Консольно-передвижной кран г/п 1,25 т



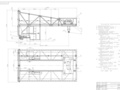
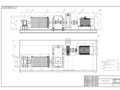
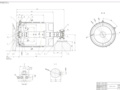
- Добавлен: 25.10.2022
- Размер: 3 MB
- Закачек: 1
Описание
Состав проекта
![]() |
![]() ![]() ![]() ![]() |
![]() ![]() ![]() |
![]() ![]() ![]() ![]() |
![]() ![]() ![]() |
![]() ![]() ![]() |
![]() ![]() |
![]() ![]() ![]() ![]() |
![]() ![]() ![]() |
![]() ![]() ![]() |
![]() ![]() ![]() |
Дополнительная информация
мех.под_.dwg

Механизм подъема (общий вид)
Техническая характеристика
Скорость подъема груза
тип. . . . . . . . . . . . . . . . MTF 111-6
кВт . . . . . . . . . . . . 2.8
тип . . . . . . . . . . . . . . . . . Ц2-200
передаточное число . . . . . . . 50
тип . . . . . . . . . . . . . . . . ТКГ-200
мой КУРСОВИК ГПМ_.docx
Расчет механизма подъема 5
1. Выбор схемы механизма подъема и выбор типа подвески 5
2. Определение максимального усилия в канате и его выбор 5
4. Расчет упругого подшипника крюка 7
5. Расчет гайки крюка 8
6. Расчет элементов подвески 8
7. Расчет блоков подвески 10
8. Расчет барабана 12
9. Расчет узла крепления каната 14
10. Расчет вала барабана 16
11. Расчет подшипников оси барабана 18
12. Выбор электродвигателя 19
13. Выбор редуктора 20
14. Расчет узла соединения редуктора барабана 22
15. Расчет и выбор тормоза 23
16. Расчет и выбор муфт 24
17. Определение времени разгона двигателя
механизма подъема 25
18. Компоновка механизма подъема 27
Механизм передвижения тележки 28
1. Выбор колес и подтележечных путей 28
2. Определение сопротивления передвижению тележки 29
3. Выбор электродвигателя 30
4. Выбор редуктора 31
5. Выбор тормоза 33
7. Проверка двигателя на время разгона 34
8. Компоновка механизма передвижения тележки 36
9. Компоновка тележки 37
Механизм передвижения крана 38
1. Определение нагрузок на колеса и ролики механизма 38
2. Определение сопротивления передвижению крана 40
3. Выбор электродвигателя 41
4. Выбор редуктора 42
5.Выбор тормоза 44 4.6. Выбор муфты 45
7. Проверка двигателя на время разгона 46 4.8. Компоновка механизма передвижения крана 48
Расчет металлоконструкции крана 49
1. Расчет балки для подтележечного пути (тележка в конце) 49 5.2. Расчет торцевой балки 52
3. Расчет оттяжекфермы 55
4.Подбор сечения поясов фермы 55
5. Подбор сечения раскосов и стоек фермы 58
Выбор устройств безопасности 60
Техническое задание.
Спроектировать консольный передвижной кран с грузовой тележкой
Грузоподъемность Q = 125 т.
Скорость передвижения груза Vгр. = 16 ммин.
Скорость передвижения крана Vкр. = 40 ммин.
Скорость передвижения тележки Vт. = 24 ммин.
Высота подъема груза Н = 10 м.
Режим работы механизма по ГОСТ 25835-83 3М.
Общий вид крана- 1лист А1.
Барабан в сборе-1лист А1.
Тележку крана с механизмами подъема и передвижения-2 листа А2.
Рис.1.1.Кинематическая схема крана.
Расчет механизма подъема
Выбор схемы механизма подъема и выбор типа подвески.
Для расчета и выбора элементов механизма подъема составляем его кинематическую схему. Схема механизма подъема включает в себя: электродвигатель 1; зубчатую муфту 2 с тормозным шкивом; тормоз 3 редуктор 4; барабан 5; полиспаст 6 (для крана гп 125 т принимаем число ветвей на которых висит подвеска = 2) крюковую подвеску 7:
рис. 1 . Схема запасовки полиспаста.
Кратность полиспаста определяем по формуле
где z – число ветвей каната на которых висит подвеска;
zб – число ветвей каната сбегающих с барабана
2. Определение максимального усилия в канате и его выбор.
Усилие в канате набегающем на барабан
где: G — номинальная грузоподъемность; n— число полиспастов в системе mn— кратность полиспаста; о— общий КПД полиспаста и обводных блоков:
где: бл – КПД блока; t – число отклоняющих блоков в полиспасте.
Расчетное разрывное усилие в канате
где: S = Sб – максимальная нагрузка на канат идущий на барабан; k = 355 - коэффициент запаса прочности для режима работы 3М.
P≥619 · 355=2197 кН=2197 КГС
Выбираем канат двойной свивки типа ЛК-Р конструкции 8х19(1+6+ 66)+1о.с. по ГОСТ 7670—69 диаметром d = 83 мм имеющим при пределе прочности проволок В = 160 кгсмм2 расчетное разрывное усилие Р = 3270 кгс.
Выбираем канат грузовой нераскручивающийся крестовой свивки из материала высшей марки со светлой поверхностью проволоки. Условное обозначение выбранного каната:
Канат 83-Г-B-Н-160 ГОСТ 7670—69.
Фактический запас прочности каната
Выбор крюка производим по заданной грузоподъемности и режиму работы крана. По ГОСТ 6627-74 выбираем однорогий удлиненный крюк (тип А) N010 с размерами: D=55 мм; S = 40 мм; b = 34 мм; h = 52 мм; d2 = 35 мм; d1 = 30 мм; d0 = М30 мм; L=155 мм; l1 = 45 мм Размеры l и l2 определяются после расчета траверсы.
4.Расчет упорного подшипника крюка
Поскольку вращение крюка является только установочным то расчет подшипника ведется по статической грузоподъемности по формуле:
где kД=12 – динамический коэффициент;
= 12×1250×981 = 14715 Н.
Упорный подшипник выбираем согласно ГОСТ 6874-75 исходя из расчетной нагрузки и диаметра хвостовика крюка (d1) Выбираем шариковый упорный подшипник 8106: d = 30 мм D = 47 мм H = 11 мм = 33500 Н
рис..3. Подшипник упорный
Гайка крюка выполняется с уширением нижней части которая охватывает упорный подшипник Наименьший диаметр гайки определяется по формуле:
где d0 – диаметр резьбы хвостовика крюка мм;
Стопорение гайки осуществляется при помощи планки которая устанавливается в шлице на торцовой части хвостовика и крепится болтами в тело хвостовика
6.Расчет элементов подвески.
Траверса подвески работает на изгиб. Расчет траверсы ведется по двум опасным сечениям: в середине (А-А) и в месте изменения сечения (В-В).
Рис. 2.4. Схема к расчету траверсы.
Размеры типовой подвески для гп 125 т.:
b = 100 мм. - расстояние между блоками;
b1 = 70 мм. – длина средней части траверсы;
bтр = D + (10 15) = 47 + 11 = 58 мм. – ширина траверсы (D – наружный диаметр упорного подшипника);
dтр = d1 + (2 5) = 30 + 2 = 32 мм. – диаметр отверстия под хвостовик крюка.
Максимальный изгибающий момент в сечении А-А:
MA-A = 1250×981×014 =3065 Н×м;
Момент в сечении В-В равен:
MB-B = 1250×981×(01-007)4 = 9197 Н×м;
Параметры траверсы определяем проектным расчетом из условия прочности при изгибе:
где М - момент действующий в расчетном сечении Н×м;
W – момент сопротивления расчетного сечения см3;
[s] = 14×s-1(K0×[n]) – допускаемое напряжение изгиба МПа;
где K0 - коэффициент учитывающий конструкцию детали принимаем K0=25;
[n] – допускаемый коэффициент запаса прочности для лёгкого режима работы [n]=14;
s-1 – предел выносливости материала траверсы принимаем s-1=250 Мпа;
[s] = 14×250(25×14) = 100 МПа;
Момент сопротивления в сечении А-А:
= 3065100 = 306 см3;
WA-A = (bтр-dтр)×h 26 h =
WA-A =(58-3.2) h26=0.43h2
Момент сопротивления в сечении B-B:
Определяем размеры крюка:
l2 = h + H2 = 302 + 112 = 357 мм.
l = LБ –( l1- l2) = 155-45-357 = 1457 мм.
7. Расчет блоков подвески.
Диаметр блока по центру каната определяется из условия ГГТН:
где dк – диаметр каната мм;
e – коэффициент учитывающий допустимый перегиб каната для лёгкого режима работы e = 20;
D = 11 ×20 = 220 мм.
Диаметр блока по дну канавки:
Dбл =220 - 11 = 209 мм;
Затем из ряда предпочтительных чисел выбираем Dбл = 250 мм
Для диаметра каната 11 мм блок будет иметь следующие параметры:
dk = 11 мм. R = 8 мм.
B = 28 мм.B1 = 40 мм.
Рис. 2.5.Профиль канавки блока.
Блок устанавливается на двух радиальных подшипниках. Нагрузка на один подшипник при максимальном грузе:
где kД = 12 - динамический коэффициент;
kv = 135 – коэффициент вращения (при вращении наружного кольца подшипника);
nбл = 1 – число блоков в подвеске.
Однако в связи с тем что кран работает с разными грузами расчет следует вести по эквивалентной нагрузке определяемой по формуле:
где кпр = 06 – коэффициент приведения для лёгкого режима работы;
Pэкв = 06×993262 = 595957 Н.
Требуемая долговечность подшипника определяется по формуле:
где Lh =1000 ч – долговечность подшипника для лёгкого режима;
nбл – частота вращения блока мин-1.
nбл = 32(314×025) = 407 мин-1.
L = 60×407×1000106 = 24 млн. об.
Расчетная динамическая грузоподъемность подшипника:
C = 595957×(24)13 = 106829 Н.
Подшипник выбираем согласно ГОСТ 8338 - 75. Принимаем подшипник радиальный шариковый особо легкой серии 106:
B = 13 ммC = 13300 HC0 = 6800 H.
Рис. 2.6. Шарикоподшипник.
Барабан изготавливается литым из стали 25Л.
Диаметр барабана определяем по формуле:
где e – коэффициент учитывающий допустимый перегиб каната для лёгкого режима работы e =18
Диаметр барабана по дну канавки:
Dб = 198 – 11 = 187 мм;
Из ряда предпочтительных чисел выбираем Dб = 200 мм.
Размеры профиля канавок барабана по нормали МН 5365-64:
dk = 11 мм. - диаметр каната.
r = 7 мм. радиус канавок.
h = 4 мм. – высота канавок.
t = 13 мм. – шаг канавок.
Рис. 2.7. Профиль канавок барабана
Толщина стенки стального барабана предварительно принимается равной:
Принятое значение толщины стенки проверяем на сжатие по формуле:
sсж = Fmax(×t) [sсж]
[sсж] – допускаемое напряжение сжатия МПа;
где [sТ] – предел текучести для Сталь 25Л [sТ] = 240 МПа.
– коэффициент запаса прочности для стали.
[sсж] = 24015 = 160 МПа.
sсж = 619318(132×13) = 36 160 МПа.
Длина барабана при использовании одинарного полиспаста определяется по формуле:
lр – длина участка для навивки рабочей ветви каната мм:
Н – высота подъема груза.
lр = 13102(314 0.2) = 414 мм
Lб = 36+20+414+213.2 = 500 мм.
9. Расчет узла крепления каната
В механизмах подъема кранов крепление каната на барабане производится при помощи одноболтовых или двухболтовых прижимных планок. Количество планок определяется расчетом. В случае применения одноболтовых планок независимо от расчета их должно быть не менее двух. Они устанавливаются с шагом в 600.
Для уменьшения нагрузки на прижимные планки правилами предусматривается наличие запасных витков трения. С учетом влияния этих витков усилие в канате перед прижимной планкой можно определить по формуле Эйлера:
где f – коэффициент трения каната о барабан; f=01 012;
а – угол обхвата барабана витками трения; а = 3p.
Рис. 2.8. Схема крепления каната на барабане.
С учетом всех сил трения которые удерживают канат на барабане усилие в болте определяем по формуле.
f1 – коэффициент трения каната о планку; при клиновой канавке f1 = 024;
При диаметре каната 11 мм. выбираем болт М12. Проверяем его на растяжение:
где 13 – коэффициент учитывающий кручение и изгиб болта;
кз =18 – коэффициент запаса крепления;
Sб – площадь сечения болта см2;
- допускаемое напряжение растяжения. Для Ст.3 117 МПа.
Fp = 2 ×2510(1 ×(01 + 024)×(e024×2×314+1)) = 26845 Н;
sР =13 ×18 ×26845(314×36) =555 МПа 117 МПа.
Принимаем что крепление каната к барабану будет произведено двумя одноболтовыми планками.
10. Расчет вала барабана.
Соединение вала барабана с выходным валом редуктора может производиться при помощи зубчатых муфт допускающих значительную несоосность соединяемых валов. Эти муфты характеризуются высокой надежностью но имеют большие габариты. Поэтому в современных конструкциях механизмов подъема для обеспечения компактности применяется специальное зубчатое зацепление в виде зубчатого венца (конец тихоходного вала) входящего в зацепление с другим венцом укрепленным непосредственно на барабане. При таком соединении крутящий момент передается через болты соединяющие венец-ступицу с обечайкой барабана и следовательно вал барабана работает только на изгиб.
Схемы к расчету оси барабана представлены на рисунке 2.9.:
Рис. 2.9. Расчетная схема оси барабана.
Для предварительного расчета длину оси барабана принимаем:
l = LБ + (150 200) = 500 + 150 = 650 мм.
Поскольку ступицы находятся на разных расстояниях от опор то нагрузки на ступицы также будут разными. Расстояния от центров ступиц до центров подшипников l1 и l2 принимаем предварительно: l1 = 70 мм l2 = 90 мм.
Реакция Т=Fmax=619318 Н.
Расчет оси барабана сводится к определению диаметров цапф и ступицы из условия работы оси на изгиб в симметричном цикле:
где К0 - коэффициент учитывающий конструкцию детали (для валов осей и цапф К0 = 20 .. 28 (принимаем К0 = 25);
[n] – допускаемый коэффициент запаса прочности (для лёгкого режима работы [n] = 14);
-1 – предел выносливости (для Сталь 45 -1 = 260 МПа)
[-1] = 260(14×25) = 7428 МПа.
Рассмотрим 1-ю схему:
Наибольший изгибающий момент в сечении под ступицей:
Определение опорных реакций:
RA = 619318 (650-70)650 =552622 Н;
RB = 619318 (650-90)650 = 533566 Н;
Mст =5526220.07=38684 Нмм
Рассмотрим 2-ю схему:
Mст = 533566009= 4802 Нмм.
Для дальнейших расчётов используем наибольший момент.
Момент сопротивления этого сечения:
Принимаем оба диаметра под ступицы одинаковыми а расчет dст ведем по наибольшему из моментов:
dст ≥ [3238684(74.28314)]13 = 403мм
принимаем dст = 40 мм.
Наибольший момент для цапфы:
Мц = 552622 (70 – 40) = 165786 Нмм;
Диаметр цапфы из условия прочности:
dц ≥ [32165786(74.28314)]13 = 283 мм
принимаем dц = 30 мм
Диаметр правой цапфы в целях унификации подшипников принимаем равным диаметру левой цапфы
11. Расчет подшипников оси барабана.
Для компенсации несоосности опор ось барабана размещается на самоустанавливающихся сферических двухрядных шариковых или роликовых подшипниках ГОСТ 5720 – 75.
Эквивалентная нагрузка на правый подшипник равна:
Рэкв = RВ × kv × kд × kпр
где kv – коэффициент вращения при вращении внутреннего кольца kv =1;
kД – динамический коэффициент для механизмов подъема kД = 12;
kпр – коэффициент приведения для лёгкого режима работы kпр = 06.
Рэкв = 533566 ×1 ×12 ×06 = 384167 Н.
Расчетную динамическую грузоподъемность шарикового подшипника определяем по формуле
L – требуемая долговечность подшипника (определена в пункте 2.7)
C = 384167 × (183)13 = 4610 Н;
Выбираем подшипник 107:
d = 35 мм D=62 мм B=14 мм C0= 8500 H При выборе подшипника учитываем необходимый диаметр цапфы вала барабана и диаметр расточки под подшипник в полумуфте выходного вала редуктора (редуктор Ц2-200 D=62 мм).
Поскольку в левом подшипнике вращаются оба кольца то его можно рассчитывать по статической грузоподъемности:
С0 = 552622 ×06 ×12 = 397887 Н.
В целях унификации оба подшипника принимаем одинаковыми.
12. Выбор электродвигателя.
Статическая мощность при подъеме номинального груза:
Nст = Q × g × vгр(10 3×0)
где 0 – К.П.Д. механизма подъема 0 = 085.
Nст = 1250 ×981 ×(1660)(10 3×085) = 384 кВт.
Расчет двигателя ведем по эквивалентной нагрузке; потребная мощность двигателя определяется по формуле:
где kпр – коэффициент приведения для лёгкого режима работы kпр= 06.
Nэкв = 384 ×06 = 23 кВт.
По эквивалентной мощности выбираем электродвигатель с фазным ротором МTF 111-6. Параметры двигателя:
N = 2.8 кВт nдв = 920 обмин Mma
L = 586 мм h =132 мм h31 = 342 мм b31 =145 мм d1 = 35 мм.
Рис. 2.10. Двигатель MTF 111 – 6.
13. Выбор редуктора.
В пункта 2.11 определили что по конструкции валов подходит редуктор Ц2 - 200
Редуктор выбирается по статической мощности передаточному отношению частоте вращения вала двигателя и режиму работы.
Мощность редуктора определяем по формуле:
где kр – коэффициент запаса для редукторов типа Ц2 kр = 1.
Np = 3.84 ×1 = 3.84 кВт.
Передаточное отношение:
Выбираем редуктор Ц2 – 200 с передаточным числом iр = 19.83 частотота вращения быстроходного вала редуктора до n=1000 обмин мощностью на быстроходном валу до N = 10.5 кВт.
пфакт. = 92019.05 = 48.29 обмин.
Vфакт. = 48.29×314 ×(02+0011) = 31.9 ммин.
Vгр. = 31.92 = 15.9 ммин.
Nст = 1250 ×981 ×(15.960)(10 3×085) = 3.8 кВт.
Nэкв = 3.8 ×06 = 2.28 кВт. (перегруз двигателя 22%)
Np = 2.28 ×1 = 2.28 кВт.
Размеры редуктора Ц2-200:
B = 230 мм Н0 = 140 мм H = 266 мм L =434 мм L10 = 159 мм Ат = 125 мм Аб = 75 мм.
Рис.2.11. Редуктор Ц2 – 200.
Рис. 2.12. Валы редуктора Ц2 – 200.
Размеры концов валов редуктора (рис. редуктора Ц2 – 200):
B =150 мм; L2 = 160 мм; L3 = 172 мм; d2 = 62 мм; D3 = 126 мм; z = 40; m = 3 мм; d = 25 мм; d1 = 40мм; L1 = 185 мм; l1 = 45 мм.
14. Расчет узла соединения редуктора с барабаном.
Так как крутящий момент передается через призонные болты то проводится проверочный расчет болтов на срез:
= 2 × Mб(Dокр × zб ×025××d2) []
где Mб – крутящий момент на барабане Н;
Mб = Dб × Qгр(2 × а × hпл)
где а – кратность полиспаста; а = 2
hпл – КПД полиспаста; при а = 2 hпл = 099
Mб = 02 ×1250 ×981(2×2×099) = 61931Н
zб – число болтов zб = 4;
d – диаметр цилиндрической части призонного болта d = 10 мм;
Dокр – диаметр окружности установки болтов. В предварительном расчете принимаем Dокр= Dб +(d ×2) = 200+10×2 =220 мм.
[] – допускаемое напряжение среза [] 06× [р];
[] = 06 × 117 = 702 МПа.
= 2 ×619.31(022 ×4 ×025 ×314× 102) = 17.9 Мпа [] = 702 МПа.
Следовательно четырёх болтов достаточно для крепления вала редуктора с барабаном. Призонные болты выбираем по ГОСТ 7817 - 72.
15. Расчет и выбор тормоза
Тормоз устанавливается на быстроходном валу редуктора. Расчетный тормозной момент на валу равен:
Мт = kт × Q × g × Dб(2×
где kт – коэффициент запаса торможения для лёгкого режима работы kт = 15.
Мт = 15 ×1250 ×981 ×02 ×(2 ×2 ×5094) ×085 = 1534 Н×м.
по значению расчетного тормозного момента подбираем тормоз ТГТ-200 с параметрами:
диаметр тормозного шкива – 200 мм
тормозной момент – 300 Н × м.
D = 200 мм H = 436 мм h = 170 мм А = 530 мм l = 213 мм B = 100 мм.
Рис. 2.13. Тормоз ТКГ – 200.
16. Расчет и выбор муфт.
Муфта соединяющая вал электродвигателя с валом редуктора выбирается по расчетному крутящему моменту и диаметру:
где kз - коэффициент запаса;
где k1 – коэффициент учитывающий степень ответственности механизма для механизма подъема k1 = 13;
k2– коэффициент учитывающий режим работы для лёгкого режима работы k2=11;
Мм = 12509.80.21.43(2250.940.85) = 2022 Нм.
Для соединения вала двигателя и быстроходного вала редуктора применяются зубчатые муфты и промежуточный вал.
номинальный вращающий момент Мном = 250 Н×м
момент инерции муфты Jм=005 кг×м2;
Размеры зубчатой муфты:
D = 140 мм; L = 165 мм; l = 80 мм.
Рис. 2.14. Зубчатая муфта.
17. Определение времени разгона двигателя механизма подъема.
Для механизма подъема груза наибольшее время разгона получается при разгоне на подъем (2 - 5сек.).
tр.факт .- время при разгоне на подъем с
дв .- угловая скорость двигателя рад.с
дв.= 2 ·314 ·92060 = 963 радс.
Jn - момент инерции механизмов подъема кранов приведенных к валу двигателя при пуске
Jn = (11 12) · Jб + mгр.·
(11 12) – коэффициент учета инерции вращающихся масс на 2-ом 3-ем и последующих валов механизма
Jб = Jр.дв. + Jм + Jт.ш. – момент инерции соответственно ротора двигателя Jр.дв. муфты Jм тормозного шкива Jт.ш.
m т.ш. – масса тормозного шкива m т.ш = 15 кг.
- радиус тормозного шкива = 015 м.
Jт.ш = 15 · 0152 · 06 = 02 кгм2.
Jn = 11 · (0312 + 008 + 02) + 1250 · = 065 кгм2
Мп.ср. – среднепусковой момент двигателя Н·м
МН – номинальный момент двигателя;
МН = Nдв. · 9550пдв.
п.ср. – кратность среднепускового момента двигателя
п.ср. = (15 16) – для двигателя с фазным ротором.
Мп.ср. = 28 ·9550920 · 16 = 465 Н·м.
Мс - момент статического сопротивления при разгоне приведенный к валу двигателя Н·м
= 21 с. - время разгона лежит в заданных пределах (2 5 с.).
18. Компоновка механизма подъема.
Рис. 2.15. Компоновка механизма подъема.
Механизм передвижения тележки.
Крановая тележка 1 (рис. ) обычно устанавливается на четырех ходовых колесах 2 два из которых являются приводными. Вращение на колеса передается от электродвигателя 5 через редуктор 3 и трансмиссионные валы 6. Быстроходные валы электродвигателя и редуктора соединяются зубчатой муфтой 4тихоходные валы - зубчатыми муфтами 7.
Рис. 3.1. Кинематическая схема механизма передвижения тележки.
1. Выбор колес и подтележечных рельсов:
Выбор колес тележки производим по нагрузке на одно колесо:
где Gгр – вес груза кН;
Gт. – вес тележки кН
Вес тележки приблизительно определяется по формуле:
Gт. = 04 × 125 ·981 = 49 кН;
Тк. = (49 + 125 · 981)4 = 429 кН;
По справочным данным для данной нагрузки выбираем колеса диаметром Dк.=200 мм. Для передвижения тележки будем использовать двухребордные цилиндрические крановые колеса ГОСТ 3569-74 имеющие следующие параметры.
D = 200 мм D1 = 230 мм d = 50 мм d1 = 80 мм d2 = 175 мм B = 50 мм B1 = 80 мм S=18 мм.
Рис. 3.2. Ходовое колесо тележки.
По сортаменту выбираем рельс Р24 ГОСТ 6368-82 с выпуклой головкой. Параметры рельса:
A = 108 мм B= 92 мм C = 50 мм D = 105 мм R = 200 мм F=3179 см2 Z1 = 53.3 мм z2 = 54.7 мм.
Рис. 3.3. Рельс Р24.
2. Определение сопротивления передвижению тележки
Полное сопротивление передвижению тележки W (кН) в период разгона приведенное к ободу колеса определяем по формуле:
W=Wтр+Wукл+Wин+Wгиб+ Wв.
где Wтр - сопротивление создаваемое силами трения;
Wтр= (Gт + Gгр)×(2 · m + f · dц) × kдопDк;
где Gт. и Gгр – соответственно вес тележки и номинального груза;
Dк – диаметр колеса;
dц – диаметр цапфы вала колеса;
m - коэффициент трения качения колеса по рельсу для Dк. = 200 мм. m = 04.
f – приведенный коэффициент трения скольжения в подшипниках колес тележки f=0015;
kдоп – коэффициент дополнительных сопротивлений определяемый в основном трением реборд о головку рельса и трением элементов токосъемного устройства kдоп = 25;
Wтр= (49 + 1226)×(2 · 04 + 0015 · 50) × 25200 = 033 кН.
Wукл - сопротивление создаваемое уклоном пути;
Wукл= a ×(Gт. + Gгр);
где a - уклон рельсового пути для тележки a=0002;
Wукл= 0002×(49+1226) = 0034 кН;
Wин - сопротивление создаваемое инерцией вращающихся и поступательно движущихся частей крана;
где d - коэффициент учитывающий инерцию вращающихся частей механизма при скорости 1 мс. d =125;
mпост – масса тележки
a – ускорение при разгоне значения а предварительно принимаем из условия:
где [a] – допускаемое ускорение при ручной строповке и гп. 125 т. [a] = 015 мс2.
а = 015 · 1 = 015 мс2;
Wин = 125 × 05 × 015 = 009 кН.
Wгиб - сопротивление создаваемое раскачиванием груза на гибкой подвеске. Wв. - сопротивление ветра. Эти величины принимаем =0.
W = 033 + 0034 + 009 = 045 кН.
3. Выбор электродвигателя
Необходимую мощность двигателя определяем по формуле:
Nэкв = W · Vт(yп.ср. · 0)
где Vт - скорость передвижения тележки.
yп.ср. - кратность среднепускового момента двигателя по отношению к номинальному для двигателя с фазным ротором yп.ср =15.
– К.П.Д. привода 0 = 085.
Nэкв = 045 × (2460)(085 × 15) = 014 кВт.
По эквивалентной мощности выбираем двигатель МTF 011-6 с параметрами:
мощность на валу при ПВ 60% - 12 кВт;
частота вращения – 910 обмин;
максимальный момент – 39 Н×м;
момент инерции ротора – 0021 кг×м2;
L = 5155 мм h = 112 мм h31 = 302 мм b31 =133мм d1 = 28 мм.
Рис. 3.4. Электродвигатель МТF 011-6.
Nст = 045 · (2460)085 = 021 кВт.
kр – коэффициент запаса для редукторов типа ВКН для режима 3М kр = 1.
Np = 021×1 = 021 кВт.
Выбираем редуктор ВКН – 420 с параметрами: передаточным числом iр = 25 частотота вращения быстроходного вала редуктора до n = 1000 обмин мощностью на быстроходном валу до N = 44 кВт.
пфакт. = 91025 = 364 обмин.
Vфакт. = 364 ×314 ×02 = 2285 ммин.
Nст = 045 ×(228560)(085 × 15) = 013 кВт.
Размеры редуктора ВКН-420:
Рис. 3.5. Редуктор ВКН – 420.
Размеры концов валов редуктора (рис. редуктора ВКН – 420):
-быстроходный вал: d = 25 мм; d1 = 40 мм;
-тихоходный пустотелый вал: d2 = 51 мм; d3 = 65 мм; D = 42 мм; z = 18; m = 25мм; l6 = 166 мм. l7 = 37 мм.
Рис. 3.6. Валы редуктора ВКН – 420.
Согласно правилам ГГТН тормоза в механизмах передвижения можно не устанавливать в тех случаях если: кран предназначен для работы в помещении кран или тележка перемещаются на надземном рельсовом пути со скоростью не более 053мс. (318 ммин.). Скорость передвижения тележки удовлетворяет заданным условиям следовательно установка тормоза на механизме передвижения не требуется.
6. Выбор муфт (зубчатая).
Муфту соединяющую вал электродвигателя с валом редуктора выбираем по диаметрам валов двигателя и редуктора (dmaх = 28 мм):
номинальный вращающий момент Мном = 1000 Н×м
момент инерции муфты Jм = 005 кг×м2;
Размеры выбранной муфты не более:
d = d1 = 40 мм; D = 145 мм; D1 = 105 мм; D2 = 60 мм; L = 174 мм; A = 60 мм; z = 30; m = 25 мм.
Рис. 3.7. Зубчатая муфта.
7. Проверка двигателя на время разгона.
Выбранный двигатель необходимо проверить на время разгона:
tр..- время разгона с
дв.= 2 ·314 ·91060 = 953 радс.
Jмех.р. = Jпост.р. + Jр.дв. + Jм + Jт.ш. – момент инерции соответственно поступательно движущихся частей ротора двигателя. муфты тормозного шкива.
где тпост - масса поступательно движущихся частей
Jпост.р. = = 03 кгм2
Jмех.р. = 03 + 0021 + 005 = 038 кгм2.
Мп.ср. = 12 ·9550910 · 15 = 1889 Н·м.
Мст.р - момент статического сопротивления при разгоне Н·м
8. Компановка механизма передвижения тележки.
Рис. 3.8. Компановка механизма передвижения тележки.
9. Компановка тележки.
Рис. 3.9. Компановка тележки.
Механизм передвижения крана.
Рис. 4.1. Схема крана.
1.Определение нагрузок на колеса и ролики механизма передвижения крана.
Вес крана определяем по приближенной формуле:
Gкр. = 12 · 1226 = 1471 кН.
Нагрузку на ходовое колесо определяем из условия статического равновесия:
где пк - число колес пк = 2
где пр - число роликов пр = 2.
а = 025 · 5 = 125 м.
По справочным данным для данной нагрузки выбираем ролики и колеса диаметром D=200мм.
Будем использовать двухребордные цилиндрические крановые колеса ГОСТ 3569-74 имеющие следующие параметры.
D = 200 мм D1 = 230 мм d = 50 мм d1 = 80 мм d2 = 175 мм B = 50 мм B1 = 80 мм S = 18 мм.
Рис. 4.2. Ходовое колесо тележки.
По сортаменту выбираем рельс Р18 ГОСТ 6368-82 с выпуклой головкой. Параметры рельса:
A = 90 мм B = 80 мм C = 40 мм D = 11 мм F = 2288 см2.
Рис. 4.3. Рельс Р18.
2. Определение сопротивления передвижению крана..
Сопротивление передвижению крана W (кН) в период разгона приведенное к ободу колеса определяем по формуле:
W = Wтр+ Wукл+ Wин+ Wгиб+ Wв.
Wтр= (Gкр + Gгр) × (2 · m + f · dц) × kдопDк;
где Gкр. и Gгр – соответственно вес крана и номинального груза;
m - коэффициент трения качения колеса по рельсу для Dк. = 200 мм. m = 06.
f – приведенный коэффициент трения скольжения в подшипниках колес f=0015;
kдоп – коэффициент дополнительных сопротивлений определяемый в основном трением реборд о головку рельса и трением элементов токосъемного устройства kдоп = 11;
Wтр= (147 + 1226)×(2 · 06 + 0015 · 50) × 11200 = 0289 кН.
Wукл= a ×(Gкр. + Gгр);
где a - уклон рельсового пути для крана a=0001;
Wукл= 0001 ×(147 + 1226) = 002 кН;
Wин = 125 × 15 × 015 = 028 кН.
W = 0289 + 002 + 028 = 0589 кН.
3. Выбор электродвигателя.
Nэкв = W · Vкр(yп.ср. · 0)
где Vкр - скорость передвижения крана.
– К.П.Д. привода 0 = 08.
Nэкв = 0589 × (4060)(08 × 15) = 033 кВт.
По эквивалентной мощности выбираем двигатель МTF 012-6 с параметрами:
мощность на валу при ПВ 40% - 22 кВт;
частота вращения – 890 обмин;
максимальный момент – 56 Н×м;
момент инерции ротора – 0029 кг×м2;
L = 5505 мм h = 112 мм h31 = 302 мм b31 =133мм d1 = 28 мм.
Рис. 4.4. Электродвигатель МТF 011-6.
Nст = 0589 · (4060)08 = 05 кВт.
kр – коэффициент запаса для редукторов типа Ц2 для режима 3М kр = 08.
Np = 08*05 = 04 кВт.
Выбираем редуктор Ц2 – 200 с передаточным числом iр = 163 частота вращения быстроходного вала редуктора до n = 1000 обмин мощностью на быстроходном валу до N = 125 кВт.
пфакт. = 890163 = 546 обмин.
Vфакт. = 546 ×314 ×05 = 857 ммин.
Nэкв = 0589 × (85760)(08 · 15) = 07 кВт.
Np = 07 ×08 = 056 кВт.
B = 230 мм Н0 = 140 мм H = 266 мм L = 434 мм L10 = 159 мм Ат = 125 мм Аб = 75 мм.
Рис. 4.5. Редуктор Ц2 – 200.
тихоходный валбыстроходный вал
Рис. 4.6. Валы редуктора Ц2 – 200.
Размеры концов валов редуктора (рис. редуктора Ц2 – 300):
-быстроходный вал: d = 25 мм; d1 = 40 мм; l1 = 20 мм.
-Тихоходный вал: d 8 = 50 мм; d9 = 70 мм; l8 = 32 мм.
Необходимый тормозной момент определяем по формуле:
где Мин. - момент сил инерции поступательно и вращательно движущихся масс приведенный к валу двигателя.
ат - замедление при торможении
кин - коэффициент неучтеных масс кин = 11 13
Мс - момент сил сопротивления приведенный к валу двигателя.
Wст. - статическое сопротивление движению крана
Wст. = Wтр. = 289 Н.
Мт. = 136 – 208 = 1152 Н·м.
По значению расчетного тормозного момента подбираем тормоз ТКТ-200 с параметрами:
-диаметр тормозного шкива: Dт.ш. = 200 мм.
-тормозной момент Мт. = 160 Н×м.
-масса тормоза т = 35 кг.
Основные размеры тормоза ТКТ - 200:
D = 200 мм L = 660 мм l2 = 322 мм h = 170 мм H = 367 мм A = 175 мм l1 = 394 мм B = 177 мм b1 = 90 мм b2 = 90 мм.
Рис. 4.7. Тормоз ТКТ – 200.
Для соединения вала электродвигателя с валом редуктора выбираем зубчатую муфту в сборе с тормозным шкивом:
номинальный вращающий момент Мном = 2500 Н×м
d = d1 = 60 мм; D = 185 мм; D1 = 135 мм; D2 = 85 мм; L = 220 мм; B = 95 мм; Dт=200 мм;
Рис. 4.8. Зубчатая муфта в сборе с тормозным шкивом.
дв.= 2 ·314 ·89060 = 932 радс.
Jмех.р. = Jпост.р. + Jр.дв. + Jм + Jт.ш. – момент инерции соответственно поступательно движущихся частей ротора двигателя муфты тормозного шкива.
Jпост.р. = = 113 кгм2
m т.ш. – масса тормозного шкива (вместе с полумуфтой) m т.ш = 20 кг.
- радиус тормозного шкива = 01 м.
Jт.ш = 20 · 012 · 06 = 012 кгм2.
Jмех.р. = 113 + 0029 + 012 = 128 кгм2.
Мп.ср. = 22 ·9550890 · 16 = 378 Н·м.
8. Компановка механизма передвижения крана.
Рис. 4.9. Компоновка механизма передвижения крана.
Расчет металлоконструкции крана.
Металлоконструкция крана состоит из двух ездовых балок 2 соединенных на конце пролета концевой балкой 3двух вертикальных ферм 1. Расчёт металлоконструкций выполнен по методике приведённой в [Л. 4. Стр. 141]
Рис.5.1. Схема металлоконструкции крана.
1. Расчет балки для подтележечного пути (тележка находится на конце балки).
Ездовая балка рассчитывается при положении тележки на конце пролета. При этом на балку действуют: распределённая нагрузка от веса самой балки нагрузка от колёс тележки вес кабины.
Рис 5.1. Эпюра изгибающих моментов балки для подтележечных путей с тележкой находящейся в конце балки.
Распределённая нагрузка от веса балки:
где Kq – коэффициент перегрузки Kq=11;
Gб – вес балки (принимаем ориентировочно Gб=1500 Н);
Вес кабины: Gк=15000 Н;
Нагрузка от колес тележки:
P1=P2=Kq(Gm+Gгр.)z;
где z – число колес тележки; z=4;
Kq – коэффициент перегрузки Kq=11;
Gm – вес тележки Gm=4900 Н;
Gгр – вес груза Gгр=12260 Н;
P1=P2=11(4900+12260)4=4719 Н
Определяем реакции в опорах:
ΣМА=0; Gк09Р236Р15q525+RВ5=0
RВ=(Gк09+Р236+Р15+q525)5;
RВ=(1500009+471936+47195+330525)5= 1164168Н
ΣМВ=0; Р214Gк41 q525+ RА5=0
RА=(Р214+Gк41+ q525)5;
RА=(471914+1500041+ 330525)5=1444632Н
446321500047194719+11641683305=0
Строим эпюру изгибающих моментов:
х=09; Мизг.=1444632093300922=12868038Н.
х=09; Мизг.= 12868038 Н;
х=25; Мизг.=144463225330252215000(2509)=1108455 Н.
х=36; Мизг.=144463236330362215000(3609)=9368352 Н
х=36; Мизг.= 9368352 Н;
х=5; Мизг.=1444632533052215000(509) 4719(536)=0;
Благодаря этому расчету мы нашли Rmax=1444632 Н которая действует на торцевую балку если тележка находится в конце пролета.
2. Расчет торцевой балки (при нахождении тележки на конце пролета).
Торцевую балку рассчитываем при положении тележки на максимальном вылете. При этом на балку на балку действуют две нагрузки от подрельсовых балок R=1444632 Н и распределенная нагрузка от веса самой балки.
Рис 5.2. Эпюра изгибающих моментов торцевой балки.
Gб – вес балки (принимаем ориентировочно Gб=1200 Н);
ΣМА=0; R1115q47235R2355+ RB47=0
RВ=( R1115+q47235+R23.55)47
RВ=( 1444632115+28047235+14446323.55)47=1510432 Н
ΣМВ=0; R2115q47235R1355+ RА47 =0
1043214446321444632+151043228047=0
х=115; Мизг.= 151043211528011522=17184818Н.
х=115; Мизг.= 17184818Н;
Мизг.= 1510432235280235221444632(235115)= 17386418Н;
Мизг.= 1510432355280355221444632(355115)= 17184818Н.
х=355; Мизг.= 17184818Н;
Мизг=15104324728047221444632(47115)1444632(47355)=0.
Определяем осевой момент сопротивления балки:
где mo коэффициент неполноты расчетов;
где m1коэффициент учитывающий ответственность конструкции m1=09;
m2 коэффициент учитывающий отклонения в геометрических размерах конструкции m2=095; m3 коэффициент учитывающий несовершенство расчета m3=08;
Rрасчетное сопротивление материала на изгиб (R=210 МПа для стали Ст 3)
По сортаменту в качестве профиля торцевой балки выбираем швеллер № 18 у которого Wx=121 см3 m (1 метра)=163 кг из этого следует что расчетный вес балки был задан правильно.
Основные параметры двутавра: h=180 мм; В=70 мм; S=51 мм; t=87 мм.
3. Расчет оттяжек фермы.
Вес всей конструкции (включая вес кабины) принимаем равным весу крана Gкр.=147 Н распределяем этот вес по узлам конструкции. G1=G2=G3=4 кН
В узле №10 приложена реакция торцевой балки R=1510432 Н=151 кН с учетом того что тележка с грузом находится в крайнем левом положении фермы. Усилия в стержнях фермы для особой точности и быстроты расчетов определяем с помощью компьютерной программы СКАТ.
4.Подбор сечения поясов фермы.
Максимальные усилия в стержнях поясов фермы:
-Растяжение Nmax=30.3 кН
Сечение сжатого стержня подбираем из условия жесткости и проверяем на устойчивость.
Минимальный радиус инерции определяем по формуле:
где – коэффициент приведения длины стержня зависящий от условий его закрепления; для закрепления стержней ферм =1;
λ – гибкость; для сжатых поясов главных ферм λ=120.
rmin≥(1125)120=104см.
По сортаменту ГОСТ 8509-72 подбираем равнополочный уголок №4:
rm площадь поперечного сечения F=37см2.
Определяем фактическое значение гибкости:
λ факт.= (1125)(1210-2)=1042
Подобранный уголок проверяем на устойчивость:
Условие устойчивости:
где у – напряжение устойчивости.
[у] – допускаемое напряжение устойчивости;
[р] – допускаемое напряжение при растяжении;
для Ст3 СП ГОСТ 380-94 [р]=160МПа.
φ – коэффициент уменьшения допускаемых напряжений при продольном изгибе центрально сжатых стержней. Для Ст3 при λ=1167 φ=0473.
[у]=0473160=757 МПа.
NF=31.7103(3710-4)85МПа>757МПа–стержень потеряет устойчивость
Площадь сечения подбираем из условия устойчивости:
NF=31.7103(757106)4.1см2;
Подбираем уголок №5 F=4.63см2 rmin=3.77см.
Сечение растянутого стержня подбираем из условия жесткости и проверяем на прочность.
Максимальный радиус инерции
для растянутых поясов главных ферм λ=150.
rmin≥(1126)150=084см.
По сортаменту ГОСТ 8509-72 подбираем равнополочный уголок №32:
rm площадь поперечного сечения F=243см2.
NF=303103(24310-4)125МПа>160МПа–условие выполняется.
Для стержней работающих на сжатие требуется больший угол в итоге для поясов ферм берем уголок №5.
5.Подбор сечения раскосов и стоек фермы(уголок).
-Сжатие Nmax=40.3 кН
-Растяжение Nmax=151 кН
λ – гибкость; для сжатых поясов главных ферм λ=150.
rmin≥(1126)150=095см.
λ факт.= (1126)(09610-2)=149
φ – коэффициент уменьшения допускаемых напряжений при продольном изгибе центрально сжатых стержней. Для Ст3 при λ=149 φ=0324.
[у]=0324160=5184 МПа.
NF=40.3103(24310-4)165МПа≤518МПа условие выполняется
По сортаменту ГОСТ 8509-72 подбираем равнополочный уголок №25:
rm площадь поперечного сечения F=186см2.
NF=151103(18610-4)81МПа≤160 МПа–условие выполняется.
Выбор устройств безопасности.
Для ограничения высоты подъема выбираем рычажный конечный выключатель КУ 703.
Контактные системы удерживаются в замкнутом положении грузом 1 при переходе крюка за допустимый предел высоты крюковая подвеска упирается в груз 1 и приподнимает его. Контр груз немедленно размыкает контактную систему.
Для ограничения массы поднимаемого груза выбираем ограничитель грузоподъемности с восприятием натяжения грузового каната. Он ограничивает подъем когда масса поднимаемого груза на 10% превышает грузоподъемность равную 125т.
При подъеме груза превышающего грузоподъемность хвостовой конец через рычаг действует на контактную систему.
В ходе курсового проекта был спроектирован консольный передвижной кран с тележкой. Были произведён проектировочный и проверочный расчеты всех механизмов крана: подъема передвижения тележки передвижения крана. Также рассчитали металлоконструкцию крана: подтележечную балку торцевую балку ферму. Графическая часть курсового проекта содержит 4 чертежа: общий вид крана сборочный чертеж барабана механизм подъема и передвижения тележки.
Александров М.П. “Подъемно-транспортные машины”: 5-е изд.-М.: Высшая школа1979.
А. А. Вайнсон. Подъемно – транспортные машины: Учебник для вузов. – 4 – е изд. перераб. и доп. – М.: Машиностроение 1989. – 536 с.
А. В. Кузьмин Ф. Л Марон. Справочник по расчетам механизмов подъемно – транспортных машин. – 2 – е изд. перераб. и доп. – Мн.: Высш. шк. 1983. – 350 с.
Иванченко Ф.К. Расчеты грузоподъемных и транспортирующих машин. Высш. шк. 1983. – 350 с.
ПБ 10-382-00 Правила устройства и безопасной эксплуатации грузоподъемных кранов.
Руденко Н.Ф. Руденко В.Н. “Грузоподъемные машины ”:Атлас конструкций.-М.: Машиностроение1970.
Справочник конструктора-машиностроителя: Анурьев В.И. в 3 т. – 8-е изд. перераб. и доп. Под ред. И. Н. Жестковой. – М.: Машиностроение 2001.
Справочник конструктора в 2 т. - Под ред. Золин И.М. Зыбкин В.В. – Ниж.Новгород.: Внте-2 2003.
Учебно-методическое пособие Грузоподъемные машины. - Под ред. Быков П.М. Череповец.: ЧГУ 2005.
Учебно-методическое пособие №2213 Подъемно-транспортные устройства. - Череповец.: ЧГУ.
ГОСТ 6368 – 82 «Рельсы железнодорожные узкой колеи»
Г.Н. Краузе С.А. Сыцко «Редукторы» Справочное пособие. – М.: Машиностроение Ленинград 1972 г.
Кран_.dwg

ЧГУ.Д.190205.КП.000001.ВО
тип . . . . . . . . . . . . . . ТКТ-200
тип . . . . . . . . . . . . . . .ТUТ-200
передсточное число . . . . . .41
тип . . . . . . . . . . . . . . . .Ц2-300
передаточное число . . . . . . 50
Электродвигатель механизма:
Группа режима работы . . . . . . . .3М
Высота подъема груза
т . . . . . . . . .1
Техническая характеристика
тип . . . . . . . . . . . . . . .ВКН-420
передвижения тележки:
передаточное число . . . . . .19
тип . . . . . . . . . . . . . . . .Ц2-200
кВт . . . . . . . . . . 2
тип . . . . . . . . . . . . . МТF 011-6
кВт . . . . . . . . . . 1
тип . . . . . . . . . . . . . . .МТF012-6
кВт . . . . . . . . . . . 2
тип . . . . . . . . . . . . . .МТF111-6
передвижения крана . . . . . . . . 40
передвижения тележки. . . . . . . . 24
подъема груза . . . . . . . . . . . . 16
ТЛК-Р 6*19(1+6+66)+1
спец. передвиж..doc
Ограничитель движения
Электродвигатель MTF011-6
Механизм передвижения
Передвижения_.dwg
ЧГУ.Д.190205.КП.000001.ВО
тип . . . . . . . . . . . . . . ТКТ-200
тип . . . . . . . . . . . . . . .ТКГ-300
передсточное число . . . . . .41
тип . . . . . . . . . . . . . . . .Ц2-300
передаточное число . . . . . . 50
Электродвигатель механизма:
Группа режима работы . . . . . . . .5М
Высота подъема груза
т . . . . . . . . . 10
Техническая характеристика
тип . . . . . . . . . . . . . . .ВКР-420
передвижения тележки:
передаточное число . . . . . .50
тип . . . . . . . . . . . . . . . .Ц2-500
кВт . . . . . . . . . . 2
тип . . . . . . . . . . . . . МТF 112-6
кВт . . . . . . . . . . 1
тип . . . . . . . . . . . . . . .МТF011-6
кВт . . . . . . . . . . . 11
тип . . . . . . . . . . . . . .МТН312-8
передвижения крана . . . . . . . . 35
передвижения тележки. . . . . . . . 12
подъема груза . . . . . . . . . . . . 8
ТЛК-Р 6*19(1+6+66)+1
ЧГУ.Д.190205.КП.000004.ВО
Скорость подъема груза
тип. . . . . . . . . . . . . . . НТМ 312-6
кВт . . . . . . . . . . . . 11
тип . . . . . . . . . . . . . . . . . Ц2-500
передаточное число . . . . . . . 50
тип . . . . . . . . . . . . . . . . ТКГ-300
Механизм передвижения
Барабан1_.dwg

мой КУРСОВИК ГПМ.docx
Расчет механизма подъема 5
1. Выбор схемы механизма подъема и выбор типа подвески 5
2. Определение максимального усилия в канате и его выбор 5
4. Расчет упругого подшипника крюка 7
5. Расчет гайки крюка 8
6. Расчет элементов подвески 8
7. Расчет блоков подвески 10
8. Расчет барабана 12
9. Расчет узла крепления каната 14
10. Расчет вала барабана 16
11. Расчет подшипников оси барабана 18
12. Выбор электродвигателя 19
13. Выбор редуктора 20
14. Расчет узла соединения редуктора барабана 22
15. Расчет и выбор тормоза 23
16. Расчет и выбор муфт 24
17. Определение времени разгона двигателя
механизма подъема 25
18. Компоновка механизма подъема 27
Механизм передвижения тележки 28
1. Выбор колес и подтележечных путей 28
2. Определение сопротивления передвижению тележки 29
3. Выбор электродвигателя 30
4. Выбор редуктора 31
5. Выбор тормоза 33
7. Проверка двигателя на время разгона 34
8. Компоновка механизма передвижения тележки 36
9. Компоновка тележки 37
Механизм передвижения крана 38
1. Определение нагрузок на колеса и ролики механизма 38
2. Определение сопротивления передвижению крана 40
3. Выбор электродвигателя 41
4. Выбор редуктора 42
5.Выбор тормоза 44 4.6. Выбор муфты 45
7. Проверка двигателя на время разгона 46 4.8. Компоновка механизма передвижения крана 48
Расчет металлоконструкции крана 49
1. Расчет балки для подтележечного пути (тележка в конце) 49 5.2. Расчет торцевой балки 52
3. Расчет оттяжекфермы 55
4.Подбор сечения поясов фермы 55
5. Подбор сечения раскосов и стоек фермы 58
Выбор устройств безопасности 60
Техническое задание.
Спроектировать консольный передвижной кран с грузовой тележкой
Грузоподъемность Q = 125 т.
Скорость передвижения груза Vгр. = 16 ммин.
Скорость передвижения крана Vкр. = 40 ммин.
Скорость передвижения тележки Vт. = 24 ммин.
Высота подъема груза Н = 10 м.
Режим работы механизма по ГОСТ 25835-83 3М.
Общий вид крана- 1лист А1.
Барабан в сборе-1лист А1.
Тележку крана с механизмами подъема и передвижения-2 листа А2.
Рис.1.1.Кинематическая схема крана.
Расчет механизма подъема
Выбор схемы механизма подъема и выбор типа подвески.
Для расчета и выбора элементов механизма подъема составляем его кинематическую схему. Схема механизма подъема включает в себя: электродвигатель 1; зубчатую муфту 2 с тормозным шкивом; тормоз 3 редуктор 4; барабан 5; полиспаст 6 (для крана гп 125 т принимаем число ветвей на которых висит подвеска = 2) крюковую подвеску 7:
рис. 1 . Схема запасовки полиспаста.
Кратность полиспаста определяем по формуле
где z – число ветвей каната на которых висит подвеска;
zб – число ветвей каната сбегающих с барабана
2. Определение максимального усилия в канате и его выбор.
Усилие в канате набегающем на барабан
где: G — номинальная грузоподъемность; n— число полиспастов в системе mn— кратность полиспаста; о— общий КПД полиспаста и обводных блоков:
где: бл – КПД блока; t – число отклоняющих блоков в полиспасте.
Расчетное разрывное усилие в канате
где: S = Sб – максимальная нагрузка на канат идущий на барабан; k = 355 - коэффициент запаса прочности для режима работы 3М.
P≥619 · 355=2197 кН=2197 КГС
Выбираем канат двойной свивки типа ЛК-Р конструкции 8х19(1+6+ 66)+1о.с. по ГОСТ 7670—69 диаметром d = 83 мм имеющим при пределе прочности проволок В = 160 кгсмм2 расчетное разрывное усилие Р = 3270 кгс.
Выбираем канат грузовой нераскручивающийся крестовой свивки из материала высшей марки со светлой поверхностью проволоки. Условное обозначение выбранного каната:
Канат 83-Г-B-Н-160 ГОСТ 7670—69.
Фактический запас прочности каната
Выбор крюка производим по заданной грузоподъемности и режиму работы крана. По ГОСТ 6627-74 выбираем однорогий удлиненный крюк (тип А) N010 с размерами: D=55 мм; S = 40 мм; b = 34 мм; h = 52 мм; d2 = 35 мм; d1 = 30 мм; d0 = М30 мм; L=155 мм; l1 = 45 мм Размеры l и l2 определяются после расчета траверсы.
4.Расчет упорного подшипника крюка
Поскольку вращение крюка является только установочным то расчет подшипника ведется по статической грузоподъемности по формуле:
где kД=12 – динамический коэффициент;
= 12×1250×981 = 14715 Н.
Упорный подшипник выбираем согласно ГОСТ 6874-75 исходя из расчетной нагрузки и диаметра хвостовика крюка (d1) Выбираем шариковый упорный подшипник 8106: d = 30 мм D = 47 мм H = 11 мм = 33500 Н
рис..3. Подшипник упорный
Гайка крюка выполняется с уширением нижней части которая охватывает упорный подшипник Наименьший диаметр гайки определяется по формуле:
где d0 – диаметр резьбы хвостовика крюка мм;
Стопорение гайки осуществляется при помощи планки которая устанавливается в шлице на торцовой части хвостовика и крепится болтами в тело хвостовика
6.Расчет элементов подвески.
Траверса подвески работает на изгиб. Расчет траверсы ведется по двум опасным сечениям: в середине (А-А) и в месте изменения сечения (В-В).
Рис. 2.4. Схема к расчету траверсы.
Размеры типовой подвески для гп 125 т.:
b = 100 мм. - расстояние между блоками;
b1 = 70 мм. – длина средней части траверсы;
bтр = D + (10 15) = 47 + 11 = 58 мм. – ширина траверсы (D – наружный диаметр упорного подшипника);
dтр = d1 + (2 5) = 30 + 2 = 32 мм. – диаметр отверстия под хвостовик крюка.
Максимальный изгибающий момент в сечении А-А:
MA-A = 1250×981×014 =3065 Н×м;
Момент в сечении В-В равен:
MB-B = 1250×981×(01-007)4 = 9197 Н×м;
Параметры траверсы определяем проектным расчетом из условия прочности при изгибе:
где М - момент действующий в расчетном сечении Н×м;
W – момент сопротивления расчетного сечения см3;
[s] = 14×s-1(K0×[n]) – допускаемое напряжение изгиба МПа;
где K0 - коэффициент учитывающий конструкцию детали принимаем K0=25;
[n] – допускаемый коэффициент запаса прочности для лёгкого режима работы [n]=14;
s-1 – предел выносливости материала траверсы принимаем s-1=250 Мпа;
[s] = 14×250(25×14) = 100 МПа;
Момент сопротивления в сечении А-А:
= 3065100 = 306 см3;
WA-A = (bтр-dтр)×h 26 h =
WA-A =(58-3.2) h26=0.43h2
Момент сопротивления в сечении B-B:
Определяем размеры крюка:
l2 = h + H2 = 302 + 112 = 357 мм.
l = LБ –( l1- l2) = 155-45-357 = 1457 мм.
7. Расчет блоков подвески.
Диаметр блока по центру каната определяется из условия ГГТН:
где dк – диаметр каната мм;
e – коэффициент учитывающий допустимый перегиб каната для лёгкого режима работы e = 20;
D = 11 ×20 = 220 мм.
Диаметр блока по дну канавки:
Dбл =220 - 11 = 209 мм;
Затем из ряда предпочтительных чисел выбираем Dбл = 250 мм
Для диаметра каната 11 мм блок будет иметь следующие параметры:
dk = 11 мм. R = 8 мм.
B = 28 мм.B1 = 40 мм.
Рис. 2.5.Профиль канавки блока.
Блок устанавливается на двух радиальных подшипниках. Нагрузка на один подшипник при максимальном грузе:
где kД = 12 - динамический коэффициент;
kv = 135 – коэффициент вращения (при вращении наружного кольца подшипника);
nбл = 1 – число блоков в подвеске.
Однако в связи с тем что кран работает с разными грузами расчет следует вести по эквивалентной нагрузке определяемой по формуле:
где кпр = 06 – коэффициент приведения для лёгкого режима работы;
Pэкв = 06×993262 = 595957 Н.
Требуемая долговечность подшипника определяется по формуле:
где Lh =1000 ч – долговечность подшипника для лёгкого режима;
nбл – частота вращения блока мин-1.
nбл = 32(314×025) = 407 мин-1.
L = 60×407×1000106 = 24 млн. об.
Расчетная динамическая грузоподъемность подшипника:
C = 595957×(24)13 = 106829 Н.
Подшипник выбираем согласно ГОСТ 8338 - 75. Принимаем подшипник радиальный шариковый особо легкой серии 106:
B = 13 ммC = 13300 HC0 = 6800 H.
Рис. 2.6. Шарикоподшипник.
Барабан изготавливается литым из стали 25Л.
Диаметр барабана определяем по формуле:
где e – коэффициент учитывающий допустимый перегиб каната для лёгкого режима работы e =18
Диаметр барабана по дну канавки:
Dб = 198 – 11 = 187 мм;
Из ряда предпочтительных чисел выбираем Dб = 200 мм.
Размеры профиля канавок барабана по нормали МН 5365-64:
dk = 11 мм. - диаметр каната.
r = 7 мм. радиус канавок.
h = 4 мм. – высота канавок.
t = 13 мм. – шаг канавок.
Рис. 2.7. Профиль канавок барабана
Толщина стенки стального барабана предварительно принимается равной:
Принятое значение толщины стенки проверяем на сжатие по формуле:
sсж = Fmax(×t) [sсж]
[sсж] – допускаемое напряжение сжатия МПа;
где [sТ] – предел текучести для Сталь 25Л [sТ] = 240 МПа.
– коэффициент запаса прочности для стали.
[sсж] = 24015 = 160 МПа.
sсж = 619318(132×13) = 36 160 МПа.
Длина барабана при использовании одинарного полиспаста определяется по формуле:
lр – длина участка для навивки рабочей ветви каната мм:
Н – высота подъема груза.
lр = 13102(314 0.2) = 414 мм
Lб = 36+20+414+213.2 = 500 мм.
9. Расчет узла крепления каната
В механизмах подъема кранов крепление каната на барабане производится при помощи одноболтовых или двухболтовых прижимных планок. Количество планок определяется расчетом. В случае применения одноболтовых планок независимо от расчета их должно быть не менее двух. Они устанавливаются с шагом в 600.
Для уменьшения нагрузки на прижимные планки правилами предусматривается наличие запасных витков трения. С учетом влияния этих витков усилие в канате перед прижимной планкой можно определить по формуле Эйлера:
где f – коэффициент трения каната о барабан; f=01 012;
а – угол обхвата барабана витками трения; а = 3p.
Рис. 2.8. Схема крепления каната на барабане.
С учетом всех сил трения которые удерживают канат на барабане усилие в болте определяем по формуле.
f1 – коэффициент трения каната о планку; при клиновой канавке f1 = 024;
При диаметре каната 11 мм. выбираем болт М12. Проверяем его на растяжение:
где 13 – коэффициент учитывающий кручение и изгиб болта;
кз =18 – коэффициент запаса крепления;
Sб – площадь сечения болта см2;
- допускаемое напряжение растяжения. Для Ст.3 117 МПа.
Fp = 2 ×2510(1 ×(01 + 024)×(e024×2×314+1)) = 26845 Н;
sР =13 ×18 ×26845(314×36) =555 МПа 117 МПа.
Принимаем что крепление каната к барабану будет произведено двумя одноболтовыми планками.
10. Расчет вала барабана.
Соединение вала барабана с выходным валом редуктора может производиться при помощи зубчатых муфт допускающих значительную несоосность соединяемых валов. Эти муфты характеризуются высокой надежностью но имеют большие габариты. Поэтому в современных конструкциях механизмов подъема для обеспечения компактности применяется специальное зубчатое зацепление в виде зубчатого венца (конец тихоходного вала) входящего в зацепление с другим венцом укрепленным непосредственно на барабане. При таком соединении крутящий момент передается через болты соединяющие венец-ступицу с обечайкой барабана и следовательно вал барабана работает только на изгиб.
Схемы к расчету оси барабана представлены на рисунке 2.9.:
Рис. 2.9. Расчетная схема оси барабана.
Для предварительного расчета длину оси барабана принимаем:
l = LБ + (150 200) = 500 + 150 = 650 мм.
Поскольку ступицы находятся на разных расстояниях от опор то нагрузки на ступицы также будут разными. Расстояния от центров ступиц до центров подшипников l1 и l2 принимаем предварительно: l1 = 70 мм l2 = 90 мм.
Реакция Т=Fmax=619318 Н.
Расчет оси барабана сводится к определению диаметров цапф и ступицы из условия работы оси на изгиб в симметричном цикле:
где К0 - коэффициент учитывающий конструкцию детали (для валов осей и цапф К0 = 20 .. 28 (принимаем К0 = 25);
[n] – допускаемый коэффициент запаса прочности (для лёгкого режима работы [n] = 14);
-1 – предел выносливости (для Сталь 45 -1 = 260 МПа)
[-1] = 260(14×25) = 7428 МПа.
Рассмотрим 1-ю схему:
Наибольший изгибающий момент в сечении под ступицей:
Определение опорных реакций:
RA = 619318 (650-70)650 =552622 Н;
RB = 619318 (650-90)650 = 533566 Н;
Mст =5526220.07=38684 Нмм
Рассмотрим 2-ю схему:
Mст = 533566009= 4802 Нмм.
Для дальнейших расчётов используем наибольший момент.
Момент сопротивления этого сечения:
Принимаем оба диаметра под ступицы одинаковыми а расчет dст ведем по наибольшему из моментов:
dст ≥ [3238684(74.28314)]13 = 403мм
принимаем dст = 40 мм.
Наибольший момент для цапфы:
Мц = 552622 (70 – 40) = 165786 Нмм;
Диаметр цапфы из условия прочности:
dц ≥ [32165786(74.28314)]13 = 283 мм
принимаем dц = 30 мм
Диаметр правой цапфы в целях унификации подшипников принимаем равным диаметру левой цапфы
11. Расчет подшипников оси барабана.
Для компенсации несоосности опор ось барабана размещается на самоустанавливающихся сферических двухрядных шариковых или роликовых подшипниках ГОСТ 5720 – 75.
Эквивалентная нагрузка на правый подшипник равна:
Рэкв = RВ × kv × kд × kпр
где kv – коэффициент вращения при вращении внутреннего кольца kv =1;
kД – динамический коэффициент для механизмов подъема kД = 12;
kпр – коэффициент приведения для лёгкого режима работы kпр = 06.
Рэкв = 533566 ×1 ×12 ×06 = 384167 Н.
Расчетную динамическую грузоподъемность шарикового подшипника определяем по формуле
L – требуемая долговечность подшипника (определена в пункте 2.7)
C = 384167 × (183)13 = 4610 Н;
Выбираем подшипник 107:
d = 35 мм D=62 мм B=14 мм C0= 8500 H При выборе подшипника учитываем необходимый диаметр цапфы вала барабана и диаметр расточки под подшипник в полумуфте выходного вала редуктора (редуктор Ц2-200 D=62 мм).
Поскольку в левом подшипнике вращаются оба кольца то его можно рассчитывать по статической грузоподъемности:
С0 = 552622 ×06 ×12 = 397887 Н.
В целях унификации оба подшипника принимаем одинаковыми.
12. Выбор электродвигателя.
Статическая мощность при подъеме номинального груза:
Nст = Q × g × vгр(10 3×0)
где 0 – К.П.Д. механизма подъема 0 = 085.
Nст = 1250 ×981 ×(1660)(10 3×085) = 384 кВт.
Расчет двигателя ведем по эквивалентной нагрузке; потребная мощность двигателя определяется по формуле:
где kпр – коэффициент приведения для лёгкого режима работы kпр= 06.
Nэкв = 384 ×06 = 23 кВт.
По эквивалентной мощности выбираем электродвигатель с фазным ротором МTF 111-6. Параметры двигателя:
N = 2.8 кВт nдв = 920 обмин Mma
L = 586 мм h =132 мм h31 = 342 мм b31 =145 мм d1 = 35 мм.
Рис. 2.10. Двигатель MTF 111 – 6.
13. Выбор редуктора.
В пункта 2.11 определили что по конструкции валов подходит редуктор Ц2 - 200
Редуктор выбирается по статической мощности передаточному отношению частоте вращения вала двигателя и режиму работы.
Мощность редуктора определяем по формуле:
где kр – коэффициент запаса для редукторов типа Ц2 kр = 1.
Np = 3.84 ×1 = 3.84 кВт.
Передаточное отношение:
Выбираем редуктор Ц2 – 200 с передаточным числом iр = 19.83 частотота вращения быстроходного вала редуктора до n=1000 обмин мощностью на быстроходном валу до N = 10.5 кВт.
пфакт. = 92019.05 = 48.29 обмин.
Vфакт. = 48.29×314 ×(02+0011) = 31.9 ммин.
Vгр. = 31.92 = 15.9 ммин.
Nст = 1250 ×981 ×(15.960)(10 3×085) = 3.8 кВт.
Nэкв = 3.8 ×06 = 2.28 кВт. (перегруз двигателя 22%)
Np = 2.28 ×1 = 2.28 кВт.
Размеры редуктора Ц2-200:
B = 230 мм Н0 = 140 мм H = 266 мм L =434 мм L10 = 159 мм Ат = 125 мм Аб = 75 мм.
Рис.2.11. Редуктор Ц2 – 200.
Рис. 2.12. Валы редуктора Ц2 – 200.
Размеры концов валов редуктора (рис. редуктора Ц2 – 200):
B =150 мм; L2 = 160 мм; L3 = 172 мм; d2 = 62 мм; D3 = 126 мм; z = 40; m = 3 мм; d = 25 мм; d1 = 40мм; L1 = 185 мм; l1 = 45 мм.
14. Расчет узла соединения редуктора с барабаном.
Так как крутящий момент передается через призонные болты то проводится проверочный расчет болтов на срез:
= 2 × Mб(Dокр × zб ×025××d2) []
где Mб – крутящий момент на барабане Н;
Mб = Dб × Qгр(2 × а × hпл)
где а – кратность полиспаста; а = 2
hпл – КПД полиспаста; при а = 2 hпл = 099
Mб = 02 ×1250 ×981(2×2×099) = 61931Н
zб – число болтов zб = 4;
d – диаметр цилиндрической части призонного болта d = 10 мм;
Dокр – диаметр окружности установки болтов. В предварительном расчете принимаем Dокр= Dб +(d ×2) = 200+10×2 =220 мм.
[] – допускаемое напряжение среза [] 06× [р];
[] = 06 × 117 = 702 МПа.
= 2 ×619.31(022 ×4 ×025 ×314× 102) = 17.9 Мпа [] = 702 МПа.
Следовательно четырёх болтов достаточно для крепления вала редуктора с барабаном. Призонные болты выбираем по ГОСТ 7817 - 72.
15. Расчет и выбор тормоза
Тормоз устанавливается на быстроходном валу редуктора. Расчетный тормозной момент на валу равен:
Мт = kт × Q × g × Dб(2×
где kт – коэффициент запаса торможения для лёгкого режима работы kт = 15.
Мт = 15 ×1250 ×981 ×02 ×(2 ×2 ×5094) ×085 = 1534 Н×м.
по значению расчетного тормозного момента подбираем тормоз ТГТ-200 с параметрами:
диаметр тормозного шкива – 200 мм
тормозной момент – 300 Н × м.
D = 200 мм H = 436 мм h = 170 мм А = 530 мм l = 213 мм B = 100 мм.
Рис. 2.13. Тормоз ТКГ – 200.
16. Расчет и выбор муфт.
Муфта соединяющая вал электродвигателя с валом редуктора выбирается по расчетному крутящему моменту и диаметру:
где kз - коэффициент запаса;
где k1 – коэффициент учитывающий степень ответственности механизма для механизма подъема k1 = 13;
k2– коэффициент учитывающий режим работы для лёгкого режима работы k2=11;
Мм = 12509.80.21.43(2250.940.85) = 2022 Нм.
Для соединения вала двигателя и быстроходного вала редуктора применяются зубчатые муфты и промежуточный вал.
номинальный вращающий момент Мном = 250 Н×м
момент инерции муфты Jм=005 кг×м2;
Размеры зубчатой муфты:
D = 140 мм; L = 165 мм; l = 80 мм.
Рис. 2.14. Зубчатая муфта.
17. Определение времени разгона двигателя механизма подъема.
Для механизма подъема груза наибольшее время разгона получается при разгоне на подъем (2 - 5сек.).
tр.факт .- время при разгоне на подъем с
дв .- угловая скорость двигателя рад.с
дв.= 2 ·314 ·92060 = 963 радс.
Jn - момент инерции механизмов подъема кранов приведенных к валу двигателя при пуске
Jn = (11 12) · Jб + mгр.·
(11 12) – коэффициент учета инерции вращающихся масс на 2-ом 3-ем и последующих валов механизма
Jб = Jр.дв. + Jм + Jт.ш. – момент инерции соответственно ротора двигателя Jр.дв. муфты Jм тормозного шкива Jт.ш.
m т.ш. – масса тормозного шкива m т.ш = 15 кг.
- радиус тормозного шкива = 015 м.
Jт.ш = 15 · 0152 · 06 = 02 кгм2.
Jn = 11 · (0312 + 008 + 02) + 1250 · = 065 кгм2
Мп.ср. – среднепусковой момент двигателя Н·м
МН – номинальный момент двигателя;
МН = Nдв. · 9550пдв.
п.ср. – кратность среднепускового момента двигателя
п.ср. = (15 16) – для двигателя с фазным ротором.
Мп.ср. = 28 ·9550920 · 16 = 465 Н·м.
Мс - момент статического сопротивления при разгоне приведенный к валу двигателя Н·м
= 21 с. - время разгона лежит в заданных пределах (2 5 с.).
18. Компоновка механизма подъема.
Рис. 2.15. Компоновка механизма подъема.
Механизм передвижения тележки.
Крановая тележка 1 (рис. ) обычно устанавливается на четырех ходовых колесах 2 два из которых являются приводными. Вращение на колеса передается от электродвигателя 5 через редуктор 3 и трансмиссионные валы 6. Быстроходные валы электродвигателя и редуктора соединяются зубчатой муфтой 4тихоходные валы - зубчатыми муфтами 7.
Рис. 3.1. Кинематическая схема механизма передвижения тележки.
1. Выбор колес и подтележечных рельсов:
Выбор колес тележки производим по нагрузке на одно колесо:
где Gгр – вес груза кН;
Gт. – вес тележки кН
Вес тележки приблизительно определяется по формуле:
Gт. = 04 × 125 ·981 = 49 кН;
Тк. = (49 + 125 · 981)4 = 429 кН;
По справочным данным для данной нагрузки выбираем колеса диаметром Dк.=200 мм. Для передвижения тележки будем использовать двухребордные цилиндрические крановые колеса ГОСТ 3569-74 имеющие следующие параметры.
D = 200 мм D1 = 230 мм d = 50 мм d1 = 80 мм d2 = 175 мм B = 50 мм B1 = 80 мм S=18 мм.
Рис. 3.2. Ходовое колесо тележки.
По сортаменту выбираем рельс Р24 ГОСТ 6368-82 с выпуклой головкой. Параметры рельса:
A = 108 мм B= 92 мм C = 50 мм D = 105 мм R = 200 мм F=3179 см2 Z1 = 53.3 мм z2 = 54.7 мм.
Рис. 3.3. Рельс Р24.
2. Определение сопротивления передвижению тележки
Полное сопротивление передвижению тележки W (кН) в период разгона приведенное к ободу колеса определяем по формуле:
W=Wтр+Wукл+Wин+Wгиб+ Wв.
где Wтр - сопротивление создаваемое силами трения;
Wтр= (Gт + Gгр)×(2 · m + f · dц) × kдопDк;
где Gт. и Gгр – соответственно вес тележки и номинального груза;
Dк – диаметр колеса;
dц – диаметр цапфы вала колеса;
m - коэффициент трения качения колеса по рельсу для Dк. = 200 мм. m = 04.
f – приведенный коэффициент трения скольжения в подшипниках колес тележки f=0015;
kдоп – коэффициент дополнительных сопротивлений определяемый в основном трением реборд о головку рельса и трением элементов токосъемного устройства kдоп = 25;
Wтр= (49 + 1226)×(2 · 04 + 0015 · 50) × 25200 = 033 кН.
Wукл - сопротивление создаваемое уклоном пути;
Wукл= a ×(Gт. + Gгр);
где a - уклон рельсового пути для тележки a=0002;
Wукл= 0002×(49+1226) = 0034 кН;
Wин - сопротивление создаваемое инерцией вращающихся и поступательно движущихся частей крана;
где d - коэффициент учитывающий инерцию вращающихся частей механизма при скорости 1 мс. d =125;
mпост – масса тележки
a – ускорение при разгоне значения а предварительно принимаем из условия:
где [a] – допускаемое ускорение при ручной строповке и гп. 125 т. [a] = 015 мс2.
а = 015 · 1 = 015 мс2;
Wин = 125 × 05 × 015 = 009 кН.
Wгиб - сопротивление создаваемое раскачиванием груза на гибкой подвеске. Wв. - сопротивление ветра. Эти величины принимаем =0.
W = 033 + 0034 + 009 = 045 кН.
3. Выбор электродвигателя
Необходимую мощность двигателя определяем по формуле:
Nэкв = W · Vт(yп.ср. · 0)
где Vт - скорость передвижения тележки.
yп.ср. - кратность среднепускового момента двигателя по отношению к номинальному для двигателя с фазным ротором yп.ср =15.
– К.П.Д. привода 0 = 085.
Nэкв = 045 × (2460)(085 × 15) = 014 кВт.
По эквивалентной мощности выбираем двигатель МTF 011-6 с параметрами:
мощность на валу при ПВ 60% - 12 кВт;
частота вращения – 910 обмин;
максимальный момент – 39 Н×м;
момент инерции ротора – 0021 кг×м2;
L = 5155 мм h = 112 мм h31 = 302 мм b31 =133мм d1 = 28 мм.
Рис. 3.4. Электродвигатель МТF 011-6.
Nст = 045 · (2460)085 = 021 кВт.
kр – коэффициент запаса для редукторов типа ВКН для режима 3М kр = 1.
Np = 021×1 = 021 кВт.
Выбираем редуктор ВКН – 420 с параметрами: передаточным числом iр = 25 частотота вращения быстроходного вала редуктора до n = 1000 обмин мощностью на быстроходном валу до N = 44 кВт.
пфакт. = 91025 = 364 обмин.
Vфакт. = 364 ×314 ×02 = 2285 ммин.
Nст = 045 ×(228560)(085 × 15) = 013 кВт.
Размеры редуктора ВКН-420:
Рис. 3.5. Редуктор ВКН – 420.
Размеры концов валов редуктора (рис. редуктора ВКН – 420):
-быстроходный вал: d = 25 мм; d1 = 40 мм;
-тихоходный пустотелый вал: d2 = 51 мм; d3 = 65 мм; D = 42 мм; z = 18; m = 25мм; l6 = 166 мм. l7 = 37 мм.
Рис. 3.6. Валы редуктора ВКН – 420.
Согласно правилам ГГТН тормоза в механизмах передвижения можно не устанавливать в тех случаях если: кран предназначен для работы в помещении кран или тележка перемещаются на надземном рельсовом пути со скоростью не более 053мс. (318 ммин.). Скорость передвижения тележки удовлетворяет заданным условиям следовательно установка тормоза на механизме передвижения не требуется.
6. Выбор муфт (зубчатая).
Муфту соединяющую вал электродвигателя с валом редуктора выбираем по диаметрам валов двигателя и редуктора (dmaх = 28 мм):
номинальный вращающий момент Мном = 1000 Н×м
момент инерции муфты Jм = 005 кг×м2;
Размеры выбранной муфты не более:
d = d1 = 40 мм; D = 145 мм; D1 = 105 мм; D2 = 60 мм; L = 174 мм; A = 60 мм; z = 30; m = 25 мм.
Рис. 3.7. Зубчатая муфта.
7. Проверка двигателя на время разгона.
Выбранный двигатель необходимо проверить на время разгона:
tр..- время разгона с
дв.= 2 ·314 ·91060 = 953 радс.
Jмех.р. = Jпост.р. + Jр.дв. + Jм + Jт.ш. – момент инерции соответственно поступательно движущихся частей ротора двигателя. муфты тормозного шкива.
где тпост - масса поступательно движущихся частей
Jпост.р. = = 03 кгм2
Jмех.р. = 03 + 0021 + 005 = 038 кгм2.
Мп.ср. = 12 ·9550910 · 15 = 1889 Н·м.
Мст.р - момент статического сопротивления при разгоне Н·м
8. Компановка механизма передвижения тележки.
Рис. 3.8. Компановка механизма передвижения тележки.
9. Компановка тележки.
Рис. 3.9. Компановка тележки.
Механизм передвижения крана.
Рис. 4.1. Схема крана.
1.Определение нагрузок на колеса и ролики механизма передвижения крана.
Вес крана определяем по приближенной формуле:
Gкр. = 12 · 1226 = 1471 кН.
Нагрузку на ходовое колесо определяем из условия статического равновесия:
где пк - число колес пк = 2
где пр - число роликов пр = 2.
а = 025 · 5 = 125 м.
По справочным данным для данной нагрузки выбираем ролики и колеса диаметром D=200мм.
Будем использовать двухребордные цилиндрические крановые колеса ГОСТ 3569-74 имеющие следующие параметры.
D = 200 мм D1 = 230 мм d = 50 мм d1 = 80 мм d2 = 175 мм B = 50 мм B1 = 80 мм S = 18 мм.
Рис. 4.2. Ходовое колесо тележки.
По сортаменту выбираем рельс Р18 ГОСТ 6368-82 с выпуклой головкой. Параметры рельса:
A = 90 мм B = 80 мм C = 40 мм D = 11 мм F = 2288 см2.
Рис. 4.3. Рельс Р18.
2. Определение сопротивления передвижению крана..
Сопротивление передвижению крана W (кН) в период разгона приведенное к ободу колеса определяем по формуле:
W = Wтр+ Wукл+ Wин+ Wгиб+ Wв.
Wтр= (Gкр + Gгр) × (2 · m + f · dц) × kдопDк;
где Gкр. и Gгр – соответственно вес крана и номинального груза;
m - коэффициент трения качения колеса по рельсу для Dк. = 200 мм. m = 06.
f – приведенный коэффициент трения скольжения в подшипниках колес f=0015;
kдоп – коэффициент дополнительных сопротивлений определяемый в основном трением реборд о головку рельса и трением элементов токосъемного устройства kдоп = 11;
Wтр= (147 + 1226)×(2 · 06 + 0015 · 50) × 11200 = 0289 кН.
Wукл= a ×(Gкр. + Gгр);
где a - уклон рельсового пути для крана a=0001;
Wукл= 0001 ×(147 + 1226) = 002 кН;
Wин = 125 × 15 × 015 = 028 кН.
W = 0289 + 002 + 028 = 0589 кН.
3. Выбор электродвигателя.
Nэкв = W · Vкр(yп.ср. · 0)
где Vкр - скорость передвижения крана.
– К.П.Д. привода 0 = 08.
Nэкв = 0589 × (4060)(08 × 15) = 033 кВт.
По эквивалентной мощности выбираем двигатель МTF 012-6 с параметрами:
мощность на валу при ПВ 40% - 22 кВт;
частота вращения – 890 обмин;
максимальный момент – 56 Н×м;
момент инерции ротора – 0029 кг×м2;
L = 5505 мм h = 112 мм h31 = 302 мм b31 =133мм d1 = 28 мм.
Рис. 4.4. Электродвигатель МТF 011-6.
Nст = 0589 · (4060)08 = 05 кВт.
kр – коэффициент запаса для редукторов типа Ц2 для режима 3М kр = 08.
Np = 08*05 = 04 кВт.
Выбираем редуктор Ц2 – 200 с передаточным числом iр = 163 частота вращения быстроходного вала редуктора до n = 1000 обмин мощностью на быстроходном валу до N = 125 кВт.
пфакт. = 890163 = 546 обмин.
Vфакт. = 546 ×314 ×05 = 857 ммин.
Nэкв = 0589 × (85760)(08 · 15) = 07 кВт.
Np = 07 ×08 = 056 кВт.
B = 230 мм Н0 = 140 мм H = 266 мм L = 434 мм L10 = 159 мм Ат = 125 мм Аб = 75 мм.
Рис. 4.5. Редуктор Ц2 – 200.
тихоходный валбыстроходный вал
Рис. 4.6. Валы редуктора Ц2 – 200.
Размеры концов валов редуктора (рис. редуктора Ц2 – 300):
-быстроходный вал: d = 25 мм; d1 = 40 мм; l1 = 20 мм.
-Тихоходный вал: d 8 = 50 мм; d9 = 70 мм; l8 = 32 мм.
Необходимый тормозной момент определяем по формуле:
где Мин. - момент сил инерции поступательно и вращательно движущихся масс приведенный к валу двигателя.
ат - замедление при торможении
кин - коэффициент неучтеных масс кин = 11 13
Мс - момент сил сопротивления приведенный к валу двигателя.
Wст. - статическое сопротивление движению крана
Wст. = Wтр. = 289 Н.
Мт. = 136 – 208 = 1152 Н·м.
По значению расчетного тормозного момента подбираем тормоз ТКТ-200 с параметрами:
-диаметр тормозного шкива: Dт.ш. = 200 мм.
-тормозной момент Мт. = 160 Н×м.
-масса тормоза т = 35 кг.
Основные размеры тормоза ТКТ - 200:
D = 200 мм L = 660 мм l2 = 322 мм h = 170 мм H = 367 мм A = 175 мм l1 = 394 мм B = 177 мм b1 = 90 мм b2 = 90 мм.
Рис. 4.7. Тормоз ТКТ – 200.
Для соединения вала электродвигателя с валом редуктора выбираем зубчатую муфту в сборе с тормозным шкивом:
номинальный вращающий момент Мном = 2500 Н×м
d = d1 = 60 мм; D = 185 мм; D1 = 135 мм; D2 = 85 мм; L = 220 мм; B = 95 мм; Dт=200 мм;
Рис. 4.8. Зубчатая муфта в сборе с тормозным шкивом.
дв.= 2 ·314 ·89060 = 932 радс.
Jмех.р. = Jпост.р. + Jр.дв. + Jм + Jт.ш. – момент инерции соответственно поступательно движущихся частей ротора двигателя муфты тормозного шкива.
Jпост.р. = = 113 кгм2
m т.ш. – масса тормозного шкива (вместе с полумуфтой) m т.ш = 20 кг.
- радиус тормозного шкива = 01 м.
Jт.ш = 20 · 012 · 06 = 012 кгм2.
Jмех.р. = 113 + 0029 + 012 = 128 кгм2.
Мп.ср. = 22 ·9550890 · 16 = 378 Н·м.
8. Компановка механизма передвижения крана.
Рис. 4.9. Компоновка механизма передвижения крана.
Расчет металлоконструкции крана.
Металлоконструкция крана состоит из двух ездовых балок 2 соединенных на конце пролета концевой балкой 3двух вертикальных ферм 1. Расчёт металлоконструкций выполнен по методике приведённой в [Л. 4. Стр. 141]
Рис.5.1. Схема металлоконструкции крана.
1. Расчет балки для подтележечного пути (тележка находится на конце балки).
Ездовая балка рассчитывается при положении тележки на конце пролета. При этом на балку действуют: распределённая нагрузка от веса самой балки нагрузка от колёс тележки вес кабины.
Рис 5.1. Эпюра изгибающих моментов балки для подтележечных путей с тележкой находящейся в конце балки.
Распределённая нагрузка от веса балки:
где Kq – коэффициент перегрузки Kq=11;
Gб – вес балки (принимаем ориентировочно Gб=1500 Н);
Вес кабины: Gк=15000 Н;
Нагрузка от колес тележки:
P1=P2=Kq(Gm+Gгр.)z;
где z – число колес тележки; z=4;
Kq – коэффициент перегрузки Kq=11;
Gm – вес тележки Gm=4900 Н;
Gгр – вес груза Gгр=12260 Н;
P1=P2=11(4900+12260)4=4719 Н
Определяем реакции в опорах:
ΣМА=0; Gк09Р236Р15q525+RВ5=0
RВ=(Gк09+Р236+Р15+q525)5;
RВ=(1500009+471936+47195+330525)5= 1164168Н
ΣМВ=0; Р214Gк41 q525+ RА5=0
RА=(Р214+Gк41+ q525)5;
RА=(471914+1500041+ 330525)5=1444632Н
446321500047194719+11641683305=0
Строим эпюру изгибающих моментов:
х=09; Мизг.=1444632093300922=12868038Н.
х=09; Мизг.= 12868038 Н;
х=25; Мизг.=144463225330252215000(2509)=1108455 Н.
х=36; Мизг.=144463236330362215000(3609)=9368352 Н
х=36; Мизг.= 9368352 Н;
х=5; Мизг.=1444632533052215000(509) 4719(536)=0;
Благодаря этому расчету мы нашли Rmax=1444632 Н которая действует на торцевую балку если тележка находится в конце пролета.
2. Расчет торцевой балки (при нахождении тележки на конце пролета).
Торцевую балку рассчитываем при положении тележки на максимальном вылете. При этом на балку на балку действуют две нагрузки от подрельсовых балок R=1444632 Н и распределенная нагрузка от веса самой балки.
Рис 5.2. Эпюра изгибающих моментов торцевой балки.
Gб – вес балки (принимаем ориентировочно Gб=1200 Н);
ΣМА=0; R1115q47235R2355+ RB47=0
RВ=( R1115+q47235+R23.55)47
RВ=( 1444632115+28047235+14446323.55)47=1510432 Н
ΣМВ=0; R2115q47235R1355+ RА47 =0
1043214446321444632+151043228047=0
х=115; Мизг.= 151043211528011522=17184818Н.
х=115; Мизг.= 17184818Н;
Мизг.= 1510432235280235221444632(235115)= 17386418Н;
Мизг.= 1510432355280355221444632(355115)= 17184818Н.
х=355; Мизг.= 17184818Н;
Мизг=15104324728047221444632(47115)1444632(47355)=0.
Определяем осевой момент сопротивления балки:
где mo коэффициент неполноты расчетов;
где m1коэффициент учитывающий ответственность конструкции m1=09;
m2 коэффициент учитывающий отклонения в геометрических размерах конструкции m2=095; m3 коэффициент учитывающий несовершенство расчета m3=08;
Rрасчетное сопротивление материала на изгиб (R=210 МПа для стали Ст 3)
По сортаменту в качестве профиля торцевой балки выбираем швеллер № 18 у которого Wx=121 см3 m (1 метра)=163 кг из этого следует что расчетный вес балки был задан правильно.
Основные параметры двутавра: h=180 мм; В=70 мм; S=51 мм; t=87 мм.
3. Расчет оттяжек фермы.
Вес всей конструкции (включая вес кабины) принимаем равным весу крана Gкр.=147 Н распределяем этот вес по узлам конструкции. G1=G2=G3=4 кН
В узле №10 приложена реакция торцевой балки R=1510432 Н=151 кН с учетом того что тележка с грузом находится в крайнем левом положении фермы. Усилия в стержнях фермы для особой точности и быстроты расчетов определяем с помощью компьютерной программы СКАТ.
4.Подбор сечения поясов фермы.
Максимальные усилия в стержнях поясов фермы:
-Растяжение Nmax=30.3 кН
Сечение сжатого стержня подбираем из условия жесткости и проверяем на устойчивость.
Минимальный радиус инерции определяем по формуле:
где – коэффициент приведения длины стержня зависящий от условий его закрепления; для закрепления стержней ферм =1;
λ – гибкость; для сжатых поясов главных ферм λ=120.
rmin≥(1125)120=104см.
По сортаменту ГОСТ 8509-72 подбираем равнополочный уголок №4:
rm площадь поперечного сечения F=37см2.
Определяем фактическое значение гибкости:
λ факт.= (1125)(1210-2)=1042
Подобранный уголок проверяем на устойчивость:
Условие устойчивости:
где у – напряжение устойчивости.
[у] – допускаемое напряжение устойчивости;
[р] – допускаемое напряжение при растяжении;
для Ст3 СП ГОСТ 380-94 [р]=160МПа.
φ – коэффициент уменьшения допускаемых напряжений при продольном изгибе центрально сжатых стержней. Для Ст3 при λ=1167 φ=0473.
[у]=0473160=757 МПа.
NF=31.7103(3710-4)85МПа>757МПа–стержень потеряет устойчивость
Площадь сечения подбираем из условия устойчивости:
NF=31.7103(757106)4.1см2;
Подбираем уголок №5 F=4.63см2 rmin=3.77см.
Сечение растянутого стержня подбираем из условия жесткости и проверяем на прочность.
Максимальный радиус инерции
для растянутых поясов главных ферм λ=150.
rmin≥(1126)150=084см.
По сортаменту ГОСТ 8509-72 подбираем равнополочный уголок №32:
rm площадь поперечного сечения F=243см2.
NF=303103(24310-4)125МПа>160МПа–условие выполняется.
Для стержней работающих на сжатие требуется больший угол в итоге для поясов ферм берем уголок №5.
5.Подбор сечения раскосов и стоек фермы(уголок).
-Сжатие Nmax=40.3 кН
-Растяжение Nmax=151 кН
λ – гибкость; для сжатых поясов главных ферм λ=150.
rmin≥(1126)150=095см.
λ факт.= (1126)(09610-2)=149
φ – коэффициент уменьшения допускаемых напряжений при продольном изгибе центрально сжатых стержней. Для Ст3 при λ=149 φ=0324.
[у]=0324160=5184 МПа.
NF=40.3103(24310-4)165МПа≤518МПа условие выполняется
По сортаменту ГОСТ 8509-72 подбираем равнополочный уголок №25:
rm площадь поперечного сечения F=186см2.
NF=151103(18610-4)81МПа≤160 МПа–условие выполняется.
Выбор устройств безопасности.
Для ограничения высоты подъема выбираем рычажный конечный выключатель КУ 703.
Контактные системы удерживаются в замкнутом положении грузом 1 при переходе крюка за допустимый предел высоты крюковая подвеска упирается в груз 1 и приподнимает его. Контр груз немедленно размыкает контактную систему.
Для ограничения массы поднимаемого груза выбираем ограничитель грузоподъемности с восприятием натяжения грузового каната. Он ограничивает подъем когда масса поднимаемого груза на 10% превышает грузоподъемность равную 125т.
При подъеме груза превышающего грузоподъемность хвостовой конец через рычаг действует на контактную систему.
В ходе курсового проекта был спроектирован консольный передвижной кран с тележкой. Были произведён проектировочный и проверочный расчеты всех механизмов крана: подъема передвижения тележки передвижения крана. Также рассчитали металлоконструкцию крана: подтележечную балку торцевую балку ферму. Графическая часть курсового проекта содержит 4 чертежа: общий вид крана сборочный чертеж барабана механизм подъема и передвижения тележки.
Александров М.П. “Подъемно-транспортные машины”: 5-е изд.-М.: Высшая школа1979.
А. А. Вайнсон. Подъемно – транспортные машины: Учебник для вузов. – 4 – е изд. перераб. и доп. – М.: Машиностроение 1989. – 536 с.
А. В. Кузьмин Ф. Л Марон. Справочник по расчетам механизмов подъемно – транспортных машин. – 2 – е изд. перераб. и доп. – Мн.: Высш. шк. 1983. – 350 с.
Иванченко Ф.К. Расчеты грузоподъемных и транспортирующих машин. Высш. шк. 1983. – 350 с.
ПБ 10-382-00 Правила устройства и безопасной эксплуатации грузоподъемных кранов.
Руденко Н.Ф. Руденко В.Н. “Грузоподъемные машины ”:Атлас конструкций.-М.: Машиностроение1970.
Справочник конструктора-машиностроителя: Анурьев В.И. в 3 т. – 8-е изд. перераб. и доп. Под ред. И. Н. Жестковой. – М.: Машиностроение 2001.
Справочник конструктора в 2 т. - Под ред. Золин И.М. Зыбкин В.В. – Ниж.Новгород.: Внте-2 2003.
Учебно-методическое пособие Грузоподъемные машины. - Под ред. Быков П.М. Череповец.: ЧГУ 2005.
Учебно-методическое пособие №2213 Подъемно-транспортные устройства. - Череповец.: ЧГУ.
ГОСТ 6368 – 82 «Рельсы железнодорожные узкой колеи»
Г.Н. Краузе С.А. Сыцко «Редукторы» Справочное пособие. – М.: Машиностроение Ленинград 1972 г.
Спец. крана.docx
Привод передвижения крана
Привод передвижения тележки
Привод подъема подвески
Консольно-передвижной кран
Спец. к м. подъема.doc
Ограничитель подъема
Электродвигатель МТF 111-6
ЧГУ.Д.190205.КП.000002. ВО