Горизонтальный консольно-фрезерный станок




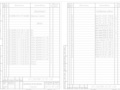
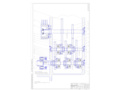
- Добавлен: 25.10.2022
- Размер: 1 MB
- Закачек: 1
Описание
Состав проекта
![]() |
![]() ![]() ![]() ![]() |
![]() |
![]() ![]() |
![]() ![]() ![]() ![]() |
![]() ![]() |
![]() |
![]() ![]() ![]() ![]() |
![]() ![]() |
![]() |
![]() ![]() ![]() |
![]() ![]() ![]() |
Дополнительная информация
Чертёж 1 листа.dwg

Кинематическая схема и график чисел оборотов горезонтально-фрезерного станка модели 6Н81Г.
Кинематическая схема и график чисел оборотов горизонтально-фрезерного станка модели 6П80Г.
Кинематическая схема привода главного движения и график чисел оборотов проектируемого станка .
Спецификация.dwg

КП-206998-25-МС-418-17-11-001
КП-206998-25-МС-418-17-10-002
КП-206998-25-МС-417-17-10-003
КП-206998-25-МС-417-17-10-004
КП-206998-25-Т-415-06-08-005
КП-206998-25-Т-415-06-08-006
КП-206998-25-Т-415-06-08-007
КП-206998-25-Т-415-06-08-008
КП-206998-25-Т-415-06-08-009
КП-206998-25-Т-415-06-08-010
КП-206998-25-Т-415-06-08-011
КП-206998-25-Т-415-06-08-012
КП-206998-25-Т-415-06-08-013
КП-206998-25-Т-415-06-08-014
КП-206998-25-Т-415-06-08-015
КП-206998-25-МС-417-17-10-000СБ
Винт М5 х 12 ГОСТ 17475-80
Винт М6 х 8 ГОСТ 11074-93
Винт М12 х 18 ГОСТ 11738-84
Винт М4 х 8 ГОСТ 11738-84
Подшипник 205 ГОСТ 8338-75
Кольцо стопорное В28.Ц15хр ГОСТ 139442-86
Гайка М10-6Н.88.35Х.016 ГОСТ 5927-70
Муфта 125-28-1-У1 ГОСТ 21424-75
Кольцо стопорное В19.Ц15хр ГОСТ 139442-86
Кольцо стопорное В23.Ц15хр ГОСТ 139442-86
Кольцо стопорное В32.Ц15хр ГОСТ 139442-86
Подшипник 204 ГОСТ 8338-75
Подшипник 206 ГОСТ 8339-75
Шайба 10 65Г 02 9 ГОСТ 6402-70
Шпонка 8х7х28 ГОСТ 23360-78
Шпонка 8х7х36 ГОСТ 23360-78
Кольцо запорное 45 МН 470-61
Э1М072-2Н ГОСТ 21573-76
Чертеж 2 листа.dwg

Минимальная частота вращения n
Максимальная частота вращения n
Мощность двигателя N
Cмазка разбрызгиванием масло Индустриальное И-20А ГОСТ
Развёртка коробки скоростей
Технические требования
Доклад.doc
Назначение. Станок Предназначен для выполнения разнообразных фрезерных работ цилиндрическими торцевыми концевыми и фасонными фрезами при обработке деталей из черных и цветных металлов а также других материалов инструментом из быстрорежущей стали или оснащенным пластинками твердых и сверхтвердых синтетических материалов.
Аннотация. В данном курсовом проекте проанализированы несколько станков близких типоразмеров и приведены их технические характеристики.
Цель: разработать привод вращения шпинделя с автоматической коробкой скоростей.
Рассчитать основные технические характеристики проектируемого станка.
Составить кинематическую схему станка.
Произвести расчёт элементов привода вращения шпинделя.
Разработать сборочный чертёж спроектированной автоматической коробки скоростей.
По операции фрезерования паза в углеродистой Стали 45 прорезной фрезой диаметром из быстрорежущей стали определяется минимальная частота вращения шпинделя обмин.
Максимальная частота вращения шпинделя определяется по операции фрезерования паза концевой фрезой диаметром оснащённой винтовыми твёрдосплавными пластинами обмин.
Согласно рекомендациям нормали Н11-1 выбирается знаменатель геометрической прогрессии получаем 12 ступенчатую коробку скоростей.
Далее производим разработку структурной схемы станка которая заключается в следующем: обработка исходных данных и построение структурной сетки. На основе структурной сетки строится график частот вращения по которому производится кинематический расчёт целью которого является определение параметров зацепления зубчатых колёс коробки скоростей а именно определяются передаточные отношения и число зубьев с последующей их проверкой. На основе полученных данных составляется кинематическая схема развёртки коробки скоростей.
Следующим этапом является силовой расчет элементов привода. На этом этапе рассчитываются мощности и крутящие моменты на валах определяются модули групп передач определяются параметры зубчатых колёс прочностной расчёт валов.
Конструктивные особенности. Проектируемый станок будет обладать прочностью рабочих механизмов мощностью привода автоматической коробкой скоростей и широким диапазоном скоростей резания позволяющим использовать режущий инструмент оснащенный твёрдым сплавом.
Для сокращения вспомогательного времени на станке обеспечена возможность автоматического переключения скоростей вращения шпинделя за счёт электромагнитных муфт.
Смазка. Для подачи масла в систему используем плунжерный насос с механическим приводом.
Смазке подлежат подшипники электродвигателя подшипники и шестерни коробки скоростей а также электромагнитные муфты.
В проектируемом станке применено циркулярное смазывание и смазывание под давлением от насоса маслом Индустриальное И-20А.
Записка Моя по Станкам.doc
ГОУ ВПО “Омский государственный технический университет”
Кафедра: «Металлорежущие станки и инструменты»
Пояснительная записка к курсовому
проекту на тему: Горизонтальный консольно-фрезерный станок
Начальным этапом проектирования станка является анализ аналогичных станков данной группы с целью определения наиболее подходящего. Далее производим разработку структурной схемы станка которая заключается в следующем: обработка исходных данных и построение структурной сетки. На основе структурной сетки строится график частот вращения по которому производится кинематический расчет целью которого является определение параметров зацепления зубчатых колес коробки скоростей а именно определяются передаточные отношения и число зубьев с последующей их проверкой. На основе полученных данных составляется кинематическая схема развертки коробки скоростей.
Следующим этапом является силовой расчет элементов привода. На этом этапе рассчитывается мощности и крутящие моменты на валах определяются модули групп передач определяются параметры зубчатых колес прочностной расчет валов.
Заключительным этапом проектирования является расчет компоновки привода.
Технические характеристики станков близких типоразмеров ..
Разработка кинематической схемы коробки скоростей .
Определение технических характеристик станка
Определение мощности двигателя
Кинематический расчет .
1 Выбор структурного варианта коробки скоростей .
2 Определение чисел зубьев шестерен
3 Определение мощностей на валах
4 Определение крутящего момента на валах
Расчет зубчатых передач
1 Допускаемые напряжения зубчатых колёс
2 Определение ширины венцов зубчатых колес. ..
1 Диаметры валов выбор подшипников
2 Выбор валов подбор муфт
Расчет разъемных соединений ..
Проверка прочности шлицевого соединения .
Расчет шпоночных соединений
Станок данной конфигурации предназначен для фрезерования различных деталей из стали чугуна и цветных металлов сравнительно небольших размеров. Обработка деталей осуществляется цилиндрическими дисковыми фасонными угловыми модульными торцевыми и прорезными фрезами как встречным так и попутным фрезерованием. Станок используется в условиях индивидуального и серийного производства. При наличии делительной головки можно фрезеровать прямозубые шестерни рейки канавки и т.п.
Достаточная мощность приводов и широкий диапазон скоростей и подач позволяют успешно работать на станке как фрезами из быстрорежущей стали так и фрезами оснащенными пластинками твердого сплава.
Технические характеристики станков близких типоразмеров
Рабочая поверхность стола мм
Число скоростей шпинделя
Частота вращения шпинделя обмин
Число скоростей подач
Мощность электродвигателя главного движения кВт
Разработка кинематической схемы коробки скоростей
Для обеспечения кинематических расчетов сложных коробок применяется графоаналитический метод который заключается в графическом изображении чисел оборотов и передаточных отношений в виде графиков чисел оборотов и структурных сеток.
При изображении структурных сеток приняты следующие условности:
· Каждому валу коробки скоростей соответствует своя шкала чисел оборотов на которой точками отмечается число скоростей которое может иметь данный вал;
· Числа оборотов на каждой шкале изображаются в логарифмическом масштабе поэтому геометрический ряд чисел оборотов изображается в виде точек расположенных на одинаковом расстоянии (оно равно j - знаменателю геометрической прогрессии);
· Передаточные отношения изображаются в виде линий соединяющих точки соответствующих чисел оборотов соседних валов; наклон линии характеризует величину передаточного отношения параллельные линии означают одинаковые передаточные отношения.
Знаменатель геометрической прогрессии определяется по формуле (1):
- максимальная чистота вращения шпинделя = 2000 обмин
- минимальная чистота вращения шпинделя = 160 обмин
z - число ступеней частот вращения = 12
Принимаем j = 126 (табл. 4 [5])
В соответствии с принятым j стандартный ряд частот вращения выглядит следующим образом:
Число z определяется по формуле (2):
где Д – диапазон регулирования
Вариант выбирается по следующим рекомендациям:
· в одной группе следует делать не более 4-х передач;
· группы передач с большим числом передач следует располагать в области высоких частот вращения (на входе) т.к. эти передачи имеют меньшие габариты;
· если число z нельзя расположить то следует принять большее и сделать перекрытие.
Принимаем z=2*3*2 рис. 1
рис. 1 Структурная сетка
Определение технических характеристик станка
Определение основных технических характеристик ведется исходя из того что на станках средних размеров обрабатываются стали близкие по свойствам к стали 45.
Минимальная частота вращения nmin определяется по операции прорезки паза в углеродистой Стали 45 прорезной фрезой диаметром шириной при глубине фрезерования из быстрорежущей стали при соответствующих режимах резания: подаче Sz пр скорости резания Vпр и стойкости фрезы Тм.
Vпр= Vтабл * k1*k2*k3
k1 - коэффициент зависящий от обрабатываемого материала;
k2 - коэффициент зависящий от стойкости инструмента;
k3 - коэффициент зависящий от отношения длинны резания к обрабатываемому материалу;
- глубина фрезерования мм; t=6 мм
- ширина фрезы мм; мм
Sz пр =0035 ммзуб - подача
Vрез= 48*1*1*1=48 ммин
Принимаем минимальную частоту вращения nmin=160 обмин
Максимальная частота вращения шпинделя определяется по операции обработки паза концевой фрезой оснащённой винтовыми твёрдосплавными пластинами диаметром при соответствующих режимах резания
Принимаем nmax=2000 обмин
Минимальная частота вращения шпинделя принимается равной 160 обмин при прорезки паза в углеродистой Стали 45 прорезной фрезой диаметром .
Максимальная частота вращения шпинделя принимается равной 2000 обмин при обработке паза концевой фрезой оснащённой винтовыми твёрдосплавными пластинами диаметром .
Сила Pz определяется по операции фрезерования максимальным диаметром при соответствующих режимах: подачи и скорости резания. Для проектируемого станка сила Pz=2756 Н.
Главная составляющая силы резания при фрезеровании - окружная сила Н определяющаяся по формуле (3):
где z - число зубьев фрезы; n - частота вращения фрезы обмин.
Мощность резания кВт
Определение мощности двигателя
Привод главного движения. Большинство приводов главного движения универсальных станков работают в повторно-кратковременном режиме при котором периоды работы под нагрузкой имеют такую длительность и так чередуются с паузами такой продолжительности что температура нагрева обмотки электродвигателя не превышает допустимой величины. Мощность электродвигателя работающего в указанном режиме определяют по формуле (4):
Nдв = Nрез max hпр*l (4)
где hпр - КПД привода ориентировочно принимается hпр = 07 - 085;
Nдв=843085*2=496 кВт
Выбран двигатель АИР132S серии 4А мощностью 52 кВт.
На рисунке 2 приведен эскиз электродвигателя
Кинематический расчет.
Целью кинематического расчета является определение параметров зацепления проектируемой коробки скоростей.
Сначала строится график частот вращения. Построение ведется аналогично построению структурных сеток но имеются свои особенности:
-добавляется вал электродвигателя
-построение начинается из точки соответствующей частоте вращения двигателя;
График частот вращения приведен на рисунке 3
По графику частот вращения определяется передаточное отношение через знаменатель геометрической прогрессии j и в зависимости от него определяются числа зубьев.
1 Выбор структурного варианта коробки скоростей
Из структурной сетки получим следующие соотношения передаточных чисел:
2 Определение чисел зубьев шестерен
Результаты приведены в таблице 2.
Чтобы проверить правильность выбора чисел зубьев зубчатых колес составляем уравнения кинематической цепи для каждой частоты вращения из которых определяются фактические частоты вращения. Также определяем относительную погрешность D (5)
nфакт - фактическая частота вращения обмин
nст - стандартная частота вращения обмин
Dдоп - допускаемая относительная погрешность %
Расчеты сведены в таблицу 3
Левая часть уравнения кинематической цепи
Относительная погрешность %
40*(4050)*(7145)*(140125)
40*(3555)*(7145)*(140125)
40*(3643)*(7145)*(140125)
0*(4050)*(7145)*(140125)
0*(3555)*(7145)*(140125)
0*(3060)*(7145)*(140125)
40*(4050)*(3383)*(140125)
40*(3555)*(3383)*(140125)
40*(3060)*(3383)*(140125)
0*(4050)*(3383)*(140125)
0*(3555)*(3383)*(140125)
0*(3060)*(3383)*(140125)
В связи с тем что погрешность величин скоростей не превышает допустимых на коробке скоростей указывается стандартные величины скоростей. Схема развертки коробки скоростей приведена на рис. 4
рис. 4 Кинематическая схема коробки скоростей проектируемого станка
3 Определение мощностей на валах
Мощность на i -том валу определяется по формуле (6):
Ni = Ni -1 ×h1 ×h2 (6)
Где Ni -1 - мощность на предыдущем валу кВт
h1 - КПД пары подшипников h1 = 099
h2 - КПД зубчатой передачи h2 = 097
N2 = Nдв = 515*099*097 = 49 кВт
N3 = Nдв =10*099*0972 = 46 кВт
4 Передаваемые крутящие моменты
Крутящий момент на валах определяется:
Результаты расчетов сводим в таблицу 4
Частота вращения валов обмин
Передаваемая мощность кВт
Передаваемые крутящие моменты T2 Н*м
Проверочный расчёт зубьев на выносливость
1 Допускаемые напряжения зубчатых колёс
Для изготовления зубчатых колёс в приводе главного движения проектируемого станка используем материал улучшенная сталь 45 HB 220 250 [2 с. 553] у которой
[и]= 18000 - допускаемое напряжение изгиба Нсм2;
[к]= 60000 – допускаемое контактное напряжение Нсм2.
Напряжения изгиба определяются по формуле (7) [5 c. 99]:
k = 13 –коэффициент нагрузки (при симметричном расположении зубчатых колёс относительно опор);
– мощность передаваемая зубчатым колесом кВт;
γ = 125 – коэффициент износа;
y – коэффициент формы зуба зависящий от числа зубьев и смещения инструмента [5 с.97];
z – число зубьев колеса;
n – частота вращения вала обмин;
m –модуль колеса см;
– ширина венца зубчатого колеса см;
и= 96433 Нсм2 ≤ [] и=18000 Нсм2
Контактные напряжения
Контактные напряжения определяются по формуле (8) [5 c. 92]:
U – передаточное отношение;
– межосевое расстояние:
k = 13 - коэффициент нагрузки;
- мощность передаваемая зубчатым колесом кВт;
b– ширина венца зубчатого колеса см;
n – частота вращения вала обмин.
к = 569792 Нсм2 ≤ [ к]=60000 Нсм2
Условия прочности зубьев по контактным напряжениям и напряжениям изгиба выполняются следовательно принимаем:
2 Определение ширины венцов зубчатых колес.
bZ1 = bZ2 = bZ3 = bZ4 = bZ5 = bZ6 =ym m1 = 6*3 = 18 мм принимаем = 18 мм
bZ7 = bZ8 = bZ9 = bZ10 = ym m2 = 6*3 = 18 мм принимаем = 18 мм
– делительный диаметр мм;
– диаметр вершин зубьев мм;
– диаметр впадин мм;
Сведем все расчеты в таблицу 5
Ширины зубчатых венцов мм
1 Диаметры валов выбор подшипников.
Определение расчётной частоты вращения по формуле (9):
nрас. = nмin =3008 обмин (9)
Таким образом превратим коробку скоростей в многоступенчатый редуктор [5 стр.119].
При переменной нагрузке и малых изгибающих моментах или при постоянной нагрузке и средних изгибающих моментах диаметр вала определяется по формуле: [1 с. 19]:
Определим предварительные диаметры валов по уравнению (10):
Диаметр I - ого вал.
Принимаем по ГОСТ 12080 - 66 d1 = 20 мм.
Диаметр II - ого вала.
Принимаем по ГОСТ 12080 - 66 d2 = 20 мм.
Диаметр III - ого вала.
Принимаем по ГОСТ 12080 - 66
В зависимости от этих диаметров внутренних колец подшипников выписываются из таблиц по ГОСТ диаметры наружных колец ширины колец B мм
d1 = 20 D = 47 B = 14; C = 12700 Н
d2 = 20 D = 47 B = 14; C = 12700 Н
d3 = 30 D = 62 B = 16; C = 19500 Н
Выбираем шариковые однорядные подшипники по ГОСТ 12080 - 66.
I вал 204 подшипник легкой серии диаметров (значения см. выше);
II вал 204 подшипник легкой серии диаметров (значения см. выше);
III вал 206 подшипник легкой серии диаметров (значения см. выше);
2 Выбор валов подбор муфт.
Выбор муфт осуществляется по крутящему моменту на валах определяемому по формуле (11):
ni – частота вращения вала обмин.
Мкр2 = 9740= 9740 =357 Н м;
Мкр2 = 9740 =9740 =68 Н м;
Мкр3 = 9740= 9740 =1563 Н м;
Исходя из примерно среднего значения для крутящего момента на I и II валах принимаем обозначение габарита муфты 07 согласно справочнику [2с.329].
Устанавливаем следующее исполнение электромагнитной муфты Э1М
с контактным токоподводом т.к. это исполнение упростит подвод электроэнергии к муфте и её крепление в корпусе
Размер шлицевого отверстия с посадкой поРис.5
Т.к муфта имеет шлицевое отверстие целесообразно будет выбрать шлицевой вал (I – ый II – ой и III– ий).
Расчет разъемных соединений
Расчет штифтовых соединений.
В коробке скоростей поводковые втулки выполнены раздельно с шестернями и зубчатыми колесами поэтому для передачи крутящего момента применены штифтовые и шпоночные соединения.
Расчет штифтов производится на срез по формуле (12):
где Р - сила действующая поперек штифта кг
[tср] - допускаемое напряжение на срез кгс*см
Принимаем материал штифта Ст. 3 с допускаемым напряжением [tср]=750 кгс*см
Таким образом диаметр штифта удовлетворяет условиям прочности.
Проверка прочности шлицевого соединения
Условие прочности на смятие определяется по формуле (13) [5 с. 221]:
Мкр – крутящий момент на валу Н×см;
– диаметр вершин шлица см;
– диаметр впадин шлица см;
r – радиус скругления см [2 с.738];
[]см – допускаемое напряжение смятия для стали 45 без термообработки Н cм 2 [5 с.221].
Все результаты расчетов сведены в таблицу 6
Условие прочности выполняется следовательно прочность шлицевого соединения обеспечена.
Подбор подшипников качения.
По ГОСТ 8338-75 принимаем радиальный шариковый однорядный подшипник № 204205 и 206 средней серии [2с.145].
Расчёт шпоночных соединений
Для закрепления упругой втулочно-пальцевой муфты и зубчатые колеса на валу используем призматические шпонки по ГОСТ 23360-78.
Проверка прочности на смятие:
Для стандартной шпонки из углеродистой или легированной стали с твердостью ≤ НВ 240 допускаемое напряжение смятия: []cм =150 МПа [2с.736].
Мкр – крутящий момент
Заданному условию прочности удовлетворяет.
Так как привод коробки скоростей расположен в корпусе и работает в условиях средних скоростей и нагрузок смазка осуществляется из общей системы.
В качестве смазки применяем индустриальное масло общего назначения И - 20А по ГОСТ 20799-88
Анурьев В. И. Справочник конструктора-машиностроителя: Т2. – М.: Машиностроение 1992. – 784 с. ил.
Барановский Ю.В. Режимы резания металлов. – Москва Машиностроение 1972. – 407 с.
Кучер А.М. Киватицкий М.М. Покровский А.А. Металлорежущие станки. – Ленинград: Машиностроение 1972. – 300 с. ил.
Проников А.С. Расчёт и конструирование металлорежущих станков-М: Высшая школа 1962.-421 с.
Свирщевский Ю. И. Макейчик Н. Н. Расчет и конструирование коробок скоростей и подач – Минск издательство «Вышэйшая школа» 1976 г.
Петров Ю. В. Бургонова О. Ю. Кинематический расчет приводов подач универсальных металлорежущих станков – Омск издательство ОмГТУ 2000 г.
Петров Ю. В. Определение основных технических характеристик универсальных металлорежущих станков – Омск межвузовская типография ОмПИ 1990 г.
Справочник технолога машиностроителя Под ред. А.Г. Косиловой и Р.К. Мещерякова. 4-е изд. перераб. и доп. М.: Машиностроение 1985. Т. 2. 496 с.