Червячный редуктор с внешней конической зубчатой передачей. Курсовой проект




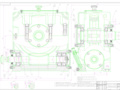
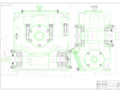
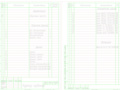
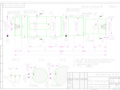
- Добавлен: 25.10.2022
- Размер: 3 MB
- Закачек: 0
Описание
Состав проекта
![]() |
![]() ![]() |
![]() ![]() |
![]() ![]() |
![]() |
![]() |
![]() |
![]() ![]() ![]() ![]() |
![]() ![]() ![]() ![]() |
![]() |
![]() |
![]() ![]() ![]() ![]() |
![]() |
![]() ![]() ![]() ![]() |
![]() ![]() ![]() ![]() |
![]() ![]() ![]() ![]() |
![]() ![]() |
![]() ![]() |
![]() ![]() ![]() |
![]() ![]() |
![]() ![]() |
Дополнительная информация
Первая компоновка-Чертеж.dwg

Редуктор червячный -СборочныйЧертеж(откат2).dwg

Наружные поверхности корпуса окрасить серой эмалью ПФ-115
Плоскость разъема покрыть тонким слоем герметика УТ-34
ГОСТ 24285-80 при окончательной сборке.
Валы редуктора должны проворачивать от руки
Регулировка соединения и зазора в подшипниках регулируется
подбором прокладок поз.11
осуществлять винтами
Передаточное число редуктора 16.
Вращающий момент на тихоходном валу 445
Частота вращения тихоходного вала 90
И-12А; объём - 17 литров.
Тихоходный вал-Чертеж.dwg

* Размер обеспечивается инструментом.
Сталь 45 ГОСТ1050-88
Редуктор червячный - сборочный Спецификация.dwg

Прокладка регулировочная
Болт М8х30 ГОСТ15589-70
Болт М10х35 ГОСТ15589-70
Винт М5х20 ГОСТ11738-84
Винт М14х80 ГОСТ11738-84
Винт М14х90 ГОСТ11738-84
Шайба 10 ГОСТ6402-70
Шайба 14 ГОСТ6402-70
Штифт 6х30 ГОСТ9464-79
Масло И-Л-А-22 ГОСТ 20799-75
Вторая компоновка-Чертеж.dwg

Колесо-Чертеж.dwg

Коэффициент смещения
Межосевое расстояние
Исходный производящий
Число витков сопряженного
сопряженного червяка
. Неуказанные радиусы 3мм
. Неуказанные уклоны 1
Курсовой.doc
Расчёт зубчатых колёс редуктора
Предварительный расчёт валов редуктора
Конструктивные размеры червяка и колеса
Конструктивные размеры корпуса редуктора
Расчет открытой передачи
Первый этап компоновки редуктора
Проверка долговечности подшипников
Второй этап компоновки редуктора
Выбор муфты и шпонок их проверочный расчёт
Уточненный расчёт валов редуктора
Тепловой расчёт редуктора
Выбор сорта масла и сборка редуктора
Машиностроение является ведущей отраслью. От его технического уровня в значительной мере зависят многие остальные отрасли. Курс «Детали машин» объединяет в себе несколько дисциплин: теоретическая механика сопротивление материалов.
Цель курсового проекта - проектирование привода к цепному конвейеру. Практическое использование полученных знаний в приложении к конкретной конструкторской разработке.
НАЗНАЧЕНИЕ И КРАТКОЕ ОПИСАНИЕ ПРИВОДА
Разрабатываемый привод предназначен для обеспечения работы тарельчатого питателя. Схема проектируемого привода приведена на рис.1.
Рис.1. Кинематическая схема привода цепного конвейера.
– коническая (внешняя) зубчатая передача; 2 – упругая муфта со звездочкой; 3 – двигатель; 4 – червячный редуктор; 5 – диск питателя; 6 – загрузочный бункер.
Привод состоит из приводного внешней конической зубчатой передачи редуктора упругой муфты двигателя.
Главной частью данного привода является редуктор. Редуктор – механизм состоящий из зубчатой передачи выполненный в виде отдельного агрегата и служащий для передачи вращения от вала двигателя к валу рабочей машины. Назначение редуктора – понижение угловой скорости и соответственно повышение вращающего момента ведомого вала по сравнению с ведущим. Состоит из корпуса и расположенных в нем элементов передачи: зубчатых колес валов подшипников и т.д.
В данном редукторе используется червячная передача позволяющая разместить входной и выходной валы редуктора под прямым углом друг к другу и обеспечить неподвижность исполнительного механизма при выключенном приводе. Червячная передача существенно сложнее в изготовлении по сравнению с цилиндрическими зубчатыми передачами требует применения антифрикционных материалов (бронз) особенно при высоких скоростях поэтому её применение связано с необходимостью подобного решения (например при невозможности размещения электродвигателя с цилиндрическим редуктором в определённых габаритах).
Коническая зубчатая передача как и червячная значительно сложнее в изготовлении по сравнению с цилиндрическими зубчатыми передачами поэтому её применение связано с необходимостью подобного решения.
Упругая муфта предназначена для передачи вращающего момента с вала двигателя на входной вал редуктора. За счет наличия упругого звена позволяет сглаживать толчки и удары в механизме особенно при пуске – остановке привода работая предохранительным механизмом.
ВЫБОР ЭЛЕКТРОДВИГАТЕЛЯ И КИНЕМАТИЧЕСКИЙ РАСЧЕТ ПРИВОДА
Выбор электродвигателя
Общий КПД привода определяется:
где - КПД открытой конической передачи;
- КПД червячной передачи;
- КПД подшипникового узла.
Угловая скорость вращения бункера
Мощность на приводном валу бункера
Требуемая мощность электродвигателя:
Частота вращения выходного вала привода
Частота вращения вала двигателя
В полученном диапазоне частот вращения двигателей находится большинство двигателей выпускаемых промышленностью. Использование низкоскоростных двигателей с частотами вращения 750 и 1000 обмин нежелательно двигатели с номинальной частотой 3000 обмин использовать тоже не желательно т.к. будут высокие скорости скольжения в червячной передаче что требует использования более дорогих материалов. Поэтому предварительно выбираем двигатель с номинальной частотой вращения 1500 обмин.
Выбираем двигатель 4АМ112М4У3. Основные характеристики двигателя приведены в таблице 1. Общий вид двигателя серии А4 – рис.2.
Основные характеристики двигателя 4АМ112M4У3 Таблица 1.
Номинальная мощность кВт
Синхронная частота вращения мин-1
Номинальная частота вращения мин-1
Рис.2. Электродвигатель серии 4А.
Определение общего передаточного числа и разбивка его по ступеням привода
Общее передаточное число привода
Принимаем передаточное число червячной передачи наименьшим рекомендуемым .
Передаточное число конической зубчатой передачи
Определение вращающих моментов угловых скоростей и частоты вращения валов
Угловая скорость вала двигателя определяется
Момент на валу двигателя
Момент на быстроходном валу редуктора
Момент на тихоходном валу редуктора
Момент на приводном валу бункера
Частота вращения быстроходного вала редуктора
Частота вращения тихоходного вала редуктора
Частота вращения приводного вала бункера
Угловая скорость быстроходного вала
Угловая скорость тихоходного вала
Угловая скорость приводного вала бункера
Результаты кинематического расчета привода сведены в таблице 2.
Основные кинематические данные привода.Таблица 2.
Частота вращения мин-1
РАСЧЕТ ЗУБЧАТЫХ КОЛЁС РЕДУКТОРА
Выбор материалов червяка и зубчатого венца червячного колеса
Выбор материалов для червячной передачи производится исходя из скорости скольжения в зацеплении.
Предварительно скорость скольжения определяется по формуле
Скорость скольжения близка к 5 мс в качестве материала для зубчатого венца червячного колеса применим материалы 1-й группы например бронзу БрО10Ф1 отлитую в кокиль. Для изготовления червяка применим сталь 40ХН с последующими улучшением закалкой ТВЧ и полировкой. Основные механические свойства бронзы БрО10Ф1 и стали 40ХН подвергнутой улучшению и закалке ТВЧ приведены в таблице 3.
Механические свойства материаловТаблица 3.
Определение допускаемых напряжений
Допускаемые контактные напряжения для червячного колеса
где - коэффициент учитывающий износ материала;
- коэффициент долговечности по контактным напряжениям.
Коэффициент долговечности определяется по формуле:
где- действительно действующее число циклов нагружения
где - требуемый ресурс передачи ч.
Коэффициент долговечности:
Допускаемые изгибные напряжения для червячного колеса
где - коэффициент долговечности по изгибным напряжениям.
Коэффициент долговечности по изгибным напряжениям определяется по формуле:
где- действительно действующее число циклов нагружения.
Проектный расчет червячной передачи
Проектным расчетом определяются геометрические параметры передачи (рис.3).
Рис.3. Геометрические параметры червячной передачи.
Межосевое расстояние передачи
Принимаем стандартное значение
Число заходов червяка z1 = 2 для передаточного числа U = 16.
Число зубьев червячного колеса
Принимаем стандартное значение модуля
Коэффициент диаметра червяка
Коэффициент смещения инструмента
Условие выполняется.
Проверим отклонение фактического передаточного числа из условия:
Отклонение фактического передаточного числа
Условие выполняется.
Фактическое межосевое расстояние:
Основные размеры червяка:
диаметр вершин витков
диаметр впадин витков
делительный угол подъёма линии витков
длина нарезаемой части червяка
Основные размеры венца червячного колеса:
диаметр вершин зубьев
наибольший диаметр колеса
диаметр впадин зубьев
радиусы закругления зубьев
условный угол обхвата червяка венцом колеса
Силы действующие в зацеплении приведены на рис.4.
Рис.4. Силы действующие в зацеплении червячной передачи.
Рассчитанные параметры шестерни и колеса сведены в таблицу 4.
Геометрические параметры червячной передачиТаблица 4.
Геометрический параметр
Межосевое расстояние мм
Модуль зацепления мм
Коэффициент диаметра
Делительный угол подъёма витков червяка
Угол обхвата червяка венцом
Число витков червяка
Ширина зубчатого венца мм
Длина нарезаемой части червяка мм
Диаметры червяка мм:
Проверочный расчет червячной передачи
Выполняется для проверки напряжений возникающих в передаче.
Коэффициент полезного действия червячной передачи
где - делительный угол подъёма линии червяка;
- угол трения зависящий от фактической скорости скольжения.
Фактическая скорость скольжения в зацеплении
Угол трения равен 1040.
Проверка контактного напряжения по условию
где - окружная сила в зацеплении Н;
- коэффициент нагрузки;
- уточненные допускаемые контактные напряжения.
Окружная скорость колеса
Условие пригодности по контактному напряжению выполняется.
Проверка изгибающего напряжения по условиям
где - коэффициенты формы зуба;
Эквивалентное число зубьев
Условия прочности по изгибающим напряжениям выполняются.
Результаты расчетов сведены в таблицу 5.
Результаты проверочного расчета передачиТаблица5.
Допускаемые значения
Контактные напряжения МПа
Напряжения изгиба МПа
ПРЕДВАРИТЕЛЬНЫЙ РАСЧЁТ ВАЛОВ РЕДУКТОРА
Предварительный расчет валов производят для ориентировочного определения их размеров. При расчете опираются на величину крутящего момента воздействующего на вал.
Для изготовления быстроходного вала применяется сталь 40ХН. (механические свойства приведены в таблице 3).
Для изготовления тихоходного вала применим сталь 45 (механические свойства стали приведены в таблице 6).
Механические свойства стали 45Таблица 6.
Диаметр вала определяют по формуле
где - допускаемое напряжение на кручение;
- крутящий момент на валу Нмм.
Выходной конец быстроходного вала по условию прочности имеет диаметр
Рассчитываем диаметр вала из условия
Принимаем стандартный диаметр выходного конца вала
Длина выходного конца вала l = 80мм.
Диаметр упорного буртика
Диаметр вала под подшипник
Диаметр вала под подшипник принимаем
Диаметр буртика подшипника
Диаметр буртика подшипника из условия выхода режущего инструмента для нарезания червяка
Ширину буртика подшипника примем длиной 15мм.
Червяк изготавливается как единое целое с валом.
Длины участков вала уточняются при первой компоновке и последующих расчетах.
Диаметр выходного конца тихоходного вала из условия прочности на кручение
Принимаем длину конца вала l = 110мм.
Диаметр упорного буртика подшипника
Упорный буртик подшипника также является посадочным местом для конического колеса.
Диаметр упорного буртика для колеса
Принимаем диаметр упорного буртика
КОНСТРУКТИВНЫЕ РАЗМЕРЫ ЧЕРВЯКА И ЧЕРВЯЧНОГО КОЛЕСА
Предварительно определим геометрические размеры элементов колеса. После предварительной компоновки и уточнения диаметров валов некоторые размеры изменятся. Основные размеры элементов и их соотношения приведены на рис. 8.
Рис. 5. Основные размеры элементов червячного колеса.
Диаметр ступицы редуктора
Толщина венца по диаметру впадин зубьев
Толщина упорного буртика венца
Высота упорного буртика
КОНСТРУКТИВНЫЕ РАЗМЕРЫ КОРПУСА РЕДУКТОРА
В современном машиностроении имеется тенденция к уменьшению количества элементов на наружных поверхностях корпуса редуктора. При использовании корпусов такого типа уменьшаются вибрации и шум возникающие в процессе работы. Облегчается обслуживание редукторов и повышается безопасность производственного процесса.
Толщина стенок корпуса и ребер жесткости определяется исходя из соотношения
Условие не выполняется. Принимаем толщину стенок
Диаметр фундаментных болтов принимаем в зависимости от величины межосевого расстояния при межосевом расстоянии 160мм применяются болты М16.
Для крепления крышки корпуса в основанию – болты М14.
На рис. 18 – 20 указаны варианты исполнения элементов корпуса.
Рис. 6. Опорная лапа редуктора.
Рис. 7. Крепление крышки редуктора.
Рис. 8. Фланец корпуса редуктора.
РАСЧЁТ ОТКРЫТОЙ ПЕРЕДАЧИ
Выбор материала и термической обработки материала зубчатых колес
При выборе материала для шестерни и колеса следует ориентироваться на применение одной и той же стали но с различной термической обработкой чтобы твердость шестерни была не менее чем на 20 30 единиц НВ больше твердости колеса при прямозубых передачах. При значительной разнице диаметров разница в твердости материалов шестерни и колеса может достигать 50 единиц HB.
В качестве материала для шестерни и колеса применим сталь 40ХН с улучшением. При этом твердость шестерни составит 300±10 единиц HB твердость колеса 260±10 единиц HB. Основные механические свойства стали 40ХН подвергнутой улучшению приведены в таблице 3.
Механические свойства стали 40ХНТаблица 7.
Средняя твердость рабочих поверхностей зубьев
Допускаемые контактные напряжения
где - предел контактной выносливости МПа;
Предел контактной выносливости определяется по формуле:
Коэффициент долговечности принимается в пределах для улучшенных сталей. Определяется по формуле:
- базовое число циклов нагружения
Для длительно работающих быстродействующих передач и коэффициент Поэтому для расчета принимаем
Допускаемые изгибные напряжения
где - предел изгибной выносливости МПа;
- коэффициент долговечности по изгибным напряжениям.
Предел изгибной выносливости определяется по формуле
Коэффициент долговечности по изгибным напряжениям принимается в пределах для улучшенных сталей. Определяется по формуле:
Проектный расчет конической зубчатой передачи
Проектным расчетом определяются геометрические параметры зубчатого зацепления (рис.3).
Рис. 9. Геометрические параметры конической зубчатой передачи.
Внешний делительный диаметр колеса
где- коэффициент вида конических колес (для прямозубого колеса); - коэффициент учитывающий распределение нагрузки по ширине венца (для прямозубого колеса).
Ввиду особенности конструкции привода увеличим диаметр колеса. Принимаем стандартное значение
Углы делительных конусов
Внешнее конусное расстояние
Ширина зубчатого венца
где- коэффициент ширины венца.
Принимаем ширину венца
Внешний окружной модуль
где - коэффициент учитывающий распределение нагрузки по ширине венца (для прямозубой передачи);
- коэффициент вида конических колес.
Полученный модуль увеличим на 30% учитывая износ
Из условия что передача является силовой - примем стандартный модуль m = 15мм.
Принимаем для расчета z2 = 60.
Число зубьев шестерни
Фактическое передаточное число
Отклонение от заданного в допустимых пределах выполняется условие:
Действительные углы делительных конусов
Коэффициенты смещения инструмента для шестерни и колеса:
Средний делительный диаметр
Усилия действующие в зацеплении приведены на рис.4.
Рис. 10. Силы действующие в зацеплении конической зубчатой передачи.
Рассчитанные параметры шестерни и колеса сведены в таблицу 8.
Геометрические параметры конической зубчатой
Внешнее конусное расстояние Re мм
Внешний окружной модуль me мм
Ширина зубчатого венца b мм
Внешний делительный диаметр мм
Внешний диаметр окружности вершин мм
Внешний диаметр окружности впадин мм
Угол делительного конуса град.
Средний делительный диаметр мм
Проверочный расчет конической зубчатой передачи
- коэффициент учитывающий распределение нагрузки между зубьями;
- коэффициент динамической нагрузки.
Коэффициент принимается
- коэффициент распределения нагрузки между зубьями;
- коэффициент динамической нагрузки;
- коэффициент учитывающий наклон зубьев.
шестерни коэффициент
Результаты расчетов сведены в таблицу 9.
Результаты проверочного расчета передачиТаблица 9.
На основании результатов проверки: для изготовления шестерини и зубчатого колеса внешнего зацепления можно применить вместо стали 40ХН – сталь 45 с улучшением.
ПЕРВЫЙ ЭТАП КОМПОНОВКИ РЕДУКТОРА
На первом этапе компоновки редуктора определяем взаимное расположение основных элементов расстояния для уточненного расчета валов и расчета подшипников.
ПРОВЕРКА ДОЛГОВЕЧНОСТИ ПОДШИПНИКОВ
Проверку производим на основе первой компоновки редуктора (приложение 1) которая позволяет определить основные размеры для расчёта элементов редуктора. Схема нагружения валов редуктора приведена на рис. 12.
Рис.11. Схема нагружения валов редуктора.
Определим реакции опор валов и построим эпюры нагружения валов редуктора. Эпюры нагружения валов представлены на рис. 12 13.
Нагрузка от воздействия муфты
Рис. 12. Схема и эпюры нагружения быстроходного вала редуктора.
Рис. 13. Схема и эпюры нагружения тихоходного вала редуктора.
При проверочном расчете проверяем выбранные подшипники по величине динамической грузоподъемности.
Осевые реакции подшипников
Схемы сил действующих на подшипники быстроходного вала приведена на рис.15.
Рис.14. Схема «враспор».
Осевая нагрузка действует на подшипник опоры B.
Осевая нагрузка значительно больше радиальной поэтому применим схему с одной плавающей опорой. В качестве фиксирующей опоры применим сдвоенные конические роликовые подшипники с большим углом конусности обозначение 1027308А ГОСТ 27365-87 для плавающей опоры – шариковый радиальный обозначение 308 ГОСТ 8338-75.
Динамическая грузоподъёмность комплекта роликовых подшипников
Коэффициенты для такой опоры
Произведем расчет эквивалентной нагрузки для опоры В.
где - коэффициент безопасности
- температурный коэффициент.
Расчетный ресурс подшипника часов
Условие долговечности выполняется.
Произведём расчет долговечности для подшипника опоры А.
Условие долговечности подшипника выполняется.
Схемы сил действующих на подшипники тихоходного вала приведена на рис.16.
Рис.15. Схема «враспор».
Осевая нагрузка действует на подшипник опоры С.
Расчет проведем для обеих опор: С и D.
Отношение для опоры С
Расчет производим для наиболее нагруженной опоры D.
Эквивалентная нагрузка для опоры D:
Условие долговечности выполнено.
ВТОРОЙ ЭТАП КОМПОНОВКИ РЕДУКТОРА
На втором этапе компоновки уточняются конструктивные размеры элементов редуктора и применяемые конструктивные решения.
На основе второй компоновки принимается окончательное решение о применении тех или иных вариантов решений. Выбираются допуски и посадки для соединений
Допуски и посадки для соединений элементов редуктора выбираем на основании рекомендаций методической литературы. Виды соединений и рекомендуемые допуски и посадки соединений приведены в таблице 10. Некоторые поля допусков для стандартных изделий – не приводятся указываются поля допусков для сопрягаемых с ними деталей.
Допуски и посадки соединений редуктора Таблица 10.
поле допуска отверстия
вал – зубчатое колесо
вал – уплотнительная манжета
вал закаливается и полируется
подшипник – корпус редуктора
стакан – корпус редуктора
крышка подшипникового узла – корпус редуктора крышка - стакан
выходной конец быстроходного вала
выходной конец тихоходного вала
ВЫБОР МУФТЫ И ШПОНОК ИХ ПРОВЕРОЧНЫЙ РАСЧЕТ
Для соединения быстроходного вала редуктора с валом электродвигателя применим упругую муфту с элементом в форме звездочки. Муфты данного типа обладают достаточной упругостью и малым моментом инерции что уменьшает пусковые нагрузки на вал. Также они позволяют компенсировать неточности взаимного расположения валов.
Муфты выбираются из условия
Расчетный момент муфты
где - коэффициент режима работы
Условию удовлетворяет муфта 32.125 ГОСТ 14086 – 76.
Муфты данного типа допускают радиальное смещение валов до 04мм и перекос валов до 10.
Радиальная сила вызванная смещением валов определяется
где - радиальная жесткость муфты Нмм;
- радиальное смещение валов мм.
Расчет проводится для проверки шпонок на смятие по условию
гдеh – высота шпонки мм;
t1 – глубина шпоночного паза на валу мм;
l – рабочая длина шпонки мм.
Шпоночные соединения используются для выходных концов валов и при посадке зубчатого колеса редуктора. Схема соединения представлена на рис. 16. Основные параметры проверяемых соединений приведены в табл.11.
Рис. 16. Схема шпоночного соединения.
Параметры шпоночных соединений Таблица 11.
тихоходный вал – зубчатое колесо
Выходной конец быстроходного вала
Условие прочности выполнено.
Тихоходный вал – червячное колесо
Выходной конец тихоходного вала
УТОЧНЁННЫЙ РАСЧЁТ ВАЛОВ
Уточнённый расчет ведем из условия что коэффициент запаса прочности в опасном сечении
где - коэффициент запаса прочности по нормальным напряжениям;
- коэффициент запаса прочности по касательным напряжениям;
- пределы выносливости в расчетном сечении
- пределы выносливости гладких образцов при симметричном цикле изгиба и кручения
- коэффициенты концентрации напряжения;
- эффективные коэффициенты концентрации напряжения;
- коэффициент влияния абсолютных размеров сечения;
- коэффициент влияния шероховатости.
Для быстроходного вала редуктора опасными сечениями являются:
- ступенчатый переход в месте подшипника опоры А (посадка с натягом канавка под выход шлифовального круга);
– вал под червяком который является концентратором.
В данном сечении действуют два концентратора: канавка под выход шлифовального круга посадка с натягом. Расчет произведем для наиболее опасного концентратора из условия
Для кольцевой проточки
Для посадки с натягом
Расчет производим для посадки с натягом.
Осевой момент сопротивления
Амплитуда нормальных напряжений
Полярный момент сопротивления
Амплитуда касательных напряжений
Коэффициенты концентрации
Пределы выносливости в расчетном сечении
Коэффициенты запаса прочности
Общий коэффициент запаса прочности
Концентратором является ступенчатый переход от буртика подшипника к диаметру впадин
Расчет производим для канавки под выход резца.
Условие прочности выполнено
Для тихоходного вала опасными сечениями являются:
- место посадки червячного колеса на вал (канавка под выход шлифовального круга посадка с натягом шпоночная канавка)
- ступенчатый переход от посадочного места подшипника к упорному буртику (канавка для выхода шлифовального круга посадка с натягом)
– ступенчатый переход от конца вала к посадочному месту подшипника (канавка под выход шлифовального круга посадка шестерни внешней передачи).
В данном сечении действуют три концентратора: канавка под выход шлифовального круга посадка с натягом шпоночный паз. Расчет произведем для наиболее опасного концентратора из условия
Расчет ведем для посадки с натягом.
Изгибающий момент Ми = 362487 Нмм.
Условие прочности выполняется.
ТЕПЛОВОЙ РАСЧЁТ РЕДУКТОРА
Проведём расчет теплового режима редуктора проверим температуру масла в редукторе которая не должна превышать 80-950С.
При непрерывной работе без искусственного охлаждения температуру масла можно определить по формуле:
где - мощность на быстроходном валу редуктора Вт;
- коэффициент теплопередачи ;
- площадь внешней поверхности редуктора без учёта площади основания м2.
Условие температурного режима выполняется. Для уменьшения температуры масла необходимо увеличить наружную площадь редуктора оребрением что увеличит площадь теплоотдачи и позволит снизить температуру масла. При работе в более жестких условиях в помещениях с повышенной температурой – необходимо предусмотреть установку крыльчатки охлаждения.
ВЫБОР СОРТА МАСЛА И СБОРКА РЕДУКТОРА
Для смазки зацепления применим метод окунания колеса в масляную ванну. При этом червяк опускается на глубину
Для смазки при контактных напряжениях менее 200МПа и окружной скорости
рекомендуются масла с кинематической вязкостью 20±4мм2с.
Этим условиям удовлетворяют индустриальные масла И-Л-А-22 (И-12А) И-Л-С-22 (ИГП-14). В качестве замены допустимо использовать масла: Турбинное Тп-22 или Цилиндровое 24.
Недопустимо использовать смеси разных сортов масел.
Для смазки подшипников быстроходного и тихоходного валов применим метод разбрызгивания. Окружная скорость червяка не является достаточной для образования масляного тумана который заполняет объем редуктора. Поэтому для улучшения разбрызгивания на червяк установлены разбрызгиватели. Стекая по стенкам редуктора масло попадает в подшипниковые узлы и обеспечивает их смазку.
Методика сборки редуктора
Сборку редуктора производим по узловой схеме: предварительно собираются отдельные узлы которые собирают в сборочные единицы устанавливаемые в подготовленном к сборке корпусе редуктора.
Сборка быстроходного вала.
На вал напрессовываются разбрызгиватели и подшипники предварительно нагретые в масле до температуры 80-1000С. После охлаждения подшипников на вал устанавливают фиксирующую шайбу и одевают на вал сквозную крышку.Устанавливается шпонка на выходной конец вала.
Сборка тихоходного вала.
В канавку под шпонку червячного колеса устанавливается шпонка. На вал до упора в буртик напрессовывается червячное колесо предварительно нагретое в масле до температуры 80-1000С. Напрессовываются до упора в буртик подшипники предварительно нагретые в масле до температуры 80-1000С. На вал одевается сквозная крышка. Устанавливается шпонка в паз выходного конца.
Наружные части корпуса и крышки перед сборкой покрываются грунтом внутренние части – окрашиваются маслостойкой краской и просушиваются. Фланцы корпуса – не окрашиваются. Удаляются следы краски с контактных поверхностей (фланцы корпуса отверстия для установки подшипников резьбовые отверстия).
На корпус устанавливается крышка с установочными штифтами: проверяется точность обработки отверстий под подшипниковые узлы обработка фланцев. Крышка снимается.
В корпус устанавливаются маслоуказатель и пробка спускного отверстия. Устанавливаются валы и глухие крышки. Подбором прокладок регулируются червячное зацепление и величина тепловых зазоров подшипников опор валов.
Фланец разъема корпуса покрывается герметиком (допускается посадка на краску). Устанавливается крышка и установочные штифты. Устанавливаются и предварительно закручиваются стяжные болты. Устанавливаются болты крышек подшипниковых узлов. Проверяется вращение валов. Стяжные болты корпуса и крепежные болты закручиваются перекрестно с целью избегания перекоса. Устанавливается масляный фильтр и заливается масло до минимального уровня. Уровень масла контролируется по маслоуказателю. Устанавливается и закрепляется винтами крышка смотрового люка.
Проверяется плавность вращения валов. Валы должны проворачиваться от руки с некоторым усилием без заедания. Проверяется наличие подтеков масла через уплотнение сливной пробки. Редуктор обкатывается в течение получаса без нагрузки. После обкатки редуктора – масло сливается.
При необходимости при сборке валов на выходные концы напрессовываются предварительно нагретые в масле полумуфта и шестерня внешней зубчатой передачи.
В ходе работы над курсовым проектом был спроектирован червячный редуктор с внешней конической зубчатой передачи.
При работе над курсовым проектом были рассмотрены методы расчета червячных и конических зубчатых передач методики предварительного и уточненного расчёта валов проверка шпоночных соединений подбора муфт.
В ходе работы над курсовым проектом были разработаны сборочный чертёж редуктора рабочие чертежи тихоходного вала редуктора и червячного колеса.
Чернавский С.А. и др. Курсовое проектирование деталей машин. – М.: Машиностроение. – 1976г.- 608с.
Чернавский С.А. и др. Проектирование механических передач. – М.: Машиностроение. – 1988г.- 416с.
Дунаев П.Ф. Леликов О.П. Курсовое проектирование. М.: Высшая школа 1984г.- 336с.
Штейнблит А.Е. Курсовое проектирование деталей машин. М.: Высшая школа 1991г. - 432с.
Детали машин: Атлас конструкций. В 2-х частях. Ч.1. Под общ. ред. д-ра техн. наук проф. Д. Н. Решетова. М.: Машиностроение. 1992г. - 352с.
Детали машин: Атлас конструкций. В 2-х частях. Ч.2. Под общ. ред. д-ра техн. наук проф. Д. Н. Решетова. М.: Машиностроение. 1992г. - 296с.