Крестовина деталь 25-49-46/46-01. Организация производства.




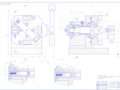
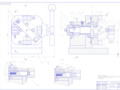
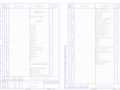
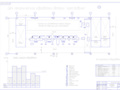
- Добавлен: 25.10.2022
- Размер: 6 MB
- Закачек: 0
Описание
Состав проекта
![]() |
![]() |
![]() |
![]() ![]() ![]() ![]() |
![]() ![]() ![]() ![]() |
![]() ![]() ![]() ![]() |
![]() ![]() ![]() ![]() |
![]() ![]() ![]() ![]() |
![]() ![]() ![]() ![]() |
![]() ![]() ![]() ![]() |
![]() ![]() ![]() ![]() |
![]() ![]() ![]() ![]() |
![]() ![]() ![]() ![]() |
![]() ![]() ![]() ![]() |
![]() ![]() ![]() ![]() |
![]() ![]() ![]() ![]() |
![]() ![]() ![]() ![]() |
![]() ![]() ![]() ![]() |
![]() ![]() ![]() ![]() |
![]() ![]() ![]() ![]() |
![]() ![]() ![]() ![]() |
![]() ![]() ![]() ![]() |
![]() ![]() ![]() ![]() |
![]() ![]() ![]() ![]() |
![]() ![]() ![]() ![]() |
![]() ![]() ![]() ![]() |
![]() |
![]() ![]() |
![]() |
![]() ![]() ![]() |
![]() ![]() |
![]() |
![]() ![]() ![]() |
![]() ![]() |
![]() |
![]() ![]() |
![]() ![]() ![]() |
![]() |
![]() ![]() ![]() |
![]() ![]() ![]() |
![]() |
![]() ![]() ![]() |
![]() ![]() |
![]() |
![]() ![]() ![]() |
![]() ![]() |
![]() |
![]() ![]() ![]() |
![]() ![]() ![]() |
![]() |
![]() ![]() ![]() |
![]() ![]() ![]() |
![]() |
![]() ![]() |
![]() |
![]() ![]() ![]() |
![]() |
![]() ![]() ![]() |
![]() ![]() ![]() |
![]() |
![]() ![]() ![]() |
![]() ![]() |
![]() |
![]() ![]() |
![]() ![]() |
![]() ![]() |
![]() ![]() |
![]() ![]() |
![]() ![]() |
![]() ![]() |
![]() |
![]() ![]() |
![]() ![]() |
![]() ![]() |
![]() ![]() |
![]() ![]() |
![]() ![]() |
![]() ![]() |
![]() ![]() |
![]() ![]() |
![]() ![]() |
![]() ![]() |
![]() ![]() |
![]() ![]() |
![]() ![]() |
![]() ![]() |
![]() ![]() |
![]() ![]() |
![]() ![]() |
![]() ![]() |
![]() ![]() |
![]() |
![]() ![]() |
![]() ![]() |
![]() ![]() |
![]() ![]() |
![]() ![]() |
![]() ![]() |
![]() ![]() |
![]() ![]() |
![]() ![]() |
![]() |
![]() |
![]() |
![]() |
![]() |
![]() |
![]() |
![]() |
![]() |
![]() ![]() |
![]() ![]() |
![]() ![]() |
![]() ![]() |
![]() ![]() |
![]() ![]() |
![]() |
![]() ![]() |
![]() ![]() |
![]() ![]() |
![]() ![]() |
![]() ![]() |
![]() ![]() |
![]() ![]() |
![]() ![]() |
![]() ![]() |
![]() ![]() |
![]() ![]() |
![]() ![]() |
![]() ![]() |
![]() ![]() |
![]() |
![]() ![]() |
![]() ![]() ![]() |
![]() ![]() |
![]() ![]() ![]() |
![]() ![]() |
![]() ![]() ![]() |
![]() ![]() |
![]() ![]() ![]() |
![]() ![]() ![]() ![]() |
![]() ![]() ![]() |
![]() ![]() ![]() |
![]() ![]() ![]() |
![]() ![]() ![]() |
![]() ![]() |
Дополнительная информация
Присп станочное №1 .dwg

Осевой люфт шестерни (поз.13) не более 0.5 мм обеспечить
устоновкой прокладок (поз.17) по месту.
Станочн приспособл лист №2 .dwg

приспособ станочное 3.dwg

Направляющая фиксатора
Винт М12x30.109.40Х.05
Гайка ВМ24х1.57Н.8.05
Карта наладки №1.dwg

Наименование и модель станка
Сверло 2300-03212 ГОСТ 10902-77
Сверло 2300-0195 ГОСТ 10902-77
Метчик 2680-0004 ГОСТ 6227-80
Сверло 2317-0019 ГОСТ 14952-75
Приспособление контрольное №1.dwg

Неперпендикулярность общей оси поверхностей Б относительно
общей оси поверхностей.
Разность размеров Г.
Оси поверхностейБ и В должны лежать в одной плоскости.
Непаралельность поверхности Д относительно общей оси призм
Несоосность калибров
635 положительных в призму (поз.1)
допускается не более 0.03 мм.
стан приспос4 прилож.dwg

Карта наладки (токарная) 1 - формат А2.dwg

Карта наладки (свер фреза) 1 - формат А2.dwg

Фрезерно-центровальный
Операция 005 Фрезерно-центровальная
Сверло 2317-0009 ГОСТ 14952-75
Эк2.dwg

показатели по участку
ОСНОВНЫЕ ТЕХНИКО-ЭКОНОМИЧЕСКИЕ
ПОКАЗАТЕЛИ ПО УЧАСТКУ
Наименование показателей
Показатели по вариантам
Абсолютные показатели
стоимость оборудования
стоимость транспортных средств
стоимость оснастки и
дорогостоящего инструмента
Общая площадь участка
Общая численность рабочих
Технологическая себестоимость
Относительные показатели
Вспомогательные рабочие в процентах
Выпуск продукции с 1 м
ЭК1.dwg

Основная заработная плата
производственных рабочих.
Дополнительная заработная плата
Отчисления на социальное
Цеховая себестоимость.
Технологическая себестоимость
по сравниваемым вариантам
Планируемое снижение себестоимости
=44566000-39282400=5284600 (руб.)
Планируемое снижение трудоёмкости
выпускаемой продукции
Процент снижения трудоёмкости %Т=
Планируемый процент роста производительности труда %П =
Планируемое снижение численности рабочих
Годовой экономический эффект Э
ПОКАЗАТЕЛИ ЭКОНОМИЧЕСКОЙ ЭФФЕКТИВНОСТИ ПРОЕКТА
Расчёт экономической эффективности
Станочн приспособл лист №2.dwg

Планировка цеха.dwg

- подвод электроэнергии
- подвод средств охлаждения
- пожарный ящик с песком
- контейнер для стружки
Эксплуатация оборудования
Фрезерно-центровальный.
Вертикально-сверлильный.
Вертикально-протяжный.
Бесцентрово-шлифовально.
Участок по изготовлению опорных втулок
(входят в сборочный узел крестовины)
Цех механической обработки детали "крестовина
График загрузки оборудования
Приспособ станочное № 2.dwg

карта наладки лист №3 - формат А2.dwg

Наименование и модель станка
Плоско-шлифовальный 3 Г 71
:24А25СМ26К6 ГОСТ 2424-83
5 91А 16ПСТ16К5 ГОСТ 2424-83
7 14А 12СТ15В ГОСТ 2424-83
плита инструм 5 прилож.dwg

Винт А. М12-6gх70.14Н
Шпонки ГОСТ 24644-81
Протяжка №1.dwg

*Размеры для справок.
Сопряжения радиусов во впадинах зубьев должны быть плавными.
режущие кромки довести.
При шлифовании угла
торец Д поднять относительно торца Е
Сопряжения радиусов во впадинахзубьев должна быть плавными.
На режущих зубьях сделать стружкоразделительные канавки
расположив их в шахмотном порядке между собой.
Маркировать: код инструмента
Протяж в сборе.dwg

Маркировать 2462-0316 Р6М5
Максимальное усилие протягивания кН 3.11
Пределы длин протягивания мм 48
Длина протягивания 45мм
Сталь 20ХН3А ГОСТ 4543-71
Присп станочное №1.dwg

Осевой люфт шестерни (поз.13) не более 0.5 мм обеспечить
устоновкой прокладок (поз.17) по месту.
Протяж в сборе .dwg

Маркировать 2462-0316 Р6М5
Максимальное усилие протягивания кН 3.11
Пределы длин протягивания мм 48
Длина протягивания 45мм
Сталь 20ХН3А ГОСТ 4543-71
Станочное приспособление лист №1.dwg

приспособл. контрольное 2.dwg

Крестовина поковк №1 - формат А2 дя 5.dwg

Класс точности T4 ГОСТ 7505-89
Неуказанные радиусы не менее 3 мм.
Штамповочные уклоны 7
Заусенец по периметру среза не более 1
Смещение по линии разъема штампа не более 0
Неперпендикулярность осей цапф 1 мм.
Допускается местные углубления не более 1
Очистить от окалины.
технические требования по ГОСТ 7505-89
Маркировать: номер детали
номер цеха изготовителя
Экономический эффект
Крестовина №1.dwg

Цементировать. На поверхностях Б и В h 1.5 2 мм
поверхностях Д 1.3 2 мм
допускается цементация
остальных поверхностей h
Овальность и конусообразность поверхностей Б и В не более
Отклонение от перпендикулярности общей оси Б относительно
общей оси поверхности В не более 0.02 мм (допуск зависимый).
Разность замера Г не более 0.1 мм.
Отклоноение от перпендикулярности поверхностей Б и В не
Направление канавок на торцах Д относительно поверхности Е
Неуказанные предельные отклонения размеров механически
обрабатываемых поверхностей: отверстий по Н14
Поковка штампованая
точности по ГОСТ 7505-74
В полостях Ж не допускается наличие окалины и образива.
отв КГ 18 ГОСТ 12717-67
О20 сверление.doc
О 2. Сверлить отверстие 1 выдержав размеры 2
ТСверло 2301-0047 ГОСТ10903-77;
Нутромер НИ 10-18 ГОСТ 868-72
Микрометр МК-50-2 ГОСТ6507-78
ТШтангенциркуль ШЦ-1-125-001 ГОСТ 166-89
О3. Рассверлить отверстие 1 под резьбу 3 выдержав размер 4
ТСверло 2373-0034 ГОСТ10903-77;
О4. Нарезать резьбу 3 выдерживая размер 5
ТМетчик 2680-4001 ГОСТ 6227-80;
О5. Контроль размеров.
О10.doc
О2. Точить последовательно с переустановкой 4 цапфы
выдержав размеры 1 2 3 4 5 6 7 и 02 м В м × Т 02 м В м
ТРезец 2103-4037 ГОСТ; Пластина 02114-120612 Т15К6 ГОСТ 19048-73 микрометр МК-50-2 ГОСТ 6507-78
штангенциркуль ШЦ-1-0.01 ГОСТ 166-89 Ррадиусный шаблон РШ-1 ГОСТ 4126-82 Приспособление специальное (48±03)
ТПриспособление 02 м Вм × Т 02 м В м
О3. Контроль размеров.
060 шлифовальная .doc
Очки 0-12-68 ГОСТ 12.4.013-85
О2. шлифовать последовательно торцы в размер 1 .
ТКруг ПП 250×32×76 24А 25 СМ2 К6 35мс ГОСТ 2424-83;Карандаш 3908-0052-2 ГОСТ 607-80;Приспособление спец.;Скоба (200) спец.
О3. Контроль размеров.
045 термическая .doc
О2. Цементировать: на поверхностях по диаметру h=1.9÷2.3м 60÷65 HRCэ сердцевина 30÷40 HRCэ; На поверхностях торцов h=1.9÷2.3м HRCэ ≥60. Допускается цементация остальных поверхностей h=2.2мм. Микроструктура цементационного слоя по ОСТ 23.4.52-83.
040 слесарная .doc
О2. Зачистить заусенцы притупить острые кромки
Напильник 2822-0119 ГОСТ 1465-80
О3. Уложить детали в тару-120шт-отправить на мойку
О4. После мойки детали уложить на контрольную плиту
О5.Готовые детали с клеймам ОТК уложить в тару -120шт.
О25 сверление.doc
О 2.Центровать отверстие 1 выдержав размеры 2 3 4
ТСверло2317-0019 ГОСТ14952-75;
Штангенциркуль ШЦ-1-125-001 ГОСТ 166-89
О3. Сверлить отверстие 1 на проход
ТСверло 2300-0195 ГОСТ10902-77;
О3. Рассверлить отверстие 1 под резьбу 3 выдержав размер 4
ТСверло 2373-0034 ГОСТ10903-77;
О4. Сверлить отверстие 7 выдержав размер 5
ТСверло 2301-4189 ГОСТ10902-77
О5. Нарезать резьбу
ТМетчик 2680-0004 ГОСТ 6227-80;
О6. Для детали 25-49-46-01 переустановить деталь
О7. Повторить переходы 2 3 4 5 6 3 раза
О8. Контроль размеров.
О15.doc
О2. Точить последовательно с переустановкой 4 цапфы
выдержав размеры 1 2 3 4 5 6 7 и 02 м В м и × Т 02 м В м
ТРезец 2103-4037; пластина 02114-120612 Т15К6 ГОСТ 19048-73
Микрометр МК-50-2 ГОСТ6507-78
Штангенциркуль ШЦ-1-125-001 ГОСТ 166-89;
Радиусный шаблон РШ-1 ГОСТ 4126-82
Приспособление специальное (48±03)
ТПриспособление (× ) специальное.
О3. Контроль размеров.
055 шлиф-ая.doc
Очки 0-12-68 ГОСТ 12.4.013-85
О2. шлифовать 4 цапфы (по 2 цапфы одновременно с переустановкой) выдерживая размеры 1 2 3 и т.т.
Круг 1.600×40×305 91А 16П СТ1 7К5 35мс А1кл ГОСТ 2424-83; (Круг 1.600×40×305 14А 16П СМ2 7К5 35мс А1кл ГОСТ 2424-83); Круг ведущий 1.350×25×127 14А 12ПС Т5В 35мс А1кл ГОСТ 2424-83;Карандаш 3908-0052 ГОСТ 607-80;
Радиусный шаблон набор №1 ТУ2-031-228-87;Скоба СР-50 ГОСТ 11098-75
Концевые меры 3-Н2 ГОСТ 9038-83.Приспособление спец.;
Микрометр МР-50 ГОСТ 4381-87
О3. Контроль размеров.
КЭ 055 .doc
КЭ 035 .doc
О35протяжная .doc
О2. Протянуть одновременно два торца выдержав размеры 1 2 3 4 5 7 и 002 Г 01 Г
ТПротяжка спец. левая; Протяжка спец. правая; Протяжка спец. (2шт.)
Микрометр МК-225-2 ГОСТ6507-78
Приспособление ( ) специальное;
Приспособление ( ÷ ) специальное
О3. Переустановить деталь
О4 . Протянуть одновременно два торца выдержав размеры 1 2 3 4 6 7 и 002 В 01 В
О5. Контроль размеров.
О05.doc
Очки 0-12-68 ГОСТ 12.4.013-85
Фрезеровать две цапфы одновременно выдержав размеры 1 2 Т 01 Б Т 01 В
Фреза 2214-0271 Т5К10 60° ГОСТ 22085-76;(Z=8)
Микрометр МК225-2 ГОСТ 6507-78
Приспособление спец. (÷)
О3. Центровать одновременно 2 отверстия 3 выдержав размеры 4 5 6 .
Штангенциркуль ШЦ-I-125-0.01 ГОСТ166-89.
Приспособление контрольное спец.
О4. Повернуть приспособление
О5. Повторить переход 2.
О6. Повторить переход 3
О7. Контроль размеров.
КЭ 050 .doc
050 шлифовальная .doc
Очки 0-12-68 ГОСТ 12.4.013-85
О2. шлифовать 4 цапфы (по 4 цапфы одновременно с переустановкой) выдерживая размеры 1 2 3 и т.т.
Круг 1.600×40×305 91А 16П СТ1 7К5 35мс А1кл ГОСТ 2424-83; (Круг 1.600×40×305 14А 16П СМ2 7К5 35мс А1кл ГОСТ 2424-83); Круг ведущий 1.350×25×127 14А 12ПС Т5В 35мс А1кл ГОСТ 2424-83;Карандаш 3908-0052 ГОСТ 607-80;Радиусный шаблон набор№1 ТУ2-031-228-87;Скоба СР-50 ГОСТ 11098-75Концевые меры 3-Н2 ГОСТ 9038-83.
Приспособление спец.;Микрометр МР-50 ГОСТ 4381-87
О3. Контроль размеров.
О30 сверление.doc
О 2. Сверлить отверстие 1 на размер 2 выдерживая размеры 3 4
ТСверло комбинированное специальное;
Штангенциркуль ШЦ-1-125 ГОСТ 166-80
О3. Сверлить отверстие 5 на размер 6
ТСверло 2301-0030 ГОСТ10903-77;
Штангенциркуль ШЦ-1-125 ГОСТ 166-80
О4. Сверлить отверстие 7 выдержав размер 8
ТСверло 2301-0024 ГОСТ10903-77;
Штангенциркуль ШЦ-1-125-001 ГОСТ 166-89
О5. Сверлить отверстие 9 на проход
ТСверло 2301-0020 ГОСТ 10903-77
О6. Контроль размеров.
3-4 Экономическая часть.doc
1 Расчет потребности в оборудовании по участку.
а)расчет потребности основного оборудования.
определяется по каждому виду работы технологического процесса.
где плановый выпуск комплектов деталей за год шт.;
норма штучного времени (трудоемкость) на
эффективный фонд времени единицы оборудования за год мин;
планируемый коэфициент выполнения нормы времени
Таблица 3.1Расчетная таблица
Фрезерно-центровальная
После расчетов и записи в графы таблицы по всем операциям значений ; ; устанавливаем принимаемое число рабочих мест Р округляя до ближайшего целого числа полученное значение .
Далее по каждой операции вычислем значение фактического коэффициента загрузки рабочего места по формуле ; стр.21[1]
Определим коэфициентзакрепления операций для нового варианта технологического процесса
где - суммарное число различных операций
- суммарное число рабочих мест
Согласно ГОСт 14.004-74 для 1≤≤10 производство крупносерийное.
Расмотрим целесобразность оргонизации многостаночного оборудования.
Многостаночное обслуживание возможно при условии
- машиное время работы на операции; - время работы на операции вручную.
Таблица 3.2Расчетная таблица.
Из таблицы видно что условием многостаночного обслуживания удовлетворяют сверлильные операции.
Норма обслуживания для многостаночного обслуживания
Строим график работы многостаночного обслуживания рабочего за смену.
Рисунок 3.1 График работы многостаночного обслуживания.
Таблица 3.3Время работы станков
Коэфициент загрузки рабочего во время многостаночного цикла
где -цикл многостаночного обслуживания мин;
-свободное время мин;
б) расчет вспомогательного оборудования
Потребное количество заточных станков общего назначения 1штук (берется в размере 5% от общего количества станков обслуживаемых заточкой).
Шлифовальные станки заточкой не обслуживаются. Потребное количество станков для ремонтной мастерской 1штук (принимается в размере 43% от общего количества станков).
Расчет баланса времени одного рабочего за год производится по календарю соответствующего года. Основной и дополнительный отпуска составляют 6% от номинального времени.
Отпуска по беременности и родам составляет 1% невыходы по болезни - 4% невыходы связанные с выполнением государственных и общественных обязанностей принимаются 04% к номинальному фонду рабочего времени. Внутрисменные потери составляют 16% в том числе сокращенный рабочий день подростков – 03% перерывы для кормящих матерей – 07% и сокращенный рабочий день рабочих с вредными условиями труда – 06% к номинальному фонду рабочего времени.
Таблица 3.4Баланс времени одного рабочего за год
Состав фонда рабочего времени
Рабочее время (номинальный фонд времени Fн.р.)
Целодневные невыходы на работу:
а) отпуска основные и дополнительные
б) отпуска по беременности и родам
в) невыходы по болезни
г) выполнение государственных и общественных обязанностей
Явочное рабочее время
Потери внутри рабочего дня:
а) сокращенный рабочий день подростков
б) перерывы для кормящих матерей
в) сокращенный рабочий день рабочих с вредными условиями труда
Итого внутрисменных потерь
Эффективный фонд времени (Fэф.р.)
Средняя продолжительность рабочего дня
2Расчет численности работающих участка.
Расчет численности работающих участка (цеха) ведется отдельно по категориям работающих.
а)определение потребного количества основных рабочих.
Расчет явочной численности основных рабочих (Rосн. чел) производится по каждой профессии по формуле:
где - эффективный фонд рабочего времени за год час смотрим таблицу 4.4.
- коэффициент многостаночного обслуживания (=15).
Явочную численностьрабочих определим по формуле стр10[15]
Где-коэффициент перевода станочного числа рабочих в явочную.
где ; - номинальный и эффективный фонд времени рабочих час.
- коэффициент перевода списочного числа рабочих в явочную.
Расчет численности основных рабочих по операциям сведем в таблицу 4.5
Таблица 3.5Численность основных рабочих по оперпациям.
Количество рабочих в две смены
Оператор станка с ЧПУ
б)определение потребного количества вспомогательных рабочих.
Численность вспомогательных рабочих принимается в размере 40-50% к основным рабочим с распределениям их по профессиям по укрупненным нормативам.
Таблица 3.6 Численность вспомогательных рабочих по профессиям и разрядам.
Профессия вспомогательных рабочих
Количество в две смены
Обслуживающие оборудование
Слесари и станочники по ремонту оборудования
Не обслуживающие оборудование
в)определние численности ИТР служащих и МОП.
Расчет ведем на основании нормативных данных в зависимости от количества основных рабочих на участке.
Расчет сведен в таблицу 4.7 с перечнем занимаемых долностей количества смен и окладов.
Таблица 3.7Численность ИТР МОП по участку.
Месячный должнестной оклад руб.
Служащие на участке отсуствуют учет выхода рабочих ведут сменые мастера.
После расчета числености работающих поотдельным категориям даные расчета сводятся в таблицу 4.8
Таблица 3.8Численность работающих на участке.
Категория работающих
Рабочие: а) основные
3Расчет площади участка.
В площадь цеха входят:
а)Производственную площадь участка по обработке комплекта деталей определяем из удельной площади станка fсi и числа станков. В удельную площадь включаются площадь станка площадь необходимая для рабочего проходов и проездов (для укрупненного расчета удельная площадь станка равна 14 м2):
где – общее количество станков шт.;
– удельная площадь станка м2.
В производственную площадь участка входит площадь поточной линии.
б)Площадь вспомогательных отделений для механических цехов:
где Fз Fp – площади вспомогательных отделений заточного и ремонтно-механического м2.
Площадь каждого из этих отделений определяется также как и для производственных участков по числу станков.
Удельная площадь станков в заточном отделении составляет 8м2 в ремонтно-механическом – 12 м2.
в)Площадь обслуживающих помещений..
Fоб=Fс.з.+Fс.г.+Fк+Fик стр.21[15]
где Fс.з. Fс.г. Fк Fик – площади соответственно склада заготовок склада готовых изделий контрольного отделения инструментально-раздаточной кладовой.
г)Площадь контрольного отделения Fк определяется от численности контролеров и площади рабочего места контролера. Площадь для одного контролера принимается равной 5м2.
где nк – число контролеров в цехе;
S – число смен работы участка.
д)Площадь инструментально-раздаточной кладовой.
где Fc – площадь кладовой приходящийся на один станок (Fc = 05м2).
м2 – дополнительная площадь по мелкому ремонту инструментов и приспособлений.
е)Площадь склада заготовок определяется по формуле:
где Q-общая масса деталей за год Т; t-число дней на которое применяется запас t=12; D- число рабочих дней в году (см. табл.4.6) g-допустимая нагрузка на пол g=4Тм2; К- коэфициент использования площади склада К=3.
Масса заготовки: m=58 кг.
ё)Площадь склада готовых изделий определяется по формуле:
где Q-общая масса деталей за год Т; t-число дней на которое применяется запас t=15; D- число рабочих дней в году (см. табл.4.6) g-допустимая нагрузка на пол g=25Тм2; К- коэфициент использования площади склада К=3.
ж)площадь служебных помещений Fсл определяется исходя из численности ИТР специалистов и служащих участка. Площадь на одного человека - 4м2.
з)площадь бытовых помещений Fб определяется исходя из числа основных и вспомогательных рабочих работающих в одну смену.
Норматив площади на одного человека – 07м2.
4Расчет общего фонда заработной платы.
Расчет общего фонда заработной платы ведем отдельно по каждой категории работающих.
Фонд заработной платы рабочих состоит из основной и дополнительной заработной платы. В основную заработную плату рабочих входит прямой фонд заработной платы рабочих-сдельщиков и рабочих повременщиков сумма премии по сдельно-премиальной и повременно-премиальной системе доплата не освобожденным бригадиром доплата за работу в ночное время рабочим сдельщикам и повременщикам.
Прямой фонд заработной платы по основным рабочим-сдельщикам участка определяется по формуле:Фn=NгодPстр 23[15]
где P – расценка на единицу комплекта деталей руб.
где - среднечасовая тарифная ставка рабочего сдельщика (станочника) соответствующая разряду выполняемых работ по участку.
где - часовая тарифная ставка 1-го разряда;
Кср – средний тарифный коэффициент соответствующий среднему разряду работ.
Кср определяется как средняя арифметическая величина тарифных коэффициентов взвешенных по трудоемкости работ.
где К1 К2 Кn – тарифные коэффициенты соответствующих разрядов работ; tp1 tp2tpn – трудоемкость работ по разрядам в нормо-часах;
- суммарная трудоемкость по всем разрядам.
Прямой фонд заработной платы вспомогательных рабочих–повременщиков определяется по формуле:
где Сч.сд.–средняя часовая тарифная ставка рабочих повременщиков соответствующая среднему разряду вспомогательных рабочих;
hвр – численность вспомогательных рабочих – повременщиков чел.
Средний разряд третий тогда
Фонд заработной платы вспомогательных рабочих
Сумма всех доплат входящих в основную зарплату рабочих берется в процентах от прямого фонда заработной платы: для рабочих – сдельщиков-30% для рабочих повременщиков – 35%.
Основная заработная плата рабочихсдельщиков
Основная заработная плата рабочих – повременщиков
Дополнительная заработная плата рабочих.
К дополнительной заработной плате рабочих относятся оплаты и доплаты рабочим за неотработанное время предусмотренное трудовым законодательством. К ним относятся: доплата за сокращенный рабочих день подростков оплата перерывов кормящим матерям оплата рабочего времени выполнения государственных и общественных обязанностей.
Дополнительная заработная плата рабочих определяется отдельно для рабочих – сдельщиков и повременщиков и составляет 015% от основной заработной платы: D=Фос.015
Общий фонд заработной платы
Делением общего фонда заработной платы на число рабочих определяется средняя заработная плата рабочих.
Расчет фонда заработной платы РК специалистов служащих и МОП.
Фонд заработной платы РК специалистов служащих и МОП определяется на основе должностных окладов и численности состава этих работников по штатному расписанию. Основная заработная плата определяется как произведение месячного оклада на число рабочих месяцев в году. Длительность отпуска 24 рабочих дня и кроме того учитываем неявку на работу по причине выполнения общественных и государственных обязанностей (исключая МОП) поэтому дополнительную заработную плату принимаем равной месячному окладу. Для МОП отпуск составляет ровно месяц.
Таблица 3.9 расчет фонда заработной платы по ИТР МОП и по участку.
Общий фонд заработной платы по всем категориям работающих участка определяется как сумма общего фонда заработной платы основных и вспомогательных рабочих руководящих кадров специалистов служащих и МОП. Расчет сводим в таблицу 3.10.
Таблица 3.10общий фонд заработной платы по участку.
Экономическая часть.
1Экономическое обоснование эффективности внедрения участка по обработке детали – крестовина 25-49-4646-01.
Разработанный проект участка по механической обработке детали крестовина 25-49-4646-01 имеет ряд преимуществ по сравнению с базовым (существующим).
Сокращение количества основного оборудования.
Уменьшение трудоемкости изготовления детали и повышение производительности
Сокращение производственных площадей
Уменьшение численности рабочих
Повышение производительности труда
Снижение себестоимости изготовления детали
Повышение эффективности обработки детали
2Методика расчета экономической эффективности от внедрения предлагаемого варианта проекта:
решение о целесообразности создания и внедрения новой техники принимается на основе экономического эффекта определяемого на годовой объем производства годовой техники в расчетном году. За расчетный год принимается первый год после окончания планируемого нормативного срока освоения новой техники;
годовой экономический эффект новый техники представляет собой суммарную экономию всех производственных ресурсов (живого труда материалов кап вложений) которую получает народное хозяйство в результате производства и эксплуатации новой техники;
определение годового экономического эффекта основывается на сопоставлении приведенных затрат по базовой и новой технике. Приведенные затраты представляют собой сумму себестоимости и нормативной прибыли. стр13[16]
где производственные затраты на единицу продукции рубль; себестоимость единицы продукции рубль; капитальные удельные вложения рубль; нормативный коэффициент эффективности капитальных вложений равный 015;
расчет годового экономического эффекта от применения новых технологических процессов механизации и автоматизации производства способов организации производства способов организации производства и труда обеспечивающих экономию производственных ресурсов при выпуске одой и той же продукции производится по формуле стр.13[16]. Где годовой экономический эффект рубль; производственные затраты на единицу продукции производимой с помощью базово и новой техники в расчетном году в натуральных единицах штук.
Эта формула может быть представлена в развернутом виде:
Где себестоимость единицы продукции до и после внедрения новой техники рубль;
капитальные удельные вложения до и после внедрения новой техники рубль
нормативный коэффициент эффективности капитальных вложений равный 015;
результаты эксплуатации плановых мероприятий по новой технике должны быть учтены в основных хозрасчетных показателях работы предприятия цеха участка. К таким показателям эффективности:
Планируемое снижение себестоимости продукции рубль. стр.13[16]
Планируемое снижение материальных затрат рубль стр.13[16]
Где стоимость материалов необходимых для изготовления единицы изделия до и после внедрения новой техники рубль.
Планируемое снижение трудоемкости выпускаемой продукции и : стр.14[16]
Где трудоемкость единицы продукции до и после внедрения новой техники.
Планируемый рост производительности труда
Планируемое сокращение численности работающих (условное высвобождение) человек.
где эффективный фонд времени одного рабочего в планируемом году час;
планируемые коэффициент выполнения нормы времени (выработки).
Планируемая экономия капитальных вложений рубль:
где удельные капитальные вложения в базовую и новою техники рубль
годовые объемы выпускаемой продукции производимой при использовании базовой и новой техники штук.
Выбор базы для сравнения и обеспечения условий сопоставимости вариантов.
Показатели экономической эффективности рассматриваемых вариантов капитальных вложений сопоставляются с нормативными показателями экономической эффективности достигнутыми в предыдущие годы.
При определении годового экономического эффекта принимаем показатели обработки детали по ранее действующей технологии.
Условия сопоставимости вариантов является определяющими для получения правильности результатов сравнения. Условия сопоставимости вариантов достигается когда по каждому из вариантов обеспечиваются:
один и тот же состав продукции (деталь);
один и тот же качество продукции;
один и тот же годовой объем продукции;
один и тот же сроки ее получения при одинаковом режиме работы во времени (смежность продолжительность смены и.т.п. а так же при сходных условиях труда).
Если варианты не соответствуют выше указанным условиям сопоставимости то необходимо привести варианты к сопоставимому виду либо путем проведения дополнительных мероприятий либо путем перерасчета на соответствующее условие. Это влечет за собой применение дополнительных средств и пойдет отражение в капитальных вложениях и себестоимости продукции по вариантам.
Условия сопоставимости включает также необходимость применения одинаковой методики определения всех элементов затрат а также одинаковой степени точности используемых нормативов исходных данных и одинаковой точности расчетов по сравниваемым вариантам.
Исходные данные для расчета показателей экономической эффективности предлагаемого варианта сводятся в таблицу.
Таблица 4.1данные для расчета
Дополнительная зарплата в % к основной Здоп. %
Отчисл. на соц. страхование в % к основной и дополнительной зарплате Зстр %;
Начисление премии в % Зпр. %
Средний разряд рабочих:
a)сдельщиков Счас.сд. руб.
b)повременщиков Счас.пов руб.
Эффективный фонд времени раб.за год Fэф час
Стоимость 1м2 производств. площади Цпл руб.
а) оборудование Ноб %
Стоимость 1 кВт ч электроэнергии Сэл руб
Коэффициент использования оборудования:
Потери от брака в % к Nшт %
Коэффициент выполнения норм времени Кн.вр.
Расчет капитальных вложений принимаемых к расчету по сравниваемым вариантам.
Капитальные вложения принимаемые к расчетному по результатам сравнения вариантов рассчитываются отдельно по первому (базовому) и второму (новому) вариантам Затем расчеты сводятся в таблицу для сравнения вариантов капитальных вложений.
Расчет капитальных вложений по первому (базовому) варианту
a.Стоимость технологического оборудования на участке включая его затраты на доставку и монтаж
Таблица 4.2стоимость оборудования.
Прейскурант основных фондов.
Токарный-гидрокопиров.
б.Стоимость зданий и сооружений определяется по формуле
-количество станков технологического оборудования -Удельная площадь занимаемая оборудованием
-коэффициент учитывающий дополнительную площадь приходящуюся на оборудование -количество типоразмеров оборудования;
h-высота помещения; (H=6м)
Цзд .-стоимость 1м3 производственного здания. (Цзд=3500руб.).
Таблица 4.3площадь станков.
Удельная площадь Si м2ед
в.Стоимость оснастки и дорогостоящего инструмента 15% от стоимости оборудования:
г.Стоимость дорогостоящего инвентаря 8% от стоимости оборудования:
Таблица 4.4капитальные вложения по одному (базовому) варианту.
Техническое оборудование включая доставку и монтаж
Оснастка дорогостоящий инструмент
Дорогостоящий инвентарь
Расчет капитальных вложений по второму (новому) варианту.
При определении экономического эффекта внедрения новой (техники технического процесса) в общих капитальных вложениях следует учитывать стоимость высвобождаемых основных фондов передаваемых для использования на других участках цехах.
где Коб Кпл Косн -стоимость выбывающего оборудования площадей оснастки руб.
Оценка выбывающего оборудования производится по его балансовой стоимости за вычетом фактического погашения износа и дополнительных затрат на демонтаж передвижку:
где Коб- стоимость реализуемого на сторону оборудования руб
Соб- балансовая (первоначальная) стоимость оборудования руб;
Сдем- затраты на демонтаж в процентах к стоимости оборудования руб;
а- годовая норма реновационных отчислений долей;
Т-время работы выбывающего оборудования лет.
где На-ежегодная норма амортизационных отчислений приходящихся на реновацию оборудования.
а)Стоимость технологического оборудования на участке по второму (новому) варианту
Таблица 4.5.Стоимость оборудования
Фрезерно-центровальный
Прейскурант основных цен.
б)Стоимость зданий и сооружений.
Площадь оборудования.Таблица № 4.6.
в)стоимость оснастки и дорогостоящего инструмента
г)стоимость дорогостоящего инвентаря
где Кнов-вновь вкладываемые капитальные вложения руб.
Таблица 4.7высвобождаемые средства подлежащие реализации руб.
Высвобождаемые средства
Сумма высвобожден. кап влож. руб.
Таблица 4.8Суммарная величина капитальных вложений по сравниваемым вариантам.
Элементы капитальных вложений
Сумма капитальных вложений руб.
Технологическое оборудование включая монтаж
Высвобождаемые кап. вложения реализуемые
Капитальные вложения подлежащие ликвидации
Всего кап. вложений принятых к расчету.
Расчет себестоимости по сравниваемым вариантам.
По первому (базовому) варианту берется готовая калькуляция себестоимости детали по цеху где она изготавливается.
По второму (новому) варианту заготовка и расход материалов не изменяется поэтому заводские станки калькуляции с 1-5 остаются без изменений. Сопоставляем затраты начиная с шестой статьи.
Содержание оборудования и других рабочих мест.
а)стоимость вспомогательных материалов
б)основная и дополнительная заработная плата вспомогательных рабочих обслуживающих оборудование определена ранее
в)отчисления на соц. страх 39% от основной и дополнительной заработной платы вспомогательных рабочих
г)затраты на эл. энергию технологическую стр.24[16]
где - расход электроэнергии в год кВт.ч
-количество установленного оборудования;
-средний коэффициент загрузки оборудования по мощности Км=07;
-коэффициент учитывающий потери в сети
Fэф- эффективный фонд времени станка
Цэл- цена 1кВт ч эл. энергии
д)затраты на сжатый воздух Sсж. в.)
где wсж.в- расход сжатого воздуха в год по всему оборудованию;
Цсж. в. – цена 1м3 (0206 руб.)сжатого воздуха.
где wсж. в - расход сжатого воздуха в год по всему оборудованию;
Нсж.в. – расход сжатого воздуха 1час на один станок (10м3час).
СОГЛАСОВАНО:УТВЕРЖДАЮ:
ПЛАНОВАЯ КАЛЬКУЛЯЦИЯ
Наименование калькуляционных статей расходов
Покупные комплектующие изделия полуфабрикаты и услуги кооперативных предприятий
Возвратные отходы (вычитаются)
Транспортно-заготовительные расходы 085%
Итого затрат на материал
Основная заработная плата производственных рабочих
Дополнительная заработная плата производственных рабочих 15%
Отчисления на социальное страхование 39%
Расходы на содержание и эксплуатацию оборудования
Цеховые расходы 3218%
Цеховая себестоимость-709%
Общезаводские расходы 210%
Прочие производственные расходы
Производственная себестоимость
Внепроизводственные расходы 13%
Полная себестоимость
Калькуляцию составил
РАСШИФРОВКА МАТЕРИАЛЬНЫХ ЗАТРАТ
РАСШИФРОВКА ЗАРАБОТНОЙ ПЛАТЫ
Расходы на текущий ремонт оборудования цехового транспорта и дорогостоящего инструмента.
Затраты на текущий ремонт определяются по проценту от стоимости оборудования транспорта и инструмента. Для оборудования этот процент принимаем 4% для транспорта – 8% для инструмента – 5%.
Расходы на текущий ремонт оборудования составляют 5%от стоимости оборудования
Расходы на текущий ремонт транспорта составляет125% от стоимости транспорта Sтр.=148752 руб.
Стоимость дорогостоящего инструмента составляет 15% от стоимости оборудования.
Содержание и расходы по эксплуатации транспорта.
Стоимость смазочных и обтирочных материалов определяется исходя из количества транспортных средств и норм расхода в год на единицу транспорта где. количества транспортных средств норм расхода в год на единицу транспорта
Расходы на амортизацию оборудования транспорта и дорогостоящего инструмента.
Затраты по данной статье определяются в соответствии с нормами амортизационных отчислений. Для оборудования амортизационные отчисления
где На.об На.т.– нормы амортизационных отчислений составляет для оборудования 12 % и для транспорта 16 %.
Для дорогостоящего инструмента амортизационные отчисления составляют 155% от их стоимости.
Расходы на содержание ремонт и замену малоценных и быстроизнашивающихся инструментов и приспособлений.
Расходы по данной статье принимаются в размере 10% от стоимости оборудования.
Цеховая себестоимость-62544%
Расчет экономической эффективности от внедрения мех участка обработки детали
где Ц оп – оптовая цена ведущей детали руб.
По первому (базовому) варианту
По второму (новому) варианту
Расчет выработки продукции за год на одного работающего товарной продукции: стр. 38[15]
где Nm- объем товарной продуции по участку руб;
R- численость работающихпо участку чел.
Расчет выработки продукции за год одного рабочего.
где Rр- численность работающих чел.
где Фосн- стоимость основных фондов по участку руб.
Расчет фондовооруженности труда.
Фондовооруженность определяет стоимость основных фондов приходящихся на одного работающего на участке и определяется по формуле:
Таблица 4.9 - Основные технико-экономические показатели по участку
А. Абсолютные показатели
Выпуск продукции N шт
Выпуск продукции N руб
Основные фонды Фруб в том числе
стоимость оборудования Фоб. руб.
стоимость зданий Фзд. руб
стоимость транспорт средствФтрздоб. руб
Общая площадь участка Fу м2
в том числе производственных Fпр. м2
Общая численность работающих Rобщ. чел.
вспомогоательных Rвсп. чел
Число рабочих дней Трдн
Полная спебестоимость еденицы руб
Оптовая цена еденицы Цоп. руб
Б. Относительные показатели
Вспомогательные рабочиее в %-ах к осн-ым %.
Среднемесячная зарплата основных раб. руб.
Выработка на одного работающего руб.
Выработка на одного рабочего руб
Фондоотдача Фотд. рубруб
ФондовооружоностьФв рубчел.
Энерговооруженность Эв. рубчел.
Выпуск продукции с 1м2 всей площади рубм2
Расчет экономической эффективности от внедрения механического участка обработки детали 25-49-46 крестовина
а)приведенные затраты по каждому из вариантов.
Снижение себестоимости
Годовой экономический эффект
Э = З1 +З2 = 46925650 – 40147050 = 6778600 руб.
б)планируемое снижение трудоемкости выпускаемой продукции
в)планируемый рост производительности труда
г)планируемое сокращение численности рабочих (условно высвобожденных)
д)планируемая экономия капитальных вложений
731000 – (-2400000) = 18131000 руб.
Аннотация.doc
Разработан рабочий маршрутно-операционный технологический процесс обработки детали. Также приведен анализ служебного назначения детали. Выполнены расчеты припусков режимов резания норм времени. Сконструированы станочные приспособления для сверлильной и шлифовальной операций. Для обработки торцевых цапф сконструированы протяжки. Разработано контрольное приспособление для контроля технических требований чертежа
В соответствии с заданием выполнены разработки по охране труда на участке.
Рассмотрены вопросы экономики и организации производства. Здесь выполнены соответствующие расчеты для участка составлена смета расходов плановая калькуляция себестоимости а также технико-экономических показателей участка.
Технологическая часть
1Назначение и конструкции детали
2Анализ технологичности конструкции детали
3Определение типа производства
4Анализ существующего технологического процесса.
5Методы получения заготовки
7Расчет режимов резания
8Расчет норм времени
Конструкционная часть.
1Расчет станочного приспособления.
2Расчет сверлильного приспособления.
3Расчет шлифовального приспособления.
4Расчет режущего инструмента.
5Расчет плоской протяжки.
6Расчет фасонной протяжки.
7Разработка контрольного приспособления.
Организационная часть.
1Расчет потребности в оборудовании по участку
2Расчет численности рабочих участка.
3Расчет площади участка.
4Расчет основного фонда заработной платы.
Экономическая часть.
1Экономическое обоснование эффективности внедрения участка
2Методика расчета экономической эффективности.
3Расчет экономической эффективности от внедрения мех участка обработки детали.
Безопасность и экологичность проекта
1Анализ техпроцесса обработки детали с точки зрения охраны труда и техники безопасности.
2Техника безопасность при работе на станках.
3Обработка резанием с применением СОЖ.
4.Производственная санитария
5.Пожарная безопасность.
6.Организация работы по охране труда на предприятии.
7.Производственное освещение.
8.Расчет уровня звукового давления в расчетной точке.
Выбор базы для сравнения и обеспечения условий сопоставимости вариантов
Расчет капитальных вложений
Расчет товарной продукции по участку.
Расчет фондовооруженности труда
Расчет экономической эффективности от внедрения механического участка обработки детали
Список использованной литературы
Человеческое общество постоянно испытывает потребность в новых видах продукции либо в сокращении затрат труда при производстве основной продукции. В общих случаях эти потребности могут быть удовлетворены только с помощью новых технологических и новых машин необходимых для их выполнения. Следовательно стимулом к созданию новой машины всегда является новый технологический процесс возможность которого зависит от уровня научного и технического развития человеческого общества.
Путь создания машины сложен. Замысел к созданию выражается в виде формулировки служебного назначения машины являющегося исходным документом в проектировании машины. Для изготовления спроектированной машины разрабатывают технологический процесс и на его основе создают производственный процесс в результате которого получается машина нужная для выполнения технологического процесса изготовления продукции и удовлетворения возникшей потребности.
Машина полезна лишь в том случае если она обладает надлежащим качеством т.е. способностью удовлетворить потребности необходимые для ее создания.
Создавая машину человек решает две задачи:
Сделать машину качественной и обеспечит экономию труда в получении производимой с ее помощью продукцией;
Затратить меньшее количество труда в процессе создания и обеспечения качества самой машины.
Производственный процесс изготовления машин является системой связи свойств материалов размерных информационных временных и экономических. Технология машиностроения исследует эти связи с целью решения задач обеспечения в процессе производства требуемого качества машины наименьшей себестоимости и повышения производительности труда.
На машиностроительных заводах успешное внедрение новой техники зависит от степени его оснащения современной технологической оснасткой. Для всех видов технологической оснастки характерно наличие значительного числа деталей разнообразной и сложной формы. Большинство деталей в процессе изготовления подвергается различным видам обработки: механической термической электрохимической и т.д.
Производительность процесса обработки зависит от режимов резания (скорости глубины подачи) а следовательно от материала режущей части инструмента его конструкции геометрических параметров лезвий инструмента и т.д.
Современное производство предъявляет повышенные требования к технологической оснастке:
точность базирования изделий
жесткость обеспечивающая полное использование мощности оборудования на черновых операциях и высокую точность обработки на чистовых операциях
высокая гибкость сокращающая время на наладку и замену оснастки
универсальность позволяющая обрабатывать изделия определенного типа размеров с минимальным временем на переналадку
Дипломный проект является большой самостоятельной работой будущего технолога направленной на решение конкретных задач в области совершенствования технологии организации производства и улучшение технико-экономических показателей работы участка. Наряду с этим дипломное проектирование закрепляет умение студента пользоваться справочной литературой ГОСТами таблицами номограммами нормами и расценками сочетая справочные данные с теоретическими знаниями полученными в процессе изучения курса. Проект закрепляет углубляет и обобщает знания полученные студентами во время лекционных и практических занятий.
Дипломный проект представляет собой расчетно-графическую работу в которой обобщаются все технологические познания и навыки приобретенные во время обучения. В дипломном проекте содержатся моменты определяющие понимание дипломантом значения для народного хозяйства той отрасли промышленности в которой разрабатывается дипломный проект. Максимальное приближение дипломного проекта к реальным условиям производства повышает заинтересованность дипломанта в более глубокой разработке проекта.
Оглавление.doc
1Назначение и конструкции детали
2Анализ технологичности конструкции детали
3Определение типа производства
4Анализ существующего технологического процесса.
5Методы получения заготовки
7Расчет режимов резания
8Расчет норм времени
Конструкционная часть.
1Расчет станочного приспособления.
2Расчет сверлильного приспособления.
3Расчет шлифовального приспособления.
4Расчет режущего инструмента.
5Расчет плоской протяжки.
6Расчет фасонной протяжки.
7Разработка контрольного приспособления.
Организационная часть.
1Расчет потребности в оборудовании по участку
2Расчет численности рабочих участка.
3Расчет площади участка.
4Расчет основного фонда заработной платы.
Экономическая часть.
1Экономическое обоснование эффективности внедрения участка
2Методика расчета экономической эффективности.
3Расчет экономической эффективности от внедрения мех участка обработки детали.
Безопасность и экологичность проекта
1Анализ техпроцесса обработки детали с точки зрения охраны труда и техники безопасности.
2Техника безопасность при работе на станках.
3Обработка резанием с применением СОЖ.
4.Производственная санитария
5.Пожарная безопасность.
6.Организация работы по охране труда на предприятии.
7.Производственное освещение.
8.Расчет уровня звукового давления в расчетной точке.
Методика расчета черновой части протяжки.
Список использованной литературы
2 Конструкторск часть.doc
1Расчет станочного приспособления.
1.1Расчет станочного приспособления для обработки на вертикально-сверлильном станке 2Р135Ф2
Операция 025 состоит из четырех переходов. Наибольшая сила резания возникает при сверлении отверстия ø 8мм
Рисунок 2.1 Схема зажима
где Q- сила необходимая для зажима Н
момент резания при сверлении Н м
коэффициент трения на направляющей поверхности
Момент резания при сверлении отв. 8мм.
Определим коэффициент запаса который применяют чтобы обеспечить надежность зажима обрабатываемой заготовки.
Зависит от состояния поверхности заготовки процесса затупления режущего инструмента и других факторов возникающие в процессе обработки.
Сила зажима одним прихватом
Усиление пневмоцилиндра для данной силы зажима
Рисунок 2.2 Схема сил зажима
где F- усиление пневмоцилиндра для получения заданной силы зажима Н.
Н-высота прихвата мм
растояние между силой зажима и усилением пневмоцилиндра мм
Расчетный диаметр пневмоцилиндра
где давление сжатого воздуха
В нашей конструкции приспособления применяется F- образный прихват который при зажиме и отжиме детали разворачивается на 90°
Высота подъема прихвата при его отводе
где S-длина дуги поворота прихвата
угл подъма винтовой канавки
угол поворота прихвата
Принимаем ход штока 35мм.
Погрешность приспособления
1.2Расчет шлифовального приспособления.
Расчет станочного приспособления для обработки на плоскошлифовальном станке 3Г71.
Рисунок 2.3 Схема сил резания и сил зажима.
где и =01-коэффтциенты трения между деталью и установочноми зажимами элементами
Сила резания при шлифовании
Сила необходимая для зажима детали
В конструкции расчетного приспособления применим винтовой откидной прихват
Рисунок 2.4 Схема действия сил при зажиме прихвата.
длины плеч рычага мм
учитывающий потерии на трение
Определим номинальный наружный диаметр винта
где -допустимое напряжение на ратяжение;
Из конструктивных соображений принимаем
Погрешность припособления
и - зазор между пальцами и втулкой.
допуск на расстояние между втулками
2Расчет режущего инструмента
2.1Расчет плоской протяжки.
Припуск на обе плоскости
Подача на зуб табл.42 стр264[11]
Шаг зубцов стр72[11]
Размер стружечных канавок
Коэффициент заполнения канавки стружкой стр80[11]
углы режущих элементов
размеры поперечного сечения секций
Размеры площадей поперечного сечения секция по первой стружечной канавке
Ширина протягиваемой плоскости
Назначаем станок 7Б705
Суммарная длина режущих кромок участвующих в резании
Число режущих зубьев
т.к пользуемся формулой 9 стр.77[11]
Сила протягивания для одной секции
Высота на первом зубце
Количество режущих зубцов:
Высота секции по последнему зубцу
Поскольку заготовка предварительно обработана буферный зубец не делается
Длина секции стр. 272[11]
Секции изготовим цельными.
2.2.Расчет фасонной протяжки.
Суммарный поъдем секции стр268[11]
Размер стружечных канавок табл.7 стр68[11]
Размеры поперечного сечения секций
Размеры отверстий под винты: Резьбовых-М10 глубина 14мм
Проходных 17мм глубина11мм.
Минимальная площадь поперечного сечения секций
Количество генераторных зубцов:
Смещение профиля на каждый зубец принимаем равным 0003 мм. стр.299[11]
Общее смещение генераторных зубцов стр. 299[11]
Общее смещение профиля калибрующих и генераторных зубцов стр. 299[11]
Профильный угол протяжки
Высота уступов измеренная нормально к боковой стороне обрабатываемого профиля. стр. 303[11]
Диаметр контрольного шарика стр. 620[19]
Где шаг резьбы; половина угла профиля
Расчет числа болтов крепящих секцию протяжки
Материал болтов Сталь 35Мпа = 300 мПа = 100 мПа
d- диаметр болта = 8.1мм
f- коэффициент трения =02
Принимаем 3 болта М10
Рисунок 2.7 Крепление инструмента.
3Разработка контрольного приспособления
Проверяемые ТУ детали 25-49-46
)- перпендикулярность
)х- пересечение осей
Работа на приспособлении.
)При проверке первого пункта ТУ деталь положить на призму (поз №1) довести до упоров (поз № 6)и (позиции №7) поставить индикатор I на «0» затем повернуть деталь в горизонтально плоскости на снова положить на призму довести до упоров и смотреть показания индикатора. Деталь считать годной если показания индикатора в пределах допуска умноженного на 2.
)При проверке второго пункта деталь положить на призму корпус (поз.№5) с индикатором II продвинуть к поверхности Д и поставить на «0». Деталь проверить противоположной стороны и посмотреть показания индикатора. Деталь считать годной если показания индикатора в пределах допуска. Повторить для других противолежащих поверхностей.
)При проверке третьего пункта положить деталь на призму довести до упоров поставить индикатор III на «0». Затем повернуть деталь в вертикальной плоскости положить снова на призму и смотреть показания индикатора. Деталь считать годной если показания индикатора в пределах допуска умноженного на 4.
цена деление индикатора.
Сх. дейст. сил.dwg

Табл Полная себестоимость и осн. ц. по срав-ым в-ам.doc
Экономия () Перерасход (+)
Транспортно-заготовительные расходы
Основная зарплата производственных рабочих.
Доп. зарплата производственных рабочих.
Отчисления на соц. страх.
Цеховая себестоимость
Общезаводские расходы
Заводская себестоимость
Воспроизведенные расходы
Полная себестоимость
Список использованной литературы.doc
Гобацевич АФ курсовое проектирование по технологии машиностроении –Мн. Высшая школа 1983-256с
Справочник технолога-машиностроителя. Под ред. АГ Косиловой. - М. машиностроение 1972-I. II.-694с
режимы резания металлов: Справочник. Под редакцией Ю.В.Барановского. - М. машиностроение 1972-408с
Никифоров Н А. Сборник задач и примеров по резанию металлов и режущему инструменту. - М. машиностроение 1990-448с
Обработка металлов резанием Справочник технолога. Под редакций А.А Панова. М. машиностроение 1988-736с
Общемашиностроительные нормативы времени вспомогательного на обслуживание рабочего места и подготовительно-заключительного для технического нормирования. Серийное производство. М. Машиностроение 1974-421с
Горошкин АК Приспособление для металлорежущих станков. Справочник М. машиностроение 1971-384с
Белоусов АП Проектирование станочных приспособлений М. машиностроение 1974-263с
Добрыднев И.С.Курсовое проектирование по предмету «Технология машиностроения». М. машиностроение 1985-184с
Станочные приспособления. Справочник под ред. БН Вардашкина. М. машиностроение 1984-I.I-592с
Щеголев ВА. Конструирование протяжек. М. Л Машшз 1960-352с
Долин ПА. Справочник по технике безопасности. М. Энергоатомиздат1984-824с
Средства защиты в машиностроении. Расчет и проектирование .под ред. СВ Белова. М. машиностроение 1989-368с
Глава СНиП II-1277. Нормы проектирования Защита от шума. М. Стройиздат 1978-49с
Организация планирование и управление предприятием машиностроения. Методические указания к курсовому проекту для студентов машиностроительного факультета.ЧГУ1986-48с
Организация планирование и управление предприятиями машиностроения. Методические указания к организационно-экономической части дипломного проекта. ЧГУ 1984-36с
Маслов ЕН. Теория шлифования материалов. М. машиностроение 1974-440с
Справочник инструментальщика. Под редакцией ИА. Ординарцова - Л. машиностроение 1987-846с
Справочник по производственному контролю в машиностроении. Под ред. АК. Кутая Л. машиностроение 1974-975с
5 БЖД часть.doc
Развитие машиностроения идет по пути разработки новых типов станков оборудования самого различного назначения совершенствования технологии производственного процесса и т.д. Все это ставит перед машиностроителями большие разносторонние и сплошные задачи по изучению вопросов охраны труда.
Улучшение условий труда повышение его безопасности и безвредности имеет большое экономическое значение. Оно влияет на экономические результаты производства – на производительность труда качество и себестоимость выпускаемой продукции.
Улучшение условий труда и его безопасность приводят: к снижению производственного травматизма профессиональных заболеваний инвалидности
А также приводит к уменьшению затрат на оплату льгот и компенсаций за работу в неблагоприятных условиях труда на оплату последствий такой работы (временной и постоянной нетрудоспособности) на лечение переподготовку работников производства в связи с текучестью кадров по причинам связанным с условиями труда.
Спроектированный в дипломном проекте участок по механической обработке детали 25-49-46-крестовина должен свести к минимуму количество случаев производственного травматизма и профессиональных заболеваний. Необходимо организовать такие условия производства при которых обеспечивается безопасность труда работников.
1Анализ техпроцесса обработки детали 25-49-46-крестовина с точки зрения охраны труда и техники безопасности.
Технологический процесс обработки крестовины состоит из двенадцати операций: фрезерно-центровальная два токарных трех сверлильных протяжная слесарная термическая и трех шлифовальных.
Усилия прилагаемые к рукояткам рычагов управления в зависимости от способов перемещения и частоты использования.
Способы перемещения (преимущественно)
Наиболее допустимое усилие Н (кгс). При частоте использования в смену.
Кистью с предплечьем
По таблице видно что заготовки подаются на стол станка одной рукой (4кг)
Рассмотрим опасные и вредные производственные факторы по отдельным операциям.
Операция 005 – фрезерно-центровальная производится на фрезерном станке модели МР-71М.
Опасными производственными факторами являются:
-движущиеся части и механизмы станка
-вращающийся инструмент
-движение стола и шпиндельных головок
-острые кромки и заусенцы деталей и заготовок.
Для обеспечения безопасности работников необходимо применять защитную спецодежду и средства индивидуальной защиты (защитные очки или маску) ограждения.
Операция 010 015-токарная станок 16А20Ф3.
Опасность представляет вращение шпинделя с закрепленной в ней деталью и перемещение суппортов с резцами.
Применяем защитный экран.
Операция 020 025 030-сверлильная станок 2Р135Ф2-1.
Вращение шпинделей и сверло. Поэтому перед работой надо проверить надежность крепления патронов в шпинделе станка. Закрепляя сверло надо следить за плотностью его посадки в патроне и точностью центрирования с осью шпинделя станка. При отсутствии осторожности шпиндель и сверло могут захватить одежду или волосы.
При работе одежда у рабочего должна быть застегнута на все пуговицы и в том числе и на рукавах а на голове должен быть головной убор также обязательно наличие защитных очков.
Применяем спецодежду и средства индивидуальной защиты (защитные очки или маску) ограждение.
Операция 040 045 050-шлифовальная. Станок ВШ-601 и ЗГ71М
Опасность представляет вращение круга и детали.
Ограждаем кожухами а для снижения пылеобразования обработку производим с СОЖ с местным отсосом пыли (предусмотренным на станке) спецодежду и средства индивидуальной защиты (защитные очки или маску).
Вредными производственными факторами при работе на металлорежущих станках является шум и воздействие СОЖ поэтому необходимо оградить воздействие вредных производственных факторов на организм работника.
2Техника безопасности при работе на станках.
2.1Фрезерно-центровальном.
Требование безопасности во время работы.
установить и снимать деталь и инструменты (режущие) только после полного останова станка;
не работать без кожуха прикрывающего сменные шестерни;
остерегаться наматывания стружки на обрабатываемый предмет и не направлять стружку на себя;
Не удалять стружку руками и инструментом пользоваться при этом специальными крючками и щетками;
при возникновении вибрации отключить станок проверить крепление фрезы и детали;
при обработке применять режимы резания указанные в операционной карте для данной операции;
не вводить руки в опасную зону вращения фрезы применять ограждения и отвода стружки.
Не удалять стружку руками и инструментом пользоваться при этом
при обработке применять режимы резания указанные в операционной карте для данной операции
Обязательно остановить станок и выключить электродвигатель:
a)при уходе от станка даже на короткое время если не поручено обслуживание двух или несколько станков;
b)при временном прекращении работы;
c)при перерыве подачи электрической энергии;
d)при уборке чистке смазке станка
e)при обнаружении неисправности в оборудовании;
f)при проверке или зачистке режущей кромки резца
Во время работы не наклонятся близко к шпинделю с режущим инструментом. Установку деталей на станок и снятие их со станка производить в том случае когда шпиндель с режущим инструментом находятся в исходном положении. А также
при переходе от работы всухую к работе с СОЖ следует подождать пока круг охладится и только после этого начинать работу с СОЖ;
по окончании работы с СОЖ выключить подачу жидкости и переключить станок на холостой ход на 2-3 минуты для подсушки круга;
прежде чем остановить станок отвести круг от детали
не приближать лицо к вращающемуся шпинделю и детали при наблюдении за ходом обработки
не выдувать ртом пыль из отверстий.
3 Обработка резанием с применением СОЖ.
Правильный выбор СОЖ и ее использование позволяют повысить стойкость инструмента уменьшить шероховатость поверхности заготовки. При обработке хрупких материалов хорошо зарекомендовали себя 3-10% эмульсии на основе эмульсора «Укронол-1»
Таблица 5.2 Содержание «Укронол-1».
Агрегатное состояние
Индустриальное масло И-12А
Перечень рекомендуемых профилактических средств выпускаемых промышленностью.
Вредные производственные факторы.
Дерматологические средства.
Защитный крем «Силиконовый» ПМС-30-чредство для рук.
Вода растворы кислота щелочь.
Защитный крем для рук «Силиконовый» защитная паста ИЭР-2ФС42-95-72
Паста отмывочнозащитная с солидолом ФС42-382-72 паста защитная «Айро» средство защиты для рук «Невидимка»
В соответствии с перечнем рекомендуемых профилактических средств при работе с СОЖ применяем дерматологические средства. Защитный крем для рук «Силиконовый» защитная паста иэр-2ФС4295-72.
Меры предосторожности при работе при СОЖ.
Для защиты от вредного влияния СОЖ на кожу необходимы установка щитков защищающих от брызг жидкости; применяем щеток для уборки со станка; наличие обтирочного материала; мытье рук и предплечий теплой водой с мылом смена специальной одежды; профилактическое смазывание кожи рук для защиты.
4Производственная санитария.
Обеспечение санитарных условий труда предназначено для соблюдения санитарных норм воздушной среды освещенности чистоты участков. Одним из необходимых условий здорового труда является обеспечение санитарных норм воздушной среды в рабочей зоне помещений те в пространстве высотой до 2метров над уровнем пола.
Оптимальные нормы влажности воздуха и скорости движения воздуха в рабочей зоне производственных помещений.
Относительная влажность %
V движение воздуха мс не более
Холодный и переходный период года.
В соответствии с таблицей в зависимости от сезона года категории работ температура оптимальная влажность скорость движения воздуха должны соответствовать оптимальным нормам на производственных участках.
Обслуживание работающих предназначено для создания нормальных условий работы путем организации бытового и медицинского обслуживания. К ним относятся в радиусе 50-80м-курительные санитарные узды питьевые устройства санитарные посты с предметами первой медицинской помощи.
5Пожарная безопасность.
В нашем случае в цехе обрабатывается негорючие вещество сталь 20ХМ3А и материалы в холодном состоянии. В соответствии СН и II-2-80 цех относится к категории «Д» по пожарной опасности и «II» степени огнестойкости здания.
Минимальные допустимые пределы огнестойкости:
несущие стены кологнны-2 часа;
наружные стены из навесной панели-025часа
внутренние стены и перегородки -025часа
несущие перекрытия -75часа
несущие конструкции покрытий-025часа
Для зданий II ступени огнестойкости распространение огня допускается лишь по конструкциям перегородок на величину не более 40см
На участке необходимо установить первичные средства пожаротушения: вода ящики с песком ломы топоры лопаты огнетушители ОЖ-7 (водный раствор сульфата) ПК на расстоянии 25м друг от друга.
Для предотвращения пожара проводятся мероприятия: организационные эксплуатационные технические и режимного характера.
Организационные мероприятия это обучение рабочих и служащих пожарной безопасности проведение бесед лекций инструктажи.
Эксплуатационные правильная эксплуатация оборудования своевременные осмотры ремонт.
Режимные. Запрет курения - в неустановленном месте. Хранить отработанную ветошь в специально отведенном месте с вентиляций с цель предотвращения самовозгорания.
6Организация работы по охране труда на предприятии.
Охрана труда на предприятии связана с профилактикой травматизма и заболеваемости с сохранением работоспособности в течение всего рабочего дня. В соответствии с ГОСТ 12.0.004-74 установлены обязательные инструктажи по безопасности труда.
Таблица 5.5 Инструкция по ТБ
В связи с чем проводятся
В отделе охраны труда.
Инструктор по охране.
В связи с поступлением на работу
На рабочем месте (индивидуально)
Обучение безопасным приемам работы.
На рабочем месте с группой рабочих одной профессии.
Через 6 месяцев с целью проверки знаний по охране труда.
С изменением правил по охране труда (тех прочеса)
Перед выполнением опасных работ.
На всех предприятиях широко применяется трехступенчатый контроль
Таблица 5.6 Трехступенчатый контроль
Мастер общественный инспектор по охране труда
Ежедневно перед началом работы
Начальник цеха инженер по охране труда
Главный инженер председатель профкома с привлечением гл. инженера и энергетика.
Обеспечение средствами индивидуальной защиты производится во всех необходимых случаях: спец. одежда обувь очки и т.д.
7Производственное освещение.
Правильно рассчитанная и смонтированная система освещения играет существенную роль в снижении производственного травматизма уменьшая потенциальную опасность многих производственных факторов создавая нормальные условия работы органам зрения и повышая общую работоспособность организма.
При проектировании участка предусматриваем естественное верхнее освещение осуществляемое через световые проемы в перекрытиях через аэрационные фонари. Кроме этого вечернее время суток (вторая смена) а также в пасмурную погоду предусмотрено распределяющее световой поток без учета расположения оборудования кроме этого на каждом рабочем месте имеется местное освещение.
По всему цеху предусмотрено аварийное и эвакуационное освещение а также охранное для несения дежурства охраны.
8 Расчет уровня звукового давления в расчетной точке.
При проектировании технических процессов необходимо знать ожидаемы уровни звукового давления на рабочих местах чтобы еще на стадии проектирования принять меры по снижению шума до допустимого уровня звукового давления
Схематическое расположение станков на участке
Рисунок 5.1 Определение расчетной точки.
при r5rmin не принимаем в расчет.
В расчетах учитываем три источника шума: станки сверлильные 2Р135Ф3 и протяжной 7Б75.
Уровни звукового давления в расчетной точке при одновременной работе всех трех станков ДБ:
Где - определим по таблице 4.3 стр.107[13]
активный уровень звуковой мощности ДБ
коэффициент учитывающий влияние ближнего поля (принимается по графику рис. 4.3 стр.107[13] при )
фактор направленности иш для ши с равномерным излучением звука Ф=1;
площадь воображаемой поверхности геометрической формы окружающей источник и проходящей через расчетную точку.
постоянная помещения ; стр.4[14]
где постоянная помещения на средне геометрической частоте 1000 Гц
частный множитель тбл.4 стр.5[14]
коэффициент учитывающий нарушение диффузности звукового поля в помещении рис. 3 стр.4[14]
На спроектированном участке шум в расчетной точке не превышает допустимого уровня
Таблица 5.7 уровни звукового давления.
Средние частоты активных полос Гц.
Уровни звукового давления ДБ.
Для соблюдения требований по охране труда техники безопасности и пожарной безопасности на проектируемом участке разработаны следующие организационные мероприятия:
Обеспечение всех видов металлообрабатывающих станков оградительными устройствами;
Для лучшего освещения лампы накаливания заменены газоразрядными люминесцентными лампами;
Для защиты рабочих от поражения электрическим током оборудование должно быть заземлено. Предусмотрены СИЗ решетки резиновые коврики.
Каждый рабочий при поступлении на работу проходит инструктаж по технике безопасности инструктаж проводится параллельно с обучением рабочих безопасным приемам труда и освоением оборудования на данном участке. После прохождения рабочим вводного инструктажа он расписывается в журнале. Мастер (инструктор по технике безопасности) следит за соблюдением техники безопасности на рабочем месте. Регулярно (один раз в три месяца) мастер проводит повторный инструктаж в объеме первичного.
Рабочим выдается специальная одежда с учетом условий труда.
Для обеспечения противопожарной защиты на участке установлены огнетушители. Средства тушения должны находиться в исправном состоянии. Разработан и доведен до каждого работающего план эвакуации на случай пожара.
При размещении на участке оборудования должны быть учтены минимальные расстояния между станками (1.5 метра) стеллажами и элементами зданий (1 метр) что исключает загромождение проходов и проездов.
На участке установлены необходимые грузоподъемные механизмы.
На участке имеются информационные и предупреждающие знаки таблицы и указатели.
Научно-исследовательские разработки.
Метод расчета оптимальных параметров черновой части протяжки
Расчет черновой части протяжек включает определение геометрических параметров зубьев (шага длины задней поверхности высоты зуба) количества зубьев в группе подъема на черновые зубья. Все остальные параметры - длина протяжки число зубьев конструкция переходной чистовой калибрующей частей и т.д. - являются производными от вышеперечисленных.
Известные методы расчета протяжек основаны на назначении величины подъема черновых зубьев и последующей подгонке значений остальных параметров инструмента под выполнение условий: по осевой составляющей силы резания по прочности инструмента по помещаемости стружки по длине протяжки и т.д. Если какое-либо условие не соблюдается корректируется подъем на черновой части. При этом нет гарантии что выбранный вариант инструмента является оптимальным по принятому критерию так как для поиска оптимального решения необходим просчет множества вариантов.
Наиболее важными параметрами определение которых трудоемко являются подъемы на зубья и их шаг.Критериями оптимальности конструкции протяжки могут быть: наименьшая длина инструмента? наибольшая наработка между отказами наибольшее количество переточек наименьшее количество зубьев наименьшая осевая составляющая силы протягивания и т.п. Конструктором выбирается один критерий оптимизации а остальные рассматриваются как ограничения. Задача одновременного соответствия нескольким критериям оптимизации не ставится хотя очевидно что например протяжка имеющая одновременно наибольшую наработку и наибольшее количество переточек лучше чем протяжка имеющая только наибольшую наработку.Ниже предлагается метод расчета рабочей части протяжного инструмента который позволяет не только совместить насколько это возможно критерии оптимизации но и исключает необходимость ее пересчета для поиска оптимального варианта удовлетворяющего многочисленным ограничениям. Длина черновой части протяжки L0 определяется по формуле.
L0= Lобщ-Lп-Lк=Aо ZztоSо(6.1)
где Lобщ - общая длина рабочей части протяжки мм;
Ln Lч Lк -длина переходной чистовой и калибрующей частей соответственно;
А0- припуск на черновую часть на сторону мм;
Zz - число зубьев в черновой группе;
t0 - шаг черновых зубьев мм
С достаточной для практических вычислений точностью можно принять L0 =(06 08) Lобщ. Тогда рабочая часть протяжки не превысит заданной конструктором длины Lобщ если на основании (5.1) будет выполнено неравенство (6.2)
Осевая составляющая силы резания определяется по формуле:
где lp - длина режущих кромок одного зуба при Zz = 1
(например для круглой протяжки lp =D
где D- диаметр зуба мм;
Zz - число зубьев одновременно участвующих в работе (округляется до большего целого) Zp =ln t0
kp- поправочный коэффициент на условия обработки;
q- удельная осевая сила резания Нмм с достаточной степенью точности в диапазоне подъемов S0 = 002..02 мм q = 5300-S0γ-032
Осевая составляющая сила резания не превысит допустимого значения если на основании формулы (5.3) будет выполнено неравенство
где [P] - допустимое значение осевой составляющей силы резания Н.
Значение [Р] может быть принято по характеристике станка с соответствующим запасом а может быть выбрано исходя из других соображений (например по прочности детали).
Исходя из геометрических параметров профилей зубьев по ГОСТ 20365 – 75
где h0 - высота зуба мм. Поскольку h0 = 113√k0lnS0 то при
t0≥ в0+173√k0lnS0 (6.5)
будет обеспечена и требуемая помещаемость стружки ( k0— коэффициент помещаемости) и необходимая длина задней поверхности которая определяет количество переточек при правильном проектировании чистовой части. Можно принять в0 =(2 3)d2tgaк
где - допуск на размер обрабатываемой заготовки мм;
αк — задний угол последнего калибрующего зуба.
Необходимо чтобы в процессе резания участвовало не менее определенного числа зубьев одновременно. Поэтому
В неравенстве (5.6) значение Zр задается конструктором но оно не должно быть менее двух.
Если существует ограничение по равной наработке то
где Sрч - подъем на зуб удовлетворяющий равной наработке черновой и чистовой частей протяжки.
Для мелкоразмерных протяжек. если существует возможность появления опасного сечения под первым зубом можно ввести еще одно ограничение – в неравенстве (5.4) заменить [Р] на
5(Dн-226√коlпSo)2 [s]
где Dн - диаметр передней направляющей мм;
[]- допускаемые напряжения растяжения МПа.
Нетрудно видеть что условия (6.2) (6.4) - (6.7) определяют границы сочетания t0 и S0 при которых работоспособность протяжки обеспечивается по всем параметрам.
На рисунке интерпретированы эти зависимости. При этом для построения зависимостей (6.2)(6.4)(6.6) достаточно выполнить лишь одно вычисление для условия (6.5) - достаточно двух-трех вычислений для условия (6.7) вычислений не требуется. Значения S0 задаются произвольно из области реальных значений (удобно принимать S0 = 005мм или S0 = 01 мм).
Заштрихованная область на рисунке является областью значений t0 и S0 при которых протяжка работоспособна.
В этой области находятся и оптимальные по различным критериям варианты и все остальные. Имея график конструктор не только может выбрать оптимальный по заданному критерию вариант но и изменять этот критерий и другие исходные данные.
Рисунок - 6.1. Область сочетаний шагов черновых зубьев t0 и подъемов на зуб S0 определяющих работоспособный вариант инструмента:
- зависимость (5.2) 2 - зависимость(5.4)
- зависимость (5.5) 4 - зависимость (56)
- зависимость (6.7).
Например если будет выбрано сочетание S0 и t0 в точке А графика то протяжка будет соответствовать критерию наибольшей наработки в точке Б - наименьшей осевой составляющей силы резания в точке В - наименьшей длины. Принятые после округления значения параметров не должны выходить из области допустимых значений. При этом рекомендуется S0 округлять с точностью до 0005мм t0 - с точностью до 05 мм.
Следует отметить что любой из вариантов выбранный из области допустимых значений параметров удовлетворяет и критерию оптимизации «наибольшее количество переточек» (поскольку зависимость (5.5) это предусматривает) и другому критерию заданному конструктором (точки А Б В). График представленный на рисунке может видоизменяться в зависимости от конкретных исходных данных Соответственно изменится и положение точек А Б В но в любом случае точка А соответствует наименьшему подъему на зуб точка Б наиболее удалена от линии 2 точка В наиболее удалена от линии 1
Предложенный метод открывает возможность отказаться от круглых протяжек с числом зубьев в группе больше двух и протяжек шлицевых эвольвентных и трапецеидальных с групповым построением зубьев поскольку всегда находится область допустимых значений параметров S0 и t0
удовлетворяющая zr=2 для круглых протяжек и zr=1для шлицевых эвольвентных и трапецеидальных При этом подъемы зубьев оказываются меньшими по величине что благоприятно сказывается на наработке. Если при проектировании прямобочкой шлицевой протяжки выбрано S0 006 то возможно применение протяжек с zr=1 без стружкоразделительных устройств. Необходимым условием работоспособности протяжки является выполнение удлиненного профиля зубьев. При расчете формулу (5.5) необходимо изменить добавив в правую часть величину удлинения (05 15 мм). Это позволяет в ряде случаев заменить двухпроходное протягивание однопроходным.
Основными достоинствами изложенного метода являются:
а) безошибочный поиск оптимального варианта по любому критерию;
б) возможность оперативного изменения исходных данных и визуальное наблюдение результатов;
в) предварительное задание требуемой длины инструмента что особенно важно при проектировании крупногабаритных протяжек когда технические данные станков ограничивают длину инструмента.
1 Технологическая часть.doc
1Назначение и конструкция детали
Крестовина предназначена для передачи крутящего момента.
Нагруженность и сложность формы крестовины предопределяют экономически целесообразный способ изготовления заготовки – поковка штампованная из материала сталь 20ХН3А
Применение легированной стали 20ХНЗА технически и экономически целесообразно и оправдано так как оно дает экономический эффект за счет повышения надежности и долговечности крестовины.
Имеет четыре тщательно обработанные цапфы ø33635h6 на которые устанавливается игольчатые подшипники без внутренней обоймы. Внутренней обоймой для подшипника является сами цапфы. Две цапфы крестовины входят в проушины фланца а две другие в проушины муфты. Вал имеет два карданных шарнира. Карданный вал соединяющий выходной вал коробки переменных передач и конических передач имеет крестовины 25-49-46-01(с четырьмя отверстиями КГ 18) для улучшения технологического обслуживания узла 46-49-112сб. В узел 46-49-111сб где техническое обслуживание доступнее устанавливается крестовина 25-49-46(с 1-им отверстием КГ 18)
Канавки на торцах цапф необходимы для поступления смазки к игольчатым подшипникам через отверстия ø8 мм. Отверстие КГ 38 является технологическим для обеспечения получения отверстий ø8 мм (для выхода сверла) при сборке оно глушится.
В процессе эксплуатации крестовина испытывает динамические знакопеременные нагрузки.
Цапфы крестовины работают на изгиб и срез. Решение повышение предела усталости предела выносливости и повышение релаксационной стойкости за счет исключения в поверхностных слоях структурных и фазовых изменений. Микротрещин и растягивающих остаточных напряжений: а) поднять предел упругости - высокое сопротивление малым пластическим деформациям; б) создать на поверхности напряжения обратного знака с целью получения низких напряжений в опасных точках.
Таким образом материал детали должен иметь:
Хром (06 09%) – повышает твердость предел прочности износостойкость коррозионную стойкость прокаливаемость пластичность жаропрочность и жаростойкость электросопротивляемость а также препятствует рост зерна.
Никель (015-030%) - повышает прочность прокаливаемость склонность к отпускной хрупкости снижает Vкр. к тому же никель обеспечивает большой запас вязкости.
Кремний (017 - 037%) - положительно влияет на структуру механические и технологические свойства стали: снижает критическую скорость охлаждения увеличивает прокаливаемость уменьшает скорость распада мартенсита сильно упрочняет феррит повышает прочность твердость и прежде всего упругие свойства стали ( в; 02; -1) увеличивает сопротивление коррозии снижает вязкость.
Крестовину изготавливают из стали 20ХНЗА с последующим термообработкой. Улучшение и цементации поверхности цапфы до твердости HV 60-65.
Таблица 11Химический состав % ГОСТ 4543-71
Механические свойства
Предел прочности при растяжении
Относительное удлинение после разрыва
Относительное сужение
Предел текучести условный
2Анализ технологичности конструкции детали
Деталь – крестовина 25-49-46 изготавливается из штампованной поковки легированная сталь 20ХНЗА. Конфигурация наружного контура не вызывает значительных трудностей при получении заготовки.
Обрабатываемые цапфы 33635h6 должны быть выполнены в пределах указанных отклонений и с заданной точностью т. к. цапфы служат внутренней обоймой одеваемых на них игольчатых подшипников.
Необходимая точность и чистота поверхности достигается путём чернового и чистового обтачивания и предварительного и окончательного шлифования. Поверхности размера 200h7 также необходимо выполнить в пределах указанных отклонений. Точность выполнения этого размера необходима для необходимо качественной сборки и надежной работы карданных валов куда входит крестовина.
Нетехнологичным является отверстие 8 длиной 75мм. Учитывая что отверстие необходимо только для подачи смазки к подшипникам т.к. не является ответственным принимаем ступенчатое сверление на вертикально-сверлильном станке последовательно 10мм глубиной 25мм 9мм а затем 8 мм также глубиной по 25мм что предотвратит увод и поломку свёрл.
Отверстие КГ 38 необходимо для обеспечения сверления отверстий 8мм оно является технологическим при сборке глушится резьбовой пробкой.
Технические требования на неперпендикулярность выдерживаем начиная с 005операции (фрезерно-центровальной) путём одновременной обработки двух противоположных цапф а также за счет поворотного приспособления применяемого на станке.
Остальные поверхности с тоски зрения обеспечения точности и шероховатости не предоставляют технологические трудности.
3Определение типа производства
Тип производства по ГОСТ 3.1108-74 характеризующие коэффициентом закрепления операций который показывает отношение всех различных технологических операций выполняемых в течение месяца к числу рабочих мест.
В нашем случае имеем
Согласно ГОСТ 14.004-74 для 1≤ ≤10 производство крупносерийное.
4Анализ существующего технологического процесса.
В связи с резким уменьшением выпуска тракторов снизилась годовая программа выпуска крестовины 25-49-4646-01. По понятным причинам простаивают дорогостоящие крупногабаритные специальные станки рассчитанные на массовое производство изготовления крестовин. Задачей дипломного проекта стоит замена существующего оборудования на универсальные быстропереналаживаемые станки с учетом существующей на данный момент программой выпуска.
Предлагаю заменить специальный продольно-фрезерный станок и агрегатно-сверлильный станком МП-71 (фрезерно-центровальный). Обработку отверстий КГ 18 и КГ 38 производить на станке 2Р135Ф2 Заменив им два сверлильных станка черновую и чистовую обточку цапф производить на станке 16А20ФЗ вместо двух гидрокопировальных. Существующее универсальное оборудование протяжной и шлифовальной операцией оставить на участке. Недогруженное оборудование загружать другими деталями.
5Методы получения заготовки и вид.
Метод получения заготовки принимаем ту которая существует в производстве.
Заготовка – поковка штампованная легированная сталь 20ХНЗА ГОСТ4543-71 II класса точности вполне обеспечивают получение необходимых размеров готовой детали. Нагруженность и сложность формы крестовины предопределят штамповку как экономически целесообразный способ изготовления.
Поступающие на обработку заготовки должны соответствовать утвержденным техническим условиям. Поверхность штамповки должны быть очищены от окалины.
Отмеченные на чертеже заготовки базы для механической обработки должны служить исходными базами при изготовлении и проверке технологической оснасти. Они должны быть чистыми гладкими без заусенцев.
Основные технические требования отражены в чертеже заготовки и договоре с поставщиком.
Расчет ведем на 33635 h6 (-0016). Исходный индекс 11 таблица №.2 стр. 10[19]. Заготовка представляет собой штампованную поковку II класса точности массой 58 кг.
Технологический маршрут обработки цапф 33635 h6 соответствует из операций обтачивание черновое чистовое; шлифование предварительное окончательное (после термообработки).
Для штампованных заготовок массой 25 25кг RZ=150мкм Т=250мкм табл.43 стр.63[1]
Для механической обработки значения Rz и T таблица № 45стр.64[19].
Суммарное значение пространственных отклонений
где при табл.47 стр.67[1]
; табл.48. стр.71[1]
таблица 8стр.18[19].
Остаточное пространственное отклонение:
k - зависит от обработки стр.73[1]
После шлифования предварительного:
Расчитаем минимального значения припусков произведем по формуллам табл. 42. стр.62[1]
) Обтачивание в центрах
) Бесцентровое шлифование поле термообработки
Расчетный размер находим путем последовательного прибавления расчетного минимального припуска каждого технологического прохода стр.89[1]
Наибольшие предельные размеры вычислим прибавлением допуска к окруженному наименьшему предельному размеру стр.90[1];
Предельные значения припусков - определим как разность наименьших предельных размеров предшествующего и выполняемого переходов стр.90[1];
Общий номинальный припуск стр.87 [1]
-нижнее отклонение заготовки и детали
Проверка правильности расчетов стр.87[1]
Все полученные данные сводим в таблицу 13
На остальные обрабатываемые поверхности крестовины припуски и допуски выбираем по таблицам 3 стр. 13 и 8так-же стр. 17 [2]
Данные сводим в таблицу 12
Рис.1. Поверхности для начисления припусков и допусков.
Технологические переходы обработки
Элементы припуска мкм
Расчетный припуск 2Zmin мкм
Предельный размер мм
Предельные значения припусков мкм
7Расчет режимов резания
7.1Операция 005фрезорно-центровальная
В-ширина фрезерования мм
По паспортным данным станка и табл. 96 стр. 188[2] принимаем
D=100мм; Z=8-число зубьев; t=24мм-глубина резания.
Подача на зуб мм. (табл. 33 стр. 283[2])
Минутная подача стр.282[2]
Скорость резания стр.282[2]
Сила резания стр.282[2]
Принимает по опаспорту станка
n=03 табл 9 стр 264[2]
Крутящий момент на шпинделе
Мощность резания (эффективная)
7.1.2.центрировальная
Глубина резания стр 276[2]
Подача таб 25 стр 277[2]
Скорость резания стр 276[2]
Мощность резания стр.278[2]
принимаем по паспорту
7.2Операция 010 токарная
Принимаем 075-поправочный коэфициент табл.11 стр266 примечание [2]
принимаем по паспорту
7.3Операция 015 токарная
Подача таб.14 стр 268 [2]
7.4Операция 020 сверлильная
)Определение длины рабочего хода стр 303 [3]
)Подачакарта с-2 стр.110[3]
)Стойкость инструмента карта с-3 стр.114[3]
карта с-3 стр.115[3]
принимаем по паспорту ;
)Мощность резания стр126[3]
карта с-6 стр.126-128[3]
) Определение длины рабочего хода стр 303 [3]
) Подачакарта с-2 стр.110[3]
) Стойкость инструмента тогда карта с-3 стр.114[3]
) Мощность резания стр126[3]
карта Р-2 стр.115[3]
7.5Операция 025 сверлильная
) Подача на оборот шпинделя карта С-2 стр.110[3]
принимаем по паспорту станка ;
) Стойкость инструментатогда карта с-3 стр.114[3]
карта с-4 стр.116[3]
) Скорость резания стр.162[3]
карта Р-2 стр.162[3]
7.6Операция 030 сверлильная
) Подача на оборот шпинделя карта с-2 стр.110[3]
Стойкость инструмента тогда карта с-3 стр.114[3]
карта с-3 стр.115-116[3]
)Определение длины рабочего хода
)Стойкость инструмента
тогда карта с-3 стр.114[3]
)Скорость резания стр.115[3]
карта с-6 стр.126[3]
7.7Определение 035 протяжная
) Определение длины рабочего хода
т.к. имеется секции с фасонным профилем то
) Силарезания на 1мм длины режущей кромки
карта П-5 стр.137[3]
(смотрим расчет протяжек)
) Стойкость инструмента карта П-5 стр. 137[3]
7.8Операция 050 шлифовальная (черновая)
)число операций-2 (черновая и чистовая)
)определение припуска-06мм стр.186[3]
)Скорость шлифовального круга стр184[3]
)Минутная поперечная подача
) Число оборотов ведущего круга
)Уточнение скорости
)Характеристики шлфовального круга 14А16ПСМ2-7К5 стр189[3]
) Время выхаживания
7.9Операция 050 шлифовальная (чистовая)
Скорость шлифовального круга см.П.8.
) минутная поперечная подача
) время выхаживания стр 189[3]
7.10 Операция 060 шлифовальная
Шлифовальный круг 24А25ПСМ26К6
) частота вращения шлифовального кругапо принятой скорости
принимаем по паспорту станка;
) Движение продольной подачи карта 19 стр194[3]
) подачу на глубину на проход
карта 1 стр190-191[3]
)длина продольного хода стола
Количество одновременно обрабатываемых деталей
8Расчет норм времени
8.I.Операция 005 фрезерно-центровальная
) Фрезерная: основное время
) Центровальная: основное время
) Основное время на операцию
)Вспомогательное вемя
карта 16 лист1 стр54[6]
- перекрыто основным не учитывается
от карта 85 стр184[6]
от карта 88 стр203[6]
8.2.Операция 010 токарная
)основное время ; стр.610[5]
)вспомогательное вемя
карта 18 лист2 стр66[6]
от карта 19 стр70[6]
8.3операция 015 токарная
вспомогательное вемя
8.4.Операция 020 СВЕРЛИЛЬНАЯ
основное время ; стр.610[5]
карта 16лист1 стр54[6]
карта 27 лист1 стр95[6]
включения и выключения вращения шпинделя
карта 27 лист1 стр96[6]
изменить число оборотов шпинделя и подач
карта 27 лист2 стр96[6]
от карта 28 стр100[6]
8.5.Операция 025 СВЕРЛИЛЬНАЯ
8.6.Операция 030 СВЕРЛИЛЬНАЯ
8.7.Операция 035 протяжная
карта П-1 стр.131[3]
карта 80 лист1 стр173[6]
поворот на следующаю позицию
карта 80 лист1 стр173[6
от карта 8 лист2 стр173[6]
8.8.Операция 050 шлифовальная.
от карта 54 стр141[6]
карта 86 лист 7стр191[6]
8.9.Операция 055 шлифовальная.
от карта 55 стр142[6]
8.10.Операция 060 шлифовальная.
от карта 48 стр137[6]