Модернизация вертикально-сверлильного станка 2Н135Н




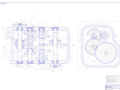
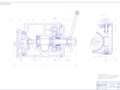
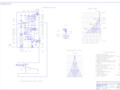
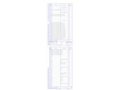
- Добавлен: 25.10.2022
- Размер: 1023 KB
- Закачек: 4
Описание
Состав проекта
![]() |
![]() |
![]() ![]() |
![]() ![]() |
![]() ![]() ![]() |
![]() ![]() |
![]() ![]() ![]() ![]() |
![]() ![]() ![]() ![]() |
![]() ![]() |
![]() ![]() |
![]() ![]() ![]() |
![]() ![]() ![]() ![]() |
![]() |
![]() ![]() ![]() |
![]() ![]() ![]() |
Дополнительная информация
Спецификация - Коробка подач.dwg

КП КССА 03.2135.02.00.000 СБ
КП КССА 03.2135.02.01.000
КП КССА 03.2135.02.02.000
КП КССА 03.2135.02.00.001
КП КССА 03.2135.02.00.002
КП КССА 03.2135.02.00.003
КП КССА 03.2135.02.00.004
КП КССА 03.2135.02.00.005
КП КССА 03.2135.02.00.006
КП КССА 03.2135.02.00.007
КП КССА 03.2135.02.00.008
КП КССА 03.2135.02.00.009
КП КССА 03.2135.02.00.010
КП КССА 03.2135.02.00.011
КП КССА 03.2135.02.00.012
КП КССА 03.2135.02.00.013
КП КССА 03.2135.02.00.014
КП КССА 03.2135.02.00.015
КП КССА 03.2135.02.00.016
КП КССА 03.2135.02.00.017
КП КССА 03.2135.02.00.018
КП КССА 03.2135.02.00.019
КП КССА 03.2135.02.00.020
Кольцо ГОСТ 13942-80
Шпонка ГОСТ 23360-78
Коробка подач.dwg

Шестерни должны иметь полное сцепление по ширине
Работа шестерни должна быть спокойной
Осевой люфт валов не более 0
Для смазки зубчатых передач и подшипников использовать масло
индустриальное И-20А ГОСТ 20799-75.
Обкатку коробки подач производить в течение 20 минут с
последовательным переключением скоростей
минут на максимальной скорости.
Кинематика.dwg

Технические характеристики
Класс точности по ГОСТ 8-82 Н
Наибольший диаметр сверления
Размер конуса шпинделя по ГОСТ 25557-82 Морзе 4 А16
Расстояние от торца шпинделя до
направляющих колонны
Наибольший ход шпинделя
Наибольшее перемещение сверлильной головки
Наибольшее расстояние от торца щпинделя
Длина и ширина рабочей поверхности стола
Наибольший ход стола
Число скоростей шпинделя 12
Пределы частоты вращения шпинделя
Размер Т-образного паза стола по
(ширина х длина х высота): 835х1030х2535
КП КССА 03.2135.00.00.000
Кинематическая схема станка
Спецификация - Тяговое устройство.dwg

КП КССА 03.2135.03.00.000 СБ
КП КССА 03.2135.03.01.000
КП КССА 03.2135.03.02.000
КП КССА 03.2135.03.03.000
КП КССА 03.2135.03.04.000
КП КССА 03.2135.03.00.001
КП КССА 03.2135.03.00.002
КП КССА 03.2135.03.00.003
КП КССА 03.2135.03.00.004
КП КССА 03.2135.03.00.005
КП КССА 03.2135.03.00.006
КП КССА 03.2135.03.00.007
КП КССА 03.2135.03.00.008
КП КССА 03.2135.03.00.009
КП КССА 03.2135.03.00.010
КП КССА 03.2135.03.00.011
КП КССА 03.2135.03.00.012
КП КССА 03.2135.03.00.013
КП КССА 03.2135.03.00.014
КП КССА 03.2135.03.00.015
КП КССА 03.2135.03.00.016
КП КССА 03.2135.03.00.017
КП КССА 03.2135.03.00.018
КП КССА 03.2135.03.00.019
Подшипники ГОСТ 8338-75
Шайба 2 Н.10 ГОСТ 11872-89
Тяговое устройство1.dwg

Размеры для справок.
Непараллельность оси шпиндельного отверстия направляющим
"Ласточкин хвост" не более 0
Защиту Т-образного паза от коррозии производить
ингибированной смазкой НТ-203 марки "В".
Содержание.docx
Выбор оптимальной структуры привода 8
Кинематический расчет привода 10
Расчет элементов коробки подач 14
Обоснование и выбор конструкции тягового механизма 25
Расчет тягового узла 26
Назначение системы смазки станка 37
Обоснование выбора органов управления коробки подач 39
Используемая литература 41
ПЗ-финал.docx
В ходе выполнения курсового проекта необходимо определить технические характеристики станка; выполнить кинематический расчёт привода подач выполнить расчет его элементов; разработать конструкцию тягового устройства; выбрать тип и систему смазки.
Расчет технических характеристик станка.
Параметры обработки:
Максимальный диаметр сверления отверстия: dmax=35 мм
Диапазон подач: S=01 25 ммоб
Пределы частот вращения шпинделя: n=315 1400 ммоб
Обрабатываемый материал: сталь 45.
Расчет ведем по наибольшим крутящему моменту и осевой силе. Обработка будет вестись в наихудших условиях при сверлении наибольшего отверстия в сплошном металле.
Расчет ведем по [1].
Выбираем подачу сверла: при сверлении отверстия d=35 мм в стали 45 сверлом из быстрорежущей стали S=01 ммоб
Скорость резания при сверлении рассчитывается по следующей формуле:
где Т – период стойкости и показатели степеней находим для сверления напроход сверлом из Р6М5 с подачей s= 01 ммоб принимаем:
СV =7; q = 04; y = 07; m = 02; T = 70 мин.
KV- общий поправочный коэффициент на скорость резания учитывающий фактические условия резания:
KV = KМV KlV KИV (1.2)
где KМV – коэффициент учитывающий качество обрабатываемого материала;
KИV – коэффициент учитывающий материал инструмента.
где sB – физический параметр характеризующий обрабатываемый материал;
КГ и nv – коэффициент и показатель степени характеризующие группу стали по обрабатываемости.
KИV = 1 (материал – Р6М5);
KlV = 1 т.к. предполагаем обработку отверстия глубиной до трех диаметров.
Тогда KV = 1×1×1 = 1
Частота вращения сверла:
Крутящий момент Mкр:
коэффициенты и показатели степеней:
СМ = 00345; у = 08; q = 2;
Коэффициент учитывающий условия обработки КР= КМР;
КМР определяется по формуле:
коэффициенты и показатели степеней определяем по таблицам:
СР = 68; у = 07; q = 1;
где f – коэффициент трения пинолью и корпусом шпинделя.
Тогда крутящий момент на валу:
где dР.К. – диаметр реечного колеса (принимаем аналогичное с прототипом).
Выбор оптимальной структуры привода.
Рассмотрим особенности различных вариантов компоновки привода станка.
Совмещенный привод выполняется в виде комплекса коробки скоростей коробки подач и шпиндельного узла помещенных в общий корпус. Такая конструкция наиболее компактна но часто имеет неудовлетворительные динамические характеристики и теплостойкость так как колебания и выделяемая в коробке теплота передается на шпиндель. Подача в этом случае задается на оборот шпинделя. Механизм подачи получает движение от шпинделя станка. Чтобы обеспечить жесткую кинематическую связь между шпинделем и тяговым устройством в приводе подач не рекомендуется использовать ременную и цепную передачи.
Рисунок 2.1 – Привод станка с совмещенной структурой
При реализации схемы привода с разделенной структурой механизм коробки подач получает движение от отдельного электродвигателя. Подача в этом случае задается минутная. В данном приводе между двигателем и коробкой подач необходимо большое количество понижающих передач так как необходимо понизить частоту примерно в 75 раз.
Рисунок 2.2 – Привод станка с разделенной структурой
Исходя из данных рекомендаций выбираем привод с совмещенной структурой который является наиболее оптимальным вариантом компоновки станка.
Кинематический расчет привода
Диапазон регулирования привода:
Знаменатель геометрического ряда =141.
Число ступеней привода подач:
Определяем подачи шпинделя. S1=01 ммоб; S2=014 ммоб; S3=02 ммоб; S4=028 ммоб; S5=04 ммоб; S6=056 ммоб; S7=08 ммоб; S8=1125 ммоб; S9=16 ммоб; S10=225 ммоб; S11=315 ммоб.
Составим структурную формулу привода на основании которой построим структурную сетку привода.
Рисунок 3.1- Структурная сетка привода
Строим кинематическую схему привода.
Рисунок 3.2 - Кинематическая схема привода подач
Исходя из кинематической схемы привода подач и структурной сетки строим график частот подач.
Рисунок 3.3 - График частот подач
Определяем передаточные отношения для каждой передачи. Покажем расчет для одной пары зубчатых колес остальные расчеты сведем в таблицу 3.1.
Суммарное число зубьев Z=60; i1ф=1.
Числа зубьев червячной передачи и передачи реечное колесо-рейка принимаем одинаковые со станком прототипом. Тогда
Вертикальный ход шпинделя на 1 оборот реечного колеса: zркmрк= 133
Для определения передаточного отношения пары зубчатых колес связывающих коробку скоростей и коробку подач запишем следующее уравнение:
Отсюда находим i1=1079.
Таблица 3.1 - Передаточные отношения
Передаточные отношения
Фактическое передаточное отношение
Определяем фактические величины подач и их отклонения от стандартных значений n1ф=1об. i1 i4 i6 i8=10805036025=00992 ммоб.
Отклонение от стандартного значения:
Аналогично находим значения для других частот.
Результаты расчета занесем в таблицу 3.2.
Таблица 3.2 - Частоты и их отклонения от стандартных значений
Определяем крутящие моменты на валах:
Расчет элементов коробки подач.
1 Расчет параметров зубчатых передач.
Произведем расчет самой нагруженной зубчатой передачи.
Выбираем материал колёс – сталь 40Х. Для этого материла среднее значение твёрдости НВср = 2855 тогда допускаемое контактное напряжение при числе циклов перемены напряжений NHO []H0 =18· НВср+ 67 = 18·2855+ 67 = 5809 Нмм2. Допускаемое контактное напряжение изгиба зубьев при числе циклов перемены напряжений NFO []F0 =103 · НВср = 103 · 2855 = 294 Нмм2.
где u - передаточное отношение рассчитываемой ступени.
Определим коэффициент долговечности:
где NHO= 25·106 ч – число циклов перемены напряжений соответствующее пределу выносливости;
N – число циклов перемены напряжений за весь срок службы.
где – угловая скорость вала с-1;
Lh – срок службы привода ч.
Lh = 365· Lr·tc ·Lс
где Lr = 6 лет – срок службы привода;
tc = 8 – продолжительность смены;
Lс = 2 – число смен.
Lh = 365· 6·8 ·2 = 35040 ч.
N = 576·065·35040 = 13· 107 ч
т.к. N > NHO то принимаем КHL = 1.
Поэтому []H1 = []H0 и []F1 = []F0.
Определяем главный параметр – межосевое расстояние аw мм:
где Ка – вспомогательный коэффициент Ка = 495;
u – передаточное отношение u = 4;
Т2 – вращающий момент на тихоходном валу редуктора;
a – коэффициент ширины венца колеса a = 012;
[]H – допускаемое контактное напряжение колеса Нмм2;
КН – коэффициент неравномерности нагрузки по длине зуба КН = 1.
Полученное значение округляем до ближайшего из ряда нормальных линейных размеров. Принимаем аw = 40 мм.
Определяем модуль зацепления.
гдеКm = 68 – вспомогательный коэффициент;
d2 – делительный диаметр колеса мм;
d2 = 2·aW·u(u+1)= 2·40·4(4+1)=64 мм.
b2 – ширина венца колеса мм;
b2 = a · aW = 012·40 =5 мм.
[]F – допускаемое напряжение изгиба колеса []F = 294 Нмм2.
Принимаем стандартное значение m=1 мм.
Вследствие наложения венца зубчатого колесо на тело смежного вала конструктивно увеличиваем модуль до 125 мм.
Уточняем межосевое расстояние:
Основные геометрические параметры передачи
Геометрические параметры передачи i7 принимаем конструктивно с учетом ранее определенного межосевого расстояния и модуля.
Проверка межосевого расстояния:
Проверка пригодности заготовок колёс.
Dзаг. ≤ Dпред.; Sзаг ≤ Sпред
Диаметр заготовки шестерни Dзаг= da1+6=20+6=26 мм ≤125 мм
Размер заготовки колеса Sзаг=b2+4=10+4=14 мм ≤80 мм
Проверка на контактные напряжения H:
где Ft-окружная сила в зацеплении Н;
Ft=2 T2 103d2=2 273 10380 = 6825 H
K - вспомогательный коэффициент для прямозубых K=436
KHα = 1 - коэффициент учитывающий распределение нагрузки между зубьями;
KHv - коэффициент динамической нагрузки. Определяется в зависимости от окружной скорости v:
Принимаем девятую степень точности.
Проверка на напряжения изгиба зубьев шестерни F1 и колеса F2.
где = 1 - коэффициент учитывающий распределение нагрузки между зубьями;
=1205 - коэффициент динамической нагрузки;
=407;=361 - коэффициенты формы зуба шестерни и колеса.
=1 - коэффициент учитывающий наклон зуба.
Проверочный расчёт для проектируемой зубчатой передачи выполняется.
Расчет последующих зубчатых передач проведем по аналогичной методике результаты расчетов внесем в таблицу 4.1.
Таблица 4.1 - Геометрические параметры передач.
Примечание: Во всех передачах модуль был конструктивно увеличен до 125 мм чтобы избежать наложение венцов зубчатых колес на тело смежного вала в передаче i1 модуль принимаем такой же как в прототипе (m=2 мм).
2 Расчет диаметров валов и выбор посадок
Диаметры посадок подшипников на валы:
где Т – момент на соответствующем валу Нм.
Предварительно выбираем шариковые радиальные однорядные подшипники ГОСТ 8338-75.
Внешний диаметр шлицев:
где r-радиус скругления у подшипника r=1 мм.
Принимаем прямобочные шлицы 611143 мм.
3 Составление расчетной схемы и определение реакций опор.
Для определения реакций в подшипниках будем рассматривать вал как балку нагруженную силами действующими на колеса.
АВ = 145 мм; ВС = 645 мм; CD = 595 мм.
Окружные силы действующие на колесо:
т.к. колеса прямозубые то радиальные составляющие находятся по формуле:
Составим уравнения моментов сил действующих на вал относительно точек D (задняя опора вала) и В (передняя опора вала):
Подставляя числовые значения проекций сил найдём составляющие реакций в опорах:
RBY = – 120 Н; RBX = 674 Н;
RDY = 515 Н; RDX = 71 Н.
X: –FrA + RBX – FrC + RDX = – 497 + 674 – 248 + 71 = 0
Y: FtA + RBY – FtC + RDY =1365 – 120 – 683 + 515 = 0
Силы действующие на вал в плоскости YOZ:
Рисунок 4.1 - Схема нагружения вала в плоскости YOZ.
Строим эпюры изгибающих моментов действующих на вал в плоскостях YOZ.
Рисунок 4.2 - Эпюра изгибающих моментов.
Реакции действующие на вал в плоскости XOZ:
Рисунок 4.3 - Схема нагружения вала в плоскости XOZ.
Строим эпюры изгибающих моментов действующих на вал в плоскостях XOZ.
Рисунок 4.4 - Эпюра изгибающих моментов.
Определяем суммарные реакции в подшипниках:
4 Проверочный расчёт валов.
Проверочный расчёт валов на прочность выполняем на совместное действие изгиба и кручения.
Цель расчёта – определить коэффициенты запаса прочности в опасных сечениях вала и сравнить их с допускаемыми.
Анализ конструкции вала а также эпюр изгибающих моментов МX и МY показывает что наиболее опасными сечениями являются сечения В и С.
Расчет сечения B на сопротивление усталости.
Концентратор напряжений в сечении B – посадка внутреннего кольца подшипника с натягом.
Определим соотношения ККd и К Кd концентратора напряжений.
Принимаем ККd = 25; К Кd = 19.
Так как посадочная поверхность вала шлифуется то KF=1 а также так как поверхность вала дополнительно не упрочняется то KV=1.
Суммарные коэффициенты КD и КD:
КD= (ККd+ KF-1) KV=(25+1-1)1=25(4.15)
КtD = (КtКd+ KF-1) KV=(19+1-1)1=19(4.16)
Результирующий изгибающий момент в рассматриваемом сечении B:
Осевой момент сопротивления сечения
Полярный момент сопротивления сечения
Амплитуда напряжений цикла:
а=И=MW=21×103100=21 МПа(4.20)
а=K 2=MK2WK=273×1032×200=68 МПа (4.21)
где MK – крутящий момент в сечении B.
Среднее напряжение цикла:
=002+2×10-4В=002+2×10-4×900=02(4.22)
Коэффициенты запаса по нормальным и касательным напряжениям:
Коэффициент запаса прочности по усталости в сечении B:
Сопротивление усталости в сечении B обеспечивается.
Расчет сечения C на сопротивление усталости.
Концентратор напряжений в сечении C – прямобочные шлицы.
К =17; К=155; Кd=077.
Тогда ККd = 17077=221; К Кd = 155077=201.
КD= (ККd+ KF-1) KV=(221+1-1)1=221
КtD = (КtКd+ KF-1) KV=(201+1-1)1=201
Результирующий изгибающий момент в рассматриваемом сечении C:
а=И=MW=31×103781=4 МПа
а=K 2=MK2WK=273×1032×266=51 МПа
где MK – крутящий момент в сечении C.
=002+2×10-4В=002+2×10-4×900=02
Коэффициент запаса прочности по усталости в сечении C:
Сопротивление усталости в сечении С обеспечивается.
5 Расчёт подшипников
Для рассчитываемого вала проверяем наиболее нагруженный подшипник.
Выбираем подшипник шариковый радиальный однорядный ГОСТ 8338 –75 с параметрами d = 10 мм D = 22 мм В = 6 мм Cr = 334 кН Cor = 135 кН.
Пригодность подшипников определяется сопоставлением расчётной динамической грузоподъёмности с базовой или базовой долговечности с требуемой по условиям:
Crp ≤ Cr или L10h ≥ Lh.
Требуемая долговечность подшипника Lh = 14·104.
Расчётная динамическая грузоподъёмность определяется по формуле:
где RE – эквивалентная динамическая нагрузка Н;
- угловая скорость вала с-1;
m – показатель степени m = 3.
RE = V· Rr ·Kб ·Kт(4.29)
где V – коэффициент вращения V = 1;
Rr – суммарная реакция подшипника;
Kб – коэффициент безопасности =14;
Kт – температурный коэффициент = 1.
RE = 1· 1376 ·14 ·1 = 1926 Н
Условие Crp ≤ Cr выполняется.
Произведём расчёт подшипника на долговечность:
Расчёт подшипника на долговечность выполняется. Выбранный подшипник обеспечивает основные эксплуатационные требования
Обоснование и выбор конструкции тягового механизма.
Рассмотрим характеристики различных тяговых механизмов.
Передача винт-гайка качения:
Передача винт-гайка качения обладает свойствами позволяющими применять ее как в приводах подач без отсчета перемещений (универсальных станков силовых столов агрегатных станков) так и в приводах подач и позиционирования станков с ЧПУ. Передача обеспечивает высокую осевую жесткость и равномерность движения. Для передачи характерны высокий коэффициент полезного действия (08-09) небольшое различие между силами трения движения и покоя незначительное влияние частоты вращения винта на силу трения в механизме полное отсутствие осевого зазора. Недостатками являются высокая стоимость пониженное демпфирование отсутствие самоторможения достаточно низкая нагрузочная способность.
Передача винт-гайка скольжения:
Для передачи винт-гайка скольжения характерны:
Возможность использования малого шага и соответственно малое передаточное отношение при однозаходной резьбе и небольшой скорости подачи;
Самоторможение при использовании одно- и двухзаходных винтов и соответственно возможность применения передачи для вертикальных движений и узлов совершающих установочные перемещения под нагрузкой;
Относительно низкая износостойкость;
Низкий коэффициент полезного действия.
Передача зубчатое колесо – рейка:
К недостаткам передачи можно отнести: сложность обеспечения равномерности медленных движений особенно в точных станках отсутствие самоторможения. Однако большое передаточное отношение простота и высокий КПД делают этот привод высокоэффективным в токарных револьверных сверлильных станках а также в приводе различных вспомогательных перемещений.
Также существует несколько типов тяговых механизмов имеющих узконаправленную область применения. Так например в приводах подач автоматических и полуавтоматических станков широко применяются кулачковые механизмы. Для поперечно-строгальных станков в основном используется кулисный привод.
Исходя из приведенных характеристик тяговых механизмов для проектируемого привода подач выбираем в качестве тягового механизма передачу зубчатое колесо-рейка.
Расчет тягового узла.
1 Расчет параметров передачи зубчатое колесо–рейка.
Исходные данные для расчета:
z=13 – число зубьев шестерни;
m=3 мм – модуль передачи;
Т=104 Н·м – крутящий момент на валу.
Модуль передачи должен удовлетворять условию:
где km=13 – вспомогательный коэффициент для прямозубых передач;
kF=14 – коэффициент нагрузки на шестерне;
YF1- коэффициент учитывающий форму зуба;
z1 – число зубьев шестерни;
bm=12 - отношение ширины колеса к модулю;
FP1 - допускаемое напряжение для материала шестерни МПа.
FP=04·Flimb ·kFL (6.2)
kFL =21 – коэффициент режима нагружения и долговечности.
>246 мм значит модуль передачи удовлетворяет условию.
Геометрические параметры передачи занесем в таблицу.
Таблица 6.1 – Геометрические параметры передачи зубчатое колесо-рейка.
2 Расчет параметров червячной передачи.
Выбор материала червяка и венца червячного колеса. Наибольшей нагрузочной способностью обладают червячные передачи у которых червяки выполнены из легированной стали и витки подвергнуты термообработке до твердости (закалка ТВЧ цементация и пр.) с последующим их шлифованием и полированием.
Принимаем материал червяка – сталь 40Х закалка ТВЧ до твердости с последующим шлифованием и полированием витков. Тип червяка – эвольвентый.
В качестве венца червячного колеса принимаем безоловянную бронзу БрА9ЖЗЛ :
Определение основных параметров червячной передачи.
Коэффициент диаметра червяка q рекомендуется принимать в диапазоне:
Принимаем стандартное значение q=16.
Модуль упругости материалов червяка и колеса: МПа - сталь; МПа - бронза. Тогда приведенный модуль упругости
Определим скорость скольжения vs. Для этого определим окружную скорость червяка v1:
где n1 – частота вращения вала червяка.
Тогда скорость скольжения vs:
Так как червяк расположен вне масляной ванны то полученное значение уменьшаем на 15%. Тогда окончательно принимаем [H]=255 МПа.
Предварительная величина межосевого расстояния
По ряду Ra40 принимаем ближайшее стандартное значение aW=80 мм
Предварительная величина модуля зацепления
Принимаем стандартное значение m=2 мм.
Коэффициент смещения
При этом необходимо выполнения условия
Размеры нарезанной части червяка:
– делительный диаметр
– делительный угол подъема линии витков
– начальный угол подъема линии витков
– высота головки витков
где - коэффициент высоты головки (для всех видов червяков);
– диаметр вершин витков
– высота ножки витков
– диаметр впадин витков
Определяем длину нарезаемой части червяка b1. При x= -05 мм
Для шлифуемого червяка увеличиваем b1 на 35 мм. Тогда
Размеры венца червячного колеса:
– высота головки зубьев
где - коэффициент высоты головки зубьев для передачи со смещением;
– диаметр вершин зубьев колеса в среднем сечении
– высота ножки зубьев
где для эвольвентных червяков коэффициент высоты ножки
– диаметр впадин зубьев колеса в среднем сечении
– наибольший диаметр червячного колеса
В нашем примере при
Принимаем b2=27 мм.
Условный угол обхвата 2 червяка венцом колеса:
что находится в рекомендуемых пределах
Проверочный расчет передачи на сопротивление контактной усталости активных поверхностей зубьев червячного колеса.
Торцовый коэффициент перекрытия в средней плоскости червячного колеса
Принимаем коэффициент расчетной нагрузки KH=1.
Расчетное контактное напряжение
Условие сопротивления контактной усталости:
Условие выполняется.
Определение допускаемых напряжений изгиба при расчете зубьев колеса на сопротивление усталости при изгибе.
Так как червячная передача работает на очень низких скоростях принимаем коэффициент долговечности YN=1.
Проверочный расчет зубьев червячного колеса на сопротивление усталости при изгибе.
Окружная сила на червячном колесе
Эквивалентное число зубьев колеса
Принимаем коэффициент формы зуба червячного колеса в зависимости от .
В нашем примере для линейным интерполированием
Коэффициент расчетной нагрузки при расчете зубьев колеса на сопротивление усталости при изгибе
Напряжения изгиба зубьев колеса
Проверочный расчет выполняется.
3 Расчет диаметров валов и выбор посадок
Расчет вала-червяка.
Диаметр шейки вала под ступицей зубчатого колеса:
Принимаем диаметр буртика подшипника и диаметр распорного кольца 14 мм.
Расчет вала-шестерни.
Диаметр шейки вала под внутреннее кольцо подшипника:
Принимаем диаметр распорного кольца 40 мм.
4 Составление расчетной схемы и определение реакций опор.
АВ = 40 мм; ВС = 43 мм; CD = 20 мм.
Определим силы действующие на вал:
Осевая сила в зацеплении червячной передачи:
где и - крутящий момент на червяке и делительный диаметр червяка соответственно.
Составим уравнения моментов сил действующих на вал относительно точек C (задняя опора вала) и A (передняя опора вала):
RAY = – 3156 Н; RAX = – 1020 Н;
RCY = – 517 Н; RCX = – 316 Н.
X: RAX + FrB + RCX – FrD = – 1020 + 1937 – 316 – 601 = 0
Y: RAY + FtB + RCY – FtD = – 3156 + 5323 – 517 – 1651 = 0
Рисунок 6.1 - Схема нагружения вала в плоскости YOZ.
Рисунок 6.2 - Эпюра изгибающих моментов.
Рисунок 6.3 - Схема нагружения вала в плоскости XOZ.
Рисунок 6.4 - Эпюра изгибающих моментов.
5 Проверочный расчёт валов.
Анализ конструкции вала а также эпюр изгибающих моментов МX и МY показывает что наиболее опасным сечением является сечение В.
Концентратор напряжений в сечении B – ступенчатый переход от 45 к 30 с галтелью.
Принимаем К= 225; К = 175; Kd=077.
Тогда К Kd=292; К Kd=227.
КD= (ККd+ KF-1) KV=(292+1-1)1=292
КtD = (КtКd+ KF-1) KV=(227+1-1)1=227
а=И=MW=1324×1032700=49 МПа
а=K 2=MK2WK=104×1032×5400=96 МПа
6 Расчёт подшипников
Выбираем подшипник шариковый радиальный однорядный со стопорной канавкой ГОСТ 2893 –82 с параметрами d = 30 мм D = 62 мм В = 16 мм Cr = 195 кН Cor = 10 кН V=1 (вращается внутреннее кольцо подшипника) X=056.
Подшипники установлены по схеме враспор.
Определяем отношение
Тогда принимаем e=019 Y=23.
Так как >e то расчётная динамическая нагрузка определяется по формуле:
где КБ = 14 – коэффициент безопасности;
КТ = 1 – температурный коэффициент
Расчётная динамическая грузоподъемность
Расчёт подшипника на долговечность выполняется. Выбранный подшипник обеспечивает основные эксплуатационные требования.
Назначение системы смазки станка
Смазка станка осуществляется:
а)циркуляционной системой смазки сверлильной головки коробок скоростей и подач;
б)непосредственной набивкой полостей подшипников электродвигателя шпинделя;
в)смазкой зубчатых зацеплений и винта подъема стола;
г)поливкой маслом направляющих колонны.
Циркуляционная система смазки (рисунок 7.1) включает в себя резервуар 1 заполняемый маслом через отверстие 7 в правой стенке сверлильной головки насос шестеренный 4 пробку сливную с сетчатым фильтром 6. Насос приводиться в движение от вала коробки подач.
Подаваемое насосом масло поступает на смазку узлов коробки скоростей и коробки подач а затем сливаясь в резервуар 1 расположенный в корпусе сверлильной головки смазывает все ее механизмы.
Контроль за подачей смазки и ее уровнем в резервуаре осуществляется визуально при помощи маслоуказателей 2 (наличие масла) и 3 (уровень масла в резервуаре).
Рисунок 7.1 – Схема смазки принципиальная
Все вращающиеся поверхности смазка которых специально не оговорена должны быть смазаны смазкой ЦИАТИМ-201 ГОСТ 267-74.
Точки смазки периодичность смазочный материал указаны в таблице 7.1.
Таблица 5.1 - Перечень точек смазки.
ЦИАТИМ-201 ГОСТ 6267-74
Подшипники и зубчатые колеса
Коробка скоростей подач механизм подачи шпинделя
Обоснование выбора органов управления коробки подач
Рассмотрим достоинства и недостатки различных вариантов управления коробкой подач.
Коробки со сменными колесами применяют для упрощения конструкции станка в тех случаях когда потеря времени на перенастройку мала по сравнению с общим временем. Достоинства этой передачи – в малых осевых размерах; конструкция допускает большое количество передач; исключена аварийность.
Коробки подач с передвижными колесами позволяют передавать большие мощности и крутящие моменты при минимальных радиальных размерах. Передачи не участвующие в работе не изнашиваются поэтому данные коробки получили широкое распространение. Из недостатков таких коробок следует отметить сложность переключения передач связанную с остановкой привода; значительно большие осевые размеры; необходимость больших усилий при переключении крупных блоков.
Преимущества коробок с муфтами: малые осевые перемещения незначительные усилия при переключении возможность передачи вращения шевронными и косозубыми колесами. Недостатками их являются большие радиальные размеры потери и износ при холостом вращении постоянно сцепленных передач пониженный КПД коробки (затраты на трение в выключенных муфтах).
В современном станкостроении применяют механические электрические и гидравлические устройства переключения. Выбор системы управления зависит главным образом от того как часто приходится переключать и насколько велико время затрачиваемое на эту операцию по сравнению со штучным временем. Если станок предназначается для крупносерийного или массового производства то управление им должно быть полностью или частично автоматизировано. Органы ручного управления предусматривают рычажные реечные и винтовые механизмы. Используются они в тех случаях когда время переключения мало по сравнению с общим временем обработки.
В последнее время стали широко применять системы дистанционного управления. Одним из наиболее простых и надежных устройств является переключение коробок с электромагнитными муфтами.
Таким образом для проектируемого привода коробки подач используем метод переключения передвижными колесами с ручными органами управления.
В ходе выполнения курсового проекта произвели модернизацию вертикально-сверлильного станка 2Н135Н.
Были определены основные технические характеристики станка (диапазон частот вращения необходимую мощность электродвигателя).
Произведена модернизацию привода подач: выбрана и обоснована кинематическая схема привода определены геометрические параметры зубчатых передач валов. Выполнены проверочные расчеты основных элементов коробки подач (зубчатых передач валов подшипников).
Разработана конструкция тягового устройства.
Выбрана система смазки станка.
Используемая литература
Косилова А.Г. Мещеряков Р. К. Справочник технолога-машиностроителя – М.: Машиностроение; 1985 – 496 с.
Ф. М. Санюкевич Детали машин. Курсовое проектирование -
Брест БГТУ.; 2003 - 462с.
Шейнблит А. Е. Курсовое проектирование деталей машин –
Мн.: Выш. шк.; 1991 – 432 с.
Кочергин А. И. Конструирование и расчёт металлорежущих станков и станочных комплексов – Мн.: Выш. шк.; 1991 – 382 с.
Пуш В. Г. Конструирование металлорежущих станков –
М.: Машиностроение; 1977– 390 с.
Рекомендуемые чертежи
- 07.06.2021