Кран литейный г/п 225 т


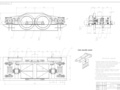
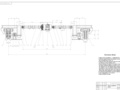
- Добавлен: 25.10.2022
- Размер: 823 KB
- Закачек: 0
Узнать, как скачать этот материал
Подписаться на ежедневные обновления каталога:
Описание
Кран литейный г/п 225 т
Состав проекта
![]() |
![]() |
![]() ![]() ![]() ![]() |
![]() ![]() ![]() ![]() |
![]() |
![]() ![]() ![]() |
![]() |
![]() ![]() |
Дополнительная информация
Контент чертежей
Механизм передвижения.dwg

ПК 0982.00.00.001 СБ
Сборку механизма производить в состветствииТУ24-1-173-70. 2. Радиальное смещение верхнего вала редуктора относительно вала электродвигателя не более 2 мм 3. Радиальное биение обода тормозного шкива после посадки на вал двигателя не должно превышать 0
мм. 4. Механизм обкатать без нагрузки в обе стороны в течении часа для каждого направления вращения при рабочем числе оборотов При обнаружении каких-либо дефектов обкатка прекращается для устранения
после чего проводится повторная обкатка. Во время обкатки не должно быть пропска масла через разъём з убчатых муфт. Нагрев подшипников не должен превышать 70 5. Оси балансиров устанавливаются смазочными отверстиями наружу 6. Тормоз отрегулировать на МТ= 327
Нм 7. Кожухи установить при сборке.
Механизм подъема.dwg

ПК 0982.00.00.000 СБ
Открытые передачи должны быть выверены по зубчатым зацеплениям.
непараллельность и перекос открытых зубчатых пар
а также контакт зубьев парных колес и боковые зазоры должны соответствовать нормам 9-й степени точности.
После сборки механизма подшипники заполнить смазкой и провернуть механизм за тормозной шкив вручную до полного оборота барабана.
Все болтовые соединения должны быть туго затянуты.
Cобранный механизм подвергнуть обкатке без нагрузки.
Отклонения межцентровых
Радиальное биение тормозных шкивов после посадки на вал не должно превышать 0
мм на 100 мм диаметра шкива.
Схема запасовки каната
СПЕЦКРАНЫ ЗАПИСКА РАСПЕЧАТКА.doc
ПРИАЗОВСКИЙ ГОСУДАРСТВЕННЫЙ ТЕХНИЧЕСКИЙ УНИВЕРСИТЕТ
ПРОЕКТ КРАНА ЛИТЕЙНОГО Г.П. 225 Т
ПОЯСНИТЕЛЬНАЯ ЗАПИСКА
студент группы ПТМ-05
использованных источников 4;
ЛИТЕИНЫИ КРАН ТРАВЕРСА ПЛАСТИНЧАТЫЙ КРЮК НАГРУЖЕНИЕ МЕХАНИЗМ ПЕРЕДВИЖЕНИЯ РЕДУКТОР ТИПА ВКУ УРАВНИТЕЛЬНОЕ КОРОМЫСЛО ПОЛИСТПАСТНАЯ СИСТЕМА.
Выполнен расчет механизма главного подъёма механизма передвижения которые представлены на чертежах.
Расчёт механизма подъёма. 4
1 Исходные данные. 4
2 Выбор кратности и схемы запасовки полиспастной системы 6
4 Определение размеров барабанов и блоков. 8
5 Расчет барабана на прочность. 10
З.6 Крепление каната к барабану. 11
7 Выбор электродвигателей. 12
8 Определение передаточного числа привода механизма. 14
9 Выбор редуктора 14
Проверка механизма подъема в аварийном режиме работы. 16
1 Определение вращающих моментов на валах привода. 16
2 Проверка двигателя в аварийном режиме работы. 17
3 Проверка редуктора в аварийном режиме работы. 17
Расчет открытой зубчатой передачи. 18
Расчет тормозного момента и подбор тормоза. 20
Выбор соединительных муфт. 21
Расчёт механизма передвижения. 21
1 Выбор кинематической схемы. 21
2 Расчёт и выбор ходовых колёс. 22
3 Расчёт сопротивления передвижению тележки. 22
4 Расчёт мощности и выбор двигателя. 23
5 Выбор редуктора. 24
6 Расчёт тормозного момента и выбор тормоза. 25
Литейные краны являются тяжело нагруженными грузоподъемными машинами работающими с расплавленным металлом. Их конструкция расчет и проектирование имеют ряд существенных особенностей отличающих их от обычных мостовых кранов.
Литейные краны мостового типа применяются в мартеновских электроплавильных и кислородно-конверторных цехах металлургического производства и предназначены для транспортирования заливки или разливки расплавленного металла а также для выполнения ряда вспомогательных операций по обработке ковшей ремонту оборудования и уборке цехов.
В курсовом проекте приведены характеристика и устройство литейного крана. Методика выполнения проекта излагается параллельно с проектным расчетом.
Расчет механизма подъёма
Грузоподъёмность (т) Q 225
Высота подъёма (м) H 24
Скорость подъёма (мc) V 005
Скорость передвижения тележки (мc) V 035
Вес траверсы (т) Gт 126
Вес канатов (т) Gк 28
Вес тележки (т) Gтел 89
Род тока переменный 220В
механизм подъёма ПВ40%
механизм передвижения тележки ПВ25%
2 Выбор кратности и схемы запасовки полиспастной системы.
Необходимая кратность полиспаста Un подвески траверсы зависит от грузоподъемности скорости подъема типоразмера каната. Её ориентировочные значения при проектировании с учетом возможной унификации параметров механизма принимают в зависимости от номинальной грузоподъемности по графику рис.1 в заштрихованной зоне или близкой к ней. Соответственно выбранной кратности изображают и оценивают с точки зрения целесообразности схему запасовки полиспастной системы.
Рисунок 1 Рекомендуемые кратности полиспастов Un механизма главного
В некоторых случаях кратность полиспаста может быть уменьшена что продлевает срок работы каната уменьшает вес конструкции. При этом передаточное отношение редуктора не увеличивается так как диаметр барабана для таких кранов обычно принимают большим для обеспечения необходимой канатоемкости и уменьшения длины барабана.
При выборе кратности полиспаста следует иметь в виду что если его кратность (-) - величина нечетная то балансир устанавливают на траверсе а если четная (+) то на раме тележки. Последнее предпочтительнее так как упрощает конструкцию траверсы облегчает ее вес и увеличивает высоту подъема.
Принимаем кратность полиспаста
В механизме главного подъема литейных кранов применяют стальные канаты двойной свивки с линейным касанием проволок в прядях и проволочками заполнения типа ЛК - 3 и металлическим сердечником МС по ГОСТ 7667-80.
Максимальная сила натяжения одной ветви каната при статическом нагружении:
где G - суммарная сила веса поднимаемого груза с учетом весов траверсы и канатов кН;
z - общее число ветвей каната полиспастной системы на которых подвешен груз;
п - КПД учитывающий потери в полиспасте механизма.
где - масса номинального груза (номинальная грузоподъемность) т;
Qк- наибольшая масса канатов подвески при нижнем положении груза т;
g=981 мс2 - ускорение силы тяжести
где а- количество полиспастов механизма главного подъема; а=4.
Средние значения n для различных кратностей полиспаста представлены в табл. 1.
Таблица 1. Значения КПД полиспаста
Опоры на подшипниках
Значения КПД для кратностей 4
Предварительно массы траверсы и канатов могут быть выбраны по данным выполненных конструкций кранов для ряда грузоподъемностей (табл. 2).
Расчетное разрывное усилие каната:
где zp - минимальный коэффициент использования каната (коэффициент запаса прочности). принимаем для групп классификации механизмов М7.
Таблица 2. Массы траверсы и канатов.
Грузоподъемность крана Qh т
Канат выбирается по разрывному усилию каната в целом Fo из условия:
Выбираем канат двойной свивки типа ЛК-РО с металлическим сердечником ГОСТ 7667.Основные характеристики и параметры принятого каната: диаметр каната dK=42 мм; предел прочности проволок при растяжении в=1764 МПа ; разрывное усилие каната в целом Fo =1140000 Н.
4. Определение размеров барабанов и блоков.
Минимально допустимые диаметры барабанов и блоков определяются по «Правилам» [2].
Диаметры определяются по формулам:
где dK - диаметр каната мм;
Д1 и Д2 - диаметры барабана и блока;
h1 и h2 - коэффициенты зависящие от режима работы механизма.
Таблица 3. Коэффициенты выбора диаметров барабана (h1) и блока (h2).
Группа режима работы
С целью повышения долговечности грузовых канатов и унификации элементов механизма диаметры барабанов обычно увеличивают. Так для литейных кранов тяжелого режима работы принимают унифицированные значения диаметров барабанов приведены в таблице 4. Окончательно диаметры барабана можно будет установить позже при выборе редуктора и графической компоновке тележки: изменяя диаметр барабана можно изменить потребное передаточное число редуктора а также длину барабана.
Расчетный диаметр барабана по центрам сечения навитого каната
D6=D+dK= 1850 + 42 =1892 мм (7)
Таблица 4. Унифицированные значения диаметров барабанов по дну канавки.
Грузоподъемность Q т
Диаметр барабана D мм
Принимаем диаметр барабана по дну канавки D6 =1850 мм.
Обычно в литейных кранах принимают следующие унифицированные значения диаметров блоков по дну канавок: 700 900 1000 1100 1200 и 1300 мм а вместо уравнительного блока принимают рычаг (коромысло). Длину барабана определяют из условия навивки на нем каждой из двух ветвей каната обеспечивающих полную заданную высоту подъема траверсы а также дополнительно не менее 15 витков не считая витков находящихся под зажимным устройством.
Полная рабочая длина барабана при сдвоенном полиспасте
где 1н - длина нарезанной части одной половины барабана;
lгл - длина гладкой не нарезанной средней части.
где zб - полное число витков каната на одной половине барабана;
- шаг нарезки барабана (мм).
где zp - число рабочих витков; zд - число дополнительных разгрузочных витков; принимают ; z3 - число витков используемых под закрепление каната; в случае крепления прижимными планками принимают z3=2-3. Принимаем =2 ;
где LK - рабочая длина каната одного полиспаста м
Dб - расчетный диаметр барабана м.
Шаг нарезки барабана принимают
Величину гладкой части между левой и правой нарезками барабана определяют по расстоянию между наружными боками подвески траверсы с учетом возможного допускаемого угла отклонения каната:
где 1бл - расстояние между наружными блоками подвески траверсы;
- допускаемый угол отклонения от вертикального направления набегающей на барабан ветви каната; =6°.
Можно ориентировочно принять
Принимаем lгл= 395 мм.
5. Расчет барабана на прочность.
Необходимо принять материал для изготовления барабана определить толщину стенки барабана проверить ее по эквивалентным напряжениям от совместного действия изгиба сжатия и кручения.
Учитывая ответственность и тяжелый режим работы литейных кранов их грузовые барабаны изготавливаются стальными литыми или стальными сварными. Применение чугуна не рекомендуется.
Используемые стали и допускаемые напряжения сжатия приведены в табл.5.
Таблица 5. Допускаемые напряжения [сж] МПа.
Принимаем стальной литой барабан отлитый из стали 55Л ГОСТ 977-88. [сж] = 165 МПа
Толщина стенки литых стальных барабанов определяется по формуле:
+ 3 =0011850+3= 215 мм (16)
но не может быть менее 12 мм из условий технологии изготовления.
Внутренний диаметр барабана:
Проверим стенку барабана на смятие по формуле:
Проверим барабан на совместное действие изгиба и кручения.
Экваториальный момент сопротивления поперечного сечения:
Максимальный изгибающий момент :
Нормальные напряжения
Максимальный крутящий момент:
Касательные напряжения:
Эквивалентные напряжения:
Условия прочности барабана на совместное действие изгиба и кручения выполняется.
6. Крепление каната к барабану.
Канат крепится к барабану прижимными планками. Предпочтительно применять двухболтовые планки.
Количество планок определяется расчетом но должно быть не менее двух.Расчет можно выполнять по [3]. Угол обхвата барабана дополнительными витками: при 2 витках Угол обхвата барабана канатом при переходе от одной канавки к другой .
Плечо изгиба болта 1 можно ориентировочно принять:
По рекомендации выбора болтов для крепления каната в зависимости от его диаметра принимаются болт М27 23 мм .
Материал болтов и допускаемые напряжения на растяжение для болта
Принимем материал болтов .
7. Выбор электродвигателей.
Общую статическую мощность механизма главного подъема Ро кВт определяют при установившемся движении поднимаемого груза:
где G - суммарная сила веса поднимаемого номинального груза с учетом веса траверсы и канатов кН; V - скорость подъема мс; общий КПД механизма.
где КПД учитывающие потери соответственно в полиспасте на барабане открытых парах редукторе соединительной муфте.
Значения КПД обычно принимают:
8 -КПД полиспаста; =098 - барабана ; =096 -КПД открытой пары; = 093 КПД редуктора; КПД муфты - = 098
Расчетная статическая мощность одного электродвигателя
где m - число электродвигателей в механизме; m=2.
По статистической мощности и режиму работы выбираем асинхронный двигатель с фазовым ротором типа МТН или МТF или двигатель постоянного тока типа Д с последовательным возбуждением обеспечивающий плавное регулирование рабочих скоростей в широких пределах.
При выборе электродвигателя по справочнику необходимо учитывать следующее:
) номинальная мощность выбранного электродвигателя должна быть близка к расчетной
) относительная продолжительность включения двигателя ПВДВ должна соответствовать относительной продолжительности включения механизма ПВМ т.е.
) Электродвигатель должен обеспечивать кратковременную работу с полным грузом в аварийной ситуации при выходе из строя одного из приводов т.е.
Здесь - максимальный момент электродвигателя принимается по каталогу; - максимальный статический момент от груза приведенный к валу одного из электродвигателей (при аварийной работе) - определяется в разделе 4.
) Для выбранного электродвигателя необходимо проверить его загрузку по условию
где - коэффициент загрузки электродвигателя %; Рст - статическая мощность на валу каждого электродвигателя при установившемся движении поднимаемого груза кВт Рн - номинальная мощность электродвигателя кВт.
Для электродвигателей механизма главного подъема рекомендуется загрузка.
Принят двигатель MTH 711-10 ;номинальное напряжение 220 В; номинальную мощность 85 кВт; частоту вращения вала = 540 ; относительно продолжительности включения ПВдв= 40 %; максимальный момент Нм; маховый момент ротора Нм2; габаритные размеры электродвигателя: длина 1702 мм ширина 800 мм высота 810 мм; высота центра вала 405 мм; масса двигателя 2860 кг.
Выполняется проверка по условию
8. Определение передаточного числа привода механизма.
Редуцирование вращающего момента в приводе механизма главного подъема от электродвигателя до барабана обеспечивается с помощью редуктора и открытой зубчатой пары а передаточное число
где - передаточное число привода механизма главного подъема; -передаточное число редуктора; - передаточное число открытой пары.
Определяют передаточное число привода механизма по формуле
Здесь - частота вращения барабана вычисляемая через линейную скорость каната навиваемого на барабан по зависимости
где - скорость каната мс; - расчетный диаметр барабана по центрам навитого каната м.
V - скорость подъема мс.
Для принятой кинематической схемы механизма с открытой передачей передаточное число разбивается на - передаточное число редуктора и - передаточное число открытой передачи принимаемое в пределах 4-7.Принимается
В механизме главного подъема литейных кранов применяют специальные горизонтальные крановые редукторы с лапой типа ГК со встроенным храповым механизмом и межосевыми расстояниями 1000 1150 1300 1500 1700 1830 конструкции ПО «Сибтяжмаш».
) с целью рациональный разбивки передаточного числа привода с учетом открытой пары передаточное число редуктора выбирают в 4-7 раз меньшим передаточного числа привода т.е.
) номинальная расчетная мощность редуктора Рред по каталогу должна обеспечивать передачу статической мощности от груза при длительной работе т.е.
где - номинальная расчетная мощность редуктора подводимая к входному валу (указывается в характеристике редуктора); Рст - статическая мощность от груза приведенная к входному валу редуктора и определяемая по формуле
) редуктор должен допускать кратковременную передачу максимального момента от груза в аварийной ситуации при выходе из строя одного из приводов т.е.
Здесь максимально допускаемый момент на входном валу редуктора при кратковременной работе; Мред.АВ - максимальный статический момент от груза в аварийной ситуации (определяется в разделе 4.)
Для выбранного редуктора выписывают основные технические характеристики и параметры: тип редуктора ГК-1300; передаточное число 344; номинальную мощность на быстроходном валу =120 кВт; относительную продолжительность включения ПВред = 40%; частоту вращения быстроходного вала nред=600 ; параметры шестерни открытой передачи: модуль зацепления mн=24 мм число зубьев zш=15 ширину венца bш = 360 мм.
Уточняется фактическое передаточное число привода по принятому редуктору и открытой зубчатой пары:
Проверяется фактическая скорость подъема:
Отклонение от заданной скорости не должно превышать ±10-15%:
где - фактическая скорость подъема груза обеспечиваемая принятыми параметрами механизма.
Проверка механизма подъема в аварийном режиме работы.
При выходе из строя одного двигателя или редуктора (аварийный режим) должна быть обеспечена работа механизма для завершения операции. При аварийном режиме возникают увеличенные приведенные вращающие моменты на валу работающего двигателя и на валах редуктора. Проверка заключается в определении аварийных вращающих моментов и способности двигателя и редуктора работать с такими увеличенными вращающими моментами.
1. Определение вращающих моментов на валах привода.
Вращающий момент от груза на валу барабана при нормальной работе:
где R6 = 06905 м - радиус барабана
=097 - КПД барабана.
Вращающий момент от груза на валу барабана при аварийной работе одним двигателем:
где =096 - КПД открытой пары зубчатых колес.
Из этого уравнения определяется коэффициент перегрузки:
Вращающий момент от груза приведенный к валу двигателя при нормальной работе:
Вращающий момент о груза приведенный к валу двигателя при аварийной работе (работа с перегрузкой ):
2. Проверка двигателя в аварийном режиме работы.
Электродвигатель должен удовлетворять следующим условиям:
) Его номинальная мощность должна быть близка к расчетной:
) Максимальный вращающий момент развиваемый двигателем должен быть больше вращающего момента от груза приведенного к валу двигателя при аварийной работе:
Вращающие моменты двигателя
где Рн = 646 кВт - номинальная мощность
n = 550 — частота вращения
где - коэффициент перегрузки двигателя.
3. Проверка редуктора в аварийном режиме работы.
Редуктор должен удовлетворять следующим условиям:
) Частота вращения входного вала редуктора должна быть равна или больше частоты вращения двигателя:
) Номинальная мощность редуктора подводимая к входному валу должна быть равна или больше статической мощности от груза приведенной к входному валу редуктора:
) Редуктор должен допускать кратковременную передачу максимального момента от груза в аварийном режиме работы т.е.
где максимально допускаемый момент на входном валу редуктора при кратковременной работе;
максимальный статический момент от груза в аварийной ситуации приведенный к входному валу редуктора (или что то же - приведенный к валу двигателя):
Примечание: Редукторы допускают кратковременное превышение номинального момента с коэффициентом кратности m=16.
или может быть вычислен:
где и - мощность подводимая к входному валу (кВт) и частота его вращения ().
Расчет открытой зубчатой передачи.
Параметры открытой передачи определяются модулем m числом зубьев шестерни z1 диаметром шестерни d1 и ее шириной b1 приведенными в каталоге на редукторы типа ГК.
Число зубьев колеса:
Значение числа зубьев колеса z2 округляется до целого числа. Диаметр делительной окружности шестерни:
Диаметр делительной окружности колеса:
d2=m z2 =24 105 = 2520 мм . (61)
Ширина зубчатого венца колеса:
Диаметры окружности впадин:
Геометрические параметры открытой зубчатой пары должны удовлетворять условию возможности построения барабанов с находящимися в зацеплении зубчатыми венцами что осуществимо лишь в случае если диаметр окружности впадин зубчатого венца больше диаметра барабана с канатом т.е.
+ 50 = (1895 + 42) + 50 = 1990 мм; (65)
Невыполнение условия требует корректировки передаточного числа открытой пары с соответствующим изменением и пересчетом других взаимосвязанных параметров механизма вплоть до кратности полиспаста и диаметра барабана (при необходимости).
Корректировка передаточного числа открытой пары с соответствующими изменениями результата не дало.
Необходимо изменить диаметр барабана с соответствующим изменением всех показателей.
Межосевое расстояние передачи:
При аварийном режиме работы механизма зубчатая пара работающего механизма будет нагружена большим (аварийным) моментом. Поэтому зубья колеса проверяются на прочность по изгибающим напряжениям возникающим от аварийного вращающего момента приведенного от груза к валу барабана - рассчитанному по формуле (2).
Принимаются материалы передачи:
Материал шестерни - ст. 40 ХН HRC42-50.
Материал колеса- ст. 45 Л НВ 280-320.
Возникающие в зубьях колеса напряжения при аварийном режиме работы не должны превышать допускаемые напряжения:
Расчетные напряжения изгиба в зубьях колеса будут:
где: YF = 35- коэффициент формы зуба для z2>60
= 1- коэффициент неравномерности распределения нагрузки по ширине венца
KFv = 11- коэффициент динамической нагрузки
Допускаемые напряжения на изгиб определяются по формуле:
где - предел выносливости зубьев при изгибе при базовом числе на-гружений
S F =18- коэффициент безопасности;
KFL =2- коэффициент долговечности;
8- коэффициент характера нагружения для реверсивных передач.
Расчет тормозного момента и подбор тормоза.
Тормозной момент определяют в предположении что весь груз удерживается одним тормозом хотя механизм литейного крана состоит из двух приводов и на каждом из них установлено по два тормоза.
Необходимый тормозной момент выбирают с запасом торможения Кт исходя из условия обеспечения надежного удержания груза на весу в статическом состоянии.
Мт = Кт необходимый расчетный тормозной момент где КТ=11
- коэффициент запаса торможения при наличии двух тормозов на каждом приводе механизма [2] по правилам Госнадзорохрантруда Украины.
Мст - статический момент от груза приведенный к валу торможения
где общий наибольший КПД механизма
где =084 - КПД одного механизма подъема;
U - общее передаточное число механизма главного подъема
В соответствии с величиной расчетного тормозного момента и заданным режимом работы механизма по справочнику подбирают типоразмер тормоза. В механизме главного подъема литейных кранов применяют колодочные тормоза с короткоходовыми электромагнитами постоянного тока серии ТКП обладающие наиболее высокой надежностью и износостойкостью их электромагнитных приводов.
Для выбранного тормоза выписывают основные технические характеристики и параметры: при = Нм и = Нм - ТКП-500;
номинальный тормозной момент 1900 Нм; относительную продолжительность включения ПВторм=40%; диаметр шкива dшк=500 мм.
Тормоз отрегулировать на заданный тормозной момент.
Выбор соединительных муфт.
Для соединения концов валов электродвигателя и редуктора механизма главного подъема применяют муфты зубчатые по ГОСТ 5006-83. Муфты подбирают в соответствии с диаметром соединяемых концов валов и проверяют по величине вращающего момента:
где: =15 - коэффициент учитывающий степень ответственности механизма
К2 =12 - коэффициент учитывающий режим работы;
К3 =12 - коэффициент учитывающий угловое смещение;
Мст - статический момент от груза при аварийной работе приведенный к валу торможения рассчитанный по формуле (73);
Мм - наибольший вращающий момент допускаемый муфтой. Выбирается муфта МЗП по ГОСТ 5006-55.
Для выбранной муфты выписываем основные технические характеристики и параметры: номер муфты 4 ; вращающий момент 5600 Нм; диаметр вала d = 75 мм.
Расчет механизма передвижения тележки
1. Выбор кинематической схемы
Тележка имеет восемь ходовых и четыре приводных колеса. Механизм передвижения выполняется с общим приводом и центральным расположением редуктора. Кинематическая схема такого механизма представлена на рисунке 2.1.
Рисунок 2.1. - Схема кинематическая механизма передвижения крановой 1 - электродвигатель; 2 5 - зубчатая муфта типа МЗП; 3 - зубчатая муфта с тормозным шкивом; 4 - редуктор типа ВК; 6 - ходовое колесо тележки
2. Расчет ходовых колес
Нагрузка на одно ведущее колесо при условии равномерного распределения нагрузки между всеми четырьмя ходовыми колесами:
В соответствии с нагрузкой на одно колесо по таблице принимаются колеса крановые К2Р-800х110 по ГОСТ 3569-74 и рельсы КР 100 по ГОСТ 4121-76. Материал колес сталь 65Г твердость поверхности качения НВ320..350; допускаемые напряжения смятия при точечном контакте = 2200МПа.
Расчетная нагрузка на колесо:
где =1.2 - коэффициент учитывающий режим работы механизма для режима 4М;
- коэффициент учитывающий переменность нагрузки:
Колеса испытывают напряжения смятия при точечном контакте которые рассчитываются по формуле:
где т = 0.55 - коэффициент зависящий от отношения радиусов колеса и головки рельса (меньшего к большему). Принят для R1=400мм и R2 = 450 мм
(радиус закругления головки рельса);
максимальный из двух вышеуказанных радиусов.
Условие прочности по смятию колес выполняется.
3. Расчет сопротивления передвижению тележки
Сопротивление передвижению тележки с номинальным грузом при установившемся режиме работы определяем по формуле:
где =2358320 Н - суммарная сила веса поднимаемого груза с учетом весов траверсы и канатов;
Gm =872200 Н - собственный вес тележки;
DK = 800 мм - ориентировочное значение диаметра ходовых колес тележки в соответствии с [1 с. 106];
d -155 мм - диаметр цапфы колеса;
= 0015 - коэффициент трения в подшипниках колес (подшипники качения шариковые однорядные);
= 004 см - коэффициент трения качения колеса по рельсу с выпуклой головкой;
кр = 25 - коэффициент учитывающий сопротивление от трения реборд колес о рельсы и от трения токосъемников о троллеи;
Сопротивление передвижению от уклона пути где = 0001 - расчетный уклон подкранового пути
= (2358320 + 872200)0001 = 323052 Н (85)
= 0 - сопротивление от ветровой нагрузки для кранов работающих в закрытом помещении .
4. Расчет мощности двигателя
Двигатель механизмов передвижения тележек и кранов выбирается по пусковому моменту. Значение пускового момента должно быть таким при котором отсутствует пробуксовка ведущих колес незагруженной тележки крана по рельсам а коэффициент запаса должен быть не менее 12.
Для предварительного выбора двигателя определяем сопротивление передвижению загруженной тележки в пусковой период:
где а = 01 мс2 - ориентировочное значение ускорения в механизме передвижения тележки.
Мощность предварительно выбираемого двигателя:
где VT =035 мс - скорость передвижения тележки;
= 085 - ориентировочное значение КПД механизма передвижения тележки;
=17 - для асинхронного двигателя переменного тока фазовым ротором.
Требуемая статическая мощность рассчитывается по формуле:
Расчетная мощность удовлетворяет условию Рр > Рст. По каталогу [1с.489] предварительно выбираем электродвигатель MTF-312-6 с мощностью на валу 175 кВт при ПВ=25%. Частота вращения 950 обмин. Момент инерции ротора 0318. Максимальный вращающий момент развиваемый двигателем 480 Нм.
Номинальный момент электродвигателя:
Коэффициент перегрузки:
Частоту вращения колеса определяем по формуле:
Расчетное передаточное число редуктора
Выбирается редуктор типа ВКУ-750 передаточное число ир = 112 относительная продолжительность включения ПВред=25 %. Мт = 149 кНм
Фактическая частота вращения колеса:
Фактическая скорость передвижения тележки с номинальным грузом:
Относительная погрешность выбранного редуктора:
Минимальное время пуска незагруженной тележки определяем по зависимости:
где максимально допустимое ускорение незагруженной тележки:
где ппр = 4 - число приводных колес;
пх.= 8 - число ходовых колес;
= 02 - коэффициент сцепления ведущего колеса с рельсом для кранов работающих в закрытых помещениях;
ксц = 12 коэффициент запаса сцепления при пуске незагруженной тележки;
Фактический коэффициент запаса сцепления приводных колес с рельсами
Итак условие по величине коэффициента сцепления выполняется.
6. Расчет тормозного момента и выбор тормоза
Сопротивление передвижению тележки при торможении:
где все величины аналогичны величинам в формуле для Wcm
Для незагруженной тележки
Статический момент сопротивления торможению приведенный к валу двигателя. Для незагруженной тележки будем иметь:
Приведенный к валу двигателя момент инерции при торможении:
Тогда тормозной момент равен:
Принимаем колодочный тормоз типа ТКП-300 с максимальным тормозным моментом 412 Нм и диаметром тормозного шкива 300 мм.
Михеев В.А. Власов В.Т. Специальные краны. Учебник. - Мариуполь:
Правила устройства и безопасной эксплуатации грузоподъемных кранов:
ДНАОП 0.00-1.03-02. Харьков: Форт 2ОО2.-416с.
Расчеты грузоподъемных и транспортирующих машин. Иванченко Ф.К. и др.
Киев «Вища школа» 1978.-576с.
Справочник по кранам. в томах В.И. Брауде и др.; Под.ред. М.М.Гохберга .М-Л:Машиностроение 1988.
Рекомендуемые чертежи
Свободное скачивание на сегодня
Обновление через: 18 часов 6 минут