Модернизация колено-рычажного пресса СМ-1085А



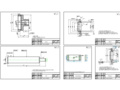
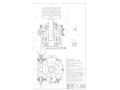
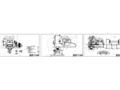
- Добавлен: 25.10.2022
- Размер: 4 MB
- Закачек: 0
Описание
Состав проекта
![]() |
![]() |
![]() ![]() ![]() |
![]() ![]() ![]() ![]() |
![]() |
![]() ![]() ![]() ![]() |
![]() ![]() ![]() |
![]() ![]() ![]() ![]() |
![]() ![]() ![]() |
Дополнительная информация
Спецификация Механизм исполнительный.doc
Подшипник 6220 ГОСТ 8338-75
Шпильки ГОСТ 22042-76
3_Lista.dwg

крепления ограждения поз.14 выполнить по месту
Отрегулировать отключение двигателя
Клей 88-Н рту38-5-880-66
верхнем и нижнем положениях винта подьема
за счет конечных выключателей
положение соответствует выходу нижних
регулятора глубины засыпки при крайних
в датчике регулятора. Крайнее верхнее
штемпелей выше уровня стола на 5 мм
нижнее положение - выходу нижних штемпелей
из прессформы на 35 мм. Увеличение хода винта
подьема более чем на 260 мм не допускается.
Обработку отверстий (см. Г-Г) под болты
Технические требования
Техническая характеристика
б) Двигателя привода регулятора глубины
а) Максимальная 100±2
б) Минимальная 65±2
а) Двигателя привода 43
в) Электроподогревателей 2
Высота общая 4640±60
Высота над уровнем пола 3175±50
а) Без электродвигателя и электрооборудования
по конструкторской документации 32000
Номинальное усилие прессования не более
Максимальная глубина засыпки массы
Производительность по кирпичу максимальная
Количество одновременно прессуемых изделий
КППМСН-19110000000 СБ
Осевой люфт червячного вала в пределах
Предельное смещение средней плоскости колеса
толщины шайбы поз. 6.
мм обеспечить за счет подбора
мм обеспечить за счет изменения
Осевой люфт червячного колеса с гайкой
мм обеспечить за счет прокладки
Контактные пятна в зацеплении должны быть не менее
% по высоте и длинне зуба при двухсторонней
ГОСТ6411-76. Температура нагрева элементов
верхней риски маслоуказателя
регулятора глубины засыпки обкатать в холостую
часа в обоих направлениях
После обкатки масло слить
обнаруженные дефекты устранить
залить маслом и обкатать в течение 10 15 мин.
вращения при снятом винте поз. 7 и заолненом до
допускается не более 60°С
После сборки механизм совместно с датчиком
БГТУ им. В.Г. Шухова
Mekhanizm_ispolnitelny.dwg

крепления ограждения поз.14 выполнить по месту
Отрегулировать отключение двигателя
Клей 88-Н рту38-5-880-66
верхнем и нижнем положениях винта подьема
за счет конечных выключателей
положение соответствует выходу нижних
регулятора глубины засыпки при крайних
в датчике регулятора. Крайнее верхнее
штемпелей выше уровня стола на 5 мм
нижнее положение - выходу нижних штемпелей
из прессформы на 35 мм. Увеличение хода винта
подьема более чем на 260 мм не допускается.
Обработку отверстий (см. Г-Г) под болты
Технические требования
Техническая характеристика
б) Двигателя привода регулятора глубины
а) Максимальная 100±2
б) Минимальная 65±2
а) Двигателя привода 43
в) Электроподогревателей 2
Высота общая 4640±60
Высота над уровнем пола 3175±50
а) Без электродвигателя и электрооборудования
по конструкторской документации 32000
Номинальное усилие прессования не более
Максимальная глубина засыпки массы
Производительность по кирпичу максимальная
Количество одновременно прессуемых изделий
Осевой люфт червячного вала в пределах
Предельное смещение средней плоскости колеса
толщины шайбы поз. 6.
мм обеспечить за счет подбора
мм обеспечить за счет изменения
Осевой люфт червячного колеса с гайкой
мм обеспечить за счет прокладки
Контактные пятна в зацеплении должны быть не менее
% по высоте и длинне зуба при двухсторонней
ГОСТ6411-76. Температура нагрева элементов
верхней риски маслоуказателя
регулятора глубины засыпки обкатать в холостую
часа в обоих направлениях
После обкатки масло слить
обнаруженные дефекты устранить
залить маслом и обкатать в течение 10 15 мин.
вращения при снятом винте поз. 7 и заолненом до
допускается не более 60°С
После сборки механизм совместно с датчиком
Верхняя часть пружин упирается в траверсу пресса
Пояснительная записка.docx
Назначение и принцип действия пресса СМ-1085А11
Сущность модернизации25
Расчет конструктивных технологических параметров27
1. Определение мощности электродвигателя и необходимого момента инерции маховика27
Прессдля изготовления кирпича —машинастатического действия для обработки материала и придания ему нужной формы (формования). Основные рабочие частипресса—ползун станина с направляющими дляползуна стол приводмеханизмуправления всеми устройствами пресса. Подвижная часть устроена следующим образом: инструмент крепится к ползуну неподвижная часть — к столу. Формование происходит между подвижной и неподвижной частями.
Основные параметры пресса — скорость движения ползуна от которого зависит производительность размеры стола номинальное усилие. Кирпич был самым древним строительным материалом изготовленным искусственно. В Древнем Египте в Монхенджо-Даро в строительстве использован обожженный кирпич в III—II тысячелетии до н. э. Кирпич использовался в Месопотамии Древнем Риме для строительства сложных декоративных конструкций узорной кладки. [1]
Возможно изготовлять кирпич с различными свойствами и назначением: сплошной дырчатый щелевой пустотелый с повышенной теплоизоляцией глиняный—лекальный. Кирпич — искусственный камень в процессе обработки получивший свойства натурального камня: прочность морозостойкость водостойкость. Он имеет правильную форму и размеры 250 х 120 х х 65 мм и 250 х 120 х 88 мм. Готовый кирпич подразделяется на марки.
Сырье для изготовления кирпича — глина суглинки пески. Дальнейшее развитие и усовершенствование конструкции формовочных машин направлено на увеличение производительности и качества создание и использование автоматических систем управления. [2]
Описание технологической схемы производства огнеупорного кирпича
Муллитокорундовые изделия общего и специального назначения марки МКС-72 предназначенные для футеровки сталеразливочных ковшей.
При производстве данных изделий используют шамот двух фракций каолин ПЛКО и лигносульфонаты технические (ЛСТ). В двухфракционном шамоте размер крупной фракции должен быть по крайней мере больше мелкой в 10 20 раз. Размер крупных частиц берется в пределах 05 – 3 мм так как фракция >3 мм не обеспечивает получение четких ребер и углов изделий. Размер мелкой фракции шамота влияет на плотность укладки но не только а также влияет физико-химические процессы при обжиге изделий прежде всего на спекание. Глина служит связующим компонентом в шамотной массе поэтому она должна быть равномерно распределена между частицами шамота для этого используется смесь совместного помола (ссп) шамота и каолина в трубной мельнице. Преимущество смешения при совместном помоле заключается в том что здесь достигается хороший контакт с частицами шамота поэтому исключается расфракционирование массы.
Каолин ПЛКО поступает на комбинат железнодорожным транспортом где так же разгружается на приёмном устройстве и хранится на складе сырья дробильно – обжигового участка.
Глинозём поставляется железнодорожным транспортом в специализированных вагонах (хоппёрах) 1. Разгрузка глинозёма производится при помощи камерного насоса 2 в силос откуда при помощи пневмокамерного насоса 4 глинозём доставляется в бункер над трубной мельницей брикетного отделения.
Всё глинистое сырьё хранится на складе в конусах в условиях исключающих смешивание загрязнение посторонними включениями и дополнительное увлажнение.
Места складирования глин каолинов обозначаются табличками аншлагами с указанием месторождения и марки.
Дробильно-помольное отделение.
Огнеупорные каолины грейферным краном 19 подаются в загрузочные бункера стругачей 20 в которых они дробится до кусков размерами не более 60 мм затем системой ленточных транспортёров 8 и элеваторов 17 измельченные каолины транспортируются в бункера 6 над сушильным барабаном 21.
Каолины сушатся в сушильном барабане 21 по принципу прямотока. Температура на входе в сушильный барабан в пределах 600 – 800 0С на выходе должна быть не ниже 100 0С. Сушка каолинов производится в соответствии с требованиями теплотехнических инструкций.
Высушенные каолины использующийся для производства шамота через камневыделительные вальцы 22 где происходит отделение каменистых включений равномерно подаются на измельчение в центробежную мельницу – дезинтегратор 23.
Каолин входящий в состав шихты для производства шамота после измельчения просеивается на вибросите 25 (зерновой состав молотой глины должен удовлетворять требованиям табл. 1.1.) и затем системой ленточных транспортёров 8 и элеватора 17 доставляется в формовочное отделение и при помощи разгрузочных кареток загружается в бункер 6 над мешалкой 10.
Из бункера глинозём подаётся на измельчение в двухкамерную трубную мельницу 9 куда для ускорения помола подаётся поверхностно-активное вещество.
Измельченный глинозём пневмокамерным насосом 4 установленным под трубной мельницей 9 подаётся в бункер 6 над мешалкой 10.
Компоненты шихты огнеупорной массы подаваемые на смешивание дозируются автоматическими весовыми дозаторами 7.
Смешивание компонентов шихты и обработка массы производится по режиму:
- загрузка глинозёма и каолина;
- увлажнение массы водой;
Огнеупорная масса от пропеллерной мешалки 10 ленточным транспортёром 8 подаётся в двухвальный смеситель 12 в котором производится дополнительное увлажнение массы водным раствором ЛСТ.
Прессование брикета из огнеупорной массы производится на прессвальцах 14. Брикет ленточным конвейером 8 через загрузочную течку загружается во вращающуюся печь печного агрегата 15. Охлаждение обожжённого шамота в холодильнике производится потоком холодного воздуха и путём орошения водой.
Шамот обожжённый во вращающейся печи подаётся в силоса 13 для промежуточного хранения.
Высокоглинозёмистый шамот из силосов 13 системой ленточных транспортёров 8 и элеватора 17 подаётся на измельчение в шаровую мельницу 16 работающую по принципу самоотсева. После чего подается на воздушный сепаратор или грохот ГИЛ-32 26 для разделения на фракции 3-05 и 05-0 мм.
Порошок шамота фракции 3-05 мм подается в отдельные бункера 6 откуда системой ленточных транспортеров 8 и элеваторов 17 подается в бункер 6 над мешалкой пропеллерной 10.
Порошок шамота фракции 0- 05 мм подается в бункер 6 над трубной мельницей 9 и используется для приготовления смеси совместного помола.
Тонкомолотая смесь муллитокорундового шамота и глинистой составляющей приготавливается путем совместного помола в трубной мельнице 9.
Зерновой состав совместного помола должен удовлетворять требованиям:проход через сито № 0063 не менее 90 %.
Компоненты шихты огнеупорной массы подаваемые на смешивание дозируются автоматическими весовыми дозаторами 7 марки с технологическим допуском ± 20%.
Шликер и раствор ЛСТ для увлажнения огнеупорной массы дозируется объемным способом при помощи мерного бачка.
Шликер вводится в огнеупорные массы для получения прочного плотного сырца изделий при полусухом прессовании. Значительная активная поверхность мелких частиц глины шликера равномерно распределенных в огнеупорных массах способствует лучшему спеканию сырца изделий.
Смешивание компонентов шихты и обработка массы производится в бегунах 29 по режиму:
- загрузка шамота увлажнение шликером и раствором ЛСТ (плотностью не менее 120гсм3 в соотношении 1:1)
- перемешивание 25-3 мин.
- загрузка смеси совместного помола обработка массы 3-4 мин.
- выгрузка массы из бегунов – 1мин.
Общая продолжительность цикла смешивания компонентов шихты и обработки огнеупорной массы должна составлять 65-80 минут.
В применяемых смесительных бегунах 29 одновременно со смешением компонентов шихты производится и уплотнение массы благодаря чему достигается хороший контакт между частицами глины и шамота. Недостаток смесительных бегунов 29 с тяжелыми катками состоит в том что при проработке массы на них происходит измельчение шамота – домол который иногда достигает существенной величины. При высоком водопоглощении шамота и низкой механической прочности относительное увеличение содержания мелкой фракции может достигнуть 10%. В результате доизмельчения шамота в некоторых случаях образуются «коржи» во избежание их образования после смешения на бегунах массу пропускают через протирочное сито.
Масса из бегунов 29 по ленточному транспортеру 8 подается в граблевую мешалку 30 где установлено протирочное сито с диаметром отверстия не 15мм.
Масса протирается через сито а затем из граблевой мешалки 30 по «рукавам» подается в пресс 31.
Прессование сырца изделий марки МКС-72 из огнеупорной массы производится на прессах «СМ-1085А».
В первый период прессования под влиянием перемещения штемпеля крупные частицы раздвигают более мелкие приходят в соприкосновение друг с другом и образуют каркас. При дальнейшем сжатии происходят пластическая упругая и хрупкая деформация. Контактные поверхности частично разрушаются. Вода выжимается в промежутке между частицами.
В целях получения продукции высокого качества прессования особо ответственных изделий применяют гидравлические пресса.
Далее изделия вручную сажаются на печные вагонетки 32 которые затем направляются в печное отделение.
Целью обжига является получение прочных плотных изделий с заданными соответствующими требованиями ГОСТа свойствами. При обжиге изделий происходит спекание а также изменение фазового состава обратимое термическое расширение и необратимое изменение объема изделий. Основные физико-химические процессы при обжиге изделий происходят в связующей глине однако и в шамоте некоторые процессы так же продолжаются. Единственной твёрдой фазой устойчивой при достаточно высокой температуре ( >1585 0С) является муллит 3 Al2O3*2 SiO2.
Сушка и обжиг сырца огнеупорных изделий производится в туннельной печи 35 сблокированной с сушилом 34на вагонетках (размеры 30-31м). Печные вагонетки 32 перед началом садки сырца должны быть осмотрены подины вагонеток должны быть ровными без отбитых углов с целой футеровкой.
Обжиг изделий производится в туннельной печи 35.Отпрессованные изделия ленточным транспортером 8 подаются к посадочному месту.
Садка сырца на печные вагонетки 32 производится автоматом-
Туннельная печь 35 длиной 168м температура обжига 1450 0С продолжительность обжига 75 ч.
Рис. 1.1. Технологическая схема производства огнеупорного кирпича
Назначение и принцип действия пресса СМ-1085А
Пресс усилием 63 МН сконструирован и первый образец его был изготовлен на харьковском заводе «Красный октябрь». Пресс СМ 1085 представляет собой модернизированную модель пресса ПК 630 и имеет в основном аналогичные схему механизм прессования узел выталкивания и станину.
Конструкция указанного пресса улучшена по сравнению с прессом ПК 630 за счёт: применения механизированного регулятора глубины засыпки прессформ с автоматическим указателем; установки пневмосъёмника отпрессованных изделий (Механизированная садка); установки приспособлений по сбору и удалению осыпи массы; усовершенствования привода засыпной каретки; крепления стола; полной автоматизации и централизации смазки и др.
Число прессований в минуту может изменяться от 6 до 85 за счёт установки сменных шкивов на валу электродвигателя.
Кинематическая схема пресса СМ 1085А Приведена на рисунке (см. рис 2.1). Передача от приводного вала к коленчатому валу осуществляется следующим образом: От приводного вала через зубчатую передачу передаётся вращение промежуточному валу на консольном конце которого расположена промежуточная шестерня находящаяся в зацеплении с зубчатым колесом насажанным на консольном конце коленчатого вала. На этом зубчатом колесе закреплён разъемный кулак 2 с которым сопряжен ролик 3 привода механизма засыпки прессформ.
Коленчатый вал 1 шарнирно связан с шатуном 4 к нижней части которого прикреплён копир 5. В результате набегания копира 5 на рол 6 происходит подъем прессующего узла и выталкивание отпрессованных изделий из прессформ; опускание прессующего узла осуществляется также при помощи копира 5. Предусмотрено два сменных копира из которых один для прессования изделий высотой 65-80 мм а второй - для изделий 80-100 мм. [3]
Рисунок 2.1 - Кинематическая схема пресса СМ 1085
От коленчатого вала 1 через шатун 4 движение передаётся верхнему 7 и нижнему 8 рычагам. В верхней части рычаг 7 свободно насажан на ось соединяющую сверху две штанги 9 а в нижней он шарнирно соединен с шатуном 4 и верхней частью рычага 8. В нижней части рычаг 8 шарнирно соединён с ползуном 10 на нижней плоскости которого на переходной плите закреплены верхние пуансоны 11. Нижние пуансоны 12 закреплены на переходной плите установленной на верхней плоскости стальной траверсы 13 с которой связаны нижние части обеих штанг 9.
Штанги 9 ось связывающая их верхние части и траверса 13 представляют собой жесткую раму узла прессования. Направляющими рамы являются плоскости штанг 9 и вкладыши станины.
Прессы оснащены автоматическими регуляторами засыпки пресспорошка.
Исполнительный механизм автоматического регулятора засыпки расположен под траверсой 13 механизма прессования и установлен на сварной конструкции прикреплённой к станине пресса.
Исполнительный механизм приводится в движение электродвигателем 14 по средством муфты 15 подсоединённой к червячному валу 16 находящемуся в зацеплении с червячным колесом 17. В центре червячного колеса закреплена гайка с трапециидальной резьбой с подъёмным винтом 18. Червячный вал 16 и колесо 17 с гайкой и винтом 18 вращающиеся в подшипниках качения помещены в корпусе и представляют собой червячный редуктор. Подъёмный винт 18 шарнирно соединён со штоком на конце которого закреплён поршень пневмоамортизационного устройства. Поршень с поршневыми кольцами расположен и перемещается в гильзе запрессованной в центральном отверстии траверсы 13 которая опирается на верхнюю торцевую поверхность поршня.
Подъёмом или опусканием подъёмного винта 18 исполнительного механизма осуществляется изменение положения нижних пуансонов за счёт поднятия или опускания прессующей рамы а следовательно и изменение глубины засыпки пресспорошка в прессформе. [6]
К исполнительному механизму посредством фланца присоединяется датчик с двухступенчатым червячным редуктором указателя глубины засыпки. Выходной червячный вал 19 указанного редуктора соединён с червячным валом 16 исполнительного механизма а с выходным валом червячного колеса 20 второй ступени двухступенчатого редуктора соединён сельсин-датчик 21 типа БД-404А. Червячный вал 22 второй ступени редуктора имеет хвостовик с резьбой сопряженный с гайкой 23. Гайка со штырём 24 кнопок управления совершает по направляющей колонне возвратно-поступательное движение между двумя кнопками управления 25 автоматического выключателя электродвигателя 14.
Сельсин-приёмник на валу которого насажана шкала глубины засыпки вмонтирован в алюминиевый корпус расположенный на пульте управления.
Засыпная каретка 26 состоит из нижней и верхней частей. Нижняя часть каретки толкаемая верхней скользит по столу пресса своими резиновыми уплотнителями предохраняющими от просыпания пресспорошка. Верхняя часть каретки продвигается по роликам расположенным вдоль её движения по четыре с обеих сторон.
Верхняя часть каретки соединяется регулируемыми тягами 27 с рычагами 29 28 и получает возвратно-поступательное движение от кулачка 2 прикрепленного к зубчатому колесу коленчатого вала 1. При обкатывании профиля кулачка роликом 3 обеспечивается плавное трогание с места каретки 26 набор скорости и плавная остановка в переднем положении. Аналогичен характер движения каретки и при возвращении её в крайнее заднее положение. Такой косинусоидальный характер движения каретки предусмотрен для устранения фракционирования пресспорошка и предотвращения ударов в шарнирных соединениях. Проходя над прессформой загрузочная каретка засыпает в неё пресспорошок а на обратном ходе разравнивает пресспорошок в прессформе. [5]
Для сталкивания кареткой отпрессованных изделий на удлинённую часть стола без пульсирующего конвейера предусмотрен сталкиватель изделий прикрепляемый к передней части засыпной каретки вместо пневмосъёмника.
Осыпь пресспорошка по лоткам и трубам подаётся на транспортёр расположенный в приямке и отводится для дальнейшей переработки.
Стол пресса состоит из переднего и заднего брусьев стягиваемых после установки между ними прессформы двумя прочными шпильками. К верхним плоскостям брусьев потайными винтами прикреплены передний и задний сменные листы по которым передвигается засыпная каретка 26. Передний и задний брусья стола вставляют в пазы станины и жестко закрепляют клиньями и болтами. Задняя часть стола опирается на угольник станины.
В брусьях стола имеются продольные пазы в которые заходит своими выступами прессформа. Прессформа крепится к столу двумя горизонтальными шпильками. Таким образом обеспечивается быстрый съём и установка прессформ Достоинства: Пресс прост в устройстве и обслуживании развивает высокое давление; высокая производительность (до 2280 шт.ч при четырех штампах).
Недостатки: Нельзя прессовать изделия высотой менее 40 мм; быстро изнашиваются зубчатые колеса в результате возникающих толчков во время работы пресса; утечка воздуха из амортизационного цилиндра приводит к тому что детали пресса воспринимают большие удары и разрушаются; сравнительно малая продолжительность сжатия и отсутствие выдержки при максимальном давлении [4]
За период эксплуатации пресса СМ-1085 был предложен ряд модернизаций узлов и механизмов пресса рассмотрим некоторые из них:
Пуансон пресса содержит корпус 1 облицовочную плиту 2 коробчатого сечения с элементами 3 ее крепления и эластичный вкладыш 5. Для увеличения срока службы и повышения качества изделий основание плиты 2 выполнено с отверстиями каждое из которых расположено вдоль соответствующей стенки плиты и выполнено в средней части с направленным к центру плиты изломом для перемещения стенки в пределах упругой деформации.
Рисунок 3.1 -Пуансон пресса. а – продольный разрез б – вид снизу.
При работе пресса в конце прессования возникает упругая деформация не только корпуса пресс-формы но и в стенках плиты 2 за счет прессующего давления передаваемого эластичным вкладышем 5. За счет выполнения отверстий 6 с изломом в средней части стенки плиты 2 начинают перемещаться параллельно своему первоначальному положению в пределах упругой деформации. В результате не происходит увеличения первоначальных технологических зазоров между боковой поверхностью облицовочной плиты пуансона и футеровочными пластинами пресс-формы и тем самым исключается возможность запрессовки в этих зазорах пресс-порошка и образование облоя что ухудшает качество изделий. После завершения процесса прессования стенки плиты 2 и стенки пресс-формы (не показана) под действием сил упругой деформации возвращаются в первоначальное положение.
) Теплоэлектронагревательное устройство штемпеля пресса (А.В. СССР № 1219363 кл. В 28 В 300 1975г) закрепленное на корпусе штемпеля пресса содержащее источник питания и электронагреватель и отличающееся тем что с целью увеличения его срока службы сокращения расхода электроэнергии и улучшения качества кирпича электронагреватель выполнен в виде трехслойного упругоэластичного покрытия расположенного на рабочей поверхности пресс-плиты и состоящего из теплоизоляционного слоя электронагревательного слоя в виде углеграфитовой ткани и термостойкого антиадгезионного слоя.
Устройство состоит (рисунок 2.2) из источника питания (не показан) и электронагревателя закрепляемого на корпусе 1 штемпеля пресса посредством крепежных отверстий 2.
Рисунок 3.2 - электронагревательное устройство
Электронагреватель выполнен в виде трехслойного упругоэластичного покрытия состоящего из теплоизоляционного слоя 3 электронагревательного слоя 4 и термостойкого антиадгезионного слоя 5.
) Центральное конструкторское бюро «Строммашина» предложило модернизацию прессформы для прессов полусухого прессования (патент ГДР № 123278 кл. В 28 306 1975).
Рисунок 3.3 – прессформа. а – поперечный разрез; б – вид снизу.
Прессформа содержит корпус 1 верхние 2 и нижние 3 штампы верхнюю плиту 4 с окнами по периметру которых установлены вертикальные пластины 5 с охватывающими их по вертикально-замкнутому контуру облицовками 6 выполненными из тонколистовой износостойкой стали. Облицовки 6 крепятся шпонками 7 таким образом что они оказываются защемленными верхней плитой 4. Вертикальные пластины 5 соединяются угловыми вставками 8 образуя замкнутый контур гнезд. Вертикальные пластины 5 и шпонки 7 прижимаются к верхней плите 4 посредством нижних пластин 9-11 которые также как и верхняя плита 4 крепятся к корпусу болтами 12.
Пресс-форма работает следующим образом:
Во время уплотнения прессуемой массы штампами силы трения стремятся сдвинуть облицовку 6 к нейтральному слою но силы прижимающие ее прессуемой массой к вертикальным пластинам 5 всегда больше сил трения поэтому облицовка 6 в процессе прессования не может деформироваться.
В момент выталкивания отпрессованного кирпича нижними штампами 3 облицовка 6 испытывает нагрузку от сил трения выталкиваемого кирпича о ее поверхность поэтому она снизу выполнена цельной в переходе из одного гнезда корпуса в смежное.
Заменяя угловые вставки 8 можно прессовать кирпич как с закругленными углами так и с прямыми. При износе рабочих поверхностей пресс-формы заменяют тонкостенные облицовки 6 сохраняя вертикальные пластины 5.
Данная прессформа отличается от обычной тем что с целью улучшения технологичности при ремонтных работах облицовки охватывают вертикальные пластины по вертикально замкнутому контуру и защемлены верхней плитой.
) Научно-производственным объединением по автоматизации горнорудных металлургических предприятий и энергетических объектов черной металлургии предложена прессформа для порошковых материалов (А.С. СССР № 147394 кл. В 28 В 302 1989г.) которая состоит из: корпуса 1 с гнездами 2. Вдоль боковых стенок гнезд 2 выполнены пазы 3 в которых размещаются концы облицовочных боковых пластин 4 имеющие длину относительно длины I гнезда пресс-формы больше на величину не менее двух 15 собственных толщин пластин. Для расклинивания боковых облицовочных пластин между ними с усилием запрессовывают торцовые облицовочные пластины 5 имеющие двухсторонние боковые уклоны площадь опоры боковой облицовочной пластины с 20 плоскостью гнезда пресс-формы воспринимающая усилие расклинивания торцовой пластиной характеризуется шириной В.
Рисунок 3.4 - Прессформа
Предлагаемая пресс-форма характеризуется значительно увеличенной жесткостью что позволяет выполнять процесс прессования при более высоких усилиях прессования и получать прессовки (сырец) с улучшенными показателями по плотности гсм3.
Пресс-форма для порошковых материалов включающая корпус с гнездами боковые и торцовые облицовочные пластины отличающаяся тем что с целью повышения качества прессования корпус пресс-формы выполнен с расположенными вдоль боковых стенок каждого гнезда пазами а длина боковых облицовочных пластин больше длины гнезда пресс-формы на величину не менее двух ее толщин.
) Рассмотрим также прессформу для прессования керамических изделий конструкция которой была предложена всесоюзным НИИ фарфоро-фаянсовой промышленности (Авторское свидетельство СССР № 640504 кл. В 28 В 300 1976г.).
Прессформа содержит (рисунок 2.5) разрезную конусную кольцевую матрицу 2 охватываемую подвижной обжимной конусной обоймой 1. сменную ленту 3 вставляемую внутрь матрицы и выполненную из упругой полосы нижний 4 и верхний 5 пуансоны регулируемые упоры 7 смонтированные на неподвижной жестко закрепленной на прессе обойме 6 и регулируемые элементы 8 выполненные в виде набора пластин и вставленные в совместный зазор ленты и разрезной матрицы.
Пресс-форма для прессования керамических изделий содержащая кольцевую разрезную матрицу верхний и нижний пуансоны подвижную обжимную обойму охватывающую матрицу размещенную внутри матрицы ленту с разъемом и регулируемые упоры отличающаяся тем что. с целью повышения срока службы пресс-формы и качества изделий а также сокращения трудозатрат на изготовление ленты с разъемом пресс-форма снабжена неподвижной обоймой жестко закрепленной на прессе и выполненными в виде съемных пластин регулируемыми элементами расположенными в разъеме ленты и матрицы. при этом регулируемые упоры установлены на неподвижной обойме а лента выполнена в виде упругой стальной полосы.
Рисунок 3.5 - Прессформа для прессования керамических изделий
Предлагаемая пресс-форма для прессования керамических изделий работает следующим образом.
) Прессформа для полусухого прессования кирпича разработанная малым предприятием «АККом» (авторское свидетельство СССР № 417288 кл. В 28В 304 1974 авторское свидетельство СССР N 887178 кл. В 28В 300 1981.) содержит составную матрицу 1 объединенный пуансон 2 и дренажные пальцы проемообразователи 3 и установлена в поворотном столе пресса. Матрица 1 выполнена из двух фигурных симметричных разъемных пар стенок 4 и 5 с фиксаторами 6 и связками 7 имеет в сборе наружную цилиндрическую форму и снабжена по высоте двумя внешними концентрическими посадочными опорами 8 и фланцем 9 с калибровочным штифтом 10.
Рисунок 3.6 - прессформа для полусухого прессования кирпича. а - общий вид по продольной оси О-О; б - то же вид сверху; в - матрица прессформы общий вид.
На внутренней поверхности стенок матрицы образованы фигурные зубчатые пазы 11 для размещения в них и фиксации быстроизнашивающихся вкладышей внешних 12 и внутренних 13 которые закреплены сверху диском 14. размещенным в верхней проточке 15 матрицы 1. Стенки матрицы имеют в нижней части удлинения в виде серьги 16 со сквозным по продольной оси 0-0 окном 17 с конусным подпятником 18. Пуансон 2 снабжен двумя параллельно расположенными П-образными стойками 19 коробчатой формы с внутренними 20 и центральной 21 дренажными полостями имеющими наклонные скаты 22 и 23. обращенные к окнам 17 серег 16 матрицы 1. Стойки 19 пуансона 2 связаны с основанием 24 пуансона имеющим центральное отверстие 25 в котором закреплен опорный валик 26. размещенный консолями 27 в окнах 17 серег 16 матрицы 1 и ограниченный в нижнем положении подпятником 18. Пресс-форма посредством болтовых соединений 28 и 29 стенок 4 и 5 матрицы 1 крепится в поворотном столе ротора. Диск 14 крепления формовочных вкладышей 12 и 13. размещенный в верхней проточке 15. крепится к матрице 1 посредством болтовых соединений 30. Дренажные пальцы - проемообразователи 3 закреплены в пресс-форме посредством валиков 31. Пуансоны 2 в верхней части имеют отверстия 32 для размещения в них дренажных пальцев- проемообразователей 3.
Рисунок 3.7 - прессформа для полусухого прессования кирпича. а б - пуансон; в - схема формования изделия.
Прессформа для полусухого прессования кирпича отличается тем что матрица снабжена по высоте двумя внешними концентрическими посадочными опорами и фланцем с калибровочным штифтом а на внутренней поверхности стенок матрицы образованы продольные пазы для размещения и фиксации от поперечного смещения вкладышей которые зафиксированы от продольного перемещения при помощи диска размещенного в верхней проточке матрицы две диаметрально противоположные стенки которой имеют каждая в нижней части удлинение в виде серьги со сквозным окном и конусным подпятником при этом пуансон снабжен двумя параллельно расположенными П-образными стойками коробчатой формы образующими внутренние и центральную дренажные полости "и имеющими сквозные отверстия в их горизонтальных полках и наклонные скаты обращенные к окнам серег стенок матрицы а основание пуансона имеет 'в центральной части сквозное горизонтальное отверстие с укрепленным в нем опорным валиком с выступающими за пределы основания консолями размещенными в окнах серег стенок матрицы и взаимодействующими в нижнем положении пуансона с конусными подпятниками. причем пресс-форма снабжена дренажными пальцами проемообразователями. пропущенными через отверстия горизонтальных полок стоек пуансона и размещенными во внутренних дренажных полостях стоек.
Вывод: В ходе проведения патентного исследования выяснилось что наибольшее внимание в патентной документации отведено разработкам связанным с улучшением качества формования изделий (модернизация пуансона прессформ улучшение зернового состава смеси технологии ее приготовления и т. п.) в то время как разработок связанных с улучшением конструктивных параметров машин представлено сравнительно меньше.
Так как улучшение конструкции машины не менее важно с точки зрения экономии материальных и финансовых средств чем улучшение качества продукции можно сказать что реконструкция пресса для полусухого прессования представленная в данной работе является обоснованной с этой точки зрения.
Сущность модернизации
Прессование изделий на прессе СМ-1085 осуществляется прессующим колено-рычажным механизмом выполненным в виде рамы образованной осью верхней серьги нижней траверсой и двумя боковыми направляющими штангами. После прессования изделия выталкиваются на уровень стола тем же прессующим механизмом и штоками закрепленными на нижней траверсе после чего нижняя траверса опускается в исходное положение. При этом общая масса опускающихся деталей составляет приблизительно 5 тонн. Для амортизации ударных нагрузок предусмотрен узел амортизации при помощи пневматического цилиндра. В процессе эксплуатации пресса гильза пневмоцилиндра как и поршень изнашиваются что приводит к возникновению ударных нагрузок кроме того имеет место перекос нижней что приводит к более быстрому износу деталей пресса в частности уплотнительных направляющих механизма прессования и отклонению от геометрической формы самих изделий. В связи с этим предлагается заменить механизм амортизации по средством пневмоцилиндра на механизм амортизации при помощи пружин сжатия это позволит устранить прекосы нижней траверсы вызванные износом пневмоцилиндра и значительно увеличить срок службы узла амортизатора.
Рисунок 4.9 - Плита амортизатора в сборе.
Модернизация реализуется следующим образом: из механизма амортизации удаляются шток пневмоцилиндра вместе с поршнем. Вместо этого на винт регулятора глубины засыпки устанавливается плита 1 (рисунок 2.9) с запрессованными в нее шестью бобышками и установленными на них пружинами сжатия. Винт регулятора глубины засыпки соединяется с плитой по средством выполненной на нем проточки и центрального отверстия в плите диаметром 65мм.
После монтажа конструкции амортизатор окажется установленным непосредственно на винт регулятора глубины засыпки а пружины 2 верхней своей частью будут прижаты к нижней части траверсы пресса (рисунок 2.10).
Рисунок 4.10 - Установка амортизатора на пресс.
Расчет конструктивных технологических параметров
1.Определение мощности электродвигателя и необходимого момента инерции маховика
Мощность электродвигателя пресса определяется для прессования кирпича наибольших размеров при наибольшем допустимом значении влажности порошкообразной массы.
Наибольшая влажность порошкообразной массы для изготовления кирпича 8%.
Наибольшее отношение m высоты H насыпанного в форму порошка к высоте h кирпича составляет 18 Следовательно рабочий ход ползуна в течение которого происходит прессование кирпича равен: Sp=(m-1)h.
где h=120 мм - наибольшая высота кирпича.
Sp=(18-1) 120=96 мм.
Наибольшее усилие Pпн прессования кирпича наибольших размеров принимается равным номинальному усилию Pн=6300 кН. График усилия Pн прессования в зависимости от хода ползуна построенный на основании кривых зависимости осадки массы при 8% влажности от удельного давления прессования (рисунок 4.1).
На основании графика усилий Pн прессования в зависимости от хода S ползуна (рисунок 4.1) и Графика хода ползуна в зависимости от угла поворота коленчатого вала построен график усилий в зависимости от угла который показан на рисунке 4.2.
Рисунок 5.1 - Зависимость усилия прессования Pп от хода ползуна S
График крутящих моментов Mк на коленчатом валу пресса в зависимости от угла строится по формуле:
где - отношение усилий действующих по шатуну к усилиям на ползуне в зависимости от угла ; mк – приведенное плечо крутящего момента мм. [7]
Рисунок 5.2 - Зависимость крутящего момента на коленчатом валу от угла
На основании графиков усилий плеча mк и отношения построен график крутящих моментов который приведен на рисунке 4.2.
Работа AР на коленчатом валу затрачиваемая на прессование кирпича наибольших размеров с учетом потерь на трение в кривошипно-шатунном механизме определяется на основании графика крутящих моментов по зависимости:
где Км – масштаб крутящих моментов: Км=800 Нммм; FР – площадь ограниченная графиком крутящих моментов (рисунок 4.3): FР=8140 мм2 ; К - масштаб углов:
АР=80000109814=71 кДж
Рисунок 5.3 - График зависимости крутящего момента Мк от угла
Из графика крутящих моментов следует что максимальный крутящий момент =90 кНм а угол к поворота кривошипа с которого начинается прессование равен 89
Так как прессование заканчивается при угле =0 то рабочий угол р=89°.
Кроме того дополнительно затрачивается работа Ап для подачи порошкообразной массы в штамп; работа АД на деформацию и работа АВ на подъем прессующего механизма (выталкивание).
Работа АП принята приближенно равной 02АР.
Работа АД затрачиваемая на деформацию прессующего механизма при малых углах поворота кривошипа и больших усилиях в среднем составляет 03 АР.
Работа АВ необходимая для подъема прессующего механизма (выталкивание изделия) равна примерно 02АР.
Следовательно суммарная работа АС которую должен отдавать электродвигатель при автоматическом режиме работы пресса за один ход равна:
где - суммарный КПД передач от вала электродвигателя к коленчатому валу:
где зуб – КПД зубчатой передачи: зуб=097; а – число ступеней зубчатых передач: а=2; кл – КПД клиноременной передачи: кл=094;
Необходимая мощность электродвигателя определяется по формуле:
NP=16310-217885=247 кВт.
где nА - Наибольшее число используемых ходов пресса в минуту: nА=85; nT - наибольшее число оборотов коленчатого вала в минуту: nT=85.
В целях значительного уменьшения необходимого момента инерции маховика согласно каталогу на прессе устанавливается электродвигатель АОС9З-8 имеющий номинальную мощность N=40 кВт при продолжительности включения ПВ=25% номинальное число оборотов nн=675 в минуту синхронное число nc=750 оборотов в минуту номинальное скольжение Sн=01 и кратность максимального момента =24
В виду того что электродвигатели кривошипных прессов работают при продолжительности включения ПВ=100% то установленный электродвигатель. имеющий согласно каталогу мощность N=28 кВт при ПВ=100% удовлетворяет необходимой расчетной мощности NP=247 кВт.
Число оборотов электродвигателя АОС93-8 соответствующее мощности N=28 кВт. При ПВ=100% равно:
Крутящий момент развиваемый электродвигателем при ПВ=100% и приведенный к коленчатому валу равен:
где i – общее передаточное число передач привода пресса.
На диаграмме момент МЭП показан пунктирной линией (рисунок 4.3)
Работа совершаемая электродвигателем за время прессования кирпича определяется на основании графика крутящих моментов по зависимости:
где Fэ - площадь соответствующая работе электродвигателя;
Аэ=40880000109=356 кНм
Работа которая должна быть совершена маховиком за время прессования равна:
Для определения необходимого момента инерции маховика требуется знать скольжение Sx электродвигателя перед началом прессования:
Для определения скольжения Sx найдем средний крутящий момент Мср на валу электродвигателя за один оборот коленчатого вала по формуле:
Скольжение Sx соответствующее моменту Мср будет равно:
где Mн – номинальный крутящий момент на валу электродвигателя.
Необходимый момент инерции Jн маховика и вращающихся деталей привода пресса определяется по Формуле:
где Sд - принятое допустимое скольжение электродвигателя АОС 93-8 в конце прессования: Sд=025.
На прессе предполагается производить прессование кирпичей при числе ходов n`т=6 в минуту при автоматическом режиме работы.
Уменьшение числа ходов с 85 до 6 осуществляется за счет увеличения передаточного числа клиноременной передачи. При числе ходов nт=6 в минуту без большой погрешности можно принять что работа А`э совершаемая электродвигателем за время прессования равна.
Следовательно работа совершаемая маховиком при n`т=6 ходах в минуту должна быть:
Передаточное число клиноременной передачи при n`т=6 ходах в минуту есть I`1=362.
Тогда необходимый момент инерции маховика должен быть равен:
Учитывая что при n`т=6 ходах в минуту необходимая мощность электродвигателя будет меньше принимается в качестве расчетного необходимый момент инерции Jн=210 Н·м2.
Момент инерции маховика имеющегося на прессе вычисляется согласно рисуно. 4.5 по формуле:
где J b D i - удельный вес элемента маховика: I=72 тм3 (маховик изготовлен из чугуна).
Результаты вычисления момента инерции маховика сведены в таблица 4.1.
Далее находятся моменты инерции деталей привода приведенные на вал маховика.
Моменты инерции деталей привода определяются по той же формуле что и момент инерции маховика при gI=785 тм3 (детали привода изготовлены из стали). При вычислении моментов инерции зубчатых колес их спицы всюду условно заменены (равновесными со спицами) дисками.
Момент инерции Jк деталей вращающихся вместе с коленчатым валом определяется согласно рисунок 4.7 результаты его вычисления даны в таблице 4.2.
Момент инерции кривошипа вычисляется по формуле:
где R - радиус кривошипа м;
Момент инерции щек коленвала вычислялся по формуле:
где а – высота щеки м; b – ширина щеки м; G3 – вес щеки; R1 – расстояние от оси до центра тяжести щеки м.
Рисунок 5.5 - Эскиз маховика
Таблица 4.1 Результаты вычислений моментов инерции Ji
Рисунок 5.6 - Маховик в сборе
Таблица 4.2 Результаты определения момента инерции Ji
Момент инерции кривошипа относительно оси вала
Момент инерции щек относительно оси вала
Приведенный к валу маховика момент инерции деталей вращающихся вместе с коленвалом равен:
где i2 - передаточное число быстроходной зубчатой передачи i2 = 546.
Момент инерции деталей вращающихся вместе с промежуточным валом определяется согласно рисунок 4.7 результаты его вычислений приведены в таблице 4.3
Рисунок 5.7 - промежуточный вал
Момент инерции приведенный на вал маховика равен:
Таблица 4.3 Результаты определения момента инерции приведенного на вал маховика
Момент инерции Jр деталей вращающихся с валом маховика после отключения муфты определяется согласно рисунке 4.8.
Результаты его вычисления сведены в таблицу (таблица 4.4)
Рисунок 5.8 - Вал маховика в сборе
Таблица 4.4 - результаты определения моментов инерции деталей вращающихся вместе с валом
Суммарный необходимый момент инерции вращающихся масс деталей приводе приведенный к маховика равен:
где k – коэффициент учитывающий момент инерции поступательно движущихся масс.
Ввиду того что суммарный момент инерции маховика и деталей привода равен:
Следовательно на прессе возможна заданная технологическая операция прессования кирпича.
В ходе выполнения курсового проекта была изучена конструкция и принцип действия Пресса СМ-1085А. Были поставлены задачи по усовершенствованию технологических и конструктивных параметров машины.
Изучив конструктив Пресса СМ-1085А были выявлены преимущества и недостатки данной машины. После чего был проведен патентный поиск.
Проведя анализ патентного поиска Сущность модернизации заключается в том что из механизма амортизации удаляются шток пневмоцилиндра вместе с поршнем. Вместо этого на винт регулятора глубины засыпки устанавливается плита.
Прессование изделий на прессе СМ-1085 осуществляется прессующим колено-рычажным механизмом выполненным в виде рамы образованной осью верхней серьги нижней траверсой и двумя боковыми направляющими штангами. После прессования изделия выталкиваются на уровень стола тем же прессующим механизмом и штоками закрепленными на нижней траверсе после чего нижняя траверса опускается в исходное положение. При этом общая масса опускающихся деталей составляет приблизительно 5 тонн.
Кашкаев И.С Шейнман Е.Ш. Производство глиняного кирпича. - М.: Высшая школа 1978 423 с.
Кондратенко В.А. Пешков В.Н. Следнев Д.В. Проблемы кирпичного производства и способы их решения Строительные материалы. № 3 2002 с. 23-27.
ГОСТ 530-2007 «Кирпич и камни керамические. Общие технические условия»
Сапожников М.Я. «Механическое оборудование предприятий строительных материалов и конструкций» М.: «Высшая школа» 1971 382с.
Бауман В. А. Механическое оборудование предприятий строительных материалов изделий и конструкций. – М.: Машиностроение 1981. – 324с.
Богданов В.С. Дмитриенко В.Г. Получение сверхтонкого мелового по- рошка в противоточных струйных мельницах. - Международная конференция. Ресурсо - и энергосберегающие технологии строительных материалов изделий и конструкций. Белгород 1995 ч.4165 с. 364 с.
Киркач Н.Ф. Баласанян Р.А. Расчет и проектирование деталей машин.
– Харьков 1991 – 273 с.
Кара-Сал Б.К. Биче-Оол Н.М. Повышение качества кирпича комбинированием составов глинистых пород Строительные материалы. 2006. № 2.- С.54-55.
деталировка.dwg

(Modell- oder Gesenk-Nr)
указанного особо. 2. Неуказанные радиусы 2мм. 3. Неуказанные предельные отклонения размеров: отаерстий Н14
кроме места указанного особо. 2. Неуказанные радиусы 2мм.
Предельные отклонения размеров отверстий Н14
Уклоны формовочные 3°. 2.Неуказанные радиусы 2 мм max. 3. Неуказанные предельные отклонения размеров: отверстий Н14
Радиусы скруглений 1
Привод шнекового полимеризатора
ось быстроходного вала редуктора
ось тихоходного вала редуктора
План размещения отверстий под фундаментные болты (1:5)
Техническая характеристика 1. Мощность электродвигателя
2. Частота вращения вала электродвигателя
обмин 1425 3. Общее передаточное число привода 38 4. Передаточное число редуктора 16 5. Крутящий момент на тихоходном валу
Н м 408 Технические требования. 1. Размеры для справок. 2. Допускаемая консольная нагрузка на быстроходный вал редуктора
Н 460 3. Допускаемые смещения валов редуктора и шнекового полимеризатора: Осевое
4. Полость цепной муфты заполнить смазкой Литол - 24 ГОСТ 21150-87. 5. Привод обкатать без нагрузки согласно программе испытаний.
Спецификация Общий вид.doc
Механизм прессования
Механизм исполнительный
ВПК 2112 У2 ступень 2
электрогидравлическим