Минипогрузчик




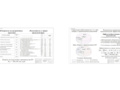
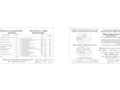
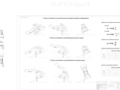
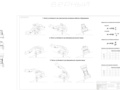
- Добавлен: 25.10.2022
- Размер: 2 MB
- Закачек: 1
Описание
Состав проекта
![]() |
![]() ![]() ![]() |
![]() ![]() ![]() |
![]() ![]() ![]() ![]() |
![]() ![]() ![]() |
![]() ![]() ![]() ![]() |
![]() ![]() ![]() |
![]() ![]() ![]() |
![]() ![]() ![]() |
![]() ![]() ![]() ![]() |
![]() ![]() ![]() ![]() |
![]() ![]() ![]() |
![]() ![]() ![]() ![]() |
![]() ![]() ![]() |
![]() ![]() ![]() ![]() |
![]() ![]() ![]() |
![]() ![]() ![]() ![]() |
![]() ![]() ![]() |
![]() ![]() ![]() ![]() |
![]() ![]() ![]() ![]() |
![]() ![]() ![]() ![]() |
![]() ![]() ![]() ![]() |
![]() ![]() ![]() ![]() |
![]() ![]() ![]() ![]() |
![]() ![]() ![]() |
![]() ![]() ![]() ![]() |
![]() ![]() ![]() ![]() |
![]() ![]() ![]() ![]() |
![]() ![]() ![]() ![]() |
![]() ![]() ![]() ![]() |
![]() ![]() ![]() ![]() |
![]() ![]() ![]() ![]() |
![]() ![]() ![]() |
![]() ![]() ![]() |
![]() ![]() ![]() ![]() |
![]() ![]() ![]() ![]() |
![]() ![]() ![]() ![]() |
Дополнительная информация
2.ИЧ ДИПЛОМ .doc
Малогабаритный погрузчик с бортовым поворотом предназначен:
- для механизации погрузочно-разгрузочных работ с грунтом I-VI категории
сыпучими и мелкокусковыми материалами как в обычных так и в стесненных
- транспортно-складских работ со штучными грузами;
- специальных работ: очистки от снега и грязи уборки отходов и др.;
Используется для эксплуатации в районах с умеренным климатом в диапазоне температур от -30°С до +40°С.
2 Описание и обоснование конструкции
В качестве источника энергии на погрузчике используется рядный 3х-цилиндровый дизель с жидкостным охлаждением. По сравнению с двигателем с искровым зажиганием дизель обладает следующими основными преимуществами:
- относительно высокий КПД (до 45%)
- высокая экономичность
- относительно низкая стоимость топлива
- более высокое значение крутящего момента на низких оборотах (тяговитость) что особенно важно при работе погрузчика.
К основным недостаткам использования дизельного двигателя можно отнести высокий уровень шума и вибрации а также трудности с пуском в холодное время года.
2.2 Ходовое оборудование
На проектируемой машине использован гидрообъемный привод колесного движителя. Колесная формула - 4x4. В качестве гидродвигателя выбран нерегули-руемый аксиально-поршневой гидромотор с наклонным блоком.
Крепление колес к раме - жесткое безрессорное. Компоновочная схема погруз-
чика включает в себя заднее расположение двигателя на сварной коробчатой раме в
лонжеронах которой размещаются гидрообъемная трансмиссия баки для топлива и
2.3. Рабочее оборудование.
К рабочему оборудованию проектируемой машины относятся многозвенная стрела и рабочий орган (ковш). Многозвенная стрела обеспечивает большую грузоподъемность большой вылет а следовательно и более высокий уровень безопасности работ.
Многозвенная стрела состоит из основания и 4х стержней. Основание имеет коробчатое сечение. Наклон стрелы осуществляется с помощью 2х гидроцилиндров двухстороннего действия с односторонним штоком. Поворот ковша осуществляется с помощью двух гидроцилиндров двухстороннего действия.
Крепление основания стрелы к раме машины и сменных рабочих органов к проушинам секции осуществляется с помощью пальцев.
Подшипники пары основание - секция смазываются пластичной смазкой.
2.4 Система управления
Управление перемещением машины.
Управление поворотом машины - бортовое. Управление скоростью движения машины осуществляется изменением подачи насоса (гидравлическая система с электрическим сервоприводом).
Управление рабочим оборудованием.
Изменение угла наклона стрелы осуществляется гидроцилиндрами двухстороннего действия с односторонним штоком. Управление - гидравлическое.
В механизме поворота ковша применена автоматическая следящая гидравлическая система работающая только при подъеме стрелы.
Рабочая тормозная система - тормоз на главном валу распределительного редуктора.
Стояночная тормозная система - механический тормоз на передние колеса.
2.5. Конструктивное исполнение кабины и рабочего пространства оператора.
Специфические особенности конструкции погрузчика.
Рабочее место оператора полностью соответствует международным стандартам защиты оператора при опрокидывании машины (Roll-over protective structures (ROPS)) и случайно падающих предметов (Falling objects protective structures (FOPS)) ИСО-34.711 ГОСТ 27714-88. Системы ROPS и FOPS объединены в одну конструкцию и выполнены заодно с кабиной.
Конструктивное исполнение кабины с учетом требований эргономики обеспечивает удобное положение оператора и хороший обзор.
Погрузчик оснащен искроулавливающим глушителем для обеспечения пожаро-безопасности при работе с легковоспламеняющимися грузами и в запыленных помещениях.
Для обеспечения свободного доступа при техническом обслуживании машины кабина и задняя панель капота выполнены откидными и фиксируются гидропневма-тическими амортизаторами.
Приборная панель содержит: часы лампы контроля фонарей безопасности хронометр индикатор грузового момента индикацию норм наработок между ТО а также приборы контроля систем дизеля и гидросистемы.
Для удобства посадки рулевая колонка выполнена откидной.
3 Описание процесса разрушения массива льда ударной нагрузкой.
При ударном приложение нагрузки характеризующемся передачей телу конечного количества движения за очень малый промежуток времени разрушение тел происходит чаще в результате упругой деформации поскольку пластические деформации не успевают развиться. Разрушение льда под действием ударной нагрузки при температуре ниже -2оС происходит в упругой области т.е. лед в условиях ударного нагружения можно считать хрупким телом. Процесс деформи-рования от момента соударения до момента разрушения льда можно расчленить на следующие этапы:
Первый этап – смятие льда под лезвием инструмента и образование контактной площадки. Происходит смятие неровностей поверхности льда и образование уплотненной зоны препятствующей дальнейшему свободному продвижению инструмента.
Второй этап – упругое взаимодействие разрушающего инструмента со льдом. Физической сущностью является создание напряженной зоны в массиве льда объем которого зависит от скорости продольной волны Vnр времени взаимодействия инструмента со льдом t и скорости поперечной волны Vnn. По мере внедрения инструмента происходит упругий прогиб его в месте контакта лезвия со льдом в результате чего появляются растягивающие напряжения вокруг контактного пятна инструмента.
Третий этап – частичное разрушение деформированного объема льда непосредственно под лезвием рабочего инструмента и на поверхности массива вокруг внедрившегося инструмента. Полный отрыв происходит после продвижения инструмента на глубину достаточную для эффективного воздействия на откалываемую часть льда.
Четвертый этап – откол от массива части объема льда ограниченной контуром сформировавшейся неравновесной трещины. Отрыв льда происходит в результате воздействия растягивающих напряжений создаваемых клиновым профилем ударного инструмента.
4 Свойства характеристики и особенности льда образующегося на
Лед является физическим телом со своеобразными свойствами. Своеобразие заключается в значительной изменчивости и полной зависимости от температуры и условий образования. Лед образующийся на дорожном покрытии имеет следующие особенности:
- имеет много примесей главным образом минерального состава.
- образование льда происходит при его интенсивном перемешивании а также при периодическом уплотнении колесами автотранспорта и пешеходами.
- имеет хаотическое структурообразование а величина сил его смерзания с дорожным покрытием зависит от состояния поверхности покрытие (шероховатость степень загрязнения) и температуры льда.
В работе имеют место следующие допущения:
- лед на дорожном покрытии в области температур от -2оС и ниже является хрупким упруго деформируемым телом с изотропными свойствами.
- при движении ударника к массиву потери энергии на преодоление сопротивле-ния воздуха отсутствует.
- отсутствует потери энергии на тепло звук разлет частиц сопровождающих процесс ударного взаимодействия инструмента со средой.
Физико-механические свойства льда образованного на дорожном покрытии городских улиц и площадей приведены в таблице 1.
Временное сопротивление
Увеличение скорости деформации приводит к снижению пределов прочности льда.
где А - эмпирический коэффициент (при -3оС А = 31; при ОоС А = 25).
S - скорость относительной деформации льда (00007 - 00417с).
Динамические характеристики льда (при t = -5 -10оС);
- модуль упругости Е= 7 * 10 3 МПа
- коэффициент Пуассона = 036
- скорость продольной волны Vпр. = 3000 мс
- скорость поперечной волны Vпп = 1700 мс
ПЧ ДИПЛОМ+ лит-ра.doc
Полную работу разрушения льда можно найти по следующей формуле:
где А1- работа упругой деформации инструмента.
А2- работа объемного сжатия локальной зоны льда под инструментом.
А3- работа расходуемая на отруб и сдвиг льда по контуру неравновесной трещины.
Для определения работы упругой деформации инструмента воспользуемся рис№1.
Рис№1. Схема к расчету работы деформации инструмента
Выделим элементарный слой dy находящийся на расстояние С от кромки лезвия инструмента. Энергия накопленная в элементарном слое высотой dy и площадью F определяется по формуле:
где у - напряжение в сечение ударника на расстояние у от лезвия Нсм2
Еg - динамический модуль упругости материала ударника
(для стали Еg = 2*105 Нсм2).
Напряжение в нижней границе элементарного объема при
Так как работа упругой деформации инструмента значительно меньше полной работы разрушения льда (А1 001А0) то ее в расчетах можно не учитывать.
Для определения потенциальной энергии упругой деформации льда при внедрение в него ударного инструмента воспользуемся известным положением теории упругости описывающий деформацию тела при сложном напряженном состоянии.
где 1 2 3 - напряжения на главных осях.
Процесс разрушения льда может протекать в случае преодоления сил упругости в зоне объемного напряжения. При этом изменение деформированного объема зависит лишь от суммы главных напряжений а не от их соотношения поэтому
так как 1 = 2 = 3 = сж то
где сж - напряжение сжатия льда Нсм2
Для нахождения объема напряженной зоны льда при ударном нагружении можно воспользоваться методом в основе которого лежит экспериментально подтвержденное положение о том что при соударение ударника с упругим полупространством объем напряженной зоны пропорционален времени контактного взаимодействия и скорости прохождения волн напряжений в нем. Упомянутый объем Vэ представляет собой часть эллипсоида
где t- продолжительность ударного взаимодействия (t = 7 * 10 -4c).
Для определения работы расходуемой на отруб и сдвиг льда по контуру неравновесной трещины воспользуемся рис№2.
Рис№2.Схема к расчету сил действующих на разрушающий инструмент
где Q- ударная сила.
N- реакция льда действующая перпендикулярно поверхности клина.
N'- сила сжатия скалываемого объема.
N"- сила отрыва скалываемого объема от массива.
Ударную силу находим следующим образом
где j' - угол трения стали по льду (j' = 0012-0015).
Следовательно можно считать что F~0 откуда имеем
Сопротивление разрушаемого объема сдвигу относительно массива льда
где Som- площадь вновь образованной поверхности отделяемого от массива куска льда
оm- предел прочности льда на отрыв
Scд- площадь контакта разрушаемого объема льда с дорожным покрытием
cд- предел прочности льда на сдвиг по плоскости дорожного покрытия
Найдем площадь вновь образованной поверхности
где h - предельная глубина внедрения в лед разрушающего инструмента см
H -высота слоя льда см
γ - угол скола льда град
- угол заточки рабочего инструмента ( = 27о)
l - шаг скола льда см
Площадь контакта разрушаемого объема льда с дорожным покрытием определяется следующим образом
где К1 – поправочный коэффициент (К1 = 115-12)
Сила сопротивления льда скалыванию
Отделения льда от массива происходит при условие т. е.
откуда необходимая ударная сила
где К - коэффициент учитывающий отклонение площади реальной поверхности отрыва льда от теоретической (К= 12)
Получаем что работа расходуемая на отруб и сдвиг льда по контуру неравновесной трещины равна
где hy - условная величина внедрения инструмента в момент скола льда
( hy = 0.815 * H0.52).
получаем полную работу разрушения льда
Необходимая для разрушения льда энергия удара зависит от: физико - механических свойств (сж ом сg g Еg ) скорости распространения в нем упругих волн напряжения (Vnn Vnp) параметров ударного инструмента (b H ) технологических параметров и режимов ( hy l) времени упругого взаимодействия инструмента со средой t .
Применительно к разрушению льда представляют интерес следующие выводы:
- энергоемкость процесса разрушения льда при динамическом нагружении выше
чем при статистическом. Применение динамического способа нагружения позволяет наилучшем образом использовать силовые агрегаты базового шасси обеспечить снижение расходов при разрушении снега и льда.
- существует оптимальная зависимость между величиной работы удара и толщиной льда. При увеличении запаса энергии больше необходимого для отделения нужного объема льда от массива энергоемкость процесса разрушения резко возрастает.
- изменение температуры льда оказывает настолько незначительное влияние на величину работы разрушения что в интервале от -2оС до -15оС ее колебания можно не учитывать.
Произведем расчет полной работы разрушения льда
сж=3МПа ом=2.4МПа сg=1.65МПа Еg=2*105Нсм2
g=0.36 Vnn =1700мс Vnp=3000мс t = 7*10-4c
= 27о К=1.2 К1=1.2 b=6cм
Полной работы разрушения куска льда шириной 6 см длиной 1 см высотой 1см равна:
Найдем работу одного ударника изображенного на рис№4. Необходимым условием разрушения куска льда шириной 6 см длиной 1 см высотой 1см является
Произведем расчет полной работы подводимой одним ударником.
Энергия которой обладает ударник перед ударом находится по формуле
где m - масса ударника кг
Vуд - окружная скорость центра масс ударника перед ударом мс
Массу ударника найдем воспользовавшись рис№3:
где ρ - плотность материала ударника (для стали ρ = 7.8 грсм3)
V - объем ударника см3
имеем V = 54cм3 отсюда m=54*7.8=420гр с учетом погрешности расчета объема ударника и наличием технологических отверстий и пазов примем m= 400гр
Найдем окружную скорость центра масс ударника перед ударом.
где n - частота вращения центрального вала щетки обмин
R - радиус от оси до центра масс ударника м
условие разрушение льда выполняется
Данный ударник позволяет откалывать лед толщиной 1см и шагом откола 1см с коэффициентом запаса энергии Кэ=1.13.
Определим поступательную скорость базовой машины с учетом эффективного
удаления льда с поверхности дорожного покрытия при размещении нескольких
ударников на одном диске щетки.
Частота вращения щетки n = 250 обмин = 4.16 обсек
Шаг скола l = 1 cмудар
Ширина захвата В = 120 см
Теоретические скорость перемещения машины и ее производительность в зависимости от количества ударников на одном диске указаны в таблице №1.
2 Расчет потребной мощности для выполнения работ по разрушению и уборки льда.
Потребная мощность определяется по формуле
N = Nтр+ Nскол+ Nпогр+ Nперем
где Nтр- мощность расходуемая на трение ворса щетки о поверхность дорожного покрытия.
Nскол- мощность необходимая для разрушения льда.
Nпогр- мощность необходимая для погрузки разрушенного льда в бункер.
Nперем- мощность расходуемая на перемещение машины вместе с бункером и рабочим оборудованием.
где Dщ- наружный диаметр щетки по ворсу м
fв- коэффициент трения ворса о дорогу (fв=03)
n- частота вращения щетки обмин (n=250)
Р- вертикальная реакция дороги на ворс Н
Определение реакции Р дороги под действием всех сил представляет большие трудности. Для упрощения задачи принимают следующие допущения:
Изгиб ворсинки рассматривают только под действием реакции дороги и
центробежных сил инерции. Силой тяжести ворсинки и силой трения ворса о
дорогу пренебрегают.
Ворсинка изгибается равномерно распределенной нагрузкой от инерционных
сил. Изменение распределенной нагрузки по длине ворсинки не учитывается.
Изгибающий момент от сил инерции изменяется по линейному закону.
Реакцию дороги находим по приближенной формуле
где Е-модуль упругости материала ворса (Е=25*105Нсм2)
J- момент инерции поперечного сечения прутка ворса (J= 3*103cм4)
Lo- свободная длина прутка ворса щетки см
DLо- радиальная деформация ворса щетки см
iкон- количество ворса находящегося в контакте с дорожным покрытием
а- коэффициент пропорциональности (а=018)
Vщ- окружная скорость щетки (при n=250обмин Vщ=786мс)
Rщ- радиус щетки по ворсу см
теперь найдем мощность расходуемую на трение ворса щетки о поверхность дорожного покрытия.
Мощность необходимая для разрушения объема льда за 1 сек.
Объем льда который убирает машина за 1 сек. равен
где b- ширина захвата щетки (b=120см)
h- толщина льда (h=1см)
Vмаш- поступательная скорость машины (при 8 ударниках Vмаш=3328 смс)
Для разрушения необходимо энергии . Составим
пропорцию и найдем количество энергии необходимой для разрушения . Получаем .
Мощность необходимая для разрушения льда за 1секунду равна
Мощность необходимая для погрузки разрушенного льда в бункер определяется по формуле
где mсльда- масса льда погружаемая в бункер за 1 сек.
g- ускорение свободного падения (g=981мс2)
h- высота на которую необходимо поднять лед для погрузки в бункер (h=30cм).
Ктр- коэффициент трения льда о сталь (Ктр=025)
S- длина дуги периферии по которой перемещается разрушенный лед до попадания в бункер ().
- к.п.д. подъема разрушенного льда в бункер (=09)
Найдем массу льда убираемую за 1 сек.
где ρльда- плотность льда (ρльда=09грсм3)
Находим мощность необходимую для погрузки разрушенного льда в бункер
Мощность расходуемая на перемещение машины вместе с бункером и рабочим оборудованием определяется по формуле
где m- полная масса машины вместе с полностью заполненным бункером кг
fкач- коэффициент сопротивления перекатыванию машины (fкач=002)
i- уклон местности (i=0)
- к.п.д. передачи от двигателя к ведущим колесам ( =08)
Для определения мощности нам необходимо знать полную массу машины вместе с полностью заполненным бункером.
где mмаш- масса погрузчика
mльда- масса льда находящегося в бункере
mмет- масса металлоконструкции бункера и рабочего органа
Mасса погрузчика mмаш = 3100кг.
Для нахождения массы льда и массы металлоконструкции воспользуемся рис№4.
Найдем полезный объем бункера:
Vбун = 75* 96 * 65 + 20 * 65 * 113 + 130 * 65 * 25 = 083м3
где Кзап- коэффициент заполнения бункера (Кзап= 1.2)
Рис№4. Рабочее оборудование снегоуборщика
Краз- коэффициент разрыхления льда при удаление его с дорожного покрытия (Краз= 1.15)
Масса металлоконструкции mмет = mщет + mбунк
где mщет- масса щетки (mщет = 140кг)
mбунк- масса бункера
Найдем массу бункера по формуле
где Vмет.бун- объем металла необходимый для изготовления бункера
ρст- плотность стали (ρст= 78грсм3)
Ккомп- коэффициент показывающий увеличение массы конструкции при сборке и сварки основных элементов (Ккомп=11)
при толщине стенки равной 6 мм.
Получаем массу бункера отсюда находим массу
всей машины целиком
Найдем мощность необходимую для перемещения машины вместе с бункером и
рабочим оборудованием отсюда
находим потребную мощность для уборки снега со льдом
N = 943 + 717 + 167 + 343 = 217кВт
Максимальная мощность развиваемая погрузчиком равна 465кВт т.е. условие работоспособности выполняется 217кВт 465кВт.
3 Проверка элементов гидравлики на работоспособность при выполнении работ по
Проверять прежде всего будем работоспособность гидроцилиндров подъема
так как для того чтобы разгрузить бункер нужно поднять его на некоторую высоту.
Задача проверки заключается в следующем:
- определить массу всего навесного оборудования вместе со льдом находящимся в нем.
- определить смогут ли гидроцилиндры подъема поднять это навесное оборудование.
Массу всего навесного оборудования вместе со льдом найдем по формуле
Массы mльда и mмет определялись ранее: и
Масса щетки известна из справочника: .
Находим массу всего навесного оборудования вместе со льдом
Согласно техническим характеристикам погрузчика его номинальная грузоподъемность равна 1100кг.
Следовательно можно сделать вывод что масса данного навесного оборудования с полностью заполненным бункером не превышает технических возможностей погрузчика.
Работа погрузчика совершается в номинальном режиме что никак не повлияет на работоспособность гидроцилиндров подъема.
Установка данного навесного оборудования не потребует замены или регулировки уже установленных элементов гидравлики.
Данное навесное оборудование является сменным рабочим оборудованием погрузчика.
4 Расчет на прочность.
При выполнении работ по уборки снега с дорожного покрытия погрузчик может встретиться с рядом препятствий:
- столкновение рабочим оборудованием с дорожным бордюром;
- столкновение с элементами городской канализационной системы;
- столкновение с ограждением и т. п.
Снегоуборочная щетка меньше всего подвержена столкновению с какими-либо препятствиями. Чаще всего с препятствием встречается металлоконструкция бункера. Поэтому рассмотрим какие напряжения возникнут в нижней балке бункера при встрече с непреодолимым препятствием (рис.№5). Сила Р действует на некотором расстояние Z от боковой стенки бункера. Задача состоит в том чтобы определить место приложения силы при котором возникает максимальный изгибающий момент в балке.
Расчет будем вести как для статически неопределимой балки. Воспользуемся
методом канонических уравнений.
Рис№5. Схема приложения непреодолимой силы к нижней балке бункера.
Рис№6. Эпюры моментов от единичных сил.
Составим систему канонических уравнений:
Находим с помощью (рис.№7) значения dij.
Подставим значения dij в систему канонических уравнений.
Определим закон изменения величины изгибающего момента в зависимости от координаты приложения силы Р. Для этого определим основные расчетные положения:
Рис№7. Основные расчетные положения
Положение 1: правая заделка
Положение 2: левая заделка
Положение 3: промежуточное положение.
Расчет для положения 1:
Найдем экстремумы функции: откуда
Рис№8. Закон изменения изгибающего момента в правой заделке
в зависимости от координаты приложения силы Р=1
Расчет для положения 2:
Рис№9. Закон изменения изгибающего момента в левой заделке
Расчет для положения 3:
Рис№10. Закон изменения изгибающего момента в промежуточном положение
Все предыдущие расчеты были для силы Р = 1. Определим характер изменения величины силы Р в зависимости от координаты ее приложения.
Рис№11. Схема к расчету силы Рмах.
Исходными данными для расчета силы тяги являются:
Вес базовой машины 31000Н
Мощность базовой машины 465кВт
Продольнаяпоперечная база 1112м
Коэф-ты сцепления колес в продольномпоперечном направлениях 0806
Получаем Рмах = 24.8кН.
Построим характеристику изменения значения силы Р в зависимости от координаты приложения ее к расчетной балке Z (см. рис.№5)
Результаты расчетов запишем в виде табл.№2.
Нас интересуют максимальные значения возникающих изгибающих моментов.
Найдем абсолютные значения моментов в тех координатах в которых они максимальны.
Из условия прочности учитывая что момент инерции
где b - основание балки треугольного сечения
[]p - предел прочности (160МПа).
Возможны различные варианты значений b и h главное чтобы выполнялось условие прочности. Принимаем bмин = 15cм hмин = 7cм (bh2 = 735cм3).
ПРАДМ 1.dwg

Зубья цементировать h=1
сердцевина зубьев 32 46 HRC
Маркировать на торце обода m=5; z=20.
Неуказанные допуски по h14
ДИП.МП.00.01.000.ТЧ.ВО.
ДИП.МП.00.00.000.ТЧ.ВО.
ДИП.МП.00.03.000.ТЧ.ВО.
ДИП.МП.00.02.000.ТЧ.ВО.
3.ТЧ ДИПЛОМ .doc
1.1. Разработка технологической карты.
Установление состава и рациональной последовательности переходов в операции.
При выборе рациональной последовательности переходов исходим из принципа максимальной концентрации операций то есть в одной операции должно быть выполнено максимальное число переходов.
Установить и снять деталь.
Сверлильная операция.
Фрезерная операция.
Термическая операция
Шлифовальная операция.
Контрольная операция
1.2. Определение межоперационных припусков и допусков.
Существуют два метода определения припусков:
расчетно-аналитический
статический (табличный).
В работе используем табличный метод расчета припусков. Припуски определяем по таблицам в зависимости от способа получения заготовки ее материала веса и конфигурации а также способа механической обработки.
Межоперационные допуски также определяем по таблицам в зависимости от метода обеспечения точности.
В ремонтном производстве применяются следующие виды заготовок:
отливки (чугунные и из цветных металлов);
сортовой материал (из стали и цветных металлов) – прокат.
Расчет нормального припуска на изготовление производится по формуле:
Z = Z1 + Z2 + Z3 + Z4 + d мм
где Z1 – размер припуска на черновую обработку в мм на диаметр;
Z2 – размер припуска на получистовую обработку в мм на диаметр;
Z3 – размер припуска на чистовую обработку в мм на диаметр;
Z4 – размер припуска на доводку в мм на диаметр;
d – допуск на заготовку в мм.
d = (03 04)(Z1 + Z2 + Z3 + Z4) мм
Припуски на диаметр 1169 мм: Z1 = 2мм; Z2 = 15мм; Z3 = 05мм.
d = (03 04)(2 + 15 + 05) = 12 16 мм
Z = 2 + 15 + 05 + 12 = 54мм
Принимаем размер болванки: диаметр 120мм ширина 40мм.
1.3. Определение режимов обработки.
Режимы резания должны обеспечивать наибольшую производительность труда и наименьшую стоимость операции.
Глубину резания рекомендуется принимать как можно больше соответственно глубине срезаемого припуска на один проход. При чистовой обработке глубина резания определяется в зависимости от степени точности и требуемой шероховатости поверхности.
Подача определяется в зависимости от материала и размеров обрабатываемой поверхности жесткости системы СПИД требуемой точности и шероховатости обрабатываемой поверхности. Рекомендуется принимать большую подачу.
Скорость резания определяется в зависимости от:
обрабатываемого материала и его механических свойств
выбранных глубины резания и подачи
характера обработки и геометрии режущего инструмента с учетом поправочных коэффициентов на измененные условия работы.
Режущий инструмент – резцы Т5 К10 ГОСТ 22736-77
измерительный инструмент – штангенциркуль ШЦ-П ГОСТ 166-80.
Вспомогательное время на установку и снятие детали вспомогательное время на проход основное время на токарную обработку - берутся из таблиц.
Дополнительное время на токарные работы составляет 8% от оперативного времени. Оперативное время рассчитывается по формуле:
где То – основное время мин;
Тв – сумма вспомогательного времени на установку и на проход мин.
По таблице определяем вспомогательное время на установку (в самоцентри-рующем патроне без выверки ) и снятие заготовки: Tв = 035мин.
Операции выполняется на токарно-винторезном станке нормальной точности с
самоцентрирующимся пневматическим патроном (16К20) проходным резцом с пластиной из твёрдого сплава ВК6 размерами 16х25. Выбор установочных и технологических баз осуществляется согласно ГОСТ 21495-76. В нашем случае в качестве установочных баз используются цилиндрическая поверхность с наибольшей длиной и диаметром: диаметр d = 1169-022 мм по IT 7 длина 33-025 мм.
Используемый станок 16К20 имеет трёхкулачковый самоцентрирующийся пневматический патрон. Для установки в центрах используется торцевая поверхность диаметр 1169-022 мм.
Переход 1. Точение поверхности шестерни.
Глубина резания: t = (120 - 1169) 2 = 155мм
t1 = 125мм – черновое точение при этом рекомендуется подача S1 = 08 12 ммоб принимаем S1 = 1 ммоб (для снижения времени выполнения процесса)
t2 = 03мм – чистовое точение при этом рекомендуется подача S2 = 015 025 ммоб принимаем S2 = 02 ммоб.
При известной стойкости резца (1 час) и подаче выбираем скорости резания:
V1 = 56 ммин V2 = 101ммин.
Частота вращения детали:
Корректируем по паспортным данным станка: n1 = 200 обмин;
Уточняем скорость резания
Техническую норму штучно - калькуляционного времени можно определить по формуле:
где tо – основное время мин;
tв – вспомогательное время мин;
aобс. – доля времени приходящаяся на обслуживание рабочего места %;
aот.л. – доля времени приходящаяся на отдых и личные нужды персонала %;
tп-з – подготовительно - заключительное время (для партии деталей
n – объём партии деталей принимаем партию 50 шт.
Основное (технологическое) время:
где L – длина рабочего хода инструмента мм;
i – число проходов инструмента (обработка за один проход).
По ремонтному чертежу детали: L = 20мм.
Вспомогательное время включает в себя ряд составляющих:
где tв1 – вспомогательное время на установку снятие и поворот детали;
tв2 – вспомогательное время связанное с выполнением основного перехода;
tв3 – вспомогательное время на измерение обрабатываемой поверхности.
По таблицам с нормами времени выбираем:
tв1 = (035 + 012) = 047 мин;
Доля времени на обслуживание рабочего места – 35%.
Доля времени на отдых и личные нужды – 6%.
Переход 2. Точение торца шестерни.
Операция выполняется том же станке (16К20) подрезным правым резцом с пластиной из твёрдого сплава ВК6 размерами 16х25.
Глубина резания t = 3 мм – черновое точение при этом рекомендуется подача
S = 016 028 ммоб принимаем S = 026 ммоб (для снижения времени
выполнения процесса).
При известной стойкости резца (1 час) и подаче выбираем скорость резания V = 49 ммин поправочный коэффициент: Kd = 096; V = 49 * 096 = 47 ммин.
Корректируем по паспортным данным станка: n = 200 обмин
Уточняем скорость резания:
где tо – основное время мин;
tп-з – подготовительно-заключительное время (для партии - 15 мин);
По ремонтному чертежу детали L = 118 2 = 59 мм (в радиальном направлении).
Доля времени на обслуживание рабочего места – 35%;
Переход 3. Точение поверхности.
Глубина резания: t = (1169 - 80) 2 = 1845 мм.
Принимаем t = 15 мм – черновое точение при этом рекомендуется подача S = 016 028 ммоб принимаем S = 026 ммоб (для снижения времени выполнения процесса) и t = 345 мм – черновое точение при этом рекомендуется подача S = 016 028 ммоб принимаем S = 026 ммоб (для снижения времени выполнения процесса).
V = 49 ммин поправочный коэффициент: Kd = 096; V = 49 * 096 = 47 ммин.
tп-з – подготовительно-заключительное время (для партии - 15мин);
где L – длина рабочего хода инструмента мм
По ремонтному чертежу детали: L = (1169 - 80) 2 = 1845 мм (в радиальном направлении).
tв1 = 035 + 012 = 047 мин;
Доля времени на обслуживание рабочего места – 35%
Доля времени на отдых и личные нужды – 6%;
Переход 4. Точение фаски вала.
Операция выполняется на том же (16К20) подрезным резцом с пластиной из твёрдого сплава ВК6 размерами 16х25. Выбор установочных и технологических баз осуществляется согласно ГОСТ 21495-76. Фаска 2х450. Глубина резания t = 2 мм при этом рекомендуется подача S = 025 ммоб.
Рекомендуемая скорость резания: V = 101ммин.
Частота вращения шпинделя станка:
Корректируем по паспортным данным станка: n = 300 обмин
Техническую норму штучно - калькуляционного времени можно определить по
i – число проходов инструмента (обработка за один проход).
По ремонтному чертежу детали: L = 2мм (размер фаски).
Вспомогательное время определяем сразу для двух сторон вала.
Техническая норма штучно - калькуляционного времени:
Общее время выполнения токарной операции составляет сумму штучно-калькуляционного времени на выполнение операций: точения поверхности торца и фаски шестерни составляет: Т6 = 145 + 19 + 13 + 068 = 533 мин.
Сверлильная операция.
Выполняется на вертикально - сверлильном станке многошпиндельном с раздвижными шпинделями (041222) - 2М150. Проходит в два этапа: сверление и рассверливание. Режущий инструмент – сверла: Dс = 10 мм и Dр = 50 мм.
Глубина сверления: t = 35 мм.
Подача: S = 0 2 ммоб.
Частота вращения: n = 125 обмин.
где tо – основное время мин.
tв – вспомогательное время мин.
aобс . – доля времени приходящаяся на обслуживание рабочего места %
aот.л. – доля времени приходящаяся на отдых и личные нужды персонала %
По ремонтному чертежу детали: L = 40мм.
где tв1 – вспомогательное время на установку снятие и поворот детали
tв2 – вспомогательное время связанное с выполнением основного перехода
tв3 – вспомогательное время на измерение обрабатываемой поверхности
tв1 = 025 + 015 = 04 мин;
Рассверливание отверстия:
Подача: S = 02 ммоб.
Общее время сверления составляет сумму штучно-калькуляционного и вспомогательного времени на установку и снятие детали которое равно 025 и включено в предыдущую формулу поэтому:
T6 = tшк1 + tшк2 = 265 + 228 = 493 мин.
Режущий инструмент – резцы Т5 К10 ГОСТ 22736-77 измерительный инструмент – штангенциркуль ШЦ-П ГОСТ 166-80.
Вспомогательное время на установку и снятие детали вспомогательное время на проход основное время на токарную обработку – берутся из таблиц.
Дополнительное время на токарные работы составляет 8% от оперативного времени.
Оперативное время рассчитывается по формуле:
По таблице определяем вспомогательное время на установку (в самоцентри-рующем патроне без выверки) и снятие заготовки: Tв = 035мм.
Операции выполняется на токарно-винторезном станке нормальной точности с самоцентрирующимся пневматическим патроном 16К20 проходным резцом с пластиной из твёрдого сплава ВК6 размерами 16х25. Выбор установочных и технологических баз осуществляется согласно ГОСТ 21495-76. В нашем случае в качестве установочных баз используются цилиндрическая поверхность с наибольшей длинной и просверленным отверстием диаметром d = 50-03 мм по IT 9 длина 33-025 мм. Используемый станок 16К20 имеет трёхкулачковый самоцентри-рующийся пневматический патрон. Для установки в центрах используется торцевая поверхность и диаметр 50-03 мм.
Глубина резания t = (120 - 1169) 2 = 155мм.
t1 = 125мм – черновое точение при этом рекомендуется подача S1 = 08 12 ммоб принимаем S1 = 1 ммоб (для снижения времени выполнения процесса).
t2 = 03мм – чистовое точение при этом рекомендуется подача S2 = 015 025 ммоб принимаем S2 = 02 ммоб.
V1 = 56 ммин; V2 = 101ммин.
Корректируем по паспортным данным станка: n1 = 200 обмин; n2 = 300 обмин.
tп-з – подготовительно - заключительное время (для партии - 15мин);
По ремонтному чертежу детали L = 20мм.
Глубина резания t = 4мм. Черновое точение при этом рекомендуется подача S = 016 028ммоб принимаем S =026 ммоб (для снижения времени выполнения процесса).
V = 49 ммин поправочный коэффициент: Kd = 096; V =49 * 096 = 47 ммин.
Корректируем по паспортным данным станка: n = 200 обмин.
Техническую норму штучно-калькуляционного времени можно определить по формуле:
По ремонтному чертежу детали L = 118 2 = 59мм (в радиальном направлении).
Переход 3. Точение торца шестерни.
Глубина резания t = 16мм – черновое точение при этом рекомендуется подача S = 016 028ммоб принимаем S = 026 ммоб (для снижения времени выполнения процесса).
По ремонтному чертежу детали L = (1169 - 80) 2 = 1845 мм (в радиальном направлении)
Операция выполняется на том же (16К20) подрезным резцом с пластиной из твёрдого сплава ВК6 размерами 16х25. Выбор установочных и технологических баз осуществляется согласно ГОСТ 21495-76. Фаска 2х450. Глубина резания t = 15 мм при этом рекомендуется подача S = 025 ммоб.
Корректируем по паспортным данным станка: n = 315 обмин
Переход 5. Точение торца шестерни.
Частота вращения детали;
По ремонтному чертежу детали: L = (64 - 50) 2 = 7 мм (в радиальном
Переход 6. Точение фаски вала.
Рекомендуется скорости резания: V = 101ммин.
По ремонтному чертежу детали: L = 2 мм (размер фаски).
По таблицам выбираем: tв1 = (035 + 012) = 047 мин;
Техническая норма штучно-калькуляционного времени:
Общее время выполнения токарной операции составляет сумму штучно-калькуляционного времени на выполнение операций: точения поверхности торца и фаски шестерни составляет:
Т6 = 1176 + 224 + 1367 + 1006 + 1126 + 1006 = 7921 мин
Протяжная операция выполняется на протяжном станке.
Скорость протяжки: V = 05мс
где L – длина протяжки мм;
V- скорость протяжки ммс
По справочнику – длина протяжки: L = 620мм длина обрабатываемого отверстия: L = 31 мм.
Общее время на протяжную операцию: T = 234 мин.
Фрезерная операция. Нарезание зубьев
Конструкция и размеры фрезы выбираются в зависимости от размеров обрабатываемой поверхности конструктивных размеров и формы деталей. Фрезы меньшего диаметра являются более производительными. При черновом фрезеровании определяется подача на зуб Sz.
Выбираем дисковую фрезу с пластинами из твёрдого сплава Т15К6. Диаметр 100 мм с режущими кромками для нарезания прямых зубьев зубчатых колес число зубьев Z = 21. Длина обработки равна ширине зуба: L = 30 мм. Подача определяется по таблицам. При мощности станка 5-10 кВт средней жёсткости системы СПИД обрабатываемом материале – сталь глубине резания t > 10мм рекомендуемая подача Sм = 340 - 360 мммин принимаем S = 360 мммин. Частота вращения фрезы n = 102 обмин. Поправочный коэффициент от марки твёрдого сплава Ки = 094.
Подача на зуб: Sz = Sм (Z * n) = 360 (21 * 102) = 016 ммзуб.
где В – ширина зуба мм
По ремонтному чертежу детали: В = 30мм.
Общее время необходимое на нарезание зубьев шестерни: Т8 = 427 мин.
Термическая операция.
Операция выполняется на круглошлифовальном универсальном станке 3А141.
Необходимо обработать рабочие поверхности зубьев шестерни. Наиболее целесообразно обработать их с одного установа одним инструментом.
Шлифовальный диск диаметром 250 мм мягкий зернистость Rшк = 40 80.
Окружная скорость круга 18 мсек.
Частота вращения шлифовального круга:
Sм- подача (120 мммин).
Общее время выделяемое на шлифовальную операцию составляет: Т = 134 мин.
Контрольная операция.
Данный контроль выполняется на последней стадии изготовления шестерни. Проверяется соответствие размеров требованиям ТД и РД отсутствие дефектов которые могут возникнуть при технологических операциях.
В данной операции используются: микрометр штангенциркуль с точностью до 005 мм калибр-скоба.
На данную операцию отводится Т = 09 минут на одну деталь.
Основное время нахождения деталей в ваннах (время наращивания металла):
где h - толщина слоя покрытия h = 025мм
γ - плотность осаждаемого хрома g = 69 гсм3
Рк - катодная плотность тока Адм2
С - электрохимический эквивалент гАч;
Хромирование выполняется при постоянном токе (нереверсивном) в самореге-лирующемся электролите состава №3 при катодной плотности тока Рк = Ра = 80 Адм2 значении электрохимического эквивалента С = 0324 гАч температуре электролита t = 45 70 0С и выходе по току = 18%;
Вспомогательное время определяется по формуле:
где tв1 - вспомогательное время перекрывающееся основным временем
tв2 - вспомогательное время не перекрывающееся основным временем
Перекрываемое вспомогательное время затрачивается на такие работы как монтаж детали на приспособление изоляция мест не подвергающихся обработке. Эти работы выполняются в период работы гальванической ванны и в расчёт не включаются.
Неперекрываемое время затрачивается на работы выполняемые при неработающей гальванической ванне на загрузку и выгрузку деталей из ванны и другие вспомогательные операции. Неперекрываемое вспомогательное время включается в норму времени на операцию.
Подготовительно - заключительное время при обслуживании одной ванны полностью перекрывается основным временем и поэтому в норму времени на операцию не входит. При обслуживании рабочим двух и более ванн дополнительное время принимается равным 12% от суммы основного и неперекрываемого вспомогательного времени. Подготовительно - заключительное время принимается равным 7 10 мин на партию деталей (в нашем случае партия составляет 50 шт.).
По таблицам с нормами времени выбираем: tв2 = 021мин
Норма времени на операцию отнесённая к одной детали:
где m - количество деталей загружаемых в одну ванну одновременно;
n - количество деталей в партии.
ПРАДМ 2_.dwg

ДИП.МП.00.05.000.ТЧ.ВО.
ДИП.МП.00.07.000.ТЧ.ВО.
ДИП.МП.00.06.000.ТЧ.ВО.
СПЕЦ3наСТРЕЛА.doc
ДИП.МП.01.000.01.ПЧ.ВО.
ДИП.МП.01.000.02.ПЧ.ВО.
ДИП.МП.01.000.03.ПЧ.ВО.
ДИП.МП.01.000.04.ПЧ.ВО.
ДИП.МП.01.000.05.ПЧ.ВО.
ДИП.МП.01.000.06.ПЧ.ВО.
ДИП.МП.01.000.07.ПЧ.ВО.
ДИП.МП.01.000.08.ПЧ.ВО.
ДИП.МП.01.000.09.ПЧ.ВО.
ДИП.МП.01.000.10.ПЧ.ВО.
ДИП.МП.01.000.11.ПЧ.ВО.
ДИП.МП.01.000.12.ПЧ.ВО.
ДИП.МП.01.000.13.ПЧ.ВО.
ДИП.МП.01.000.14.ПЧ.ВО.
ДИП.МП.01.000.15.ПЧ.ВО.
СПЕЦ1наОВ.doc
ДИП.МП.01.00.000.ПЧ.ВО.
ДИП.МП.02.00.000.ПЧ.ВО.
Гидроцилиндр подъема
ДИП.МП.03.00.000.ПЧ.ВО.
ДИП.МП.04.00.000.ПЧ.ВО.
ДИП.МП.05.00.000.ПЧ.ВО.
Рабочее оборудование
Экономика ДИПЛОМ .doc
1. Краткое описание проекта
Предлагается к рассмотрению проект модернизации малогабаритной уборочной машины. Машина предназначена для уборки снега и льда с тротуаров. Целью данной разработки является определение необходимого комплекта оборудования для выполнения этого вида работ.
В задачи проекта входило:
- разработка конструкции металлической щётки и способа её крепления
- установление способа удаления льда или снега от рабочего органа
- подбор системы привода рабочего органа.
Основное внимание в проекте уделяется улучшению качества уборки тротуа-ров снижению загрязнения окружающей среды и загрязнения общественного транспорта за счёт уменьшения или полного устранения потребления химических реагентов снижению издержек по уборке тротуаров в осенне-зимний период.
Основными социально-экономическими результатами использования предлагаемого метода должно стать снижение травматизма в зимнее время за счёт своевременной уборки снега и наледи с тротуаров улучшение внешнего вида столичных тротуаров уменьшение потребления химических реактивов.
Сумма инвестиций на разработку проекта равна 50273 руб. Размер инвестиций на переоборудование предприятия для изготовления машины с новой щёткой составляет 709356 тыс. руб. Цена базовой машины – погрузчика универсального малогабаритного без модернизации - 230 тыс. руб. (данные УВК-МАДИ (ГТУ)). Цена предлагаемой конструкции щётки – 4 тыс. руб. цена устройства для отвода снега – 18 тыс. руб.. Цена погрузчика с новой щёткой составит 269263 тыс. руб.. Капитальные вложения потребителя на приобретение доставку машины и строительство необходимых площадей для хранения машины – 40389 тыс. руб. Применяемые сегодня для аналогичных целей щётки не обеспечи-вают необходимого уровня качества уборки и имеют цену 107 тыс. руб. Себестоимость уборки одного м2 тротуара с использованием предлагаемой щётки составит по предварительным расчётам 012 руб. Себестоимость уборки одного м2
тротуара с использованием химических реагентов составляет 368 руб.
Величина чистого дисконтированного дохода за два года расчётного периода получилась равной 6.866 млн. руб.
2. Описание текущей ситуации на рынке погрузчиков
Парк погрузо-разгрузочных машин в настоящее время формируется с учетом воздействия структурных сдвигов в строительстве которые приводят к изменениям в спросе на технику для этого вида работ. Особенно вырастает потребность в многофункциональной технике индивидуального или бригадного пользования а также в малогабаритной технике выполняющей различные виды работ при уборке городов. Кроме того переход к новой структуре малообъемных работ определяют спрос на строительную и погрузочную технику средней и малой мощности. Таким образом парк дорожно-строительных машин должен обновляться и существенно видоизменяться.
Наиболее вероятными источниками финансирования обновления и переоснащения активной части основных фондов строительного комплекса являются амортизационные отчисления и собственная прибыль строительных организаций а также заемные средства и средства заказчиков. Однако в настоящее время инвестиционная активность невысока. Поэтому существенных изменений в производстве и закупке строительной техники не происходит. К сожалению отечественные производители продолжают по-прежнему ориентироваться на выпуск мощной техники не обеспечивая удовлетворения потребности в технике для небольших строительных объектов.
До 1999 г. на протяжении длительного периода в России наблюдался спад производства строительно-дорожного машиностроения. Ежегодно индексы физических объемов производства относительно предшествующих периодов сокращались на 15-20 %. Это объяснялось как спадом общего спроса на продукцию машиностроения ввиду отсутствия средств у основных покупателей так и низким курсом доллара относительно отечественного рубля что влияло на объемы продаж отечественной продукции проигрывавшей в конкурентоспособности зарубежным аналогам. Поэтому при строительстве новых и реконструкции старых автомобиль-ных дорог при механизации погрузочно-разгрузочных работ предпочтение отдавалось импортной строительно-дорожной технике. Тратя большие средства на их закупку потребитель получал выгоду за счет лучших технических характерис-тик и эксплуатационной надежности зарубежных аналогов. Но после финансового кризиса 1998 г. основные покупатели вынуждены были переориентироваться на закупку отечественных машин и оборудования. В связи с оживлением в последние годы объёмов производства и строительства можно предположить увеличение спроса на отечественную продукцию и в будущих периодах. К тому же положительную роль играет все большее понимание необходимости поддержки отечественных производителей а также социально-экономическая задача Правительства по увеличению в 2 раза валового внутреннего продукта. Спрос на погрузчики определяется состоянием действующего парка этих машин в государственном и частном секторах России.
Наличный парк ДСМ до середины 1999г. ежегодно сокращался на 6-8 % за счет увеличения износа и недостаточной замены выбывающих машин на новые. Однако с 1999 г. наблюдается меньшее сокращение наличного парка за счет увеличения закупок у отечественных производителей что способствовало увеличению объёмов их производства и оживлению рынка в России.
Объем продаж отечественных погрузчиков в России так же как и объём производства был до 1998 г. относительно стабильным но в 1998 г. резкий спад платежеспособного спроса повлиял на него очень негативно. Тем не менее в 1999 г. наблюдалось постепенное увеличение спроса и на этот вид дорожно-строительной техники.
3. Основные задачи проекта
Деятельность Российских предприятий и организаций в условиях конкурен-ции на внутреннем рынке и на внешних рынках связана с множеством проблем и преодолением большого числа трудностей. Во многом эти трудности связаны с отставанием российских систем стандартизации и сертификации от мирового уровня. В течение небольшого периода времени в нашей стране были проведены достаточно серьезные мероприятия по совершенствованию в области стандарти-зации и сертификации. Они повлекли за собой заметные положительные сдвиги в деятельности предприятий и организаций. Воплощаемая в настоящее время в жизнь новая концепция стандартизации позволит приблизить Россию к вступле-нию во Всемирную торговую организацию (ВТО). За последние годы значительно пересмотрены основные аспекты и правила сертификации расширены области её применения. Сертификации подвергаются не только продукция и производство но также услуги в том числе и коммунальные. Поэтому разработка новых методов уборки тротуаров и модернизация применяемой для этих целей техники являются важными задачами сегодняшнего этапа развития сертификации в нашей стране.
Данный проект преследует цель совершенствования методов уборки тротуаров в осенне-зимний период на основе модернизации применяемых для этих целей машин. В качестве объекта модернизации выбран универсальный малогабаритный погрузчик на который предлагается установить щётку для уборки льда и снега. Для достижения этой цели в проекте были поставлены и решены следующие задачи.
Рассмотрены основные параметры существующих машин для уборки снега конструкции применяемых щёток.
Разработана схема расположения щётки.
Разработана схема привода щётки.
Разработана конструкция металлической щётки.
Разработана методика отвода снега от рабочего органа и конструкция механизма отвода.
Разработана методика проведения испытаний.
Разработаны меры по обеспечению безопасности.
Разработана инструкция установки и обслуживания щётки в разные периоды года.
Осуществлена экономическая оценка проекта. В процессе экономической оценки проекта были решены следующие задачи:
- рассчитаны издержки на разработку проекта;
- определена себестоимость изготовления щётки;
- рассчитана себестоимость очистки тротуара от снега с применением реагентов и малой уборочной машины;
- проведена оценка показателей эффективности.
4.Определение издержек связанных с разработкой проекта
При проведении расчётов результаты округлялись до целого числа.
Состав издержек на разработку проекта.
Издержки на разработку проекта включают в себя следующие статьи:
FCзр– затраты на оплату труда исполнителей руб.;
FCесн – единый социальный налог на оплату труда исполнителей руб.;
FCмр – затраты на материалы покупные изделия руб.;
FCэр – затраты на электроэнергию руб.;
FCз ауп – затраты на оплату труда административно-управленческого вспомогательного и обслуживающего персонала (АУП и ВОП) руб.;
FCесн ауп – единый социальный налог на оплату труда административно-управленческого вспомогательного и обслуживающего персонала руб.;
FCАР – амортизационные отчисления руб.;
FСпр.н. – прочие накладные расходы руб.;
FCк.ан – контрагенские расходы руб.
Затраты на оплату труда исполнителей
СД – среднедневная ставка заработной платы руб.дн.(принимаем 2308 руб.)
– трудоемкость выполненной j-ой работы ч.-дн. (см. табл. .1)
– коэффициент учитывающий дополнительную заработную плату.
Составим перечень работ в соответствии с задачами решёнными в проекте и запишем его в табл. 1.
Оценка продолжительности и трудоемкости работ.
Продолжительность и трудоемкость выполняемых работ были определены опытным путем на основе трудоёмкости выполнения аналогичных работ.
Состав трудоемкость и продолжительность работ.
Количество исполнителей чел.
Обоснование необходимости модернизации и составление технического задания
Выбор и разработка схемы
Разработка схемы привода щётки
Разработка конструкции щётки
Разработка методики отвода льда методики проведения испытаний
Определение издержек связанных с разработкой проекта. Расчёт себестоимости очистки и оценка показателей эффективности.
Разработка мер по обеспечению безопасности
Разработка инструкций
Пример расчета затрат на заработную плату для исполнителей 2-го вида работ:
Расчет для остальных видов работ выполняется аналогично.
Суммарные затраты на заработную плату исполнителей:
Единый социальный налог на заработную плату исполнителей
где 0356 – ставка единого социального налога
Затраты на материалы при проектировании
где PMi – цена I-го вида материалов (покупных изделий) руб.ед.
mi – кол-во используемого материала (покупных изделий) i-го вида ед.
Наименование материалов и результаты расчетов сведены в таблицу 2.
Суммарные затраты на покупку материалов и изделий:
Прямые материальные затраты на разработку проекта
Наименование материалов
Канцелярские принадлежности
Справочная литература
* - все цены указаны в соответствии с прайс-листами магазинов канцелярских принадлежностей по состоянию на 16.04.2004.
Накладные расходы при проектировании включают расходы на электроэнергию амортизацию и ремонт оборудования и помещений оплату труда административно-управленческого вспомогательного и обслуживающего персонала (АУП и ВОП) с ЕСН контрагентские расходы (оплата услуг интернета экспертиза проекта и пр.).
Затраты на электроэнергию.
Определяют по формуле
Сэ - тариф за один кВтчас руб.(принимаем с учётом НДС 15 руб.);
ti - время работы i-того потребителя электроэнергии час.
Чтобы рассчитать время работы каждого потребителя электроэнергии
требуется знать срок разработки проекта в днях который определяют с учётом
рассчитанной выше (табл. 1) трудоемкости tпр работ :
Rисп - количество исполнителей чел. (см. гр.3 табл. 1);
- доля дополнительных работ (принимаем 0.1);
Кв - коэффициент использования времени (Кв = 08).
Полученные результаты продолжительности работ заносим в табл. 1 гр.4.
Затраты на ремонт и обслуживание технических средств.
При разработке проекта используются технические средства (компьютер принтер) а так же помещения в которых происходит разработка необходимо рассчитать их амортизацию и затраты на ремонт и обслуживание приходящиеся на данный проект.
- стоимость используемых технических средств (40640 руб.);
8 - норма амортизации (02) и обслуживания технических средств (008);
- стоимость используемых площадей (20 м2 * 5760 = 115200 руб.);
- время затраченное на разработку проекта в долях года (61 253= 0241).
Подставив указанные значения в формулу получим
Затраты на заработную плату АУП и ВОП.
Принимаем в размере 20% от оплаты труда разработчиков:
Единый социальный налог на заработную плату
Прочие накладные расходы
Контрагентские расходы
Принимаем в размере 1% от суммы предыдущих статей расходов:
Издержки на разработку проекта
Заработная плата исполнителей
ЕСН на оплату труда исполнителей
Затраты на материалы
Затраты на электроэнергию
Затраты на оплату труда АУП и ВОП с ЕСН ( 0.2 от п.п. 12)
Амортизация и ремонт технических средств и помещений
Прочие накладные расходы
Контрагентские расходы
Итого затрат FCпр (Кпр)
Цена проекта с учётом нормы прибыли:
где Rпр - норма прибыли на проектные работы (принимаем 25%).
Цена проекта должна быть учтена при определении цены модернизированной
машины т.к. цена проекта включается в стоимость имущества предприятия-
5. Определение себестоимости производства новой машины
5.1.Характеристика базовой техники
При расчёте себестоимости новой машины использовалась методика изложенная в. Поэтому сначала рассчитываем себестоимость базовой машины. В качестве базовой машины используем погрузчик малогабаритный универсальный ПУМ-500 со следующими экономическими характеристиками:
- цена продажи Рр=250000 рубшт;
- годовой объём производства Ар = 400 штгод;
- коэффициент доли заработной платы в цене предприятия b3V=0035
- коэффициент доли материальных затрат в цене предприятия bmv=0685
- коэффициент фондоотдачи f = 3;
- коэффициент оборачиваемости оборотных средств kоб = 63.
В состав себестоимости входят: переменные и постоянные издержки.
Годовые суммарные издержки: TC = TVC + TFC
где TVC – годовые переменные издержки руб.год;
TFC – годовые постоянные издержки руб.год.
Годовые переменные издержки TVC= AVC * А
где AVC – переменные издержки на одно изделие;
Ар – годовой объем выпуска(При расчетах VCз и VCм по новой машине величина Ар принимается на уровне 80%–ной производственной мощности предприятия);
Годовой объем продаж.
где Qp –цена без НДС:
Рn = Рp 118 = 250000 118 = 211816 руб.
Qp = 211816 * 400 = 84726400 руб.
Издержки производства и реализации
Издержки производства и реализации можно определить по следующей формуле: ТСПР = ТСЗ + 083 ТСМ + TСа + Нпл
где ТСЗ - затраты на заработную плату персонала;
ТСм - материальные затраты;
TСа - амортизационные отчисления;
Нпл - сумма налоговых платежей.
Затраты на заработную плату и материальные издержки также включают в себя переменную и постоянную части.
Затраты на заработную плату персонала
где Cзv – удельная зарплата руб.шт.
значения bзv берем из справочного материала
Сзv = 0035 * 211864 = 7415 руб.
VCз = 7415 * 400 = 2372881 руб.
FCз = 16 * 2372881 = 3796610 руб.
ТСз = 2372881 + 3796610 = 6169491 руб.
Материальные издержки
где Смv – удельные материальные затраты руб.шт. ;
значения bмv приведены в справочном материале.
Смv = 0685 * 21864 = 145127 руб.
VCм = 145127 * 08 * 400 = 46440589 руб.
FCм = (006 0065) VCм.
FCм = 006 * 46440589 = 2786435 руб.
ТСм = 46440589 + 2786435 = 49227024 руб.
Амортизационные отчисления.
САНТ = САБТ + 0075 Кп
где f – фондоотдача ([1 табл.1.3]);
КП – капитальные вложения в производство НТ (в данном случае равны 0).
САБТ = 075 * 84726400 = 717856 руб.
Налоги и отчисления (налоговые платежи)
Нпл = Нстv + НстF + Ним
где Нстv - ЕСН на переменную часть затрат на оплату труда:
НстF - ЕСН на постоянную часть затрат на оплату труда:
Ним - налог на имущество:
при этом НимНТ = НимБТ .
Нстv = 0356 * 2372881 = 844746 руб.
НстF = 0356 * 3796610 = 1351593 руб.
Ним = 02 * 717856 = 143572 руб.
Нпл = 844746 + 1351593 + 143572 = 2476911 руб.
ТС пр = 6169491 + 085 * 49227024 + 717856 + 2476911 = 51207228 руб.
Себестоимость одной базовой машины
АТС = ТС пр А = 128018 руб.
Налогооблагаемая и чистая прибыль
Налогооблагаемая прибыль
ПН = 84726400 - 51207228 = 33519172 руб.
НП = 024 * 33519172 = 8044601 руб.
ПЧ = 33519172 – 8044601 = 25474571 руб.
Рентабельность к объему продаж
Полученные результаты оформляем в виде табл.4 «Затраты и результаты в сфере производства».
5.2.Показатели модернизированной техники
Годовой объём производства
Годовой объём производства модернизированной техники предполагаем на
Затраты и результаты в сфере производства
Годовой оборот (без НДС)
Издержки производства и реализации в т.ч.:
1.Зарплата персонала в том числе:
1.1. переменная часть
1.2. постоянная часть
2.Материальные издержки в том числе:
2.1.переменная часть
2.2.постоянная часть
3.Амортизационные отчисления
4.Налоги и отчисления в том числе:
4.1.Отчисления на социальные нужды в том числе:
4.2.Имущественный налог
Рентабельность к объёму продаж
Производственные затраты по модернизированной технике
Цена производства НТ затраты на материалы и оплату труда персонала определяются следующим образом.
Удельные производственные затраты на материалы и оплату труда:
где КС и КН - соответственно коэффициенты сложности и новизны модернизированной техники по сравнению с базовой.
Принимаем КС = 1005 а КН = 101.
Удельные и годовые затраты на оплату труда персонала:
CЗVH = 7415 * 101 * 1005 = 74595 руб.
VCЗН = 74595 * 08 * 400 = 2387040 руб.
FCЗН = 16 * 2387040 = 3819264руб.
Удельные и годовые материальные издержки:
CМVH = 145127 * 101 * 1005 = 147311 руб.
VCмн = 147311 * 08 * 400 = 47139572 руб.
FCмн = 006 * 47139572 = 2828374 руб.
Амортизационные отчисления по модернизированной технике
Амортизационные отчисления по базовой и модернизированной технике одинаковы так как не требуется дополнительных капитальных вложений в производственные фонды предприятия-изготовителя.
CАН = CАБ = 717856руб.
Нстv = 0356 * 2387040 = 849786 руб.
НстF = 0356 * 3819264 = 1359658 руб.
Нпл= 849786 + 1359658 + 143572 = 2353016 руб.
ТС пр = 6206304 + 085 * 49967946 + 717856 + 2353016 = 51749930 руб.
Затраты на подготовку производства определяют по формуле:
примем их в размере 1%. Тогда подставив соответствующие значения в формулу получим:
В эту сумму включаются издержки на разработку проекта (цена проекта) и затраты на переналадку оборудования.
Цена производства модернизированной техники:
Подставив соответствующие значения в эту формулу и приняв ставку налога на прибыль dп = 024 а рентабельность к объёму продаж rо = 03006 получим:
Нижний предел PH цены модернизированной машины определяем по формуле
Верхний предел Рв цены (максимально-возможную цену) определяют по формуле:
где b - индекс производительности НТ
ИБТ ИНТ - годовые затраты потребителя на эксплуатацию БТ и НТ
r - процентная ставка (принимается 014)
ТСЛ - срок службы НТ годы
В нашем случае мы не будем использовать формулу верхнего предела так как мы будем вести сравнение использования новой машины с использованием химических реактивов.
Подставив рассчитанные выше показатели в формулу определения Рн получим значение нижнего предела цены модернизированного погрузчика:
Значение верхнего предела цены находим из условия платёжеспособного спроса коммунальных служб (спрос на средства механизации). Он равен 119 млн. руб. Разделив это значение на годовой объём выпуска новых машин получим:
Мы видим что рассчитанное значение цены лежит в пределах между нижней и верхней границами.
Годовой объём продаж модернизированной техники:
Q рн = 269263 * 400 118 = 91276 млн. руб.
Налогооблагаемая и чистая прибыль.
Пн = 91276 – (51750 + 0709) = 38817млн.руб.
Нп = 024 * 38817млн = 9316 млн. руб.
Рентабельность к объёму продаж: r1 = 295 91276 = 03232 или 3232%.
Мы видим что рентабельность к объёму продаж по модернизированному погрузчику получилась выше чем по базовой машине. Запишем показатели в сфере производства машин в табл. .4.
Сопоставим показатели в сфере эксплуатации модернизированного погрузчика с уборкой снега без погрузчика.
6. Расчёт показателей в сфере эксплуатации НТ.
Порядок расчета показателей в сфере эксплуатации НТ.
Для расчета показателей в сфере эксплуатации НТ используются Методические указания (МУ). Расчет эксплуатационной производительности НТ производится в соответствии с указаниями изложенными в разд. 8 МУ. Индекс производительности НТ b определяется по формуле (13.8) МУ.
Расчет годовых затрат на эксплуатацию ИБТ(НТ) производится в соответствии с указаниями разд. 9 МУс учетом следующих дополнений:
- при расчете затрат на заработную плату принимали значение минимальной ставки СТ = 32 рубч а часовую ставку машинистов 20 руб.
- при расчете затрат на топливо и смазочные материалы цена топлива принимается в размере 9000 руб.т (по состоянию на 01.04.2004 г.)
- при расчете затрат на гидравлическую жидкость цена гидравлического масла принималась в размере 15000 руб.т (по состоянию на 01.04.2004 г.)
Дополнительно были включены в сумму ИНТ амортизационные отчисления на реновацию НТ – SA и годовая сумму накоплений для проведения капитального ремонта НТ – SКР : SA = PP TСЛ
где ТКР - период до капитального ремонта годы (ТКР = ТМР ТГ × kЧ).
6.1.Расчет годовой эксплуатационной производительности
Годовую эксплуатационную производительность погрузчика используемого
для уборки снега и льда с тротуара можно определить по следующей формуле:
B = VПР * 1000 * ТГ ТЦ
где ТГ - годовой эффективный фонд рабочего времени ч год;
VПР - ширина захвата (убираемой полосы) VПР = 12 м;
ТЦ - время производственного цикла ч;
где Lоч - длина очищаемой поверхности Lоч = 1000 м;
LПЕР - длина пути перемещения погрузчика на другой тротуар LПЕР = 20 м;
vоч - скорость движения погрузчика при выполнении операции очистки vоч = 094 кмч;
vПЕР - скорость движения погрузчика при выполнении операции перемещения vПЕР = 60 кмч;
tМАН - время на маневрирование tМАН = 0007 ч;
где ДФ - годовой фонд рабочего времени техники = 247 дн;
tCM - продолжительность смены = 8 ч;
КСМ - коэффициент сменности = 20;
dП - продолжительность одного перебазирования машины дн;
ТОБ - среднее время работы машины на объекте ч;
ДР - удельные простои во всех видах ТО и Р дн.ч определяемые по формуле:
где dPj - продолжительность пребывания машины в j-м виде ТО или Р дн;
dgj - продолжительность доставки техники в j-й вид ремонта и обратно дн;
aj - количество j-х видов ТО и Р за межремонтный цикл ТМР;
ТМР - межремонтный цикл (ресурс до КР или списания машины) мото-ч;
КЧ - коэффициент перехода от мото-часов к машино-часам = 06;
Тг = 3320 час ДР = 001 ТЦ = 1067 часкм.
Годовая производительность модернизированной машины НТ составит:
B = 12 * 1000 * 3320 1067 = 3734400 м2 год.
6.2. Расчет годовых эксплуатационных затрат по НТ
Годовые эксплуатационные затраты по НТ рассчитываем по формуле:
где SЗП - заработная плата рабочих занятых в управлении техникой рубгод;
SЭ - затраты на энергоносители рубгод;
SС - затраты на смазочные материалы рубгод;
Sг - затраты на гидравлическую жидкость рубгод;
SТР - затраты на все виды технического обслуживания и ремонта рубгод;
SП - затраты на перебазировку рубгод;
SК - косвенные затраты рубгод;
Sа - амортизационные отчисления рубгод;
SКР - затраты на капитальный ремонт рубгод.
К этим затратам ещё следует добавить налог на имущество и на содержание стоянки для машины.
где КП - коэффициент учитывающий дополнительную заработную плату и единый социальный налог КП = 1627;
СТ - часовая тарифная ставка = 20 рубч;
SЗП = 1627 * 3320 * 20 = 108046 руб.
где ЦТ - цена топлива = 9 рубкг;
WT - часовой расход топлива кгч;
где NeH - номинальная мощность двигателя NeH = 184 кВт;
geH - удельный часовой расход топлива при номинальной мощности geH = 242 гкВт·ч;
KN - коэффициент учитывающий изменение расхода топлива в зависимости от степени использования двигателя по мощности = 08;
КДВ - коэффициент использования двигателя по времени = 086;
КДМ - коэффициент использования двигателя по мощности = 07;
WT = 103 * 184 * 242 * 08 * 086 * 07 : 1000 = 2209 кгч
SЭ = 9 * 2.209 * 3320 = 66000 руб.
где - коэффициент перехода от затрат на энергоносители к затратам на смазочные материалы = 02;
SС = 02 * 66000 = 13200 руб.
где VГ - емкость гидросистемы VГ = 29 л (дм3) = 0029 м3;
γМ - объемная масса гидрожидкости γМ = 900 кгм3;
ЦМГ - цена гидрожидкости ЦМГ = 15 руб.кг;
КДГ - коэффициент доливок жидкости в гидросистему КДГ = 15;
tМГ - периодичность замены жидкости в гидросистеме tМГ = 1000 ч;
SС = 0029 * 900 * 15 * 15 * 3320 1000 = 1305 руб.
где СР - средняя часовая тарифная ставка ремонтных рабочих СР = 20 рубч;
j - трудоемкость j-го вида ТО и Р чел.-ч;
Sк = 03 Sзп + ( Sэ + Sс + Sг + Sтр + Sп) = 54609 руб.
Sа = Pп Т сл = 269263 10 = 26926 руб.
Sпб - затраты на перебазирование техники
где tпб - продолжительность 1-й перебазировки ч
где aпб - средняя дальность 1-й перебазировки aпб =15 км
Vтр - скорость трейлера Vтр = 30кмч
G - грузоподъемность трейлера g=25т
nпб - число перебазирований в год:
- среднее время работы машины на объекте маш-ч;
dn - продолжительность 1-й перебазировки dn =tпб
Налог на имущество равен 5385 руб. (002 * 269263) затраты на содержание площадки для хранения погрузчика – 11670 руб.
Суммарные годовые затраты на содержание и эксплуатацию погрузчика:
Эксплуатационные затраты по модернизированному погрузчику в расчёте на 1м2
-в 0-м году расчётного периода когда производительность будет использована лишь на 40%: ATC 0 = 399891 3734400 * 04 = 026 рубм2;
-в 1-м году расчётного периода когда производительность будет использована на 60%: ATC 1 = 399891 3734400 * 06 = 018 рубм2;
-во 2-м году расчётного периода когда производительность будет использова-на на 100% : ATC 2 = 399891 3734400 = 012 рубм2 .
6.2.Затраты на уборку 1 м2 с применением реактивов
Расход хлористого кальция модифицированного жидкого –1л на м2.
Плотность хлористого кальция модифицированного жидкого –128 г см3 .
Цена 1 т. хлористого кальция модифицированного жидкого –270922 руб.т.
На 1 м2 расходуется 128 кг.
Расходы на материалы: Sм = 128 * 2709 = 347 руб.
Затраты на оплату труда: Sот = 20 100 = 02 руб
где 100 – производительность рабочего за 1 час м2. Прочие расходы 001руб.
Себестоимость уборки льда и снега:
7.Оценка эффективности реализации проекта
Для оценки эффективности реализации проекта связанного с использованием модернизированного погрузчика применим показатель чистого дисконтирован-ного дохода. Для подсчёта коэффициента дисконтирования принимаем норму дисконта r = 0.14.
Поскольку установить всю площадь убираемой в городе территории не представляется возможным рассчитаем показатель эффективности от применения одной машины. При этом предполагаем что одна машина сможет обслуживать несколько объёктов (поэтому при расчёте эксплуатационных затрат учитывали затраты на перебазировку машины с одного объекта на другой). Производительность машины за 5 месяцев осенне-зимнего периода в 0-м году – 1493760 в 1-м году – 2240640 и во 2-м году 3734400 * 5 : 12 = 1556000 м2.
Капитальные вложения на приобретение машины её доставку и строительство необходимых помещений К0 = Рп * 15 = 269263 * 15 = 40389 тыс. руб.
При расчёте ЧДД предполагаем что в 0-м году в связи с освоением машины производительность будет составлять 40% от расчётной.
ЧДД = 79769 млн. руб.
Полученные результаты свидетельствуют об эффективности реализации данного проекта т.к. ЧДД > 0. Расчёты показывают что только за счёт снижения расходов на реактивы затраты на приобретение машины её доставку и строительство необходимых помещений для хранения окупятся в 0-м году
Рабочее обор_.dwg

ДИП.МП.05.00.000.ПЧ.ВО.
Оборудование снегоуборочное
ДИП.МП.05.00.000.ПЧ.ВО
Неуказанные предельные отклонения размеров H14
S± 2. Несоосность отверстий не более 0
мм по ГОСТ 10356-69 3. Непараллельность поверхностей не более 0
Экономика1+1_.dwg

Заработная плата исполнителей
Затраты на материалы
Затраты на электроэнергию
Оплата труда АУП и ВОП
Амортизация и ремонт ПК и помещений
Контрагентские расходы
Затраты на подготовку производства НТ Кнт = 709
Годовой оборот(без НДС) 2. Издержки производства и реализации
в т.ч.: 2.1. Зарплата персонала
в т.ч.: 2.1.1. переменная часть 2.1.2. постоянная часть 2.2. Материальные издержки
в т.ч.: 2.2.1. переменная часть 2.2.2. постоянная часть 2.3. Амортизационные отчисления 2.4. Налоги и отчисления
в т.ч.: 2.4.1. Отчисления на социальные нужды
в т.ч.: -переменная часть -постоянная часть 2.4.2. Имущественный налог 2.4.3. Налогооблагаемая прибыль 2.4.4. Налог на прибыль 2.4.5. Чистая прибыль 2.4.6. Рентабельность к объему продаж
Qp TCnp TCз VCз FCз TCм VCм FCм Cа Hпл Hст Hстv Hстf Hим Пн Нп Пч р
Наименование показателей
Показатели в сфере производства
Экономические показатели проекта
Показатели эффективности проекта
Структура себестоимости 1 м при уборке с применением реактивов
При уборке с применением НТ
Условные обозначения
Показатели социально- экономической эффективности
Эффектообразующие показатели: 1.Снижение количества травм и ушибов 2.Механизация уборочных работ 3.Улучшение состояния тротуаров 4.Улучшение экологической обстановки 5.Улучшение условий труда
Эффективность в среде эксплуатации
Срок возврата инвестиций О-й год расчетного периода
Разделители.doc
Исследовательская часть
Технологическая часть.
Технологическая часть
Безопасность жизнедеятельности.
Безопасность жизнедеятельности
Экономическая часть.
ОВ погрузчик.dwg

Гидросистема (трансмиссия
Система охлаждения 15
Гидромотор аксиально - поршневой
Гидронасос с регулированием подачи
Скорость передвижения
Электрическая система:
Тип двигателя дизельный
Допустимая грузоподъемность при наибольшей высоте подъема ковша
Номинальная грузоподъемность
Номинальная частота вращения 2200
Максимальная мощность двигателя
Эксплуатационная масса 3100
Техническая характеристика
ДИП.МП.00.00.000.ПЧ.ВО
1.Введение ДИПЛОМ.doc
Все погрузчики имеют адекватную компоновочную схему в которую входят рама двигатель гидрообъемная трансмиссия рабочее оборудование с гидропри-водом система управления и рабочее место оператора.
Рама моноблочная сварная образована двумя коробчатыми лонжеронами соединенными между собой поперечными связями. Двигатель и приводимые им насосы устанавливаются в задней части рамы между стойками и лонжеронами там же помещаются гидро- и топливные баки. Все четыре ведущих колеса не имеют подвески и установлены на раме жестко. Над лонжеронами рамы располагаются гидроцилиндры подъема стрелы. Распределение массы погрузчика между передним и задним мостами 1: 2.
На погрузчиках применяются как карбюраторные так и дизельные двигатели имеющие в зависимости от мощности (10-60 кВт) от 1 до 4 цилиндров жидкостного или воздушного охлаждения с номинальной частотой вращения от 2000 до 3600 оборотов в минуту и выпускаемые фирмами Perkins Ford John Deer Case Kohler Deutz Isuzu Toyota и др.
Гидрообъемная трансмиссия обеспечивает ряд преимуществ перед другими видами привода. Фирмы-изготовители погрузчиков приобретают гидрообъемные трансмиссии у специализированных фирм Eaton Cessna Vickers Sundstrand Linde
Hydramatik Bosch Danfoss и др. Максимальное давление в гидросистеме 35МПа.
Гидрообъемный привод ходовой части состоит из двух независимых систем каждая из которых имеет насос переменной подачи с встроенным регулирующим устройством гидромотор постоянной подачи шланги высокого давления гидробак фильтр радиаторы и трубопроводы. Каждая система приводит во вращение колеса одного борта. Изменение скорости движения машины осуществляется подачей насосов. Реверсирование достигается изменением направления подачи тех же насосов.
Рулевой механизм в малогабаритных погрузчиках отсутствует. Поворот осуществляется за счет неодинаковой подачи насосов привода правых и левых колес (большие радиусы поворота) или изменением направления подачи насосов одного борта вызывающим вращение колес одного борта в противоположную сторону (малые радиусы поворота).
Минимальный радиус поворота равен расстоянию (в плане)от центра тяжести машины до наиболее удаленной от него точки конструкции т.е. возможен разворот вокруг центра масс. Торможение также осуществляется за счет гидропривода при уменьшении подачи от максимума до нуля.
Гидропривод работает от трех насосов. два насоса переменной подачи (привод хода) и один насос постоянной подачи (привод рабочего оборудования). Они соединены с двигателем через клиноременную передачу или шестеренный редуктор. Известно конструктивное решение привода насосов с непосредственным соединением их валов с коленчатым валом двигателя. В качестве промежуточного элемента используется упругая муфта (фирма EricksonШвеция). Однако такие насосы должны иметь соосное исполнение.
Ходовая часть включает в себя шестеренные или цепные бортовые передачи.
Шестеренные передачи представляют собой редуктор соединяющий передние и задние колеса. Одна из шестерен приводится во вращение гидромотором. На практике применяются одноступенчатые передачи но иногда при больших передаточных отношениях применяются двухступенчатые передачи (фирма Hydra
Мас США). Цепная передача выполнена в виде двух контуров привода передних и задних колес от одной двухрядной звездочки приводимой гидромотором.
Контур приводящий передние колеса имеет большее межцентровое расстояние
чем контур привода задних колес. Он снабжен натяжным устройством в виде дополнительной звездочки с перемещаемой осью вращения.
Большинство погрузчиков имеют один диапазон скорости максимум которых находится в пределах 7-11 кмч. Находит применение двухступенчатый привод с двумя скоростными диапазонами: рабочим и транспортным (фирмы Sperry Newho максимальная скорость 19 кмч.
Колеса погрузчика приводятся во вращение от конечных звездочек или шестерен валы которых являются одновременно валами колес.
Малогабаритные погрузчики имеют минимальную базу определяемую размером шин; отношение колеи к базе равно 13 15.
Каждая фирма для конкретной модели рекомендует 2-3 типоразмера шин. Предлагаемый набор шин часто включает балластируемые шины для увеличения устойчивости шины с пенистым наполнителем металлическим каркасом и др. Для увеличения тягово-сцепных свойств на грунтах с малой несущей способностью погрузчики оборудуются резинометаллической гусеничной лентой охватывающей передние и задние колеса.
В основное рабочее оборудование входят стрела и ковш. Стрела выполнена из двух коробчатых лонжеронов каждый из которых состоит из двух прямолинейных участков расположенных под тупым углом друг к другу и соединенных спереди поперечиной. Как правило на погрузчиках устанавливаются два гидроцилиндра подъема-опускания стрелы и два гидроцилиндра поворота ковша. Такая конструкция проста но ковш при подъеме запрокидывается поворачиваясь на тот же угол что и стрела (фирма Clark).
Дополнительные рабочие органы могут навешиваться на стрелу или непосредственно на раму машины. Для быстрой смены рабочих органов стрела оборудована специальными устройствами. Смена рабочих органов и их фиксация на стреле могут осуществляться из кабины машиниста. Для установки рабочего оборудования на раме предусмотрены специальные присоединительные устройства.
Для обеспечения автоматического поступательного перемещения ковша и улучшения эксплуатационных характеристик (больший угол запрокидывания при наборе материала и увеличенный угол разгрузки предотвращающий залипание ковша) используются подвески гидроцилиндров поворота ковша с применением дополнительных рычажных механизмов сходных с применяемыми на традиционных одноковшовых фронтальных погрузчиках (фирмы Case Letkat Toyota и др.). С этой же целью погрузчики оснащаются гидравлической скользящей системой с дополнительным гидроцилиндром выравнивающим ковш за счет поступления рабочей жидкости из дополнительного гидроцилиндра в соответствующие полости гидроцилиндров поворота ковша при подъеме стрелы (фирма Case погрузчики ЧССР).
Дополнительные рабочие органы могут навешиваться на стрелу или непосредственно на раму машины. Для быстрой смены рабочих органов стрела оборудована специальными устройствами. Смена рабочих органов и их фиксация на стреле могут осуществляться из кабины машиниста. Для установки рабочего оборудования на раме предусмотрены специальные присоединительные места.
Комплект сменных рабочих органов включает в себя до 20 наименований ковшей различного назначения вилы для штучных и тарных грузов челюстные захваты кирковщик задней навески канавокопатели бурильное бульдозерное экскаваторное подметально-уборочное и снегоочистительное оборудование планировщики поверхностей с фрезерным рабочим органом крановый гусек и др.
Гидропривод рабочего оборудования содержит в себе насос двухзолотниковый (реже трехзолотниковый) гидрораспределитель две группы исполнительных гидроцилиндров гидробак фильтры и трубопроводы. По специальному заказу могут устанавливаться дополнительные секции гидрораспределителя для управления сменными рабочими органами. Силовые гидроцилиндры двойного действия имеют диаметры 50 - 75 мм с отношением диаметра к ходу поршня около 1:10 для механизма подъема и 1:5 для механизма поворота ковша. Подача насосов составляет 30 - 80 лмин (в зависимости от типоразмеров) давление предохрани-
тельного клапана—14-17 МПа.
В системе управления предусмотрены два конструктивных исполнения: ручное или комбинированное (ручное и ножное). Ручное управление (фирмы Erickson Hydra Mac) обеспечивает со специального пульта установленного в середине кабины перед машинистом. Пульт выполнен в виде коробчатой стойки с двумя Т-образными рычагами. С помощью одного рычага управляется трансмиссия ( движение машины вперед назад поворот влево и вправо). С помощью другого рычага управляется рабочее оборудование (подъем - опускание стрелы и поворот ковша).
Широкое применение находят погрузчики фирмы Clark Owatonna с комбинированным управлением у которых вручную управляется трансмиссия а для управления рабочим оборудованием используются две педали.
Кроме рычагов управления трансмиссией и рабочим оборудованием в кабине имеются рычаг стояночного тормоза механического типа и педаль управления подачей топлива.
Рабочее место оператора оборудуется либо кабиной либо (чаще) жестким каркасом защищающим оператора при опрокидывании машины или от случайно выпавшего из ковша груза.
Боковые части каркаса закрываются специальными защитными решетками исключающими защемление оператора элементами рабочего оборудования. В передней части такие каркасы открыты для входа на рабочее место и хорошего обзора.
Особое внимание при создании машины уделяется легкости и удобству обслуживания. С этой целью задняя панель капота делается съемной или откидной что упрощает доступ ко всем обслуживаемым местам двигателя и гидроаппаратуры. На погрузчиках фирмы Clark устанавливается откидывающаяся кабина. На погрузчиках фирмы Hydra Mac фильтры расположены сбоку и через специальные окна в раме выведены наружу. В погрузчиках с цепными передачами ходовой части регулировочные приспособления натяжения цепи выведены на наружные стенки коробчатых лонжеронов.
Мой диплом Сварка_.dwg

Сварные швы по ГОСТ 5264 - 80
Несоосность отв. 35 с 0
Непараллельность осей отверстий с 1 мм на 1 м.
При сварке закреплять на монтажных оправах.
ДИП.МП.01.00.000.ПЧ.ВО.
Непараллельность осей отверстий с1мм на1м.
Сварные швы по ГОСТ 5264 -80
Ст.10Х ГОСТ 19281-73
СПЕЦ2наРО.doc
Рабочее оборудование
ДИП.МП.05.001.00.ПЧ.ВО.
ДИП.МП.05.002.00.ПЧ.ВО.
ДИП.МП.05.003.00.ПЧ.ВО.
Экономика1+1.dwg

Заработная плата исполнителей
Затраты на материалы
Затраты на электроэнергию
Оплата труда АУП и ВОП
Амортизация и ремонт ПК и помещений
Контрагентские расходы
Затраты на подготовку производства НТ Кнт = 709
Годовой оборот(без НДС) 2. Издержки производства и реализации
в т.ч.: 2.1. Зарплата персонала
в т.ч.: 2.1.1. переменная часть 2.1.2. постоянная часть 2.2. Материальные издержки
в т.ч.: 2.2.1. переменная часть 2.2.2. постоянная часть 2.3. Амортизационные отчисления 2.4. Налоги и отчисления
в т.ч.: 2.4.1. Отчисления на социальные нужды
в т.ч.: -переменная часть -постоянная часть 2.4.2. Имущественный налог 2.4.3. Налогооблагаемая прибыль 2.4.4. Налог на прибыль 2.4.5. Чистая прибыль 2.4.6. Рентабельность к объему продаж
Qp TCnp TCз VCз FCз TCм VCм FCм Cа Hпл Hст Hстv Hстf Hим Пн Нп Пч р
Наименование показателей
Показатели в сфере производства
Экономические показатели проекта
Показатели эффективности проекта
Структура себестоимости 1 м при уборке с применением реактивов
При уборке с применением НТ
Условные обозначения
Показатели социально- экономической эффективности
Эффектообразующие показатели: 1.Снижение количества травм и ушибов 2.Механизация уборочных работ 3.Улучшение состояния тротуаров 4.Улучшение экологической обстановки 5.Улучшение условий труда
Эффективность в среде эксплуатации
Срок возврата инвестиций О-й год расчетного периода
БЖД ДИПЛОМ .doc
1 Основы законодательства Российской Федерации об охране труда.
Законодательство по безопасности труда в РФ представляет собой правовую основу при проведении организационных технических и санитарно-гигиенических мероприятий направленных на создание безопасных высоко-производительных условий труда.
Безопасность труда (охрана труда) - это система законодательных актов социально-экономических организационных технических гигиенических и лечебно-профилактических мероприятий и средств обеспечивающих безопас-ность сохранение здоровья и работоспособность человека в процессе труда.
Безопасность труда вписывается в интегральную концепцию инфраструктуры "Безопасности жизнедеятельности" и является основной и главной в обеспечении безопасности человека как самого активного и важного субъекта в системах "человек - производственная среда" "человек - среда рабочей зоны".
Правительством РФ 12 августа 1994 года принято постановление №937 «О государственных нормативных требованиях по охране труда в РФ которым установлено что в РФ действует система нормативных правовых актов содержащие единые нормативные требования по охране труда обязательные для применения при проектировании строительстве и эксплуатации объектов конструировании машин механизмов и оборудования разработке технологичес-ких процессов организации производства и труда.
Действие указанных основ распространяется на: предприятия учреждения всех форм собственности независимо от сферы хозяйственной деятельности и ведомственной подчиненности; работодателей; работников состоящих с работодателями в трудовых отношениях; работников кооперативов; студентов общеобразовательных учреждений высшего и среднего профессионального образования учащихся образовательных учреждений среднего начального профессионального образования и образовательных учреждений основного общего образования проходящих производственную практику; военнослужащих привлекаемых для работы на предприятиях и другие категории граждан.
В основах законодательно определены конкретные права работника на охрану труда которые дополняют трудовые права работников определенные статьями 2 25 108 129 статьями Х КЗоТ РФ. Одним из главных является право работника на рабочее место с безопасными и здоровыми условиями труда на получение достоверной информации от работодателя или государственных и общественных органов о состоянии условий и охраны труда на рабочем месте работника о существующем риске повреждения здоровья. Порядок оформления трудовых отношений между работодателем и работником определен статьей 15 КЗоТ РФ в соответствии с которой между указанными сторонами заключается трудовой договор (контракт).
2 Надзор и контроль за соблюдением законодательства об охране труда.
Основами (статьей 24) предусмотрен государственный надзор и контроль за соблюдением законодательных и иных нормативных правовых актов по охране труда. То есть законодатель предложил осуществлять эти функции государству которые раньше были закреплены за профсоюзами.
Ответственность работников за нарушение требований законодательных и иных нормативных актов об охране труда определена статьей 27 в соответствии с которой работники предприятий привлекаются к дисциплинарной а в соответствующих случаях к материальной и уголовной ответственности в порядке установленном законодательством РФ и республик в составе РФ.
Дисциплинарная ответственность заключается в наложении на должностное лицо или работника одного из следующих дисциплинарных взысканий: замечание выговор строгий выговор увольнение (статья 135 КЗоТ РФ).
Материальная ответственность наступает в случае ущерба нанесенного предприятию из-за несоблюдения работником требований и норм охраны труда.
Основной документ регулирующий трудовые отношения всех работников и
всех работодателей - Кодекс законов о труде РФ(КЗоТ РФ).
При подготовке коллективного договора проводят паспортизацию условий труда на всех рабочих местах и заполняют паспорта санитарно-технического состояния цехов. По условиям коллективного договора администрация должна
взять на себя обязанности по:
- обеспечению бесперебойной работы и надлежащему содержанию санитарно-бытовых помещений;
- предоставлению дополнительных отпусков и сокращению рабочих дней;
- содержанию в порядке территории предприятия;
- обеспечению безопасности эксплуатации оргтехнического и другого оборудования;
- обеспечению специальной одеждой обувью и другими средствами индивидуальной защиты:
- строгому соблюдению требований охраны труда технологической дисциплины графиков планово-предупредительных ремонтов;
- обеспечению бесперебойной работы вентиляции исправного состояния оборудования нанесения на нем требуемой окраски и т.д.
Взаимные обязательства администрации и профсоюзного комитета предусматривают:
- внедрение мероприятий системы управления охраной труда
- административно-общественный (трехступенчатый) контроль за состоянием охраны труда
- материальное и моральное стимулирование членов трудовых коллективов за работу без аварий и травмирования работающих;
- изготовление обновление и пополнение стендов по охране труда и т.д.
3 Анализ объекта проектирования с точки зрения безопасности
При работе погрузчика возможно возникновение ряда аварийных ситуаций
которые могут привести к выходу из строя механизмов погрузчика а также к
производственным травмам обслуживающего персонала. Самыми вероятными и
наиболее частыми причинами травматизма при работе погрузчика являются:
-Опрокидывание погрузчика;
-Возникновение пожара;
-Вредное воздействие вибрации;
-Недопустимый уровень шума;
-Недостаточная вентиляция кабины и т.д.
Безопасность проведения работ подъемно-транспортными машинами целиком и полностью зависит от работы приборов безопасности к которым относятся:
-Ограничители грузоподъемности;
-Указатели грузоподъемности;
-Концевые выключатели;
-Комбинированные приборы и др.
Все работы связанные с производством монтажом обслуживанием и ремонтом данных приборов подчиняются общим правилам при работе с электроприборами и правилам ГОСГОРТЕХНАДЗОРА.
В соответствии с этими правилами погрузчики должны иметь выше перечисленные приборы безопасности. Каждый прибор должен иметь свой паспорт который выдается предприятием-изготовителем и в котором отражаются все изменения проводимые в процессе эксплуатации и ремонта.
4 Пожарная безопасность при эксплуатации погрузчика.
Предотвращение пожара (как неконтролируемого горения вне специального очага наносящего материальный ущерб) обеспечивается пожарной безопасностью. Пожарная безопасность (согласно ГОСТ 12.1.004-76 «Пожарная безопасность»)- это такое состояние объекта при котором исключается возможность пожара а в случае возникновения предотвращается его опасное воздействие на людей и обеспечение защиты материальных ценностей. Пожарная безопасность обеспечи-вается системами предотвращения пожара и пожарной защитой. Под системой предотвращения пожара имеется в виду комплекс организационных мероприятий и технических средств направленных на исключение возможности возникновения пожара. Под системой пожарной защиты понимают комплекс организационных мероприятий и технических средств на предотвращение воздействия на людей опасных факторов пожара и ограничение материального ущерба от него.
В целях обеспечения пожарной безопасности погрузчики оборудуются
углекислотными огнетушителями в которых огнегасящее вещество не является
При хранении погрузчиков под открытым небом двигатели внутреннего сгорания подогревают паром из специальной установки. Весьма часто такие двигатели загораются из-за применения открытого огня для их подогрева (факелов костров паяльных ламп жаровен). Заправлять топливом машины допускается только при заглушенном двигателе и выключенном зажигании. При эксплуатации погрузчика пожары в большинстве случаев возникают по нескольким причинам:
- из-за воспламенения оставшейся внутри двигателя горючей смеси
- из-за неправильного расположения баков с горюче-смазочным материалом
- из-за маслопроводов и топливопроводов по отношению к трубопроводу выхлопных газов и глушителю
- из-за воспламенения разлитых масел и горючего под картером двигателя
- из-за отсутствия искрогасителей на выпускных трубах
- из-за курения при заправке машины топливом.
Пожары возникают также в случаях:
- утечки горючего из топливопроводов
- утечки отработанных газов в выпускных трубопроводах
- неисправности кранов перекрывающих топливопроводы
- самовозгорания использованных обтирочных материалов.
Работы на строительной площадке должны вестись в соответствии с Правилами пожарной безопасности при производстве строительно-монтажных работ утвержденными ГУПО МВД. В случае возникновения пожара для быстрого прекращения горения машина должна быть оборудована автоматической пожарной
сигнализацией а также автоматической и ручной системами пожаротушения.
5 Обеспечение необходимой вентиляции в кабине.
Для создания в кабинах погрузчиков воздушной среды удовлетворяющей
санитарно-гигиеническим требованиям и условиям производства (ГОСТ 12.4.021-75 «Системы вентиляционные»). Это достигается удалением загрязненного воздуха из рабочей зоны и замены его чистым воздухом. По способу перемещения воздуха вентиляционные системы делят на вентиляцию с естественным и вентиляцию с механическим побуждениями. Естественная вентиляция может быть неорганизо-ванной когда смена воздуха т.е. проветривание кабины осуществляется через неплотности ограждения. Такой воздухообмен не постоянен так как он зависит от температуры снаружи и внутри кабины силы и направления ветра и размеров неплотностей ограждения. Назначение вытяжной вентиляции – локализовать вредные выделения в производственных процессах предотвращая тем самым распространение их в рабочей зоне и в помещении.
В кабинах погрузчиков требуется как зимой так и летом обеспечить постоян-ство температуры относительной влажности и скорости движения воздуха независимо от метеорологических условий внешней среды. Для поддержания заданных параметров воздуха применяют различные системы кондиционирования.
Для обеспечения в кабине микроклимата и предельно-допустимых концентра-ций вредных веществ в воздухе в соответствии с нормами ГОСТ 12.1.005-76 12.1.007-76 12.2.019-76 и 12.2.023-76 устанавливают естественную вентиляцию (люки форточки опускающиеся стекла) и принудительную а также пылеуловите-ли воздухоохладители кондиционеры и отопители. В кабине применяют кондиционирование воздуха с помощью испарительных кондиционеров. Простейшим кондиционером испарительного типа является вентиляционная установка с воздухоохладителем (в кабину поступает воздух очищенный от пыли увлажненный и охлажденный
6 Средства и методы защиты от шума.
Звуковые колебания возникают в результате колебания частиц в твердой
жидкой и газообразной средах. По происхождению эти колебания делят на:
- механические (от колебания машины)
- аэродинамические (от колебаний при течении газов)
- гидродинамические (от колебаний при течении жидкостей)
- электромагнитные (в связи с переменой магнитных и электрических полей).
Шум - совокупность слышимых звуков сочетающая множество различных тонов и частот с беспорядочной интенсивностью и продолжительностью. Но под шумом понимают также нежелательный для человека звук мешающий восприятию необходимых звуков или нарушающих тишину. Действие шума на организм человека проявляется в поражении органов слуха и нарушении систем (сердечно-сосудистой центральной нервной) а также ослаблении памяти изменении кожной чувствительности.
В погрузчике основным источником шума является двигатель внутреннего сгорания (вентилятор системы охлаждения система впуска и выпуска механизмы газораспределения процесс сгорания кривошипно-шатунный механизм). Уровень шума от рабочего и ходового оборудования а также от отдельных элементов машины меньше уровня шума от двигателя.
Классификация средств и методов защиты от шума установлена
ГОСТ 12.1.029-80 “Средства и методы защиты от шума”.
Классификация средств снижающих шум:
- снижение шума в источнике его возникновения (механического аэродинамического гидродинамического и электромагнитного).
- снижение шума на пути его распространения (передача воздушного и структурного шумов).
- акустические средства защиты от шума: звукоизоляция (ограждения экраны кожуха кабины) звукопоглощение (облицовка поглотители звука)
- демпфирование (с сухим трением вязким трением внутренним трением)
- глушители шума (абсорбционные реактивные комбинированные).
Средства индивидуальной защиты (наушники вкладыши шлемы каски костюмы).
Средства снижения шума в источнике его возникновения должны
реализовываться в процессе проектирования машины или технологического процесса. Методы снижения шума в этом случае применяют в зависимости от конструктивных особенностей машины. Глушители предназначены для глушения шума возникающего при перемещении воздуха и других газов. Эффективность глушителя должна обеспечивать снижение уровня шума двигателя до норм внешнего шума по ГОСТ 19358-74.
7 Электробезопасность .
При прохождении электрического тока через организм человека возникают электротравмы которые по признаку поражения делят на электрические удары и травмы. Действие электрического тока на организм человека может быть химическим приводящим к разложению крови и тепловым вызывающим ожог участков тела. Возможны также металлизация кожи биологическое воздействие при котором нарушается электрические процессы (биотоки). Степень опасности воздействия тока на организм человека зависит от величины тока длительности его воздействия рода и частоты его электрической сопротивляемости тела человека а также от напряжения и схемы включения тела в электрическую цепь.
Строительно-монтажные работы в охранной зоне действующей линии электропередачи следует производить под непосредственным наблюдением инженерно-технического работника.
Расстояние от выдвижной части строительной машины в любом ее положении до вертикальной плоскости образуемой проекцией на землю ближайшего провода находящегося под напряжением воздушной линии электропередачи должно быть не менее указанного ниже:
Напряжение воздушной линии кВт.
Наименьшее расстояние м.
8 Воздействие вибрации.
Тело работающего человека условно рассматривают как своеобразную колеблющуюся систему поскольку под воздействием вибрации части тела человека перемещаются относительно друг друга с амплитудами в зависимости от источника колебаний и массы органов. Относительные перемещения частей тела приводят к напряжениям в связках между частями тела взаимному соударению и надавливанию. Действующие гигиенические оценки вибрации изложены в
По способу передачи на человека вибрацию делят на:
- общую передающуюся через опорные поверхности на тело сидячего или стоящего человека
- локальную передающуюся через руки человека.
Двигатель внутреннего сгорания подвешенный на упругих элементах - амортизаторах к раме погрузчика представляет собой колебательную механическую систему с шестью степенями свободы. Источником колебаний двигателя является опрокидывающий момент неуравновешенные силы моменты сил инерции и возмущения передающиеся двигателю от дороги. При разгоне и торможении погрузчика возникают дополнительные силы воздействующие на двигатель.
Для снижения колебаний (вибрации) передаваемых от двигателя к раме предусматривают виброизоляцию – амортизаторы устанавливаемые между двигателем и рамой. В большинстве случаев применяют резинометаллические амортизаторы в которых арматуру крепят к резине способом вулканизации. Эти амортизаторы работают на сжатие сдвиг или на оба усилия одновременно. Резину применяют марок 7-1847 и 7-2959 на основе натурального каучука.
9 Постановка задачи.
С целью увеличения безопасности обслуживающего персонала при проведении подъемно - транспортных работ на случай возникновения аварийных ситуаций необходимо разработать проектно конструкторские решения служащие для предупреждения машиниста о возможной потере устойчивости препятствующие возникновению опрокидывания а также обеспечивающие безопасные условия в кабине при опрокидывании погрузчика.
10 Устойчивость погрузчика.
Способность машины противостоять опрокидыванию характеризует ее устойчивость против опрокидывания которая с одной стороны зависит от конструктивных параметров машины а с другой стороны от действий оператора управляющего машиной. Условно можно различать собственную и управляемую устойчивости машины: первая зависит от конструктивных параметров машины а вторая — от действий оператора направленных на сохранение устойчивости машины в критических ситуациях (наезд или съезд с препятствия движение на повороте по склону и т. п.) путем соответствующего изменения скорости движения или положения машины и ее рабочего оборудования. Элементы машины посредством которых оператор управляет устойчивостью характеризуют «активную» безопасность машины так как она реализуется через активные действия человека-оператора.
Различают статическую и динамическую устойчивость против опрокидывания. Первая характеризуется равновесным состоянием машины под действием внешних нагрузок постоянных по значению и направлению. При расчете статической устойчивости определяют условие которому должна удовлетворять система сил нагружающих машину чтобы последняя находилась в равновесии. Состояние статического равновесия характеризуется при этом тем что машина длительное время пребывает в покое. Нарушение такого состояния вызывает практически мгновенное опрокидывание машин.
Способность машины противостоять действию максимальных статических опрокидывающих нагрузок определяет ее предельную устойчивость против опрокидывания. Опрокидывание машины сопровождается ее поворотом вокруг некоторой воображаемой неподвижной оси которая называется осью опрокидывания. В статике положение осей опрокидывания постоянно и зависит от конструкции ходовой части машины.
В зависимости от направления опрокидывания различают оси бокового и продольного опрокидывания.
Для строительных машин такого класса наиболее актуальной проблемой обеспечения техники безопасности является устойчивость машины. Общие требования безопасности к строительным и дорожным машинам изложены в ГОСТ12.2.011-75 «Машины строительные дорожные».
Для погрузчиков определяют собственную и грузовую устойчивость т.е. без груза и с грузом в ковше при полностью заправленном погрузчике и с водителем на своем рабочем месте. Расчет устойчивости рассматривают при трех положениях стрелы: в транспортном на максимальном вылете ковша и наибольшем подъеме
когда погрузчик стоит на месте.
Продольную устойчивость погрузчиков рассчитывают одинаково относительно передней и задней оси опрокидывания. Продольная статическая устойчивость характеризуется предельными углами подъема aП и уклона aУ на которых может стоять заторможенный погрузчик под действием силы тяжести не опрокидываясь.
Предельные углы продольной статической устойчивости на подъем определяют по формуле:
Предельные углы продольной устойчивости под уклон составят
Боковую устойчивость рассчитывают в соответствии с типом и конструкцией ходовой части и принятым опорным контуром по предельным углам в боковом направлении. При этом погрузчик располагают на наклонной поверхности таким образом чтобы боковые грани опорного контура были перпендикулярны основной линии склона.
Предельные углы боковой устойчивости определяются по формуле:
Расчет устойчивости погрузчика
Собственная продольная устойчивость.
Транспортное положение стрелы
Максимальный вылет ковша
Наибольший подъем ковша
Грузовая продольная устойчивость
Транспортное положение стрелы
Максимальный вылет ковша
Наибольший подъем ковша
Собственная боковая устойчивость. Грузовая боковая устойчивость.
С целью предупреждения о превышении предельно допустимых кренов при
работе на склонах на машине требуется установить сигнализатор крена.
Сигнализатор крена (рис.1) комплектуется из датчика крена 1 и панели сигнализации 2. Датчик крена (рис.2) состоит из металлического шарика 1 демпфирующей жидкости 2 залитой в корпус 3 катушки индуктивности 4 электронного преобразователя 5 и уровня 6.На панели сигнализации размещают реле Р предохранитель Пр и две сигнальные лампы: ЛК- красная и ЛЗ – зеленая. Датчик крена и панель сигнализации соединены кабелем через штепсельные разъемы. Сигнализатор работает по принципу пространственного бесконтактного датчика дискретного действия.
При крене менее допустимого или при горизонтальном положении
Рис №1 Сигнализатор крена Рис. №2 Датчик крена.
металлический шарик находящийся в магнитном поле катушки индуктивности срывает колебания высокочастотного генератора и электронный преобразователь подает ток на реле которое включает сигнальную зеленую лампу. Если крен машины будет больше допустимого металлический шарик выкатится из магнитного поля и в высокочастотном генераторе возникает генерация тока. Этот сигнал обесточит реле сигнальная зеленая лампа отключится и включится красная лампа. В этом случае водитель машины должен выровнять крен машины до допустимого при котором включится зеленая лампа. Уровень на датчике крена предназначен для регулировки при монтаже на кронштейне. Сигнализатор присоединяется к бортовой сети машины напряжением 12 В постоянного тока.
На машину требуется установить устройство защиты при опрокидывании ГОСТ 27714-88 «Машины землеройные устройства защиты от опрокидывания». Это устройство служит для выполнения основного назначения – снижения риска нанесения повреждения оператору в случае опрокидывания управляемой им
машины при условии применения оператором ремней безопасности.
При установке на машину выше перечисленных устройств гарантируется
обеспечение безопасности оператора управляющего данной машиной.
Технология работ.dwg

Транспортное положение
Разгрузочное положение
Мой диплом ГС.dwg

Гидроцилиндр поворота ковша
Гидроцилиндр подъема стрелы
Насос привода рабочего оборудов.
Насос привода трансмиссии
Гидромотор аклиально-поршневой
схема гидравлическая
ДИП.МП.00.00.000.ПЧ.ГС
ОВ погрузчик_.dwg

Гидросистема (трансмиссия
Система охлаждения 15
Гидромотор аксиально - поршневой
Гидронасос с регулированием подачи
Скорость передвижения
Электрическая система:
Тип двигателя дизельный
Допустимая грузоподъемность при наибольшей высоте подъема ковша
Номинальная грузоподъемность
Номинальная частота вращения 2200
Максимальная мощность двигателя
Эксплуатационная масса 3100
Техническая характеристика
ДИП.МП.00.00.000.ПЧ.ВО
Рабочее обор.dwg

ДИП.МП.05.00.000.ПЧ.ВО.
Оборудование снегоуборочное
ДИП.МП.05.00.000.ПЧ.ВО
Неуказанные предельные отклонения размеров H14
S± 2. Несоосность отверстий не более 0
мм по ГОСТ 10356-69 3. Непараллельность поверхностей не более 0
Маршрут. картыДИПЛОМ.dwg

Точить поверхность D=116
с подрезанием торца и фаски.
Сверло диаметром 50 мм.
Сверлить сквозное отверстие диаметром 50 мм.
Сталь 20ХН3А-3 ГОСТ 4543 - 71
Обозначение документа
Наименование детали
наименование оборудования
наименование операции
Протяжка для отверстия с прямобочным профилем d=55
Протягивать отверстие d=55.
Фреза дисковая с пластинами Т15К6 (DxBxZ=100х20х21)
Нарезать зубья D=116.9
Провести термообработку зубьев шестерни
Печи для термообработки СШЗ 4.1210.
Калибр-скоба ГОСТ 24705-81; Штангенциркуль; Микрометр.
Контролировать D=116.9 и шлицы d=55
Шлифовать зубья D=116.9 до устранения следов износа и дефектов формы
Круг шлифовальный плоский 24А60П С26К5 ПП250х50х40 ГОСТ 2424-83
ДИП.МП.00.00.000.ТЧ.
Расчет на прочность.dwg

Система канонических уравнений
Решение системы канонических уравнений
Определение суммарного изгибающего момента в точке приложения силы Р.
Определение координат точек
в которых изгибающий момент максимальный
Характер изменения значения силы Р в зависимости от координаты приложения ее к расчетной балке.
Закон изменения изгибающего момента в зависимости от координаты приложения силы Р=1 (положение 1)
Закон изменения изгибающего момента в зависимости от координаты приложения силы Р=1 (положение 2)
Закон изменения изгибающего момента в зависимости от координаты приложения силы Р=1 (положение 3)
Максимальные значения изгибающего момента при Р=1:
Абсолютные значения максимального изгибающего момента:
Основные расчетные положения
Эпюра изгибающего момента
действующего на балку
при приложение силы Р=1 в точку с координатой Z=0.3l
ЛитератДИПЛОМ .doc
Политковская И.В. Оценка экономической эффективности инвестиционных проектов. Москва: «Экон-Информ».2003 –64 с.
Самойлович В.Г. "Экономическая оценка вариантов технических решений". Москва: МАДИ(ТУ) – 1993.
Иванов А.Н. Мишин В.А. "Снегоочистители отбрасывающего действия". Москва "Машиностроение"1981.
Гусев Л.М. "Расчет и конструкции подметально-уборочных машин". Машгиз1963.
Бялобжеский Г.В. Иванов А.Н. Шалман Д.А. "Очистка автомобильных дорог от снега". Москва 1972.
Гуленко Н.Н. "Снегоуборочные машины и механизмы". Москва 1973.
Косилова А.Г. Мещеряков Р. К. "Справочник технолога-машиностроителя". Москва " Машиностроение"1986.
Карабан Г.Л. Баловнев В.И. Засов И.А. "Машины для содержания и ремонта автомобильных дорог и аэродромов". Москва "Машиностроение"1975.
Гоберман Л.А. "Основы теории расчета и проектирования строительных и дорожных машин". Москва "Машиностроение"1988.
Живейнов Н.Н. Карасев Г.Н. Цвей И.Ю. "Строительная механика и металлоконструкции строительных и дорожных машин". Москва "Машиностроение"1988.
Зеленин А.Н. Баловнев В.И. Керов И.П. "Машины для земляных работ". Москва "Машиностроение"1975.
Чернавский С.А. Рещиков В.Ф. "Справочник металлиста".Том 1. Москва "Машиностроение"1976.
Живов М.А. Лифшиц Б.А."Организация и технология уборки городов". Москва "Стройиздат" 1969.
Шалман Д.А. "Снегоочистители". Москва "Машиностроение"1967.
Гоберман Л.А. Степанян К.В. "Строительные и дорожные машины". Атлас конструкций. Москва "Машиностроение"1985.
Бородачев И.П. "Справочник конструктора дорожных машин". Москва "Машиностроение"1965.
Николаев Г.А. Куркин С.А. Винокуров В.А. "Сварные конструкции". Москва Высшая школа1982.
ПРАДМ 1_.dwg

Зубья цементировать h=1
сердцевина зубьев 32 46 HRC
Маркировать на торце обода m=5; z=20.
Неуказанные допуски по h14
ДИП.МП.00.01.000.ТЧ.ВО.
ДИП.МП.00.00.000.ТЧ.ВО.
ДИП.МП.00.03.000.ТЧ.ВО.
ДИП.МП.00.02.000.ТЧ.ВО.
ПРАДМ 2.dwg

ДИП.МП.00.05.000.ТЧ.ВО.
ДИП.МП.00.07.000.ТЧ.ВО.
ДИП.МП.00.06.000.ТЧ.ВО.
БЖД.dwg

Расчет устойчивости при максимальном вылете ковша.
Расчет устойчивости при максимальном подъеме ковша.
Предельные углы боковой устойчивости:
Предельные углы продольной статической устойчивости:
Значение углов грузовой устойчивости
Значения углов собственной устойчивости
(чертеж общего вида)
БЖД__recover000.dwg

Расчет устойчивости при максимальном вылете ковша.
Расчет устойчивости при максимальном подъеме ковша.
Предельные углы боковой устойчивости:
Предельные углы продольной статической устойчивости:
Значение углов грузовой устойчивости
Значения углов собственной устойчивости
(чертеж общего вида)
Технология работ_.dwg

Транспортное положение
Разгрузочное положение
БЖД_.dwg

Расчет устойчивости при максимальном вылете ковша.
Расчет устойчивости при максимальном подъеме ковша.
Предельные углы боковой устойчивости:
Предельные углы продольной статической устойчивости:
Значение углов грузовой устойчивости
Значения углов собственной устойчивости
(чертеж общего вида)
Расчет на прочность_.dwg

Система канонических уравнений
Решение системы канонических уравнений
Определение суммарного изгибающего момента в точке приложения силы Р.
Определение координат точек
в которых изгибающий момент максимальный
Характер изменения значения силы Р в зависимости от координаты приложения ее к расчетной балке.
Закон изменения изгибающего момента в зависимости от координаты приложения силы Р=1 (положение 1)
Закон изменения изгибающего момента в зависимости от координаты приложения силы Р=1 (положение 2)
Закон изменения изгибающего момента в зависимости от координаты приложения силы Р=1 (положение 3)
Максимальные значения изгибающего момента при Р=1:
Абсолютные значения максимального изгибающего момента:
Основные расчетные положения
Эпюра изгибающего момента
действующего на балку
при приложение силы Р=1 в точку с координатой Z=0.3l
Титульный Диплом.doc
Дорожных и технологических машин факультет
Кафедра Дорожно-строительных машин
ПОЯСНИТЕЛЬНАЯ ЗАПИСКА
к дипломному проекту
на тему Машина для уборки снега
Главный консультант Карасев Г. Н.
по экономической части Политковская И. В.
по технологической части Пономарев В. А.
СПЕЦ4наЩЕТКУ.doc
ДИП.МП.05.03.100.ПЧ.ВО.
Планетарный редуктор
ДИП.МП.05.03.200.ПЧ.ВО.
Аксиально-поршневой насос
ДИП.МП.05.03.003.ПЧ.ВО.
ДИП.МП.05.03.004.ПЧ.ВО.
ДИП.МП.05.03.005.ПЧ.ВО.
ДИП.МП.05.03.006.ПЧ.ВО.
ДИП.МП.05.03.007.ПЧ.ВО.
ДИП.МП.05.03.008.ПЧ.ВО.
ДИП.МП.05.03.009.ПЧ.ВО.
ДИП.МП.05.03.010.ПЧ.ВО.
ДИП.МП.05.03.011.ПЧ.ВО.
ДИП.МП.05.03.012.ПЧ.ВО.
Манжета 164 ГОСТ 15643-78
ДИП.МП.05.03.013.ПЧ.ВО.
Подшипник 7332 ГОСТ 6874-75
ДИП.МП.05.03.014.ПЧ.ВО.
Болт М16х60 ГОСТ 1476-75
ДИП.МП.05.03.015.ПЧ.ВО.
Болт М10х40 ГОСТ 1476-75
ДИП.МП.05.03.016.ПЧ.ВО.
Болт М12х50 ГОСТ 1476-75
ДИП.МП.05.03.017.ПЧ.ВО.
Шайба 16.65Г.3.5 ГОСТ 6402-70
ДИП.МП.05.03.018.ПЧ.ВО.
Шайба 10.65Г.2.5 ГОСТ 6402-70
ДИП.МП.05.03.019.ПЧ.ВО.
Шайба 12.65Г.3 ГОСТ 6402-70
ДИП.МП.05.03.020.ПЧ.ВО.
Гайка М16 ГОСТ 15523-70
Мой диплом Сварка.dwg

Сварные швы по ГОСТ 5264 - 80
Несоосность отв. 35 с 0
Непараллельность осей отверстий с 1 мм на 1 м.
При сварке закреплять на монтажных оправах.
ДИП.МП.01.00.000.ПЧ.ВО.
Непараллельность осей отверстий с1мм на1м.
Сварные швы по ГОСТ 5264 -80
Ст.10Х ГОСТ 19281-73
Мой диплом ГС_.dwg

Гидроцилиндр поворота ковша
Гидроцилиндр подъема стрелы
Насос привода рабочего оборудов.
Насос привода трансмиссии
Гидромотор аклиально-поршневой
схема гидравлическая
ДИП.МП.00.00.000.ПЧ.ГС
Маршрут. картыДИПЛОМ_.dwg

Точить поверхность D=116
с подрезанием торца и фаски.
Сверло диаметром 50 мм.
Сверлить сквозное отверстие диаметром 50 мм.
Сталь 20ХН3А-3 ГОСТ 4543 - 71
Обозначение документа
Наименование детали
наименование оборудования
наименование операции
Протяжка для отверстия с прямобочным профилем d=55
Протягивать отверстие d=55.
Фреза дисковая с пластинами Т15К6 (DxBxZ=100х20х21)
Нарезать зубья D=116.9
Провести термообработку зубьев шестерни
Печи для термообработки СШЗ 4.1210.
Калибр-скоба ГОСТ 24705-81; Штангенциркуль; Микрометр.
Контролировать D=116.9 и шлицы d=55
Шлифовать зубья D=116.9 до устранения следов износа и дефектов формы
Круг шлифовальный плоский 24А60П С26К5 ПП250х50х40 ГОСТ 2424-83
ДИП.МП.00.00.000.ТЧ.