Гидропривод бетоносмесительного ковша




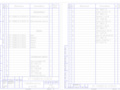
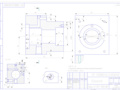
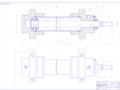
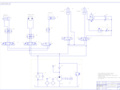
- Добавлен: 25.10.2022
- Размер: 1 MB
- Закачек: 0
Описание
Состав проекта
![]() |
![]() |
![]() ![]() ![]() ![]() |
![]() ![]() ![]() ![]() |
![]() ![]() ![]() ![]() |
![]() ![]() ![]() ![]() |
![]() ![]() ![]() ![]() |
![]() ![]() |
![]() ![]() |
![]() ![]() ![]() ![]() |
![]() ![]() ![]() ![]() |
![]() ![]() |
![]() ![]() |
![]() ![]() |
![]() ![]() |
![]() ![]() |
![]() ![]() ![]() ![]() |
![]() ![]() |
![]() ![]() ![]() ![]() |
![]() ![]() |
![]() |
![]() ![]() ![]() |
![]() ![]() ![]() |
![]() ![]() ![]() |
Дополнительная информация
ШТОК A3.dwg

Циклограмма A1.dwg

Циклограмма работы и
гистограмма расходов
Суммарная гистограмма расходов
Гидросхема моя A1.dwg

Схема изображена в исходном положении.
Напряжение электромагнитов 111 В.
Рабочая жидкость гидросистемы - масло ИГП-30
Смазочный материал системы импульсной смазки - масло И-30А
Поршень А4.dwg

Отливку выполнить по 3 кл. точности ГОСТ 1855-82
Не допускаются раковины
Отливку подвергнуть искусственному старению
Kryshka A3.dwg

Сталь 45 ГОСТ 1050-88
Спецификация цил.dwg

КП 1.150802.65.12.00.00 СК
Гидравлический цилиндр
КП 1.150802.65.12.00.00 ПЗ
Пояснительная записка
КП 1.150802.65.12.00.01
КП 1.150802.65.12.00.02
КП 1.150802.65.12.00.03
КП 1.150802.65.12.00.04
КП 1.150802.65.12.00.05
КП 1.150802.65.12.00.06
цилиндрA1.dwg

Цилиндр А3.dwg

Технические требования
Структурная схема МОЯ А1.dwg

list_zd.doc
федерального государственного автономного образовательного учреждения
высшего профессионального образования
«Казанский (Приволжский) федеральный университет»
Отделение энергетики и информатизации
Специальность 150802.65 «Гидравлические машины гидроприводы
и гидропневмоавтоматика»
(фамилия имя отчество)
Содержание расчётно-пояснительной записки (перечень подлежащих разработке вопросов)__Описание устройства; обзор научно-технической и патентной литературы; энергетический расчет; гидравлический расчет; тепловой расчет; энергетический расчет насосной установки; надежность гидропривода; расчет гидроцилиндра Ц5; заключение
Дата выдачи заданияЗадание выдал:
(Фамилия И.О. подпись)
(1) (Восстановлен).doc
Энергетический расчет
Выбор насосной установки
Расчет диаметров трубопроводов
Подбор гидроаппаратуры
Гидравлический расчет
Расчет цилиндра на прочность
Гидропривод – это совокупность устройств предназначенных для приведения в движение машин и механизмов посредством гидравлической энергии. Обязательными элементами гидропривода являются насос и гидродвигатель.
Гидропривод представляет собой своего рода "гидравлическую вставку" между приводным электродвигателем и нагрузкой (машиной и механизмом) и выполняет те же функции что и механическая передача (редуктор ременная передача кривошипно-шатунный механизм и т.д.). Основное назначение гидропривода как и механической передачи - преобразование механической характеристики приводного двигателя в соответствии с требованиями нагрузки (преобразование вида движения выходного звена двигателя его параметров а также регулирование защита от перегрузок и др.).
Приводным двигателем насоса могут быть электродвигатель дизель и другие поэтому иногда гидропривод называется соответственно электронасосный дизельнасосный и т.д.
К основным преимуществам гидропривода относятся: возможность универсального преобразования механической характеристики приводного двигателя в соответствии с требованиями нагрузки; простота управления и автоматизации; простота предохранения приводного двигателя и исполнительных органов машин от перегрузок; широкий диапазон бесступенчатого регулирования скорости выходного звена; большая передаваемая мощность на единицу массы привода; надежная смазка трущихся поверхностей при применении минеральных масел в качестве рабочих жидкостей.
К недостаткам гидропривода относятся: утечки рабочей жидкости через уплотнения и зазоры особенно при высоких значениях давления; нагрев рабочей жидкости что в ряде случаев требует применения специальных охладительных устройств и средств тепловой защиты; более низкий КПД (по приведенным выше причинам) чем у сопоставимых механических передач; необходимость обеспечения в процессе эксплуатации чистоты рабочей жидкости и защиты от проникновения в нее воздуха; пожароопасность в случае применения горючей рабочей жидкости.
При правильном выборе гидросхем и конструировании гидроузлов некоторые из перечисленных недостатков гидропривода можно устранить или значительно уменьшить их влияние на работу машин. Тогда преимущества гидропривода перед обычными механическими передачами становятся столь существенными что в большинстве случаев предпочтение отдается именно ему.
Сейчас трудно назвать область техники где бы ни использовался гидропривод. Эффективность большие технические возможности делают его почти универсальным средством при механизации и автоматизации различных технологических процессов. В частности в горной промышленности он используется в креплении подземных горных выработок: в очистных забоях применяются индивидуальные гидравлические стойки и гидравлические комплексы выполняющие основные и вспомогательные операции по передвижке как самих крепей так и другого механического оборудования в лаве; широко применяются крепи сопряжения горных выработок. Практически все комбайны для ведения очистных и нарезных работ проведения подготовительных выработок имеют гидропривода подачи исполнительного органа на забой и механизмов для выполнения различных вспомогательных операций. Гидропривод является неотъемлемым элементом буровых установок. Большинство приводов шахтных конвейеров снабжено гидродинамическими муфтами. [1]
Объемный гидропривод сегодня широко применяется в машиностроении и стал неотъемлемой составной частью современных мобильных машин и промышленного оборудования. В технически развитых странах машину без гидропривода встретить почти невозможно. В России ситуация иная – здесь редкость отечественное оборудование с современным гидроприводом.
Рисунок 1 – Преобразование крутящего момента
За что же так ценят в современном мире гидропривод? Прежде всего это наиболее простое преобразование крутящего момента первичного источника механической энергии (двигателя внутреннего сгорания – ДВС или электродвигателя) и передача гидравлической мощности гидродвигателям. Гидродвигатели преобразуют энергию потока рабочей жидкости (РЖ) в энергию выходного звена и передают ее исполнительным механизмам. Исполнительными механизмами в передаче энергии являются гидроцилиндры и гидромоторы. Первые служат для создания силы при возвратно-поступательном движении штоков вторые – для создания крутящего момента на валу при вращательном движении.
Гидропривод дает возможность бесступенчато регулировать скорость движения и частоту вращения приводного ДВС максимально использовать его мощность повышать коэффициент использования улучшать эксплуатационные качества машины. Небольшая инерционность обеспечивает хорошие динамические свойства привода позволяет сократить время рабочего цикла и повысить производительность машины. В гидроприводе с высокомоментными гидромоторами передаточное число достигает 1000 и более т. е. имеется возможность реализации больших передаточных чисел.
Легкость и удобство управления рабочими органами которые характеризуются небольшими усилиями на рукоятках управления создают комфортные условия труда машиниста. Применение направляющих распределителей с пропорциональным электрогидравлическим управлением исполнительными механизмами и регулирующих гидроаппаратов управляющих давлением и расходом с пропорциональными электромагнитами позволяет автоматизировать технологические процессы выполняемые машинами. При установке микропроцессоров и подключении их к компонентам с пропорциональными электромагнитами можно автоматизировать рабочий цикл или весь технологический процесс выполняемый машиной. Перед переходом на автоматическое управление оператор нажимает кнопку «памяти» и выполняет необходимую технологическую операцию вручную. Затем он включает кнопку «автоматический режим» и процессор по заданному алгоритму будет повторять этот режим работы. Машина в таких случаях работает с максимальной производительностью а роль оператора ограничивается наблюдением.
Рисунок 2 – Рабочий орган клапана
Независимое расположение сборочных единиц гидропривода позволяет оптимально разместить их в машине. Надежно предохраняют от перегрузок приводного двигателя гидросистемы металлоконструкций и рабочих
органов клапаны предохранительные переливные разгрузочные разности давлений тормозные и др. а также блоки клапанов. Пожалуй это наиболее важное свойство объемного гидропривода. Компоненты гидропривода компактны у них небольшая масса благодаря отсутствию в машине с гидроприводом таких традиционно применяемых деталей и механических узлов как шестеренные и цепные редукторы муфты тормоза барабаны лебедок полиспастные блоки канаты и другие быстро изнашивающиеся детали требующие регулярного техобслуживания. У объемного гидропривода есть и недостатки например его работоспособность и безотказность зависят от температуры окружающей среды точнее – от вязкости и других свойств рабочей жидкости.
По характеру движения выходного звена различают объемные гидроприводы вращательного поступательного и поворотного движения приводимые гидромотором гидроцилиндром или поворотным гидродвигателем. По возможности регулирования различают гидроприводы регулируемые и нерегулируемые по способу регулирования – с ручным и автоматическим управлением. В регулируемом гидроприводе скорость выходного вала может меняться.
Принцип действия гидропривода основан на законе Паскаля согласно которому внешнее давление Р возникающее в результате воздействия на свободную поверхность жидкости находящейся в замкнутом объеме передается равномерно во все стороны. Значение давления зависит от величины силы F направленной перпендикулярно поверхности поршня S на которую действует сила:
Если к сосуду с замкнутым объемом жидкости присоединить второй сосуд посредством трубы то в соответствии с этим законом давление Р будет передаваться во второй сосуд и создавать усилие F на его стенки. Таким образом в гидроприводе происходит передача усилия по трубопроводу на расстояние. В качестве примера на рис. 1 изображены два сосуда закрытых поршнями 1 и 2 и соединенных трубопроводом 3. Сила F1 действующая на поршень 1 площадью S1 создает в системе давление
Рисунок 3 - Гидросистема
Чтобы уравновесить это давление во втором сосуде к поршню 2 надо приложить усилие F2 = PS2. Приравняв значения давления в уравнениях (1) и (2) получаем:
Из уравнения (3) следует что усилия на поршнях прямо пропорциональны их площадям а перемещения l1 и l2 обоих поршней обратно пропорциональны их площадям т. е. соблюдается «закон рычага» – выигрывая в силе в таком же отношении проигрываем в расстоянии но можно получить значительный выигрыш в силе. Это поясняет одно из важнейших преимуществ гидропривода – способность передавать большую мощность при небольших размерах привода. Однако перемещая поршень 1 на расстояние l1 вытесняем из него объем жидкости
Этот же объем жидкости (если считать что рабочая жидкость практически несжимаема) поступает во второй сосуд и перемещает поршень 2 на расстояние
Из уравнений (4) и (5) получаем:
Подставив это отношение в уравнение (3) получаем:
Уравнение (6) аналогично уравнению рычага 1-го рода. Это наглядно показано на схеме рис. 1 б. C помощью гидравлического рычага можно получить передаточные отношения больше в 10 50 и более раз чем при помощи механического рычага.
Примером простейшей гидравлической системы является гидродомкрат. Для того чтобы поднять груз F2 в системе нужно создать давление Р = F2S2 при усилии F1 на поршне 2 в соответствии с уравнением (3). Поскольку поршни круглого сечения то
где d1 и d2 – диаметры соответствующих поршней.
Рисунок 4 - Гидросхема
В современном гидроприводе источником энергии создающим движение РЖ являются насосы приводимые от ДВС (преимущественно в мобильных машинах) или от электродвигателя (в стационарных промышленных установках). В зависимости от циркуляции РЖ гидравлические схемы подразделяются на разомкнутые и замкнутые. На рис. 2 приведены примеры наиболее часто применяемых принципиальных гидравлических схем с разомкнутым (рис. 2 а) и замкнутым (рис. 2 б) потоками.В разомкнутой (открытой) схеме гидроприводав рабочей позиции трехпозиционного распределителя 4 насос 2 всасывает РЖ из бака 1 гидросистемы и под давлением нагнетает ее в регулируемый гидромотор 5. Совершив полезную работу РЖ возвращается в бак.
При перемещении золотника распределителя в обратную рабочую позицию меняется направление потока РЖ и соответственно направление движения штока цилиндра или направление вращения выходного вала гидромотора. В средней (нейтральной позиции) распределитель 4 с ручным управлением соединяет насос с баком гидросистемы обеспечивая разгрузку насоса от давления. В нерегулируемых гидромашинах скорость перемещения штока гидроцилиндра или частота вращения вала гидромотора регулируется дросселированием потока РЖ в распределителе или с помощью регуляторов потока.
В замкнутой (закрытой) схеме гидроприводаРЖ нагнетается насосом в гидродвигатель а оттуда возвращается непосредственно во всасывающую полость насоса минуя бак. В гидроприводе с регулируемыми насосом и гидромотором направление и скорость вращения исполнительного механизма регулируются изменением рабочих объемов насоса или гидромотора или одновременно того и другого. В связи с объемными потерями в насосе и в гидромоторе во всасывающую гидролинию насоса РЖ поступает меньше на величину утечек отводимых в бак по дренажной гидролинии. Для компенсации утечек РЖ в гидропередаче с замкнутым потоком устанавливают насос подпитки 7 который под давлением 07 15 МПа нагнетает РЖ в гидролинию низкого давления. Давление в гидролинии подпитки определяется настройкой переливного клапана 10.
Под действием разности давлений в рабочих гидролиниях насоса 2 распределительный золотник 9 с гидравлическим управлением перемещается в положение при котором гидролиния низкого давления соединяется с переливным клапаном. Таким образом осуществляется постоянный обмен РЖ в замкнутом контуре и ее охлаждение. Предохранительные клапаны 3 позволяют перепускать рабочую жидкость из гидролинии высокого давления в гидролинию низкого давления и снижать динамические нагрузки при разгоне и торможении рабочего органа или ходового механизма машины. РЖ от насоса подпитки 7 поступает через фильтр 6 и один из обратных клапанов 8 в гидролинию низкого давления насоса 2 а ее избыток поступает на слив через распределительный золотник 9 и переливной клапан 10 в бак.
Рисунок 5 – Подача насоса системы подпитки
Преимущества гидропривода с замкнутым потоком
Значительно меньше объем РЖ так как потребность в ней определяется рабочими объемами гидромоторов а размеры бака выбирают исходя из подачи
насоса системы подпитки компенсирующей объемные потери насоса и гидромотора.
Избыточное давление на входе в насос обеспечивает его работу при максимальной частоте вращения что позволяет применить насос меньшего рабочего объема (т. е. меньших типоразмера массы и стоимости) и использовать объемный гидропривод в условиях холодного климата на масле МГ-15В. Кроме того избыточное давление на входе в основной насос позволяет запускать в работу машину при температуре масла МГ-15В ниже –40 °С без разогрева РЖ.
Отсутствует контакт РЖ с окружающей средой что исключает загрязнение гидросистемы увеличивает ресурс гидропривода и периодичность замены РЖ.
Регулируемые реверсивные аксиально-поршневые насосы гидроприводов с замкнутым потоком позволяют менять направление вращения вала гидромотора без золотниковых распределителей обычно используемых для этой цели в гидроприводах с разомкнутым потоком и за счет этого повысить КПД гидропривода.
Гидроприводы с замкнутым потоком все больше применяют для исполнительных механизмов вращательного движения например смесительного барабана автобетоносмесителя привода лебедок автокранов в буровых и колтюбинговых установках для кислотной промывки нефтяных скважин в агрегатах для ремонта и освоения скважин в трубоукладчиках для привода подъемников в самоходных катках и др. Особенно эффективно применение гидроприводов с замкнутым потоком в пневмоколесных машинах в том числе с шарнирно-сочлененной рамой для привода ходовых механизмов с двумя или четырьмя активными колесами в условиях бездорожья.
Современные гидроприводы пневмоколесных машин оснащают электронной системой синхронизации (рис. 3) включающей функцию «гидравлического дифференциала». Максимальный крутящий момент передаваемый от насоса на ведущие колеса определяется степенью сцепления колес с грунтом. В случае слабого сцепления происходит потеря управляемости а значит преждевременно изнашиваются шины расходуется лишнее топливо повреждается верхний слой почвы. Электронная система синхронизации гидропривода отслеживает сцепление колеса с грунтом и перераспределяет крутящий момент между ведущими колесами. Синхронизацию гидропривода осуществляют бортовой компьютер 1 сдвоенный регулирующий клапан 2 датчик 3 положения руля (установлен в корпусе колонки рулевого управления) и датчики 4 частоты вращения приводных колес. Частота вращения каждого приводного колеса непрерывно измеряется цифровыми датчиками установленными в задних крышках гидромоторов.
Бортовой компьютер сравнивает полученные значения и ограничивает при необходимости через регулирующий клапан подачу РЖ в «проскользнувшее» колесо которое начинает вращаться с большей скоростью. При стандартной электронной системе синхронизации на два приводных колеса в подводящем трубопроводе устанавливают один сдвоенный регулирующий клапан который уменьшает расход РЖ и одновременно повышает давление насоса и в гидромоторе. Это обеспечивает устойчивое передвижение машины и предотвращает пробуксовку колеса. Как только частота вращения всех колес станет одинаковой двойной регулирующий клапан снова полностью откроется но он вновь закроется если возникнет разность в частоте вращения колес. Этот процесс происходит непрерывно чтобы обеспечить параметры предусмотренные конструкцией машины.
Применение гидропривода с замкнутым потоком в мобильной машине исключает необходимость в традиционных узлах и агрегатах – муфтах сцепления коробках передач карданных валах тормозах (кроме стояночных) так как гидропривод выполняет функции тормозов и «гидравлического дифференциала».
Чтобы обеспечить надежную эксплуатацию оборудования с гидроприводом в климатических условиях России для объемных гидроприводов созданы специальные гидравлические масла основными производителями которых являются Ново-Уфимский и Волгоградский нефтеперерабатывающие заводы а также ПО «Омскнефтеоргсинтез». Согласно ГОСТу в гидроприводах используют два типа масел: МГ-15В и МГЕ-46В. МГ-15В (аналог ВМГЗ) для северных регионов страны рекомендуется как всесезонное а для средней полосы России – как зимнее. Оно вырабатывается на загущенной основе с композицией присадок обеспечивающих необходимые вязкостные низкотемпературные и антипенные свойства. Это масло позволяет работать с гидроприводами без предварительного разогрева и круглогодично эксплуатировать гидроприводные машины без сезонной смены масла в интервале температур –53 +53 °С. Гидравлическое масло МГЕ-46В (аналог МГ-30) предназначено в качестве летнего для эксплуатации гидроприводов мобильных машин и промышленного оборудования на открытом воздухе в районах с умеренным климатом и как всесезонное для районов с теплым климатом. Его используют в интервале температур –20 +75 °С а вырабатывают из нефти селективной очисткой с добавлением антиокислительной антипенной присадок и депрессатора понижающего температуру застывания. МГЕ-46В отличается хорошей смазывающей способностью стойкостью против окисления и отложения смолистых осадков а также против вспенивания.
Рисунок 6 – Гидропривод с замкнутым потоком
Недостатки гидропривода с замкнутым потоком
Ограниченность применения (в основном в механизмах вращательного движения и в редких случаях в механизмах возвратно-поступательного движения с гидроцилиндрами с двусторонним штоком). У гидроприводов с разомкнутым потоком таких ограничений нет.
Необходимость применения воздушно-масляных теплообменников (при подтверждении тепловым расчетом) в связи с ограниченным теплоотводом между гидропередачей и окружающей средой.
Периодичность замены основных сортов гидравлических масел – 3500 4000 ч но не реже 1 раза в 2 года. При отсутствии основных сортов гидравлических масел допускается их сезонная замена: зимой МГ-22А летом И-30А.
Надежная и длительная эксплуатация насосов гидромоторов и других компонентов гидропривода возможна только при условии обеспечения эффективной фильтрации рабочей жидкости от механических примесей и влаги. Очистка РЖ должна соответствовать 1915 классу по нормам ISO 4406 или эквивалентна 13 15-му классу чистоты по ГОСТ 17216–2001. При этом абсолютная тонкость фильтрации 25 мкм. Для гидроприводов с повышенными требованиями к надежности и долговечности необходима фильтрация РЖ до 1613 класса по нормам ISO 4406 или эквивалентная 11-му классу чистоты по ГОСТ 17216–2001. Абсолютная тонкость фильтрации 10 мкм.
Сегодня на российский рынок из-за рубежа поставляется широкая номенклатура современных компонентов гидропривода. Отдельные детали или агрегаты можно использовать не только для восстановления изношенных узлов и агрегатов но и самостоятельно собирать гидравлические устройства достаточно хорошего качества. Небольшой сборочный цех из нескольких человек позволяет решить немало внутрихозяйственных проблем. [2]
Рисунок 7 – Компонент гидропривода
1 (19)SU(11) 1395858 A1
(46) 15.05.88 Бюл. №18
(72) И.Х. Гетерман В.С. Зубарев В.Ю. Мордакович Ш.Р. Булиман
(56) Авторское свидетельство СССР № 1090935 Кл. F 15 B 1104 1982.
(54) Гидравлическое тормозное устройство
(57) Цель изобретения повышение надежности устройства.
2 (19)SU(11) 1483120 A1
(46) 30.05.89 Бюл № 26
(72) Б.В. Савельев и В.В. Голынный
(56) Патент США № 4397218 кл. 91-26 1983
(54) Тормозное устройство силового привода
(57) Изобретение относится к машиностроению и может быть использовано для силового цилиндра с устройством для автоматического торможения в конце хода. Целью изобретения является уменьшение габаритов. С указанной целью запорный орган отсечного и обратного клапанов тормозного устройства с подпружиненным упором размещенным на крыше силового силового цилиндра выполнен в виде втулки с фланцем подпружиненным относительно корпуса устройства.
3 (19)SU(11) 1707302 A1
(46) 21.01.92. Бюл. №3
(71) Минский завод «ударник»
(72) Г.Г Сумцов Л.А. Шаченюк
(53) Авторское свидетельство СССР
№ 13773912 Кл. F 15 B 1522 1986
(57) Изобретение относится к машиностроительному гироприводу и может быть использовано в гидравлических системах транспортно-погрузочных устройств. Цель изобретения – расширение функциональных возможностей привода.
4 (19)SU(11) 1353957 A1
(46) 23.11.87. Бюл. №43
(56) Попов Д.В. Динамика и регулирование гидропневмосистем 1977
(54) Гидравлический исполнительный механизм
(57) Изобретение используется в системах управления и регулирования. Цель изобретения – повышение демпфирующих свойст механизма.
5 (19)SU(11) 1291736 A1
(46) 23.02.86. Бюл. №7
(54) ГИДРАВЛИЧЕСКОЕ ТОРМОЗНОЕ УСТРОЙСТВО
(57) Целью изобретения является уменьшение габаритов
6 (19)SU(11) 1395858 A1
(46) 15.05.88. Бюл. №18
(72) И.В. Гетерман В.С. Зубарев
(56) Авторское свидетельство СССР Кл. F 15 B 1104 1082
7 (19)SU(11) 1652686 A1
(46) 30.05.91. Бюл№ 20
(71) Смоленский авиационный завод
(56) Авторское свидетельство СССР
№ 779668 кл. F 15 B 1522 1978.
(54) Гидравлический тормозной цилиндр
(57) Изобретение относится к машиностроению в частности к объемному гидроприводу и может быть использовано в тормозных устройствах например гидросистем подачи инструмента. Целью изобретения является расширение функциональных возможностей путем регулирования протяженности зоны взаимодействия поршня с отверстием в стенках корпуса. В корпусе размещен поршень и шток. Полости сообщены каналами причем в последних установлены обратные клапаны и дроссели. На боковых поверхностях поршня выполнены сообщенные с полостью карманы имеющие на развертке например треугольную форму. Шток снабжен рычагом с фиксатором взаимодействующим с пазами на корпусе. Когда поршень не перекрывает отверстия в стенке корпуса каналы шунтируют дроссели. Тормозное усилие на штоке мало и осуществляется движение с повышенной скоростью.
1 ЭНЕРГЕТИЧЕСКИЙ РАСЧЕТ ГИДРОЦИЛИНДРА ВЫДВИЖЕНИЯ ПОДВОД ИНСТРУМЕНТА Ц1
Статическая нагрузка на выходное звено Hс1 = 1001 H
Полное перемещение выходного звена Lп1 = 164 мм
Время перемещения выходного звена tп1 = 2 с
Приведенная к выходному звену масса mв1 = 15 кг
Номинальное давление Рном1 = 4 МПа
Определяем максимальную скорость перемещения выходного звена
Определяем значение показателя вида нагрузки н используя формулу:
Оптимальная предельная скорость выходного звена:
Ускорение выходного звена:
Полная внешняя нагрузка на выходном звене:
Предельная мощность на выходном звене:
Для определения удельного рабочего объема гидроцилиндра qп3 необходимо знать значения номинального давления механического КПД гидроцилиндра и гидравлического КПД линий и гидроаппаратов.
Значение номинального давления принимаем равным:
Значение механического КПД дм для гидроцилиндров с эластичным уплотнением составляет 085 - 095.
Значение гидравлического КПД га гидролиний и аппаратов составляет 075 09.
Тогда определяем удельный рабочий объем гидроцилиндра:
Вычисляем диаметр поршня гидроцилиндра:
Примем ближайшее большее стандартное значение диаметра поршня:
Примем стандартное значение диаметра штока гидроцилиндра:
Уточняем значение удельного рабочего объема:
Уточняем значение гидравлического КПД гидролиний и аппаратов:
Коэффициент соотношения эффективных площадей:
Окончательные параметры механизма:
Диаметр поршня 22 мм;
Коэффициент соотношения эффективных площадей
Гидравлический КПД гидролиний и аппаратов 0728
2 ЭНЕРГЕТИЧЕСКИЙ РАСЧЕТ ГИДРОМОТОРА ПОВОРОТА КОВША М
Крутящий момент на выходном звене Мкр = 2101 H·м
Шаговое перемещение выходного звена Lш = 026 рад
Шаговое время перемещения tш = 05 с
Приведенный к выходному звену момент
инерции J = 150 кг·м2
Номинальное давление Рном = 4 МПа
Для определения удельного рабочего объема гидроцилиндра qп необходимо знать значения номинального давления механического КПД гидроцилиндра и гидравлического КПД линий и гидроаппаратов.
Значение механического КПД дм для гидромоторов с эластичным уплотнением составляет 085 - 095.
Тогда определяем удельный рабочий объем гидромотора:
Вычисляем объем гидромотора:
Примем ближайшее большее стандартное значение объема гидромотора
Объем гидромотора 71 л
Шаговое перемещение 026 рад
Гидравлический КПД гидролиний и аппаратов
3 ЭНЕРГЕТИЧЕСКИЙ РАСЧЕТ ГИДРОЦИЛИНДРА ПОДВОД КОВША Ц2
Статическая нагрузка на выходное звено Hс2 = 800 H
Полное перемещение выходного звена Lп2 = 60 мм
Время перемещения выходного звена tп2 = 1 с
Приведенная к выходному звену масса mв2 = 12 кг
Номинальное давление Рном2 = 4 МПа
Для определения удельного рабочего объема гидроцилиндра qп4 необходимо знать значения номинального давления механического КПД гидроцилиндра и гидравлического КПД линий и гидроаппаратов.
Примем усилие пружины:
Учитывая усилие пружины определяем удельный рабочий объем гидроцилиндра:
Примем ближайшее большее стандартное значение диаметра поршня
Примем диаметр штока гидроцилиндра:
Диаметр поршня 32 мм;
Диаметр штока 16 мм;
Гидравлический КПД гидролиний и аппаратов 0734
4 ЭНЕРГЕТИЧЕСКИЙ РАСЧЕТ ГИДРОЦИЛИНДРА ЗАЖИМА КОВША Ц3
Статическая нагрузка на выходное звено Hс3 = 2600 H
Полное перемещение выходного звена Lп3 = 10 мм
Время перемещения выходного звена tп3 = 1 с
Приведенная к выходному звену масса mв3 = 200 кг
Номинальное давление Рном3 = 4 МПа
По графику vnср() [4]
Для определения удельного рабочего объема гидроцилиндра qп1 необходимо знать значения номинального давления механического КПД гидроцилиндра и гидравлического КПД линий и гидроаппаратов.
Учитывая противодавление в штоковой полости гидроцилиндра определяем удельный рабочий объем гидроцилиндра:
Так как у дифференциальных гидроцилиндров удельный рабочий объем штоковой полости в два раза меньше удельного рабочего объема поршневой полости то определяем удельный рабочий объем штоковой полости:
Вычисляем диаметр штока гидроцилиндра:
Примем стандартное значение диаметра штока:
Диаметр поршня 50 мм;
Диаметр штока 36 мм;
Коэффициент соотношения эффективных площадей 0975
Гидравлический КПД гидролиний и аппаратов 0701
5 ЭНЕРГЕТИЧЕСКИЙ РАСЧЕТ ГИДРОЦИЛИНДРА ПОДЪЕМ КОВША Ц4
Статическая нагрузка на выходное звено Hс4 = 2600 H
Внешняя нагрузка на поршень при рабочем ходе Нм4 = 4100 Н
Перемещение поршня при быстром подводе Lп4 = 110 мм
Перемещение поршня при рабочем ходе Lм4 = 45 мм
Скорость движения поршня при рабочем ходе .Vм4 = 10 ммс
Полное время цикла работы привода tц4 = 25 с
время выстоя поршня в исходном положении tв4 = 15 с
Приведенная к выходному звену масса mв4 = 150 кг
Номинальное давление Рном4 = 4 МПа
Первичный коэффициент асимметрии полостей
Время перемещения штока цилиндра при рабочем ходе:
Время перемещения штока цилиндра при быстром подводе:
Время перемещения штока цилиндра при быстром отводе:
Предельная скорость штока цилиндра при быстром подводе:
Предельная мощность на выходном звене при рабочем ходе:
Для определения удельного рабочего объема гидроцилиндра qп2 необходимо знать значения номинального давления механического КПД гидроцилиндра и гидравлического КПД линий и гидроаппаратов.
Так как полная нагрузка на выходном звене при рабочем ходе превышает полную нагрузку при быстром подводе то удельный рабочий объем гидроцилиндра будем находить исходя из полной нагрузки при рабочем ходе:
Диаметр поршня 45 мм;
Диаметр штока 25 мм;
Коэффициент соотношения эффективных площадей 069
Гидравлический КПД гидролиний и аппаратов 0739
Сводная таблица значений расчетов
Статическая нагрузка на выходное звено Hс (H)
Полное перемещение выходного звена Lп (мм)
Время перемещения выходного звена tп (с)
Приведенная к выходному звену масса mв (кг)
Номинальное давление Рном (МПа)
максимальную скорость перемещения выходного звена Vmax (мс)
Оптимальная предельная скорость выходного звена Vп (мс)
Полная внешняя нагрузка на выходном звене Нв (Н)
Предельная мощность на выходном звене Nв (Вт)
диаметра поршня dп (мм)
диаметра штока dш (мм)
Внешняя нагрузка на поршень при рабочем ходе Нм (Н)
Перемещение поршня при быстром подводе Lм (мм)
Скорость движения поршня при рабочем ходе Vм (ммс)
Полное время цикла работы привода tц (с)
время выстоя поршня в исходном положении tв (с)
Время перемещения штока цилиндра при рабочем ходе tм (с)
Время перемещения штока цилиндра при быстром подводе tп (с)
Время перемещения штока цилиндра при быстром отводе tн (с)
Предельная скорость штока цилиндра при быстром подводе Vп (мс)
После проведения энергетического расчета и определения типоразмеров исполнительных механизмов рассчитаем расходы требуемые данным механизмам для обеспечения заданного цикла работы и вытесняемые расходы необходимые в дальнейшем при расчете диаметров трубопроводов и проведении гидравлического расчета. Составление гистограммы расходов позволит подобрать насосную установку.
1 РАСЧЕТ РАСХОДОВ ГИДРОЦИЛИНДРА ПОДВОД КОВША Ц1
q ц1 = 00037 удельный рабочий объем гидроцилиндра м2;
v пр.х 1 = 0084 оптимальная скорость прямого хода мс;
v обр.х 1 = 00858 оптимальная скорость обратного хода мс;
= 092 коэффициент асимметрии рабочих камер гидродвигателя
ц.об1 = 082 объемный к.п.д. гидроцилиндра;
Потребляемый расход при прямом ходе:
Пересчитаем м3с в лмин.:
Q пр3 = 17·10-4·60·1000 = 88 лм
Вытесняемый расход при прямом ходе:
Q выт.пр.х1 = 15·10-4·60·1000 = 938 лм
Потребляемый расход при обратном ходе:
Q обр.х1 = 8057·10-5·60·1000 = 4834 лм
Вытесняемый расход при обратном ходе:
Q выт.обр.х1 = 1074·10-4·60·1000 = 6445 лм
2 РАСЧЕТ РАСХОДОВ ГИДРОМОТОРА ПОВОРОТА КОВША М
= 71·10-3 м3 объем гидромотора
n = 5 частота вращения гидромотора
об = 075 объемный к.п.д. гидромотора
Потребляемый расход:
Пересчитаем м3с в лм:
Q пр = 47·10-5·60·1000 = 28399 лм
3 РАСЧЕТ РАСХОДОВ ГИДРОЦИЛИНДРА ПОДВОД КОВША Ц2
q ц2 = 0008 удельный рабочий объем гидроцилиндра м2;
v пр.х 2 = 01368 оптимальная скорость прямого хода мс;
v обр.х 2 = 01368 оптимальная скорость обратного хода мс;
ц.об2 = 075 объемный к.п.д. гидроцилиндра;
Q пр2 = 1671·10-3·60·1000 = 875 лм
На основании циклограммы перемещений и полученных расходов строим гистограмму расходов.
4 РАСЧЕТ РАСХОДОВ ГИДРОЦИЛИНДРА ЗАЖИМА КОВША Ц3
q ц3 = 000183 удельный рабочий объем гидроцилиндра м2;
v пр.х 3 = 00126 оптимальная скорость прямого хода мс;
v обр.х 3 = 00126 оптимальная скорость обратного хода мс;
= 05 коэффициент асимметрии рабочих камер гидродвигателя
ц.об3. = 099 объемный к.п.д. гидроцилиндра;
Q пр3 = 328*10-5·60·1000 = 2 лм
Q выт.пр.х3 = 164·10-5·60·1000 = 1 лм
Q обр.х3 = 164·10-5·60·1000 = 1 лм
Q выт.обр.х3 = 328·10-5·60·1000 = 2 лм
5 РАСЧЕТ РАСХОДОВ ГИДРОЦИЛИНДРА ПОДЪЕМА КОВША Ц4
q ц4 = 00016 удельный рабочий объем гидроцилиндра м2;
v пр.х 4 = 005142 оптимальная скорость прямого хода мс;
v р.х 4 = 001 оптимальная скорость рабочего хода мс;
v обр.х 4 = 006030 оптимальная скорость обратного хода мс;
= 069 коэффициент асимметрии рабочих камер гидродвигателя
Q пр4 = 109·10-4·60·1000 = 658 лм
Q выт.пр.х2 = 7521·10-5·60·1000 = 4516 лм
Потребляемый расход при рабочем ходе:
Q р4 = 21·10-5·60·1000 = 127 лм
Вытесняемый расход при рабочем ходе:
Q выт.р.х4 = 1488·10-5·60·1000 = 0893 лм
Q обр.х4 = 887·10-5·60·1000 = 5257 лм
Q выт.обр.х4 = 1182·10-4·60·1000 = 7096 лм
На основании полученной в п.2 гистограммы расходов выберем насос. С учетом необходимости обеспечения требуемых значений расхода и давления выберем насос НПл 1663.
Его технические характеристики:
- рабочий объем 16 см3;
- номинальная подача 127 лмин;
- номинальное рабочее давление 63 МПа.
Для обеспечения необходимой чистоты рабочей жидкости установим в системе сливной фильтр АС42-53 ТУ2-053-1614-82.
Его технические данные:
- диаметр условного прохода 20 мм;
- номинальное рабочее давление 063 МПа;
- номинальная пропускная способность 16 лмин;
- тонкость фильтрации 40 мкм;
Для предотвращения аварийной ситуации при чрезмерном повышении давления установим в систему дополнительно предохранительный клапан Г54 -32М ТУ 2 – 053 – 1628 – 83. Его технические данные:
- диаметр условного прохода 10 мм;
- номинальное давление 20 МПа;
- диапазон регулировки давления 1 – 20 МПа;
- номинальный расход 32 лмин;
Для предотвращения обратного потока рабочей жидкости через насос при отключении станка и с учетом того что расход в системе будет отрегулирован приблизительно до 127 лмин установим на напорной линии обратный клапан Г 51 -31 ТУ 2 – 053 – 1649 – 83.
- диаметр условного прохода 8 мм;
- номинальный расход 16 лмин;
Рассчитаем мощность приводного двигателя по формуле:
где: N – мощность приводного двигателя кВт;
Р – давление в системе МПа;
Q – максимальный расход в гидросистеме лмин;
= 07 полный к.п.д. насоса по паспорту;
Выберем для расчета самый нагруженный режим – выдвижение цилиндра выдвижения устройства подачи.
Ближайший по мощности электродвигатель - АИР 80А4 11 кВт 1500 обмин.
Определим необходимый объем гидробака из ряда рекомендуемых объемов с учетом того что следует избегать чрезмерного падения уровня масла в баке при перемещении механизмов.
где: Vб – объем гидробака литр;
Vб = (3 – 7) Q max = (3 – 7)·127 = 381 – 889 = -508 л
Выберем гидробак объемом 63 л.
Расчет трубопроводов рассмотрим на примере гидроцилиндра поворота стола Ц2.
Начнем расчет для быстрого подвода гидроцилиндра. Расход прямого хода Q п.х составляет 102·10-4 м3с давление в гидросистеме до 63 МПа следовательно максимальная рекомендуемая скорость жидкости в трубопроводе 32 мс минимальную скорость жидкости в трубопроводе назначим 2 мс. Тогда внутренний диаметр трубопровода будет находиться в пределах:
Минимальный диаметр:
Максимальный диаметр:
Примем для сливной магистрали рекомендуемую скорость жидкости в трубопроводе 1 – 2 мс Q выт.п.х составляет 7649·10-5 м3с тогда внутренний диаметр трубопровода будет находиться в пределах:
Определим диаметры трубопроводов при рабочем ходе. Расход рабочего хода Qр.х составляет 1983·10-5 м3с
Для напорной магистрали:
Максимальный диаметр
Примем для сливной магистрали рекомендуемую скорость жидкости в трубопроводе 1 – 2 мс Q выт.р.х составляет 1488·10-5 м3с тогда внутренний диаметр трубопровода будет находиться в пределах:
Определим диаметры трубопроводов при обратном ходе. Расход обратного хода Qобр.х составляет 8974·10-5 м3с
Примем для сливной магистрали рекомендуемую скорость жидкости в трубопроводе 1 – 2 мс Q выт.обр.х составляет 1197·10-4 м3с тогда внутренний диаметр трубопровода будет находиться в пределах:
Выберем трубу с внутренним диаметром 8 мм.
Уточняем толщину стенки примем для всех трубопроводов рабочее давление соответствующим максимальному давлению в гидросистеме то есть 4 МПа:
Так как расчетная толщина стенки меньше чем у выбранного трубопровода будем считать что труба определена правильно.
По полученным результатам и с учетом уменьшения номенклатуры применяемых материалов выберем трубу 10 1 по ГОСТ 8734-75.
Расчет остальных трубопроводов будем производить аналогичным образом данные для расчета и результаты приведены в таблице 4.1.
Таблица 4.1 Данные для расчета и результаты расчетов трубопроводов.
Подбор гидроаппаратуры
Выбор гидроаппаратов будем производить в соответствии с расходом и давлением в каждой конкретной части гидросистемы.
Начнем с системы гидроцилиндра зажима ковша Ц1. Необходимые требования:
- давление в системе 4 МПа;
Выберем гидрораспределитель ВЕ6 573 Г110 ТУ2-053-1815-86. Его технические характеристики:
- диаметр условного прохода 6 мм;
- номинальный расход 125 лмин;
- номинальное давление 32 МПа.
Рассмотрим систему гидроцилиндра поворота стола Ц2. Необходимые требования:
Выберем гидрораспределитель 1РЕ 10.574А Г100 ТУ2-053-1815-86. Его технические характеристики:
- номинальный расход 25 лмин;
- номинальное давление 320 МПа.
Выберем также гидрораспределитель 1Р МР 10 ТУ 2-053-1815-86. Его технические характеристики:
Для обеспечения регулировки скорости движения цилиндра при быстром подводе выберем дроссель МПГ 55-12 М ТУ 2-053-1790-86. Его технические характеристики:
- номинальное давление 20 МПа.
Для обеспечения регулировки скорости движения цилиндра при рабочем ходе применим регулятор расхода МПГ 55-32 М ТУ 2-053-1790-86. Его технические характеристики:
Для обеспечения расхода жидкости через регулятор расхода при рабочем ходе применим обратный клапан Г51-32 ТУ 2-053-1649-83. Его технические характеристики:
- номинальный расход 32 лмин.
Рассмотрим систему гидроцилиндра выдвижения устройства подачи Ц3. Необходимые требования:
- давление в системе 4 МПа.
Выберем гидрораспределитель 1РЕ 10.44 Г110 ТУ2-053-1815-86. Его технические характеристики:
Для обеспечения регулировки скорости движения цилиндра в обе стороны и с учетом минимизации размеров гидростанции выберем сдвоенный дроссель с обратным клапаном модульного исполнения ДКМ 63 ТУ 2 – 053 – 1799- 83. Его технические характеристики:
- диапазон регулировки расхода 0 - 125 лмин;
Рассмотрим систему гидромотора поворота магазина ГМ. Необходимые требования:
Выберем гидрораспределитель ВЕ 6.44А Г110 ТУ2-053-1815-86. Его технические характеристики:
Для обеспечения регулировки скорости движения цилиндра в обе стороны и с учетом минимизации размеров гидростанции выберем сдвоенный дроссель с обратным клапаном модульного исполнения ДКМ 63 ТУ 2 – 053 – 1397- 78. Его технические характеристики:
Для предотвращения перегрузки гидромотора предусмотрим предохранительные клапаны для перелива жидкости из напорной линии в сливную. Применим клапан Г54-32М ТУ 2-053-1628-83. Его технические характеристики:
- диапазон регулировки давления 0-20 МПа;
Рассмотрим систему гидроцилиндра поворота стола Ц4. Необходимые требования:
- расход 10023 лмин;
Выберем гидрораспределитель 1РЕ 10.573 Г110 ТУ2-053-1815-86. Его технические характеристики:
Для обеспечения регулировки скорости движения цилиндра в обе стороны и с учетом минимизации размеров гидростанции выберем сдвоенный дроссель с обратным клапаном модульного исполнения ДКМ 103А ТУ 2 – 053 – 1799 - 86. Его технические характеристики:
- диапазон регулировки расхода 0 - 63 лмин;
Гидравлический расчёт гидросистемы проводится для определения гидравлического КПД линий и аппаратов системы.
Расчёт начнём с выбора рабочей жидкости. Рабочая жидкость гидропривода должна обеспечивать хорошие смазочные и антикоррозионные свойства. Для данного привода выбираем масло ИГП-30 по ТУ38-110-413-78.
Характеристики масла:
- плотность r = 885 кгм3;
- вязкость масла при температуре 400 С n40 = 47 сСт или (47)×10-6 м2с.
Рассмотрим метод проведения гидравлического расчета на примере гидроцилиндра поворота стола Ц2.
Трубопровод диаметром 10 мм и длиной 1 м.
Площадь трубопровода:
Скорость жидкости в трубопроводе:
Определим число Рейнольдса:
Т.к. полученное число Рейнольдса меньше критического числа Рейнольдса для цилиндрических труб то режим течения ламинарный.
Определяем коэффициент гидравлического сопротивления по формуле Пуазейля:
Потери на данном участке:
Обратный клапан на участке 1
Определяем коэффициент местного сопротивления:
Потери давления на данном участке:
Тройник на участке 1
Трубопровод диаметром 8 мм и длиной 35 м.
плавных и 1 резкий изгиб на участке 6
Внезапное расширение при входе в гидроцилиндр
Потери во всей напорной магистрали:
Трубопровод диаметром 8 мм и длиной 5 м.
Внезапное сужение на выходе из гидроцилиндра
плавных и 1 резкий изгиб на участке 1
Внезапное расширение при входе в гидробак
Общие потери во всей сливной магистрали:
Давление в напорной камере:
Давление в сливной камере:
Тогда КПД гидролиний и аппаратов:
Трубопровод диаметром 8 мм и длиной 65 м.
плавных и 2 резких изгиба на участке 1
плавных изгиба на участке 1
Результаты гидравлического расчета остальных гидродвигателей представлены в таблице 6.1
Таблица 6.1 Данные и результаты гидравлического расчета гидродвигателей
Продолжение таблицы 6.1
Целью теплового расчета является определение температуры рабочей жидкости при работе гидропривода и принятие решение о необходимости установки теплообменника.
Расчет будем вести следующим образом:
Фактическая температура рабочей жидкости в гидросистеме определяется по формуле:
Тж - фактическая температура рабочей жидкости в гидросистеме 0С;
Тн - начальная температура рабочей жидкости в гидросистеме примем для расчета 22 0С;
DТ – приращение температуры жидкости при установившемся тепловом режиме работы гидропривода 0С.
Приращение температуры жидкости при установившемся тепловом режиме работы гидропривода определяется по формуле:
где: DТ – приращение температуры жидкости при установившемся тепловом режиме работы гидропривода 0С.
Nт.и – средняя за цикл мощность источников тепловой энергии кВт;
Pт.п - удельная мощность теплоотдачи в окружающую среду при перепаде температур 1 0С кВт 0С
Средняя за цикл мощность источников тепловой энергии рассчитывается по формуле:
где: DNср. – средняя за цикл мощность источников тепловой энергии кВт;
DNт.и. – мощность выделенных источников тепловой энергии кВт;
ty – полное время цикла с;
Рассчитаем полную мощность потребляемую насосом по формуле:
где Nн – полная мощность потребляемая насосом В;
Pн – давление насоса Па;
Qн - подача насоса м зс;
hн - полный к.п.д. насоса.
Определим мощности тепловых источников выделенных частей гидропривода по формуле:
где: DN- потеря мощности кВт;
Nн- полная мощность потребляемая насосом насосом кВт;
hг.п.- полный к.п.д. выбранной части гидропривода.
К.п.д. гидропривода каждой части гидросистемы определяем по формуле:
hг.п.= hн*hо.д.*hм.д.*hг.а.
где: hг.п. – полный к.п.д. гидропривода;
hн - полный к.п.д. насоса;
hо.д - объемный к.п.д. двигателя выделенной части системы;
hм.д – механический к.п.д. двигателя выделенной части системы;
hг.а. – к.п.д. гидролиний и аппаратов выделенной части системы;
Для удобства данные для расчета и результаты представим в виде таблицы
Расчет средней за цикл мощности источников тепловой энергии рассчитаем в соответствии с формулой данные для расчета и результат приведены в таблице 2.7.2.
Таблица Данные и результаты расчета мощности тепловых источников выделенных частей гидропривода.
Выделенная часть гидропривода
Таблица Данные и результаты расчета средней за цикл мощности тепловых источников.
Средняя мощность за цикл
Рассчитаем удельную мощность теплоотдачи в окружающую среду при перепаде температур 1 0С. Расчет ведется по формуле:
Pт.п = k т.п. * S c
где: Pт.п - удельная мощность теплоотдачи в окружающую среду при перепаде температур 1 0С Вт 0С;
k т.п – коэффициент теплопередачи от жидкости через стенку в окружающее пространство Вт(м2 * 0С);
S c – площадь теплопередающей поверхности м2;
Площадь теплопередающей поверхности:
Sп = Sтр + Sб + Sга
где: Sтр – суммарная площадь теплопередающих поверхностей трубопроводов м2
Sб – суммарная площадь теплопередающей поверхности гидробака м2
Sга– суммарная площадь теплопередающих поверхностей гидроаппаратов м2
Площадь поверхностей трубопровода:
Где Sтр – площадью поверхности трубопроводов м2;
dтр – наружный диаметр трубопровода м;
Lтр. – длина трубопровода с данным диаметром;
Данные по длине и диаметрам трубопроводов берем из гидравлического расчета результаты приведены в таблице.
Площадь гидробака определяется по формуле:
Так как объем бака составляет 250 литров площадь составит:
Таблица Данные и результаты расчета площади поверхностей трубопроводов.
Длина трубопроводов (м)
Площадь трубопроводов (м2)
Площадь гидроаппаратов составляет 36 м2.
Sп = 25 + 229 + 36 = 874 м2
Удельная мощность теплоотдачи в окружающую среду при перепаде температур 1 0С с учетом того что коэффициент теплопередачи от жидкости через стенку в окружающее пространство при естественной циркуляции воздуха составляет 20 Вт(м2 * 0С) будет равна:
Pт.п = 20. * 874 = 17482 Вт 0С
Тогда приращение температуры жидкости при установившемся тепловом режиме работы гидропривода составит:
DТ = 11006 17482 = 63 0С
Фактическая температура рабочей жидкости в гидросистеме с учетом принятой начальной температуры 22 0С составит:
Тж = 22 + 63 = 283 0С
Рекомендуемая температура рабочей жидкости в гидроприводе должна находиться в пределах от 20 до 50 0С фактическая температура рабочей жидкости 283 0С таким образом устанавливать в гидросистеме после модернизации теплообменник нет необходимости.
Проведем прочностные расчеты гидроцилиндра выдвижения устройства подачи Ц3. Расчеты будем вести в соответствии с методиками указанными в [4].
1 РАСЧЕТ ТОЛЩИНЫ СТЕНКИ ГИДРОЦИЛИНДРА
Для расчета необходимой толщины стенки гидроцилиндра воспользуемся следующей формулой:
где D - внутренний диаметр цилиндра мм;
р – внутреннее давление кгсм2;
[] – допускаемое напряжение кгсм2.
Диаметр и давление принимаем из энергетического расчета:
Допускаемое напряжение для стали принимаем:
Тогда необходимая толщина стенки гидроцилиндра:
Примем толщину стенки 5 мм.
2 РАСЧЕТ ГИДРОЦИЛИНДРА НА ПРОЧНОСТЬ И УСТОЙЧИВОСТЬ
Для расчетов будем пользоваться следующей схемой:
l1 – расстояние от головки штока гидроцилиндра до точки А в см.
l2 – рассточние от переходной точки А до шарнира корпуса гидроцилиндра в см.
l = l1+l2 - длина гидроцилиндра точки А до шарнира корпуса гидроцилиндра в см.
a – расстояние от начала передней направляющей штока до конца поршня в см.
Δ1 – зазор на диаметр направляющих штока в см.
Δ2 – зазор на диаметр между поршнем и цилиндром в см.
J1 и J2 – моменты инерции сечения на длинах l1 и l2 в см.
– начальный прогиб гидроцилиндра
P – наибольшая рабочая продольная нагрузка в кг.
Х – Расстояние от головки штока гидроцилиндра до места наибольшего прогиба под нагрузкой в см.
Q – поперечная сила в кг.
G – вес гидроцилиндра в кг.
– наибольший прогиб домкрата под нагрузкой в см.
Рассчитаем гидроцилиндр с D = 40 мм; d = 20 мм; при р = 40 кгсм2 и ходе 165 мм. Гидроцилиндр нагружен только центральными продольными нагрузками
Определяем остальные исходные величины:
а) Расчет на устойчивость
По графику рис.109 [4] находим
Условие устойчивости выдержано.
б) Расчет штока на прочность
Начальный прогиб (по 4-ой схеме):
3 РАСЧЕТ РЕЗЬБОВЫХ СОЕДИНЕНИЙ В ГИДРОЦИЛИНДРЕ
Проведем расчет на прочность резьбового соединения с помощью шпилек.
Растягивающее напряжение:
где k – коэффициент затяжки; k = 15;
P – усилие действующее на резьбовое соединение; Р = 1256 кг;
d – диаметр проточки под резьбу; d = 11 см;
z – количество резьбовых соединений участвующих в работе; z = 4.
Наибольшее касательное напряжение в резьбе:
где d0 – наружный диаметр шпильки; d0 = 1 см;
k1 – коэффициент зависящий от трения фрикционной пары; k1 = 012
Приведенное напряжение в резьбе:
Коэффициент запаса по пластическим деформациям:
Навроцкий К. Л. Теория и проектирование гидро-и пневмоприводов : Учебник для вузов по специальности "Гидравлические машины гидроприводы и гидропневмоавтоматика" К. Л. Навроцкий . – М. : Машиностроение 1991 . – 384 с.
Свешников В.К. Усов А.А. Станочные гидроприводы. Справочник. — 2-е изд. перераб. и доп. — М.: Машиностроение 1988. — 512 с. ил. (Б-ка конструктора)
Анурьев В.И. Справочник конструктора-машиностроителя: В 3 т. Т.1. - 8-е изд. переработ. и доп. Под ред. И.Н. Жестковой. - М.: Машиностроение 2001. - 902 с.:ил. (Том 1)
Анурьев В.И. Справочник конструктора-машиностроителя: В 3 т. Т.2. - 8-е изд. переработ. и доп. Под ред. И.Н. Жестковой. - М.: Машиностроение 2001. - 902 с.:ил. (Том 2)
Анурьев В.И. Справочник конструктора-машиностроителя: В 3 т. Т.3. - 8-е изд. переработ. и доп. Под ред. И.Н. Жестковой. - М.: Машиностроение 2001. - 902 с.:ил. (Том 3)
Гидравлика гидромашины и гидроприводы: Учебник для машиностроительных вузов Т. М. Башта С. С. Руднев Б. Б. Некрасов и др. — 2-е изд. перераб. — М.: Машиностроение 1982.
Клапан обратный Г51-32 ТУ 2-053-1649-83
Клапан обратный 15с546k ГОСТ 274 77-87
Клапан предохранительный ДКМ 63 ТУ 2 – 053 – 1397- 78.
Гидромотор поворота ковша
Манометр ГОСТ 8053-73
Гидроцилиндр выдвижения
Гидроцилиндр подвода
Гидроцилиндр подъема
Сливной фильтр АС42-53 ТУ2-053-1614-82.
Распределитель 32 Г51-32 ТУ 2-053-1649-83
Распределитель 32 ВЕ6 573 Г110 ТУ2-053-1815-86
Распределитель 43 1Р МР 10 ТУ 2-053-1815-86
Распределитель 32 1РЕ 10.574А Г100 ТУ2-053-1815-86
Распределитель 32 1РЕ 10.44 Г110 ТУ2-053-1815-86
Распределитель 32 ВЕ 6.44А Г110 ТУ2-053-1815-86
Регулируемый дроссель
Сдвоенный дроссель с обратным клапаном модульного исполнения ДКМ 63 ТУ 2 – 053 – 1799- 83.
Дроссель с обратным клапаном модульного исполнения
Регулятор потока МПГ 55-32 М ТУ 2-053-1790-86
tit.doc
ФЕДЕРАЛЬНОГО ГОСУДАРСТВЕННОГО АВТОНОМНОГО
ОБРАЗОВАТЕЛЬНОГО УЧРЕЖДЕНИЯ ВЫСШЕГО
ПРОФЕССИОНАЛЬНОГО ОБРАЗОВАНИЯ
«КАЗАНСКИЙ (ПРИВОЛЖСКИЙ) ФЕДЕРАЛЬНЫЙ УНИВЕРСИТЕТ
по дисциплине: «Теория и проектирование гидро - и пневмоприводов»
на тему: «Проектирование гидропривода бетоносмесительного ковша»
КП.1.150802.65.13.10.00.00
студент группы 2091173
Рекомендуемые чертежи
- 20.06.2021