Изготовление корпуса подшипника




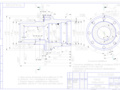
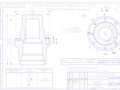
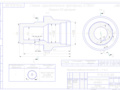
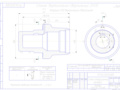
- Добавлен: 25.10.2022
- Размер: 4 MB
- Закачек: 2
Описание
Состав проекта
![]() |
![]() |
![]() ![]() |
![]() |
![]() ![]() |
![]() ![]() |
![]() ![]() |
![]() ![]() |
![]() |
![]() |
![]() |
![]() |
![]() |
![]() |
![]() |
![]() |
![]() |
![]() |
![]() |
![]() ![]() |
![]() ![]() |
![]() ![]() |
![]() |
![]() ![]() |
![]() ![]() |
![]() ![]() |
![]() ![]() |
![]() ![]() |
![]() ![]() |
![]() ![]() |
![]() ![]() |
![]() ![]() |
![]() ![]() |
![]() ![]() |
![]() ![]() |
![]() ![]() |
![]() ![]() |
![]() ![]() |
![]() ![]() |
![]() ![]() |
![]() ![]() |
![]() |
![]() ![]() ![]() ![]() |
![]() ![]() ![]() ![]() |
![]() ![]() ![]() ![]() |
![]() ![]() |
![]() ![]() |
![]() ![]() |
![]() ![]() |
![]() ![]() ![]() ![]() |
![]() ![]() |
![]() ![]() ![]() ![]() |
![]() |
![]() ![]() |
![]() ![]() ![]() ![]() |
![]() ![]() |
![]() ![]() |
![]() ![]() ![]() ![]() |
![]() ![]() ![]() ![]() |
![]() ![]() ![]() ![]() |
![]() ![]() |
![]() |
![]() ![]() ![]() ![]() |
![]() ![]() |
![]() ![]() ![]() ![]() |
![]() ![]() |
![]() |
![]() ![]() ![]() ![]() |
![]() ![]() |
![]() ![]() |
![]() ![]() ![]() ![]() |
![]() ![]() |
![]() ![]() ![]() ![]() |
![]() ![]() |
![]() ![]() ![]() ![]() |
![]() ![]() ![]() |
![]() |
![]() ![]() ![]() ![]() |
![]() ![]() ![]() ![]() |
![]() ![]() ![]() ![]() |
![]() ![]() |
![]() ![]() |
![]() ![]() |
![]() ![]() ![]() ![]() |
![]() ![]() |
Дополнительная информация
резец.dwg

КФ МГТУ им. НЭ Баумана
Технические требования:
Пластины - твердый сплав Т15К6
Спецификация-резец.dwg

Заготовка.dwg

Условный контур относится к готовой детали.
Неуказанные радиусы R=5 мм.
Технические требования:
фреза.dwg

На режущих кромках не допускаются:
Неуказанные предельные отклонения
Маркировать: марку завода изготовителя
число зубьев нарезаемого колеса.
Задание.dwg

Технические требования к отливке по инструкции 02130-13И.
Точность отливки17-12 ГОСТ 26645-85
Неуказанные предельные отклонения обрабатываемых
Гидроиспытать внутреннюю полость давлением 01. МПа
на плотность. Течи и отпотевания не допускаются.
Покрытие наружних необработанных поверхностей
красить в 2 слоя красно-коричневой краской
Технические требования
Пробка.dwg

Технические требования по ГОСТ 2015-84.
Маркировка калибров-скоб по ГОСТ 2015-84.
калибр-пробка.dwg

Технические требования по ГОСТ 2015-84.
Маркировка калибров-скоб по ГОСТ 2015-84.
055.dwg

Неуказанные предельные отклонения H14
Операция 055 шлифование
Станок шлифовальный 3М153
050.dwg

Неуказанные предельные отклонения размеров
Операция 050 шлифование
Станок шлифовальный 3М153
Спецификация-приспособление.dwg

Уплотнительные кольца
Корпус пневмоцилиндра
Болт М16 ГОСТ 22034-76
Болт М12 ГОСТ 22034-76
Призматические зажимы
Болт М10 ГОСТ 22034-76
Приспособление.dwg

020.dwg

Неуказанные предельные отклонения H14
Станок токарно-винторезный 1К62
Операция 020 токарная чистовая
010.dwg

Неуказанные предельные отклонения H14
Станок токарно-винторезный 1К62
Операция 010 токарная черновая
025.dwg

Неуказанные предельные отклонения H14
Операция 025 фрезерная
Станок горизонтально-фрезерный 6Т804Г
015.dwg

Неуказанные предельные отклонения H14
Станок токарно-винторезный 1К62
Операция 015 токарная черновая
Записка.doc
Расчетно-пояснительная записка к
курсовому проекту по
Технологии подъемно-транспортного машиностроения
«Изготовление корпуса подшипника»
Технологическая часть:
Назначение детали в узле (Введение) 3
Определение годового объема выпуска и типа производства 3
Анализ технологичности конструкции детали . 4
Выбор и обоснование способа получения заготовки и ее расчет 5
Выбор технологических баз 5
Разработка маршрута обработки заготовки .. 6
Расчет операционных припусков 7
Расчет режимов резания .. 9
Расчет мерительного инструмента .. ..23
Техническое нормирование 24
Конструкторская часть:
Проектирование станочного приспособления 25
Список литературы 36
Корпус подшипника – это узел в котором установлен подшипник предназначенный для опоры вращающейся детали. В настоящем курсовом проекте разработан технологический процесс изготовления корпуса подшипника который удерживает вращающейся в нем вал.
Предназначен для фиксации вала в моторе и для предохранения от попадания инородных частиц внутрь него.
Определение типа производства
Годовой объём выпуска определяем по формуле:
Где: m=1 – количество одноимённых деталей в машине
M=10000 – годовой объём выпуска машин
γ=3 – количество запасных частей в процентах
=7 – процент брака и технологических потерь включая детали используемые для настройки стан в процентах.
Масса детали 1215 кг
По таблице [3 c.24] определяем тип производства : Крупносерийное
Анализ технологичности конструкции детали
Каждая деталь должна изготавливаться с минимальными трудовыми и материальными затратами. Эти затраты можно сократить в значительной степени от правильного выбора варианта технологического процесса и его оснащение механизации и автоматизации применения оптимальных режимов обработки и правильной подготовки производства.
При оценке технологичности учитываются следующие характеристики:
Обрабатываемость материала резанием;
Рациональность выбора заготовки;
Рациональность постановки размеров;
Технологичность отдельных элементов;
Точность и шероховатость поверхностей;
Следует предусматривать плавные переходы в местах сопряжений;
Не рекомендуется предусматривать выступы не вписывающиеся в контур детали;
Физико-механические и механические свойства материала жесткость детали ее форма и размеры должны соответствовать требованиям технологии изготовления;
Конструкция детали должна состоять из стандартных и унифицированных конструктивных элементов или быть стандартной в целом.
Технологичность детали характеризуется коэффициентом использования материала:
где Q1 – масса детали;
Q2 – масса заготовки.
где V – объем заготовки;
ρ – плотность стали.
где d – диаметр заготовки;
l – длина заготовки.
Т.к. Кm=85% то можно сделать вывод что материал расходуется рационально .
Качественно технологичность детали можно оценить как хорошую
Малый процент металла уходит в стружку
Выбор и обоснование способа получения заготовки
Правильно выбрать заготовку – значит правильно определить рациональный метод ее получения установить припуски на ее механическую обработку.
Целесообразность экономичность и эффективность применения того или иного вида заготовки зависит от нескольких факторов:
- технологических свойств материала;
- конструкции и размеров детали;
- точности выполнения заготовки и требуемого качества ее поверхности;
- программы выпуска;
На основании анализа вышеперечисленных факторов выбираем в качестве заготовки корпуса - отливку.
Выбор технологических баз
Технологической называют базу используемую для определения положения заготовки или изделия при его изготовлении или сборке.
Выбор технологических баз является сложной задачей проектирования технологического процесса. От правильного выбора технологических баз в значительной мере зависят:
Точность получения заданных размеров
Правильность взаимного расположения поверхностей
Степень сложности технологической оснастки режущего и измерительного инструментов.
Операция 010 Токарная (черновая)
Технологическая база – обработанная поверхность ø125 мм
Операция 015 Токарная (черновая)
Технологическая база - обработанная поверхность ø165 мм.
Операция 020 Токарная (чистовая)
Технологическая база - обработанная поверхность ø95 мм.
Операция 025 Фрезерная
Технологическая база – внутренняя обработанная поверхность ø165 мм.
Операция 030 - Сверлильная
Операция 040 Сверлильная
Технологическая база – обработанная поверхность ø165 мм торец обработанной поверхности ø165 мм
Операция 045 Токарная (чистовая)
Технологическая база – обработанная поверхность ø165 мм
Операция 050 Сверлильная (резьбонарезная)
Операция 055 Шлифовочная
Операция 060 Шлифовочная
Разработка маршрута обработки заготовки
Операция 000 Заготовительная:
Залить металл в форму
Операция 005 Заготовительная:
Извлечь заготовку отбить облой.
Операция 010 Токарная (черновая):
Подрезать торец в размер 250 мм и угол 60град. точить поверхность ø125 мм и ø165 мм на длину 105мм и 130мм соответственно точить внутреннюю полость ø108 мм ø99 ø88 и ø60 мм на длину 21мм 45 мм 105 мм и 280 мм соответственно.
Операция 015 Токарная (черновая):
Подрезать торец в размер 237 мм точить поверхность ø165 мм ø110 мм ø109 мм ø95мм и ø152 мм на длину 105мм согласно чертежа точить радиус R8 мм.
Операция 020 Токарная (чистовая):
Расточить поверхность ø110 мм ø101 мм ø90 мм ø62 мм ø111 и ø91 мм согласно чертежа.
Операция 025 Фрезерная:
Фрезеровать паз дисковой фрезой согласно чертежа.
Операция 030 Сверлильная:
Сверлить 1 отверстие ø5 мм.
Операция 040 Сверлильная:
Сверлить 8 отверстий ø12 мм и зенковать 8 отверстий зенкером ø18 мм согласно чертежа.
Операция 045 токарная:
Точить сферу R9.5 согласно чертежа.
Операция 050 Сверлильная:
Нарезать резьбу в 8 отверстиях М12-6Н мм на глубину 22 мм.
Операция 055 Шлифование:
Шлифовать поверхности ø110 мм ø90 мм и ø62 мм.
Операция 060 Шлифование:
Шлифовать поверхности ø110 мм.
Расчёт операционных припусков и межоперационных размеров
Технологический маршрут (операции)
Элементы припуска мкм
Допуск на изготовление Td мм
Погрешность установки
Минимальный припуск на черновую обработку
Максимальный припуск на черновую обработку
Величина остаточного суммарного расположения
Величина погрешности при чистовой обработке
Припуск на чистовую обработку
Припуск на шлифование
Промежуточные расчётные размеры по обрабатываемым поверхностям
для чистовой токарной обработки
для черновой токарной обработки
для заготовки детали
Минимальные промежуточные размеры
Максимальные промежуточные размеры
Расчёт режимов резания
Т=90 мин – Стойкость инструмента
Силовые параметры [2.c271]
Выбираем станок 1К62
Операция 025 Фрезерная
V – скорость резания
С – эмпирический коэффициент
q xyupm – показатели степеней
принимаем n=300 обмин
Выбираем станок Вертикально-фрезерный 6Т804Г
Операция 030 Сверлильная
qym – показатели степеней
Принимаем n=2500 обмин
Выбираем станок вертикально сверлильный 2H135
Операция 040 Сверлильная
Принимаем n=550 обмин
Выбираем станок вертикально - сверлильный 2Н135
Операция 045 токарная (предпочтительно выполнить на станке с ЧПУ)
Операция 050 Сверлильная
Нарезание резьбы ø12 мм
Принимаем n=350 обмин
Выбираем станок вертикально-сверлильный 2Н135
Операция 055 Шлифование
Vk = 30 мс [ист.3 с.301]
Где эмпирические коэффициенты: [ист.3 с.303]
принимаем n = 150 обмин
Выбираем станок шлифовальный 3М135
Операция 060 Шлифование
Расчёт мерительного инструмента
Расчёт исполнительных размеров калибр-пробки
Исполнительные размеры проходных калибров-пробок
Где - наименьший предельный размер изделия мм
- отклонение середины поля допуска на изготовление проходного калибра для отверстия относительно предельного размера изделия мкм
- допуск на изготовление калибров мкм
Исполнительные размеры непроходных калибров-пробок
Где - наибольший предельный размер изделия мм
Предельный размер изношенного калибра-пробки
Где - допустимый выход размера изношенного проходного калибра для отверстия за границу поля допуска изделия
Расчёт исполнительных размеров калибров-скоб
Исполнительные размеры проходных калибров-скоб
- допуск на изготовление калибров для вала мкм
Исполнительные размеры непроходных калибров-скоб
Предельный размер изношенного калибра-скобы
Где - допустимый выход размера изношенного проходного калибра для вала за границу поля допуска изделия
Техническое нормирование
В крупносерийном и массовом производстве общая норма времени на механическую обработку одной заготовки
Где технологическое время
-время на обслуживание рабочего места
- вспомогательное время
Технологическое время для многих видов обработки
Конструкторская часть
Проектирование станочного приспособления
Рис.1. Тиски переналаживаемые с поднятыми губками.
Для выполнения фрезерной операции (020) я выбрал такой тип приспособления как тиски переналаживаемые с поднятыми губками с пневматическим зажимом.
На рисунке 1 изображена схема установки и связь их с пневмоприводом. Тяга пропущенная через рычаг своим левым концом связана со штоком привода а правым с корпусом связанную с держателем. Последний служит для установки губок необходимый зазор обеспечивается с помощью регулировочного винта. Окончательный зажим обеспечивается с помощью пневматического привода. Усилие зажима при давлении до 5000кгс.
Расчет приспособления:
Расчет сил зажатия заготовки пневмоприводом (рис. 1.). [ист.2 с.114]
Пневматические силовые приводы широко применяются в приспособлениях разнообразных типов. Быстрота легкость постоянство силы зажима возможность её регулирования и контроля а также дистанционное управление зажимами являются основными преимуществами пневмоприводов для зажима обрабатываемых заготовок. Пневматические приводы широко применяются в крупносерийном и массовом производстве.
Для обеспечения надёжности зажима заготовки определим коэффициент запаса
Определим необходимую силу зажима для обрабатываемой заготовки
Определим расчётный диаметр пневмоцилиндра
Выбираем стандартный диаметр пневмоцилиндра
Определим действительную силу зажима пневмоцилиндра
Определим время срабатывания пневмопривода
где - длина хода поршня =12 см.
- диаметр воздуховода =06.
- скорость перемещения воздуха =180 (мс)
Общее время срабатывания пневмоцилиндра показывает производительность данного зажимного устройства. Ход поршня устанавливают в зависимости от конструктивных особенностей станочного приспособления обрабатываемой детали и технологического оборудования.
Технические характеристики станков
Станок токарно-винторезный 1К62
Наибольший диаметр обрабатываемой заготовки:
Наибольший диаметр прутка проходящего через
отверстие шпинделя 53
наибольшая длина обрабатываемой заготовки 1000
Шаг нарезаемой резьбы:
Метрической 05- 112
Дюймовой число ниток на дюйм 56-05
Модульной модуль 05-112
Частота вращения шпинделя обмин 1600
Число скоростей шпинделя 22
Наибольшее перемещение суппорта:
Подача суппорта ммоб (мммин):
Число ступеней подач 24
Скорости быстрого перемещения суппорта мммин:
Мощность электродвигателя главного привода кВт 11
Габаритные размеры (без ЧПУ):
Станок токарно-винторезный 16Л20
отверстие шпинделя 34
наибольшая длина обрабатываемой заготовки 1500
Метрической 025- 56
Дюймовой число ниток на дюйм 56-025
Питчевой питч 112-05
Число скоростей шпинделя 21
Число ступеней подач -
Мощность электродвигателя главного привода кВт 63
Станок Вертикально-сверлильный 2Н135
Наибольший условный диаметр сверления в стали 18
Рабочая поверхность стола 320х360
Наибольшее расстояние от торца шпинделя
до рабочей поверхности стола 650
Наибольший ход шпинделя 150
Наибольшее вертикальное перемещение:
Револьверной головки 300
Конус Морзе отверстие шпинделя 2
Число скоростей шпинделя 9
Частота вращения шпинделя обмин 180-2800
Число подач шпинделя -
Подача шпинделя ручная
Мощность электродвигателя привода
главного движения кВт 15
Габаритные размеры:
Станок Вертикально-фрезерный 6Т804Г
Размеры рабочей поверхности стола 400х1000
Наибольшее перемещение стола:
Шпиндельной бабки 430
Перемещение гильзы со шпинделем 120
Внутренний конус шпинделя (конусность 7:24) -
Число скоростей шпинделя 50
Частота вращения шпинделя обмин 315-1600
Число подач стола 12
Шпиндельной бабки 4-800
Скорость быстрого перемещения мммин:
Шпиндельной бабки 800
Мощность электродвигателя привода главного
Масса (без выносного оборудования) кг 6500
Станок шлифовальный 3М153
Устанавливаемой заготовки 400
Устанавливаемой заготовки в кожухе 250
Наибольшая длина Устанавливаемой заготовки 125
Рекомендуемый (или наибольший) диаметр шлифования: 5-150
Наибольший ход стола 450
Наибольшее наладочное поперечное перемещение
Наибольший угол поворота бабки заготовки 45
Наибольший диаметр и высота шлифовального круга 80*50
Скорость автоматического перемещения стола
При правке круга 01-2
При быстром подводе и отводе 10
Частота вращения обмин шпинделя
Внутришлифовального 9000-12000
Бабки заготовки 60-120
Торцешлифовального приспособления 5600
Габаритные размеры (с приставным оборудованием):
Масса (с приставным оборудованием) кг 4300
А.Г.Косилова Р.К.Мещереков«Справочник технолога машиностроителя» том 1 Машиностроение 1986г.
А.Г.КосиловаР.К.Мещереков «Справочник технолога машиностроителя» том 2 Машиностроение 1986г
И.С. Добрыднев Курсовое проектирование по предмету “Технология машиностроения” >> Машиностроение. 1985г.
М. Е. Егоров «Технология машиностроения» Высшая школа 1976г.
В. Э. Пуш «Металлорежущие станки» Машиностроение 1985г.
Д. А. Локтев «Металлорежущие станки» Машиностроение 1968г.
В. И. Анурьев «Справочник конструктора - машиностроителя » том 2 Машиностроение 1978г.
045.dwg

Неуказанные предельные отклонения Н14
Станок вертикально-сверлильный 2Н135
Операция 045 вертикально-сверлильная
*Закрепляется в делительной головке
035.dwg

Неуказанные предельные отклонения Н14
Станок токарно-винторезный 1К62
Операция 035 токарная чистовая
Для данной операции целесообразно пременить станок с ЧПУ
030.dwg

Неуказанные предельные отклонения Н14
Станок вертикально-сверлильный 2Н135
Операция 030 вертикально-сверлильная
040.dwg

Неуказанные предельные отклонения Н14
Станок вертикально-сверлильный 2Н135
Операция 040 вертикально-сверлильная
*Закрепляется в делительной головке.
Сверление через кондукторную плиту.
Рекомендуемые чертежи
- 29.07.2014