Кран консольный с электроталью грузоподъемностью 0,5 т




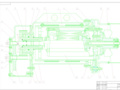
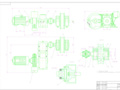
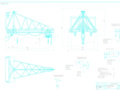
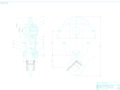
- Добавлен: 25.10.2022
- Размер: 1 MB
- Закачек: 0
Описание
Состав проекта
![]() |
![]() ![]() ![]() |
![]() |
![]() |
![]() ![]() ![]() ![]() |
![]() ![]() ![]() ![]() |
![]() ![]() ![]() ![]() |
![]() ![]() ![]() ![]() |
![]() ![]() |
![]() ![]() ![]() |
![]() ![]() ![]() |
![]() ![]() |
![]() ![]() |
![]() ![]() ![]() |
![]() ![]() |
![]() ![]() ![]() |
Дополнительная информация
СПЕЦ1.doc
Манжеты ГОСТ 8752-79
Подшипники ГОСТ8338-7
Электромагнит МО-100Б
02281-Механизм передвижения крана.dwg

Остальные технические требования по СТБ 1022-96
Таль.dwg

Общий Вид.dwg

передвижения тали ммин 16
Высота подъема груза
Схема запасовки каната
Кинематическая схема
02167-Подвеска_крюковая.dwg

записка ПТМ.doc
грузоподъёмностьQ = 32 т
скорость подъёма грузаVгр = 12 ммин
скорость передвижения электроталиVT = 16 ммин
высота подъёма грузаН = 12 м
группа режима работы кранаА4
рисунок 1.1 – Кинематическая схема механизма подъема.
2Выбор конструкции полиспаста кинематическая схема
полиспаста КПД полиспаста
По рекомендациям принимаем одинарный полиспаст (а=1)
Рисунок 1.2 – Схема полиспаста
КПД полиспаста определим по формуле:
где hбл=097 098 – КПД блоков
n=7 – количество подвижных и неподвижных блоков
3 Выбор каната и крюка
Максимальное натяжение в канате набегающем на барабан при подъёме груза определяется по формуле (125 [1]):
где Q -- грузоподъемность;
hп – КПД полиспаста;
Канат выбираем по разрывному усилию:
где np= 55 – коэффициент запаса для режима работы А4
По полученному разрывному усилию выбираем канат стальной двойной свивки типа ЛК-О конструкции 6x19(1+9+9)+1о.с. ГОСТ 7665-69 диаметром dк=13 мм площадью сечения всех проволок Fк=6094 мм2 и с разрывным усилием Sр=98 кН.
По номинальной грузоподъёмности и режиму работы выбираем крюк однорогий тип А №12 ГОСТ 6627-74.
4 Расчёт диаметров барабана и блоков определение длины барабана
Диаметр блоков по средней линии навитого каната определяем по формуле:
где h2=20 – коэффициент выбора диаметра для блока для режима работы А4;
Диаметр барабана по средней линии навитого каната определяем по формуле:
где h1=20 – коэффициент выбора диаметра для барабана
Из конструктивных соображений принимаем диаметр барабана мм так как при меньшем диаметре значительно увеличивается длина барабана.
Длина барабана определяется по формуле:
Определяем шаг нарезки на барабане
– общее число витков на барабане;
где – число рабочих витков;
– количество запасных витков которое остается на барабане при спуске груза на полную высоту;
5 Определение мощности на подъём груза номинальной массы при
установившемся движении механизма выбор двигателя
Определяем мощность на подъем груза номинальной массы по формуле :
Подбираем электродвигатель серии MTF-211-6 при ПВ=25% номинальная мощность (Nн) 9 кВт частота вращения ротора n1=915 мин-1 момент инерции ротора Iр=0117 кг·м2.
Определяем частоту вращения барабана:
Следовательно потребное передаточное отношение механизма:
Редуктор электротали двухступенчатый. Принимаем передаточное число тихоходной ступени: тогда передаточное число быстроходной ступени: .
Модуль быстроходной ступени мм тихоходной – мм.
Межосевое расстояние:
Фактическое передаточное число редуктора:
Фактическая скорость подъема
Делительный диаметр d мм
Ширина зубчатого венца b мм
Номинальный момент на валу электродвигателя:
Номинальные крутящие моменты на валах редуктора.
Статический крутящий момент на валу барабана при подъеме груза:
где – к.п.д. зубчатой передачи одной ступени.
7 Проверка редуктора на прочность и выносливость
Произведем проверочный расчет закрытых зубчатых передач на выносливость по контактным напряжениям и на прочность зубьев при изгибе.
Зубчатые колеса редуктора механизма подъема изготавливаются из материала сталь45 и подвергаются термообработке до твердости НВ 241 277.
Определяем допустимые контактные напряжения.
где – коэффициент безопасности ;
– коэффициент долговечности .
Определяем допустимые изгибные напряжения.
где – коэффициент учитывающий двустороннее приложение нагрузки
– коэффициент долговечности ;
– коэффициент безопасности .
Для расчета берем меньшее из допускаемых напряжений МПа и МПа расчет ведем по шестерням.
Определяем окружные силы в зацеплениях:
Окружные скорости шестерен:
Удельные окружные динамические силы:
где– коэффициент учитывающий влияние вида зубчатой передачи и модификации профиля на динамическую нагрузку;
– коэффициент учитывающий влияние разности шагов зацепления зубьев шестерни и колеса.
Удельная расчетная окружная сила в зоне ее наибольшей концентрации:
где – коэффициент учитывающий неравномерность распределения нагрузки по ширине венца.
Коэффициенты учитывающие динамические нагрузки в зацеплениях:
Удельные расчетные окружные силы:
где – коэффициент внешней динамической нагрузки.
Расчетные контактные напряжения:
где– коэффициент учитывающий форму сопряженных поверхностей зубьев для прямых зубьев;
– коэффициент учитывающий механические свойства материалов колес;
– коэффициент учитывающий суммарную длину контактных линий для прямых зубьев;
Условие выносливости по контактным напряжениям выполняется.
где– коэффициент учитывающий влияние вида зубчатой передачи и модификации профиля на динамическую нагрузку.
Удельные расчетные окружные силы в зоне их наибольшей концентрации:
где– коэффициент учитывающий неравномерность распределения нагрузки по ширине венца.
Удельные расчетные окружные силы при изгибе:
Расчетные напряжения изгиба зубьев:
где– коэффициент учитывающий форму зуба;
– коэффициент учитывающий наклон зуба для прямых зубьев;
– коэффициент учитывающий перекрытие зубьев для прямых зубьев.
Условие прочности по напряжениям изгиба выполняется.
8 Выбор тормоза проверочный расчёт тормоза
Статический момент на тормозном валу:
где – КПД полиспаста;
– КПД зубчатой передачи;
где km=15 – коэффициент запаса торможения.
Расчет тормоза электротали.
Расчетная схема тормоза приведена на рисунке 1.8. необходимое усилие пружины замыкающей тормоз:
где – коэффициент трения между сталью и асбестовой лентой;
– коэффициент учитывающий потери на трение в опорах рычагов.
Момент требуемый для размыкания тормоза с учетом трения между рабочими поверхностями:
где – коэффициент трения сталь по стили;
м – средний диаметр рабочих поверхностей.
Тогда необходимое усилие на штоке электромагнита:
Угол поворота рычага тормоза для отвода колодок на 06 мм определяется по формуле:
где м – отход колодки от шкива;
м – допустимый износ колодок
Требуемый ход штока электромагнита:
По необходимому тяговому усилию и ходу подбираем электромагнит серии МИС-3100 со следующими характеристиками:
Тормоз регулируется на необходимый тормозной момент.
Проверочный расчёт по удельному давлению:
где м – ширина тормозного шкива;
– допускаемое удельное давление;
– угол обхвата шкива
Удельное давление в допускаемых пределах.
Проверочный расчёт на нагрев:
где [qv] – допускаемая удельная мощность трения;
– окружная скорость вращения шкива;
Выбранный тормоз отвечает условию нагрева.
Расчет грузоупорного тормоза
Определим угол трехзаходной резьбы тормозного вала:
где: α =3 –число заходов резьбы
Осевая сила возникающая при торможении и зажимающая фрикционные кольца тормоза:
где: ρ=2 3 – угол трения в резьбовой паре при работе в масляной ванне
f=012-коэффициент трения вальцованной ленты по стали в масле
Rc=00925-средний радиус поверхности трения
Тормозной момент грузоупорного тормоза:
где: n=2-число пар трущихся поверхностей
Тормозной момент должен удовлетворять следующему условию:
Грузоупорный тормоз в электротали используется в качестве второго тормоза механизма подъема поэтому коэффициент запаса торможения принимается равным 1.25
Надежность удерживания груза в подвешенном состоянии обеспечивается при соблюдении зависимости:
Движущийся вниз груз остановится при условии:
Проверка резьбы на смятие:
где: dН-диаметр наружный винтовой резьбы
dВ-диаметр внутренний винтовой резьбы
z-число витков резьбы воспринимающих нагрузку
9 Проверка двигателя на пусковые перегрузки
Для проверки электродвигателя на пусковые перегрузки определяем статический момент валу двигателя при пуске:
Минимальный пусковой момент электродвигателя
где y1 = 16 – кратность минимального пускового момента
Возможность пуска электродвигателя под нагрузкой определяется по условию т.е. 1515 > 749. Условие выполняется.
где y2 = 21 – кратность максимального пускового момента
Определяем средний пусковой момент двигателя:
Потребное время пуска электродвигателя определим по формуле (4.1 [4]):
где с-1 – угловая скорость двигателя;
- момент инерции всех движущихся частей механизма приведенный к валу электродвигателя;
где - момент инерции вращающихся частей механизма;
- момент инерции поступательно движущихся частей механизма;
где g =11 12 – коэффициент учёта инерции вращающихся масс расположенных на втором третьем и последующих валах механизма
кг.м2 – момент инерции вращающихся масс на первом валу
где. – момент инерции тормозного шкива;
– момент инерции ротора электродвигателя.
где rб – радиус барабана по центру наматывания каната
Динамический момент при пуске определяем по формуле:
Определяем потребный средний пусковой момент:
Следовательно двигатель выдержит пусковые перегрузки.
10 Проверка двигателя на нагрев по среднеквадратичному моменту
Среднеквадратичный момент определяется по формуле:
где - средний пусковой момент
- суммарное время пуска в течение одного цикла
- время установившегося движения
- сумма квадратов статических моментов при подъёме и опускании груза
- продолжительность цикла
Определим моменты развиваемые двигателем в различные периоды его работы и при транспортировании различных по весу грузов. Вес грузов принимается в соответствии с графиком использования механизма подъёма по грузоподъёмности: Q 075Q 02Q (рис. 158 [3]).
Статический момент при подъёме определяется по формуле:
где - натяжение каната на барабане при подъёме груза заданного веса
- КПД механизма принимаемый по экспериментальному графику рис. 101 [3]
где - коэффициент учитывающий потери на блоках;
i – кратность полиспаста.
Статический момент при опускании заданного груза:
где - натяжение каната на барабане при опускании груза заданного веса
Определяем время установившегося движения:
где – средняя высота подъема.
Время пуска двигателя при подъёме и опускании груза равно:
Тс – статический момент при подъёме или опускании груза
Знак «–» – при подъёме «+» – при опускании.
Расчёты для грузов массами 075Q и 02Q заносим в таблицу 1.10.
Таблица 1.10 – Результаты расчёта по проверке двигателя на нагрев
Натяжение каната при подъеме груза Н
Момент при подъеме груза Н·м
Натяжение каната при опускании груза Н
Момент при опускании груза Н·м
Время пуска при подъеме с
Время пуска при опускании с
Используя данные таблицы получаем :
Среднеквадратичная мощность двигателя:
Так как = 757 кВт = 9 кВт то выбранный двигатель удовлетворяет условию нагрева
11 Определение толщины стенки барабана
Барабан отлит из Сталь 20 с пределом прочности на сжатие (таблица 5.2 [4]).
Предварительно толщину стенки барабана определяем из расчёта на сжатие:
Из условия технологии изготовления литых барабанов толщина стенки их должна быть не менее 6 мм и может быть определена по формуле:
Принимаем толщину стенки мм.
Расчёт крепления каната к барабану
Рисунок 2 – Крепление каната к барабану
Определим выдергивающее усилие:
где: a - угол обхвата канатом барабана принимаем a=4p
f - коэффициент трения между канатом и барабаном (f=0.10 0.16)
Необходимое осевое усилие болта:
где - приведенный коэффициент трения между канатом и барабаном
где b =40о – угол заклинивания каната
a1=2p - угол обхвата барабана канатом при переходе от одной канавки планки к другой
Необходимое число планок крепления :
где []—допускаемое напряжение сжатия болта.
d1=13 – внутренний диаметр болта М14 изготовленного из Ст3
Принимаем две прижимные планки.
Суммарное напряжение в болте при затяжке крепления с учётом растягивающих и изгибающих усилий:
где n=1.5 – коэффициент запаса надёжности крепления каната к барабану
l=10 мм – расстояние от дна канавки на барабане до верхней плоскости прижимной планки
Допускаемое напряжение для болта:
Мпа - предел текучести для стали Ст3
Так как болты отвечают условию прочности
13 Расчет валов тали
Произведём расчёт быстроходного вала редуктора.
Определим минимальный диаметр вала:
=30 МПа – допустимые касательное напряжение.
Принимаем диаметр вала под подшипники мм
Рассчитаем промежуточный вал:
Минимальный диаметр вала исходя из условия прочности равен:
Диаметр вала под подшипник принимаем мм.
Рассчитаем тихоходный вал.
Внутренний диаметр полого тихоходного вала принимаем мм внешний мм. Проверяем вал на прочность:
– допустимые касательные напряжения.
Условие прочности выполняется.
14 Выбор подшипников электротали
Выбор подшипников осуществляем по посадочному диаметру на валу и динамической нагрузке.
Определяем радиальные нагрузки действующие на подшипники быстроходного вала. Схема нагружения вала представлена на рисунке 1.14.1.
Определяем силу в месте посадки ротора электродвигателя:
Определяем усилия в зацеплении:
Определим реакции опор в горизонтальной плоскости. Составим сумму моментов относительно опоры А.
Составим сумму моментов относительно опоры В.
Запишем сумму моментов относительно опоры А в вертикальной плоскости:
Определяем суммарные реакции в опорах А и В:
Выбор подшипников производим по наибольшей нагрузке Н частота вращения вала обмин.
Требуемая долговечность: ч.
Принимаем шариковый радиальный однорядный подшипник №106 у которого: d = 30 мм; B = 13 мм; D = 55 мм; C = 68 кН.
Определяем приведенную нагрузку подшипника.
где –коэффициент учитывающий динамичность внешней нагрузки;
–коэффициент учитывающий влияние температуры подшипникового узла;
Расчетная динамическая радиальная грузоподъемность.
где m = 3 – для шарикоподшипников;
n = 920 обмин – частота вращения тихоходного вала.
У принятого подшипника кН > кН. Следовательно подшипник подобран правильно
Определяем радиальные нагрузки действующие на подшипники быстроходного вала. Схема нагружения вала представлена на рисунке 1.14.2.
Строим эпюру изгибающих моментов в горизонтальной плоскости. Определим реакции опор в горизонтальной плоскости. Составим сумму моментов относительно опоры А.
Строим эпюру изгибающих моментов в вертикальной плоскости.
Запишем сумму моментов относительно опоры А:
Предварительно принимаем шариковый радиальный однорядный подшипник №311 у которого: d = 55 мм; B = 18 мм; D = 90 мм; C = 281 кН.
n = 250 обмин – частота вращения тихоходного вала.
У принятого подшипника кН > кН. Следовательно подшипник подобран правильно.
Определяем радиальные нагрузки действующие на подшипники быстроходного вала. Схема нагружения вала представлена на рисунке 1.14.3.
Определяем силу сгибающую барабан:
n = 8913 обмин – частота вращения тихоходного вала.
У принятого подшипника кН > кН. Следовательно подшипник подобран правильно. Из конструктивных особенностей на опору А выбираем подшипник серии 1000916 у которого: d=80мм; B=16мм; D=110мм; C=275 кН.
15 Расчёт подшипников блоков
Выбор подшипников производим по нагрузке Н частота вращения вала:
Dбл – диаметр блока по центру наматывания каната.
Предварительно принимаем шариковый радиальный однорядный подшипник №104 у которого: d = 20 мм; B = 12 мм; D = 42 мм; C = 128 кН.
n = 7419 обмин – частота вращения тихоходного вала.
14 Расчёт крюковой подвески
14.1 Упорный подшипник
Расчётная нагрузка на подшипник должна быть равна или меньше статической грузоподъёмности:
где - коэффициент безопасности (прил. Х [1])
Для крюка №12 диаметром шейки d1=40 мм выбираем упорный однорядный подшипник средней серии 8208 (ГОСТ 6874-75) со статической грузоподъёмностью С0=39400 Н внутренний диаметр d=40 мм наружный D=68 мм (прил. IX [1]).
14.2 Расчёт траверсы крюка
Траверса изготовлена из Стали 45 имеющей предел прочности sв=600 Мпа предел текучести sт=420 Мпа предел выносливости s-1=240 Мпа.
Траверсу рассчитывают на изгиб при допущении что действующие на неё силы сосредоточенные. Расстояние между осями щек b=60 мм.
Максимальный изгибающий момент (сечение А – А):
где Qp – расчётная нагрузка на траверсу (как и на упорный подшипник)
Момент сопротивления среднего сечения траверсы:
где [s] – допускаемое напряжение материала на изгиб
где d2 =d1+(2 5) =44 мм
b1 – ширина траверсы; назначается с учётом наружного диаметра D1 посадочного гнезда для упорного подшипника
b1=D1+(10 20)=68+10=78 мм
Рисунок 1.14.2 – Траверса
Момент сопротивления среднего сечения траверсы ослабленной отверстием:
W = (b1-d2)*h2= (60-44)*302 = 2.4 см3
Изгибающий момент в сечении Б-Б:
M = Qр*(b2-l2)2 = 37632*(003-0025)2 = 9408 см3
Расчёт механизма передвижения электротали
1 Выбор кинематической схемы
Механизм передвижения электротали состоит из электродвигателя закрытого одноступенчатого редуктора трех открытых зубчатых передач и четырех конических колес с ребордами два из которых (с одной стороны) на реборде имеют зубчатые венцы и приводятся во вращение от электродвигателя.
Расчет механизма передвижения тали
1 Кинематическая схема
Рисунок 2.1 - Кинематическая схема механизма передвижения тали
2 Сопротивление передвижению тали
При расчётах подвесных кранов работающих в закрытых помещениях сопротивление передвижению тележки вычисляют по формуле:
где d=40 мм – диаметр цапфы ходового колеса
f=0.015 – коэффициент трения в подшипниках колёс
m=0.4 мм – коэффициент трения качения колеса по рельсу с выпуклой головкой
kp=2.5 – коэффициент учитывающий сопротивление от трения реборд о рельсы и от трения токосъёмников о троллеи (табл. 28 [1]).
a=0.003 – расчётный уклон пути
Сопротивление создаваемое уклоном:
Сопротивление создаваемое силами инерции:
где: -коэффициент учитывающий инерцию вращающихся частей механизма
а=0.15- ускорение при разгоне
Сопротивление создаваемое раскачиванием груза на гибкой подвеске:
Полное сопротивление передвижению тали:
3 Расчёт мощности двигателя
Предварительное значение КПД механизма принимаем равным hпр=0.85
Определяем необходимую мощность:
Выбираем двигатель типа АОЛ2-31-6 (прил. ХХХIV [1]) имеющий параметры: N=15 кВт; ПВ=25 %; n=950 мин-1; J=0.00135 кг.м2.
Частота вращения колеса:
Требуемое передаточное отношение:
Фактическая скорость передвижения тали:
4 Расчет закрытой зубчатой передачи
Расчет производится на выносливость по контактным напряжениям и на прочность зубьев при изгибе:
Принимаем модуль зубчатого зацепления m=2
Передаточное число первой ступени: U1=z1 z2 =11013=84
Передаточное число второй ступени: U2=z1 z2 =6114=44
Делительный диаметр: мм
Выбираем Ст.20 : HB =150
4.1 Проверка расчетных контактных напряжений
Окружная сила в зацеплении:
Коэффициент учитывающий динамическую нагрузку в зацеплении:
Коэффициент учитывающий неравномерность распределения нагрузки по ширине венца: кH =1.05
Удельная расчетная окружная сила:
zн =177 ( коэф. учитывающий форму сопряженных поверхностей зубьев )
zЕ =275 МПа ( коэф. учитывающий механические свойства материалов колес )
z =1 ( коэф. суммарной длины контактных линий)
Запас прочности по контактным напряжениям:
Условие прочности соблюдается.
4.2 Проверка расчетных напряжений изгиба
Удельная расчетная окружная сила при изгибе:
Коэффициент учитывающий неравномерность распределения нагрузки по ширине венца: кF =1
Коэффициент учитывающий неравномерность распределения нагрузки для одновременно зацепляющихся пар зубьев: кFα =1
Коэффициент внешней динамической нагрузки: кА=125
Расчетные напряжения изгиба:
YFS=4.2 (коэффициент учитывающий форму зуба)
Y=1 (коэффициент учитывающий наклон зуба)
Y=1 (коэффициент перекрытия зубьев)
Запас прочности по напряжениям изгиба:
Условие прочности выполняется
5 Расчёт тормозного момента и выбор тормоза
Сопротивление передвижению тали без груза от уклона:
Сопротивление создаваемое трением:
Сопротивление создаваемое инерцией:
Момент создаваемый уклоном:
Момент создаваемый силами трения:
Момент создаваемый силами инерции:
Расчетный тормозной момент механизма передвижения тали при работе без груза:
Исходя из того что значение требуемого тормозного момента очень мало и
учитывая рекомендации тормоз на механизм передвижения электротали можно не устанавливать.
6 Проверка электродвигателя на время разгона.
Номинальный момент двигателя:
Среднепусковой момент двигателя:
Момент статических сопротивлений при разгоне приведенный к валу двигателя:
Момент инерции при разгоне поступательно движущихся частей механизма приведенный к валу двигателя:
Момент инерции при разгоне всех движущихся частей механизма приведенный к валу двигателя:
Время разгона для механизма передвижения тали:
Время разгона для тали не должно превышать 4 с [1]. Полученное время tр.ф. удовлетворяет этому условию. Следовательно выбранный двигатель обеспечит необходимую интенсивность работы.
Проверим среднее ускорение при разгоне:
Это значение не превышает среднего допускаемого [а]=03 мс2 [1]
7 Проверка запаса сцепления колес с опорной поверхностью при разгоне
Минимальное значение коэффициента сопротивления передвижению при Кдоп=1
Статическое сопротивление движению при разгоне:
Сила инерции масс тали:
Запас сцепления ходовых колес с опорной поверхностью при разгоне на подъем:
Для обеспечения запаса сцепления сделаем два приводных колеса.
Ксц=07*2=14>[Ксц]=12
-коэффициент сцепления приводного колеса с опорной поверхностью
[ксц]-допускаемый коэффициент запаса сцепления при работе без ветровой нагрузки. Запас сцепления колес с опорной поверхностью обеспечен.
Смазка узлов и деталей крана
В зависимости от требований предъявляемых к смазочным материалам узлы детали крановых механизмов делятся на следующие основные группы: редукторы и зубчатые муфты открытые передачи подшипники качения и скольжения реборды ходовых колес рельсы и направляющие канаты.
Для редуктора применимы трансмиссионные масла. Существенные особенности трансмиссионных масел по ГОСТ 23652-79 – их всесезонность длительные сроки службы и высокая нагрузочная способность.
Для подшипников качения предпочтительны всесезонные смазки из числа обладающих хорошим антикоррозионным действием и длительным сроком службы.
Реборды ходовых колес смазывают с помощью графитных стержней (ТУ 32ЦТ 558-74).
Пресс солидол С. ГОСТ 4366-76 - смазка для подшипников открытых передач направляющих.
Графитная смазка ГОСТ 333-80 применяется для смазки реборд ходовых колёс и канатов.
Смазочные материалы не должны содержать посторонних примесей.
Техника безопасности
К управлению краном допускаются лица не моложе 18 лет имеющие соответствующее удостоверение и прошедшие медицинский осмотр для пригодности работы на кране.
Перед началом работы машинист обязан проверить техническое состояние основных механизмов и узлов крана (тормозов крюка канатов блоков металлоконструкции крана) и исправной работы приборов безопасности.
Эксплуатация электроталей и надзор за ними должны производится в соответствии с изданными Госгортехнадзором «Правилами устройства и безопасной эксплуатации грузоподъемных кранов».
Надзор за электроталями возлагается распоряжением администрации на определенное лицо технического персонала обладающее соответствующей квалификацией и опытом которое и является ответственным за исправное состояние электроталей и их безопасную эксплуатацию.
Напряжение в электросети не должно быть ниже действующих норм в противном случаи электроталь тормоз и магнитные пускатели будут работать ненормально.
Не допускается подъем грузов превышающих номинальную грузоподъемность а также превышение указанного в технической характеристике режима работы и эксплуатация электроталей в условиях не допускающих их применение.
При управлении электроталью рабочему следует находиться со стороны открытой части барабана.
Нельзя допускать такой подвески груза при которой получается недопустимое нагружение острия крюка. В таких случаях крюк может заметно разогнуться.
Подтаскивание грузов электроталью при косом натяжении канатов отрывание прикрепленных предметов а также производство с помощью электротали несвойственных для нее работ запрещается.
Категорически запрещается пользоваться шланговым проводом в качестве тяги для горизонтального перемещения электротали.
Правилами ГГТН а также стандартом СЭВ 725-77 на грузоподъёмных кранах с электрическим приводом предусмотрена установка концевых выключателей для автоматической остановки:
крана если его скорость может превышать 0533 мс (по стандарту СЭВ–05 мс);
механизма подъёма грузозахватного устройства перед подходом к упору.
При подъеме груза не следует доводить обойму крюка до конечного выключателя.
Конечный выключатель является аварийным ограничителем. Пользоваться им как постоянно действующим автоматическим остановом не разрешается.
Совершенно необходимо в начале каждой смены проверять исправность действия конечного выключателя.
Концевой выключатель механизма передвижения устанавливают таким образом чтобы в момент выключения тока расстояние от буфера до упоров составляло не менее половины пути торможения. Концевые выключатели устанавливают в электрической цепи так чтобы при их размыкании сохранилась цепь для обратного движения механизма. Для данного крана применяем концевой выключатель ВПК-2110.
Концевой выключатель механизма подъёма устанавливают так чтобы после остановки грузозахватного устройства зазор между ним и упором на тележке составлял не менее 200 мм. Для этой цели применяют выключатели типа КУ 703 имеющий двуплечий рычаг.
Основной целью данного курсового проекта было обучение основам конструирования сложной машины закрепление углубление и обобщение знаний приобретенных при изучении теории дисциплины “Грузоподъемные машины” и ”Строительная механика и металлоконструкции подъемно-транспортных машин”.
В данном курсовом проекте был разработан кран на колонне грузоподъемностью 05 т. Произведены расчеты механизмов крана подобраны двигатели редуктора тормоза механизма подъема поворота крана передвижения электротали а так же даны рекомендации по технике безопасности при работе с краном и условия смазки узлов. Проверочные расчёты показали что спроектированный кран отвечает всем требованиям стандартов и способен выполнять необходимые технологические операции.
Список использованных источников
Иванченко Ф.А. и др. Расчеты грузоподъемных и транспортирующих машин.-2изд. перераб. и доп.–Киев.: Вища школа 1978.–574 с.
Анфимов М.И. Редукторы. Конструкции и расчет: Альбом.–4-е изд. перераб. И доп. –М.: Машиностроение 1993.–464с.
Курсовое проектирование грузоподъёмных машин. Руденко Н.Ф. Александров М.П. и Лысяков А.Г. Изд. 3-е перераб. и доп. М.: Машиностроение 1971 464 с.
Курсовое проектирование грузоподъёмных машин: Учеб. Пособие для студентов машиностр. вузов; Под ред. С.А. Казака.-М.:Высш. Шк. 1989. – 319 с.
Курмаз Л.В. Детали машин. Проектирование: Учеб. пособие –Мн.: УП «Техноприт» 2001.-290 с.
СПЕЦ2.doc
Кольцо ГОСТ 13943-86
Подшипники ГОСТ8338-7