Двухвалковая зубчатая дробилка СМД-153





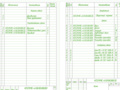
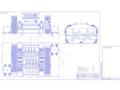
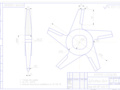
- Добавлен: 25.10.2022
- Размер: 2 MB
- Закачек: 0
Описание
Состав проекта
![]() |
![]() ![]() |
![]() |
![]() ![]() ![]() ![]() |
![]() ![]() ![]() ![]() |
![]() ![]() ![]() ![]() |
![]() ![]() ![]() ![]() |
![]() ![]() ![]() ![]() |
![]() ![]() ![]() ![]() |
![]() ![]() ![]() ![]() |
![]() ![]() |
![]() ![]() |
![]() ![]() ![]() |
![]() |
![]() ![]() |
![]() ![]() |
![]() ![]() |
![]() ![]() |
![]() ![]() |
![]() ![]() |
![]() ![]() |
![]() ![]() |
![]() ![]() ![]() ![]() |
![]() ![]() |
![]() ![]() ![]() |
![]() ![]() ![]() |
Дополнительная информация
Вал.dwg

Остальные технические требования по СТБ 1014-95
Зубчатый диск.dwg

* Размер для справок
стальные технические требования по СТБ 1014-95
СМД153ВО.dwg

КП.СМ.МС-41.00.00.000 ВО
Базовая модель СМД-153
Размер куска исходного материала
Размер готового продукта
Частота вращения валков
Мощность электродвигателя
Хомут _ КП.СМ.МС-41.01.03.000.dwg

Сталь 20 ГОСТ 1577-81
Остальные технические требования по СТБ 1014-95
Спецификация.dwg

КП.СМ.МС-41.01.00.006
КП.СМ.МС-41.00.00.000.ВО
Разрабатываемые изделия
КП.СМ.МС-41.01.00.000.СБ
КП.СМ.МС-41.01.00.001
КП.СМ.МС-41.01.00.002
КП.СМ.МС-41.01.00.003
КП.СМ.МС-41.01.00.004
Болт М20 х 100 ГОСТ 15589-70
Гайка М20 ГОСТ 15526-70
Шайба 20 ГОСТ 6402-70
КП.СМ.МС-41.02.00.000.СБ
Болт М12 х 70 ГОСТ 15589-70
КП.СМ.МС-41.01.00.005
Шайба 12 ГОСТ 6402-70
КП.СМ.МС-41.03.00.000.СБ
КП.СМ.МС-41.01.00.007
ВалокСБ.dwg

Дисбаланс не более 0
Остальные технические требования по СТБ 1022-96
Диск.dwg

Сталь 20 ГОСТ 1577-81
Технические требования по СТБ 1014-95
Титульники.docx
Учреждение образования
«БЕЛОРУССКИЙ ГОСУДАРСТВЕННЫЙ УНИВЕРСИТЕТ ТРАНСПОРТА»
Кафедра «Детали машин путевые и строительные машины»
«Строительные машины и монтажное оборудование»
ПРОЕКТ МОДЕРНИЗАЦИИ ВАЛКОВОЙ ДРОБИЛКИ
студент группы МС-41ассистент
ПОЯСНИТЕЛЬНАЯ ЗАПИСКА
Спецификация.dwg

КП.СМ.МС-41.01.00.006
КП.СМ.МС-41.00.00.000.ВО
Разрабатываемые изделия
КП.СМ.МС-41.01.00.000.СБ
КП.СМ.МС-41.01.00.001
КП.СМ.МС-41.01.00.002
КП.СМ.МС-41.01.00.003
КП.СМ.МС-41.01.00.004
Болт М20 х 100 ГОСТ 15589-70
Гайка М20 ГОСТ 15526-70
Шайба 20 ГОСТ 6402-70
КП.СМ.МС-41.02.00.000.СБ
Болт М12 х 70 ГОСТ 15589-70
КП.СМ.МС-41.01.00.005
Шайба 12 ГОСТ 6402-70
КП.СМ.МС-41.03.00.000.СБ
КП.СМ.МС-41.01.00.007
содержание.docx
Анализ уровня техники в области двухвалковых дробилок. Исследовательская часть проекта 7
Выбор прототипа. описание конструкции принципиальной кинематической схемы двухввалковой зубчатой дробилки 16
Определение основных параметров дробилки20
1 Расчет технологических параметров валковой дробилки 20
1.1 Расчет геометрических параметров 20
1.2 Расчет кинематических параметров 22
1.3 Расчет производительности дробилки 22
1.4 Расчет мощности привода 23
1.5 Определение усилий в деталях валковой дробилки 30
2. Конструктивный расчет 31
2.1 Расчет на прочность вала валковой дробилки 31
Эскизное конструирование валковой дробилки 36
Разработка мероприятий по технике безопастности охране окружающей среды энергоресурсозбережению при работе дробилки37
1 Общие требования безопасности37
2 Требования безопасности перед началом работы 42
3 Требования безопасности во время работы 43
4 Требования безопасности в аварийных ситуациях 46
5 Требования безопасности в аварийных ситуациях 47
6 Охрана окружающей среды 48
Список использованных источников51
пояснительная записка.docx
Недостатками валковых дробилок являются большие эксплуатационные расходы быстрое изнашивание деталей большой расход электроэнергии значительная часть которой потребляется непроизводительно образование пылевидных фракций неоднородность измельченного продукта. Развитие технологий в области валковых дробилок направлено на устранение этих недостатков.
Целью данного курсового проекта является модернизация двухвалковой зубчатой дробилки для повышения эффективности дробления увеличения производительности снижения металлоемкости и уменьшения капитальных затрат. Модернизация предусматривает изменение конструкции дробилки а именно изменение конструкции валка дробилки что увеличивает его долговечность и уменьшение затрат на ремонт.
В проекте произведен анализ патентно-технической литературы рассмотрены зарубежные аналоги дробилок.
Назначение краткое описание устройства и работы двухвалковой дробилки
Валковая дробилка предназначена для дробления горных пород путем затягивания материала силами тренияи раздавливания между двумя параллельнымицилиндрическимивалками вращающимися с одинаковой скоростью навстречу друг другу и отсеивания негабаритных кусковгорной породы.
Основным рабочим элементом валковой дробилки является вращающийся на горизонтальной оси цилиндрический валок. Подлежащий дроблению материал подается сверху затягивается между валками или валком и футеровкой камеры дробления и в результате этого дробится.
Валковые дробилки бывают одно- двух- трех- и четырехвалковые. Четырехвалковую дробилку в ряде случаев можно рассматривать как две двухвалковые смонтированные в одном корпусе.
Поверхности валков бывают гладкие рифленые ребристые и зубчатые: длинно- и короткозубчатые (длиннозубчатые – при высоте зуба более 01 диаметра валка; короткозубчатые – при высоте зуба менее 01 диаметра валка). Сочетание дробящих поверхностей может быть различным: например оба валка могут иметь гладкую поверхность или один гладкую другой – рифленую. Дробилки с гладкими и рифлеными валками обычно применяют для дробления материалов средней прочности (до сж = 150 МПа); дробилки с зубчатыми валками – для измельчения каменного угля и подобных материалов малой прочности (до сж = 80 МПа). Крупность продукта дробления валковой дробилки зависит как от размера выходной щели между валками так и от типа поверхности рабочих органов. В мировой практике валковые дробилки используют как правило на заключительных стадиях дробления (среднее и мелкое дробление).
Привод валков осуществляется так как показано на рисунке 1.1.
Рисунок 1.1- Варианты привода валков двухвалковых дробилок:
– шкив; 2 – шестеренчатая передача; 3 – редуктор; 4 – кардан; 5 – электродвигатель.
Наиболее распространена двухвалковая дробилка. По ней изготовляют большинство валковых дробилок. Валки вращаются навстречу один другому захватывают и дробят попавший между ними материал раздавливая его и частично истирая. Иногда для увеличения истирающего эффекта необходимого при измельчении некоторых материалов валкам сообщают разную окружную скорость.
Корпуса подшипников вала одного из валков опираются на пружины и могут перемещаться. В результате этого при попадании недробимого предмета один валок может отойти от другого и пропустить недробимый предмет после чего под действием пружин возвратиться в исходное положение. Имеются конструкции в которых подпружинены оба валка. Их применяют там где в исходном материале много недробимых включений.
Широко распространенная до последнего времени «традиционная» двухвалковая дробилка (рисунок 1.2) выполнена по схеме приведенной на рисунке 1.1 а.
Рисунок 1.2-Двухвалковая дробилка с рифленым и гладким валками
Шкив 2 дробилки приводится во вращение электродвигателем далее через одноступенчатый редуктор закрытый кожухом 8 вращение передается первому рифленому валку 3 корпуса подшипников которого неподвижно прикреплены к раме 1 дробилки. Подшипники 7 второго гладкого валка 4 прижаты к упору амортизационными пружинами 5 и могут перемещаться сжимая пружины увеличивая зазор между валками и пропуская недробимый предмет. Вращение от первого (ведущего) валка передается второму (ведомому) валку с помощью шестерен с удлиненными зубьями допускающими изменение межцентрового расстояния между валами валков. Шестерни вращаются в масляной ванне и закрыты кожухом 6.
В последнее время появились конструктивные решения в которых каждый валок приводится от электродвигателя (см. рисунок 1.1 б) или через редуктор 3 и карданные валы 4 (см. рисунок 1.1 в).
Существенным недостатком валковых дробилок является интенсивное и неравномерное изнашивание рабочих поверхностей валков (бандажей) при обработке прочных и абразивных горных пород. Бандаж изнашивается в основном в средней части валка что не дает возможности поддерживать стабильный размер выходной щели по всей ее длине. Кроме того валковые дробилки обладают сравнительно невысокой удельной производительностью.
Тем не менее анализ зарубежного опыта показывает большое распространение валковых дробилок различных конструкций для дробления самых разнообразных материалов особенно в составе передвижных дробильно-сортировочных установок. Это объясняется тем что валковые дробилки наиболее приспособлены для переработки очень распространенных материалов склонных к налипанию или содержащих липкие включения. Во время работы дробилок налипший на поверхность валков материал срезается очистными скребками и при необходимости отводится в сторону. Применение дробилок других типов на переработке таких материалов или вообще невозможно или вызывает частые простои связанные с длительной и трудоемкой работой по очистке камеры дробления. Возможность перерабатывать материалы склонные к налипанию на рабочих органах выгодно отличает валковые дробилки от других типов дробильного оборудования.
Анализ уровня техники в области двухвалковых дробилок. Исследовательская часть проекта
Многие известные зарубежные фирмы выпускают двухвалковые дробилки разных типоразмеров с зубчатыми рифлеными и гладкими валками. Например в проспектах фирмы «БШС» ФРГ за 1988 г. предложены двухвалковые дробилки с рифленым и гладким валками привод которых осуществляется электродвигателем через конический редуктор и клиноременную передачу (рисунок 1.1 г). Все узлы дробилки в том числе редуктор и электродвигатель собраны на общей раме. Второй валок (дальний от редуктора) опирающийся на амортизационную систему может отходить от первого увеличивая зазор между валками. Для обеспечения этого клиноременная передача валка оборудована натяжным роликом позволяющим изменять межцентровое расстояние шкивов.
Для обеспечения равномерности загрузки дробилки над ее загрузочной воронкой установлен электромагнитный питатель.
Фирма «Бержо» (Франция) выпускает двухвалковые дробилки с зубчатыми рифлеными и гладкими валками. Валки имеют индивидуальные приводы с помощью клиноременной передачи от электродвигателей расположенных на общей раме с основными узлами дробилки.
В таблице 2.1 приведена техническая характеристика двухвалковых дробилок фирм «БШС» (ФРГ) и «Бержо» (Франция).
Таблица 2.1-Техническая характеристика двухвалковых дробилок
зарубежного производства
Частота вращения валка обмин
Производительность тч
Крупность готового продукта мм
Мощность двигателя кВт
Окончание таблицы 2.1
Фирма «Бержо» (Франция)
Завод им. Э. Тельмана (ГДР) выпускал такие валковые дробилки трех типоразмеров для первичного и вторичного дробления (таблица 2.2).
В промышленности строительных материалов для перерабатывания глиняной массы и удаления из нее камней применяют так называемые дезинтеграторные вальцы (рисунок 2.1). Они состоят из двух валков из которых валок 1 большего диаметра имеет гладкую поверхность а на рабочей поверхности валка 3 меньшего диаметра предусмотрены ребра высотой 8–10 мм. Ребристый валок совершает 500 – 600 обмин гладкий – 50 – 60 обмин.
Таблица 2.2-Техническая характеристика дробилок
с короткозубчатыми валками
Зазор между валками мм
Максимальная крупность исходного материала для дробления мм
Производительность при зазоре между валками 100 мм м3 ч
Мощность электродвигателя кВт
дробилки (без привода)
привода (без двигателя)
Необходимая площадь для монтажа и обслуживания м (ширина длина)
Исходный материал загружается в воронку 2 и поступает на быстроходный валок. Комок глины ударяясь о ребро валка деформируется «теряет» скорость и затягивается в зазор между валками. Твердые включения например камни будут отбрасываться ребрами валка и попадать в отводной лоток. Таким образом в дезинтеграторных вальцах измельчение глины сочетается с ее очисткой от твердых примесей.
Для переработки глиняной массы предназначены также дырчатые вальцы конструкции ВНИИстройдормаша. Рабочие поверхности валков дырчатые. Исходная масса подается в приемную воронку и затягивается между двумя валками вращающимися навстречу один другому где глиняная масса разминается растирается благодаря разной окружной скорости валков и продавливается сквозь отверстия внутри валков. Далее она попадает на отводящий конвейер. При этом имеющиеся в глиняной массе твердые включения дробятся так как сила предварительного натяжения пружин тихоходного валка рассчитана на такие усилия.
Рисунок 2.1-Дезинтеграторные вальцы
Валково-зубчатые дробилки надежны в работе и имеют высокую производительность при сравнительно небольших габаритах и массе (таблица 2.2).
Короткозубчатая двухвалковая дробилка СМД-175А с ротором размером 15001200 мм предназначена для дробления известняка мергеля угля соли и других подобных материалов с пределом прочности до 120 МПа и температурой до 40 °С.
На сварную раму дробилки в подшипниках качения установлены два валка подшипники одного из которых неподвижны подшипники второго опираются на амортизационные устройства и при попадании между валками недробимого предмета валок может отходить от неподвижного и возвращаться обратно.
К валу валка (рисунок 2.2) прикреплены две ступицы на которых болтами закреплены рабочие зубчатые сегменты. В нижней части рамы закреплены металлические гребенки для очистки рабочей поверхности валков от материала налипшего на них в процессе дробления. Каждый валок имеет индивидуальный привод состоящий из электродвигателя эластичной муфты редуктора и универсального шпинделя.
Рисунок 2.2-Валок двухвалковой зубчатой дробилки СМД-175А:
– корпус подшипника; 2 – ступица; 3 – болт крепления; 4 – сегмент; 5 – зуб; 6 – шпонка; 7 – вал.
Таблица 2.2- Двухвалковые зубчатые дробилки
длиннозубчатая СМД-153
короткозубчатая СМД-175А
Номинальная частота вращения валков обмин
Производительность тч не менее
Размер загружаемого материала мм не более
Размер исходного материала мм не более
Мощность электродвигателей кВт не более
Масса дробилки без электродвигателей т не более
Рассмотрим несколько полезных изобретений в области валковых дробилок.
Первое полезное изобретение которое мы рассмотрим относится к валкам дробилки. Целью изобретения является повышение надежности работы и ремонтопригодности за счет обеспечения возможности оперативного устранения зазоров между дробящими сегментами и барабанами. Валок (рисунок 2.3) валковой дробилки состоит из вала 1 барабанов 2 дробящих сегментов 3 и П-образных скоб 4. Каждая П-образная скоба 4 имеет на отгиб ее выполненную с уклоном α внутреннюю поверхность 5 контактирующую с опорной поверхностью 6 барабана 2 выполненную с таким же уклоном поверхности 5 и 6 наклонены к оси ОО валка 1 на угол α меньший чем угол трения металлов из которых изготовлены скоба и барабан. Внутренняя поверхность 7 другого отгиба скобы 4 параллельна оси валка и контактирует с параллельной этой оси опорной поверхностью 8 открытого опорного паза 9 образованного на рабочей поверхности дробящего сегмента 3. Каждая скоба 4 зафиксирована болтовым соединением 10 в опорном пазе 9 переходящем в торцовый паз 11 сегмента 3 и в торцовый паз 12 барабана 2 при этом между внутренней поверхностью 13 перемычки 14 скобы 4 и соответствующими поверхностями торцовых пазов 11 и 12 имеется регулировочный зазор и эти поверхности не контактируют между собой. Своими боковыми поверхностями 15 скоба 4 контактирует со смежными боковыми поверхностями 16 и 17 пазов 11 и 12 сегментов 3 и барабана 2.
Рисунок 2.3-Валок валковой дробилки и вид А
В перемычке 14 скобы 4 (рисунок 2.4) имеется одно или несколько сквозных отверстий 18 для вывода регулировочных винтов 19 на внешнюю сторону 20 перемычки 14 скобы 4. Каждый регулировочный винт 19 соединен с закладной гайкой 21 установленной в кармане 22 барабана 2 без возможности проворота и осевого смещения.
Рисунок 2.4-П-образная скоба
Предусмотрена возможность соединения регулировочного винта 19 с резьбой 23 выполненной непосредственно в теле барабана 2.
Отверстия 18 в перемычке скобы 4 и отверстия 24 в теле барабана могут выполняться продолговатыми в виде сквозных пазов при этом первые ориентированы радиально а вторые вдоль оси валка.
Предлагаемая конструкция валка позволяет повысить его надежность и ремонтопригодность.
Изобретение расширяет диапазон применения известного устройства позволяет предотвратить (на сборке) и устранить (после приработки в эксплуатации) люфты и болтанки сегмента в тех пределах в которых они еще допускаются П-образной скобой обеспечивая в дополнение к визуальному контролю обнаружения поломок новую возможность: оперативное регулирование зазора и устранение люфта в процессе сборки и эксплуатации при этом предлагаемое техническое решение позволяет усилить отдельные преимущества известного устройства (например повысить жесткость П-образной скобы) и обеспечивает достижение нового указанного положительного эффекта.
Следующее изобретение рассматриваемое нами относится к дробилкам ударного действия для измельчения материалов и может быть использовано в промышленности строительных материалов например для измельчения различных твердых материалов. Его целью является повышение надежности работы и эффективности процесса дробления.
Валковая дробилка (рисунок 2.5) состоит из кожуха 1 в подшипниках 2 которого установлены два горизонтально расположенных дробящих валка 3 с ударными элементами 4.
Рисунок 2.5-Поперечный разрез валковой дробилки разрезы А-А и Б-Б
Вдоль дробящих валков ниже и параллельно им размещена балка 5 снабженная зубчатыми абразивостойкими дисками 6 с.возможностью их свободного вращения на балке а также относительно друг друга смонтированная в упругих опорах выполненных в виде смонтированных в корпусах 7 наборов резиновых шайб 8 (рисунок 2.5).
Кроме того упругие опоры содержат упорные втулки 9 и 10 прижимные кольца 11 и гайки 12. Упругость опор зависит от твердости дробимого материала и регулируется количественным набором резиновых шайб 8. Балка своими корпусами 7 монтируется на опорных площадках кожуха 1 расположенных с наружной стороны его боковых стенок.
Эта дробилка отличается тем что балка выполнена с установленными на ней с возможностью свободного вращения абразивостойкими дисками а опоры балки выполнены упругими в виде набора резиновых шайб.
Рассмотрим еще одно полезное изобретение касающееся конструкции валка дробилки. Это полезное изобретение повышает надежность и долговечность упрощает конструкцию и снижает трудоемкость изготовления валка.
Валок дробилки (рисунок 2.6) содержит барабан 1 и бандаж 2 выполненный из секций 3. Барабан 1 снабжен зубьями 4 выполненными расширяющимися к периферии барабана образуя ячейки 5 трапецеидальной формы. Секции 3 бандажа 2 в местах крепления к барабану 1 выполнены подобными по форме ячейкам 5 с шириной меньшей размера ячейки 5 между зубьями 4 причем большее основание а трапеции секции 3 меньше меньшего основания б трапеции ячейки. Секции 3 внутренней поверхностью оперты о дно ячейки 5 а между ее боковыми гранями и боковыми гранями зубьев 4 установлены клиновые вставки 6.
Секции 3 бандажа 2 (рисунок 2.7) могут быть выполнены гладкими рифлеными зубчатыми и т.н. Закрепление вставок 6 от выпадания осуществлено посредством сварки. Вставки 6.установлены перед секциями 3 по ходу вращения валка.
Рисунок 2.6-Общий вид валка дробилки
Рисунок 2.7-Вид А валка дробилки
Валок дробилки отличается тем что зубья выполнены расширяющимися к периферии барабана причем большее основание опорных частей продольных секций меньше расстояния между образующими ячейку зубьями на уровне их свободных концов и оперто на большее основание секции а между боковыми гранями зубьев и опорных частей продольных секций смонтированы клиновые вставки.
Так же валок отличается тем что клиновые вставки установлены перед продольными секциями бандажей по ходу вращения валка.
Выбор прототипа. Описание конструкции принципиальной кинематической схемы двухвалковой зубчатой дробилки
Выбираем в качестве прототипа дробилку СМД-153.В некоторых литературных источниках двухвалковую зубчатую дробилку СМД-153 (рисунок 3.1) называют дискозубчатой. Применяют ее обычно для грубого дробления угля в системе топливоподачи электростанций а также для дробления других материалов с пределом прочности при сжатии до 45 МПа в которых могут попадаться отдельные включения горных пород с пределом прочности при сжатии до 60МПа. Эксплуатация дробилки допускается как в закрытых помещениях так и на открытых площадках при температуре окружающего воздуха от – 40 до + 40 °С.
Рисунок 3.1-Двухвалковая зубчатая дробилка СМД-153.
Для удобства демонтажа валков корпус дробилки выполнен разъемным и состоит из нижней 5 и верхней 4 частей. В боковых частях корпуса дробилки предусмотрены люки 11 для осмотра и ремонта рабочих органов дробилки. К верхней части корпуса прикреплена загрузочная воронка 3. Места разъемов уплотнены резиновыми прокладками.
Для устранения напряжений от изгиба в раме и разгрузки болтов крепления подшипников их корпуса в верхней части соединены между собой стяжками 1.
Каждый валок диаметром 1100 мм и длиной 1000 мм имеет индивидуальный привод от асинхронного двигателя. Крутящий момент от электродвигателя валкам передается с помощью клиноременной передачи 2.
Для исключения поломки механизмов дробилки при попадании недробимых тел в камеру дробления приводы дробилки снабжены такими же предохранительными устройствами как и приводы описанных щековых дробилок.
Зубчатые валки расположены в горизонтальной плоскости вращаются навстречу один другому с различной частотой (170 и 200обмин). Зубчатый валок представляет собой вал 9 квадратного сечения со смонтированными на нем зубчатыми дисками состоящими из двух полузвездочек: 6 и 7 соединенных между собой болтами 10 из стали 40Х что обеспечивает возможность замены дисков без демонтажа валка.
Материал поступает в дробилку сверху через загрузочную воронку 3 дробится и выходит через разгрузочное отверстие. В средней части станины дробилки под валками установлена балка 8 препятствующая прохождению кусков материала более 200 мм. Для обогрева дробилки в холодное время года чтобы устранить намерзание материала на стенке корпуса в раме дробилки смонтированы змеевики в которые подается теплоноситель. На конце вала закреплен шкив с вмонтированным в него предохранительным устройством.
Для привода дробилки установлены два трехфазных короткозамкнутых электродвигателя мощностью 30 кВт которые питаются от сети переменного тока (380 В; 50 Гц). Электросхемой предусмотрен раздельный пуск электродвигателей с помощью реле времени. Управление электроприводом дробилки дистанционное кнопочное. С помощью постов управления дробилки ее можно пустить с различных точек производственного помещения. Пусковая электроаппаратура смонтирована на отдельной панели открытого исполнения которую устанавливают в электрошкаф.
Дискозубчатая дробилка СМД-153 надежны в работе и имеет высокую производительность при сравнительно небольших габаритах и массе (таблица 3.1).
Таблица 3.1- Технические характеристики дробилки
Дробилка длиннозубчатая СМД-153
Размер готового продукта мм не более
В качестве модификации валковой дробилки возьмем за основу следующее полезное изобретение так как оно упрощает конструкцию валка и повышает технологичность его изготовления.
Валок дробилки отличается тем что он снабжен кольцами из пластичного материала каждая дисковая шайба выполнена с проточкой на периферии наружной цилиндрической поверхности а бандаж — с проточками на внутренней поверхности причем кольца из эластичного материала установлены в полостях образованных проточками бандажа и дисковых шайб внутренний диаметр колец из эластичного материала соответствует наружному диаметру проточек на дисковых шайбах а наружный меньше диаметра проточек бандажа. Валок так же отличается тем что он снабжен дополнительными кольцами из эластичного материала а вал выполнен с буртом между дисковыми шайбами причем дополнительные кольца из эластичного материала установлены между буртом и дисковыми шайбами.
Валок дробилки состоит из вала 1(рисунок 3.2) ступицы выполненной в виде двух дисковых шайб 2 стянутых болтами (шпильками) 3 и бандажа 4. В проточках бандажа 4 и дисковых шайб 2 установлены кольца 5 из эластичного материала например резины. На валу 1 в его центральной части соответствующей продольной оси дробилки имеется бурт 6. Между внутренними торцовыми частями дисковых шайб 2 и буртом 6 установлены кольца 7 также из эластичного материала. Дисковые шайбы 2 фиксируются на валу 1 с помощью шпонок 8.
Рисунок 3.2-Общий вид валка.
Возможен вариант исполнения валка (рисунок 3.3) в котором бурт 6 развит а кольца 7 установлены в проточках дисковых шайб 2.Диаметры колец 5 и 7 обеспечивают свободную посадку на сопрягаемые детали.
Рисунок 3.3-Вариант установки на валу колец из эластичного материала
Учитывая что коэффициенты трения таких материалов как резина о сталь имеют высокие значения предлагаемое крепление обеспечивает передачу значительных крутящих моментов при относительно небольших усилиях стягивания шайб 2.
Определение основных параметров дробилки
1 Расчет технологических параметров валковой дробилки
1.1 Расчет геометрических параметров
Некоторые технические характеристики принятого прототипа представлены в таблице 4.1
Таблица 4.1- Технические характеристики дробилки
Мощность электродвигателей кВт
Одним из основных геометрических параметров валковой дробилки является угол захвата т.е угол между двумя касательными к поверхности валков в точках соприкосновения с дробимым материалом.
На кусок дробимого материала (рисунок 4.1) имеющего форму шара и массу m которой ввиду ее незначительности можно пренебречь действуют силы давления Р от обоих валков и силы трения равные fP (здесь f — коэффициент трения материалов о валок). Для упрощения эти силы показаны на рисунке 4.1 для одного валка.
Кусок будет затягиваться валками если 2Pfcosα ≥ 2Рsinα или f ≥ tgα а так как f = tgφ (здесь φ — угол трения) то α φ. Но = 2α значит 2φ. Таким образом так же как у щековых и конусных дробилок угол захвата у валковых дробилок для нормального дробления не должен превышать двойной угол трения.
Рисунок 4.1-Расчетная схема валковой дробилки.
Размер куска захватываемого валками можно определить пользуясь схемой на рисунке 4.1. Если принять что
где D – диаметр валка(таблица 4.1) м;
d – диаметр куска материала м. Примем в соответствии с заданием размер куска дробимого материала равным d = 08 м;
а – ширина выходной щели м. Согласно задания примем а = 02 м что допустимо (таблица 4.1) .
Из формулы (4.1) выразим угол захвата материала
Следовательно α=460 48
Найдем степень измельчения материала по формуле (4.3)
1.2 Расчет кинематических параметров
Частоту вращения валков (обс) определяют по формуле (4.4) предложенной проф. Л. Б. Левенсоном
где f —коэффициент трения угля о валок f=03;
ρ — плотность угля кгм3 ρ = 1350 кгм3;
d — диаметр куска исходного материала м;
D — диаметр валка м.
Значит частота вращения валка должна быть тем меньше чем больше его диаметр чем больше диаметр поступающих кусков и их плотность и чем меньше коэффициент трения между куском материала и валками. По данной формуле определяют максимально возможную частоту вращения валков.
Обычно конструктивно предусматривают минимальную и максимальную частоту вращения которую затем выбирают по конкретным условиям эксплуатации (например при дроблении материалов с малым пределом прочности при сжатии можно принять более высокую частоту чем при дроблении материалов средней прочности).
Примем частоту вращения первого и второго валка n = 200 обмин.
1.3 Расчет производительности дробилки
Производительность валковых дробилок можно вычислить если представить процесс дробления как движение ленты материала. За один оборот валка объем ленты материала (м3) прошедший через выходную щель определяется по формуле (4.5)
где D — диаметр валка м;
L — длина валка(таблица 4.1) м;
α — ширина выходной щели м.
Производительность дробилки (м3с) при частоте вращения вала n определяется по формуле (4.6)
Так как обычно длина валка используется не полностью и материал выходит из дробилки в разрыхленном виде а не плотной лентой то в формулу производительности вводят коэффициент учитывающий степень разрыхленности материала. Для прочных материалов = 02÷03; для влажных вязких = 04÷06. Примем для угля = 02
При работе машины на прочных материалах под действием усилий дробления предохранительные пружины несколько деформируются и валки расходятся поэтому при расчетах размер выходной щели назначают равным 125α. В формулу (4.6) вводят также объемную массу дробимого материала ρ (кгм3) тогда производительность валковой дробилки (кгс) определяют по формуле (4.7)
Подставив значения получим
Полученное значение производительности переведем в тч
1.4 Расчет мощности привода
Установочную мощность электродвигателя валковой дробилки Nдв можно определить если учесть затраты мощности на дробление материала и трение в подшипниках т. е. на преодоление всех сопротивлений при работе машины :
где N1 — мощность расходуемая на дробление материала;
N2 — мощность расходуемая на трение в подшипниках;
При захвате валками кусков материала среднее суммарное усилие дробления Рср вызывает силу трения равную fPcp (здесь f коэффициент трения). Произведение этой силы на радиус валка R представляет собой момент силы на преодоление которого расходуется мощность двигателя.
Произведение момента силы трения и угловой скорости валка определяет мощность N1 необходимую для дробления:
Мощность необходимая на преодоление трения в подшипниках:
где z — диаметр шейки вала м z = 019 м;
f1 — коэффициент трения качения приведенный к валу;
— нагрузка на подшипники Н;
Q — сила тяжести валка Н;
Рср — среднее усилие дробления(см. пункт 4.1.5) Н.
Из формул (4.9)—(4.10) окончательно формула 4.11 для определения установочной мощности электродвигателя валковой дробилки будет иметь вид
где L – длина валка м;
Произведем расчет мощности двигателя:
Рисунок 4.1-Кинематическая схема валка валковой дробилки
– электродвигатель; 2 – ременная передача; 3 – валок.
Выбираем двигатель 4AP225M6Y3 с мощностью N=37 кВт и частотой вращения n=1000 обмин
Передаточное число ременной передачи
Определим частоты вращения валов привода по формуле (4.12)
где – частота вращения
– передаточное число передачи.
Определим мощности кВт на валах привода по формуле (4.13)
– КПД передачи и подшипников.
Определим крутящие моменты Нм на валах по формуле (4.14)
– частота вращения i вала обмин.
Рассчитаем клиноременную передачу.
По полученному значению крутящего момента на ведущем шкиве выбираем клиновой ремень нормального сечения C (В) ГОСТ 1284.1–89. Характеристики ремня приведены в таблице 4.2.
Таблица 4.2–Характеристики клинового ремня
Диаметр ведущего шкива определяется по формуле (4.15)
где – коэффициент пропорциональности. Примем C = 38 42 для ремней нормального сечения.
Примем диаметр шкива
Диаметр ведомого шкива определяется по формуле (4.16)
где – коэффициент упругого скольжения .
Предварительно межосевое расстояние мм определяется по формуле 4.17
где – высота ремня (таблица 4.2) мм.
Длина ремня определяется по формуле (4.18)
Из ряда длин [6 с.17] выбираем
Уточняем межосевое расстояние по формуле (4.19)
Угол обхвата ремнём меньшего шкива определяется по формуле (4.20)
где – допускаемый угол обхвата для клиноременных передач
Условие выполняется.
Скорость ремня определяется по формуле (4.21)
Необходимое число ремней определяется по формуле (4.22)
где Р – передаваемая мощность (всеми ремнями) кВт;
– расчётная допустимая мощность передаваемая одним ремнём кВт;
Cz – коэффициент учитывающий неравномерность распределения нагрузки между ремнями.
Значения коэффициента Cz принимают в зависимости от предварительного числа ремней определяемого по формуле [6 с.16]
где – расчётная допустимая мощность передаваемая одним ремнём определяется по формуле (4.24)
где – допустимая мощность передаваемая одним ремнём кВт определяется по таблице 2.2.7 или таблице 2.2.8 [6 с.17];
– коэффициент учитывающий угол обхвата ведущего шкива ремнем [6 с.12];
– коэффициент учитывающий длину ремня;
– коэффициент учитывающий передаточное число;
– коэффициент учитывающий режим работы и характер нагрузки Ср = 1.
Коэффициент учитывающий длину ремня определяется по формуле (4.25)
де – базовая длина ремня определяется по таблице 2.2.6 [6 с.17].
Расчётная допустимая мощность передаваемая одним ремнём
Предварительное число ремней
Требуемое число ремней
Окончательно принимаем
1.5 Определение усилий в деталях валковой дробилки
Усилия в деталях валковой дробилки определяются нагрузкой которая создается пружинами предохранительного устройства. Эта нагрузка зависит от многих факторов и может быть вычислена лишь приближенно.
Предположим что суммарное усилие (Н) между валками при дроблении материала равно Р. Площадь (м2) на которой будет действовать это усилие найдем по формуле (4.26):
где L — длина валков м;
— длина дуги на участке измельчения материала м;
R — радиус валка м;
Поскольку α=460 48 то
Суммарное усилие дробления (Н)
где — предел прочности материала при сжатии Нм2;
— коэффициент разрыхления материала (для прочных пород = 02÷03; для глины = 04÷06).
Подставив значения и в формулу (4.28) получим:
2 Конструктивный расчет
2.1 Расчет на прочность вала валковой дробилки
Расчет вала выполняется на кручение
Крутящий момент вала T = 1661 Нм
Определяем действующий на вал горизонтальные и вертикальные составляющие.
Находим окружное усилие соответствующее результирующее усилие:
Находим проекции результирующего усилия на оси x и y по формуле (4.31) и формуле (4.32).
Строим эпюры изгибающих моментов. Вал рассматриваем как балку на двух опорах:
а) нагрузка в горизонтальной плоскости
Находим опорные реакции
Σх = 0; HА - Px + HВ =0
Строим эпюру Мкг кНм
ΣMк1г = 10325095 = 098 кНм
б) Нагрузка в вертикальной плоскости.
Находим опорные реакции
Σу = 0; -RA + Px - RВ =0
-11005+ 2201-11005 = 0
Строим эпюру Мхб кНм
ΣМхв = 11005 095 = 104 кНм
Рассчитываем диаметры ступенчатого вал по формуле (4.33):
где Мг – крутящий момент в горизонтальной плоскости
Мв – крутящий момент в вертикальной плоскости
Диаметр вала определяется по формуле (4.34):
где [] – допускаемое напряжения [] = 15 МПа
Выполняем расчет вала на выносливость общий коэффициент запаса выносливости определяется по формуле (4.35):
где n – коэффициент запаса усталостной прочности по нормальным
n – коэффициент запаса усталостной прочности по касательным напряжениям.
где 1 – нормальное напряжение 1 = 550МПа;
- - коэффициент концентратор напряжений.
где К – коэффициент концентратор при = 800МПа и = 18;
Е – масштабный фактор Е =02;
– коэффициент качества обработки поверхности =085;
– коэффициент упрочнения частоты =15.
где Мn – результирующий крутящий момент Мn =141кНм
где -1– касательное напряжение = 400 МПа;
– эффективный концентратор напряжения;
а с – касательные напряжения.а = с = max2.
φ – характеристика циклов нагружения φ = 006
где К – коэффициент концентрации К = 17;
Е – масштабный фактор Е = 08;
– коэффициент качества обработки поверхности = 085.
где Wр – геометрическая характеристика продольного сечения см3.
Определяем общий коэффициент запаса выносливости:
Необходимо выполнения условия для обеспечения прочности вала:
Эскизное конструирование валковой дробилки
Эскизное конструирование выполняют с целью установления принципиальных (конструктивных схемных и др.) решений изделия дающих общее представление о принципе работы и (или) устройстве изделия.
Агрегаты на раме установки необходимо устанавливать компактно с целью уменьшения габаритных размеров однако также необходимо учитывать требования техники безопасности. Двигатели в дробилке ставятся по обе стороны не выходят за ширину дробилки это обусловлено уменьшением габаритных размеров а также приводом валков.
Ременная передача должны быть установлены в защитные кожухи.
Рисунок 5.1-Компоновачная схема двухвалковой дробилки СМД-153
Разработка мероприятий по технике безопастности охране окружающей среды энергоресурсозбережению при работе дробилки
1 Общие требования безопасности
К работе дробильщиком допускаются лица не моложе 18 лет признанные годными к данной работе медицинской комиссией прошедшие обучение по учебной программе дробильщика имеющие удостоверение на право выполнения данной работы.
Поступающий на работу дробильщик должен пройти вводный инструктаж по безопасным методам и приемам труда экологическим требованиям а также первичный инструктаж на рабочем месте о чем должны быть сделаны соответствующие записи в журналах с обязательной подписью инструктируемого и инструктирующего.
Первичный инструктаж на рабочем месте производится с каждым дробильщиком индивидуально с практическим обучением безопасным методам и приемам производства работ.
Все дробильщики после первичного инструктажа на рабочем месте и проверки знаний в течение первых 3-5 смен (в зависимости от стажа опыта и характера работы) выполняют работу под наблюдением бригадира или мастера после чего оформляется допуск их к самостоятельной работе. Допуск к самостоятельной работе фиксируется датой и подписью инструктирующего в журнале регистрации инструктажа.
Повторный инструктаж с дробильщиком должен проводиться не реже чем через 3 месяца. Периодическая проверка знаний по безопасности труда должна проводиться один раз в 12 месяцев.
При изменении правил по охране труда условий и характера работ (получение нового задания переход на другой участок работы замена или модернизация узлов или деталей приспособлений и т.п.) нарушении действующих норм и правил по охране труда которые привели или могут привести к травматизму аварии пожару при перерывах в работе более 30 календарных дней по требованию органов надзора проводится внеплановый инструктаж.
О проведении повторного и внепланового инструктажа производится соответствующая запись в журнале регистрации инструктажа на рабочем месте с обязательной подписью инструктируемого и инструктирующего. При регистрации внепланового инструктажа указывается причина вызвавшая его проведение.
Знания полученные при инструктаже проверяет работник проводивший инструктаж.
Дробильщик получивший инструктаж и показавший неудовлетворительные знания к работе не допускается.
Он обязан вновь пройти инструктаж.
Дробильщик должен иметь II квалификационную группу по технике безопасности. Квалификационная группа должна подтверждаться ежегодно в установленном порядке.
Дробильщик должен знать принцип работы и устройство дробилок дробильно-сортировочных установок и ее агрегатов технологию производства работ инструкцию завода-изготовителя по эксплуатации дробилок дробильных агрегатов инструкцию по охране труда правила внутреннего распорядка организации труда работников дробильно-сортировочной установки требования по выполнению режимов труда и отдыха.
Рабочее место дробильщика - кабина обзора рабочая зона обслуживания - камнедробильная установка должны удовлетворять нормативным требованиям охраны труда.
Технологический процесс переработки камня на щебень сопровождается вредными факторами неблагоприятно воздействующими на организм человека.
Основными вредными производственными факторами являются: пыль вибрация шум.
Нормативные показатели этих факторов не должны превышать:
- запыленность - 10 мгм3(для кварцевой пыли 2 мгм3 при содержании кварца более 10%);
- вибрация - до 02 амплитуды;
Средствами защиты от вредных факторов при работе камнедробилки и смежных с ней агрегатов являются от:
- пыли - орошение водой аспирация;
- вибрации - установка камнедробилки на виброфундаменты виброгасящие прокладки;
- шума - установка кожухов звукоизолирующих кабин;
- пыли вибрации и шума - средства индивидуальной защиты.
При превышении нормативных предельных значений вредных факторов рабочие дробильно-сортировочных установок (заводов) обязаны пользоваться средствами индивидуальной защиты.
Запыленность воздуха определяется аспирационным прибором АЭ-1-4 счетчиком пыли СМ-2 ТВК-3 "Оуэнса".
Камнедробилки и связанные с ними технологическим процессом агрегаты и механизмы (питатели грохота бункера течки) должны быть оборудованы пылеулавливающими устройствами подсоединенными к аспирационной системе.
Аспирационные устройства должны включаться в работу до пуска технологической системы и выключаться через 5-7 мин. после прекращения работы технологического оборудования.
На рабочем месте дробильщика должны быть:
- необходимый инструмент и инвентарь (молоток слесарный кувалда зубило слесарное гаечные ключи отвертки слесарно-монтажные плоскогубцы комбинированные кусачки торцевые лопаты совковые (2 шт.) лом крюк для извлечения негабаритов скребок для уборки просыпи метла и веник лестница длиной до 5 метров);
- смазочный инвентарь (шприц винтовой емкость для хранения солидола канистра воронка ящик для ветоши);
- противопожарный инвентарь (ящик для песка огнетушители ОУ-2 ОХВП-10 ведро топор лопата багор и др.);
- связь (телефон пульт звуковой и световой сигнализации);
- средства индивидуальной защиты;
- средства оказания первой помощи пострадавшим (аптечка);
- принадлежности личной гигиены (полотенце мыло рукомойник шкафчик для спецодежды спецобуви и других средств индивидуальной защиты);
- питьевая кипяченая вода;
- достаточное освещение (50-100 лк);
- техническая и производственная документация (технологическая карта переработки камня на щебень по циклам инструкция завода-изготовителя (ксерокопия или выписка) по эксплуатации камнедробилки (установки) инструкция по охране труда инструкция по оказанию первой доврачебной помощи пострадавшим экологические требования режим труда и отдыха запасные предупреждающие и запрещающие знаки).
Дробильщик должен работать в спецодежде спецобуви и средствах индивидуальной защиты установленных стандартами (куртка и брюки на утепленной подкладке комбинезон рабочий сапоги валяные с резиновым низом перчатки резиновые диэлектрические и рукавицы специальные отмывочно-защитная паста каска “Труд” наушники противошумные пылезащитные очки респиратор "Лепесток" резиновые коврики для ног предохранительный пояс).
Дробильщик обязан знать значение звуковой и световой сигнализации установленных на дробильно-сортировочных установках (заводах) а также сигналов применяемых при производстве взрывных работ.
В случае нарушений требований безопасности другими работниками дробильщик обязан принять возможные меры к предупреждению и устранению опасности и доложить об этом бригадиру или мастеру.
При ведении технологического процесса переработки камня на щебень нахождение посторонних лиц в рабочей зоне запрещается.
Оборудование камнедробилки (установки) должно быть надежно заземлено.
Все передаточные механизмы камнедробилки (зубчатые цепные и ременные передачи) должны быть надежно и прочно ограждены или закрыты кожухами.
Молотковые и валковые камнедробилки должны быть снабжены герметическими сплошными кожухами в которых устроены плотно закрывающиеся смотровые прорези.
Загрузка дробилок должна быть механизирована. При подаче материалов в дробилки (щековые валковые) над их загрузочными отверстиями должны быть установлены прочные металлические решетки из прутьев с размером ячеек 150х150 мм.
Камнедробилки должны быть оборудованы механизмами для подъема плит и щек а также специальными приспособлениями (крючками) для удаления из зева заклинивающих негабаритных кусков камней.
Во избежание выброса кусков дробленого материала из камнедробилок загрузочные отверстия конусных дробилок должны закрываться глухими съемными ограждениями.
Щековые камнедробилки должны иметь боковые глухие ограждения высотой не менее 11 м.
Приемный бункер должен быть огражден с трех сторон (с боков и со стороны противоположной загрузочной стороне) прочными перильными ограждениями высотой 11 м.
Перед приемным бункером должен быть закреплен упорный брус ограждающий движение автосамосвала задним ходом.
Подъезды разгрузочные площадки приемных бункеров камнедробильной установки должны иметь спланированную поверхность обеспеченный водоотвод.
Разгрузочные площадки приемных бункеров должны иметь звуковую и световую сигнализацию для оповещения о приближении транспортных средств.
На разгрузочной площадке не должно быть посторонних предметов просыпей и завалов горной массы.
При приближении транспортных средств к приемному бункеру рабочие должны отойти в сторону на расстояние не менее 2 м.
Перед разгрузкой необходимо убедиться в отсутствии людей в бункере и на питателе подать сигнал разгрузки и произвести выгрузку горной массы.
Мостики и лестницы ведущие к местам осмотра камнедробилок должны быть металлическими с рифленой поверхностью и не располагаться над зевом дробилки. Переносные лестницы должны быть прочны надежны и оборудованы подстраховочными приспособлениями.
Проходы вокруг дробилок двигателя и других механизмов должны быть шириной не менее 10 м.
Проходы под конвейерами грохотами и другими агрегатами и механизмами должны быть сверху ограждены прочными и надежно закрепленными кожухами сплошными настилами с козырьками.
Места выхода дробленого материала на конвейеры или элеваторы должны быть ограждены прочно укрепленными защитными кожухами.
Разгрузочные желоба камнедробилок должны иметь регулируемый наклон обеспечивающий плавность прохождения материала и устраняющие образование подпора дробленого материала в бункере из-под дробилки.
Для разбивки негабаритных камней кусков сырья должно быть оборудовано специальное рабочее место защищенное от атмосферных осадков и ветра.
Металлическая решетка для разбивки должна быть надежно закреплена. Рабочий обязан работать в спецодежде спецобуви и предохранительных средствах. Стекла очков должны иметь металлическую защитную решетку.
Производить разбивку негабаритных камней вне оборудованного рабочего места и без защитных средств запрещается.
Допуск дробильщиков в нетрезвом состоянии на рабочее место запрещается. Дробильщики оказавшиеся при исполнении служебных обязанностей в нетрезвом состоянии немедленно отстраняются от работы и привлекаются к строгой ответственности в соответствии с действующим законодательством.
Дробильщик обязан содержать свое рабочее место и зону обслуживания в чистоте и порядке.
Пользоваться водой для питья необходимо из специальных закрытых баков с фонтанирующимися насадками или газированной водой.
Работа дробильно-сортировочной установки при грозе должна быть приостановлена.
За невыполнение требований инструкции по охране труда разработанной на основе данной типовой инструкции дробильщик несет ответственность согласно правилам внутреннего трудового распорядка и действующему законодательству об охране труда.
2 Требования безопасности перед началом работы
Перед началом работы дробильщик обязан:
- надеть спецодежду и спецобувь подготовить средства индивидуальной защиты проверить их исправность;
- ознакомиться с условиями работы предыдущей смены;
- получить на рабочем месте точные и конкретные указания от бригадира (мастера) по выполнению задания безопасным приемам и методам труда;
- ознакомиться с технологической картой производства работ.
- исправность телефонной связи и освещения;
- наличие и исправность комплекта инструментов и принадлежностей;
- наличие необходимых средств пожаротушения и оказания первой доврачебной помощи.
Перед пуском камнедробилки дробильщик обязан проверить:
- исправность звуковой и световой сигнализации;
- наличие и целостность заземления путем наружного осмотра;
- исправность системы гидрообеспыливания и герметизации укрытий пылящих точек;
- состояние крепления болтовых соединений всех частей и узлов фундаментных болтов;
- наличие в достаточном количестве масла в системе подшипников и других трущихся узлах камнедробилки;
- исправность защитных ограждений и предохранительных приспособлений;
- состояние электрооборудования и электроприводов блокировочных устройств;
- надежность и исправность рычагов включения обеспечивающих плавность включения и исключающих самопроизвольное переключение с холостого хода на рабочий;
- техническое состояние шкивов зубчатых и других передач рамы плит дробления и других деталей;
- работу грузоподъемных механизмов и захватных приспособлений для удаления негабаритных камней из камнедробилки и конвейера;
- исправность решетки и козырька загрузочного отверстия. При выявлении неисправности электродвигателя пусковых устройств нарушения изоляции открытых токоведущих частей электрооборудования заземления дробильщик должен немедленно доложить мастеру для устранения неисправностей.
Дробильщику запрещается устранять неисправности электротехнического оборудования камнедробилки.
Другие неисправности кроме электротехнических дробильщик должен устранять своими силами а при невозможности - доложить мастеру (механику).
Дежурному электротехнику восстановить и проверить отключенную систему энергообеспечения за счет постановки на место распределительных щитов и пускового устройства.
О всех замеченных и выявленных неисправностях камнедробилки дробильщик должен доложить мастеру. До устранения неисправностей и разрешения мастера пуск камнедробилки запрещается.
3 Требования безопасности во время работы
Пуск камнедробилки (установки) дробильщик должен производить через 1-2 минуты после подачи общего сигнала о начале работы дробильно-сортировочной установки (завода).
Подачу предупредительных сигналов о запуске камнедробилки (установки) производить только с разрешения мастера смены.
Всякий непонятный сигнал должен восприниматься дробильщиком как сигнал "Стоп!
Эксплуатация дробилки производится в соответствии с действующей инструкцией завода-изготовителя.
После пуска дробилки дробильщик должен проверить ее работу на холостом ходу до достижения нормальной работы. При появлении ненормального стука и шума необходимо дробилку выключить и доложить мастеру об ее неисправности и не включать до устранения неисправностей.
Во время ведения технологического процесса дробления дробильщик обязан:
- содержать в рабочем состоянии камнедробилку питатели и конвейеры подающие сырье или материалы и обеспечивать их бесперебойную работу;
- проводить только заданный технологический процесс дробления;
- обеспечивать выпуск качественной продукции заданных фракций;
- регулировать подачу сырья и воды на орошение;
- вести наблюдение за сигналами и подавать необходимые сигналы по ведению технологического процесса иметь постоянную связь со смежными участками;
- не допускать присутствия посторонних лиц в рабочей зоне;
- подготавливать пробы продукции для лабораторного анализа;
- управлять подъемно-транспортным оборудованием при строповке и извлечении негабаритных камней и посторонних предметов из дробильной камеры.
- подавать сырье в камнедробилку только после набора электродвигателем полных оборотов;
- не допускать попадания на конвейер и камнедробилку негабаритных камней и посторонних предметов.
Запрещается работа на камнедробилке при:
- отсутствии предохранительных приспособлений;
- ослаблении шпонок у зубчатых колес шкивов или маховиков а также ослаблении крепежных болтов;
- повреждении пружины натяжения у щековых дробилок;
- ослаблении крепления дробящих плит;
- отсутствии предохранительных шпилек к муфте приводного шкива камнедробилки;
- образовании трещин и сколов станины дробящих плит и других деталях;
- нарушении устойчивости камнедробилки и повышении вибрации.
Во время работы камнедробилки дробильщику запрещается:
- допускать посторонних лиц в рабочую зону;
- загромождать подходы к камнедробилке проходы к агрегатам;
- засорять рабочую площадку;
- становиться на камнедробилку;
- класть инструмент и другие предметы на корпус и ограждения камнедробилки;
- оставлять без присмотра закрепленные за ним машины и механизмы и отлучаться с рабочего места без разрешения мастера смены или бригадира;
- допускать к машинам и механизмам лиц не связанных с их эксплуатацией или обслуживанием;
- отвлекаться от работы и заниматься другими делами.
При ведении технологического процесса дробления запрещается:
- подтягивать и поправлять болты пружины и другие детали;
- регулировать размер разгрузочной щели;
- снимать и устанавливать ограждения;
- надевать или снимать ремни передач;
- смазывать подшипники вручную;
- производить очистку дробилки и уборку рабочего места;
- заглядывать в зев дробилки;
- проталкивать или вытаскивать заклинившиеся во время дробления куски камня или посторонние предметы. Для этого необходимо пользоваться только специальными приспособлениями не допуская использования для этих целей случайных предметов.
Указанные работы разрешается выполнять только после полной остановки камнедробилки и смежных с ней агрегатов отключенных от электросети силовых установках снятых электрослесарем предохранителях или изъятых вилок разрыва пусковых устройств. На пусковых устройствах необходимо вывесить плакат "Не включать - работают люди!
Не разрешается производить дробление негабаритных камней в зеве дробилки с помощью кувалд. Эту работу необходимо производить на специальном рабочем месте на металлической решетке.
Находясь на рабочем месте дробильщик должен:
- быть внимательным ко всем предупредительным и запрещающим знакам установленной сигнализации;
- незамедлительно подавать необходимые установленные сигналы;
- иметь в рабочей зоне необходимые предупредительные и запрещающие знаки;
- следить за сохранностью ограждений плакатов по охране труда предупредительных и запрещающих знаков установленных и вывешенных в рабочей зоне на видном месте.
При любых работах связанных с ремонтом камнедробилки дробильщик должен иметь наряд-допуск на производство ремонтных работ.
Ремонт производится только после полного отключения камнедробилки и всех смежных механизмов от электродвигателей изъятии электрослесарем предохранителей и вилок разрыва пускового устройства.
Должен быть полностью исключен случайный пуск камнедробилки или смежных механизмов.
На пусковых устройствах должны быть таблички:
“Не включать - работают люди!
Включить установленный световой сигнал запрещающий пуск смежных механизмов и камнедробилки.
Выполнение ремонтных работ производить в спецодежде спецобуви с применением предохранительных средств (предохранительных поясов очков).
Над загрузочным отверстием дробилки должен быть устроен временный настил с козырьком исключающий падение различных предметов на людей работающих в зоне ремонта дробилки.
Дробильщик и другие рабочие выполняющие ремонтные работы на высоте более 13 м в случае отсутствия подмостей должны пользоваться специальными металлическими лестницами и исправными предохранительными поясами. Место закрепления предохранительного пояса указывается руководителем работ.
При производстве ремонтных работ присутствие мастера обязательно.
При выполнении ремонтных работ дробильщик обязан:
- пользоваться исправным набором инструментов. Молотки и кувалды должны быть прочно насажены на деревянные ручки и не иметь трещин выщербин и т.д. Гаечные ключи должны соответствовать размерам гаек;
- при обрубке металла и рубке троса зубилом надевать защитные очки;
- работая зубилом надо становиться так чтобы не нанести осколками металла травмы себе и товарищам.
Ремонтные работы производить только при условии нормального освещения места работы.
Выполнение ремонтных работ при грозе запрещается.
По окончании работ дробильщик обязан проверить не осталось ли на дробилке инструмента и других предметов.
Пуск камнедробилки и других агрегатов в работу после ремонта и опробования на холостом ходу дробильщик должен производить под руководством мастера или механика производившего ремонтные работы.
4 Требования безопасности в аварийных ситуациях
В случае внезапной остановки камнедробилки необходимо немедленно выключить электродвигатель.
При появлении ненормальных стуков увеличении вибрации неравномерной работы застревании негабаритных камней и посторонних предметов дробильщик обязан немедленно выключить силовые установки и прекратить технологический процесс не дожидаясь окончания дробления сырья находящегося в дробильной камере. О создавшейся ситуации немедленно доложить мастеру.
Удаление застрявших в дробильной камере негабаритных камней посторонних предметов очистку камеры от непереработанного сырья а также уборку крупных камней с питателей камнедробилки производить только с применением подъемно-транспортных механизмов и приспособлений. Эти работы разрешается производить только после полной остановки дробилки и питающих ее систем при отключенных от сети электродвигателях снятых электрослесарем предохранителях или изъятых вилок разрыва пускового устройства включенной световой аварийной сигнализации и установке на пусковом устройстве плаката "Не включать - работают люди!
Очистка зева дробилки и разгрузочной щели от застрявшего в ней материала осуществляется только сверху. Указанные работы а также резка и извлечение попавшего в камнедробилку металла производятся только под наблюдением мастера или механика.
При нарушении всей установленной сигнализации или одной из них дробильщик должен прекратить работу и о причине остановки доложить мастеру.
При несчастных случаях подать сигнал аварийной остановки остановить работу дробилки и приступить к оказанию доврачебной помощи пострадавшему. При необходимости вызвать врача.
Пуск камнедробилки и обслуживающих ее агрегатов после устранения аварийной ситуации производить только после разрешения мастера или механика в установленном порядке.
5 Требования безопасности по окончании работы
После поступления общего сигнала об окончании работы дробильно-сортировочной установки дробильщик обязан:
- подать через 1-2 минуты световые и звуковые сигналы об окончании приема материала и окончания работы;
- прекратить подачу камня в бункер питателя;
- закончить переработку всего загруженного в бункер питателя каменного материала;
- разгрузить переработанный материал;
- прекратить подачу воды;
- при работе зимой слить воду из водяных камер;
- полностью отключить камнедробилку и смежные агрегаты с изъятием электрослесарем плавких предохранителей и вилок разрыва пускового устройства.
На время уборки осмотра и обслуживания камнедробилки вывесить табличку "Не включать - работают люди!
Очистить от сырья материала и мусора камнедробильную установку рабочее место подходы и проходы.
При невозможности или неудобстве очистки камнедробилки в огражденных местах допускается временное снятие ограждений которые после необходимой очистки устанавливаются на место и надежно закрепляются.
После очистки дробильной установки следует проверить:
- ременные и цепные передачи; при необходимости отрегулировать их;
- корпус и рабочие органы камнедробилки (износ трещины сколы) крепление деталей и узлов;
- состояние конвейеров питателей приемного бункера.
Выявленные при осмотре неисправности следует устранить а в случае невозможности ликвидации их своими силами доложить об этом мастеру.
После очистки осмотра и устранения неисправностей дробильной установки необходимо произвести смазку всех узлов и агрегатов.
Если по окончании работы дробильно-сортировочной установки не производится централизованное отключение агрегатов от электросети то дробильщик должен убрать в определенное место в рабочей кабине снятые электротехником пусковые устройства и распределительные щиты.
Проверить комплектность инструмента и принадлежностей и убрать в отведенное место в рабочей кабине.
Проверить и привести в порядок средства индивидуальной защиты и предохранительные приспособления.
Спецодежду спецобувь и защитные средства дробильщик должен хранить в шкафу отдельно от повседневной одежды.
Принять душ или вымыть лицо и руки теплой водой с мылом переодеться.
Доложить мастеру об окончании работы и работе камнедробилки в течение смены закрыть замком рабочую кабину и передать ключ дежурному.
При сменной работе дробильно-сортировочной установки передать смену сменщику информировать его о работе камнедробилки поступающем материале записях в журнале работы камнедробилки возможных случаях возникновения аварийной ситуации нарушениях охраны труда и принятых мерах. Передать ключ от рабочей кабины сменщику.
Сдачу и принятие смены производить в присутствии сменного мастера или бригадира
6 Охрана окружающей среды
Главными вредными производственными факторами на валковой дробилке является повышенная запыленность атмосферы производственные шумы вибрация что оказывает отрицательное воздействие на окружающую среду.
Уменьшение производственных шумов может осуществляться как за счет улучшения конструкции дробилки и ее узлов так и за счет улучшения технической эксплуатации дробилки своевременного ремонта оборудования применения звукопоглощающих (мягких) футеровок установки кожухов глушителей шума. Существенное уменьшение производственных шумов происходит при автоматизации управления процессом когда оборудование и обслуживающий персонал размещаются в различных изолированных друг от друга помещениях.
Для защиты от воздействия вибраций применяют виброизоляцию которая может быть активной и пассивной. Активная виброизоляция ставит своей целью уменьшение колебаний фундамента на котором установлено оборудование являющееся источником колебаний или сотрясений. Для этого между фундаментом и машиной укладывают виброизолирующие прокладки. При пассивной виброизоляции применяют виброизолирующие площадки. При этом рабочие должны иметь специальную противовибрационную одежду – ботинки и рукавицы в которых изолирующим материалом служит мягкая крупнопористая резина.
Наиболее действенным способом уменьшения запыленности атмосферы является герметизация пылящих объектов в сочетании с системами пылеудаления путем отсоса загрязненного воздуха или его обеспыливания гидравлическими брызгальными устройствами.
При концентрации пыли в удаляемом воздухе свыше 10 мгм3 выбрасываемый в атмосферу воздух должен очищаться в циклонах.
При выполнении данного курсового проекта я получил теоретические навыки по валковым дробилкам а также ознакомился с методикой расчета основных параметров дробилки её привода. Данная курсовая работа была направлена на модернизацию дискозубчатого валка дробилки СМД-153.
Все разработки направлены на повышение производительности и подавление вибраций при переработке материала уменьшение материалоемкости снижению себестоимости повышение экономичности.
Инженер–механик при создании новых машин механизмов инструмента и другой продукции большое внимание отводится вопросам улучшения условий труда обслуживающего персонала а именно механизации и автомати-зации опасных и трудоемких процессов улучшению ремонтопригодности повышению долговечности машин.
Список использованных источников
Клушанцев Б.В.Дробилки. Конструкция расчет особенности эксплуатации Б.В. Клушанцев А.И. Косарев Ю.А. Муйземнек. – М. : Машиностроение 1990. – 320 с.: ил.
А. с. 1389841 СССР МПК5 B 02 C 430. Валов валковой дробилки Ф.Л. Лаевский Г.А. Недзвецкий В.Д. Лагода В.Г. Нестеренко и А.Е. Тарасенко (СССР). – № 415288025-33 заявл. 28.11.86; опубл. 23.04.88 Бюл. № 15 – 4 с.; ил.
А. с. 1360790 СССР МПК5 B 02 C 408. Валковая дробилка А.Н. Суворов (СССР). – № 403203929 заявл. 06.03.86; опубл. 23.12.87 Бюл. № 47 – 2 с.; ил.
А. с. 1304868 СССР МПК5 B 02 C 430. Валок дробилки В.П. Нерадов В.Д. Герасимов Е.Д. Горбунов Г.А. Курочкин А.С. Матренин И.К. Шилько и А.А. Кириченко (СССР). – № 380140929-33 заявл. 17.10.84; опубл. 07.04.86 Бюл. № 113 – 2 с.; ил.
Иванов М.Н. Детали машин: Учеб. для студентов вузов Под ред. В.А.Финогенова. – 6-е изд. перераб. – М.: Высш. шк. 2000. – 383 с.: ил
Курмаз Л.В. Детали машин. Проектирование: Справочное учебно-методическое пособие Л.В. Курмаз А.Т. Скойбеда. – 2-е изд. испр.: Высш. Шк 2005. -309 с.
Кузьмин А. В. Справочник по расчетам механизмов подъёмно-транспортных машин А. В. Кузьмин Ф. Л. Марон. – Минск: Выш. шк. 1983. – 350 с.