Автогрейдер




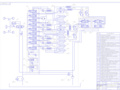
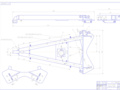
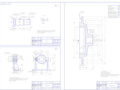
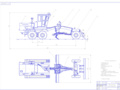
- Добавлен: 25.10.2022
- Размер: 2 MB
- Закачек: 1
Описание
Состав проекта
![]() |
![]() |
![]() |
![]() ![]() ![]() ![]() |
![]() ![]() ![]() ![]() |
![]() ![]() ![]() ![]() |
![]() ![]() ![]() ![]() |
![]() |
![]() ![]() ![]() |
![]() ![]() ![]() |
![]() ![]() ![]() |
![]() ![]() ![]() |
![]() ![]() ![]() ![]() |
![]() ![]() ![]() ![]() |
![]() ![]() ![]() ![]() |
![]() ![]() ![]() ![]() |
![]() |
![]() ![]() ![]() |
![]() ![]() ![]() |
![]() ![]() ![]() |
![]() ![]() ![]() |
![]() ![]() ![]() |
![]() ![]() ![]() |
![]() ![]() ![]() |
Дополнительная информация
А1 Рама тяговая.cdw

7 Схема гидравлическая.cdw

Гидроусилитель сцепления
Гидроусилитель тормозов
Гидрозамок двусторонний системы
управления рабочим органом
Клапан предохранительный
Гидромотор шестеренный ГМШН25
Насос шестеренный НШ-32У-3
Гидрораспределитель рулевого
Гидроцилиндр подъема и опускания
тяговой рамы Ц80.6 (200-700)
Гидроцилиндр выноса отвала
Гидроцилиндр наклона колес
Гидроцилиндр выноса тяговой рамы
Гидроцилиндр дополнительного
рабочего органа Ц63.6 (50-100)
Гидроцилиндр изменения угла
резания Ц30.6 (10-200)
Гидроцилиндр поворота основной
А1 Чертеж общего вида.cdw

Боковой вынос грейдерного отвала
в обе стороны относительно тяговой рамы
Кабина одноместная закрытого типа
* Размеры для справок
ДЕТАЛИРОВКА.cdw

Уклоны формовочные 7
Неуказанные радиусы R3.
Сталь 45 ГОСТ 1050-74
Неуказанные радиусы 2мм .
Коэффициент смещения
Сталь45 ГОСТ 1050-74
7 Схема гидравлическая.dwg
Гидроусилитель сцепления
Гидроусилитель тормозов
Гидрозамок двусторонний системы
управления рабочим органом
Клапан предохранительный
Гидромотор шестеренный ГМШН25
Насос шестеренный НШ-32У-3
Гидрораспределитель рулевого
Гидроцилиндр подъема и опускания
тяговой рамы Ц80.6 (200-700)
Гидроцилиндр выноса отвала
Гидроцилиндр наклона колес
Гидроцилиндр выноса тяговой рамы
Гидроцилиндр дополнительного
рабочего органа Ц63.6 (50-100)
Гидроцилиндр изменения угла
резания Ц30.6 (10-200)
Гидроцилиндр поворота основной
ДЕТАЛИРОВКА.dwg
Уклоны формовочные 7
Неуказанные радиусы R3.
Сталь 45 ГОСТ 1050-74
Неуказанные радиусы 2мм .
Коэффициент смещения
Сталь45 ГОСТ 1050-74
А1 Чертеж общего вида.dwg
Боковой вынос грейдерного отвала
в обе стороны относительно тяговой рамы
Кабина одноместная закрытого типа
* Размеры для справок
А1 Рама тяговая.cdw

7 Схема гидравлическая.cdw

Гидроусилитель сцепления
Гидроусилитель тормозов
Гидрозамок двусторонний системы
управления рабочим органом
Клапан предохранительный
Гидромотор шестеренный ГМШН25
Насос шестеренный НШ-32У-3
Гидрораспределитель рулевого
Гидроцилиндр подъема и опускания
тяговой рамы Ц80.6 (200-700)
Гидроцилиндр выноса отвала
Гидроцилиндр наклона колес
Гидроцилиндр выноса тяговой рамы
Гидроцилиндр дополнительного
рабочего органа Ц63.6 (50-100)
Гидроцилиндр изменения угла
резания Ц30.6 (10-200)
Гидроцилиндр поворота основной
А1 Чертеж общего вида.cdw

Боковой вынос грейдерного отвала
в обе стороны относительно тяговой рамы
Кабина одноместная закрытого типа
* Размеры для справок
ДЕТАЛИРОВКА.cdw

Уклоны формовочные 7
Неуказанные радиусы R3.
Сталь 45 ГОСТ 1050-74
Неуказанные радиусы 2мм .
Коэффициент смещения
Сталь45 ГОСТ 1050-74
4 РК.docx
1 Выбор основных параметров автогрейдера
Выбор основных параметров автогрейдера производится из такого расчета что рассчитываемая нами машина является модификацией автогрейдера ДЗ - 122 поэтому задаемся следующими параметрам:
- колесная формула 1х2х3
- масса машины G кН 140
- мощность Nд кВт 99 29
- частота вращения n обмин 1700
- размер шин 14.00.х20
- давление в шинах МПа 0 4
- скорости движения мс:
- рабочая минимальная Vр 061
- транспортная максимальная VT max 1000
2 Тяговый расчет автогрейдера
В процессе работы автогрейдера возникают различного характера и величины силы сопротивления его движению. Исходя из этих сопротивлений рассчитывают силовую установку машины и определяют усилия возникающие в элементах конструкции для расчета их на прочность.
Различают два характерных режима движения автогрейдера: тяговый или рабочий и транспортный. Тяговым называется режим движения машины в процессе резания и перемещения грунта или выполнения других видов работ транспортным - движение машины с поднятым рабочим оборудованием холостым ходом по участку работ или с одного объекта работ на другой. Для тягового режима характерны большие тяговые усилия и малые скорости передвижения автогрейдера для транспортного - большие скорости движения и малые тяговые усилия.
Для определения сопротивлений возникающих в рабочем режиме при резании и перемещении грунта автогрейдером должны быть известны:род грунта и его характеристики; размеры рабочего органа и углы его установки; вес автогрейдера.
Тяговый расчет сводится к определению силы тяги на ведущих колесах РК общего сопротивления WРАБ и свободной силы тяги автогрейдера φСЦ·GCЦ . Для нормальной работы автогрейдера необходимо чтобы соблюдалось условие:
Тяговый расчет автогрейдера производится при следующих условиях:
- режим работы установившийся рабочий
- грунт .. IIIIII категорий
- коэффициент трения грунта о грунт ..07
- коэффициент трения грунта по металлу ..05
Потребная сила тяги на ведущих колесах.
Потребная сила тяги на ведущих колесах автогрейдера определяется из отношения максимальной мощности установленного двигателя и рабочей минимальной скорости значения которых были взяты из [5] :
где NДВ – максимальная мощность установленного двигателя кВт;
VP – скорость рабочая минимальная мс ;
б) Максимальная свободная сила тяги.
Максимальная свободная сила тяги на ведущих колесах автогрейдера определяется по формуле :
где φСЦ – коэффициент сцепления колес автогрейдера с грунтом ;
GСЦ – сцепной вес автогрейдера то есть вес приходящийся на ведущие колеса и он равен :
где – коэффициент веса который приходится на ведущие колеса автогрейдера ( для колесной формулы 1х2х3: = 07 [9])
Таким образом окончательно получим
Для нормальной работы автогрейдера необходимо соблюдение следующего условия
Pк ≥ Wраб ≤ φсц × Gсц ( 4.1 )
где Pк – сила тяги на ведущих колесах кН;
Wраб – общее сопротивление при установившемся рабочем режиме кН;
φсц – коэффициент сцепления ведущих колес с грунтом φсц=075
Gсц – сцепной вес автогрейдера кН.
Общее сопротивление при установившемся рабочем режиме складывается из следующих составляющих
Wраб = Wр + Wп + Wв + Wт ( 4.2 )
где Wр – сопротивление грунта резанию ножом кН;
Wп – сопротивление поступательному перемещению перед отвалом
призмы волочения грунта кН;
Wв – сопротивление грунта при движении его вверх по отвалу кН;
Wт – сопротивление перекатыванию колес кН;
Определим сопротивление Wр
где к – удельное сопротивление грунта резанию кНм2;
F – площадь поперечного сечения вырезаемой стружки м2.
F = × φсц × G ( кк × m ) ( 4.4 )
где – коэффициент использования сцепного веса автогрейдера;
G – сила тяжести автогрейдера кН;
кк – удельное сопротивление грунта копанию кНм2;
m – коэффициент учитывающий неравномерность сечения стружки при
= 045; кк = 240 кНм2 ; m = 135.
F = 045 × 075 × 131 ( 240 × 135 ) = 013 м2.
Wр = 140 × 013 = 182 кН.
Определим сопротивление Wп
Wп = Qгр × f ( 4.5 )
где Qгр – вес призмы грунта перед отвалом кН;
f – коэффициент внутреннего трения грунта.
Qгр = Vф × λ ( 4.6 )
где Vф – объем призмы волочения перед отвалом м3 ;
λ – насыпной вес призмы волочения кНм3 .
Vф = ( H – hср)2 × l × кз (2 × tgφ ) ( 4.7 )
где Н – высота отвала м;
hср – среднее значение глубины резания м;
кз – коэффициент заполнения отвала;
φ – угол естественного откоса грунта град.
Н = 062 м; кз = 093; φ = 35 град.
hср = 008 4 = 002 м;
Vф = ( 062 – 002 )2 × 65 × 093 ( 2 × tg35) = 155 м3 ;
Qгр = 155 × 160 = 248 кН.
Wп = 248 × 073 = 181 кН.
Определяем сопротивление Wв
Wв = Qгр × cos2 × f1 ( 4.9 )
где – угол резания ножа град. ;
f1 – коэффициент трения грунта об отвал.
Wв = 248 × cos245 × 075 = 93 кН.
Определяем сопротивление Wт
где – коэффициент сопротивления качению колес по грунту;
Wт = 131 × 016 = 210 кН.
Таким образом общее сопротивление равно
Wраб = 182 +181 + 93 + 210 = 666 кН.
Максимальная сила тяги автогрейдера определяемая по сцепному весу автогрейдера равна
φсц × Gсц = φсц × 0 × G ( 4.11 )
где φсц – коэффициент сцепления ведущих колес с грунтом;
φсц × Gсц = 075 × 082 × 131 = 806 кН.
Значит условие ( 5.1 ) выполняется то есть Wраб φсц × Gсц
Определяем величину тяговой силы
Рк = Me × iт × м ( rc × 1000 ) ( 4.12 )
где Me – максимальный крутящий момент на валу двигателя Н×м;
м – коэффициент полезного действия трансмиссии;
rc – силовой радиус колеса м.
Me = 641 Н×м; м = 097.
где rст – статический радиус колеса rст = 06 м;
rc = 093×06 = 056 м.
Рк = 641 × 90 × 097 ( 056 × 1000 ) = 100 кН.
Следовательно условие ( 4.1 ) выполняется то есть Рк > Wраб.
Таким образом в тяговом расчете были определены: площадь поперечного сечения вырезаемой стружки грунта F = 013 м2; общее сопротивление при установившемся рабочем режиме автогрейдера Wраб = 666 кН; а также величина силы тяги колес Рк = 100 кН.
Определение сопротивлений и мощности для передвижения автогрейдера в транспортном режиме
а) Сопротивление от перемещения автогрейдера как тележки:
где – коэффициент сопротивления перекатыванию колес по плотно укатанному грунту ( = 004..006)
i - уклон местности ( i = 006..008 )
б) Сопротивление передвижению от воздуха.
Следует так же учесть сопротивление воздуха которое при движении автогрейдера на транспортных скоростях составляет значительную величину.
Это сопротивление определяют по формуле :
где КВОЗ – коэффициент сопротивления воздуха равный 006-008;
FЛ - лобовая площадь сопротивления м2;
VTMAX - транспортная максимальная скорость передвижения кмч;
в) Сопротивление от сил инерции.
При движении автогрейдера с ускорением что имеет место при переключении на более высокую скорость а так же при трогании с места имеют место силы сопротивления инерции которые определяются по формуле :
где WИН - сопротивление от сил инерции кН;
G - вес автогрейдера кН;
а - ускорение автогрейдера мс2 (для расчета принимается равным а = 002 мс2)
г) Общее сопротивление при транспортном режиме.
Общее сопротивление будет равно сумме всех сопротивлений возникающих при установившемся рабочем режиме то есть :
д) Потребная мощность на передвижение автогрейдера:
3 Расчет сил действующих на автогрейдер
Основные несущие металлоконструкции автогрейдера имеют простые конструктивные формы. Определение их параметров ведется с учетом предельных нагрузок которые возникают в следующих трех расчетных положениях.
После определения действующих сил производится расчет на прочность элементов металлоконструкции.
Расчетное положение I.
Для расчетов приняты следующие данные:
- масса автогрейдера на задний мост GСЦ кН 98
- статический радиус колеса гС м 0 62
- поперечный уклон дна кювета град 15
- база автогрейдера L0 м 583
- колея автогрейдера В м 20
- расстояние от грунта до оси переднего моста h м . 095
- положение центра тяжести по высоте h3 м 112
- положение центра тяжести по оси L1 м 1 75
В соответствии с методикой второе расчетное положение автогрейдера соответствует действию случайных нагрузок возникающих при встрече с непреодолимым препятствием. Такое положение соответствует выполнению автогрейдером планировочных работ при горизонтальной установке шнеково-фрезерного оборудования (рис.4.6). В этом положении предполагается что автогрейдер передвигаясь с наибольшей скоростью при выполнении планировочной операции (7 кмч = 196 мс) уперся шнеком в трудно преодолимое препятствие. При выявлении динамических нагрузок предполагается что масса препятствия по сравнению с массой автогрейдера велика. Нагрузки действующие на шнек в этом случае нагружения рассматриваются как редко действующие. С ними обычно связано появление в основной раме наибольшего изгибающего момента в горизонтальной плоскости.
Для последующего расчета примем следующие значения положения внеково-фрезерного оборудования :
Определим реакции и силы действующие на автогрейдер :
а) Продольная сила инерции.
При таком случае нагружения к центру тяжести машины дополнительно приложено продольное инерционное усилие. Значение продольной силы инерции РИ определяют для случая встречи автогрейдера массой m движущийся со скоростью VP с препятствием на основе дифференциального уравнения его движения в первом приближении:
где Vр- скорость автогрейдера мс;
m - масса автогрейдера т;
СM- приведенная жесткость взаимодействующих систем: препятствие с его жесткостью С2 и автогрейдера С1 у которого определяющей является жесткость рабочего оборудования относительно точки приложения нагрузки kНм
Приведенная жесткость определяем из следующего выражения :
где h3 -ордината центра тяжести автогрейдера м:
С1 - жесткость металлоконструкции (С1 = 1700 kНм [11]);
С2 - жесткость препятствия приведенная к параметрам шин ( С2 = 900 kHм при давлении 04 МПа [11]);
Рисунок 4.1 - Расчетная схема сил действующих на автогрейдер в первом расчетном положении.
Таким образом подставляя известные величины скорости массы и приведенной жесткости конструкции получим что продольная сила инерции будет равна ;
б) Вертикальные реакции.
Это реакции которые возникают в вертикальной плоскости и действуют на балансирную ( Z1Z2 ) и переднюю Z3 подвеску.
Так как в вертикальной плоскости нет действия реактивных сил то на оси балансирной подвески будут действовать равные реакции Z1 и Z2 которые приведем к общей реакции задней подвески Z12 и она будет равна их сумме то есть .
Реакцию Z12 (рис.4.4) определим из равенства суммы моментов относительно точки 3 (точки приложения реакции Z3 ) которая выразится как :
где L0- расстояние между осью симметрии балансирной подвески и передней осью м (L0 =5 83 м );
h3- положение центра тяжести по вертикали м;
Таким образом реакции Z1 и Z2 будут равны :
Реакцию Z3 определим из суммы проекций действующих сил на вертикальную ось которая будет равна :
где G - вес автогрейдера кН;
в) Силы тяги на колесах:
Так как вертикальные реакции на задней подвеске равны то и силы тяги по осям задней подвески будут равны ( т.е. Х1 = Х1 ) и которые приложим к оси симметрии балансирной подвески :
где φСЦ - коэффициент сцепления колес автогрейдера с грунтом;
Так как автогрейдер старается развернуться под действием внешней нагрузки в горизонтальной плоскости то определим боковые реакции возникающие на колесах.
На передних колесах эти боковые реакции как и силы тяги на задних колесах зависят от коэффициента сцепления колес с грунтом :
Боковая реакция на задней подвеске имеет более сложный характер и включает в себя действие силы тяги продольной силы инерции и боковой реакцией на передней подвеске. Эту реакцию определим из суммы моментов действующих сил относительно кромки рабочего органа которая запишется как:
Из этого уравнения выразим реакцию Y12 которая составит :
Подставляя все полученные и заданные значения получим что боковая реакция Y12 будет равна :
д) Силы действующие на кромке рабочего органа.
Нагрузки действующие на кромку рабочего органа находят по следующим формулам :
- Продольная нагрузка RX :
- Боковая нагрузка RY :
- Вертикальная нагрузка RZ в данном положении отсутствует т.е. RZ = 0 kH.
4 Расчет тяговой рамы
Конструктивно тяговая рама представляет собой равнобедренный треугольник. Боковые стороны выполнены и профиля и основание из листового металла. Боковые стороны дополнительно связаны основанием для крепления редуктора. Расчетная схема тяговой рамы и ее размеры представлены на рис. 4.2. Сечение балок рамы - коробчатый профиль 180 х 140 х 8 мм УМТУ 2-128-70.
Основные параметры сечения профиля:
- площадь сечения F см2 48 64
- момент сопротивления изгибу WY см3 320 86
- момент сопротивления изгибу WZ см3 252 65
- момент сопротивления при кручении WKP см3 442.79
- коэффициент концентрации напряжений αK 113
На основании расчетов сил проведенных в предыдущих разделах и анализа конструкции рабочего оборудования можно сделать вывод о нагружении тяговой рамы. На тяговую раму действуют следующие силы.
В точках 1 2 3 (рис.4.2) действуют усилия в гидроцилиндрах. В точке 8 приложены силы шарового шарнира. В точках 4567 которые являются местами крепления опорных башмаков поворотного круга действуют силы передаваемые от рабочего оборудования на раму. Конструкция тяговой рамы позволяет сделать следующий вывод; - участок между сечениями А и Б можно считать жестким в горизонтальной плоскости а наибольшая деформация балок рамы происходит вокруг оси Y сечения. Исходя всего из выше сказанного можно считать сечения А и Б заделкой и рассматривать прочность только сечения А как наиболее опасного. Остальная часть тяговой рамы закрепленная на жестком поворотном круге деформации не подвергается.
Рисунок 4.2 - Расчетная схема сил действующих на тяговую раму
Для первого расчетного случая нагружения автогрейдера имеем следующие исходные данные:
- силы резания: RX =20872 kН; RY =8460 kН; RZ=0 kН;
- сила инерции: РИ =14990 kН;
- расстояния: L1= 232 м ; L2= 060 м ; h1= 065;
а) Формулы для определения усилий в шаровом шарнире. Неизвестные силы находим из уравнений (рис.4.9) :
- продольная реакция:
- поперечная реакция: (4.28)
- вертикальная реакция: (4.29)
где RX RY RZ - силы резания в расчетном положении Kн;
GTP GPO - соответственно вес самой тяговой рамы и рабочего оборудования которые ориентировочно принимаем:
L1 L2 L3 h1 b1 - соответствующие расстояния в расчетном положении автогрейдера м;
б) Формулы для определения сил и напряжений возникающих в тяговой раме для проведения прочностного расчета .
где αTP - угол между осями балок тяговой рамы и равен αTP =12°40’;
- изгибающий момент: (4.33)
- крутящий момент: (4.34)
- нормальные напряжения: (4.35)
- касательные напряжения: (4.36)
- эквивалентное напряжение:
-коэффициент запаса прочности: (4.39)
Для аварийного нагружения тяговой рамы коэффициент запаса прочности принимают равным 11 при расчете было получено значение 113 следовательно сечение балки было подобрано правильно.
5 Расчет гидроцилиндра
Рабочее оборудование автогрейдера приводятся в движение с помощью гидроцилиндров. Только поворотное движение рабочий органа относительно тяговой рамы осуществляется посредством гидродвигателя. Скорости подъема рабочего органа и дополнительного сменного оборудования обычно находятся в пределах 10..20 смс. Опускание и боковой вынос рабочий органа осуществляется соответственно со скоростью около 8 и 4 смс. При определении параметров гидроцилиндров подъема рабочий органа обычно принимают что последний установлен с углом захвата φ0 =90° и разрабатывает грунт одним из его концов. Подъем рабочий органа поворотного круга и тяговой рамы общим весом G0 осуществляется одним гидроцилиндром.
Исходные данные для расчета:
- общая масса рабочего оборудования G0 кН 20.20 кН
- расстояния: L1 м 2205 м
В данном случае нагружения рассмотрим действие только сил веса рабочего оборудования так как вертикальная составляющая сил резания рыхлящих элементов направлена вверх тем самым помогая гидроцилиндру при подъеме. Поэтому наиболее нагруженным вариантом будет случай когда рабочее оборудование будет полностью вывешено на гидроцилиндре.
Усилие в гидроцилиндре подъема рабочий органа находят из выражения (рис. 4. 3):
Рисунок 4.3 - Расчетная схема сил действующих на гидроцилиндр
Для обеспечения устойчивости штока гидроцилиндра необхадимо чтобы соблюдалось условие : dD ≥ 03 следовательно
где d - диаметр штока гидроцилиндра м;
D - диаметр поршня гидроцилиндра м.
Рабочий ход гидроцилиндра т.е его поднимание осуществляется штоковой полостью гидроцилиндра следовательно эффективная площадь поршня будет равна:
Диаметр поршня гидроцилиндра определим из уравнения:
где РГЦ - усилие подъема гидроцилиндра Н;
F3 - эффективная площадь м2;
р - давление в гидросистеме Нм2;
- потери в гидросистеме( = 09 ).
Подставляя в уравнение (4.42) формулы (4.41) (4.43) и выражая диаметр поршня D получаем:
Подставляя в уравнение (4.44) известные значения получаем:
Следовательно на основе расчета принимаем:
- диаметр поршня гидроцилиндра D = 90 мм
- диаметр штока гидроцилиндра d = 40 мм.
5 ТЭР.docx
1 Расчёт эксплуатационной производительности техники
В расчетах технической эффективности строительных и дорожных машин их производительность может быть выражена абсолютным показателем - годовой эксплуатационной производительностью ПЭ
Годовая эксплуатационная производительность ПНЭГ ПбЭГ при выполнении данного вида работ устанавливается равенством м3год:
где ПЭЧ - эксплуатационная среднечасовая производительность м3маш. -ч;
КПР - коэффициент учитывающий простои в работе техники не учтенные в часовой эксплуатационной производительности (табл. 32 [5]); ТГ - количество машино-часов работы техники в году маш.-ч (для автогрейдеров ТГ = 1335 маш. –ч [5]);
- Эксплуатационная среднечасовая производительность при наличии актов приемочных испытаний рассчитывается м3маш. -ч:
где ПТЧ - техническая часовая производительность м3 маш.-ч;
КТ - коэффициент перехода от технической часовой производительности к эксплуатационной среднечасовой производительности ( КТ = 04 [4] табл. 32 ).
Техническая часовая производительность автогрейдера может находиться в зависимости от объема вынутого или перемещенного грунта длины построенной дороги спланированной площадки.
При разработке грунта техническая часовая производительность равна:
где FС - площадь срезаемой стружки м2;
VР - рабочая скорость автогрейдера мч;
Площадь срезаемой стружки можно определить через возможное тяговое усилие автогрейдера:
где К1 - удельное сопротивление грунта копанию кПа К1=250 кПа ( [3]);
Техническая часовая производительность:
Эксплуатационная среднечасовая производительность
Эксплуатационная годовая производительность м2год.
2 Удельные технико – экономические показатели
) Nуд = N Пэч – энергоёмкость.
N = 99 кВт Пэч = 317 м2час.
Nуд = 99 317 = 0312 кВт·ч м2.
) Gуд= GПэч– металлоёмкость.
Gуд= 143317 = 0045 т·ч м2.
) Pуд= PПэч – трудоёмкость.
P = 1 – количество рабочих обслуживающих машину.
Pуд= 1317 = 315· 10-3 чел·ч м2.
1 Обз.doc
1 Взаимодействие ножа автогрейдера с грунтом
В зависимости от условий работы нож автогрейдера может быть установлен под разными углами захвата резания и наклона. Резание может осуществляться в двух различных режимах: концом ножа при профилировочных работах и всей кромкой ножа (плоское резание) при планировке. В связи с этим затрудняется определение величины направления и точки приложения реакции грунта на нож для различных положений ножа в пространстве и режимов резания.
Строго говоря сложное воздействие грунта на большую поверхность ножа не приводится только к равнодействующей. Это выявляется например при попытке найти на ноже точку О1 через которую проходит равнодействующая R реакции грунта на нож (рисунок 63). Искомые координаты точки О1 обозначим через l1 и b1 и h1. Разложим R на составляющие Rx Ry и Rz.
Рисунок 1.1 – Схема сил действующих на нож автогрейдера
Рассматривая тяговую раму с ножом в равновесии составим для нее уравнения моментов относительно осей X Y и Z проходящих через шаровой шарнир (точку О):
M -Rzb1 + Ryh1 + A = 0;
M z = 0; -Rxb1 + Ryl1 + C = 0.
Буквами A B и C обозначены в нераскрытом виде моменты от усилий в трех тягах подвески тяговой рамы относительно соответствующих осей.
Определитель составленный из коэффициентов при неизвестных имеет вид
т. е. система не имеет определенного решения. Это объясняется тем что реакция грунта не приводится только к равнодействующей а приводится к динаме т. е. к главному вектору и к главному моменту действующему в плоскости перпендикулярной к главному вектору.
Ввиду того что нахождение положения в пространстве главной оси динамы и координат точки ее пересечения с ножом является очень трудоемким процессом удобнее не находить координаты этой точки а задаваться своей характерной точкой например центром тяжести сечения срезаемой стружки как это принято в тяговых расчетах. Примем теперь что точка О1 (рис. 1.1) является центром тяжести стружки. При такой замене главный вектор как бы сдвигается в пространстве параллельно самому себе (в точку О1). Получается новая система: равнодействующая R равная по величине главному вектору и момент M который и по величине и по направлению отличается от главного момента. Разложим равнодействующую R и момент М на составляющие относительно осей X1 Y1 и Z1 проходящих через точку О1 и имеющих продольное поперечное и вертикальное направления относительно всей машины.
Итак действие грунта на нож сводится к действию трех составляющих Rx Ry и Rz пересекающихся на ноже в центре тяжести сечения вырезаемой стружки и трех моментов Mx Мy и Mz дополняющих каждую составляющую и лежащих в плоскостях перпендикулярных к этим составляющим.
Как показали экспериментальные исследования эти моменты при резании концом ножа достигают в отдельных случаях 10 кН·м а при плоском резании – до 20 – 26 кН·м и иногда до 40 – 45 кН·м. Как по величине так и по знаку моменты непостоянны не имеют явно выраженной зависимости от каких-либо факторов поэтому вводить их в расчеты особенно тяговые пока нецелесообразно.
Величина и направление равнодействующей R зависят от множества факторов: свойств грунта формы и размеров поперечного сечения срезаемой стружки углов установки ножа состояния его режущей кромки и т. д. Поэтому до сих пор сопротивление резанию от которого в основном зависит величина продольной составляющей реакции грунта на нож определяют упрощенным способом. Учитывается только площадь поперечного сечения вырезаемой стружки и степень трудности резания грунта характеризуемая удельным сопротивлением резанию К. Остальную часть сопротивления ножу грунт оказывает за счет призмы волочения.
Существует и еще более упрощенный способ когда всю продольную составляющую реакции грунта на нож относят к площади поперечного сечения стружки. Получающаяся при этом величина – удельное сопротивление копанию Ккоп – имеет большее числовое значение чем К. Экспериментально найдено: К = 25÷14 Нсм2 Ккоп = 10÷30 Нсм2.
Направление равнодействующей принято задавать соотношением ее составляющих:
Rz Rx = m и Ry Rz =n.
Коэффициент n положителен в том случае если реакция грунта действует в ту же сторону (вправо или влево) в какую направлена нормаль опущенная на нож. Коэффициент m положителен если реакция направлена вниз т. е. при резании «затягивает» нож в грунт.
При скорости резания до 15 – 2 мсек изменение ее мало влияет на сопротивление грунта резанию. Но с увеличением скорости резания выше указанного значения сопротивление грунта резко возрастает; эта разница становится соизмеримой с сопротивлением которое соответствует скорости резания близкой к нулю а при определенных скоростях и превосходит его.
Исследованием влияния скорости резания на сопротивление грунта резанию занимались А. Д. Далин П. В. Павлов Ю. A. Beтров и др. В последнее время наиболее подробно этот вопрос осветили II. Г. Домбровский и II. Д Устинкнн.
В основном на изменение сопротивления резанию при увеличении скорости резания оказывают влияние сила инерции срезаемого и отбрасываемого пласта и изменение сопротивления деформации грунта.
Для выяснения влияния силы инерции рассмотрим рисунок 1.2. На нож перемещающийся со скоростью р действует сила сопротивления отделению пласта S и сила трения грунта по ножу Т. Проектируясь на направление движения ножа они дают суммарное сопротивление резанию Рx При больших скоростях резания возникает сила инерции грунта Ри которая направлена противоположно абсолютной скорости перемещения частиц грунта. Нормальная составляющая силы инерции увеличивая прижатие грунта к ножу вызовет приращение силы трения ΔT. За счет этого поднимающийся пласт сильнее прижимается к массиву и сопротивление отделения пласта возрастает на ΔS. Касательная составляющая силы инерции и приращения сил ΔS и ΔT проектируясь на направление движения дадут приращение суммарного сопротивления от инерции Δ.
Рисунок 1.2 – Схема увеличения сил от инерции срезаемого пласта
По данным Н. Г. Домбровского и Н. Д. Устинкина для суглинка при
р = 3 мсек и при угле резания γ = 25° сила инерции составляет 307% сопротивления резанию соответствующего скорости р близкой к нулю; при
р = 74 мсек она равна сопротивлению Рх а при р = 10 мсек превышает Рх в 176 раза.
Изменение сопротивления деформации грунта при увеличении скорости резания объясняется тем что в грунте усилия сжатия при резании передаются от слоя к слою сравнительно медленно. При малых скоростях резания перед ножом успевает образоваться зона опережающего разрушения облегчающая отделение стружки. При больших скоростях такой зоны нет и отделение стружки осуществляется при больших деформациях грунта а следовательно и при больших усилиях.
По Н. Г. Домбровскому и Н. Д. Устинкину на суглинке при γ = 25 величина Δ составляет при скоростях резания 1; 5 и 8 мсек соответственно 17; 449 и 1101% от усилия при скорости резания близкой к нулю.
Следует отметить что вопрос о скорости резания грунта весьма актуален и требует дальнейших исследований.
2 Классификация. Основные конструктивные схемы
Автогрейдеры относятся к числу наиболее распространенных дорожно-строительных машин. Они применяются как при строительстве дорог гак и при их содержании.
В классификации дорожно-строительных машин по технологическому признаку автогрейдеры часто выделяют в отдельную группу так называемых профилирующих машин так как основным назначением их является профилирование и отделка земляного полотна. Однако правомерно будет также отнести автогрейдеры наряду со скреперами бульдозерами и грейдер-элеваторами к более широкой группе землеройно-транспортных машин так как они производят как разработку так и перемещение грунта позволяют осуществить почти весь комплекс земляных работ.
Автогрейдер предназначен выполнять следующие операции:
- возведение насыпей при постройке дорог;
- профилирование дорожного основания;
- устройство корыт и боковых канав;
- профилирование откосов;
- перемешивание грунтов с добавками и вяжущими материалами на полотне дороги:
- киркование изношенного дорожного полотна;
- очистка дорог от снега.
Большое разнообразие работ выполняемых автогрейдером обеспечивается особенностью его конструкции : рабочий орган располагающийся между колесной базой машины может принимать различные установки в плане вертикальной плоскости а также имеет значительный вынос в сторону.
Наличие на автогрейдерах дополнительного рабочего оборудования (кирковщика откосника бульдозерного оборудования и т.д.) увеличивает эксплуатационные способности машины а возможность установки различного сменного оборудования еще более расширяет область применения автогрейдеров и их сезонное использование
Современный автогрейдер представляет собой самоходную с одномоторным приводом машину состоящую из следующих главных частей: основной рамы являющейся основой машины и несущей все остальные ее узлы; тяговой рамы со смонтированным на ней поворотным кругом; рабочего оборудования; дополнительного рабочего оборудования; двигателя; пневмоколесной ходовой части; механизмов трансмиссии и управления; кабины оператора.
Конструкция автогрейдера характеризуется прежде всего принятой для его ходовой части колесной схемой. Последняя определяется так называемой колесной формулой:
где А - число осей с управляемыми колесами;
В - число осей с ведущими колесами;
С - общее число осей.
Выбор колесной схемы имеет большое значение так как она в значительной степени влияет на тяговые свойства автогрейдера его устойчивость маневренность и планирующую способность.
Большинство выпускаемых в настоящее время автогрейдеров (порядка 70-75 % производимых в мире моделей) строятся с колесной формулой 1х2х3. Эта схема обеспечивает автогрейдеру при достаточной простоте конструкции хорошую планирующую способность.
Автогрейдеры с колесной формулой 2х2х2 получаются более маневренными за счет меньшего радиуса поворота однако по сравнению с автогрейдерами со схемой 1х2х3 они обладают худшей планирующей способностью.
Колесные схемы 1х3х3 и 3х3х3 обеспечивают автогрейдеру высокие тяговые качества и проходимость а также хорошую маневренность. Однако автогрейдеры построенные по этим схемам значительно сложнее конструктивно и в эксплуатации а следовательно более дороги. Поэтому их изготавливают в небольших количествах для работы в особо тяжелых грунтовых условиях.
Легкие автогрейдеры предназначенные для работ по содержанию и ремонту дорог могут быть с колесными схемами 1х1х2 и 3х2х2.
У автогрейдеров с ведомыми колесами последние обычно снабжаются механизмом наклона при помощи которого они могут устанавливаться под углом к вертикали.
Наклонная установка колес улучшает восприятие машиной боковых нагрузок и увеличивает ее устойчивость. Управление механизмом наклона выполняют механическим или гидравлическим.
У автогрейдеров со всеми ведущими колесами механизма наклона обычно не предусматривают. Поперечная устойчивость машин с такими колесными схемами достигается за счет поворота колес относительно оси машины.
У трехосных автогрейдеров задние мосты обычно выполняют с балансирной подвеской колес что обеспечивает лучшее сцепление колес с грунтом и повышает приспособляемость их к неровностям почвы.
В целях сохранения максимального сцепления колес с грунтом в различных условиях и снижения их сопротивления перекатыванию колеса автогрейдеров всех типов часто снабжаются устройством регулирования
Привод ведущих колес автогрейдера осуществляется от общего двигателя внутреннего сгорания через тот или иной вид трансмиссии (рис. 1.3). Наибольшее распространение в настоящее время имеет механическая трансмиссия в которой силовая передача от двигателя на ведущие колеса идет через многоступенчатую коробку передач раздаточную коробку и ряд редукторов количество и компоновка которых определяется количеством ведущих осей в данной конструкции автогрейдера.
Рисунок 1.3 - Основные схемы трансмиссий автогрейдеров
Для тяжелых и особо тяжелых автогрейдеров применяют гидромеханическую трансмиссию в которой вместо муфты сцепления установлен гидротрансформатор или гидрообъемный привод колес. В последнем случае на ведущих колесах устанавливаются индивидуальные гидродвигатели работающие от гидравлического насоса приводимого в действие от двигателя внутреннего сгорания.
Для осуществления поворота управляемых колес на автогрейдерах устанавливается либо механическое либо гидравлическое рулевое управление. Механическое управление часто снабжается гидравлическим или пневматическим усилителем.
Управление основным рабочим оборудованием автогрейдера а также кирковщиком которым в качестве дополнительного оборудования снабжаются все автогрейдеры заключается в подъеме и опускании всего отвала или поочередно его правого или левого концов повороте в плане выдвижении его в бок выносе тяговой рамы в сторону подъеме и опускании кирковщика. Привод этих механизмов осуществляется от общего двигателя автогрейдера и бывает редукторно-карданным гидравлическим или комбинированным.
Основные рамы автогрейдеров чаще всего выполняются цельными. Возможны конструкции основных рам которые можно удлинять за счет специальной вставки что увеличивает размер колесной базы автогрейдера и улучшает таким образом его планирующую способность. Существуют также конструкции в которых две части основной рамы в горизонтальной плоскости соединяются между собой шарнирно. Шарнирные рамы давая возможность сдвигать передние колеса в сторону относительно задних позволяют увеличить устойчивость автогрейдеров к боковым нагрузкам а также снизить величину радиуса поворота машины. Кроме того шарнирное устройство основной рамы позволяет при необходимости отсоединить переднюю ее часть вместе с тяговой рамой и использовать заднюю часть в качестве двухосного тягача.
3 Обзор существующих конструкций
Автогрейдеры оборудованы колодочными стояночным и колесными тормозами. На автогрейдере имеются электрооборудование сигналов для движения по дорогам и работы в темное время суток осветительные приборы.
Автогрейдер ДЗ -143 (рисунок 1.4) и его модификации по конструкции аналогичны автогрейдеру ДЗ-122А и имеют много унифицированных узлов.
В зависимости от модификации на автогрейдере устанавливается двигатель А-01М с пускачом или А-01МС с электростартерным пуском. В отличие от ДЗ-122А на автогрейдере ДЗ-143 установлен более мощный рыхлитель-кирковщик расположенный сзади.
– рыхлитель-кирковщик; 2 – рама подмоторная; 3 – гидробак; 4 – ящик аккумуляторный; 5 – задний мост; 6 – бак топливный; 7 – кабина; 8 – гидроцилиндр выноса отвала; 9 – гидроцилиндр подъема отвала; 10 – тяговая рама; 11 – основная рама; 12 – бульдозер; 13 – передняя ось; 14 – поворотный круг; 15 – отвал; 16 – коробка передач
Рисунок 1.4 – Схема автогрейдера ДЗ-143
Предусмотрена возможность агрегатирования его с поставляемым по особому заказу дополнительным оборудованием – плужным снегоочистителем удлинителем отвала толкающей плитой щеткой и др.
Автогрейдер ДЗ-98А представленный на рисунке 1.5 – трехосная машина со всеми ведущими колесами. Задняя двухосная тележка образуется из двух одинаковых ведущих мостов. Передний ведущий мост – управляемый. На автогрейдере установлена механическая коробка передач обеспечивающая шесть передач переднего и заднего хода. Автогрейдер оборудован кирковщиком в передней части машины.
Управление рабочими органами гидравлическое обеспечивающее все изменения положения отвала тяговой рамы и кирковщика из кабины машиниста. Управление поворотом передних колес осуществляется рулевым механизмом с гидроусилителем. Автогрейдер оборудован стояночным тормозом и многодисковыми колесными тормозами среднего и заднего ведущих мостов. Привод колесных тормозов пневматический от компрессора на двигателе. Привод имеет два контура которые управляют тормозами среднего и заднего мостов раздельно. На автогрейдере предусмотрено электрооборудование с необходимым комплектом указателей и осветительных приборов.
– силовая установка; 2 – кабина; 3 – рама; 4 – гидросистема; 5 – тяговая рама; 6 – кирковщик; 7 – передний ведущий мост; 8 – отвал; 9 – поворотный круг; 10 – средний ведущий мост; 11 – подвеска мостов; 12 – задний ведущий мост
Рисунок 1.5 – Схема автогрейдера ДЗ - 98А
Автогрейдер ДЗ-140 и его модификации выполнены по традиционной схеме ходовой части с задней балансирной ведущей тележкой. Передние ведущие колеса приводятся с помощью гидромотора и планетарного редуктора включаются на первой передаче переднего хода. Трансмиссия автогрейдера гидромеханическая установлены две коробки передач унифицированные с автогрейдерами класса 160. Предусмотрена модернизация автогрейдера с установкой более мощной коробки передач и двигателя мощностью 220 кВт. Основная рама автогрейдера шарнирно сочленена с гидравлическим управлением поворота полурам. Имеются модификации автогрейдера оборудованные системами «Профиль-20» и «Профиль-30». Автоматическое управление отвалом автогрейдера. Автогрейдеры всех классов оборудуются одной из систем автоматического управления отвалом: «Профиль-10» «Профиль-20» «Профиль-30».
«Профиль-10» предназначен для автоматического обеспечения заданного углового положения отвала автогрейдера в поперечной плоскости независимо от поперечного профиля полотна и применяется при окончательной отделке или планировке поверхности. Система позволяет работать как в режиме ручного управления отвалом так и в режиме автоматического выдерживания заданного поперечного профиля полотна.
Модификация автогрейдера ДЗ - 122А - 6 (рисунок 1.6) оборудована шарнирно сочлененной рамой. Поворот передней полурамы производится гидроцилиндром. Наличие такой рамы позволяет значительно сократить радиус поворота машины а также повысить устойчивость автогрейдера при копании за счет движения «крабом».
Рисунок 1.6 – Схема автогрейдера с шарнирно сочлененной рамой:
а – положение для крутого поворота; б – положение при движении «крабом»
Автогрейдер класса "140" (рис. 1.7) — новая эффективная машина оснащенная гидромеханической трансмиссией с автоматической коробкой перемены передач фирмы "ZF" (Германия) а также балансирной тележкой фирмы "NAF" (Германия) с дифференциалом типа "No-Spin". Возможность установки двигателя ЯМЗ (Россия) или "DEUTZ" (Германия) позволяет автогрейдеру ГС-14.03 эффективно осваивать требуемые объемы при выполнении землеройно-профилировочных работ строительстве и содержании дорог.
Рисунок 1.7 – Автогрейдер ГС – 14.03
Автогрейдер ГС-14.03 — машина для выполнения землеройно-профилировочных работ строительства и содержания дорог. ГС-14.03 может использоваться на работах по перемещению и распределению грунта и дорожно-строительных материалов планировке откосов насыпей устройству корыта и боковых кюветов. В зимний период времени можно использовать для очистки дорог от снега. Кроме того автогрейдер ГС-14.03 применяется для смешения грунтов с добавками и вяжущими материалами на полотне дороги а также для рыхления асфальтовых покрытий булыжных мостовых и тяжелых грунтов с помощью дополнительного рабочего органа — рыхлителя.
Технические характеристики.
Колесная формула 1 х 2 х 3
Двигатель DEUTZ BF04M1013
Трансмисссия гидромеханическая
Число передач впередназад 63
Гавариты L x B x H м 94 х 253 х 358
Выполнение основных функций автогрейдера ГС-14.03 происходит с помощью специального рабочего органа — отвала с ножом который смонтирован на раме машины и приводится в действие от дизельного двигателя. Его можно поднимать опускать поворачивать в горизонтальной и вертикальной плоскости. Автогрейдер обладает хорошей маневренностью и возможностью изменения углов установки отвала в горизонтальной и вертикальной плоскостях а также он может осуществлять вынос отвала в сторону.
С целью повышения производительности труда и улучшения условий работы оператора в автогрейдере содержащем основную раму рабочий орган балансиры и систему автоматического управления положением отвала пропорциональные датчики автоматической системы управления установлены между балансиром и основной рамой. Помимо этого на втором балансире устанавливается дополнительный датчик.
Дополнительное навесное оборудование: отвал поворотный комплект ножей снегоочистительных кирковщик передний рыхлитель задний боковое рабочее оборудование.
На автогрейдере ГС-18.05 (рис. 1.8) установлен 180-сильный дизель ЯМЗ-236Д4 и механическая КПП с гидропружинными муфтами.
Рисунок 1.8 – Автогрейдер ГС – 18.05
Двигатель ЯМЗ – 236Д4
Трансмисссия механическая
Число передач впередназад 124
Гавариты L x B x H м 94 х 255 х 358
Автогрейдер ГС-18.05 предназначен для возведения земляного полотна устройства дорожных оснований и покрытий разнообразных планировочных работ отделки дорожного полотна и профилирования а также для ремонта и содержания дорог городских проездов и площадей.
Шарнирно сочлененная рама поворотный грейдерный отвал позволяют производить широкий захват дорожного полотна эффективно используя бульдозерный и грейдерный отвалы.
Задний мост самоблокирующийся с дифференциалом свободного хода.
Полноповоротный грейдерный отвал позволяет проводить профилирование дорожного полотна при движении задним ходом что повышает производительность.
Кабина повышенной обзорности с удобно расположенным отопителем обеспечивающим максимально комфортный режим снабжена дополнительными фарами.
Автогрейдер ГС - 18.05 снабжен рабочей стояночной и резервной тормозными системами что обеспечивает не менее пяти торможений при неработающем двигатели или вышедшем из строя насосе.
Благодаря полноповоротности грейдерного отвала можно вести профилирование при движении задним ходом.
Автогрейдер TG 180 (рис. 1.9) предназначен для выполнения больших объемов землеройных и профилировочных работ при строительстве и содержании дорог.
Рисунок 1.9 – Автогрейдер ТG 180
Автогрейдер оборудован комфортабельной кабиной с инновационной системой трансформации обеспечивающей удобное управление как сидя так и стоя. Новый дизайн копотной системы соответствует всем современным требованиям эргономики и обеспечивает свободный доступа к узлам и агрегатам при проведении ТО. TG 180 комплектуется мощным двигателем 147 кВт гидромеханической трансмиссией с автоматической коробкой передач фирмы «ZF» тандемной тележкой фирмы «NAF» с дифференциалом типа "No-Spin" что позволило значительно увеличить производительность машины и сократить расходы на ее техническое обслуживание. Для автогрейдера имеется большой набор сменного рабочего оборудования (поворотный бульдозерный отвал боковой грейдерный отвал рыхлитель заднего расположения).
По желанию потребителя автогрейдер может комплектоваться полноприводной трансмиссией.
Колесная формула 1 х 2 х 3 (1 x 3 x 3)
Двигатель Сummins 6CTAA 83 – C215
Мощность кВт 158 147
Гавариты L x B x H м 94 х 249 х 328
Трансмиссия марки ZF типа " full-power-shift" с преобразователем крутящего момента 6 передних 3 задних скоростей. Гидростатический привод передней оси без развала колёс. Многодисковый тормоз с масляной ванной с резервом тормозных сил. Рабочая гидравлика типа " load sensing".
Длина отвала 3660 мм прочность материала ножей HB 450. Поворотный круг на скользящих направляющих с предохранительной муфтой в приводе поворотного круга. Шарнирно сочлененная рама с изломом оси на 30 град. влевовправо.
откидывающаяся кабина РОПСФОПС на упругой подвеске полностью облицованная (с оптимальной изоляцией от шума и вибраций) с отоплением в режимах со всасыванием свежего воздуха либо с закрытой циркуляцией форсунка обдува для ветрового стекла система всасывания свежего воздуха с противопылевым фильтром 2 откидных наружных зеркала 1 зеркало внутри стеклоочистительно-промывная установка для ветрового стекла стеклоочиститель сзади два стеклоочистителя слева и справа на нижнем переднем стекле солнцезащитные шторки спереди и сзади шумоизоляционная облицовка затемненное стекло ЕВРО-управление электронный мультифункциональный индикатор с указателем для температуры трансмиссионного масла числа оборотов двигателя температуры охлаждающей жидкости счётчик моточасов счетчик пройденного пути (за деньвсего) цифровая индикация скорости часы индикатор бортового напряжения указатель сервисных интервалов.
Автоматическая предупреждающая индикация для температуры трансмиссионного масла температуры охлаждающей жидкости запаса топлива 310 л (1-ый сигнал визуальный 2-ой сигнал акустический) сигнализаторы и индикаторы остановки двигателя загрязнения фильтров рабочей и транспортной гидросистемы неполадок тормозной системы воздушного фильтра стояночного тормоза контроля заряда аккумулятора давления трансмиссионного масла тахометра дальнего света сигнально-мигающего света проверки освещения. Перемещаемый пульт управления (4 положения) а также регулируемое сидение с амортизацией и ремнем безопасности.
Шины 13.00 - 24 TG 12PR с баластиром. Вертикально расположенная труба выхлопных газов. Грузовые клапаны для цилиндров регулировки угла резания отвала. Защитный кожух цилиндра регулировки угла резания отвала
сигнализация обратного хода
Также по желанию клиента можно дооснастить грейдер следующими опциями: система нивелирования САУ; предпусковой подогреватель аудиосистема; гидравлическое и трансмиссионное масла для Севера; рыхлитель.
Гарантия 12 месяцев или 1000 моточасов в зависимости от того что наступит ранее.
4.1 Механизм подвески отвала на хребтовой балке [8]
Механизм подвески отвала (рис. 1.10) включает установленный на хребтовой балке с возможностью поперечного перемещения кронштейн для соединения с ним рабочим оборудованием и гидроцилиндра управления кронштейном отличающийся тем что с целью повышения производительности автогрейдера грейдерного типа кронштейн выполнен с направляющей поперечной прорезью для размещения в ней хребтовой балки а механизм подвески снабжен установленными по концам прорези с возможностью поворота вдоль своей продольной оси втулками с вырезами образующими торцевые стороны направляющей прорези и закрепленными соответственно на втулках плоскими упорами для взаимодействия с кронштейном а на кронштейне дуговыми опорами для взаимодействия с хребтовой балкой. В исходном положении кронштейн 2 симметричен хребтовой балке 1. Это положение не рабочее и используется при транспортировке . Для перевода в рабочее положение рабочего оборудования подают рабочую жидкость например в бесштоковую полость гидроцилиндра 4 шток выдвигается влево перемещая подвижный кронштейн 6 вследствие чего отвал выдвинется вслед за кронштейном и одновременно наклонится по часовой стрелке под углом относительно продольной оси автогрейдера.
Подача рабочей жидкости в штоковую полость гидроцилиндра приведет к перемещению кронштейна 6 вправо относительно хребтовой балки и произойдет поворот отвала против часовой стрелки.
Рисунок 1.10 - Схема механизма подвески отвала на хребтовой балке
4.2 Балансирная подвеска [9]
Автогрейдер (рис. 1.11) включает в себя основную раму 1 тяговую раму с рабочим оборудованием 2 задние 3 и передние 4 балансиры с несущими колесами поперечную балку. Сущность изобретения заключается в том что благодаря возможности изменения базы балансира 4 с помощью гидроцилиндра 11 эту величину подбирают так чтобы она была как можно ближе к длине полуволн неровностей по которой идет балансир. При выполнении этого условия центр балансира (поперечная балка) имеет минимальные колебания по высоте благодаря равенству размеров верхних половин рычагов 7 и распорных тяг 9 также из-за того что тяги к рычагам прикреплены по середине. В целом рама автогрейдера и тяговая рама с рабочим оборудованием имеют взаимные. Сущность изобретения заключается в том что благодаря возможности изменения базы балансира 4 с помощью гидроцилиндра 11 эту величину подбирают так чтобы она была как можно ближе к длине полуволн неровностей по которой идет балансир. При выполнении этого условия центр балансира (поперечная балка) имеет минимальные колебания по высоте благодаря равенству размеров верхних половин рычагов 7 и распорных тяг 9 также из-за того что тяги к рычагам прикреплены по середине. В целом рама автогрейдера и тяговая рама с рабочим оборудованием имеют взаимные колебания что в целом ведет к улучшению планирующих свойств автогрейдера а следовательно к увеличению производительности.
Работа автогрейдера осуществляется в автоматическом или ручном режимах. В первом случае (наиболее эффективном) автоматика которая анализирует спектр длин или длины волн впереди лежащих неровностей непосредственно во время работы управляет нужной величиной базы балансира для достижения наибольшей планирующей способности.
Рисунок 1.11 - Схема балансирной подвески автогрейдера
Регулировка происходит следующим образом: под воздействием управляющего сигнала шток гидроцилиндра 11 выдвигается или вдвигается изменяя таким образом базу балансира.
Применение такой балансирной подвески позволяет уменьшить количество проходов при планировочных работах с 5-ти до 2-х.
4.3 Шнековый откосник непрерывного действия [10]
Цель изобретения заключается в снижении энергоемкости и повышении надежности работы планировщиков на влажных и липких грунтах.
Рисунок 1.12 - Схема шнекового откосника непрерывного действия
Шнековый откосник изображенный на рис.1.12 имеет установленные на валу 1 по винтовой линии спицы 2 с резцами 3 и закрепленный на спицах 2 транспортирующий спиральный элемент который выполнен из струн 5
Каждая из спиц 2 выполнена серповидной в поперечном сечении и имеет отверстия 4 в которых размещены струны 5 транспортирующего элемента.
Свободные концы струн 5 соединены с крайними спицами 2 общим упругим элементом и металлической пластиной. Причем один торец упругого элемента жестко соединен с боковой поверхностью спицы 2 а другой - с боковой поверхностью металлической пластины.
При вращательно-поступательном движении откосника резцы 3 скалывают грунт. Он поступает на струны 5 и транспортируется по ротору. При этом струны 5 за счет связи с упругим элементом совершают колебательное движение что позволяет струнам 5 самоочищаться от налипшего грунта.
4.4 Рабочее оборудование автогрейдера [11]
Изобретение относится к землеройно-транспортным машинам в частности к управлению рабочими органами автогрейдеров предназначенных главным образом в строительстве.
Целью изобретения является повышение эффективности путем стабилизации глубины резания при изменении угла резания отвала в процессе работы. На рис.1.13а изображено рабочее оборудование автогрейдера в одном из вариантов соединения двуплечего рычага а на рис.1.13б в другом соединении двуплечего рычага.
Механизм изменения угла резания отвала автогрейдера содержит поворотный круг 1 с кронштейном 2 отвал 3 соединенный в верхней части шарниром 4 со штоком гидроцилиндра 5 корпус которого в шарнире 6 соединен с неподвижным кронштейном 7 поворотного круга 1. Гидроцилиндр 5 может быть установлен в середине отвала 3 или в количестве двух штук по его краям. В нижней части отвал 3 соединен в шарнире 8 с двуплечим рычагом 9 который в шарнире 10 соединен со свободным концом кронштейна 2 поворотного круга 1. Привод двуплечего рычага 9 осуществляется от корпуса гидроцилиндра 5 тягой 11 управления соединенной с ними в шарнирах 12 и 13.
Рисунок 1.13 - Схема рабочего оборудования автогрейдера
Предлагаемый механизм является шестизвенным с одной степенью свободы (ведущее звено - шток с поршнем гидроцилиндра 5 ведомое звено - отвал 3 неподвижное звено - поворотный круг 1 с кронштейнами 2 и 7). Механизм по рис.1.13а работает следующим образом: при подаче от гидросистемы автогрейдера масла под давлением в первом случае в поршневую полость гидроцилиндра 5 поршень со штоком выдвигается из его корпуса. При этом отвал 3 поворачивается в шарнире 8 по часовой стрелке увеличивая угол резания γ и глубину резания hр а корпус гидроцилиндра 5 поворачивается в шарнире 6 по часовой стрелке перемещая через шарнир 13 тягу 11 управления вниз так как шарнир 4 (рис.1.13а) при изменении угла резания отвала от минимального до максимального значений находится по вертикали справа от опорного шарнира 8.
Тяга 11 управления перемещаясь вниз через шарнир 12 поворачивает двуплечий рычаг 9 в шарнире 10 против часовой стрелки. При этом через шарнир 8 двуплечего рычага 9 отвал 3 перемещается вверх уменьшая глубину резания 11р на величину ее увеличения при своем первоначальном повороте в шарнире 8тем самым стабилизируя глубину резания hр установленную машинистом путем опускания поворотного круга 1.
Для стабилизации первоначально установленной глубины резания расстояния между шарнирами 810 и 12 двуплечего рычага 9 а также между шарнирами 6 и 13 корпуса гидроцилиндра 5 подобраны так что при изменении угла резания отвала от минимального до максимального значений режущая кромка его перемещается горизонтально.
Если при изменении угла резания отвала от минимального до максимального значений шарнир 4 расположен по вертикали слева от опорного шарнира 8 то соединение отвала 3 двуплечего рычага 9 кронштейна 2 и тяги 11 управления в шарнирах 810 и 12 выполняется по схеме показанной на рис. 1. 13 б.
Расположение шарнира 4 относительно опорного шарнира 8 влияет на характер движения корпуса гидроцилиндра 5 и тяги 11 управления при изменении угла резания отвала 3. Их взаимное расположение определяется условиями компоновки механизма для конкретной модели автогрейдера.
На основании анализа патентов авторских свидетельств и существующих конструкций можно сделать вывод о том что автогрейдер является машиной наиболее удачно сочетающей универсальность (в достаточно широком диапазоне отраслей) и простоту как самой конструкции автогрейдера так и навески различного рабочего технологического оборудования.
Были выявлены следующие тенденции дальнейшего развития конструкций автогрейдеров:
- увеличение единичной мощности;
- создание маневренных мини-автогрейдеров для работы в условиях
города и фермерских хозяйств;
- применение динамических рабочих органов для интенсификации рабочего процесса;
- расширение универсальности за счет появления других типов рабочего оборудования;
- внедрение рабочих процессов основанных на прогрессивных методах дорожного строительства (например повышение производительности получение более сложных по профилю канав и кюветов снижение энергоемкости процесса и т.п.);
-более широкое внедрение систем автоматического управления рабочими органами улучшение их технических характеристик и создание комплексных систем автоматического управления обеспечивающих контроль как поперечного так и продольного профиля дорожного полотна.
3 ОК.docx
Основной несущей конструкцией автогрейдера (рис. 3.1) является гнутая в вертикальной плоскости сварная рама. Сверху на нее устанавливается двигатель 1 а снизу она связана с задним мостом механизма передвижения 11.
– силовая установка; 2 – топливный бак; 3 – кабина; 4 – рама; 5 – гидросистема; 6 – отвал бульдозера; 7 – кирковщик; 8 – передняя ось; 9 – тяговая рама; 10 – отвал; 11 – задний мост
Рисунок 3.1 – Схема автогрейдера АС - 1
Механизм передвижения включает в себя коробку переменны передач карданную передачу балансирную подвеску и колеса.
В передней части рама переходит в гнутую выпуклостью вверх прямоугольную в сечении балку 4 которую обычно называют хребтовой балкой. В средней части хребтовой балки 4 устанавливаются кронштейны для крепления гидроцилиндров 5 подъема и опускания отвала а впереди заканчивается стойкой с проушинами для шарнирного присоединения балки к переднему мосту 8 и навески дополнительного рабочего оборудования: бульдозерного отвала 6 и кирковщика 7 которое приводится в движение гидроцилиндрами.
С внутренней стороны к стойке хребтовой балки с помощью шарового шарнира присоединена тяговая рама 9 с рабочим оборудованием. Тяговая рама 9 осуществляет передачу к рабочему органу тягового усилия от основной рамы автогрейдера. В передней части тяговая рама заканчивается шаровым пальцем с помощью которого она присоединяется к стойке хребтовой балки. На другом конце тяговая рама имеет поперечную балку с шаровыми пальцами по бокам для присоединения штоков гидроцилиндров 5 подъема и опускания рабочего органа.
Техническая характеристика автогрейдера
Тип автогрейдера средний
Мощность двигателя кВт 99
Угол наклона отвала град 40 90 (50)
Угол резания град 30 70 (40)
Угол поворота отвала град 360°
Вынос отвала в сторону м 081
Высота подъема отвала м 04
Колесная формула 1x2x3
Давление в гидроприводе МПа 16
Радиус поворота м 14
Тип трансмиссии гидромеханическая
Дорожный просвет м 04
Скорости передвижения кмч:
Габаритные размеры мм:
Эксплуатационная масса т 143
Оконч.doc
В результате работы над курсовым проектом было выполнено:
- обзор и анализ существующих конструкций;
- обзор теорий резания и копания грунтов рабочими органами землеройных машин;
- проведен патентный обзор;
- изучена и разработана технология производства работ автогрейдерами.
Произведен тяговый расчет выполнены расчеты на прочность оборудования автогрейдера.
Автогрейдер АС - 1 имеет гидрофицированный кирковщик который позволяет управлять кирками во время рыхления или взламывания дорожного полотна.
Система автоматики обеспечивает ровность поверхности при работе машины на приготовлении полотна дороги или сравнивания больших площадей в строительстве причем с большей точностью и производительностью.
Проведенный технико-экономический расчет с целью оценки экономической целесообразности разработки автогрейдера позволил определить эксплуатационную производительность спроектированного автогрейдера рассчитать удельные технико-экономические показатели.
Это в конечном итоге позволяет сделать вывод о целесообразности проведенной работы.
Список использованных источников
Ветров Ю.А. Баладинский В.Л.Машины для специальных земляных работ. - Киев: Вища школа 1980. – 192 с.
Волков Д.П. Машины для земляных работ: Учебник для студентов.-М.: Машиностроение 1992 . - 448 с.
Анурьев В.И. Справочник конструктора-машиностроителя. В 3-х т. Т.2. - М.: Машиностроение 1992. - 584 с.
Хархута Н. Я. Дорожные машины. Теория конструкция и расчет. Л.: Машиностроение 1976. – 454 с.
Ронинсон Э.Г. Автогрейдеры. - М.: Высшая школа 1982. – 283 с.
Севров К.П. Горячко Б. В. Автогрейдеры: конструкция теория расчет. - М.: Машиностроение 1970 . – 252 с.
Справочник конструктора дорожных машин Под ред. Бородачева И.П.- М.: Машиностроение 1975. – 594 с.
Пат. 2036278 РФ МПК E 02 F 376. Автогрейдер.– опубл. 27.05.95 Бюл. №15.
Пат. 2046887 РФ МПК E 02 F 376. Балансирная подвеска автогрейдера. – опубл. 27.10.95 Бюл.№30.
Пат. 2036277 РФ МПК E 02 F 376. Откосник автогрейдера. – опубл. 27.05.95 Бюл. №15.
Пат. 2041319 РФ МПК E 02 F 376. Рабочее оборудование автогрейдера. – опубл. 09.08.95 Бюл. № 22.
начало.doc
Автогрейдер основная рама с хребтовой балкой тяговая рама земляное полотно гидромотор гидроцилиндр обзор описание расчеты
Объектом исследования является автогрейдер средний с колесной формулой 1х2х3. Он предназначен для ведения землеройно-транспортных и строительных работ на грунтах I – III категории.
Цель работы – разработать и рассчитать конструкцию среднего автогрейдера.
В результате выполнения курсового проекта была разработана конструкция автогрейдера среднего.
Проведена классификация принципиальных схем автогрейдеров выполнен обзор и анализ существующих конструкций автогрейдеров рассмотрены новые принципиальные конструктивные решения по патентной литературе.
Приводится описание спроектированной конструкции.
Выполнены прочностные тяговые и технико-экономические расчеты.
В технико-экономическом расчете была рассчитана эксплуатационная производительность автогрейдера и определены удельные технико-экономические показатели.
Обзор и анализ существующих конструкций . 7
1 Взаимодействие ножа автогрейдера с грунтом 7
2 Классификация. Основные конструктивные схемы 11
3 Обзор существующих конструкций 14
4 Патентный обзор 22
Технология производства работ 29
Описание конструкции 33
Расчет конструкции 35
1 Выбор основных параметров 35
2 Тяговый расчет автогрейдера 35
3 Расчет сил действующих на автогрейдер 41
4 Расчет тяговой рамы 46
5 Расчет гидроцилиндра 50
Технико-экономический расчет 52
Список использованных источников 55
Машины для земляных работ являются одними из основных видов машин с помощью которых осуществляется комплексная механизация в строительстве в промышленности строительных материалов горной и цветной металлургии мелиорации сельского хозяйства и других отраслях народного хозяйства.
Интенсификация рабочих органов машин для земляных работ в строительстве осуществляется главным образом на базе:
а) создания и внедрения в производство принципиально новой технологии и материалов;
б) создания машин большой единичной мощности и производительности;
в) агрегатов которые работают на основе использования новых технических эффектов.
Реализация этих положений основывается на повышении эффективности исследований и сокращения сроков внедрения достижений науки и техники в производство и модульного принципа создания систем машин.
Оснащение строительства надежными высокоэффективными машинами ускоренная замена устаревшей техники новыми высокопроизводительными машинами выпуск строительных роботов и машин с многофункциональными рабочими органами-манипуляторами - один из важных рычагов повышения эффективности работ в строительстве.
Создание высокопроизводительных землеройных машин осуществляется по следующим направлениям:
Совершенствование рабочих органов и машин традиционного типа которые находятся в настоящее время в эксплуатации.
Производство принципиально новых рабочих органов и машин на базе использования достижений фундаментальных наук.
Улучшение их социальной приспособленности повышение основных эргономических эстетических и экологических качеств.
Автоматизация управления машиной и комплексами совместно работающих машин а также применению микропроцессоров и бортовых ЭВМ.
Комплекс вопросов которые возникают при разработке новой техники установлении рациональных параметров машин и оборудования охватывает решение ряда задач по конструированию надежных ресурсосберегающих машин обеспечивающих снижение металлоемкости энергоемкости и сокращение трудовых затрат.
Существующие рекомендации по созданию землеройных машин основываются на рассмотрении примеров касающихся разработки частных решений что обеспечивает успешную разработку в основном аналогичных конструкций. Такая методика без разработки общих фундаментальных положений оказывается недостаточной при решении новых сложных задач совершенствования землеройной техники.
Выпуск высокоэффективного землеройного оборудования требует разработки методики синтеза рабочих органов которая позволяет на широкой научной основе осуществлять формирование новых технических решений. Отсутствие общих методологических положений затрудняет ориентацию в непрерывно обновляющемся многообразном мире строительной техники особенно в условиях широкого использования в практике создания новых землеройных машин систем автоматизированного проектирования (САПР).
Применение автоматического управления рабочим процессом машин повышает качество работ и снижает их трудоемкость.
В настоящее время совершается переход от проектирования отдельных машин к проектированию и внедрению комплекса машин. Это позволяет наиболее широко унифицировать машины и упорядочить их выпуск и применение в строительстве. Комплексное проектирование производится на базе типажа машин. Типаж разрабатывается для каждого вида оборудования. Им предусматриваются ряды машин каждого вида которые могут полностью удовлетворить запросы строительного производства. Типажом оговаривается значение тех главных параметров машин от которых зависят основные показатели их работы. Так главными параметрами машин являются: для автогрейдеров - длина ножей; для экскаваторов и скреперов - емкость ковшей; для бульдозеров - тяговые усилия и т.д.
Повышение производительности и снижение себестоимости единицы продукции является важной народнохозяйственной задачей. Такая задача поставлена как перед эксплуатационниками так и перед конструкторами машин. Повысить производительность дорожных машин можно путем увеличения размеров их рабочих органов уменьшения времени затрачиваемого на совершение рабочих операций и снижения непроизводительных потерь.
2 Техн раб.docx
Придавая рабочему оборудованию посредством механизмов управления различное положение путем его подъема и опускания установки под тем или иным углом захвата смещая его в ту или иную сторону от продольной оси машины и устанавливая его с различным углом к горизонту автогрейдером можно выполнять разнообразные рабочие операции :
- резание грунта с одновременным его перемещением в сторону;
- разравнивание и планировку грунта и других материалов слоем определенной толщины и уклона;
- перемещение сыпучих материалов (гравия щебня снега и т.п.) в сторону вверх или вниз по откосу;
- смешивание различных грунтов и сыпучих материалов на дороге между собой и с добавками.
В связи с такими возможностями автогрейдеров их широко применяют в строительстве и содержании автомобильных дорог и аэродромов а так же и на других земляных и планировочных работах.
На строительстве и содержании автомобильных дорог автогрейдером как одной из основных дорожных машин выполняют следующие работы:
а) Постройка земляного дорожного полотна за счет грунта вырезаемого с боков дороги. При этом производится перемещение и разравнивание грунта на полотне дороги отделка кюветов с приданием их откосам требуемого наклона и. наконец планировка грунта на полотне для получения ровной поверхности с необходимым поперечным уклоном. В зависимости от высоты насыпи дорожного полотна и следовательно требуемого для ее возведения объема грунта кюветы при заданной их глубине делаются большей или меньшей ширины. Обычно наибольшая высота насыпи которая может быть построена автогрейдером не превышает 0 7 м.
б) Постройка дорожного полотна на косогорах насыпью или полувыемкой-полунасыпью.
в) Разравнивание и планировка грунта при постройке дорожного полотна или иного сооружения где используются другие машины - экскаваторы и грейдер-элеваторы. В этом случае вырезание грунта и перемещение его в насыпь производятся этими машинами; для возки грунта в насыпь им придаются при необходимости транспортные средства. Автогрейдер производит только разравнивание грунта и затем окончательную отделку поверхности полотна с приданием ей необходимого поперечного уклона. Отделка резерва по окончании работ также может быть выполнена автогрейдером.
г) Устройство в земляном полотне корыта при постройке дорожного покрытия.
д) Разравнивание песка гравийного и щебеночного материала слоем определенной толщины из куч или валов при постройке дорожного покрытия.
е) Перемешивание грунта и гравийного материала с различными добавками при улучшении покрытия дорог.
ж) Прочистка канав и восстановление поперечного профиля грунтовых дорог.
з) Кирковка гравийной и щебеночной одежды дорожного полотна.
и) Планировка откосов земляных выемок и насыпей.
к) Расчистка дорожного полотна от снега.
Постройка земляного дорожного полотна производится путем последовательных проходов автогрейдера с вырезанием грунта из кювета перемещением грунта на полотно дороги и разравниванием с требуемым уклоном. Производительность автогрейдера будет находится в прямой зависимости от числа таких проходов для выполнения работы. Это число зависит от размеров дорожного полотна рода грунта и мощности автогрейдера. За один проход автогрейдером вырезается стружка 012-014 м2. Для устройства нормальных кюветов глубиной 05-06 м потребуется при такой стружке сделать четыре-пять проходов автогрейдера только по вырезанию грунта. Общее число проходов зависит так же и от порядка и последовательности с какой они выполняются. Поэтому до того как приступить к работе необходимо определить потребное наименьшее число проходов а так же разработать порядок и последовательность их выполнения имея в виду зависимости производительности от числа проходов. Этот порядок для наглядности вычерчивают в виде схемы которая обычно называется с х е м о й п р о ф и л и р о в а н и я. Она является руководством при производстве работ автогрейдером в данных условиях. На рис.2.1 изображена схема проходов при постройке дорожного полотна с глубиной кюветов 06 м. На рис.2.2 показана одна из возможных схем проходов автогрейдера по устройству корыта в земляном дорожном полотне.
Рисунок 2.1 - Схема проходов при постройке дорожного полотна с глубиной кюветов 0 6 м
Рисунок 2.2 - Схема проходов автогрейдера по устройству корыта в земляном дорожном полотне