Башенный кран г/п 28 т




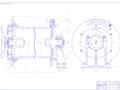
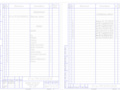
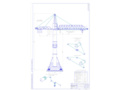
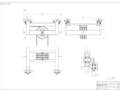
- Добавлен: 25.10.2022
- Размер: 1 MB
- Закачек: 0
Описание
Состав проекта
![]() |
![]() |
![]() ![]() ![]() ![]() |
![]() ![]() ![]() ![]() |
![]() ![]() ![]() ![]() |
![]() ![]() ![]() ![]() |
![]() ![]() |
![]() ![]() ![]() |
![]() ![]() |
![]() ![]() ![]() |
![]() ![]() |
![]() ![]() |
Дополнительная информация
Чертеж каретки.dwg

Технические требования..
Размеры для справок.
Спецификация на барабан мой.dwg

КП по ГПМ 031113.00.00.СБ
Подшипник 1314 ГОСТ 28428-90
Болт 1М16*1.25-6g605835ХГОСТ4695-86
Болт 1М8*1.25-6g605835ХГОСТ40598-79
Гайка А М16 х 6.7H.35.3.019.3 ОСТ 9064-75
Шайба 30.20.III.4.029 ОСТ 26-204096
-6g х 120.109.40Х.26 ГОСТ 22034-76
Чертеж барабана.dwg

КП по ГПМ 041069.00 СБ
Отвертие для вывода
мой кран.dwg

Лебедка механизма передвижения
Механизм передвижения
Схема запасовки грузового каната
Схема запасовки каната
Техническая характеристика
моя по ГПМ.doc
При выполнении работы студент должен:
– изучить конструкции башенных кранов и анализировать условия работы;
– составлять кинематические схемы механизмов;
– овладеть методикой расчета крановых механизмов;
– осуществлять компоновку машины;
– определять параметры устойчивости башенных кранов;
– проводить исследования по определению оптимальных параметров машины и отдельных ее элементов.
КР по ГПМ 041069.00 ПЗ
Башенные краны перемещают грузы по сложным пространственным траекториям. Благодаря стреле закрепленной в верхней части башни они имеют большое подстреловое пространство в котором размещается возводимое здание или сооружение.
Основные параметры башенных кранов: Q кН – грузоподъемность – максимальная масса груза который может поднять кран причем обычно кран может поднять наибольший груз при минимальном вылете однако в ряде конструкций для удобства эксплуатации она является постоянной величиной; L м– вылет стрелы это расстояние от центра массы груза до оси вращения крана; М кН – грузовой момент который определяется по формуле:
Для башенных кранов грузовой момент является главным параметром. К основным параметрам также относят высоту подъема H скорость всех рабочих перемещений базу В колею и габариты установленную мощность механизмов массу.
Наибольшее распространение получили краны с поворотной башней и нижним расположением опорно–поворотного устройства и с неповоротной башней и верхним расположением опорно–поворотного устройства. Изменение вылета стрелы обеспечивается наклоном стрелы и передвижением тележки по стреле. Сочетание указанных конструктивных признаков может быть любым.
Кран с вращающейся стрелой рис.1 состоит из неповоротной платформы 13 поворотной платформы 12 башни 10 стрелы 8 подстрелка 6 механизмов передвижения крана 1 подъема груза 5 изменения угла наклона стрелы 3 механизма поворота 11 стрелового полиспаста 4 крюковой подвески 7 кабины крановщика 9 балласта 2.
Башенные краны с вращающейся башней более устойчивы так как их центр тяжести расположен ниже а изгибающий момент действующий на башню от веса консоли и поднимаемого груза компенсируется соответствующей запасовкой канатов. Однако при большой грузоподъемности с большой высотой подъема груза получается значительное увеличение всей массы крана. Поэтому башенные краны грузоподъемностью более 10 т изготовляются с неповоротной башней и вращающейся только верхней частью крана.
Индексация: КБ–кран башенный – первая цифра означает размерную группу крана и характеризует его грузовой момент две последующие цифры – порядковый номер модели четвертая цифра – номер модели крана характеризующий отличия в длине стрелы высоте подъема и других параметрах. Первое буквенное обозначение указывает номер модернизации которой подвергался кран. Если модернизация не проводилась это обозначение отсутствует. Последнее буквенное обозначение указывает на климатическое исполнение крана: ХЛ – северное Т и ТВ – соответственно для сухих и влажных тропиков. Для умеренного климата буквенное обозначение не проставляется.
Например индекс КБ – 674.3А обозначает: кран башенный шестой размерной группы т.е. грузовой момент 3000 5500 кН·м с неповоротной башней третье исполнение после первой модернизации предназначен для работы в умеренном климате.
КР по ГПМ 031113.00 ПЗ
Определение основных параметров и расчет механизмов подъема груза
Механизм подъема груза является основным механизмом любой ГПМ предназначенным для перемещения груза в вертикальном направлении (подъем или опускание) и состоит из лебедки установленной на поворотной платформе стрелового крана силового полиспаста неподвижные блоки которого устанавливаются на тележке каната и крюка. Рабочим органом лебедки является барабан а полиспаста — подвижный блок (крюковая подвеска).
При включении двигателя крутящий момент с его вала через упругую компенсирующую муфту передается на входной вал редуктора. Увеличенный крутящий момент с выходного вала редуктора через зубчатую компенсирующую муфту передается на вал барабана лебедки. На вращающийся барабан лебедки навивается (свивается) канат что вызывает изменение длины грузового полиспаста и соответственно подъем или опускание крюковой подвески крана. Подвижная ветвь грузового каната проходит с головного блока стрелы на барабан лебедки через систему отводных (направляющих) блоков. Для ограничения высоты подъема крюковой подвески предназначен ограничитель. Обычно тормоз устанавливают на быстроходном (ведущем) валу редуктора.
Механизм подъема груза имеющий одну и ту же принципиальную схему может быть конструктивно выполнен по-разному в зависимости от требований предъявляемых к нему или крану в целом. Наибольшее распространение получила установка одной из опор барабана внутри консоли выходного вала редуктора т. е. подшипник конца выходного вала редуктора служит опорой для оси барабан. Конец выходного вала редуктора выполнен в виде зубчатой полумуфты которая через другую зубчатую полумуфту установленную на барабане передает крутящий момент непосредственно к барабану. Другой конец оси установлен на опоре. Упрощается расчет узел соединения получается компактным технологичным для сборки и позволяет применить унификацию деталей.
При значительной высоте подъема груза для увеличения производительности крана скорость опускания груза увеличивают по сравнению со скоростью подъема. В то же время монтажные краны предназначенные для ведения СМР должны обеспечивать плавность и точность опускания груза и иметь малые (посадочные) скорости. Несколько скоростей подъема (опускания) груза обеспечивают применением многоскоростного двигателя например электродвигателя с фазным ротором.
1 Выбор типа и кратность полиспаста
Тип полиспаста одинарный (простой) или сдвоенный определяется схемой навивки каната на барабан. При непосредственной навивке каната на барабан (мостовые козловые и т.п. краны) во избежание вращения груза при подъеме применяют сдвоенные полиспасты. В поворотных кранах где канат проходит через направляющий блок на конце стрелы возможна установка одинарных (простых) полиспастов.
В соответствии с грузоподъёмностью выбираем одинарный полиспаст кратностью 4 табл. 2.1 [5].
2 Выбор грузового крюка
Тип крюка (однорогий или двурогий) зависит от грузоподъемности крана. При грузоподъемности более 30 40 т применяют двурогие крюки. В ряде случаев тип крюка определяется габаритами поднимаемых грузов. В соответствии с грузоподъёмностью и режимом работы выбираем однорогий крюк №22 грузоподъёмностью 40 тонн с трапециевидной резьбой 110×12 и массой 154 кг [3 с. 22].
3 Выбор типа крюковой подвески
На башенных кранах чаще применяют двух – и трехосные подвески позволяющие разнести ветви грузового полиспаста и тем самым исключить закручивание грузового каната при возведении зданий повышенной этажности (более 9–ти этажей). Разнесенные блоки позволяют изменять кратность грузового полиспаста с 2 на 4 что дает возможность поднимать тяжелые грузы без повышения мощности привода лебедок и без увеличения диаметра канатов и блоков. В целях уменьшения массы крюковой подвески а также массы и размеров грузовой каретки в соответствии с резьбой крюка выбираем крюковую подвеску грузоподъёмностью 40 тонн с неразнесёнными блоками и максимальным диаметром каната 27 мм масса 475 кг [3 с. 24].
4 Определение усилий в грузовом канате и подбор каната
Усилие в ветви каната наматываемого на барабан:
где Q –вес поднимаемого груза Н; Uп – кратность полиспаста; o – общий КПД канатно–блочной системы определяется по формуле:
где п – КПД полиспаста табл. 1.1 [4]; б=096 098 – КПД одного блока; п – число отклоняющих блоков канатно–блочной системы.
Подставляя численные значения в формулу (3) получаем:
Подставляя численные значения в формулу (2) получаем:
Определяем разрывное усилие в канате:
где nк – коэффициент запаса прочности каната табл. 2.2 [5].
Подставляя численные значения в формулу (4) получаем:
Sp = 7631807·55=419кН
По найденному разрывному усилию выбираем канат двойной свивки типа ЛК-РО 6×36 dк=25мм с разрывным усилием Sp = 429кН прочностью 1960МПа табл. П 2.1 [4].
Каретка механизма подъёма показаны на рисунке 2.
5 Определение основных размеров барабана
Минимальный диаметр барабана и блоков по центру витков каната принимают в зависимости от диаметра каната и от режима работы крана табл. 2.2 [5].
Определяем минимальный диаметр барабана:
где dк – диаметр каната мм.
Подставляя численные значения в формулу (5) получаем:
Длина каната подлежащего навивке на барабан с учетом длины трех запасных витков и двух дополнительных витков для разгрузки мест крепления каната:
где H–высота подъема.
Подставляя численные значения в формулу (6) получаем:
Рабочая длина барабана:
где т – число слоев навивки каната на барабан.
Подставляя численные значения в формулу (7) получаем:
Максимальный диаметр навивки каната на барабан:
Dmax=D6+2m·dK мм. (8)
Подставляя численные значения в формулу (8) получаем:
Dmax= 450+2·2·25=550 мм.
Средний диаметр навивки каната на барабан:
Dср=Dб+(m–1)·dK мм. (9)
Подставляя численные значения в формулу (9) получаем:
Dср=450+(2-1)·25=475 мм.
Диаметр барабана по ребордам:
Dр=Dб+2dK·(m+2) мм. (10)
Подставляя численные значения в формулу (10) получаем:
Dр=450+2·25·(2+2)=650 мм.
По найденному значению диаметра барабана Dб выбираем барабан БКС–525
[3 с. 20] . Общий вид барабана показан на рисунке 3.
6 Расчет и выбор электродвигателя и редуктора
Подъемные механизмы строительных кранов и лебедок приводятся в действие крановыми двигателями переменного тока асинхронными с фазным ротором серии MTF и MTH с короткозамкнутым ротором серии MTKF и двигателями постоянного тока. Двигатели рассчитаны на повторно-кратковременный режим работы.
Статическая мощность электродвигателя при подъеме номинального груза кВт:
где Vк – скорость навивки каната мс; м = 08 092 – КПД механизма с цилиндрическими зубчатыми колесами при опорах качения.
Скорость навивки каната на барабан:
где Vг – скорость подъёма груза мс.
Подставляя численные значения в формулу (12) получаем:
Подставляя численные значения в формулу (11) получаем:
По рекомендациям [6] необходимую статическую мощность найдём по формуле:
Подставляя численные значения в формулу (13) получаем:
По каталогу [6] выбираем электродвигатель МТН 612-6 N=80 кВт при ПВ 40% Мma =101 с-1 Мном=649 Нм J=165 кг×м2 масса 930 кг.
Частота вращения барабана мин-1:
Подставляя численные значения в формулу (14) получаем:
nб=60·12(·0475)=4826 мин-1.
Необходимое передаточное число редуктора:
Подставляя численные значения в формулу (15) получаем:
По передаточному числу и номинальной мощности выбираем редуктор Ц2-650: N=111кВт ПВ 40% Uр=25 быстроходный вал двухсторонний для установки муфты и тормоза по разные стороны редуктора масса 1090 кг [3 с.34].
Проверка возможности установки барабана и электродвигателя по одну сторону редуктора:
где Ас – межосевое расстояние редуктора мм; Δ=40 50 мм – зазор между ребордой барабана и корпусом электродвигателя; В – габаритный радиус корпуса электродвигателя мм.
Подставляя численные значения в формулу (16) получаем:
Равенство выполняется значит можно оставить выбранный редуктор и разместить двигатель и барабан по одну сторону от редуктора.
7 Расчет и выбор тормоза
Расчетный тормозной момент по рекомендации Горгостехнадзора:
МТ = KТ ·МСТТ Нм (17)
где КТ – коэффициент запаса торможения КТ = 17 для среднего (4М) режимов работы; МСТТ – статический тормозной момент кН находится по формуле:
Подставляя численные значения в формулу (18) получаем:
Подставляя численные значения в формулу (17) получаем:
МТ=175·56525=9892 Нм.
По табл. 2.8 [1] выбираем тормоз двухколодочный нормально - замкнутый ТТ-400 с наибольшим тормозным моментом 1600 Нм диаметр тормозного шкива DТ=400 мм.
В крановых подъемных механизмах соединение вала электродвигателя с валом редуктора осуществляется зубчатыми муфтами типа МЗ или упругими втулочно–пальцевыми муфтами типа МУВП с тормозными шкивами или без них Условие выбора муфты: диаметр шкива муфты должен быть равен диаметру шкива тормоза если он есть; момент передаваемый муфтой должен быть равным или больше момента Мт создаваемого тормозом или больше момента среднего пускового момента двигателя.
Для соединения вала электродвигателя с быстроходным валом редуктора выбираем муфту упругую втулочно – пальцевую МУВП-7 с максимальным передаваемым моментом 1300 Нм с тормозным шкивом [3 с. 42]. Момент инерции муфты Jм=11 кг·м2.
9 Проверка электродвигателя на продолжительность времени пуска
Среднее время пуска при подъеме номинального груза:
где дв = ·n30 – угловая частота вращения вала электродвигателя Jnp– момент инерции механизма подъема при пуске приведенный к валу двигателя кг·м2:
где Jp – момент инерции ротора двигателя (по каталогу двигателей) кг·м2;
Jм – момент инерции муфты кг·м2; JТШ – момент инерции тормозного шкива кг·м2;
= 12 – коэффициент влияния вращающихся масс не лежащих на валу двигателя;
Rcp=Dcp2 – радиус навивки по среднему слою м;
Подставляя численные значения в формулу (20) получаем:
Средний пусковой момент электродвигателя найдём по формуле:
Мпср =(Mmax+11·Mном)2 Нм (21)
где Мma Мном – номинальный момент электродвигателя Нм;
Подставляя численные значения в формулу (21) получаем:
Мпср =(3580+11·106623)2=237643 Нм
Статический момент от веса груза найдём по формуле:
Подставляя численные значения в формулу (22) получаем:
Подставляя численные значения в формулу (19) получаем:
Среднее ускорение подъема груза:
Подставляя численные значения в формулу (23) получаем:
агр=12·2232(25·075)=14 мс2.
10 Проверка электродвигателя по моменту
Условие правильности выбора электродвигателя:
где К = 15– коэффициент перегрузки для механизмов подъема груза; m=m1 ·m2– коэффициент условия работы; m1 – коэффициент ответственности табл. 2.3 [5]. т2 = 08 – коэффициент учитывающий условия работы для электродвигателей механизмов подъема груза и стрелы при проверке по наибольшему моменту.
Подставляя численные значения в формулу (24) получаем:
Неравенство верно значит работа электродвигателя обеспечена.
11 Проверка тормоза на продолжительность времени торможения
Время пуска двигателя находится по формуле:
где Jпрт – момент инерции механизма подъема при торможении приведенный к валу двигателя находится по формуле:
Подставляя численные значения в формулу (26) получаем:
12 Проверка работоспособности фрикционных накладок тормоза
Условие достаточной работоспособности фрикционных накладок когда удельное давление передаваемое колодкой на шкив меньше допускаемого давления т.е. р [р] которое для вальцованной ленты [р] =(06 07) МПа.
Удельное давление колодки на тормозной шкив:
где f =035 – коэффициент трения; F – площадь фрикционной накладки:
где =70° – угол обхвата шкива колодкой; BТ – ширина колодки м; Dt – диаметр тормозного шкива м;
Подставляя численные значения в формулу (27) получаем:
Определение основных параметров и расчет механизма поворота
Механизм вращения поворотной части состоит из двух взаимозаменяемых элементов – собственно механизма вращения и опорно–поворотного устройства (ОПУ) с которым механизм воздействует. ОПУ выполняют в виде подшипника большого диаметра (1 3 м) с телами качения (шариками или роликами) однорядного или двухрядного. Одно из колец ОПУ крепится на неповоротной раме крана второе – на поворотной. Закрепленное кольцо выполняют в виде зубчатого обода – наружного или внутреннего с которым взаимодействует шестерня механизма вращения закрепленного на поворотной части крана. При вращении шестерня обкатывается по зубчатому ободу что приводит к вращению всей поворотной части вокруг оси вращения.
Механизм вращения выполняют по стандартной схеме двигатель – тормоз – редуктор – приводная шестерня взаимодействующая с ОПУ с вертикальным или горизонтальным размещением приводного двигателя. Тормоза обычного типа. Ввиду малой частоты вращения поворотной части (025 2 обмин) редуктор выполняют с большим передаточным числом а также с планетарными и волновыми передачами.
Особенностью механизмов вращения кранов является кратковременность работы в период одного цикла ввиду поворота на небольшой угол (90 180°) и большой момент инерции вращающихся частей не только механизма но и крана с грузом находящемся на большом вылете.
1 Расчет опорно–поворотного устройства
Определяем наибольший момент действующий на опорно–поворотный круг:
M = Q·A + Gс·a4 + Gб·a3 –Gп·a5 –Gбл·a2–Gпл·a1 кН·м (29)
где Q Gс Gб Gп Gбл Gпл – вес соответственно груза стрелы башни стрелового полиспаста балласта и поворотной платформы кН; A a4 a3 a5 a2 a1 – плечи вышеприведённых элементов крана соответственно м.
Подставляя численные значения в формулу (29) получаем:
М=27468·14 + 34·10 – 147 ·11 – 360·35 – 112·2=268535 .
Наибольшая вертикальная нагрузка равна сумме действующих сил
V = Q + Gc+Gб+Gбл +Gп+Gпл кH. (30)
Подставляя численные значения в формулу (30) получаем:
V =27468+34+360+147+112=79538 кН.
По величине V и М выбираем шариковый опорно–поворотный круг со следующими характеристиками: Vma Мma Dср=2065 м; dш=445 мм;
nш=252 шт.; Zв=90; Zш=16; передаточное отношение ОПУ Uопу=5625 [3 с. 30]
Примечание: dш – диаметр шариков; Dcp – средний диаметр ОПУ; Мma nш – количество шариков.
1.1 Определение моментов сопротивление повороту крана
Суммарный статический момент сопротивления повороту:
Мст = ΣМтр+Му+Мв кН·м (31)
где ΣМтр – суммарный статический момент от сил трения в ОПУ кН·м; Мв– момент создаваемой силой ветра кН·м; Му– момент сил возникающий при уклоне кН·м.
1.2 Момент сил трения
Момент сил трения будем определять для двух диаметрально противоположных шариков так как общее сопротивление практически не зависит от количества шариков одновременно находящихся под нагрузкой.
Сила вертикальной нагрузки действующая на условный шарик:
Подставляя численные значения в формулу (32) получаем:
Вертикальное давление на условный шарик от момента:
Подставляя численные значения в формулу (33) получаем:
Nм=2685352065=134268 кН.
Суммарное вертикальное давление на условный шарик:
Подставляя численные значения в формулу (34) получаем:
N`1=39769+134268 =174037 кН.
N`2=39769-134268 = - 94499 кН.
Примечание: знак плюс – для правого шарика знак минус – для левого шарика.
Полное давление на шарик:
N12 = N`12 cos45 кН; (35)
Подставляя численные значения в формулу (35) получаем:
N1=174037cos45=246163 кН.
N2=-94499cos45=-133662 кН.
Определение моментов сил трения качения:
M12=Fтр·Dcp2 = 2N12··Dcp(dш2) ·2 кH·м (36)
где =005– коэффициент трения качения.
Подставляя численные значения в формулу (36) получаем:
M1=2·246163 ·005·206544=1119 .
M2=2·(-133662) ·005·206544=-6076 .
Суммарный статический момент от сил трения в ОПУ:
ΣМтр=М1+М2 кН·м. (37)
Подставляя численные значения в формулу (37) получаем:
ΣМтр=1119+6076=17266 .
1.3 Момент от сил давления ветра на кран и груз
Мв=Мгр +Мкр кН·м (38)
где Мкр – суммарный момент сил ветра действующих на кран:
Mкр=Wca4+Wба3-Wплa1-Wбпa2 кН·м (39)
где Lc и bс – длина и высота стрелы м; φ – коэффициент заполнения: для решетчатых конструкций φ =02 04 для сплошных φ=1 γ–коэффициент учитывающий влияние второй фермы (для решетчатых конструкций γ =15 для сплошных γ =1) q =150 Па (Нм2) – скоростной напор ветра; Н6 и d6– высота и диаметр башни м; Lпл и bпл – длина и ширина платформы м Lбл и Нбл – длина и высота балласта м.
Подставляя численные значения в формулу (39) получаем:
Мгр – момент сил ветра действующих на груз:
Mгр=Fгр · q ·A кH·м (40)
где Fгр – наветренная площадь груза м2:
Подставляя численные значения в формулу (41) получаем:
Подставляя численные значения в формулу (40) получаем:
Mгр=1693·150·14=3555 .
Подставляя численные значения в формулу (38) получаем:
2 Момент сопротивления вращения от уклона крана
где α = 1 3°– угол наклона крана.
Подставляя численные значения в формулу (42) получаем:
Mу=268535·sin2=2685 .
Подставляя численные значения в формулу (31) получаем:
Мст=17266+4178+2685=2413 .
3 Момент от сил инерции при пуске
где J – суммарный момент инерции масс механизма вращения (груза стрелы балласта платформы башни) приведенный к оси вращения крана:
J= · (mгр ·А:+mстр · (r2+rA+A2)3 + mбл·a22+m6 ·a23+ mп ·a21) кг·м2 (44)
где =11 13– коэффициент учитывающий влияние вращающихся масс привода механизма поворота на величину суммарного момента инерции; m – масса отдельного элемента кг; – угловая частота вращения крана с–1; tn – время пуска при линейном ускорении конца стрелы не более 1 мс2 табл. 3.1 [5].
Подставляя численные значения в формулу (44) получаем:
J=12·(28000·142+3400·(1252+125·14+142)3+36000·352+9400·092)=679838357 .
Подставляя численные значения в формулу (43) получаем:
Мин=679838357·0110=6798384 Нм
4 Определение расчетной мощности и выбор двигателя
N = (Мст + Мин )nкр(9550·м·ср) кВт (45)
где ср=16 18– средний коэффициент перегрузки для асинхронных электродвигателей с фазовым ротором.
Подставляя численные значения в формулу (45) получаем:
N=(241300+6798384) ·1(9550·085·17)=2241 кВт.
По каталогу [6] выбираем электродвигатель МТН 411–6 N=22 кВт при ПВ 40%
Мma Zш=16; передаточное отношение ОПУ Uопу=5625 [3 с. 30]
Общее передаточное число механизма вращения:
где nдв – частота вращения вала двигателем мин–1; nкр – частота вращения крана мин–1.
Подставляя численные значения в формулу (46) получаем:
5 Расчет параметров планетарного редуктора
На кранах в механизмах вращения нашли широкое применение трёхступенчатые планетарные редукторы. Планетарный редуктор состоит из венцовой неподвижной шестерни водила с сателлитами и солнечной шестерни. Приняв число зубьев солнечной шестерни равным Zсолн=18 а также примем одинаковые передаточные числа у всех трёх ступеней тогда число зубьев венцовой шестерни найдём по формуле:
Подставляя численные значения в формулу (47) получаем:
6 Определение времени пуска
Среднее время пуска:
tп=Jпр· ·(Мпср– M'ст) с (48)
где Jпр – приведенный к валу двигателя момент инерции крана а также самой передачи находится по формуле:
Jпр= ·(Jр+Jм) + mгр·А2 (Uм2м)+ mбл·а2(Uм2м)+ mгр·(r2+rA+A2 ) (Uм2м) кг·м2 (49)
где Jр – момент инерции вала двигателя кг·м2; Jм – момент инерции зубчатой муфты с тормозным шкивом кг·м2; = 105 125 – коэффициент учитывающий моменты инерции масс деталей вращающихся медленнее чем вал двигателя.
Подставляя численные значения в формулу (49) получаем:
Jпр=11·(2+195) + 28000·142(9602·085)+ 36000·352(9602·085)+ +3400·(1252+14+142(9602·085) = 1062 .
Мпср =(638+11·21885)2=4394 Нм.
Суммарный момент статического сопротивления приведенный к валу двигателя:
M'ст=Mст(Uм· м) Нм. (50)
Подставляя численные значения в формулу (50) получаем:
M'ст =241300(960·085)=2137 Нм.
Подставляя численные значения в формулу (48) получаем:
tп=1062·1005(4394-2137)=47 с.
7 Проверка двигателя по моменту
Условие правильности выбора двигателя:
где к = 13– коэффициент перегрузки при проверки двигателей механизмов поворота по наибольшему моменту; т = 095 – коэффициент условий работы.
Подставляя численные значения в формулу (51) получаем:
Верно значит работа двигателя при максимальной нагрузке обеспечена.
8 Определение коэффициента динамичности
Коэффициент динамичности определим по формуле:
Кд = Мд maх M'ст (52)
где Мд max – максимальный момент сил упругости в линии привода механизма в период неустановившегося режима работы:
Мд maх = M'ст +2(Mmax– M'ст)·(Jnp–Jмех) Jnp Нм. (53)
Подставляя численные значения в формулу (53) получаем:
Мд maх =2137+2· (638-2137) · (1062-435)1062=7147Нм.
Подставляя численные значения в формулу (52) получаем:
9 Определение тормозного момента и выбор тормоза
Для того чтобы силы инерции при торможении не превышали сил инерции при пуске принимаем время торможения равным времени пуска т.е. tn=tт.
Линейное замедление конца стрелы:
а = А··nкр30tт мс2. (54)
Допустимое замедление а = 1 мс2.
Подставляя численные значения в формулу (54) получаем:
а = ·130·47=002 мс2 1
Неравенство верно значит линейное ускорение конца стрелы не превышает критического.
Необходимый тормозной момент:
Мт = Мвт +Мут+Мд11 +Мд 111-Мтр 1Нм Нм (55)
где Мвт +Мут – сумма моментов сил ветра уклона и трения при торможении приведенных к валу двигателя (тормоза):
Мвт +Мут =(Мв+Мут) ·мU Нм . (56)
Подставляя численные значения в формулу (56) получаем:
Мст пр =(41780+26850)·085960=6078 Нм.
Мд11 +Мд 111 - момент от вращательно движущихся масс механизма крана и груза:
Мд11 +Мд 111=Jкр пр·tT Нм . (57)
Мтр 1 =Мтр· мU Нм (58)
Подставляя численные значения в формулу (58) получаем:
Подставляя численные значения в формулу (57) получаем:
Мд11 +Мд 111=1062·100547=2271 Нм.
Подставляя численные значения в формулу (55) получаем:
Мт =6078+2271-15288=135 Нм.
По табл. 2.11 [1] выбираем тормоз с электрогидротолкателем ТТ-200 с номинальным тормозным моментом 200 Нм и регулируем его на требуемый момент. Тормозы этого типа являются нормально – закрытыми. Применение тормоза такого типа обосновано использованием крана для подъёма груза на высоту до 20 метров.
Расчет механизма передвижения крана
В условиях эксплуатации кран может опираться на четыре три и две условные точки опоры (ходовые колеса или балансирные тележки).
Из–за неточности устройства подкрановых путей или из–за неравномерной осадки кран может опираться на три точки опоры. Однако при некоторых перемещениях стрелы может иметь место случай когда кран опираетесь только на две точки. Считается этот случай наиболее опасным а следовательно расчетным.
1 Определение давления на колесо
Давление на опорную точку определяем по формуле:
где Vm – нагрузка от результирующего момента относительно оси вращения кН·м;
V – нагрузка от вертикальных сил (вес груза балласта поворотной и неповоротной платформы стрелы башни) на две точки определяется по формуле:
V = (Q +Gбл + Gн+Gпл+Gc+G6 +Gнб)2 кН·м. (60)
Подставляя численные значения в формулу (60) получаем:
V = (280+34+94+360+147+112)2=44469
Нагрузка от момента относительно оси башенного крана:
Vm =М(В·cosα) = (Q ·A – G6л · b – Gпл ·с + GC ·L2)(B·cosα) кН (61)
Подставляя в формулу (61) численные значения получаем:
Vm=(280 ·14 - 360 ·36-112 +34 · 15)(75cos2)=35016 кН.
Подставляя численные значения в формулу (59) получаем:
R=44469+35016=79485 кН.
По табл. 4.1 [5] принимаем для среднего режима работы ходовое колесо диаметром Dк=500 и рельс с допускаемой нагрузкой 296 кН. Таким образом в одной опорной точке будет располагаться ходовая тележка с тремя колесами и общей максимальной нагрузкой 23619 кН.
2 Определение сопротивления передвижению башенного крана
Определим сопротивления передвижению башенного крана:
W =Wтр + Wв + Wу кH (62)
где Wтр – сопротивление от сил трения:
где fk – коэффициент сопротивления качению колеса табл. 4.2 [5].
Подставляя численные значения в формулу (63) получаем:
Wин=11·2·44469·015981=1496 кН.
Wв – сопротивление от сил ветра:
Wв= Wкр+ Wгр кН (64)
где Wкр – силы ветра действующие на кран:
Wкр =Fкр·q·k·c·(1 + ) кH (65)
где Fкр – наветренная площадь крана
Fкр =Hб ·dб · γ ·φ+Lc·bc·φ + Fпл +Fн+ Fбл м2 (66)
где Fпл – наветренная площадь поворотной платформы с балластом м2; FH – наветренная площадь неповоротной части крана м2; q =125 Па – динамическое давление ветра; к – коэффициент возрастания динамического давления ветра по высоте табл. 5.1 [5]; с – коэффициент аэродинамической силы: для конструкций из труб 06 08; коробчатые конструкции и грузы 12; плоские из прямоугольных профилей 15 16; (1+ )=12 13– динамический коэффициент пульсации ветрового воздействия. В нормальных условиях принимают k·c·(1+)=16 25.
Подставляя численные значения в формулу (66) получаем:
Fкр=18·09·16·1 +14·078·1+75·1+945·1=4407 м2.
Подставляя численные значения в формулу (65) получаем:
Момент от сил ветра действующих на груз:
Wгр=Fгр·q·k·c·(1 + ) кН (67)
Подставляя численные значения в формулу (67) получаем:
Wгр=1693·0125·125=317 кН.
Подставляя численные значения в формулу (64) получаем:
Сопротивление передвижению от уклона пути:
где α=19° – наклон основания крана при расчете механизма передвижения.
Подставляя численные значения в формулу (68) получаем:
Wу=2·44469·sin2=2579 кH
Подставляя численные значения в формулу (62) получаем:
W=9+1143+2579=46 кН.
3 Определение инерционных сопротивлений в пусковой период
Определим силы инерции при пуске крана:
Wин=11·2·V·ag кH (69)
где а = 015 мс2 – среднее ускорение рельсоколесного крана при спуске.
Подставляя численные значения в формулу (69) получаем:
Wин=11·2·4732·015981=15934 кН.
4 Определение мощности двигателей механизма передвижения
Мощность привода механизма передвижения
N=(W + Wин) ·Vк(ср·м) кВт (70)
где Vк – скорость передвижения крана мс; м =085.
Подставляя численные значения в формулу (70) получаем:
N = (46+1496) ·033(16·085)=169 кВт.
На башенном кране целесообразно применить механизм передвижения с раздельным приводом где применяются два двигателя с редукторами. Мощность каждого из двух двигателей:
Подставляя численные значения в формулу (71) получаем:
5 Выбор двигателя и редуктора
По каталогу [6] принимаем электродвигатель МТН 311-6: N=11 кВт при ПВ 40% Мmax=314 Нм n=940 обмин. =9681с-1 Мном=1342 Нм J=09 кг·м2 масса 170 кг.
Общее передаточное число механизма:
где nk – частота вращения ходового колеса тележки передвижения крана:
nk= 60·VкDк мин–1. (73)
Подставляя численные значения в формулу (73) получаем:
nk=60·033· 05=13 мин-1.
Подставляя численные значения в формулу (72) получаем:
Передаточное число редуктора механизма передвижения:
где U=137 – передаточное число открытой зубчатой пары.
Подставляя численные значения в формулу (75) получаем:
По каталогу выбираем редуктор С-250 с передаточным числом Uр=28 способный передавать мощность N=76-186 кВт.
tп=Jпр·(Mпср–Мст)с (75)
где Jпр – приведенный к валу двигателя момент инерции одного приводного агрегата и половины масс крана:
Jnp= ·(Jр+Jм)+V·Rк2 (g ·Uм2·nм) кг·м2 (76)
где Jм – момент инерции упругой муфты с тормозным шкивом кг·м2; – угловая частота вращения вала двигателя с–1; Rк – радиус ходового колеса м.
Мпср=(314+11·11176)2=21847 Н.
Статический момент от половинного сопротивления передвижению крана:
Мcт = 06·W · Rк (Uм ·м) Нм (77)
Подставляя численные значения в формулу (77) получаем:
Мcт=46000·05(2·59·085·2)=112 нм.
Подставляя численные значения в формулу (76) получаем:
Jnp=125·(09+195)+444690·0252(981·592·085)=42 .
tп=42· 984(218-112)=35 с.
к·M'ст ≤ m·Mmax (78)
где К = 12– коэффициент перегрузки; т=095 – коэффициент ответственности.
Подставляя численные значения в формулу (78) получаем:
Неравенство верно значит двигатель по моменту подходит.
8 Определение тормозного момента и выбор тормоза
Расчетный тормозной момент на валу двигателя:
Мт = Мвт +Мут+Мдт -Мтр Нм (79)
где Мвт +Мут – приведённый момент от статических сил ветра уклона и сил трения:
Мст=06·(Wвт + Wук – Wтр)·Rк·мUм Нм. (80)
Подставляя численные значения в формулу (80) получаем:
Мвт +Мут =06×(11430 + 25790) ·0.52·59 · 0.85=877 Нм.
Мдт – приведённый к валу двигателя динамический момент массы крана и двигателя:
Мдт = Jпр· tт Нм (81)
где Jпр – приведённый момент инерции массы крана и ротора двигателя:
Jпр =·(Jр+Jм)+V· Rк2·м g· Uм2 кгм2; (82)
Подставляя численные значения в формулу (82) получаем:
Jпр=125·(09+195)+06 ·444690·0252·085(981·592)=386 .
Принимаем время торможения равным времени пуска tп=12сек.
Подставляя численные значения в формулу (81) получаем:
Мдт=386·98435=1085 Нм.
Подставляя численные значения в формулу (79) получаем:
Мт=877+1085-265=169 Нм.
По табл. 2.8 [1] выбираем тормоз ТТ-200 с тормозным моментом Мт=200 Нм и регулируем его на расчетный момент.
Тормозной путь найдём по формуле:
Подставляя численные значения в формулу (83) получаем:
9 Проверка запаса сцепления при спуске
Коэффициент запаса сцепления
где G– вес крана кН; Gсц– сцепной вес т. е. вес на приводные колеса кН; φ=012 – коэффициент сцепления для кранов работающих на открытом воздухе; f =008– коэффициент трения в цапфах при подшипниках качения шариковых и роликовых; d=70 – диаметр оси ходового колеса; a=009 мс2 – ускорение при пуске.
Вес крана найдём по формуле:
G= (2 ·V – Q) кН. (85)
Подставляя численные значения в формулу (87) получаем:
G =44469 · 2-280=6094 кН.
Подставляя численные значения в формулу (86) получаем:
Gсц =G2=60942=3047 кН.
W "=826+2579=3405 кН.
Подставляя численные значения в формулу (84) получаем:
Kсц=3047· (012+0015·70500)3405+6094·009981=67 > 12.
Запас сцепления для работы крана достаточный.
10 Проверка отсутствия "юза "при торможении
Машина будет скользить на пути S = Vк·tт если силы инерции больше сил сцепления между колесами и рельсами т. е.
·V·Vкg·tm>Pх·f·Zх+Pт·Zт·(φ + f·dDк) (88)
где Vk – скорость крана м с; Рт и Рх –нагрузка на тормозные и холостые колеса соответственно кН; Zm u Z φ – коэффициент сцепления колеса с рельсом.
Подставляя численные значения в формулу (88) получаем:
·44469·033(981·35) >44469·012+44469·(012+0015·00705)
Неравенство неверно значит юз при торможении будет отсутствовать
Определение параметров устойчивости башенного крана
Коэффициент запаса устойчивости нормируемый правилами Госгортехнадзора определяется для двух случаев опрокидывания крана: в сторону груза К1 – грузовая устойчивость; в сторону противовеса К2 – собственная устойчивость. Силы создающие опрокидывающий момент Моп: основная нагрузка (масса груза и грузозахватных устройств); дополнительные нагрузки (инерционные силы торможения и изменения скоростей механизмов подъема передвижения поворота и изменения вылета и наклона стрелы) ветровое давление на наветренную часть крана и груза а также атмосферные осадки. Противодействие опрокидыванию свободно стоящего крана оказывает только собственная сила тяжести которая создает удерживающий момент Муд.
1 Определение коэффициента грузовой устойчивости
Кран рассматривается на горизонтальной площадке. Силы ветра и инерции не учитываются.
Условие грузовой устойчивости:
где а – вылет стрелы м; b – половина колеи м; с – расстояние от оси вращения крана до центра тяжести крана по горизонтали находится по формуле:
Подставляя численные значения в формулу (90) получаем:
Подставляя численные значения в формулу (89) получаем:
Верное равенство указывает на соблюдение условия грузовой устойчивости крана.
2 Определение коэффициента собственной устойчивости
В соответствии с правилами Госгортехнадзора коэффициент собственной устойчивости определяют для следующих условий: кран находится в нерабочем состоянии груза на крюке нет стрела горизонтальна уклон пути в направлении
противовеса. Со стороны стрелы дует ветер с динамическим давлением q=450 Па (Нм2) – для нормальных условий эксплуатации ориентируются на третий район установки крана:
где Wcк – сила давления ветра на стрелу и кабину с торца:
где Fcк=25 м2 К – коэффициент роста динамического давления по высоте табл. 5.1 [5];
Подставляя численные значения в формулу (92) получаем:
Wб – сила давления ветра на башню:
Подставляя численные значения в формулу (93) получаем:
Wпб – сила давления ветра на платформу и балласт:
где Fпб=10 м2 – наветренная площадь платформы и балласта;
Подставляя численные значения в формулу (94) получаем:
Горизонтальная координата центра тяжести крана не изменилась и равна с=17 м.
Вертикальная координата центра тяжести крана:
где h4 h3 h2 h1 h – вертикальные ординаты центров тяжести стрелы башни балласта поворотной и неповоротной платформы соответственно м.
Подставляя численные значения в формулу (95) получаем:
Определение производительности строительных кранов
Техническая производительность определяется конструктивно – кинематическими параметрами машины. Эксплуатационная производительность меньше технической и определяется как параметрами технической производительности.
Среднечасовая эксплуатационная производительность строительных кранов характеризуется массой поднятых грузов за один машино–час:
ПЭЧ=60·Q·Кг·Квtц тч (96)
где Q – грузоподъемность тонн; Кг– коэффициент использования грузоподъемности при крюковом оборудовании Кг =08 09; Кв – коэффициент использования внутрисменного времени Кв=086;
tu– продолжительность рабочего цикла:
tц=tм + tрп мин (97)
где tм – продолжительность машинного времени цикла мин; tpn – продолжительность ручных операций по строповке наводке и установке груза в проектное положение мин.
где H – высота подъема груза м; Vг – скорость подъема (опускания) груза ммин;
V1– скорость изменения вылета ммин; V2– скорость передвижения крана ммин;
α – угол поворота крана (стрелы) град; к – коэффициент совмещения операций к =08;
п – частота вращения крана (стрелы) мин–1.
Подставляя численные значения в формулу (98) получаем:
Подставляя численные значения в формулу (96) получаем:
ПЭЧ=60·28·085·086102=1228 тч.
Годовую эксплуатационную производительность можно определить через среднечасовую по формуле:
ПЭГ = ПЭЧ ·Т·Кв тгод (99)
где Т – рабочее время крана в году чгод табл. 5.1 [5]; Кв = 08 – коэффициент внутрисменных потерь времени.
ПЭГ=1228·3110·08=305546 тгод.
Производительность во многом зависит от организации работ на строительстве.
Эксплуатационная годовая производительность определяется по формуле:
Пг=Gcp·Nч·Т·Кв тгод (100)
где Gcp = 05·Gma Gma Nч – число циклов подъема в час;
Nч=Nсмt циклчас (101)
где t – число циклов в рабочей смене (t=683 при шестидневной рабочей неделе t=82 при пятидневной). Число циклов подъёма в смену Nсм обычно планируется строительной организацией и составляет 20 80 циклов.
Подставляя численные значения в формулу (101) получаем:
Подставляя численные значения в формулу (100) получаем:
Пг=14 ·24·3110·08=835968 тгод.
КР по ГПМ 031124.00 ПЗ
содержание.doc
1 Выбор типа и кратность полиспаста
2 Выбор грузового крюка
3 Выбор типа крюковой подвески
4 Определение усилий в грузовом канате и подбор каната
5 Определение основных размеров барабана
6 Расчет и выбор электродвигателя и редуктора
7 Расчет и выбор тормоза
9 Проверка электродвигателя на продолжительность времени пуска
10 Проверка электродвигателя по моменту
11 Проверка тормоза на продолжительность времени торможения
12 Проверка работоспособности фрикционных накладок тормоза
Определение основных параметров и расчет механизма поворота
1 Расчет опорно–поворотного устройства
1.1 Определение моментов сопротивление повороту крана
1.2 Момент сил трения
1.3 Момент от сил давления ветра на кран и груз
2 Момент сопротивления вращения от уклона крана
3 Момент от сил инерции при пуске
4 Определение расчетной мощности и выбор двигателя
5 Расчет параметров планетарного редуктора
6 Определение времени пуска
7 Проверка двигателя по моменту
8 Определение коэффициента динамичности
9 Определение тормозного момента и выбор тормоза
Расчет механизма передвижения крана
1 Определение давления на колесо
2 Определение сопротивления передвижению башенного крана
3 Определение инерционных сопротивлений в пусковой период
4 Определение мощности двигателей механизма передвижения
5 Выбор двигателя и редуктора
8 Определение тормозного момента и выбор тормоза
9 Проверка запаса сцепления при спуске
10 Проверка отсутствия "юза "при торможении
Определение параметров устойчивости башенного крана
1 Определение коэффициента грузовой устойчивости
2 Определение коэффициента собственной устойчивости
Определение производительности строительных кранов
Список используемой литературы