Кран козловой грейферный 10 т. Курсовой проект.




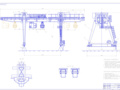
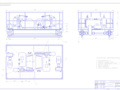
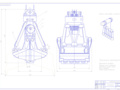
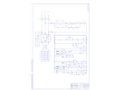
- Добавлен: 25.10.2022
- Размер: 1 MB
- Закачек: 0
Описание
Состав проекта
![]() |
![]() |
![]() |
![]() ![]() ![]() ![]() |
![]() ![]() ![]() ![]() |
![]() ![]() ![]() ![]() |
![]() ![]() ![]() ![]() |
![]() ![]() ![]() ![]() |
![]() ![]() ![]() ![]() |
![]() ![]() ![]() ![]() |
![]() ![]() ![]() |
![]() |
![]() ![]() |
![]() ![]() |
![]() ![]() |
![]() ![]() |
![]() ![]() |
![]() ![]() |
![]() ![]() |
Дополнительная информация
Общий вид А0.dwg

Высота подъема груза
Скорость подъема груза
Скорость передвижения крана
. Режим работы L2 M6
Технические требования
Необработанные поверхности должны быть
окрашены масляной краской.
Обработанные поверхности должны быть
смазаны маслом либо покрыты лаком.
Испытания крана на месте производится
после окончания монтажа и сдачи заказчику.
механ. подъема А1.dwg

Скорость передвижения
Группа классификации механизма М6
Электрическая схема А1.dwg

Грейфер А1.dwg

Вместимость грейфера 2м
Объемная масса материала 2тм
Наибольший размер кусков 0.05м
Размер кусков материала 50мм
Схема запасовки каната
тележка.dwg

Электродвигатель 4МТF
Механизм передвижения
Спецификация козловой кран.dwg

Козловой грейферный кран
Механизм передвижения
Спецификация грейфер.dwg

записка1.doc
Факультет: Конструкторско-механический (КМК)
Кафедра: «Детали машин и подъёмно-транспортное оборудование» К3-КФ
Расчётно-пояснительная записка
по дисциплине: Специальные ГПМ
на тему: Кран козловой грейферный
Расчет механизма подъема .
Выбор каната и барабана
Выбор электродвигателя .
Компоновка механизма
Расчет механизма передвижения тележки .
Определение предварительной массы тележки .
Выбор ходовых колес
Выбор электродвигателя
Проверка двигателя по пусковому моменту .
Коэффициент запаса сцепления приводных ходовых колес с рельсом .
Расчет подшипников ходового колеса
Расчет механизма передвижения крана .
Расчет сопротивления передвижению крана .
Коэффициент запаса сцепления приводных ходовых колес с рельсом ..
Выбор электродвигателя .
Требования предъявляемые к механизмам козлового крана
Выбор системы управления крановыми двигателями ..
Козловой грейферный кран грузоподъемностью 10 т. предназначен для выгрузки щебня.
Щебень поступает на предприятие по изготовлению железобетонных конструкций по железной дороге в саморазгружающихся полувагонах типа «Гондола» разгружается на эстакаде приемного устройства и из отвалов под эстакадой ленточными конвейерами в цеха.
Кран устанавливается на открытом складе. Диапазон рабочих температур от -40° до +40°С.
Дано: грузоподъёмность;
режим нагружения L2 - умеренный;
группа классификации механизма – М6
Выбор каната и барабана
Грузоподъёмная сила
где - ускорение свободного падения.
Наибольшее натяжение ветви каната набегающего на барабан
где - число полиспастов;
коэффициент загрузки механизма замыкания грейфера;
кратность полиспаста;
Для козлового крана т.е. оба конца каната закреплены на барабане для строго вертикального подъёма груза выравнивания усилий на опоры
Разрывное усилие каната в целом
где =5.6 - минимальный коэффициент использования каната
Для козлового крана работающего на открытом воздухе при наличии пыли и влаги следует выбирать канат типа ГОСТ 2688-80 с малым количеством проволок большого диаметра. Абразивная и коррозионная износостойкость этого каната выше.
По найденному разрывному усилию находим значение диаметра каната по таблице 1 приложения 2 [1] находим значение диаметра каната
где - коэффициент выбора диаметра барабана [1]
Длина барабана с двусторонней нарезкой
где - коэффициент длины средней (не нарезанной) части барабана
Проверка размеров барабана по условиям
Угловая скорость барабана
где - скорость подъёма
Статическая мощность электродвигателя
где - предварительное значение КПД (для механизма подъёма с цилиндрическим редуктором).
По приложению 1 выбираем ПВ=40% и мощности электродвигатель серии 4MTF. Технические данные двигателей принимаем приложению 4 [1].
МТF(H)225М6 (Р=37 кВт р=6 m=420 кг n=965 обмин
l30-l1=960-140=820 мм d11=435 мм.
где ()- длина двигателя без посадочной части вала мм.
Угловая скорость двигателя
Расчет редуктора по радиальной консольной нагрузке
где – действующая радиальная (консольная) нагрузка. Полагаем что наибольшее усилие от левой ветви каната набегающей на барабан Fa действует на консоль выходного вала редуктора . То же от правой ветви каната действует на опору справа от барабана;
Fy – допускаемая радиальная консольная нагрузка на выходном валу редуктора по каталогу (приложение 3) [1].
Выберем редуктор Ц2-500.
Передаточное число редуктора
Определим расчетное передаточное число редуктора формула (11) и округлим его до номинального значения по каталогу (прилож.3) [1].
Грузовой момент на барабане
где – число полиспастов.
Проверка редуктора по грузовому моменту
где - допускаемый крутящий момент на валу редуктора.
Статический момент на входном валу редуктора при торможении
где - КПД механизма который можно принять равным КПД редуктора
Тормозной момент на который регулируют тормоз
где - коэффициент запаса торможения =1.5
Выбираем тормоз ТКГ-300 с тормозным моментом Тmax=300Нм приложение 3 [1] масса 55 кг L=772 мм.
Компоновка механизма
Условие соседства электродвигателя и барабана
где – суммарное межосевое расстояние редуктора
- габаритный размер электродвигателя
- размер от оси вращения барабана до наружного конца шпильки крепления каната
Условие соседства тормоза и барабана
где – модуль зубчатого венца;– число зубьев венца по справочнику (приложение 3) [1];
– размер от оси вращения барабана до крайней точки зубчатой ступицы
– диаметр тормозного шкива;
– размер от оси вращения тормозного шкива до наружной поверхности рычага тормоза.
Дано. Грузоподъемность ; щебень ; угол внутреннего трения ; коэффициент внутреннего трения ; уголь трения о сталь ; коэффициент трения о сталь ; угол естественного откоса ; начальное сопротивление материала сдвигу ; расчетный размер куска ; коэффициент наполнения и уплотнения материала .
Корректирующие коэффициенты: .
Геометрические размеры при закрытом грейфере:
где - ширина челюсти;
- высота челюсти до шарнира тяги;
- коэффициент ширины челюсти;
- коэффициент длины челюсти;
- коэффициент высоты челюсти.
- угол наклона к горизонтали хорды челюсти.
2. Условный радиус (высота до центрального шарнира) челюсти:
3. Условная высота призмы материала:
4 Зазор между верхней точкой пизмы и центром шарнира:
5 Полная высота закрытого грейфера:
6 Расстояние от центрального шарнира челюстей до верхней кромки головки:
7 Длина тяг связывающих головку грейфера с челюстью:
Углы наклона тяг к вертикали закрытого грейфера в плане () и профиле ():
; - конструктивные размеры головки грейфера;
8. Радиус поворота (высота) челюсти:
где - расстояние от центральной оси грейфера до центра шарнира;
- угол наклона радиуса поворота челюсти закрытого грейфера к вертикали.
9. Расстояние между шарнирами (плечо) челюсти:
10. Радиус центра тяжести челюсти:
11. Толщина ножа челюсти:
12. Толщина кромки челюсти:
Геометрические размеры при открытом грейфере:
где ; - координаты центра тяжести челюсти
; - координаты центра тяжести перегружаемого материала
- угол между высотой и хордой челюсти у закрытого грейфера
- угол прямоугольного треугольника построенного на плече Е т.е. на прямой соединяющей оси шарниров челюсти
- угол между высотой R0 и плечом Е челюсти
- угол между хордой М и плечом Е челюсти.
1. При полностью открытом грейфере длина раскрытия:
где - полуразмах челюсти.
2. Необходимый ход траверсы для полного раскрытия челюстей:
Максимально допустимая по грузоподъемности масса грейфера:
Минимально допустимое масса грейфера:
где с=1.5- коэффициент жесткости.
Оптимальная величина mгр находится в границах:
где кр=0.8 – коэффициент учитывающий перенос равнодействующей сил сопротивления на режущую кромку челюсти;
кф=2 – коэффициент учитывающий влияние формы челюстей;
- задний угол челюсти в конечный момент зачерпывания;
- коэффициенты учитывающие соответственно относительные массы головки нижней траверсы тяг и челюстей.
где - угол скольжения материала при зачерпывании.
1. Кратность полиспаста:
где uп – силовая кратность замыкающего полиспаста;
- КПД блока с подшипниками качения.
2. Удельное сопротивление зачерпыванию:
где - расчетное среднее заглубление челюсти;
Кпз =0.3 – коэффициент учитывающий гранулометрический состав материала.
3. Сила сопротивления зачерпывания челюстей:
4. Сила сопротивления перемещению материала по челюсти и трения по ней:
где - первоначальное заглубление челюсти;
- действительный угол наклона закрытого грейфера;
- коэффициент учитывающий степень заглубления и физико-механические зачерпываемого материала.
5. Обобщенный параметр:
где - обобщенный коэффициент;
- средний задний угол челюсти;
6. Аналитические зависимости:
Зачерпывающая способность грейфера по линейной нагрузке на кромке челюсти:
1. Наибольшая нагрузка тяги челюстей:
где - усилие на головку грейфера;
- вес зачерпнутого материала.
Нагрузка действующая на нижнюю траверсу грейфера:
Вертикальная составляющая реакции в шарнирах челюсти:
Горизонтальная составляющая силы сопротивления при зачерпывании:
Вертикальная составляющая при зачерпывании:
Общая сила сопротивления:
Расчет механизма передвижения тележки
Определение предварительной массы тележки
где тг=10000кг – масса груза
Вес тележки с грузом:
Максимальная статическая нагрузка на ходовое колесо
где z=4 – количество ходовых колес;
Примем диаметр ходового колеса Dxk=320мм [3] с.319 диаметр внутреннего отверстия подшипника d=60мм. Выбираем рельс Р24 [3] с.325.
Расчет сопротивления передвижению:
Сила сопротивления передвижению тележки с грузом (при отсутствии уклона и ветра)
где =0.04 – коэффициент трения колеса по рельсу [4] с.260
f=0.015 – коэффициент трения качения подшипника буксы [4] с.259
кр=2 – коэффициент сопротивления реборды [3] с.422.
Выбор электродвигателя
Мощность электродвигателя:
где V=0.63мс – скорость передвижения;
=0.9 – КПД механизма передвижения;
Выбираем двигатель 4АС90LE6 со встроенным механическим тормозом [5]с.84 мощность Рэ=1.7кВт тормозной момент ТТЭ=16Нм частота вращения nэ=930обмин момент инерции Jэ=0.0073кг×м2 пусковой момент Тп=33Нм.
Минимальный пусковой момент:
Номинальный момент электродвигателя:
Угловая скорость ходового колеса:
где V=0.63мс – скорость передвижения тележки;
Dхк=0.32м – диаметр ходового колеса тележки.
Передаточное число редуктора:
Выбираем навесной редуктор типа ВКН-420
Проверка двигателя по пусковому моменту
Динамический момент сопротивления вращению электродвигателя во время пуска:
где J1 – момент инерции частей вращающихся со скоростью вала электродвигателя;
где Jэ=0.0073кг×м2 – момент инерции электродвигателя;
Jм=0.025кг×м2 – момент инерции муфты выбираем муфту МУВП
J1=0.0073+0.025=0.032кг×м2
3. Коэффициент полезного действия механизма:
где р=0.96 – КПД редуктора ВКН-420;
м=0.98 – КПД муфты МУВП.
3. Время пуска и торможения:
где а=0.25мс2 - допускаемое максимальное значение ускорения и замедления тележки [4] с.269.
т.е. Tnmin=26.4>22.13=TД условие пуска выполняется.
Коэффициент запаса сцепления приводных ходовых
где Fсц – сила сцепления приводных колес с рельсами;
FCT – сила статического сопротивления передвижению тележки без груза и без учета трения в подшипниках приводных колес;
FДТ – сила динамического сопротивления передвижению тележки без груза;
[ксц]=1.2 – допускаемое значение коэффициента запаса сцепления [4] с.266.
где fсц=0.12 – коэффициент сцепления приводного ходового колеса [4] c.266.
Zпр=2 – количество приводных колес.
т.е. запас сцепления при пуске достаточен.
Расчет подшипников ходового колеса
Подшипники качения ходового колеса должны выбираться по статической грузоподъемности или по динамической приведенной нагрузке.
Расчет по динамической приведенной нагрузке:
где Fхк=3200кг – максимальное давление на колесо;
Кхк=0.75 – коэффициент учитывающий переменность нагрузки на колесо;
γ=0.8 – коэффициент учитывающий режим работы механизма передвижения.
где пф – частота вращения ходового колеса
Lh=3500 – ресурс подшипников зависит от режима работы.
Динамическая грузоподъемность:
где α=3 – показатель степени
Выбираем шариковый радиальный сферический двухрядный подшипник средней серии №3628 его статическая грузоподъемность 2700.
где ТИН – момент инерции вращающихся и поступательно движущихся масс приведенных к валу тормоза. Тормоз расположен на валу электродвигателя.
Тс – статический момент сопротивления движению тележки при торможении.
т.е. встроенный тормоз подходит.
Расчет механизма передвижения крана
Расчет сопротивления передвижению крана
Полное сопротивление движению:
где WТР – коэффициент сопротивления трения в ходовых частях без учета трения торцов и ступиц Н;
WУК – сопротивление от уклона подкрановых путей Н;
WВ =360000Н– сопротивление от действия ветровой нагрузки по паспорту.
1 Сопротивление от трения при движении крана:
где =0.06 – коэффициент трения колеса по рельсу [4] с.260
кр=2 – коэффициент сопротивления реборды [3] с.422
Сопротивление от уклона подкрановых путей:
где α=0.002 – коэффициент учитывающий уклон рельсового пути [4] с.272
тогда полное сопротивление:
Коэффициент запаса сцепления приводных ходовых колес с рельсом
Zпр=4 – количество приводных колес.
где VКР =1.16 мс– скорость передвижения крана
=0.9 – КПД механизма передвижения
W – полное сопротивление.
Выбираем двигатель МТН411-8 [6] с.41 мощность Рэ=15 кВт частота вращения пэ=705 обмин максимальный момент Мтах=580 Н·м маховой момент ротора Мр=2.15 кг·м2 масса т=280 кг.
Проверка двигателя по условиям пуска:
Условие пуска выполняется.
1. Угловая скорость ходового колеса:
где V=1.16мс – скорость передвижения крана;
Dхк=0.56м – диаметр ходового колеса крана.
где э – угловая скорость электродвигателя
Выбираем червячный редуктор типа РЦЧ-210 КПД=0.8 передаточное отношение U=20.
Для разрабатываемого крана принимаем тормоз ТГК-160. Тормозной момент ТТ=100Нм..
кр=1 – коэффициент сопротивления реборды [3] с.422
d=15 cм – диаметр подшипникового колеса
Суммарное давление ведущих колес на рельсы:
На кране установлено 4 тормоза по одному на привод.
Общий тормозной момент:
Усилие тормоза приведенное к валу колес:
Конструкция сварной балки пролетом l=32 м. Балка нагружена равномерной нагрузкой от собственного веса q=035 Тм и двумя сосредоточенными грузами Р=35 Т (от веса тележки с грузом) которые могут перемещаться по балке.
Расстояние между осями тележки d=18 м; материал – сталь Ст. 3; допускаемое напряжение []р=16 кГмм2. Наибольший прогиб балки f от сосредоточенных грузов не должен превышать 1500 ее пролета.
Конструирование балки следует начать с определения расчетных усилий М и Q.
Построим линии влияния моментов чтобы знать их максимально возможные значения в разных сечениях балки.
В сечении Ордината линии влияния
l M=025l=025·32=800
Величина изгибающего момента от сосредоточенных сил:
Р – величина сосредоточенного груза.
В сечении при l=32 м и d=1.8 м
Определим изгибающие моменты от равномерно распределенной нагрузки:
Вычислим суммарные величины моментов в сечениях от сосредоточенных сил и равномерной нагрузки:
Таким образом расчетной величиной момента для балки является М=97.65 Тм=976500 Нм.
Требуемый момент сопротивления балки для этого усилия равен:
Производим построение линии влияния поперечной силы:
в сечении х=0 ордината линии влияния Q0=1;
в сечении х=0.2l ордината линии влияния Q0=0.8
Определим расчетные усилия от сосредоточенных сил в каждом из указанных сечений того что одна из них располагается над вершиной линии влияния:
В сечении х=0 при l=32 м и d=1.8 м
Поперечные силы Q от собственного веса q равны;
Расчетные значения поперечных сил от сосредоточенных и равномерно распределенных нагрузок:
Требуемая высота балки из условий жесткости:
При этом h=0.053·3200=85.33 см.
Толщина вертикального листа:
Требуемая высота из условия наименьшего веса.
Принимаем высоту балки h=175 см
Высота вертикального листа hв=173 см
Момент инерции поперечного сечения сварной балки:
Момент инерции подобранного вертикального листа 1730×8 мм:
Требуемый момент инерции горизонтальных листов балки (поясов):
Сечение одного пояса балки:
Уточненное значение момента инерции подобранного поперечного сечения балки:
Наибольшее нормальное напряжение в крайнем волокне балки:
Касательное напряжение на уровне центра тяжести балки в опорном ее сечении:
где Q=12403 кГ – расчетная поперечная сила;
S – статический момент половины площади сечения относительно центра тяжести балки.
Эквивалентное напряжение:
где 1 – нормальное напряжение от М;
– касательное напряжение от Q;
где S=12.5·1·87=1087.5 – статический момент площади сечения горизонтального листа относительно центра тяжести;
где b – ширина пояса;
sГ – толщина горизонтального листа;
l0= 10÷20=1245 см – расстояние между закреплениями.
Зная функцию α по графику [12 с.315] определяем коэффициент =1.73
Момент инерции балки:
Найдем коэффициент φ:
устойчивость обеспечена
Устойчивость вертикального листа:
Привариваем к листу ребра жесткости. Расстояние между ними
Среднее касательное напряжение от поперечной силы:
Местное напряжение под сосредоточенной силой:
где z – условная длина на которой сосредоточенный груз распределяется в вертикальном листе;
где JП – момент инерции верхнего пояса с приваренным к нему рельсом;
где JП - момент инерции относительно оси а;
у – ордината центра тяжести сечения пояса и рельса;
Проверим правильность постановки ребер жесткости:
где – отношение большей стороны к меньшей; в принятой конструкции аhв=1.5;
d – наименьшая из сторон пластин (а или hв) заключенных между поясами и ребрами жесткости; В данном случае d=hв=173 см;
По графику определяем К1=8.6 [12 с.318]
Местная устойчивость вертикального листа:
Устойчивость в опорных сечениях:
Устойчивость обеспечена.
Требования предъявляемые к механизмам козлового крана
По условиям использования кран относится к группе машин универсального назначения используемых для работы на открытом воздухе в одну-две смены в повторно-кратковременном режиме.
Механизмы кранов характеризуются относительной продолжительностью включения когда время включения и время пауз регулярно чередуется.
Режим работы грузоподъемной машины циклический. Цикл состоит из перемещения груза по заданной траектории и возврата машины к исходному положению для нового цикла.
Группа режима работы крана по ГОСТ 25835-83 – М6 характеризуется следующими показателями:
коэффициент сменности работы крана – 2;
среднесуточное время работы (включения) механизма - 4÷10 часов.
Классификация режима работы электрооборудования по правилам Госгортехнадзора для М6 следующая:
режим работы механизма или электрооборудования – Т (тяжелый);
коэффициент использования крана по грузоподъемности Кгр – 075÷1;
ПВ (продолжительность включения)– 40 % ;
число включений в час среднее за смену – 240.
Так как кран работает на открытом воздухе среднесуточное изменение температуры может доходить до 30. Это приводит к выпадению на поверхности частей крана конденсата атмосферной влаги и соляного тумана. В смеси с производственной пылью конденсат вызывает снижение поверхностной изоляции между токоведущими частями и коррозию металлических деталей. Для обеспечения необходимой надежности электрооборудования оно должно отвечать следующим основным требованиям ГОСТ 15150-69:
температура окружающей среды – от -40 до+40;
относительная влажность воздуха - 95% при +20;
вибрация – частота 1-50Гц с ускорением 05g.
Для предохранения от воздействия неблагоприятных факторов внешней среды крановое электрооборудование должно быть достаточно защищенным размещаться в кожухах и оболочках с необходимой степенью защиты ГОСТ 14254-80.
Крановые электроприводы получают питание от трехфазной сети переменного тока. Основным напряжением для питания крановых механизмов является напряжение 380 В.
К козловому крану предъявляются следующие требования:
электропитание крана и тележки осуществляется с помощью гибкого кабеля;
для обеспечения достаточного запаса колес тележки с рельсами и исключение пробуксировки применены два привода передвижения тележки;
вся аппаратура управления размещена в герметизированном контейнере со степенью защиты от внешней среды ТР44;
электроприводы крана имеют глубокое регулирование скорости в связи с этим нагрузка тормозов минимальная;
резисторы выбраны из стандартных блоков Б6 и БК 12.
Для механизмов передвижения крана и тележки принята система с импульсно-ключевым регулированием обеспечивающая устойчивое регулирование скорости в двигательном и тормозных режимах в диапазоне 1:10. При этом обеспечивается снижение нагрузок на механические тормоза до минимума и точный вывод крюка на бункеры без дополнительного количества толчковых включений. Поскольку оперативным торможением является электрическое торможение противовключением механические тормоза имеют необходимые тормозные противоугонные моменты.
Защита главных электрических цепей крана осуществляется защитными устройствами с использованием автоматических включений с высокой коммутационной защитной способностью.
Системы с импульсно-ключевым регулированием имеют по технологическому процессу диапазон регулирования наилучшие экономические показатели.
Выбор системы управления крановыми двигателями
Под системой управления электроприводом подразумевается комплекс состоящий из преобразователя электрической энергии аппаратуры управления для коммутации тока в цепи электродвигателя орган ручного управления или автоматического (программного) контроля органа скоростного путевого или иного контроля а так же элементов защиты электрооборудования и механизма действующих в конечном счете на устройства отключения электропривода.
Аппаратура управления электропривода является комплексом включающим контактные и бесконтактные устройства коммутации в цепях электродвигателя преобразователей энергии и управления а так же элементы защиты электрических цепей.
Если контактные коммутационные элементы аппарата с непосредственно ручным приводом предназначаются для коммутации цепей главного тока то такое устройство называется силовым кулачковым контроллером а если эти элементы служат для коммутации цепей управления то такой аппарат называется командоконтроллером.
Система управления крановыми механизмами применяющаяся в данном козловом кране относится к категории устройств находящихся под непрерывным контролем оператора то есть в этой системе выбор момента начала операции скоростных параметров и момента окончания операции осуществляется лицом управляющим механизмом. В свою очередь система управления обеспечивает необходимую последовательность переключения для реализации желаемых скоростных параметров предотвращает при этом недопустимые перегрузки и обеспечивает необходимую защиту.
В нашем случае применяется крановый электропривод переменного тока: асинхронный двигатель с фазным ротором управляемый силовым контроллером (КС).
Расчет механизма подъема: Методическое пособие
Справочник по кранам: В 2т. Т. 2; Под ред. М.П. Александров
М.М. Гохберг – М:. Высш. шк. 1988
Подъемно транспортные машины: М.П. Александров – М:. Высш.
Крановый электропривод: Справочник А.Г. Яуре – М:. Энергоатомиздат 1988
Приводы машин: Справочник В.В. Длоугий – Л:. Машиностроение 1982
Справочник технолога-машиностроителя. т.1 под ред. А.Г.Косиловой и Р.К.Мещерякова. – М.: Машиностроение 1985 г.
Рекомендуемые чертежи
Свободное скачивание на сегодня
Другие проекты
- 29.08.2014