Модернизация механизма привода режущего аппарата зерноуборочного комбайна ДОН-1500Б




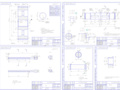
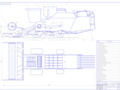
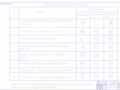
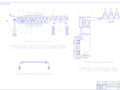
- Добавлен: 25.10.2022
- Размер: 1 MB
- Закачек: 2
Описание
Состав проекта
![]() |
![]() |
![]() ![]() ![]() |
![]() ![]() ![]() ![]() |
![]() ![]() ![]() |
![]() ![]() ![]() |
![]() ![]() ![]() ![]() |
![]() ![]() ![]() ![]() |
![]() ![]() ![]() |
![]() ![]() ![]() |
![]() ![]() ![]() ![]() |
![]() ![]() ![]() |
![]() ![]() ![]() ![]() |
![]() ![]() ![]() |
![]() ![]() ![]() ![]() |
![]() ![]() ![]() |
![]() ![]() ![]() ![]() |
![]() ![]() ![]() ![]() |
![]() ![]() ![]() |
![]() ![]() ![]() ![]() |
![]() |
![]() ![]() ![]() |
![]() ![]() ![]() |
![]() ![]() ![]() |
![]() ![]() ![]() |
![]() ![]() ![]() |
![]() ![]() ![]() |
![]() ![]() ![]() |
![]() ![]() ![]() |
![]() ![]() ![]() |
![]() ![]() ![]() |
![]() ![]() ![]() |
Дополнительная информация
Лист 1.dwg
Валовое производство
кормовых корнеплодов
Характеристика хозяйственной
деятельности ОАО"Столбцовский райагросервис
- естественные сенокосы и пастбища
Валовое производство зерна
Количество тракторов
Среднегодовое количество работающих
Валовое производство сахорной свеклы
лист 9.cdw

Эксплуатационные затраты
производительности труда
Удельная материалоёмкость
Технико-экономические
Производительность труда
Срок возврата инвестиций
Удельная энергоёмкость
Годовой объём работы
Прямые затраты труда
Технико-экономические показатели.
Лист 7.dwg
а) без установки упругих элементов
б) при установке упругих элементов.
Спектограммы усилия и
Лист 3.dwg
-система упругих элементов.
Механизм разгона ножа
привод режущего аппарата
и установка пружины на жатке.
Привод режущего аппарата
Схема установки пружин на жатке
лист 4.cdw

Харктер зависимости усилий в приводе от жёсткости
упругих элементов механизма разгона
Результаты исследований режущего аппарата
жатки и зависимостьусилия в приводе
от жёсткости упругих элементов
Результаты лабораторных исследований режущего аппарата жатки
Лист 7.cdw

а) без установки упругих элементов
б) при установке упругих элементов.
Спектограммы усилия и
лист 4.dwg
Харктер зависимости усилий в приводе от жёсткости
упругих элементов механизма разгона
Результаты исследований режущего аппарата
жатки и зависимостьусилия в приводе
от жёсткости упругих элементов
Результаты лабораторных исследований режущего аппарата жатки
Лист 6.dwg
Максимальный крутящий момент на приводном
Средний крутящий момент на приводном
Верхние значения соответствуют работе механизма привода без упругого
нижние-с упругими элементами.
Поступательная скорость агрегата
Максимальное усилие в шатуне
Коэффициент вариации крутящего момента
Коэффициент стабилизации круцящего момента
Мощность на привод режущего аппарата
Результаты полевых исследований жатки
Лист 2.cdw

Лист 8.dwg
Неуказанные предельные отклонения размеров:
Радиусы закруглений - 3 мм.
Неуказанные предельные отклонения размеров:
Точность зубчатого колеса в соответствии
Неуказанные предельные отклонения
Сталь 45 ГОСТ 9650-80
Угол накл. линии зуба
Норм. исходный контур
Лист 1.cdw

Валовое производство
кормовых корнеплодов
Характеристика хозяйственной
деятельности ОАО"Столбцовский райагросервис
- естественные сенокосы и пастбища
Валовое производство зерна
Количество тракторов
Среднегодовое количество работающих
Валовое производство сахорной свеклы
Лист 5.dwg
качающейся шайбы: а) при установке упругих элементов; б) при стандартом приводе.
Зависимость изменения средних значений крутящего момента в зависимости от частоты вращения приводного
вала механизма качающейся шайбы: а) при установке упругих элементов; б) при стандартном приводе.
Зависимость изменения значений
велечины усилия привода ножа и
крутящего момента от частоты
вращения приводного.
Лист 8.frw

Неуказанные предельные отклонения размеров:
Радиусы закруглений - 3 мм.
Неуказанные предельные отклонения размеров:
Точность зубчатого колеса в соответствии
Неуказанные предельные отклонения
Сталь 45 ГОСТ 9650-80
Угол накл. линии зуба
Норм. исходный контур
Лист 5.cdw

качающейся шайбы: а) при установке упругих элементов; б) при стандартом приводе.
Зависимость изменения средних значений крутящего момента в зависимости от частоты вращения приводного
вала механизма качающейся шайбы: а) при установке упругих элементов; б) при стандартном приводе.
Зависимость изменения значений
велечины усилия привода ножа и
крутящего момента от частоты
вращения приводного.
Лист 3.cdw

-система упругих элементов.
Механизм разгона ножа
привод режущего аппарата
и установка пружины на жатке.
Привод режущего аппарата
Схема установки пружин на жатке
лист 9.dwg
Эксплуатационные затраты
производительности труда
Удельная материалоёмкость
Технико-экономические
Производительность труда
Срок возврата инвестиций
Удельная энергоёмкость
Годовой объём работы
Прямые затраты труда
Технико-экономические показатели.
Лист 6.cdw

Максимальный крутящий момент на приводном
Средний крутящий момент на приводном
Верхние значения соответствуют работе механизма привода без упругого
нижние-с упругими элементами.
Поступательная скорость агрегата
Максимальное усилие в шатуне
Коэффициент вариации крутящего момента
Коэффициент стабилизации круцящего момента
Мощность на привод режущего аппарата
Результаты полевых исследований жатки
ВВЕДЕНИЕ ( с 8 ).docx
С появлением на рынке высокопроизводительных комбайнов эффективность их использования значительно снизилась из-за уменьшения урожайности убираемых культур. Технические возможности этих машин зачастую остаются нереализованными в результате чего сроки уборки и себестоимость производства зерна фактически увеличиваются.
В этих условиях загрузить высокопроизводительные комбайны можно как за счет увеличения поступательной скорости так и ширины захвата агрегата.
Увеличение ширины захвата агрегата приводит к созданию громоздких маломаневренных и ненадежных машин.
Одним из перспективных направлений повышения поступательной скорости машины является увеличение числа двойных ходов ножа режущих аппаратов сегментно-пальцевого типа с одновременным снижением инерционных сил за счет установки упругих элементов между ножом и пальцевым брусом.
Актуальным остаются вопросы энергетических соотношений работы периода пуска и остановки режущего аппарата с введением в механизм привода упругих элементов в связи с чем необходимо дальнейшее изучение этого направления.
2 характкристика работы + литература (20).docx
1 Повышения производительности и снижения энергоёмкости
привода режущего аппарата.
Результаты исследований конструкций приводных механизмов режущего аппарата жаток свидетельствуют о большом их разнообразии. Наиболее перспективным является механизм качающейся шайбы обеспечивающий малую энергоемкость привода.
При создании скоростных режущих аппаратов выгоднее увеличивать
число двойных ходов ножа. Это направление требует наименьших изменений в конструкции существующего аппарата и конструкциях уборочных машин в
целом. Следовательно в большей степени сохраняются наиболее отработанные и проверенные долголетней эксплуатацией элементы конструкцийа также не нарушается взаимосвязь массовых деталей режущего аппарата.
Режущий аппарат нормального резания с одинарным пробегом ножа
являясь лучшим по качеству выполнения технологического процесса надежности метали - и энергоемкости способен обеспечить качественный срез зерновых культур с возрастанием поступательной скорости при пропорциональном увеличении числа двойных ходов ножа.
Увеличение числа двойных ходов ножа режущего аппарата приводит к повышению динамической нагруженности звеньев приводного механизма инерционными силами. При этом следует уделить серьезное внимание уравновешиванию силы инерции ножа. Существенную пользу в этом вопросе может оказать создание искусственной колебательной системы: постановкой упругого элемента определенной жесткости между ножом и пальцевым брусом. В этом случае кинематическая цепь привода разгружается от действия силы инерции которые будут передаваться на раму.
2 Теоретическое обоснование параметров упругого элемента для
внутренего уравновешивания режущего аппарата.
Теоретическое исследование основных кинематических параметров режущего аппарата позволило определить что нож приводимый в действие механизмом качающейся шайбой совершает не чисто гармонические колебания.
Перемещение скорости х и ускорение х ножа режущего аппарата от средины хода можно выразить через следующие зависимости:
где r - наибольшее перемещение ножа от середины хода;
соs - частота вращения приводного вала;
ат- угол установки оси шайбы к оси ведущего вала;
Для определения жесткости уравновешивающей пружины воспользуемся условием уравновешивания любых механизмов
где T П - кинетическая и потенциальная энергия механизма;
qi - обобщенная координата.
По этому условию для уравновешивания силы инерции жесткость упругого элемента с линейной характеристикой должна соответствовать
При установившемся движении разность Рр силы инерции Pj и упругости Рп в любой момент времени будет
Тогда максимальное значение силы в приводе при установке упругого элемента равно
Максимальное значение силы в приводе без установки упругого элемента
Определим отношение максимального значения силы в приводе без упругого элемента к максимальному значению силы в приводе с упругим элементом
Анализ показывает что для режущего аппарата с углом установки качающейся шайбы аг=15° амплитуда разности сил при введении упругого элемента с линейной характеристикой составит менее 8% от силы инерции без введения последнего.
Выявление нагрузочных способностей позволило определить наиболее приемлемую конструкцию упругого элемента - это цилиндрическая винтовая пружина растяжения-сжатия.
Учитывая то что пружина может иметь начальную кривизну и некоторую несоосность витков и что сила может оказаться приложенной с небольшим
эксцентриситетом необходимо во избежание выпучивания пружины ставить ее на оправках и монтировать в гильзах что приводит к нежелательному трению о направляющие.
По этому предложено заменить пружину растяжения-сжатия парой пружин растяжения предварительно натянутых в диаметрально противоположные стороны (не менее половины хода ножа).
Для того чтобы блок уравновешивания не препятствовал свободному сходу скошенной массы с режущего аппарата предложено вывести упругие элементы из зоны резания и установить их на боковинах жатки (рис. 1). Соединение пружины с режущим ножом выполнено гибким элементом (тросом) переброшенным через роликовые блоки.
Рисунок 2.1 - Схема установки пружин на жатке.
При установке вместо одной пружины растяжения-сжатия двух пружин растяжения для компенсаций одних и тех же силы инерции необходимо чтобы их жесткость была в два раза меньшей. То есть при установке n-ого количества пружин жесткость каждой должна быть в п раз меньше необходимой.
Решение задачи внутреннего уравновешивания созданием колебательной системы нож - упругий элемент - пальцевой брус на ряду со снижением нагрузки при установившемся режиме работе не позволяет уменьшить конструктивные размеры звеньев механизма привода так как сопротивлениеупругого элемента в момент пуска может оказаться значительным.
Наиболее неблагоприятным случаем при пуске является нахождение ножа в крайних положениях. При этом привод испытывает сопротивление от сил трения и сил упругости деформирующейся пружины. В этот момент преобладание силы сопротивления при пуске десятикратное над максимальной силой пульсирующей в приводе при установившемся режиме работе.
Рисунок 2.2 - Механизм разгона ножа.
-колебатель 2-тяга 3-толкатель 4-двухполостный цилиндор
и 6-упругие элементы 7 и 8-шайбы 9-буртик 10-нож.
Для снижения пускового момента разработан механизм разгона ножа выполненный в виде симметричного двухполостного цилиндра 4 корпус которого жестко связан с режущим ножом 10 (рис. 2). В каждой из полостей цилиндра расположены предварительно сжатые упругие элементы 5 и 6 оси которых расположены вдоль линии возвратно-поступательного движения ножа. Упругие элементы опираются на шайбы 7и 8 которые в свою очередь опираются на буртик 9 расположенный внутри корпуса механизма разгона. Между этими шайбами установлен толкатель 3 который шарнирно связан при помощи тяги 2 с концом колебателя 1механизма качающейся шайбы.
Устройство работает следующим образом.
С началом движения колебателя 1 по часовой стрелке его воздействие через тягу 2 толкатель 3 шайбу 8 упругий элемент 5 корпус 4 механизма разгона передается ножу 10 движущемуся в этом случае вправо и деформирует систему упругих элементов 11. Она деформируется до тех пор пока возрастающая сила их сопротивления не станет равной силе предварительного сжатия упругого элемента 5.
С этого момента наряду с продолжающейся деформацией упругих элементов 11 начинается сжатие упругого элемента 5 а поскольку его жесткость С; меньше суммарной жесткости с2 системы упругих элементов 11 т. е. Ci c2 он деформируется более интенсивно. При этом приводу оказывает сопротивление система элементов состоящая из упругих элементов 11 упругого элемента 5 суммарная жёсткость которой из условия
имеет величину меньшую меньшей из жестокостей соответственно и сила в приводе вызванная перемещением толкателя 3 будет меньше чем усилие вызванное деформацией системы упругих элементов 11 при отсутствии упругих элементов в механизме разгона.
При максимальном повороте колебателя 1 он заставит толкатель 3 пройти половину длины рабочего хода ножа 10. Перемещение самого ножа 10 меньше на величину деформации упругого элемента 5. Сопротивление максимально в точке В - крайней правой точке движения колебателя и составляет величину р11 которая значительно меньше р (рис. 3). С началом обратного движения -против часовой стрелки колебатель ослабляет воздействие на упругие элементы 11 и упругий элемент 5 давая им возможность разжиматься. Поворачиваясь от нейтрального положения колебатель подталкивается некоторое время в этом направлении силами инерции ножа 10 движущегося справа налево и получающего энергию от упругого элемента 11 накопившего ее при деформации.
Рисунок 2.3 - Характер зависимости усилий в приводе от жёсткости
упругих элементов механизма разгона.
Движение из нейтрального положения влево нож 10 осуществляет под воздействием колебателя 1 и упругих элементов 11 и таким образом импульс получаемой ножом энергии больше чем мгновением ранее при движении его вправо когда он находился под воздействием колебателя а упругий элемент оказывал сопротивление этому воздействию. Именно поэтому при крайнем левом положении колебателя ход ножа а соответственно и деформация упругих элементов 11 на некоторую величину превышают ход его и деформацию этих упругих элементов в предыдущем крайнем положении - в правом а деформация упругого элемента 6 несколько меньше деформации элемента 5.
В следующий момент начинается движение ножа вправо осуществляемое воздействием колебателя и разгибающегося упругого элемента 11. Поскольку в крайнем левом положении деформация упругого элемента 11 по абсолютной величине превышает деформацию ее в предыдущем крайнем правом положении значит больше запас энергии накопленный указанным упругим элементом при изгибе и то усилие с которым он помогая колебателю воздействует на нож снова заставляя его двигаться вправо. Благодаря указанному усилию на нож при движении его вправо он получит большее
перемещение чем в предыдущем цикле - движение влево а деформация упругого элемента 5 по сравнению с деформацией элемента 6 уменьшится. Таким образом при разгоне с каждым последующим движением ножа величина хода его из стороны в сторону увеличивается а деформация упругих элементов 5 и 6 уменьшается доходя после завершения фазы разгона до величины их предварительного сжатия. Этот момент можно считать началом установившегося движения.
Совершая возвратно-поступательное движение нож осуществляет технологический процесс скашивания сельскохозяйственных культур. Необходимо отметить что такое плавное выведение режущего аппарата на рабочий режим с постепенным увеличением длины хода ножа за счет сокращения величины деформации упругих элементов 5 и 6 механизма разгона возможно лишь при совпадении частоты возмущающего воздействия колебателя с собственной частотой колебании ножа с упругими элементами 11.
Как известно при совпадении собственной и вынуждающей частот колебаний наступает явление резонанса войдя в который нож рискует увеличить амплитуду колебаний выше пределов позволяемых кинематикой привода. Однако отрицательного влияния резонансного разгона ножа на привод не происходит так как включаются упругие элементы 5 и 6 оказывающие в этом случае тормозящие воздействия на стремящийся к увеличению свой амплитуды нож. Таким образом система привода режущего аппарата находится в режиме близком к автоколебанию когда колеблющийся в резонансной зоне нож осуществляет процесс скашивания сельскохозяйственной культуры а привод играет роль своеобразной «подпитки» восполняющей потери энергии ножа на сопротивление срезу трение и. т. п.
Для того чтобы в процессе резания не происходила деформация упругих
элементов что может привести к снижению скорости резания и соответственно к забиванию режущего аппарата необходимо чтобы усилие предварительного сжатия упругих элементов было больше сил трения и сопротивления срезу
Минимальная величина предварительной деформации упругого элемента механизма разгона определится по следующей формуле
Жесткость упругих элементов 5 и 6 найдем из условия равенства максимального усилия сжатия системы элементов состоящей из упругих элементов 5 и 11 максимальной силе пульсирующей в механизме привода при установке упругого элемента
3 Экспериментальные исследования.
Согласно программе исследований на основании предложенной конструкции привода режущего аппарата а также теоретически обоснованных конструктивных параметров была изготовлена лабораторная установка на базе жатки ЖКС-7 комбайна ДОН-1500Б с экспериментальным режущим аппаратом которая отвечала всем требованиям работы серийного механизма привода ножа режущего аппарата комбайновых жаток (рис. 4). Для бесступенчатой регулировки частоты вращения приводного вала механизма качающейся шайбы использовали электродвигатель постоянного тока с изменением напряжения на обмотках возбуждения.
Испытания режущего аппарата проводили с использованием тензометрического оборудования и специально спроектированного оборудования на основе фотодиодов. Для этого были разработаны стенды и лабораторные установки позволяющие выявить конструктивно-режимные параметры режущего аппарата.
Обработку результатов исследований вели с использованием ПЭВМ методом вариационной статистики а также регрессионного и корреляционного анализа с использованием программ MathCAD 2000 professional и AutoCAD 2002.
Экспериментальные исследования проведены с регистрацией ряда силовых и кинематических параметров а именно:
-крутящий момент приводного вала - с помощью проволочных датчиков сопротивления наклеенных по мостовой схеме с последующим увеличением сигнала усилителем УБУ-5. Подвод питания и съем полученных электрических сигналов осуществлялся ртутно-амальгамированным токосъемником типа ТРАП конструкции ЦМИС;
-усилие на колебателе - проволочными датчиками сопротивления по мостовой схеме с последующим увеличением сигнала усилителем;
-угловая скорость приводного вала - предварительно - тахометром точно - специально разработанным механизмом на основе фоторезисторов;
-неравномерность вращения приводного вала и положение режущего аппарата - специально разработанным механизмом на основе фоторезисторов;
-поступательная скорость агрегата - штатным оборудованием комбайна ДОН-1500Б;
-вибрация жатки - вибрографом ВР-1А У 4.2.
Обработка и анализ полученных данных выполнены на основе теории ошибок с определением величины погрешности конечного результата и доверительной вероятности которой эта погрешность соответствует и математической статистики. Доверительная вероятность во всех случаях положена равной 095 (уровень значимости 005) что вполне достаточно для анализа исследуемых закономерностей. С целью вскрытия внутренней структуры динамики привода в процессе скашивания определены корреляционные функций и спектральные плотности крутящего момента приводного вала и усилия на колебателе.
4 Результаты экспериментальных исследования.
Результаты статистической обработки реализаций усилий и крутящих моментов в приводе режущего аппарата жатки с упругими элементами и без них в зависимости от частоты вращения приводного вала представлены в таблице 2.1.
Таблица 2.1. - Результаты лабораторных исследований режущего
Номинальный режим (5236 с"1)
Повышенный режим (62.83 с'1)
Без упру-гого эле-мента
С упру-гим элементом
Макси-мальное усилие Н
Макси-мальный крутящий момент Нм
Средний крутящий момент Нм
Зависимость изменения максимальных значений усилия в зависимости от вращения приводного вала механизма качающейся шайбы при установке упругих элементов и без них представлена на рисунке 5.
Рисунок 5. 4 - Зависимость максимальной величины усилия привода ножа
от частоты вращения приводного вала механизма ачающейся
а) при установке упругих элементов; б) при стандартном
Зависимость максимальных значений усилия в стандартном приводе и при установке упругих элементов от частоты вращения приводного вала описывается полиномами второго порядка что согласуется с теоретическими выкладками.
Коэффициент корреляции уравнения для свободного привода равен 0995; при установке упругих элементов - 0818.
Зависимость изменения средних значений крутящего момента от частоты вращения приводного вала механизма качающейся шайбы свободного привода и при установке упругих элементов представлена на рисунке 6.
Рисунок 2.5 - Зависимость изменения средних значений крутящего момента в
зависимости от частоты вращения приводного вала механизма
качающейся шайбы: а) при установке упругих элементов;
б) при стандартном приводе
Зависимость средних значений крутящего момента в свободном и экспериментальном приводе от частоты вращения приводного вала описывается полиномами второго порядка.
Коэффициент корреляции уравнения для свободного привода равен 0995; при установке упругих элементов - 0894.
Анализ результатов обработки данных по усилиям и крутящим моментам в приводе и показывает что динамическая напряженность работы механизма качающейся шайбы при ведении упругих элементов с линейной характеристикой снижается; усилие колебателя на всех режимах уменьшается наибольший эффект наблюдается при работе в зоне резонанса где максимальное усилие колебателя снижается до величины 205 Н против 2000 Н; одновременно падает величина среднего крутящего момента - на резонансной частоте момент снижается до величины 78 Нм против 108 Нм; почти на треть уменьшается амплитуда крутящего момента.
Анализ работы режущего аппарата на повышенном режиме выявил возможность увеличения частоты вращения приводного вала выше резонансного числа двойных ходов ножа с введением упругих элементов - при работе механизма даже на зарезонансном режиме (600 двойных ходов ножа) нагрузка на колебателе составила всего 612 Н что вдвое меньше нагрузки при работе свободного механизма на минимальном режиме (400 двойных ходов ножа) -1311 Н.
Неравномерность хода в зоне резонанса при установке уравновешивающих пружин снижается до 24% против 42% при свободном механизме. Это позволяет уменьшить нагруженность звеньев привода потери от повышенного среза и износ ременной передачи.
На привод режущего аппарата с упругими элементами требуется меньшая мощность - в зоне резонанса уменьшение достигает порядка 04 кВт (снижение на 178%) что позволит снизить энергоемкость привода и соответственно расход топлива.
Уровень шума косвенно характеризующий удары в сочленениях ниже на всех скоростных режимах соответственно увеличивается долговечность и повышается надежность работы режущего аппарата.
Длительность разгона и выбега при работе механизма привода с упругими элементами меньше чем без упругих элементов. В первом случае упругие элементы способствуют введению механизма в резонансный режим где режущий аппарат работает в устойчивой зоне динамического равновесия а при остановке - поглощают часть кинетической энергии накопленной механизмом.
Нагрузка колебателя при пуске режущего аппарата как с упругими элементами так и без них остается на уровне усилия при работе на номинальных оборотах без упругого элемента.
Наибольшее значение крутящего момента при пуске режущего аппарата с упругими элементами на всех режимах за исключением работы на номинальных оборотах выше чем при работе без упругих элементов однако значения моментов - величины одного порядка. В этом случае динамическая нагрузка от маховых масс меньше чем нагрузка создаваемая упругими элементами при работе вне резонансной зоны. При пуске режущего аппарата на номинальных оборотах наибольшее значение момента приводного вала в обоих случаях совпадает что объясняется кратковременностью переходного процесса когда динамические нагрузки от действия маховых масс становятся преобладающими.
Длительность разгона при работе привода с механизмом разгона дольше чем при его выключении что объясняется включением в работу механизма разгона. При этом нож режущего аппарата разгоняется постепенно достигая (после завершения фазы разгона) максимального значения хода.
При анализе результатов эксперимента выявлена тенденция уменьшения времени разгона режущего аппарата при увеличении частоты вращения приводного вала что хорошо согласуется с теоретическими предположениями.
При минимальных оборотах на фазу разгона понадобилось 65 двойных ходов ножа; при номинальной частоте - 5 и всего 4 цикла понадобилось при повышенной частоте вращения приводного вала механизма качающейся шайбы.
Нагрузка на колебателе и крутящий момент на приводном валу при пуске режущего аппарата на номинальной частоте с механизмом разгона остаются на уровне усилий при работе режущего аппарата на резонансной частоте что позволяет уменьшать конструктивные размеры приводного механизма а соответственно и металлоемкость конструкции.
Результаты эксперимента показали уменьшение вибрации при работе с упругим элементом в 14 точко-направлениях из 18.
Методика проведения производственных испытаний результаты производственных испытаний и расчет экономической эффективности применения скоростной жатки.
5 Производственные испытания
Результаты полевых исследований представлены в таблице 2.
Таблица 2.2 - Результаты полевых исследований жатки.
Число двойных ходов ножа режущего аппарата в минуту
Поступательная скорость агрегата мс
Максимальное усилие в шатуне Н
Максимальный крутящий момент на приводном валу Нм
Средний крутящий момент на приводном валу Нм
Коэффициент вариации крутящего момента
Коэффициент стабилизации крутящего момента
Мощность на привод режущего аппарата кВт
Верхние значения соответствуют работе механизма привода без упругого элемента нижние - с упругими элементами.
Максимальное усилие в приводе средний крутящий момент приводного вала и амплитуда колебаний момента при работе с упругим элементом во всех случаях ниже чем при работе без упругого элемента. Наибольший эффект имеет место на резонансном числе двойных ходов ножа (500) где усилие в приводе снижается в 49 раза а средний крутящий момент достигает 878 Нм против 1318 Нм. Коэффициент вариации уменьшается с 070 до 039 соответственно коэффициент стабилизации повышается до 179. Одновременно уменьшается мощность на привод снижение на резонансном режиме составляет 045 Н.
Информацию о внутренней структуре процессов дают корреляционные функции спектральные плотности усилия в приводе и крутящего момента на валу (рис. 7) при скашивании с упругими элементами и без них.
Рисунок 2.6 - Спектрограммы усилия (I) и крутящего момента (П) в приводе:
а) без установки упругих элементов б) при установке упругих элементов.
Анализ нормированной корреляционной функции усилия в приводе при скашивании без упругого элемента показывает что процесс носит ярко выраженный колебательный характер причем основная доля дисперсии приходятся на весьма узкий диапазон частот (порядка 1 Гц) близкий к частоте изменения силы инерции.
При скашивании с упругим элементом характер процесса резко изменяется: последний хоть и носит колебательный характер что связано с возвратно-поступательным движением ножа однако амплитуда колебаний стала намного ниже; сектор частот располагается в весьма широком диапазоне от _f= 0 до f = 6 Гц; максимум амплитуды спектральной плотности равен 05 Н2сек и в 8 раз меньше максимума при работе без упругого элемента. Анализ нормированных корреляционных функций крутящего момента приводного вала при кошении без упругого элемента и с ним показывает что процессы носят колебательный характер однако в первом случае процесс более динамичен
время корреляционной связи составляет 00051 сек против 00083 сек и имеет место значительное превышение амплитуды. Основной спектр частот при работе без упругого элемента приходится на область от f =1 до f =3 Гц с четко выраженным максимумом на частоте f =2 Гц. При работе с упругим элементом спектр дисперсий растягивается максимум не имеет такого четкого выражения и смещается в область частот порядка f =35 Гц. Значение последнего 2810"3 Нм2сек что в 25 раза меньше максимума при кошении без упруго элемента.
Список использованных источников.
Хайбуллин Р.Р. Обоснование метода внутреннего уравновешивания режущего аппарата уборочных машин. Сборник материалов региональной научно-практической конференции молодых ученых и специалистов часть 3. Оренбург РИК ГОУ ОГУ2004.-с. 148-150.
Хайбуллин Р.Р. Основные направления проектирования режущих аппаратов для работы на повышенных скоростях. Сборник докладов международной научно-технической конференции «Совершенствование инженерно-технического обеспечения технологических процессов АПК» выпуск 6 Оренбург 2005. - с. 43 45.
Хайбуллин P.P. Обоснование основных параметров механизма разгона режущего аппарата. Сборник докладов международной научно-технической конференции «Совершенствование инженерно-технического обеспечения технологических процессов АПК» выпуск 6 Оренбург 2005. - с. 45 47.
Хайбуллин P.P. Энергетические параметры режущего аппарата при введении упругого элемента в кинематическую цепь нож- пальцевый брус. Сборник докладов международной научно-технической конференции «Совершенствование инженерно-технического обеспечения технологических процессов АПК» выпуск 6 Оренбург 2005.-е. 47 50.
Хайбуллин P.P. Теоретическое исследование кинематики режущего аппарата приводимого в действие механизмом качающейся шайбы. Материалы международной научно-практической конференции «Эколого-технологическая правовая и социально-экономическая политика в сельском хозяйстве: история и современность» под общ. ред. С.А. Соловьева Н.Н. Дубачинской Оренбург: Издательский центр ОГАУ 2005. - с. 103 111.
Эксплуатация машинно-тракторного парка. Учебн. пособие. Под редакцией Ю.В.Будько.-Мн.:Ураджай1991.
Системы ведения сельского хозяйства РБ-Мн.:БелНИИЭИ АПК1996.- 332с
Концепция развития механизации и автоматизации сельскохозяйственного производства РБ на период до 2000 года -Ураджай1996.- 286 с.
Индустриальные технологии на мелиорированных земляхР.А.Мышко Г.Ф.Добыш и др.-Мн.: Ураджай1987.-195 с.
Нормирование и оплата труда в сельском хозяйстве. Методич. указания.Бусел И.П.Силкович Г.А.Шкор Т.И.-Мн.: Ротапринт БАТУ1995.-29 с.
Планирование и организация использования машинно-тракторного парка. Метод.указания.Бусел И.П.Силкович Г.А.Шкор Т.И.-Мн.: Ротапринт БАТУ1994. – 42 с.
Каталоги сельскохозяйственной техники нормативная и справочная литература периодические издания .
Техническая эксплуатация машинно-тракторного парка. Аллилуев В.А. и др. -М.:Агропромиздат 1991.- 285 с.
Сборник материалов паспортизации полей многолетних насаждений улучшенных кормовых угодий. - Мн.: Ротапринт БИМСХ1986.- 86 с.
Стандарт предприятия СТП БАТУ 01.01-96.Указания по оформлению документов дипломного и курсового проектов.-Мн.:БАТУ1996.- 58 с.
Эксплуатация машинно-тракторного парка. Ляхов А.П. Новиков А.В. и др. - Мн.: Ураджай 1991. – 248 с.
Техническая эксплуатация сельскохозяйственных машин (с нормативными материалами). - М.: ГОСНИТИ 1993. -327 с.
Методические указания по курсовому и дипломному проектированию “Проектирование центральных ремонтных мастерских хозяйств”. - Мн.: БАТУ 1994. -132 с.
Методические указания к практическому занятию на тему: “Научные основы распределения работ по ремонту и ТО машинного парка между уровнями РОБ АПК”. - Мн.: БАТУ 1993. -20 с.
Курсовое и дипломное проектирование по надежности и ремонту машин А.П. Смелов И.С. Серый В.Е. Черкун. -М.: Агропромиздат 1991.-184 с.
Технологические рекомендации по техническому перевооружению и реконструкции центральных ремонтных мастерских хозяйств. -М.: ГОСНИТИ 1989. -67 с.
Рекомендации по организации рабочих мест и их техническому оснащению в мастерских колхозов и совхозов. -М.: ГОСНИТИ 1989. -67
Ремонт и хранение техники в сельском хозяйстве. Суслов В.П. Подлекарев Н.Н. Суслов В.В. -Мн.: Ураджай 1989. -175 с.
Табель оборудования и оснастки ремонтных мастерских колхозов и совхозов. -М.: ГОСНИТИ 1991. -29 с.
Руководство по организации ремонта машин в мастерских хозяйств с табелем оборудования. -М.: ГОСНИТИ 1987. -96 с.
Конструирование узлов и деталей машин. Учебное пособие для вузов. 3-е изд. перераб. и доп. Дунаев И.Ф. -М.: Высшая школа. -1988. -357 с.
Охрана труда. Копарев Ф.М. -М.: Колос 1980. -438 с.
Охрана труда в сельском хозяйстве. Гришин Г.И. Справочник. -М.:Киев1980.-640 с.
Методические указания к экономическому обоснованию дипломных проектов по центральным ремонтным мастерским хозяйств для специальности 3113 “Механизация сельского хозяйства”. -Мн.: БАТУ -1991. -36 с.
СТП БАТУ 01.01-96. Указания по оформлению курсовых и дипломных проектов по специальности С 03.01.00 “Механизация сельского хозяйства”. -Мн.: БАТУ 1996 -145 с.
РЕФЕРАТ.doc
Графическая часть представлена на 9 листах формата А1.
Ключевые слова: эксплуатация модернизация комбайн нож режущий аппарат показатели.
Целью работы: является обоснование конструктивных параметров и режимов работы механизма привода режущего аппарата сегментного типа с возвратно-поступательным движением ножа при установке упругих элементов и увеличения за счет этого скорости движения аппарата резания жатки.
Для достижения цели поставлены следующие задачи:
Теоретическое обоснование уравновешивания силы инерции режущего
аппарата с помощью упругих элементов.
Обоснование параметров и режимов работы упругого элемента для
внутреннего уравновешивания механизма привода.
Разработка обоснование параметров и режимов работы механизма разгона
для снижения пускового момента режущего аппарата с упругими элементами.
Определение экономической эффективности применения
уравновешивающего элемента в режущих аппаратах жатвенных машин.
3 Консрукторская11 (9).doc
1 Описание режущего аппарата.
Режущий аппарат служит для срезания растений при прямом комбайнировании. Он состоит из пальцев и ножа с сегментами. Пальцы снабжены противорежущими пластинами. Ножи режущего аппарата совершаюет возвратно-поступательное движение. При движении комбайна в промежутки между неподвижными элементами режущего аппарата заходят стебли растений подвижные элементы прижимают их к острой кромке неподвижных режущих элементов и срезают.
Для качественного среза стеблей носки сегментов должны прилегать к пластинам (зазор не более 05 мм). Зазор между сегментом и задним краем пластины должен быть 05 1 мм а между прижимом 5 и сегментом 2 — не более 05 мм. Зазоры регулируют рихтовкой прижимов установкой прокладок и смещением пластин трения. Отрегулированный нож должен свободно перемещаться от усилия руки.
Для подъема полеглых стеблей на пальцы режущего аппарата закрытого типа устанавливают стеблеподъемники. Их закрепляют хомутами на каждом втором пальце при уборке изреженных и на каждом третьем-четвертом при уборке густых и длинносоломистых полеглых хлебов.
Делители предназначены для отделения срезаемых стеблей от хлебного массива и подвода крайних стеблей к ножу. При уборке короткостебельных хлебов делителями служат боковины жатки удлиненные съемными мысами.
Для уборки длинносоломистых полеглых и спутанных хлебов применяют прутковые делители или торпедные снабженные регулируемыми внешними и внутренними стеблеотводами.
Высоту среза регулируют переставляя копирующие башмаки относительно днища жатки (работа с копированием) или поднимая жатку гидроцилиндрами (без копирования). Полеглые и низкорослые хлеба срезают на минимальной высоте. При уборке прямостоячих хлебов высоту среза выбирают в зависимости от длины стеблей.
Для нормальной работы режущего аппарата жатки комбайна «Дон-1500Б» натягивают приводной ремень так чтобы прогиб ремня при натяжении с усилием 40 Н был 12 14 мм. Пальцевой режущий аппарат закрытого типа применяют для скашивания прямостоячих хлебов беспальцевой аппарат и пальцевой открытого типа —для скашивания сильно полеглых и засоренных подгоном хлебов.
Нож режущих аппаратов приводится в возвратно-поступательное движение механизмом качающейся шайбы (в комбайне «Дон-1500Б»). Механизм качающейся шайбы (МКШ) снабжен коленчатым ведущим валом на шейке которого на подшипниках смонтировано водило. Пальцами водило кинематически соединено с вилкой колебательного вала. На конце вала закреплен рычаг соединенный с головкой ножа звеном состоящим из двух накладок. Сферические выточки накладок охватывают головку рычага и ножа образуя шаровые шарниры. Они компенсируют взаимные отклонения рычага и ножа в горизонтальной и вертикальной плоскостях. При вращении вала водило совершает колебательные движения вокруг оси проходящей через ось вала. Колебательные движения водила пальцами передаются вилке вала и через рычаг звено ножу режущего аппарата.
Для определения реакций в опорах вала сначала необходимо построить схему его нагружения.
Чертим расчетную схему вала при помощи которой определяем реакции в опорах и изгибающие моменты на валу. Для этого рассмотрим вал в горизонтальной и вертикальной плоскости как балку лежащую на двух опорах.
Горизонтальная плоскость:
Строим эпюру МИН (Нмм)
Вертикальная плоскость:
Определяем изгибающий момент МИ от осевой силы FА
Строим эпюру МИV (Нмм)
Определяем ΣМИ (Нмм)
Строим эпюру ΣМИ (Нмм).
Рисунок 3.1 – Эпюры изгибающих моментов вала.
Наиболее опасным является сечение вала в месте посадки подшипника.
Определяем реакции в опорах:
Проверочный расчет вала на усталостную прочность при изгибе.
где: S и S коэффициенты запаса по изгибающим и крутящим напряжениям;
[ S ]– допускаемое значение коэффициента запаса равно 25 .
где -1 и -1 – пределы выносливости для материала вала при симметричном цикле изгиба; КD и КD эффективные коэффициенты концентрации напряжений; Kd – коэффициент влияния абсолютных размеров поперечного сечения; KV – коэффициент влияния поверхностного упрочнения; и – коэффициенты чувствительности к асимметрии цикла; а и а – амплитудные напряжения; m и m – средние напряжения цикла ( в нашем расчете m m и принимаем равными 0).
КD = К + КF – 1 =16+12 – 1 = 18 (7.4)
КD = К + КF – 1 =14+12 – 1 = 16 (7.6)
- Условие прочности выполняется
3 Расчёт подшипников качения.
Существует два вида расчетов подшипников качения:
)по статической грузоподъемности для предотвращения пластических деформаций тел и дорожек качения. Расчет выполняют при частоте вращения n 1 мин-1;
)по динамической грузоподъемности для предотвращения усталостного контактного выкрашивания тел и дорожек качения.
Расчет выполняется при n>1 мин-1.
Рисунок 3.2 - Схема установки подшипников.
По каталогу находим статическую грузоподъемность предварительно выбранного подшипника С0 = 500 кН.
Определяем коэффициент е по формуле:
Вычисляем осевые составляющие реакций опор от действия радиальных сил которые зависят от угла контакта .
S1=e×RA=0237× 99998 = 2369 Н (7.9)
S2 = e × RB = 0237 × 3952 = 936 Н.
Определяем расчетные осевые нагрузки Fа1 и Fа2 .
S1 > S2 и Fа > 0 Fа1 = S1 ; Fа2 = S1 + Fа (7.10)
Fа2 = 936 + 344 = 4376 Н.
Определяем соотношение и сравниваем его с е. При этом если соблюдается условие то Х = 1 Y = 0; если то Х и Y
находят по каталогу [1].
следовательно Х = 0.46 Y = 1.34.
Определяем эквивалентную динамическую нагрузку:
где: R – радиальная нагрузка действующая на подшипник
V – коэффициент вращения. При вращении внутреннего кольца V=1.
Kd – коэффициент безопасности. Kd = 12 .
KT – температурный коэффициент. KТ = 1 при температуре подшипника менее 1000С.
Вычисляем требуемую динамическую грузоподъемность подшипника
Сравниваем полученное значение С с табличным значением.
1 кН 627 кН Условие выполняется
4 Расчет шпонок на смятие и срез.
Зубчатые колеса шкивы звездочки и другие детали крепятся на валах с помощью шпоночных соединений. Длину шпонки принимают по длине ступицы с округлением в меньшую сторону до стандартной
где: - длина шпонки мм
Шпонки рассчитываются на смятие и на срез по формуле:
Рисунок 3.3 - Основные параметры шпонок.
где:- напряжение смятия Нмм
- напряжение на срез Нмм
- крутящий момент на валу Нмм
- диаметр вала вместе посадки шпонки мм
- рабочая длина шпонки мм
-параметры шпонки смотри выше мм
- допускаемое напряжение смятия 110-190 Нмм2
- допускаемое напряжение среза 75-100 Нмм2
Z – количество шпонок.
Параметры шпонки: b = 12 мм h = 8 мм l = 48 мм t1 = 5 мм t2 = 38 мм lр = l – b = 48 – 12 = 36 мм d = 42 мм .
- Условие прочности выполняется
1 Характеристика хозяйсво (21).doc
1 Общие сведения о хозяйстве.
Целью деятельности хозяйства является насыщение рынка качественной продукцией обеспечение эффективной работы предприятия и на этой основе получения постоянного прироста прибыли необходимого для удовлетворения социальных и экономических интересов членов трудового коллектива и государства. За хозяйством закреплено общая земельная площадь 5632 га.
В структуре сельскохозяйственных угодий пашня составляет 77% 68%-сенокосы 156% пастбища. Банитет почвы: пашня-36 баллов сельхозугодия-36 баллов. В растениеводстве образованы 3 производственных участка.
Недалеко от хозяйства проходит усовершенствованное шоссе Брест-Москва а ближайшая железнодорожная станция находится в г.Столбцы.
Таблица 1.1 - Производственные показатели хозяйства.
Валовое производство
Среднегодовое количество
Продолжение таблицы 1.1
Приходиться основных средств производства на 100 га с.-х. угодий тыс. руб
Приходится на одного среднегодового работника
на 100 га с.-х. угодий
Уровень рентабельности %
Вывод: Как видно из данных таблицы площадь сельхозугодий в 2007 году по сравнению с предыдущими годами выросла увеличилось среднегодовое количество работающих. На землях хозяйства возделываются различные сельскохозяйственные культуры. Земли – дерново-подзолистые торфяно-болотные и суглинистые.
1.2 Природно-климатические условия.
Умеренно континентальный климат республики с мягкой и влажной зимой и относительно прохладным солнечным летом можно характеризовать как благоприятный для возделывания большинства сельскохозяйственных культур средней полосы.
Одним из определяющих условий роста и развития растений является сумма положительных температур ( среднесуточная температура воздуха свыше 11 0С ) за период активной вегетации растений. Этот показатель в республике колеблется от 2000 до 2600 0С.
Почвенный покров Республики Беларусь весьма разнообразен но в основном распространены два типа почв – дерново-подзолистые и торфяно-болотные. Дерново-подзолистые почвы занимают около 70 % территории и характеризуются наличием перегнойного горизонта мощностью 20 – 25 см. Кроме того заболачиваемые почвы составляют 122 %. Торфяно-болотные почвы занимают около 25 % территории республики. Дерново-подзолистые суглинистые почвы слабо насыщены основаниями (40 – 70%) и нуждаются в известковании. Естественное плодородие этих почв невысокое они содержат в среднем около 2 % гумуса. Однако пищевой режим для растений на этих почвах более благоприятный чем на супесчаных и песчаных.
Под пашню используются в основном дерново-подзолистые суглинистые супесчаные и частично песчаные почвы. В составе пахотных земель суглинистые почвы занимают 42% песчаные – около 33 и супесчаные – 19%. Торфяно-болотные почвы составляют свыше 6 % и с каждым годом их количество увеличивается.
Только 10 % почв хорошо и средне обеспечено фосфором и 43 % - калием. Около 80 % пахотных земель нуждается в известковании. Однако рациональное применение минеральных органических удобрений в сочетании с известкованием позволяет получать на таких почвах высокие и устойчивые урожаи сельскохозяйственных культур.
Данные паспортизации полей:
-средневзвешенное удельное сопротивление почвы на вспашке : 47Нсм2
-обобщённый поправочный коэффициент к норме выработке на пахотных работах: 094
-обобщённый поправочный коэффициент к расходу топлива на пахотных
-обобщённый поправочный коэффициент к норме выработке на непахотных работах: 095
-обобщённый поправочный коэффициент к расходу топлива на непахотных работах: 103
-средняя длина гона м: 400 600
-средний угол наклона град: 12
В целом почвенно-климатические условия Столбцовского района можно охарактеризовать как благоприятные для возделывания сельскохозяйственных культур о чём свидетельствуют данные передовых хозяйств района где ежегодно выращивают высокие урожаи.
2 Краткая характеристика растениеводства.
Составляющие земельного фонда
Общая земельная площадь
Естественные сенокосы и пастбища
Вывод: Как видно из данной таблицы процентное содержание сх угодий в общей земельной площади в 2007 году по сравнению с предыдущими годами повысилась.
Структура посевных площадей и урожайность сельскохозяйственных культур приводятся в табл. 1.3 и 1.4.
Таблица 1.3 - Состав и структура посевных площадей.
Наименование культуры
Зерновые и зернобобовые
в т.ч. кукуруза на силос
Однолетние травы всего
Многолетние травы всего
Вывод: Как видно из данной таблицы засеваемая площадь по таким культурам как озимые зерновые кукуруза яровым зерновым зернобобовым однолетние и многолетние травы увеличилась за счет увеличения площадей пашни.
Таблица 1.4 - Урожайность сельскохозяйственных культур цга.
Продолжение таблицы 1.4
Вывод: Как видно из данной таблицы урожайность культур за последние три года варьируется в небольших пределах что в основном связано с различными погодными условиями различных лет. Особо следует лишь отметить увеличение урожайности кормовых корнеплодов и кукурузы.
Экономические показатели возделывания культур и структуру себестоимости продукции сводятся в таблицу.
Таблица 1.5 - Затраты труда и себестоимость продукции растениеводства.
Кормовые корнеплоды:
Продолжение таблицы 1.5
Многолетние травы: сено
Вывод: Как видно из данной таблицы трудозатраты на производство таких культур как зерновые многолетние травы снизились.
Структура себестоимости производства зерновых и зернобобовых культур представлена в таблицах 1.6.1 - 1.6.7
Таблица 1.6.1 - Структура себестоимости производства озимых зерновых.
Зарплата с начислениями
Удобрения и средства защиты
Амортизация основных средств
Прочие прямые затраты
Продолжение таблицы 1.6.1
Затраты по организации производства и управлению
Таблица 1.6.2 - Структура себестоимости производства яровых зерновых.
Удобрения и средства защиты растений
Таблица 1.6.3 - Структура себестоимости производства зернобобовых.
Продолжение таблицы 1.6.3
Таблица 1.6.4 - Структура себестоимости производства кормовых
Таблица 1.6.5 - Структура себестоимости производства многолетних трав.
Таблица 1.6.6 - Структура себестоимости производства однолетних трав.
Таблица 1.6.7 - Структура себестоимости производства кукурузы на силос.
Важное условие получения высоких и устойчивых урожаев - правильная система применения удобрений и комплекс мероприятий по сохранению и повышению плодородия почв. Влияние величины вносимых удобрений на урожайность выращиваемых культур представлено в таблице 1.7.
Таблица 1.7 – Внесение доз удобрений.
Перечень мероприятий
Внесение органических удобренийтга
Внесение минеральных удобрений
Продолжение таблицы 1.7
3 Анализ показателей состава и использования МТП.
3.1.Показатели технической оснащенности.
Для оценки эффективности и использования средств механизации и энергетики хозяйства применяются показатели технической оснащенности хозяйства которое приведены в таблице 2.1.
Таблица 2.1 - Техническая и энергетическая обеспеченность хозяйства.
Приходится на 100 га пашни:
физических тракторов шт.
условных эталонных тракторов
Энергообеспеченность кВт100 га пашни
Энерговооруженность труда кВтрабочего
3.2. Состав и показатели использования тракторного парка.
Таблица 2.2 - Показатели состава и использования тракторов.
Перечень показателей
Количество тракторов всего шт.
Продолжение таблицы 2.2
Количество условных тракторов всего шт.
на 100 га с.-х. угодий
Количество пашни на усл. эт. трактор га
Удельный вес тракторов %
Объём механизированных тракторных работ усл.эт.гага пашни
Колчество дней работы в году на один трактор:
Коэффициент сменности:
Коэффициент использования тракторов в году:
Расход топлива на усл.эт.га кг усл.эт.га
Как видно из табл. 2.2. по коэффициентам использования тракторный парк используется не эффективно. Это связано в первую очередь с уменьшением уровня механизированных технологических процессов. Он снизился из-за нехватки ГСМ и средств на приобретение запасных частей и ремонта техники.
3.3 Обеспеченность хозяйства сельскохозяйственными машинами и анализ использования комбайнов.
Таблица 2.3 - Наличие комбайнов и сельскохозяйственных машин.
Комбинированные агрегаты
Продолжение таблицы 2.3
Разбрасыватели органических удобрений
Машины для подготовки и внесения минеральных удобрений
3.4 Показатели состава и использования автомобилей в хозяйстве.
О состоянии дел в автотранспортном подразделении хозяйства свидетельствуют данные таблиц 2.4 и 2.5
Таблица 2.4 - Автомобильный парк
Автомобили общего назначения
Механизированные средства ТО и заправки машин
Сделав анализ табл. 2.4 можно сделать вывод что в хозяйстве транспортных средств в достаточном количестве но эта вся техника в основном старых моделей
Таблица 2.5 - Показатели использования автомобильного транспорта.
Среднегодовое число машин шт.
Средняя грузоподъемность одной машины тонн
Отработано на одну машину дней
Коэффициент использования автопарка
Общий пробег одной машины за год км.
Среднесуточный пробег одной машины км.
Среднесуточный пробег одной машины с грузом км.
3.5 Ремонто-обслуживающая база. Нефтехозяйство. Инженерно-техническая служба.
Ремонтная мастерская хозяйства рассчитана на обслуживание парка тракторов в количестве 75 штук. Ремонтная мастерская оснащена почти всем не обходимым оборудованием для ремонта сельскохозяйственной техники.
В настоящее время в хозяйстве принята планово-предупредительная система ТО тракторов автомобилей и сельскохозяйственной техники. Техническое обслуживание тракторов планируется по расходу топлива и выполняется на пункте технического обслуживания. Работы по техническому обслуживанию тракторов самими трактористами-машинистами а сложные работы мастерами-наладчиками.
Руководство работой ЦРМ осуществляется заведующим ремонтной мастерской. В его подчинении находятся слесари-ремонтники токари сварщики кузнец и младший обслуживающий персонал мастерской.
Вся техника в хозяйстве поставлена на длительное хранение. Хранится она на открытых площадках кроме зерноуборочных комбайнов комбинированным способом а снимаемое оборудование на складе.
Вся техника находящаяся на длительном хранении контролируется специальной службой машинного двора ежемесячно а обнаруженные при осмотрах неисправности сразу же устраняются.
В хозяйстве имеется нефтесклад где хранится топливо в цистернах а также смазочные материалы в бочках. Поставляет ГСМ в хозяйство районная нефтебаза. Отпуск ГСМ в хозяйстве осуществляется по лично – заборным карточкам которые заведены на каждый трактор и автомобиль.
Инженерно-техническую службу хозяйства возглавляет главный инженер. В его подчинении находятся руководители структурных подразделений и специалисты: заведующий ремонтной мастерской заведующий автогаражем бригадиры тракторных бригад главный зоотехник и заведующий складом ГСМ.
Проанализировав выше изложенный материал можно сделать вывод что хозяйство располагает всей необходимой техникой для выполнения всех сельскохозяйственных работ. В хозяйстве в основном вся старых марок и требуется замена ее на наиболее современные марки которые выполняют те же операции с меньшими затратами. Но для этого нужны материальные средства и помощь государства которая в последнее время осуществляется.
4 Интенсивная технология возделывания и уборки озимого тритикале в хозяйстве.
В Беларуси возделываются преимущественно зерновые сорта тритикале. Круг отраслей использующих зерно тритикале достаточно широк его применяют для кормления сельскохозяйственный животных прежде всего свиней и птицы. Установлено что замена до 40 % зерна в обычных комбикормах зерном тритикале увеличивает привесы свиней при откорме на 18-20 % при экономии корма 15-20 %.
Требования к температуре. В период всходов и кущения оптимальная температура 14-16°С минимальная - 5 °С максимальная-35 °С. Всходы появляются на 5-7 день после посева. Зимостойкость озимого тритикале выше чем озимой пшеницы но ниже чем озимой ржи. При изреживании посевов растения тритикале проявляют высокую способность к дополнительному кущению весной. Семена начинают прорастать при температуре 1-2 оС оптимальная температура прорастания 6—12 °С.
Требования к влаге. Наиболее требовательны к влаге в период от выхода в трубку до цветения происходит интенсивное накопление биомассы.
Требования к почве. Рекомендуются дерново-подзолистые легко- и среднесуглинистые и связносупесчаные почвы подстилаемые моренным суглинком а также осушенные торфяники низинного типа.
Наиболее высокую урожайность озимое тритикале формирует на связных почвах со слабокислой или нейтральной реакцией среды (pH 5.5-7.0) содержание гумуса не менее 16 % Р2О5 и К2О не менее 150 мгкг.
Хорошими предшественниками являются скороспелые диплидные сорта гречихи рапса зернобобовые смеси на зеленый корм однолетние и многолетние бобовые травы кукуруза. Очень неблагоприятным является посев этой культуры по стерневым предшественникам - ячменю и озимой пшенице после которых тритикале подвергается болезням поражающим основание стебля и корни растений.
При недостатке хороших предшественников тритикале можно размещать после овса При размещении озимого тритикале после овса и льна снижение урожайности этой культуры по сравнению с посевом после горохо-овсяной смеси составило только 2-3 %. Не рекомендуется возделывать озимое тритикале после многолетних злаковых трав.
Система обработки почвы разрабатывается в зависимости отпредшественника и засоренности полей. На дерново-подзолистых почвах с небольшим пахотным слоем хорошие результаты дает рыхление подпахотного слоя или его припашка. Глубина припашки зависит от мощности пахотного слоя и норм внесения органических удобрений.
Сразу после уборки стерневых культур проводят лущение на глубину 6-8 см за 2-3 недели до сева поле пашут на глубину пахотного горизонта плугами в агрегате с катком. В зависимости от уплотненности почвы можно пахать с предплужниками и одновременно бороновать или обрабатывать культиватором. Вслед за уборкой пропашных применяют безотвальную обработку почвы. В годы с засушливым летне-осенним периодом более эффективна поверхностная обработка почвы дисковыми и корпусными лущильниками .без отвала с одновременным боронованием и прикатыванием Исключение составляют лишь тяжелые по гранулометрическому уставу почвы а также поля засоренные корнеотпрысковыми сорняками. Перед посевом проводят обработку агрегатами РВК или АКШ.
На формирование 1 Ц зерна и соответствующего количества соломы по данным кафедры растениеводства ТСХА тритикале выносит 4-5 кг азота 13-16 - фосфора и 34-4 кг калия. Наибольшее потребление элементов питания - в фазу выхода в трубку и в период формирования и налива зерна. Дозы удобрения должны определяться плодородием почвы обеспеченностью растений влагой и уровнем планируемой урожайности. В качестве основного удобрения под тритикале вносят органические удобрения: 20-30 тга полуперепревшего навоза или 30-40 тга торфо-навозного компоста и минеральные удобрения
N 45-60 Р 60-65. К 45-60Азотные удобрения следует вносить весной в период начала активной вегетации растений когда сумма весенних положительных температур составит 100-200 оС. При рН менее 55 проводят известкование.
Подготовка семян к посеву.
Качество семян – одно из важнейших условий получения высокого урожая.
При необходимости посева свежеубранными семенами с пониженной влажностью но высокой жизнеспособностью следует перед посевом прогреть семена на солнце в течение 3-5 дней или в зерносушилке при температуре 45-48 оСв течение 2-3 ч.
Для борьбы с пыльной головней применяют термический способ: семена замачивают в воде при температуре 28-32 °С в течение 4 ч. затем их прогревают 8 мин при температуре 52 °С после этого семена охлаждают и просушивают. Хорошие результаты дает обработка семян препаратами витавакс 200 ФФ 34% в.с.к. - 2 лт семян. Эффективный прием подготовки семян к посеву - обработка их препаратами-регуляторами роста.
Для сева используют семена не ниже 2-3 репродукций. Один из решающих факторов благополучной перезимовки озимых — оптимальные сроки сева. В северной части республики - это последняя декада августа центральной - первая декада сентября южной -110 по 20 сентября.
При слишком раннем посеве растения обладают пониженной морозостойкостью и зимостойкостью. При поздних сроках сева тритикале как правило уходят в зиму слабыми. В производственной практике получил распространение обычный рядовой (с междурядьем 15 см) способ который позволяет более равномерно распределить семена по площади благодаря чему растения лучше развиваются меньше угнетают друг друга увеличивают продуктивную кустистость и мощность корневой системы полнее используют свет влагу питательные вещества и дают более высокий урожай. Используют сеялки СЗ-36 СЗУ-36 СЗЛ-36 СЗК-36 СПУ-6 типа Аккорд.
В Беларуси на мягких почвах глубина заделки семян 4-5 см на суглинистых – 2-3 см.
Норма высева на песчаных почвах составляет 5-6 на супесчаных – 4-5 на суглинистых – 4-4.5 млн. всхожих семян на 1 га.
Для борьбы с сорняками на посевах этой культуры сразу после уборки предшественника необходимо использовать почвенные гербициды. Наиболее эффективным препаратом в этом отношении является: раундап 36 % в.р. - 40-60 лга. При этом уничтожаются многолетние сорняки: пырей ползучий осот и бодяк полевой. Если посевы тритикале засорены однолетними двудольными сорняками то весной в фазу кущения их необходимо обрабатывать гербицидами агритокс в.к. — 10-15 лга базагран М - 20-40 лга.
Также при уходе за посевами применяют прикатывание подкормки снегозадержание весеннее боронование.
Зерно тритикале плотно заключено в колосковых чешуях при созревании не осыпается. Применяют однофазный способ уборки
Оптимальная фаза уборки посевов на семенные цели - при влажности зерна 15-20 % на товарные - до 26 %.
Очистка и сортировка зерна проводится на обычных зepноочистительных машинах но решета ставят с более крупными отверстиями.
ЗАКЛЮЧЕНИЕ.docx
Обоснована наиболее приемлемая конструкция упругих элементов для режущего аппарата жатки в виде цилиндрических винтовых пружин растяжения установка которых на боковинах жатки посредством гибкой связи (тросов) перекинутых через роликовые блоки позволяет повысить число двойных ходов ножа при уменьшении прежнего напряженного состояния деталей механизма привода. Обоснованы конструкция и основные параметры механизма разгона режущего аппарата снижающего пусковой момент что позволяет уменьшить размеры звеньев механизма привода.
На основе теоретических и экспериментальных исследований разработана и изготовлена конструкция режущего аппарата нового типа с упругими элементами и механизмом разгона который успешно прошел производственные испытания на уборке зерновых культур.
ОБЩИЕ ВЫВОДЫ И ПРЕДЛОЖЕНИЯ.docx
Дальнейшее повышение производительности режущего аппарата связано с увеличением числа двойных ходов ножа что приводит к повышению динамической нагруженности звеньев приводного механизма.
Уравновешивание режущего аппарата с возвратно-поступательным движением ножа возможно созданием искусственной колебательной системы постановкой упругого элемента определенной жесткости между ножом и пальцевым брусом что позволяет одновременно со снижением нагрузок на звенья и их сочленения увеличить скорость движения ножа уменьшить затраты мощности и повысить долговечность надежность работы механизма привода и производительность агрегата.
Для снижения пускового момента режущего аппарата обоснован и разработан механизм разгона ножа рабочими элементами которого являются предварительно сжатые упругие элементы. Закономерности изменения жесткости и минимальной величины предварительной деформации определяется уравнениями (11) и (12).
Анализ результатов исследований усилий в приводе показываетчто напряженность работы механизма качающейся шайбы снижается: наибольший эффект наблюдается при работе в зоне резонанса здесь максимальное усилие колебателя снижается в 976 раза; одновременно падает величина среднего крутящего момента - на резонансной частоте крутящий момент снижается в 138 раза; почти на треть уменьшается амплитуда крутящего момента. Коэффициент вариации крутящего момента уменьшается с 070 до 039 коэффициент стабилизации равен 179. Снижение мощности на привод режущего аппарата составляет 17%.
Вибрация жатки с ведением в механизм привода упругих элементов уменьшается на 55%.
Записка.doc
Для определения реакций в опорах вначале необходимо построить схему нагружения валов редуктора.(см. приложение 1).
Чертим расчетную схему вала (см. приложение 2) при помощи которой определяем реакции в опорах и изгибающие моменты на валу. Для этого рассмотрим вал в горизонтальной и вертикальной плоскости как балку лежащую на двух опорах.
Горизонтальная плоскость:
Строим эпюру МИН (Нмм)
Вертикальная плоскость:
Определяем изгибающий момент МИ от осевой силы FА
Строим эпюру МИV (Нмм)
Определяем ΣМИ (Нмм)
Строим эпюру ΣМИ (Нмм)
Наиболее опасным является сечение вала в месте посадки подшипника.
Определяем реакции в опорах:
Проверочный расчет вала на усталостную прочность при изгибе.
где : S и S коэффициенты запаса по изгибным и крутящим напряжениям ;
S – допускаемое значение коэффициента запаса = 1.1 – 2.5 .
где -1 и -1 – пределы выносливости для материала вала при симметричном цикле изгиба ([1] таблица 11.5) ; КD и КD эффективные коэффициенты концентрации напряжений; Kd – коэффициент влияния абсолютных размеров поперечного сечения ([1] таблица 11.6); KV – коэффициент влияния поверхностного упрочнения; и – коэффициенты чувствительности к асимметрии цикла ([1]таблица 11.5); а и а – амплитудные напряжения; m и m – средние напряжения цикла ( в нашем расчете m m и принимаем равными 0).
КD = К + КF – 1 =1.6+1.2 – 1 = 1.8 (7.4)
КD = К + КF – 1 =14+12 – 1 = 16 (7.6)
Условие прочности выполняется
Проверочный расчет подшипников.
Существует два вида расчетов подшипников качения:
)по статической грузоподъемности для предотвращения пластических деформаций тел и дорожек качения. Расчет выполняют при частоте вращения n 1 мин-1;
)по динамической грузоподъемности для предотвращения усталостного контактного выкрашивания тел и дорожек качения. Расчет выполняется при n>1 мин-1.
рис.7.1 Схема установки подшипников.
По каталогу [1] находим статическую грузоподъемность предварительно выбранного подшипника С0 = 120 кН.
Определяем коэффициент е по формуле:
Вычисляем осевые составляющие реакций опор от действия радиальных сил которые зависят от угла контакта .
S1 = e × RA = 0237 × 1950 = 462 Н (7.9)
S2 = e × RB = 0237 × 1531 = 363 Н
Определяем расчетные осевые нагрузки Fа1 и Fа2 .
S1 > S2 и Fа > 0 Fа1 = S1 ; Fа2 = S1 + Fа (7.10)
Fа2 = 363 + 344 = 707 Н
Определяем соотношение и сравниваем его с е. При этом если соблюдается условие то Х = 1 Y = 0; если то Х и Y находят по каталогу [1].
следовательно Х = 0.46 Y = 1.34.
Определяем эквивалентную динамическую нагрузку:
где: R – радиальная нагрузка действующая на подшипник
V – коэффициент вращения. При вращении внутреннего кольца V=1.
Kd – коэффициент безопасности. Kd = 1.2 (стр.141 [1])
KT – температурный коэффициент. KТ = 1 при температуре подшипника менее 1000С.
Вычисляем требуемую динамическую грузоподъемность подшипника
g = 6.36 ( см 1 табл 11.2)
Сравниваем полученное значение С с табличным значением.
кН 22 кН Условие выполняется
Чертим расчетную схему вала (см. приложение 3) при помощи которой определяем реакции в опорах и изгибающие моменты на валу. Для этого рассмотрим вал в горизонтальной и вертикальной плоскости как балку лежащую на двух опорах.
Вертикальная плоскость
КD = К + КF – 1 =1.6+1.2 – 1 = 1.8
КD = К + КF – 1 =14+12 – 1 = 16
Условие прочности выполняется
По каталогу [1] находим статическую грузоподъемность предварительно выбранного подшипника С0 = 23.2 кН.
S1 = e × RA = 0353 × 5706 = 2014 Н
S2 = e × RB = 0353 × 8592 = 3033 Н
S1 S2 и Fа S2 – S1 Fа1 = S2 – Fа ; Fа2 = S2
Fа1 = 3033 – 628 = 2405 Н
следовательно Х = 046 Y = 134.
g = 391 ( см 1 табл 11.2)
5 кН 389 кН Условие выполняется
Проверочный расчет шпонок
Зубчатые колеса шкивы звездочки и другие детали крепятся на валах с помощью шпоночных соединений. Сечение шпонки выбирают в зависимости от диаметра вала (см.1табл.7.7). Длину шпонки принимают по длине ступицы с округлением в меньшую сторону до стандартной (см.примечание к табл.7.7)
где: - длина шпонки мм
Шпонки рассчитываются на смятие по формуле:(см.1с.94)
рис.7.2 Основные параметры шпонок
где:- напряжение смятия Нмм
- крутящий момент на валу Нмм
- диаметр вала вместе посадки шпонки мм
- рабочая длина шпонки мм
-параметры шпонки смотри выше мм
- допускаемое напряжение смятия 110-190 Нмм2
Z – количество шпонок.
Шпонка на первом валу (меньшая):
параметры шпонки: b = 6 мм h = 6 мм l = 28 мм t1 = 35 мм t2 = 28 мм lр = l – b = 28 – 6 = 22 мм d = 20 мм .
Поскольку меньшая шпонка удовлетворяет условиям прочности то большую не проверяем.
Шпонка на втором валу (меньшая):
параметры шпонки: b = 8 мм h = 7 мм l = 56 мм t1 = 40 мм t2 = 33 мм lр = l – b = 56 – 8 = 48 мм d = 30 мм .
5 Экономика (11).doc
1 Расчет производительности зерноуборочного комбайна
Производительность комбайна на механизированных полевых работах за 1 час сменного времени (Wч) рассчитываем по формуле (5.1):
где Вр – рабочая ширина захвата м.;
Vр – средняя рабочая скорость движения агрегата кмч.;
– коэффициент использования смены исчисляется как отношение времени чистой работы к времени смены.
Wч1=0164507 = 189 гач
Перспективный вариант:
Wч2 =0164508 = 216 гач.
Годовой объем работы (Wг) исчисляем по формуле (5.2):
где Тг – годовая загрузка комбайна часов сменного времени.
Wг2=216200 = 432 га.
2 Расчет трудозатрат и роста производительности труда.
Прямые затраты труда (tn) в расчете на единицу работы агрегата определяем по формуле (5.3):
где Л – количество работников обслуживающих агрегат чел.
Экономию затрат труда (ч) рассчитываем по формуле (5.4):
Эт =( tn1- tn2)Wг2 (5.4)
Эт =(105-092)432= 5616 ч.
Рост производительности труда исчисляем по формуле (5.5):
3 Удельная материалоемкость процесса.
Материалоемкость (металлоемкость) производственного процесса представляет собой суммарное отношение массы сельскохозяйственных машин к их годовой выработке.
Удельная материалоемкость (Ме) в расчете на единицу механизированной работы определяют по формуле:
где nj – количество j-х машин в агрегате шт; Мj – масса j-й машины участвующей в производственном процессе кг; Тгj – годовая загрузка j-й машины.
Снижение удельной материалоемкости производственного процесса определяем по формуле (5.7):
4 Удельная энергоемкость работы.
Величину энергоемкости работы определяем как отношение эффективной мощности двигателя (Ne) к часовой производительности агрегата по формуле (5.8):
где α-коэффициент использования мощности двигателя на данной работе.
Снижение удельной энергоемкости процесса исчисляем по формуле (5.9)
Расход топлива на единицу работы (G) рассчитываем по формуле (5.10):
где Ne – номинальная мощность двигателя кВт.;
g – удельный расход топлива на единицу мощности двигателя кг.
Снижение расхода топлива (IG) рассчитываем по формуле (5.11):
Экономию основного топлива на годовой объем работы проектируемой машины рассчитываем по формуле (5.12):
Эт=( G1– G2 )Wг2 (5.12)
Эт=(218 – 199)432 = 8208 кг.
6 Капиталоёмкость процесса.
Капитальные вложения на единицу работы (Куд) определяем по формуле (5.13):
где Бсj– балансовая или восстановительная стоимость j-ой машины участвующей в процессе работы руб.
Куд1=3005 тыс.рубга
Куд2=2629 тыс.рубга.
7 Расчет эксплуатационных затрат и их экономии.
Прямые затраты на единицу работы (Uэ) рассчитываем по формуле (5.14):
Uэ= Uз+ Uсоц + Uгсм+ Uр+ Uа+ Uпр (5.14)
где Uз – затраты на оплату труда обслуживающего персонала руб.;
Uсоц- отчисления на социальные нужды тыс.руб.;
Uгсм - стоимость горючего и смазочных материалов тыс.руб.;
Uр- затраты на ТО и ремонт сельхозтехники тыс.руб.;
Uа – амортизационные отчисления на реновацию сельхозтехники тыс.руб.;
Uпр –прочие затраты тыс.руб.
Затраты на оплату труда обслуживающего персонала на единицу работы определяем по формуле (5.15):
Uз=ΣnjСtjКув (5.15)
где nj –количество обслуживающего персонала j-го разряда чел.;
Сtj-тарифная часовая ставка оплаты труда обслуживающего персонала j-го разряда тыс.руб.;
Кув-коэффициент увеличения тарифного заработка.
Uз1= 115442= 1634 тыс.рубга
Uз2=115442=1430 тыс.рубга.
Расчет отчислений на социальные нужды по формуле:
Базовый вариант: Uсоц1=031634= 0492 тыс.рубга
Перспективный вариант: Uсоц2=031430= 0429 тыс.рубга.
Затраты на ГСМ рассчитываем по формуле (5.17):
Uгсм =GЦком (5.17) где Цком-комплексная цена приобретения 1кг основного топливатыс.руб..
Цком =(Цт11)086=(202011)086=2583 тыс.руб.
Базовый вариант: Uгсм1 =2182583=56325 тыс. рубга
Перспективный вариант: Uгсм2 =1992583=51416 тыс.рубга.
Затраты на ТО и ремонт сельхозтехники рассчитываем по формуле (5.18.):
где rк –норматив затрат на ремонт и ТО комбайна %;
rм- норматив затрат на ремонт и ТО сельхозмашины %.
Uр1== 63857 тыс.рубга
Uр2== 55875 тыс.рубга.
Амортизационные отчисления на реновацию сельхозтехники в расчете на единицу работы определяем по формуле (5.19):
где ак-норма ежегодных амортизационных отчислений от балансовой стоимости трактора %;
ам-норма ежегодных амортизационных отчислений от балансовой стоимости сельхозмашины % .
Uа1== 39629 тыс.рубга
Uа2== 34125 тыс.рубга.
В прочие затраты Uпр включаем издержки на страхование и хранение сельскохозяйственной техники и рассчитываем по формуле (5.20):
где Нск – норматив затрат на страхование и хранение трактора;
Нсхм – норматив затрат на страхование и хранение сх машины.
Uпр1== 6532 тыс.рубга
Uпр2== 5625 тыс.рубга.
Общая сумма эксплуатационных затрат составит:
Uэ1=1634+0492+56325+63857+39629+6532=168470 тыс.рубга
Uэ2=1430+0429+51416+55875+34125+5625=148900 тыс.рубга.
Снижение эксплуатационных издержек рассчитываем по
формуле (5.21): Iиз=100 (5.21)
Годовую экономию эксплуатационных затрат рассчитываем по формуле (5.22):
Эиг=(Uэ1- Uэ2)Wг2 (5.22)
Эиг=(168470 -148900)432=8454512 тыс.руб.
Таблица 5.1 - Состав и структура эксплуатационных издержек
Отчисления на социальные нужды
Стоимость горючего и смазочных материалов
Техническое обслуживание и ремонт с.-х. техники
а. Всего материальных затрат (3+4)
Амортизационные отчисления
8 Расчет эффективности капитальных вложений (инвестиций)
Годовой доход Дг рассчитываем по формуле (5.23):
Дг=Эиг+(Uа2Wг2-Uа1Wг1) (5.23)
Дг=8454512 +[34125 432–39629378]=8216738 тыс.руб.
Чистый дисконтированный доход (ЧДД) рассчитываем по формуле (5.24):
где αт-коэффициент приведения во времени к началу расчетного
периода рассчитываем по формуле (5.25):
где Е - банковская ставка за долгосрочный кредит(Е=015);
Т-средний амортизационный срок службы сельскохозяйственной техники лет. рассчитываем по формуле (5.26):
где К-дополнительные капитальные вложения руб. рассчитываем по формуле (5.27):
где К1 и К2 – капитальные вложения рассчитываем по формуле:
К=8454512-7443194=1011317 тыс. руб .
ЧДД=8216738449-1011317=35881839 тыс.руб.
Коэффициент возврата капитальных вложений рассчитываем по формуле (5.28):
Срок возврата капитальных вложений рассчитываем по формуле (5.29):
Таблица 5.2 - Показатели сравнительной экономической эффективности средств механизации .
Технико-экономические
1. Производительность гач
2. Годовой объем работы га
3. Удельная материалоемкость
4. Удельная энергоемкость
5. Расход топлива кгга
6. Экономия топлива на годовой объем работы кг (ц т)
Показатели затрат труда
1. Прямые затраты труда чга
2. Рост производительности труда
Показатели экономической эффективности
1. Эксплуатационные затраты
2. Годовая экономия эксплуатационных затрат тыс.руб.
3. Капиталоемкость тыс.руб.га
4. Годовой доход тыс.руб.
6. Коэффициент возврата инвестиций
7. Срок возврата инвестиций лет
В течении одного года
Анализ экономического обоснования показал что годовая эканомия эксплуатационных затрат составила 8454512 тыс.руб. в проектируемом
варианте. Годовой доход составил 8216738 тыс.руб. а чистый дисконтированный доход составил 35881839 тыс.руб.
Рост производительности труда увеличился на 141 %. Срок окупаемости капитальных вложений 012 года.
Технико-экономические расчеты показывают эффективность предлагаемого решения.
- - - Титульник.doc
Учреждение образования
БЕЛОРУССКИЙ ГОСУДАРСТВЕННЫЙ АГРАРНЫЙ
ТЕХНИЧЕСКИЙ УНИВЕРСИТЕТ
доцент канд. тех. наук
РАСЧЕТНО-ПОЯСНИТЕЛЬНАЯ ЗАПИСКА
к дипломному проекту
на тему: "Повышение эффективности уборки зерновых путём модернизации механизма привода режущего аппарата зерноуборочного комбайна
Малявко Виталий Борисович
Консультант: доцент канд. тех. наук
Руководитель проекта:
Консультант по технологической части:
Консультант по безопасности жизнедеятельности:
ст. преподаватель БЖД
Консультант по экономической части:
доцент канд. экон. наук
4 БЖД (15).doc
1 Анализ состояния охраны труда на “Cтолбцовском райагросервисе” и мераприятия по его улучшению.
В разработке и проведении мероприятий по охране труда в хозяйстве участвуют главные специалисты специалисты среднего звена и инженер по охране труда. Решением правления назначены лица ответственные за состояние охраны труда на каждом отдельно взятом участке. Инженером по охране труда с учетом предложений специалистов по отраслям составляется план по улучшению условий охраны труда и санитарно-оздоровительных мероприятий годовой план организационно-технических мероприятий по технике безопасности пожарной безопасности и производственной санитарии.
Каждый месяц инженер по охране труда контролирует состояние безопасности на каждом производственном участке проводит консультации. В последнее время повысился уровень проведения инструктажей что привело к существенному снижению травматизма (табл.6.1).
Распределение несчастных случаев по отраслям производства приведено в табл.6.2. Основным показателем производственного травматизма являются коэффициент частоты травматизма (Кч) коэффициент тяжести (Кт).
Показатель частоты травматизма Кч представляет собой отношение количества пострадавших n1 к среднесписочному числу рабочих и служащих np за учетный период отнесенное к тысяче работающих
Коэффициент частоты травматизма на 2007 год
Показатель тяжести травматизма Кт характеризует среднюю длительность временной нетрудоспособности пострадавших
Показатель тяжести травматизма Кт на 2005 год
Таблица 6.1 - Состояние травматизма в хозяйстве
Среднесписочное число работников
Количество несчастных случаев
Количество дней нетрудоспособности
Коэффициент частоты травматизма
Коэффициент тяжести травматизма
Таблица 6.2 - Распределение несчастных случаев на производстве.
Ремонтные мастерские
Основными причинами травматизма являются нарушение технологии работ не выполнение правил техники безопасности неосторожность. Как видно из табл.6.1. коэффициенты к 2007 году снизились. Это явилось с одной стороны результатом увеличения средств на улучшение условий труда и техники безопасности а с другой стороны улучшением работы специалистов по охране труда. По сравнению с 2005 годом затраты на охрану труда значительно возросли. Проектом разработаны предложения по улучшению охраны труда в хозяйстве и на проектируемой ферме которые выглядят следующим образом:
Инженеру по охране труда систематически проверять качество проведения инструктажей по охране труда.
Организовать прием зачетов по технике безопасности и аттестацию персонала а также ввести день охраны труда.
Обеспечить санитарно-бытовые помещения необходимой мебелью и провести ремонт этих помещений.
2 Анализ опастных и вредных производственных факторов при эксплуатации зерноуборочного комбайна ДОН 1500Б.
2.1 Общие требования безопасности.
При наружной мойке комбайнов горячим раствором под давлением с помощью моечной машины следят за тем чтобы никто из обслуживающего персонала не находился в камере во избежание! ожогов и поражения дыхательных путей.
К самостоятельной работе на комбайнах допускаются лица не моложе 18 лет прошедшие специальную подготовку имеющие удостоверение на право управления той или иной машиной выданное квалификационной комиссией а также прошедшие вводный инструктаж по технике безопасности на рабочем месте. Инструктаж по технике безопасности на рабочем месте необходимо проводить при каждом изменении условий работы но не реже двух раз в год.
Прежде чем приступить к работе машинист комбайна обязан щательно осмотреть машину и убедиться в ее исправности.
Запрещается выезжать на работу при наличии каких-либо неисправностей машины: у комбайна при неисправности двигателя рулевого управления и ходовой части муфты сцепления тормозного устройства муфты управления; топливных баков топливопроводов и карбюраторов (подтекание топлива) прицепного устройства а также при отсутствии крыльев (щитков) у колесных тракторов.
Каждый комбайн должен быть закреплен приказом (распоряжением) за определенным машинистом.
Запрещается приступать к работе на незакрепленной машине или на машине закрепленной за другим машинистом.
При использовании машин должна быть обеспечена обзорность рабочей зоны с рабочего места машиниста. В том случае когда машинист управляющий машиной не имеет достаточного обзора или не видит рабочего подающего ему сигналы между машинистом и рабочим сигнальщиком необходимо устанавливать двухстороннюю радиосвязь.
Машинист комбайна должен быть обеспечен спецодеждой предусмотренной действующими нормами:
полукомбинезон хлопчатобумажный рукавицы комбинированные.
Для безопасной работы в темное время суток машины должны быть оснащены исправными светильниками (фарами).
Запрещается во время работы смазывать и крепить детали заправлять регулировать и очищать от грязи тягач и прицепные машины.
Открывать крышку радиатора неохлажденного двигателя следует обязательно в рукавицах или используя концы и ветошь.
При открывании крышки радиатора лицо необходимо держать подальше от заливной горловины радиатора и находиться с наветренной стороны. Необходимо также соблюдать осторожность при сливе горячей воды из радиатора.
Запрещается во время работы двигателя регулировать натяжение ремня вентилятора и производить какие-либо ремонтные работы.
Перед заправкой расположите комбайн на очищенной от стерни сухой травы и опаханной площадке или пахоте заглушите двигатель.
В целях предотвращения загорания комбайна своевременно очищайте валы рабочих органов (битеров барабанов соломонабивателя кривошипа режущего аппарата шнека мотовила)от намоток растительной массы.
Не допускайте перегрева подшипников и деревянных полуподшипников своевременно проводите их смазку согласно таблице смазки.
Не разводите костры и не сжигайте поживные остатки ближе 200 м от убираемых массивов и вблизи стоянок комбайнов.
Удаляйте пыль солому с двигателя и электропроводки не реже 2-х раз в смену через 3 дня очищайте выпускные трубы и искрогасители от нагара.
Сварочные работы на убираемом массиве разрешается проводить только в исключительных случаях. при этом необходимо очистить участок от стерни.
Промасленную ветошь паклю и др. обтирочный материал собирайте в металлический ящик с крышкой.
3 Мероприятия по созданию здоровых и безопасных условий труда при эксплуатации зерноуборочного комбайна ДОН 1500Б.
Перед началом работы машинист комбайна должен ознакомиться с зоной производства работ: рельефом местности выяснить и установить местонахождение подаваемых коммуникаций линий электропередач.
Перед запуском двигателя необходимо:
а) убедиться в отсутствии посторонних предметов на вращающихся деталях двигателя коробке
б) убедиться что рычаг переключения скоростей находится в нейтральном положений;
в) вытереть насухо все наружные части машины на которые попали бензин или масло во избежание возможного воспламенения.
При запуске двигателя трактора все пальцы руки должны быть расположены с одной стороны пусковой рукоятки. Запрещается брать пусковую рукоятку в обхват.
Запрещается заводить перегретый двигатель во избежание обратного удара от преждевременной вспышки (вследствие самовоспламенения рабочей смеси).
Запрещается пользоваться открытым огнем для подогрева двигателя при его заводке а также эксплуатировать бульдозер при наличии течи в топливной или в масляной системе. Подогрев масла разрешается производить только в специальных маслогрейках.
При подсоединении наклонной камеры к молотилке или жатки к наклонной камере –не находитесь на узлах и между ними.
Перед проведением работ под жаткой установите ее на специальные металлические подставки перекройте кран гидроцилиндров .
Перед началом движения к месту работы установите выступающие за габариды машины узлы в транспортное положение . Подайте звуковой сгнал убедитесь что на пути движения комбайна нет людей и только после этого начинайте движение.
На специализированных предприятиях по ремонту зерновых комбайнов наибольшее количество несчастных случаев приходится на монтажно-демонтажные работы.
Объясняется это тем что на сборке разборке комбайнов и Других рабочих постах рабочие не всегда применяют рекомендуемые технологией приспособления подставки и лестницы а пользуются молотком кувалдой зубилом бородком всевозможными нестандартными оправками и выколотками которые зачастую бывают неисправными.
Правильная с точки зрения техники безопасности организация работ способствует снижению травматизма.
Между ремонтируемыми комбайнами (молотилками или жатками) их боковыми сторонами и торцами необходимо придерживаться расстояния не менее 12 м между комбайном и стеной или ремонтно-технологическим оборудованием- не менее 12 м а между комбайном и колонной здания- не менее 07 м. Расстояние между комбайном и наружными воротами расположенными против рабочих мест предусматривается не менее 2 м между движущимся комбайном (молотилкой жаткой) при въезде или выезде с рабочего места и комбайнами стоящими на соседних рабочих местах элементами зданий или стационарным оборудованием - не менее 07 и между комбайнами при их маневрировании в проезде и границами проезда с каждой стороны - не менее 1м.
Располагать рабочие места в помещении для осмотра разборки и сборки комбайна следует так чтобы полностью устранять возможность случайного наезда на работающих.
Комбайны в мастерскую доставляют трактором и лебёдкой. Перед мойкой из систем комбайна и двигателя сливают воду масло и топливо в специальные ёмкости. Нельзя разливать масло и топливо на полу так как это повышает опасность возникновения пожара и травмирования рабочих. При наружной мойке комбайнов горячим раствором под давлением с помощью моечной машины следя за тем чтобы никто из обслуживающего персонала не находился в камере во избежание ожогов и поражения дыхательных путей.
3.1 Требования безопасности машиниста комбайна во время работы.
Во время работы машинист комбайна обязан:
перевести машину из транспортного положения в рабочее положение
нахождение посторонних людей на комбайне не допускается
перед началом передвижения а также перед поворотом убедиться в отсутствии на пути препятствий или посторонних предметов после чего дать предупредительный сигнал;
Во время работы запрещается:
передавать управление другому лицу или перевозить в кабине бульдозера людей кроме лиц которые проходят практику;
сидеть и стоять на раме и других частях машины;
ставлять машину с работающим двигателем;
При движении с места повороте и остановке машины тракторист обязан дать предупреждающие сигналы рабочим находящимся на прицепных машинах.
Рабочая зона машины в темное время суток должна быть освещена. Норма освещенности в соответствии с правилами по проектированию электрического освещения строительных площадок..
Удалять забившуюся растительность только при выключенном двигателе при помощи спец. крюков в рукавицах .
Устранять зависание зерна в буксире с помощью деревянной лопаты.
При прокручивании молотильного барабана с помощью рычага необходимо следить чтобы руки помошника не попали в зазор между барабаном и декой.
Во время работы комбайна не подправляйте нависшие намотки растительной массы не удаляйте их руками не открывайте смотровые люки
При срабатывании сигнализации необходимо остановить машину выключить сигнализацию выяснить причину срабатывания и устраните ее.Перед начелом движения необходимо включить сигнализацию в рабочее положение.
При использовании машин в режимах установленных эксплуатационной документацией уровни шума вибрации запыленности загазованности не должны превышать значений установленных ГОСТом 12.1003-83. ГОСТ 12.1012-78.
Техническое обслуживание и текущий ремонт машины следует осуществлять в оборудованных помещениях или площадках. Для производства технического обслуживания и ремонта в условиях эксплуатации машина должна быть выведена из рабочей зоны.
Рабочие места при техническом обслуживании и текущем ремонте машин должны быть оборудованы комплектом работоспособных ручных машин (инструментов) приспособлений инвентаря грузоподъемными машинами и средствами пожаротушения.
При движении под уклон обязательно включать первую скорость. При переключении скоростей следует обязательно затормозить комбайн . При движении на подъем переключать скорости запрещается.
Запрещается передвижение комбайна поперек крутых склонов угол наклона которых превышает 30°.
Прежде чем сойти с комбайна необходимо поставить рычаг переключения скоростей в нейтральное положение и включить тормоз.
При встречном разъезде комбайнов необходимо соблюдать интервал между машинами не менее 2 м.
Не допускается работа комбайнов без ограждения движущихся деталей (приводного ремня шарнирного соединения приводного вала вала отбора мощности и др.).
В темное время суток место работы должно быть освещено.
При отсутствии кабины машинист должен иметь защитные очки предохраняющие глаза от пыли в жаркое время года необходимо устанавливать зонт для защиты от действия солнечных лучей.
Крутые повороты машины разрешаются только на первой скорости; выполнять команду «стоп" следует немедленно кем бы она ни подавалась.
Запрещается работать на машинах без действующего сигнального устройства.
При работе машин с гидравлической системой управления необходимо:
а) следить за исправностью предохранительного клапана служащего для перепуска части масла из распределителя в бак;
б) тщательно затягивать соединения гибких рукавов во избежание пропускания масла во время работы; ) в случае разрыва гибких шлангов выключить насос и остановить трактор.
Запрещается регулировать клапан "на глаз" так как чрезмерная затяжка его может привести к аварии
При движении комбайнов по полевым дорогам и при разьезде держитесь правой стороны и выдерживайте боковой интервал не менее 2м от встречных машин.
При движении техники через населенные пункты и по дорогам общего назначения выключите задние фары.
При движении уборочных машин по дорогам общего назначения в светлое время суток на узлы выступающие габариты машин установите предупредительные красные флажки а в темное время суток –красные сигнальные лампочки включите мигалку.
4 Инженерные мероприятия по обеспечению взрыво- и пожаробезопасности объекта проектирования.
На территории и внутри помещений имеются сгораемые материалы в виде мусора грубых и сухих кормов. Поэтому по степени пожарной опасности помещения фермы можно отнести к категории Д. Возможными причинами пожара могут быть следующие:
—неисправность глушителей-искрогасителей тракторов которые
используются для подвозки кормов и других материалов;
—подтекание топлива в двигателе внутреннего сгорания и воспламенение от нагретых частей или от искр электропроводки;
—неисправность электропроводки вызванные плохими контактами коротким замыканием;
—использование ''жучков" вместо плавких вставок или неправильный выбор плавких вставок предохранителей*;
—перехлестывание проводов электропроводки приводящее к искрению;
—неисправность отопительных приборов;
—захламление помещений сгораемыми материалами и нарушение правил использования открытого огня;
—курение в не отведенных местах;
—возгорание материалов при отогревании замерзших труб а также при выполнении ремонтных и других работ с использованием электрической и газовой сварки;
—трение деталей и узлов из-за отсутствия смазки;
—разряды молний в здания или технологические конструкции;
—самовозгорание сырых материалов кормов.
Поэтому при выполнении работ необходимо учитывать отмеченные выше и другие причины пожара. Главное - это создавать условия препятствующие возникновению пожара.
Возникший пожар должен быть погашен. Персонал должен знать расположение средств тушения пожара и уметь пользоваться ими. На территории мастерской необходимо оборудовать два щита с набором противопожарного инвентаря: багров лопат ведер огнетушителей. Количество огнетушителей выбирается из расчета один на 100 м" площади.
Следует учесть что пенные огнетушители нельзя хранить при низкой температуре. Для тушения пожаров могут быть использованы молоковозы и дождевальные установки. Помещения 111 1У У степени огнестойкости должны быть обустроены стержневыми или тросовыми молниеотводами. Во время грозы нельзя находиться вблизи заземляющих устройств из-за опасности поражения шаговым напряжением.
При загорании комбайна необходимо:
Выключить двигатель покинуть машину принять меры к тушению источника пожара .
Если невозможен выход из кабины через дверь –разбейте переднее стекло ногой или металлическим предметом.
Во время грозы все виды работ прекратить выйти из кабины.Не следует укрываться от грозы в скирдах стогах под одиночными деревьями под др. предметами возвышающимися над окружающейся местностью.
5 Мероприятия по обеспечению безопасности в черезвычайных и экологически неблагоприятных ситуациях.
Обеспечение безопасности жизнедеятельности в чрезвычайных ситуациях представляет собой комплекс организационных инженерно-технических мероприятий и средств направленных на сохранение жизни и здоровья населения во всех сферах деятельности.
Под устойчивостью работы объектов народного хозяйства понимают способность противостоять разрушительному воздействию поражающих факторов ЧС производить продукцию в запланированном объеме и номенклатуре обеспечивать безопасность рабочих и служащих а также приспособленность к восстановлению своего производства в случае повреждения.
Из комплекса мероприятий по повышению устойчивости работы объекта в ЧС наибольшее значение имеют мероприятия направленные на обеспечение жизнедеятельности в ЧС – защита рабочих и служащих а также исключение поражения от вторичных факторов.
Защита рабочих и служащих включает в себя:
-заблаговременное строительство убежищ на предприятиях в технологиях которых используются взрывоопасные токсичные и радиоактивные вещества;
-разработку режимов работы рабочих и служащих в условиях заражения вредными веществами;
-обучение персонала объекта выполнению работ по ликвидации очагов заражения;
-поддержание в постоянной готовности системы оповещения рабочих и служащих объекта и проживающего в близи населения об опасности исходящей от объекта.
Исключение поражения от вторичных факторов при авариях может быть достигнуто дополнительными мероприятиями включающими в себя:
-сокращение запасов сильнодействующих ядовитых взрыво- и пожароопасных веществ до минимума и хранение их в защищенных хранилищах;
-применение приспособлений исключающих разлив токсичных горючих и агрессивных жидкостей;
-размещение складов древесины ядохимикатов легковоспламеняющихся и горючих жидкостей с учетом направления господствующих ветров устройство противопожарных разрывов и пожарных проездов строительство пожарных водоемов и емкостей а также создание запасов средств пожаротушения;
-заглубление в грунт технологических коммуникаций лимит электроснабжения и других систем.
Основными способами защиты населения являются:
-укрытие в защитных сооружениях;
-эвакуация населения;
-использование средств индивидуальной защиты а также средств медицинской профилактики.
Укрытие населения в защитных сооружениях является наиболее надежным способом защиты в ЧС сопровождающихся выбросом радиоактивных и химических веществ.
Убежища рассчитываются на определенное количество людей: на одного человека предусматривается не менее 05 м2 площади пола и 15 м3 внутреннего объема.
Эвакуация населения – это организованный вывоз и вывод населения из возможных очагов поражения и опасных зон в безопасное место.
Эвакуация планируется заблаговременно а осуществляется при возникновении реальной угрозы населения в конкретной чрезвычайной ситуации.
Средства индивидуальной защиты населения предназначены для защиты от попадания внутрь организма на кожные покровы и одежду радиоактивных отравляющих веществ и бактериальных средств. Они подразделяются на средства защиты органов дыхания и средств защиты кожи. К первым относятся противогазы фильтрующие (ГП-5 ГП-5М и ГП-4у для взрослого населения ДП-6 ДП-6М ПДФ-7 ПДФ-111 для детей) и изолирующие (ИП-4 ИП-5 ИП-46 ИП-46М респираторы (Р-2)) а также противопыльные тканевые маски (ПТМ-1) и ватно-марлевые повязки; ко вторым – одежда специальная изолирующая защитная (Л-1 ОЗК) защитная фильтрующая (ЭФО) и приспособленная одежда населения.
Медицинские средства защиты включают: аптечку индивидуальную АИ-2; индивидуальный противохимический пакет; пакет перевязочный индивидуальный. Они предназначены для профилактики и оказания медицинской помощи населению пострадавшему в чрезвычайной ситуации.
5.1. Безопасность жизнедеятельности в условиях чрезвычайных ситуаций
Предположим что произошел взрыв ГСМ массой 5т.
Определяем эквивалентную массу органического вещества Qэ (кг)
где Кэ- коэффициент учитывающий эквивалентность органического
Q- масса органического вещества т.
Qэ=640*1.05 *5=3360кг.
В зоне поражения взрывной волной находится четыре сооружения: автогараж—30м склад запчастей –50м ангар для с.х.м.—45м ремонтная мастерская—80м.
Рассчитываем избыточное давление во фронте ударной волны (P кПа) от взрыва ГСМ на расстоянии Li (м)
D P=848 *Qэ13 Li+3440* Qэ23 Li2+11200*Qэ Li3 (7.8)
D P1=848 *341330+3440* 3423 302+11200*34 303 =526кПа;
D P2=848 *3413 50+3440*3423 502+11200*34503 =289кПа;
D P3=848 *3413 45+3440*3423 452+11200*34 453 =374кПа;
DP4=848 *341380+3440*3423 802+11200*34 803 =1723кПа.
Наиме-нование здания
Степень разрушения при DPфкПа
С металли-ческим каркасом
Ремонтная мастерская
Таблица 4.1 Результаты оценки устойчивости объектов.
Условные обозначения:
-слабые разрушения:
Рекомендуемые чертежи
- 26.04.2015
- 01.07.2014