице 5.4
максимальный момент Нм
Фактическая скорость передвижения крана:
отличается от ближайшего значения 063 мс по 1 с.6 из стандартного ряда на 45% что допустимо.
dk=01 – диаметр цапфы вала м;
=00005 – коэффициент трения качения ходовых колес по рельсам с плоской головкой м;
Dk=05 – диаметр ходового колеса м
Т.к. в механизме используется два электродвигателя средний пусковой момент следует умножить на два: Mср.п.=210138=20277 Нм.
гдеF’пер=42742 - сопротивление передвижению тележки без груза Н;
ip=249 – передаточное число редуктора
гдеIp=027 – момент инерции ротора электродвигателя кгм2;
Фактическое время пуска механизма передвижения крана без груза:
где=12 – коэффициент учитывающий влияние вращающихся масс привода механизма (кроме ротора двигателя и муфт) 1 с.25;
I=102 - суммарный момент инерции вращающихся масс кгм2;
n=915– число оборотов электродвигателя обмин;
Мср.п=20277 - средний пусковой момент электродвигателя Нм;
Мс=8257 - момент статических сопротивлений при работе крана без груза Нм;
m=24800 – масса крана кг;
ф=06 - фактическая скорость передвижения крана мс;
гдефпер=06 – фактическая скорость передвижения крана мс;
tфп=594 - фактическое время пуска механизма без груза с;
amax=05 – максимально допустимое ускорение крана мс2
Условие выполняется aФamax или 011 мс205 мс2.
гдеz=4 – общее число ходовых колес;
m=28400 – масса крана кг
где=139302– суммарная нагрузка на приводные колеса Н;
=42742 – полное сопротивление передвижению без груза Н;
Dk=05 – диаметр ходового колеса м;
aф=011 фактическое ускорение крана без груза мс2;
Максимальное допустимое замедление крана при торможении:
φ=015 – коэффициент сцепления ходовых колес с рельсами (при работе в помещении);
kφ=12 – коэффициент запаса сцепления;
f=002 – коэффициент трения в подшипниках опор вала ходового колеса (для конических);
Dk=05– диаметр ходового колеса м;
=00005– коэффициент трения качения ходовых колес по рельсам с плоской головкой м
по 1 с.32 принимаем =02 мс2.
Время торможения крана без груза:
где=02 максимальное допустимое замедление крана при торможении мс2;
=06фактическая скорость передвижения крана мс
Сопротивление при торможении крана без груза:
гдеm=28400 – масса кранакг
Момент статических сопротивлений на тормозном валу при торможении крана:
где =194282 -сопротивление при торможении тележки без груза Н;
ip=249 – передаточное число редуктора.
Момент сил инерции при торможении крана без груза:
где=12 – коэффициент учитывающий влияние вращающихся масс привода механизма (кроме ротора двигателя и муфт);
n=915– число оборотов двигателя обмин;
m=28400 масса крана кг
tТ=3- время торможения крана без груза с
где=9656 – момент инерции при торможении крана без груза Нм;
=2089 – момент статических сопротивлений на тормозном валу при торможении крана Нм
Так как в данном механизме используется два тормоза расчетный тормозной момент для выбора тормоза будет равен:
Из 1 с.341 выбираем тормоз ТКГ-200 с тормозным моментом 250 Нм диаметром тормозного шкива DT=200 мм.тормоза 38 кг. Регулировкой можно получить требуемый тормозной момент =7567 Нм. На рисунке 5.6 представлена конструктивная схема тормоза типа ТКГ.
Рисунок 5.6 Конструктивная схема тормоза типа ТКГ
Основные размеры тормоза типа ТКГ-200 представлены в таблице 5.5
Таблица 5.5 - Основные размеры тормоза типа ТКГ-200
гдеф=06 - фактическая скорость передвижения крана мс;
гдеtТ=3 - время торможения крана без груза с
Условие выполняется или 09м>024 м.
6 Компоновка механизма передвижения крана
На основе рассчитанных параметров и выбранных элементов механизма передвижения тележки производим компоновку всех его составных частей их взаимное расположение в масштабе представлено на рисунке 5.7.
На консольных кранах механизм передвижения с раздельным приводом имеет по одному приводу с двух сторон в нижней части крана. Ходовое колесо - 1 связано с тихоходным валом редуктора - 3 через зубчатую муфту - 2. Первый вал редуктора связан с выходным валом двигателя - 6 упругой втулочно-пальцевой муфтой - 5 половина этой муфты укрепленная на валу редуктора одновременно служит тормозным шкивом на котором находится тормоз - 4.
- ходовое колесо; 2 - муфта зубчатая; 3 – редуктор; 4 - тормоз; 5 - муфта упругая втулочно-пальцевая с тормозным шкивом; 6 - электродвигатель.
Рисунок 5.7 - Компоновка механизма передвижения крана
Расчет на прочность элементов установки барабана
1 Толщина цилиндрической стенки
Принимаем в качестве материала барабана чугун марки СЧ 15 ([]сж=130 МПа ).
Определяем приближенное значение толщины стенки барабана:
t=00135 - шаг нарезки м;
[]сж=130 - допускаемое напряжение сжатия для материала барабана МПа
Уточним полученное значение для этого определим коэффициент влияния деформации стенки барабана и каната:
гдеЕк=88260 – модуль упругости каната МПа;
Еб – модуль упругости стенки барабана для чугунных барабанов Еб=98000 МПа;
Fк=5387 – площадь сечения всех проволок каната мм2;
С учетом уточнений толщина цилиндрической стенки барабана:
Учитывая что стенка барабана в процессе эксплуатации изнашивается принимаем =10 мм.
2 Устойчивость цилиндрической стенки барабана
Для определения необходимости проверки устойчивости подсчитываем номинальное напряжение сжатия в стенке барабана:
При этих параметрах из 9 с.94 следует что проверку необходимо производить если отношение . Для проектируемого барабана . Следовательно проверки устойчивости стенки барабана не требуется.
3 Крепление каната к барабану
Наибольшее применение находит крепление каната планками прижимающими канат к барабану. При этом канат из крайней канавки барабана переводят сразу в третью для чего частично вырубают выступы нарезки которые разделяют канавки. Среднюю же канавку используют для установки крепежных болтов и шпилек. На рисунке 6.1 показана схема крепления каната на барабане прижимными планками.
Рисунок 6.1 - Схема крепления каната на барабане прижимными планками
Применяя способ крепления прижимными планками с трапециевидными пазами прижимающими два соседних витка определим суммарное усилие растяжения болтов:
где f=010..012 – коэффициент трения между канатом и
барабаном принимаем f=010;
γ=40 – угол наклона боковой грани трапециевидного выреза в
α=4 – угол обхвата барабана неприкосновенными витками;
е – основание натурального логарифма
Используя нормализованные планки ПО “Сибтяжмаш” для диаметра каната 12 мм задаемся диаметром болта М12 по диаметру отверстия в планке. Тогда необходимое число болтов выполненных из стали ВСт3сп (тек=230 МПа):
где k≥15 –коэффициент запаса надежности крепления каната к
барабану примем k=15;
- приведенный коэффициент трения между канатом и поверхностью планки где f =01 – коэффициент трения между канатом и барабаном γ=400 – угол наклона боковой грани трапециевидного выреза в планке к вертикали ;
- допускаемое напряжение растяжения болта;
d=0012 – диаметр одного болта м;
l=0045 – расстояние от дна канавки на барабане до верхней плоскости прижимной планки м
принимаем число крепежных болтов z=8.
4 Расчет болтов соединяющих зубчатый венец с барабаном
Соединение осуществляем болтами для отверстий из под развертки по ГОСТ 7817-80 материал болтов – сталь 45 предел текучести материала т=353 МПа. Болты устанавливаем на диаметре окружности Dокр=315 мм. . На рисунке 6.2 показана схема соединения зубчатого венца с барабаном.
Рисунок 6.2 - Схема соединения зубчатого венца с барабаном
Окружное перерезывающее усилие действующее на все болты:
DБ=035 – диаметр барабана м;
Dокр=0315 – диаметр окружности на которой устанавливаются
болты соединяющие зубчатый венец с барабаном м
Допускаемое напряжение среза болта:
гдет=353 - предел текучести материала МПа;
k1 – коэффициент безопасности для механизма подъема крана работающих с крюком k1=13 9 с.97;
k2 – коэффициент нагрузки для группы классификации М6 k2=11 9 с.97
Задаваясь числом болтов mб=6 определим их диаметр:
гдеPокр – усилие действующее на окружности установки болтов Н;
m’б – расчетное число болтов m’б=075mб;
mб – число установленных болтов;
[] – допускаемое напряжение среза болта МПа
Принимаем диаметр болта d=10 мм.
Определим напряжение смятия:
гдеb=0028 – расчетная длина болта м
Прочность болтов на смятие обеспечена так как допускаемые напряжения смятия болтов выполненных из стали 45 [см]=280 МПа.
5 Расчет оси барабана
При выбранном типе полиспаста положение равнодействующей натяжений каната относительно опор оси остается неизменным эта равнодействующая: .
В дальнейшем расчет будет вестись для опоры А и В равносильным т.к. барабан симметричен
Нагрузка на опору А оси при положении равнодействующей показанной на рисунке 6.1:
Нагрузка на опору В:
Нагрузка на ступицу D барабана (равнодействующую этой нагрузки полагаем приложенной в середине ступицы):
Нагрузка на ступицу C:
Определим изгибающие моменты:
Принимаем в качестве материала оси сталь 45. Предел прочности В=598 МПа предел выносливости -1=257 МПа.
Определим допускаемые напряжения при симметричном цикле:
где k0 – коэффициент учитывающий конструкцию детали (для валов осей и цапф k0=2..28 9 с.97) примем k0=25;
-1=257 - предел выносливости МПа;
[n] – допускаемый коэффициент запаса прочности для группы классификации М3 [n]=16
На рисунке 6.2 показана расчетная схема оси барабана в масштабе.
Рисунок 6.2 - Расчетная схема оси барабана
Предварительно диаметр оси под правой ступицей (здесь действует наибольший момент) определяем по формуле:
принимаем диаметр оси dD=70 мм.
6 Расчет подшипников на статическую грузоподъемность
На статическую грузоподъемность проверяют подшипники работающие при малых частотах вращения. Подбор подшипников выполняют для обеих опор вала. Выбираем подшипник шариковый радиальный сферический двухрядный по ГОСТ 28428-90.
Для диаметра оси в опоре А (см. рисунок 6.2) d=70 мм предварительно выбираем подшипник №1214 для него значение базовой статической радиальной грузоподъемности равно COr=19000 Н. При расчете на статическую грузоподъемность проверяют не будет ли радиальная Fr нагрузка на подшипник превосходить статическую грузоподъемность указанную в каталоге:
Найдем радиальные силы в точках А и В:
где RA=12567 - нагрузка на опору А Н;
Выбранные ранее подшипники удовлетворяют условию по формуле (6.20) оставляем “Подшипник 1214 ГОСТ 28428-90”
для опоры А и “Подшипник 1212 ГОСТ 28428-90” для опоры В.
Список используемых источников
Справочник по расчетам механизмов подъемно-транспортных машин. Ф.Л. Марон - 2-е изд. перераб. и доп. - Мн.: Высш. шк. 1983.- 350 с. ил.
Справочник по кранам: В 2 т. Т.1. Характеристики материалов и нагрузок. Основы расчета кранов их приводов и металлических конструкций В.И. Брауде М.М. Гохберг И.Е. Звягин и др.; Под общ. Ред. М.М. Гохберга. - Л.: Машиностроение. Ленингр. Отд-ние 1988. - 536 с.: ил.
Справочник по кранам: В 2 т. Т.2. Характеристики конструктивные схемы кранов. Крановые механизмы их детали и узлы. Техническая эксплуатация кранов М.П. Александров М.М. Гохберг А.А. Ковин и др.; Под общ. Ред. М.М. Гохберга. - Л.: Машиностроение. Ленингр. Отд-ние 1988 - 559 с.: ил.
Правила устройства и безопасной эксплуатации грузоподъемных кранов. ПБ 10-382-00. Утверждены постановлением Госгортехнадзора России от 31.12.1999г. N 38.
Курсовое проектирование грузоподъемных машин. Руденко Н.Ф. Александров М.П. и Лысяков А.Г. Изд. 3-е переработанное и дополненное. М. изд-во «Машиностроение» 1971 464 стр.
Крановое электрооборудование. Справочник под ред. канд. техн. наук А. А. Рабиновича.-М: 1979 239с. ил.
Расчеты крановых механизмов и их деталей. ВНИИПТМАШ. Издание 3-е переработанное и дополненное. М. «Машиностроение» 1971 496 стр. Додонов Б.П. Лифанов В. А. Грузоподъемные и транспортные устройства: Учебник для техникумов. - М.: Машиностроение 1984. - 136 с. ил.
Грузоподъемные машины: Учебник для вузов по специальности «Подъемно-транспортные машины и оборудование» М.П. Александров Л.Н. Колобов Н.А. Лобов и др.: - М.: Машиностроение 1986 - 400 с. ил.
Курсовое проектирование грузоподъемных машин: Учеб. пособие для студентов машиностр. спец. вузовС.А. Казак В.Е. Дусье Е.С. Кузнецов и др.; Под ред. С.А. Казака.-М.: Высш. шк. 1989.-319с.: ил.
общий вид передвижения тележки.dwg

передвижения тележки
Техническая характеристика
Скорость передвижения тележки
Кинематическая схема привода
общий вид.dwg

Механизм передвижения
подтележечного рельса
Металлоконструкция крана
Механизм передвижения крана
СФУ ИНиГ190205.65-2009 10.30.00 СБ
Продолжительность включения
передвижения тележки
Техническая характеристика
(без запасных частей)
Масса электрооборудования
Масса элементов крана
Схема запасовки каната механизма подъема
Кинематическая схема привода
механизма передвижения крана
механизма подъема крана
СФУ ИНиГ190205.65-2009 10.20.00 ОВ
сборочный сертеж передвижения крана.dwg

Сварные швы по ГОСТ 5264-80
Не стандартные швы выполнить
ручной дуговой сваркой
Контроль сварных швов - внешний
местах по всей длине каждого шва
Кинематическая схема привода
Техническая характеристика
Скорость передвижения крана
*Размеры для справок
Спецификация передвиж.dwg

СФУ НГиГ 190205.65 10.30.00 СБ
СФУ НГиГ 190205.65 10.31.00
СФУ НГиГ 190205.65 10.32.00
Болт М12-8g x 25.109.30ХГСА ГОСТ 15589-70
Шпонки ГОСТ 23360-78
Шпонка 10 x 9 x 32 ГОСТ 10748-79
Двигатель МТF 011-6 2кВт
Болт М16-8g x 25.109.30ХГСА ГОСТ 15589-70
Болт М20-8g x 25.109.30ХГСА ГОСТ 15589-70
Гайка М12 x 2-6H.04 ГОСТ 15522-70
Гайка М16 x 2-6H.04 ГОСТ 15522-70
Гайка М20 x 2-6H.04 ГОСТ 15522-70
Чертеж-барабан.dwg

Спецификация барабан.dwg

СФУ НГиГ 190205.65 10.40.00 СБ
Кольцо регулировочное
СФУ НГиГ 190205.65 10.41.00 СБ
СФУ НГиГ 190205.65 10.40.01
СФУ НГиГ 190205.65 10.40.02
СФУ НГиГ 190205.65 10.40.03
СФУ НГиГ 190205.65 10.40.04
СФУ НГиГ 190205.65 10.40.05
СФУ НГиГ 190205.65 10.40.06
СФУ НГиГ 190205.65 10.40.07
СФУ НГиГ 190205.65 10.40.08
СФУ НГиГ 190205.65 10.40.09
СФУ НГиГ 190205.65 10.40.10
СФУ НГиГ 190205.65 10.40.11
СФУ НГиГ 190205.65 10.40.12
СФУ НГиГ 190205.65 10.40.13
Рекомендуемые чертежи
Свободное скачивание на сегодня
Другие проекты
- 25.01.2023