Дезинтегратор


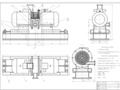
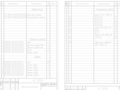
- Добавлен: 25.10.2022
- Размер: 429 KB
- Закачек: 2
Описание
Состав проекта
![]() |
![]() ![]() ![]() |
![]() ![]() ![]() |
![]() ![]() ![]() |
![]() ![]() ![]() |
![]() ![]() ![]() ![]() |
![]() ![]() ![]() |
![]() ![]() ![]() ![]() |
Дополнительная информация
1Общие сведения и классификация .docx
По характеру соприкосновения размалываемого материала и мелющих тел помольные агрегаты принципиально можно разделить на три основные группы:
-агрегаты в которых мелющие тела соприкасаются между собой и с размалываемым материалом (шаровые и вибромельницы трамбовочные дробилки и т. д.);
-агрегаты в которых размалываемый материал соприкасается с мелющими телами последние же между собой не соприкасаются (щековая дробилка дезинтеграторы дисмембраторы);
-агрегаты в которых частицы размалываемого материала соприкасаются в основном только между собой (пневматические мельницы дезинтеграторы специальной конструкции).
Теоретически возможно сконструировать агрегаты последней группы которые по эксплуатационной стойкости и энергопотребности будут самыми экономичными.
Типы дезинтеграторов целесообразно классифицировать:
Классификация по эффекту размельчения:
а) Смесительные дезинтеграторы.
Они имеют минимальный размольный эффект но совместная обработка в них компонентов смеси обеспечивает требуемую гомогенность смеси; при коэффициенте размалываемости материала равном 1 прирост удельной поверхности 50 смг. Такие дезинтеграторы используются при гомогенизации смесей для силикатного кирпича цемента песка стекла и т. п.
б) Помольные дезинтеграторы.
Обеспечивают при коэффициенте размалываемости материала 1 прирост удельной поверхности от 200 до 1000 смг требуемую технологическую активизацию и хорошую гомогенность смеси во взвешенном состоянии. Применяются для приготовления различных видов силикальцитных смесей.
в)Дезинтеграторы тонкого помола.
Обеспечивают при коэффициенте размалываемости L прирост удельной поверхности > 1000 см2г имеют более высокий эффект активизации и гомогенизации чем помольные дезинтеграторы. Применяются для приготовления смесей самых высокопрочных силикальцитных газо- и пеносиликальцитных изделий.
Классификация по конструкции:
а)Пальцевые ситовые и желобчатые дезинтеграторы.
Пальцевые можно подразделить на пальцевые двухстороннего крепления у которых пальцы одним концом закрепляются к диску другим к кольцу и пальцевые одностороннего крепления у которых пальцы проходят через диск и прикрепляются к нему а другие концы пальцев остаются свободными.
В 1951 г. было предложено заменить круги пальцев решетками из перфорированной листовой стали. Под действием центробежных сил размалываемый материал должен покрывать внутреннюю поверхность решеток (сит). Между отверстиями на ситах должны образовываться скопления (кучки) размалываемого материала высота и форма которых в основном зависят от угла внутреннего трения материала и величины центробежной силы (Рис. 237). Когда высота кучек материала превысит определенную величину часть материала скатывается с кучек песка в отверстия сита предотвращая забивку установки. Размалываемый материал проходя под действием центробежных сил через отверстия сита и ударяясь о кучки материала другого сита должен дробиться так же как это происходит в пальцевом дезинтеграторе. При этом теоретически должен размалываться материал кучек и материал ударяющийся о них (выходящий из отверстий сит другого барабана).
В данном случае расход металла должен быть значительно меньше чем в обычном дезинтеграторе так как здесь песок ударяется в основном о песок а не о сталь.
В 1951 г. был изготовлен опытный экземпляр такого дезинтегратора и проведены его испытания. При помоле в нем песка карьера завода «Кварц» была получена средняя удельная производительность 56 мвт-ч. После пропуска 45 м3 песка оказалось что расход металла сит составил 37 кг. При приросте удельной поверхности песка 256 смг удельный износ сит составил в среднем 31 мгм. Высокий износ происходил потому что препятствующие износу кучки песка не удерживались между отверстиями сит на поверхности барабанов из-за вибрации сит. Это подтверждается тем что на участках близких к дискам где вибрация сит была меньше их поверхность не истиралась.
Хотя эти опыты и не дали лучших показателей по износу металла в сравнении с пальцевым дезинтегратором но они позволяют полагать что при усовершенствовании конструкции ситового дезинтегратора можно получить более износостойкий помольный агрегат чем пальцевый дезинтегратор. Такой новой конструкцией может быть кругложе-лобчатый дезинтегратор (Рис. 2). Слой размалываемого песка скопляющийся в желобах такого дезинтегратора защищает от износа прикрепленные к диску стальные кольца в то же время зерна ударяются о размалываемый материал скопляющийся в желобах и проходящий через них дальше. Теоретически в ситовом и желобчатом дезинтеграторах должны происходить все процессы активизации и гомогенизации необходимые для приготовления силикальцитных смесей. Желобчатый дезинтегратор пока еще не создан.
Трудно предсказать также в какой мере например принцип электрогидравлического размельчения а также размельчения при помощи высоких частот и другие способы могут быть применимы и насколько они будут эффективны в производстве силикальцита.
2 Назначение и область применения дезинтегратора
Дезинтеграторы применяют для измельчения зернистых мелкокусковых материалов влажностью 9-10%: сухой глины комовой извести трепела мела мягкого известняка и других мягких материалов. При влажности материала более 10% производительность машин снижается.
Тонкость помола в дезинтеграторе зависит от величины загружаемых кусков материала числа рядов пальцев-бил и скорости их вращения. Более тонкий помол достигается за счет увеличения числа рядов бил на роторе увеличение числа оборотов ротора и уменьшения крупности подаваемого материала.
4Определение диапазона рабочих частот вращения.docx
ротора дезинтегратора
В процессе вращения ротора отрезок цепи занимает радиальное положение под действием центробежной силы:
где m - масса вращающегося отрезка цепи кг;
w - угловая скорость вращения с
R - радиус вращения центра тяжести цепи м.
Для того чтобы в процессе вращения цепь заняла радиальное положение необходимо чтобы центробежная сила превысила силу тяжести цепи: F > Fт
где Fт – сила тяжести.
Для нахождения минимального значения частоты вращения при котором будет возможна работа механизма в холостом режиме (без нагрузок) приравняем силу тяжести цепи уравнению центробежной силы:
После подстановки соответствующих значений был получен результат: n = 51 обмин. Т. е. чтобы цепи приняли радиальное положение необходимо чтобы вал вращался с частотой не менее 51 обмин.
Для узла крепления были рассчитаны напряжения среза и изгиба:
— напряжение среза: Тау = (2 · F) ( · d²)
где d - диаметр оси узла крепления м. — напряжение изгиба: = M W
где M - изгибающий момент Н · м
W - момент сопротивления сечения м³.
Т. к. с увеличением частоты вращения ротора двигателя напряжения изгиба и среза будут увеличиваться было найдено максимальное значение частоты вращения при котором материал цепи будет выдерживать соответствующие напряжения. Материал цепи - сталь 40х для неё были найдены максимальные значения напряжений. Построены графики зависимости центробежной силы напряжения среза и напряжения изгиба от частоты вращения.
Рисунок 4 — График зависимости центробежной силы от частоты вращения ротора
Рисунок 5 — График зависимости напряжений среза от частоты вращения ротора
Рисунок 6 — График зависимости напряжений изгиба от частоты вращения ротора
Построена таблица отображающая значения угловой скорости центробежной силы напряжения среза изгиба и изгибающего момента в зависимости от частоты вращения. По ней было определено что предел напряжений среза в заданном диапазоне частот не достигается т. е. им можно пренебречь. А значение предела напряжений изгиба лежит в диапазоне 1300 - 1400 обмин. Найдя точное значение частоты вращения при максимальных изгибающих напряжениях я получил диапазон частот вращения в котором будет достигаться стабильное вращение ротора с цепями в радиальном положении: (51- 1380) обмин.
3Расчет.docx
1 Расчет производительности дезинтегратора
Производительность дезинтегратора V час вычисляют по формуле:
где V - производительность дезинтегратора м3час
b - длина пальцев внутреннего круга м
а - расстояние между пальцами во внутреннем круге м
n - число оборотов внутренней корзины в минуту
k - число пальцев внутреннего (наименьшего) круга.
2 Расчет конструктивных размеров дезинтегратора
Диаметры рядов пальцев и радиусы данного дезинтегратора имеют размеры:
На рис. 7 показано минимальное расстояние P1P2 между центрами второго ряда при котором песчинка имела бы возможность пройти его не задев пальцев если бы второй ряд пальцев был неподвижен. Пренебрегая величиной песчинки р=0 и принимая количество оборотов обеих корзин равным n1=n2 находим максимальные расстояния между пальцами для трех следующих друг за другом рядов пальцев по формуле:
Рисунок 6. Детали корзины дезинтегратора:
а - два соседних пальца круга; б - круг пальцев корзины.
Рисунок 7. Схема движения песчинки между пальцами дезинтегратора
где P1 P2 - максимальное расстояние между центрами двух соседних пальцев круга т мм
Rm - радиус круга пальцев т-1 мм
Rm-1 - радиус круга пальцев т-1 мм
r - радиус пальцев одинаково принятый для всех кругов пальцев мм
i- число обмин круга пальцев т-1
nm-1 - число обмин круга пальцев m-1
Расстояние между пальцами (a+d) следует принять меньше чем найденные теоретические максимальные расстояния. Пусть оно будет в пределах между 22 и 24 мм - такое при котором число пальцев в круге дало бы целое число.
Ориентировочную длину пальца на первом круге находим по формуле
где b - длина пальцев внутреннего круга м
а - расстояние между пальцами во внутреннем круге м;
п - число оборотов внутренней корзины в минуту
k - число пальцев внутреннего (наименьшего) круга
V - производительность дезинтегратора.
3 Расчет энергопотребности дезинтегратора.
Величину находим по формуле:
где D-диаметр соответствующего круга пальцев.
Энергопотребность дезинтегратора вычисляем по формуле:
где Р1Р2 - теоретическое среднее расстояние между пальцами мм
(a+d) - расстояние между пальцами мм
G - количество материала пропускаемого через дезинтегратор тчас
n- число оборотов корзины
Энергопотребность дезинтегратора нетто составит 081*035=0284 кВт
Расход энергии брутто определится по формуле:
где Е - энергопотребность дезинтегратора нетто. Расход энергии распределяется между корзинами следующим образом по формуле:
где W ВН - мощность электродвигателя внутренней корзины
WH - мощность электродвигателя наружной корзины
D1 D3 DN-1 - диаметры кругов пальцев внутренней корзины
D2 D4 DN-2 DN - диаметры кругов пальцев наружной корзины
Следовательно мощность электродвигателя внутренней корзины должна быть не менее 0148 кВт а наружной - не менее 0248. С учетом количества загружаемого материала его физико-химических свойств а также обеспечения заданной производительности выбираем два электродвигателя мощностью 11 кВт каждый.
содержание.doc
2Назначение и область применения дезинтегратора
Описание процессов происходящих в дезинтеграторе
Расчет основных технологических и конструктивных параметров
1 Расчет производительности дезинтегратора
2 Расчет конструктивных размеров дезинтегратора
3 Расчет энергопотребности дезинтегратора
Определение диапазона рабочих частот вращения ротора дезинтегратора
Спецификации додел1.dwg

КР ППСМ-08.035.00.00.00СБ
Воронка разгрузочная
КРППСМ-08.035.01.00.00
КРППСМ-08.035.02.00.00
КРППСМ-08.035.04.00.00
КРППСМ-08.035.03.00.00
КРППСМ-08.035.05.00.00
КРППСМ-04.070.00.00.05
КРППСМ-08.035.00.00.03
КРППСМ-04.070.00.00.04
КРППСМ-08.035.00.00.02
КРППСМ-08.035.00.00.01
КРППСМ-04.070.00.00.06
Стандартные изделия
КР ППСМ-08.035.00.00.00ПЗ
Пояснительная записка
2описание процесса.docx
Дезинтегратор (рис.3) состоит из двух входящих друг в друга барабанов каждый из которых имеет собственный приводной вал в подшипниках смонтированных на одной раме. Барабан состоит из диска 8 на котором по концентрическим окружностям укреплены пальцы 9. По мере удаления от центра расстояние между пальцами уменьшается. Диск в свою очередь прикреплен к ступице 5 сидящей па приводном валу 4. Ряды пальцев одного барабана находятся между рядами пальцев другого. Барабаны вращаются в противоположных направлениях. Частота вращения ротора дезинтегратора 1000-3000 обмин. Цикл помола в дезинтеграторе практически отсутствует.
Рис 3. Дезинтегратор
— станина; 2 — стойки с подшипниками; 3 — шкив; 4 — вал; 5 — ступица; 6 — приемная воронка; 7 — кожух; 8 — диск; 9 — вальцы.
Подлежащий измельчению материал поступает через воронку 6 в центральную часть одного из барабанов и попадает между движущимися навстречу друг другу пальцами. Продвигаясь от центра к периферии барабанов частицы многократно ударяются о пальцы и разрушаются при этом интенсивность разрушения нарастает поскольку уменьшается шаг между пальцами а окружная скорость их возрастает. Чем выше скорость вращения барабанов чем больше рядов и пальцев на дисках тем выше степень измельчения материала.
Схема движения частиц материала между пальцами дисков показана на рис. 4. Частица т попавшая в дезинтегратор сначала сталкивается с пальцами первого (внутреннего) ряда и разрушается. Осколки отбрасываются по касательной к окружности вращения этого ряда и сталкиваются с идущими навстречу пальцами второго ряда. После разрушения получаются вторичные осколки которые также отбрасываются по касательной к окружности вращения второго ряда пальцев и сталкиваются с пальцами третьего ряда. Осколки из третьего ряда попадают в четвертый и т. д.
Измельченный материал выбрасывается в кожух дезинтегратора и спускается вниз к выходному штуцеру.
Если справедливо принятое ранее допущение о постоянной
степени измельчения материала одного и того же технологического
состава при однократном его разрушении то минимальная степень измельчения частицы в дезинтеграторе будет равна вели-
чине измельчения при однократном разрушении а0 в степени п
равной числу рядов пальцев в обоих барабанах т.е . Однако
фактически число столкновений частиц с пальцами а следовательно и степень измельчения в дезинтеграторе будет значительно
выше чем .Эта особенность дезинтеграторов и позволяет при-
менять их для тонкого измельчения материала.
Рис. 4. Схема движения материала в дезинтеграторе
В зависимости от размера дезинтегратора число концентрических рядов пальцев па одном барабане колеблется от 2 до 4 и следовательно на двух барабанах от 4 до 8 рядов. Пальцы барабанов изготовляют из стали бронзы дюралюминия или другого материала. Диаметр и длина пальцев определяются конкретным назначением и размером машины.
Самым уязвимым местом дезинтегратора являются пальцы барабанов. Они сравнительно быстро изнашиваются а их замена является громоздкой и длительной операцией. Эти недостатки заставляют использовать дезинтеграторы для измельчения хрупких мягких пород с малой абразивностью таких как каолин мел и др.
Дезинтеграторы применяют преимущественно для сухого измельчения материалов как в открытом цикле так и в цикле с сепаратором.
Важным фактором эффективности работы дезинтегратора является скорость вращения барабанов которая зависит от разрушающей скорости удара.
Разрушающая скорость удара представляет собой скорость соударения измельчаемой частицы с пальцами барабанов дезинтегратора при котором частица разрушается. Эта скорость есть геометрическая сумма скорости движения частицы и окружной скорости движения пальца барабана.
Начальная скорость движения частицы т. е. та скорость с которой частица поступает в дезинтегратор по сравнению со скоростью пальцев мала и ею можно пренебречь. В этом случае скорость встречи частицы с пальцами первого ряда будет равна скорости вращения этих пальцев 1. Столкнувшись с пальцами этого ряда частица отлетит от него по касательной к окружности вращения и встретится с пальцами второго ряда движущимися навстречу ей с окружной скоростью 2. Произойдет встречный удар. Скорость этого удара можно найти следующим образом (рис. 5).
Проекция скорости на касательную совпадающую с направлением скорости будет w2 =cos . Но cos = R1R2 и w2 = (R1R2).
Проекция скорости w2 имеет направление противоположное скорости поэтому скорость встречи частицы и пальца
Скорость встречи частиц с пальцами третьего ряда будет
Аналогично для п-го ряда можно записать
Если п 1 и п2 равны между собой то скорость встречи частиц с пальцами будет
Из выражений (1) и (2) следует что скорость удара возрастает с увеличением радиуса вращения пальцев т. е. по мере удаления частиц от оси к периферии барабана и пропорциональна суммарному числу оборотов.
Скорость необходимая для измельчения материала определяется опытным путем.
Следовательно скорость встречи частиц с пальцами барабанов (2) должна быть больше скорости т. е.
Входящий в эту формулу радиус вращения пальца может меняться от RB — радиуса внутреннего ряда пальцев до RH — радиуса наружного ряда. При данном числе оборотов как указывалось выше скорость столкновения частиц с уменьшением радиуса вращения пальцев падает. Чтобы минимальной скорости удара было достаточно для разрушения частиц число оборотов барабанов следует принимать по минимальному радиусу вращения пальцев т. е. по первому ряду пальцев с радиусом вращения R1=R2. Следовательно
Полученное выражение пригодно для расчетов дезинтеграторов при измельчении абсолютно упругих материалов. Для измельчения материалов неупругих имеющих кривую деформации с областью текучести необходимую скорость разрушения определяют опытным путем. Затем находят соотношение между радиусом и числом оборотов барабана дезинтегратора.
Дезинтегратор сборка1.dwg

* Размеры для справок.
Двигатели 4А80А2У3 ГОСТ 19523- 74
Размер частиц готового продукта
Размер частиц исходного материала
Частота вращения роторов
Технические характеристики
Свободное скачивание на сегодня
Другие проекты
- 25.01.2023
- 22.08.2014