Изготовление втулки направляющей




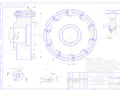
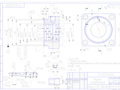
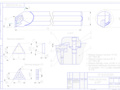
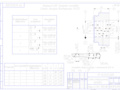
- Добавлен: 25.10.2022
- Размер: 2 MB
- Закачек: 0
Описание
Состав проекта
![]() |
![]() |
![]() |
![]() ![]() ![]() ![]() |
![]() ![]() ![]() ![]() |
![]() ![]() ![]() ![]() |
![]() ![]() ![]() ![]() |
![]() |
![]() ![]() ![]() ![]() |
![]() |
![]() ![]() ![]() ![]() |
![]() ![]() ![]() ![]() |
![]() ![]() ![]() ![]() |
![]() ![]() ![]() ![]() |
![]() |
![]() ![]() ![]() ![]() |
![]() ![]() ![]() ![]() |
![]() ![]() ![]() ![]() |
![]() |
![]() ![]() ![]() ![]() |
![]() ![]() ![]() ![]() |
![]() ![]() ![]() ![]() |
![]() ![]() ![]() ![]() |
![]() |
![]() ![]() ![]() ![]() |
![]() ![]() ![]() ![]() |
![]() ![]() ![]() ![]() |
![]() ![]() ![]() ![]() |
![]() |
![]() ![]() |
![]() ![]() |
![]() ![]() |
![]() ![]() |
![]() |
![]() ![]() |
![]() |
![]() ![]() |
![]() ![]() |
![]() ![]() |
![]() ![]() |
![]() |
![]() ![]() |
![]() ![]() |
![]() ![]() |
![]() ![]() |
![]() ![]() ![]() ![]() |
![]() ![]() ![]() ![]() |
![]() ![]() |
![]() ![]() |
![]() ![]() |
![]() ![]() |
![]() ![]() ![]() ![]() |
![]() ![]() |
![]() ![]() |
![]() ![]() |
![]() ![]() |
![]() ![]() |
![]() ![]() |
![]() ![]() |
![]() ![]() |
![]() ![]() |
![]() ![]() |
![]() ![]() ![]() ![]() |
![]() ![]() |
![]() ![]() ![]() ![]() |
![]() ![]() ![]() ![]() |
![]() ![]() |
![]() ![]() |
![]() ![]() |
![]() ![]() ![]() ![]() |
![]() ![]() ![]() ![]() |
![]() ![]() |
![]() ![]() ![]() ![]() |
![]() ![]() |
![]() ![]() |
![]() ![]() ![]() ![]() |
![]() ![]() |
![]() ![]() |
![]() |
![]() ![]() |
![]() ![]() |
![]() ![]() |
![]() |
![]() ![]() |
![]() ![]() |
![]() ![]() |
![]() ![]() |
![]() |
![]() ![]() |
![]() ![]() |
![]() ![]() |
![]() ![]() |
![]() ![]() ![]() |
Дополнительная информация
040 Cверлильная(отв с резьбой).dwg

Операция 040 Сверлильная.
Станок радиально-сверлильный 2М55
025 Токарная.dwg

Операция 025 Токарная чистовая.
Станок токарно-винторезный 16Л20
035 Cверлильная (6мм).dwg

Сверло спиральное с цилиндрическим
Операция 040 Сверлильная.
Станок вертикально-сверлильный 2М55
030 Токарная.dwg

Операция 030 Токарная чистовая.
Станок токарно-винторезный 16Л20
Установить деталь в патрон с точностью до 0
Кондуктор.dwg

020 Фрезерная.dwg

Операция 020 Фрезерная
Станок Горизонтально-фрезерный 6Р81
005 Сверлильная.dwg

Операция 005 Сверлильная
Станок Радиально-сверлильный 2М55
015 Фрезерная.dwg

Операция 015 Фрезерная
Станок Горизонтально-фрезерный 6Р81
010 Токарная.dwg

Спецификация фреза.dwg

Спецификация Кондуктор.dwg

Спецификация резец.dwg

3 Резец.dwg

Материал опорной пластины ВК-15
Материал державки сталь 45Х
Неуказанные предельные отклонения линей-
ных размеров +-IT142 угловых размеров
Пластинка режущая (2:1)
Пластинка опорная(2:1)
1 Деталь.dwg

*Размеры для справок.
Радиальное биение поверхности
f9 относительно поверхности
4 Фреза.dwg

Размеры для справок.
Поворот или замена пластинок может
производиться без съема фрезы со станка.
Допускается комплектация пластинок с откло-
нением по гобаритному размеру до0.1мм.
Маркировать:Т5К10;товарный знак предприятия-
изготовителя; количество зубьев.
2 Заготовка.dwg

Штамповочные уклоны - не более 10
Неуказанные радиусы R=4 мм
Смещение по плоскости разъема штампа до 0
Коробление не более 0
Остаток от облоя по периметру среза не более 1
Зачистка местных дефектов на глубину не более
% припуска на механическую обработку
Калибр-пробка.dwg

Калибр-скоба.dwg

050 Внутришлифовальная.dwg

Операция 050 Внутришлифовальная.
Станок внутришлифовальный 3К227А
045 Сверлильная.dwg

Операция 045 Сверлильная.
Станок радиально-сверлильный 2М55
Сверло твердосплавное
с механическим креплением
пластин из твердого сплава
Эскиз 015.dwg

Эскиз 050.dwg

Эскиз 030.dwg

Эскиз 020.dwg

Эскиз 040.dwg

Эскиз 045.dwg

Эскиз 035.dwg

Эскиз 010.dwg

Эскиз 025.dwg

Эскиз 005.dwg

Записка Мартынов.DOC
Расчетно-пояснительная записка к
курсовому проекту по
Технологии подъемно-транспортного машиностроения
«Изготовление втулки направляющей».
Руководил: СибилевН.П.
Технологическая часть:3
Назначение детали в узле.3
Определение годового объема выпуска3
и типа производства.3
Анализ технологичности конструкции детали.4
Выбор и обоснование способа получения заготовки.5
Выбор технологических баз.5
Разработка маршрута обработки заготовки.6
Расчет операционных припусков.7
Расчет режимов резания.8
Расчет мерительного инструмента.13
Расчет исполнительных размеров калибр-пробки.13
Расчет исполнительных размеров калибров-скоб.14
Конструкторская часть15
Расчет приспособления:16
Инновационный раздел17
Список литературы:30
Технологическая часть:
Назначение детали в узле.
Втулка направляющая является элементом гидравлических цилиндров. Она устанавливается в корпус цилиндра с одной стороны а с другой - вставляется аналогичная ( также может быть и глухая) втулка. Вся конструкция стягивается 4-мя болтами (шпильками). Перед сборкой в канавки втулки устанавливаются уплотнения грязесъемник направляющие кольца. Через центральное отверстие втулки проходит шток поршня гидроцилиндра.
Деталь работает в условиях высокого давления в контакте с маслом. Герметичность системы обеспечивают уплотнения. Поэтому их посадочным местам уделяется повышенное внимание – биение внутренних поверхностей канавок под уплотнения и направляющие кольца не больше 002мм.
Конструктивной особенностью данной детали является наличие канала для подачи масла в рабочую полость гидроцилиндра и резьбового отверстия для крепления штуцера.
Определение годового объема выпуска
и типа производства.
В случае если годовой объем выпуска деталей не указан в задании на курсовой проект (в моем случае) то он может быть определен по формуле:
где: m – количество одноименных деталей в цилиндре (1 шт);
M – годовой объем выпуска машин (36000 шт) ;
γ – 5 10 количество запасных частей в процентах;
– 2 6 процент брака и технологических потерь включая детали используемые для настройки станка в процентах.
Тип производства определяется по годовому объему выпуска и массе детали по табл. 1
Вес детали 259 кг следовательно при годовом объёме выпуска больше 75000 деталей тип производства будет являться массовым.
Массовое производство характеризуется узкой номенклатурой и большим объёмом выпуска изделий непрерывно изготовляемых в течение продолжительного периода времени. При массовом производстве технологические процессы разрабатываются подробно и хорошо оснащаются что позволяет обеспечить высокую точность и взаимозаменяемость деталей малую трудоёмкость а следовательно и более низкую чем при серийном производстве себестоимость изделий.
При массовом производстве возможно более широко применять механизацию и автоматизацию производственных процессов быстродействующие специальные приспособления режущий и мерительный инструмент.
Анализ технологичности конструкции детали.
Деталь должна изготавливаться с минимальными трудовыми и материальными затратами. Эти затраты можно сократить в значительной степени от правильного выбора варианта технологического процесса и его оснащения механизации и автоматизации применения оптимальных режимов обработки.
При оценке технологичности учитываются следующие характеристики:
– Конструкция детали должна состоять из стандартных и унифицированных конструктивных элементов или быть стандартной в целом. Втулка направляющая состоит из простых геометрических фигур – цилиндров и параллелепипедов. Сложных фасонных поверхностей или поверхностей получение которых не представляется возможным при современных методах обработки нет. Все элементы (канавки фаски) стандартизованы.
– Физико-химические свойства и механические свойства материала жёсткость детали её форма и размер должны соответствовать требованиям технологии изготовления. Свойства материала (Сталь 45 ГОСТ 1050-88) и геометрические параметры позволяют обрабатывать деталь без на имеющемся оборудовании с применением стандартных инструментов.
– Рациональность выбора заготовки. В крупносерийном и массовом производстве выгодно применять заготовки приближенные по размерам и форме к размерам и форме детали. Полученные штамповкой заготовки удовлетворяют этому условию.
– Технологичность отдельных элементов. Все элементы детали (фаски канавки отверстия резьба) выполняются с применением стандартного инструмента и не требуют изготовления специального.
– Точность и шероховатость поверхностей;
– Обрабатываемость материала резанием;
Технологичность детали характеризуется коэффициентом использования материала:
где Q1 – масса детали (259 кг);
Q2 – масса заготовки (311) (Рассчитано с применением системы трдотельного моделирования Solid Works)
Т.к. то можно сделать вывод что материал расходуется рационально (малое количество металла уходит в стружку).
Выбор и обоснование способа получения заготовки.
Рассматривая наиболее распространённые варианты получения заготовки я пришёл к выводу что для моего задания наиболее подходит заготовка полученная штамповкой в закрытом штампе на кривошипном горячештамповочном прессе. Т.к. втулка не имеет значительных перепадов диаметров ступеней это приведет к экономии расхода металла при механической обработке а соответственно к понижению себестоимости.
Выбор технологических баз.
Технологической называют базу используемую для определения положения заготовки или изделия при его изготовлении или сборке.
Выбор технологических баз является одной из сложных задач проектирования технологического процесса. От правильного выбора технологических баз в значительной мере зависят:
Точность получения заданных размеров;
Правильность взаимного расположения поверхностей;
Степень сложности технологической оснастки режущего и измерительного инструментов.
Операция 005 Сверлильная:
Технологическая база – необработанные торцы.
Операция 010 Токарная (черновая):
Операция 015 Фрезерная:
Технологическая база – обработанная поверхность 48 мм.
Операция 020 Фрезерная:
Технологическая база - обработанная поверхность 48 мм
Операция 025 Токарная (чистовая):
Технологическая база – обработанные торцы 108 мм
Операция 030 Токарная (чистовая):
Технологическая база – обработанные торцы 108 мм торец
Операция 035 Сверлильная:
Технологическая база – обработанные торцы 108мм.
Операция 040 Сверлильная:
Технологическая база – обработанные торцы 108 мм.
Операция 045 Сверлильная:
Технологическая база – обработанный торец 90 мм
обработанная поверхность 504 мм.
Операция 050 Шлифовальная:
Разработка маршрута обработки заготовки.
Операция 000 Заготовительная:
Заготовку получаем штамповкой в кривошипном
горячештамповочном прессе.
Просверлить отверстие 10 и рассверлить его до 35.
Точить поверхность 45 мм.
Фрезероватьать торцы в размер 108 мм.
Фрезеровать фаски 5х45
Расточить отверстие 504 мм подрезать торец 90 проточить
поверхность 90 на 16 мм расточить поверхность 82 мм
проточить конус 90 прорезать канавку 853.
Подрезать торец 108 мм прорезать канавки 586 мм 60 мм и
Сверлить отверстие 6 мм.
Сверлить коническое отверстие зенковать нарезать резьбу 38”.
Сверление 4-х отверстий 13 мм и рассверливание их до 20 на
Шлифование поверхности 505.
Расчет операционных припусков.
В подъемно – транспортном машиностроении используют два метода определения припусков на обработку: опытно–статистический и расчетно–аналитический.
Расчетно–аналитический метод.
Рассчитать поверхность .
Технологические переходы при обработке
Значения элементов припуска мкм
Расчетный миним. припуск 2z(min) мкм
Предельные значения припусков мкм
Предельные размеры мкм
Исходные данные заготовки
Δ2к = Δк = 02 130 = 26 мкм [ист. 1 стр.177]
где Dк – кривизна профиля отливки (мкм на 1 мм);
Rz – параметр шероховатости [ ист.1 стр.180-181 188 (табл.25)]
h– параметр изменения физико – механических свойств поверхностного слоя от температуры резания [ист.1 стр.180-181 188(табл.25)]
D - погрешность формы заготовки. [ ист.1 стр.180(табл.4) ист.2 стр.61]
e - погрешность закрепления [ист.1 стр.41-43(табл.12-14)]
Определение максимальных и минимальных припусков:
Определяется значение припуска на шлифование.
Минимальное значение припуска
Максимальное значение припуска
Определим значения припусков на чистовое точение.
Минимальное значение припуска
Определим значения припусков на получерновое точение.
Определим минимальные и максимальные размеры отверстия по каждому переходу.
При чистовом точении
d2min= d3min+2z3max=89920+01=90020 мм
d2max= d3max+2z3max=89950+0415=90365 мм
При черновом точении
d1min= d2min+2z2max=90020+0947=90967 мм
d1max= d2max+2z2max=90365+1430=91795 мм
d0min= d1min+2z1max=90967+18=92967 мм
d0max= d1max+2z1max=91795+243=94225 мм
На основании полученных данных составляем таблицу.
На все остальные поверхности получаем припуски опытно – статистическим методом.
Расчет режимов резания.
Операция 005 Сверлильная (Рассверлив отв ø10 до ø25мм)
V – скорость резания
С – эмпирический коэффициент
qym – показатели степеней
Принимаем n=550 обмин
Выбираем станок радиально сверлильный 2М55
Операция 010 Токарная черновая (поверхность 48мм)
Т=90 мин – Стойкость инструмента
Силовые параметры [2.c271]
Выбираем станок 16К20
Операция 015 Фрезерная (Торцы)
q xyupm – показатели степеней
принимаем n=500 обмин
но т.к. фрез установлено две примем в два раза большую мощность
Выбираем станок Горизонтально-фрезерный 6Р81
Операция 025 Токарная (поверхность 90мм)
Выбираем станок 16Л20
Операция 040 (Коническое отверстие)
Операция 050 Шлифовальная
Vk = 30 мс [ист.3 с.301]
Где эмпирические коэффициенты: [ист.3 с.303]
принимаем n = 200 обмин
Выбираем станок внутришлифовальный 3К227А
Расчет мерительного инструмента.
Расчет исполнительных размеров калибр-пробки.
а) Исполнительные размеры проходных калибров-пробок ПРп
ПРп = Dmin + 0 + Hk2
– отклонение средины поля допуска на изготовление проходного калибра для отверстия относительно предельного размера изделия мкм;
Hk – допуск на изготовление калибров мкм
ПРп = 505 + 0004 + 00052 = 505065 мм
б) Исполнительные размеры непроходных калибров-пробок НЕп
НЕп = 5053+00052=505325 мм
в) Предельный размер изношенного калибра ПРи
где - yв – допустимый выход размера изношенного проходного калибра для отверстия за границу поля допуска изделия мкм;
ПРи = 505 - 0003 = 50497 мм
Расчет исполнительных размеров калибров-скоб.
а) Исполнительные размеры проходных калибров-скоб ПРп
ПРс = Dmax - в - Hk12
где в – отклонение средины поля допуска на изготовление проходного калибра для вала относительно предельного размера изделия мкм;
Hk1 – допуск на изготовление калибров для вала мкм
ПРc = 89050 - 00005 - 00062 = 89042 мм
б) Исполнительные размеры непроходных калибров-скоб НЕс
НЕc = 89020 - 00062=42 мм
ПРи.c. = Dmax + yв1
где - yв – допустимый выход размера изношенного проходного калибра для вала за границу поля допуска изделия мкм;
ПРи.c. = 89050 + 0004 = 89054 мм
Конструкторская часть
Проектирование станочного приспособления
Рис.1. Кондуктор с дополнительной плитой
Для выполнения этого пункта курсового проекта я выбрал такой тип приспособления как кондуктор с дополнительной плитой и с пневматическим приводом (сверлильная операция).
На рисунке 1 изображена схема установки. Заготовка устанавливается центральным отверстием на выступ основной кондукторной плиты а от вращения фиксируется боковыми выступами. Далее включается пневмопривод и основная кондукторная плита через балансир и болты прижимается к станине прижимая тем самым и заготовку. В основной кондукторной плите установлены кондукторные втулки 20 мм. Так как на данной операции сверлятся отверстия двух разных диаметров (13 20) то помимо основной кондукторной плиты применена дополнительная со втулками 13 мм. Она выполнена съемной (с рукояткой). Её втулки вставляются во втулки основной плиты и с ее помощью сверлятся отверстия 13 мм. После плита снимается и через втулки основной плиты рассверливаются отверстия 20.
Расчет приспособления:
Расчет сил зажатия заготовки пневмоприводом (рис. 1.). [ист.2 с.114]
Пневматические силовые приводы широко применяются в приспособлениях разнообразных типов. Быстрота легкость постоянство силы зажима возможность её регулирования и контроля а также дистанционное управление зажимами являются основными преимуществами пневмоприводов для зажима обрабатываемых заготовок. Пневматические приводы широко применяются в крупносерийном и массовом производстве.
Для обеспечения надёжности зажима заготовки определим коэффициент запаса
где: K0 = 1.5 – коэффициент гарантированного запаса;
K1=1.0 1.2 – коэффициент учитывающий увеличение сил резания вследствие случайных неровностей на обрабатываемых поверхностях; K2=1.0 1.15 – коэффициент учитывающий увеличение сил резания в результате затупления режущего инструмента;
K3=1.2 – коэффициент учитывающий увеличение сил резания при прерывистом резании;
K4=1.0 1.3 – коэффициент учитывающий постоянство сил закрепления; K5=1.0 1.2 – коэффициент учитывающий эргономику ручных зажимных устройств (т. е. удобство закрепления).
Определим необходимую силу зажима для исключения проворота заготовки под действием момента от сверления
Определим необходимую силу зажима для обрабатываемой заготовки
Определим расчётный диаметр пневмоцилиндра
Выбираем стандартный диаметр пневмоцилиндра
Определим действительную силу зажима пневмоцилиндра
Определим время срабатывания пневмопривода
где - длина хода поршня =30 мм.
- диаметр воздуховода =6мм.
- скорость перемещения воздуха =180 (мс)
Общее время срабатывания пневмоцилиндра показывает производительность данного зажимного устройства. Ход поршня устанавливают в зависимости от конструктивных особенностей станочного приспособления обрабатываемой детали и технологического оборудования.
Инновационный раздел
Применение комбинированного инструмента.
Наиболее эффективный путь повышения производительности в автоматизированном производстве – это концентрация операций или переходов. Однако при высокой степени концентраций операций повышается сложность оборудования снижается его надежность а следовательно увеличиваются простои и растет себестоимость продукции. Концентрация переходов увеличивает сложность инструмента а оборудование упрощается. При этом увеличивается число отказов связанных с инструментом (поломки) а время на наладку инструмента сокращается.
Совместимость операций или переходов зависит от требуемой точности обработки и шероховатости поверхности. Принятый порядок выполнения операций и переходов определяет тип инструмента необходимый для их реализации.
Максимальная эффективность концентрации операций или переходов достигается за счет применения комбинированных инструментов.
Применение комбинированных инструментов обеспечивает следующие преимущества:
сокращается основное технологическое время а также вспомогательное время связанное с подводом и отводом инструмента время затрачиваемое на его смену и наладку а следовательно повышается как технологическая так и цикловая производительность;
уменьшается количество технологического оборудования благодаря чему уменьшается расход электроэнергии сокращаются производственные площади уменьшается количество основных и вспомогательных рабочих повышается надежность работы автоматических линий а следовательно снижается себестоимость продукции;
повышается соосность и точность расположения обрабатываемых поверхностей.
Комбинированные инструменты обладают рядом существенных недостатков: высокая степень концентрации режущих кромок у комбинированного инструмента обеспечивает срезание большой массы металла. А это в свою очередь увеличивает концентрацию сил и температуры резания на одном корпусе инструмента что ухудшает условия его работы. Рост сил приводит к увеличению шероховатости поверхности а иногда и к поломке инструмента. Рост температуры увеличивает износ инструмента.
Учитывая что концентрация режущих кромок также увеличивает температуру резания период стойкости комбинированного инструмента может быть значительно меньше чем у одномерных инструментов.
Необходимо отметить что недостатки присущие комбинированному инструменту в значительной степени присущи и одномерным инструментам. Учитывая многопараметрический характер воздействий рабочих процессов на комбинированный инструмент недостатки присущие одномерным инструментам при работе комбинированным инструментом проявляются еще в большей степени.
Тема работы является актуальной так как направлена на повышение производительности токарных станков за счет комбинированного инструмента которые ограниченно применяются на данном виде оборудования.
Существующие конструкции комбинированных инструментов можно классифицировать согласно представленной структурной схемы на рисунке 1
Согласно приведенной схемы комбинированный инструмент разделяется по типу на однотипный и разнотипный.
Рисунок 1 – Схема классификации комбинированных инструментов
Однотипные инструменты (рисунки 2 – 7) применяются при обработке поверхностей различных диаметров расположенных последовательно на одной оси. В некоторых случаях однотипные инструменты могут применяться для последовательной обработки поверхностей одного диаметра например черновое и чистовое развертывание отверстий нарезание и калибрование резьбы.
Рисунок 2 – Сверло двухступенчатое цельное
Рисунок 3 – Сверло двухступенчатое со сменными пластинами
Рисунок 4 – Зенкер двухступенчатый цельный
Рисунок 5 – Зенкер двухступенчатый со сменными пластинами
Рисунок 6 – Развертка двухступенчатая цельная
Рисунок 7 – Трех резцовый расточной блок
Разнотипные инструменты (рисунки 8 – 9) в большинстве случаев применяются для последовательной обработки поверхностей одного диаметра например отверстий и нарезания резьбы зенкерования и развертывания сверления и растачивания и т.д. Разнотипные инструменты применяются иногда для обработки поверхностей разных диаметров но расположенных на одной оси например одновременного сверления отверстия и наружного точения.
Рисунок 8 – Сверло–зенкер
Рисунок 9 – Сверло–развертка
По количеству ступеней используемые на практике комбинированный инструмент разделяется на 2 – 6 ступенчатые.
По конструктивному исполнению КИ разделяются на цельные составные и насадные.
Цельные комбинированные инструменты (рисунки 2 4 6 9) изготавливаются из однородных по наименованию и марке материалов.
К составным относятся инструменты (рисунки 3 5) которые состоят из корпуса к которому при помощи сварки пайки клея винтов рифлений и т.д. крепятся режущие элементы. Эффективным является применение комбинированных инструментов с неперетачиваемыми пластинками. Неперетачиваемые пластинки позволяют относительно быстро получать любую комбинацию режущих кромок. Недостатком инструментов с неперетачиваемыми пластинками является громоздкость элементов крепления.
Насадные комбинированные инструменты (рисунки 7 9) или наборы объединяют однотипные или разнотипные инструменты общей оправкой или одним из инструментов. Примером составных инструментов могут служить зенковка насаженная на сверло несколько насадных зенкеров или разверток различных диаметров закрепленных на одной оправке и т. д.
По схемам резания комбинированные инструменты разделяются на:
инструменты с параллельной схемой (рисунок 10);
инструменты с последовательной схемой (рисунок 11);
инструменты с комбинированной схемой (рисунок 12).
Рисунок 10 – Параллельная схема резания
Рисунок 11 – Последовательная схема резания
Рисунок 12 – Комбинированная схема резания
По параллельной схеме работают однотипные комбинированные инструменты например ступенчатый зенкер ступенчатая развертка. По параллельной схеме могут работать и разнотипные инструменты например развертка–метчик. Разнотипные инструменты могут работать по параллельной схеме в том случае когда инструменты всех ступеней позволяют работать с одинаковыми режимами резания что является характерным например для развертки и метчика.
Комбинированные инструменты с параллельной схемой резания обеспечивают высокую производительность обработки за счет сокращения машинного времени. Недостатком параллельной схемы является увеличение составляющих сил резания. Кроме того при параллельной схеме увеличивается количество выделяемого тепла что ведет к снижению стойкости инструмента. По последовательной схеме работают разнотипные режущие инструменты например сверло–метчик. Недостатки наблюдаемые при параллельной схеме резания при последовательной – практически устраняются. Однако при работе разнотипными инструментами по последовательной схеме переход инструмента на работу новой ступенью требует изменения режимов резания.
Комбинированная схема резания инструментов заключается в том что в работу вступает одна или несколько ступеней а затем вступают остальные ступени или наоборот: сначала в работу вступают все ступени а затем количество одновременно работающих ступеней уменьшается. Последовательность работы ступеней и количество их одновременно работающих определяется соотношением между длинами отверстий и ступенями инструментов. Комбинированная схема используется при работе как однотипных так и разнотипных инструментов. Например при обработке трехступенчатым зенкером (однотипный инструмент) двух отверстий и снятия фаски инструмент при обработке двух отверстий работает по параллельной схеме а при снятии фаски – по последовательной. При обработке отверстия сверлом-зенкером (разнотипный инструмент) вначале в работу вступает сверло (последовательная схема) затем наряду со сверлом в работу вступает зенкер (параллельная схема) а после выхода сверла работает один зенкер (последовательная схема). С увеличением количества ступеней обрабатываемого отверстий число вариантов схем резания увеличивается.
Применение комбинированной схемы резания позволяет варьировать величинами сил действующих на инструмент а следовательно исключить поломки инструментов повысить точность обработки. Производительность обработки при комбинированной схеме ниже чем при параллельной схеме резания но выше чем при последовательной.
Технические характеристики станков
Станок токарно-винторезный 16Л20
Наибольший диаметр обрабатываемой заготовки:
Наибольший диаметр прутка проходящего через
отверстие шпинделя 34
наибольшая длина обрабатываемой заготовки 1500
Шаг нарезаемой резьбы:
Метрической 025- 56
Дюймовой число ниток на дюйм 56-025
Модульной модуль 05-112
Питчевой питч 112-05
Частота вращения шпинделя обмин 1600
Число скоростей шпинделя 21
Наибольшее перемещение суппорта:
Подача суппорта ммоб (мммин):
Число ступеней подач -
Скорости быстрого перемещения суппорта мммин:
Мощность электродвигателя главного привода кВт 63
Габаритные размеры (без ЧПУ):
Станок токарно-винторезный 16К20
отверстие шпинделя 53
наибольшая длина обрабатываемой заготовки 1000
Метрической 05- 112
Дюймовой число ниток на дюйм 56-05
Число скоростей шпинделя 22
Число ступеней подач 24
Мощность электродвигателя главного привода кВт 11
Станок Радиально-сверлильный 2М55
Наибольший условный диаметр сверления в стали 50
Рабочая поверхность стола 375х1600
Расстояние от нижнего торца шпинделя до раб
поверхности плиты 450-1600
Наибольшее перемещение:
Горизонтальное 1225
Наибольшее вертикальное перемещение -
Конус Морзе отверстие шпинделя 5
Частота вращения шпинделя обмин 20-2000
Число подач шпинделя 12
Подача шпинделя мммин 0056 – 25
Мощность электродвигателя привода
главного движения кВт 55
Габаритные размеры:
Станок Вертикально-сверлильный 2М112.
Наибольший условный диаметр сверления в стали 25
Рабочая поверхность стола 400х450
Наибольшее расстояние от торца шпинделя
до рабочей поверхности стола 700
Наибольший ход шпинделя 200
Наибольшее вертикальное перемещение:
Револьверной головки 170
Конус Морзе отверстие шпинделя 3
Число скоростей шпинделя 12
Частота вращения шпинделя обмин 45-2000
Число подач шпинделя 9
Подача шпинделя 01 – 16
главного движения кВт 22
Станок Внутришлифовальный 3К227А
Устанавливаемой заготовки 400
Устанавливаемой заготовки в кожухе 250
Наибольшая длина Устанавливаемой заготовки 125
Рекомендуемый (или наибольший) диаметр шлифования: 5-150
Наибольший ход стола 450
Наибольшее наладочное поперечное перемещение
Наибольший угол поворота бабки заготовки 45
Наибольший диаметр и высота шлифовального круга 80*50
Скорость автоматического перемещения стола
При правке круга 01-2
При быстром подводе и отводе 10
Частота вращения обмин шпинделя
Внутришлифовального 9000-12000
Бабки заготовки 60-120
Торцешлифовального приспособления 5600
Мощность электродвигателя привода главного
Габаритные размеры (с приставным оборудованием):
Масса (с приставным оборудованием) кг 4300
Справочник технолога-машиностроителя. т.1 под ред. А.Г.Косиловой и Р.К.Мещерякова. – М.:Машиностроение 1985 г.
Курсовое проектирование по предмету «Технология машиностроения» Добрыднев И.С. – М.: Машиностроение 1985 г.
Справочник технолога-машиностроителя. т.2 под ред. А.Г.Косиловой и Р.К.Мещерякова. – М.:Машиностроение 1985 г.
Справочник инструментальщика. Под ред. И.А.Ординарцева. – Л.: Машиностроение. Ленигр. отд-ние 1987 г.
Приспособления для металлорежущих станков. М.А.Ансеров – М.: Машиностроение 1984 г.
Атлас металлорежущих инструментов.