Аксиально-поршневой насос F11




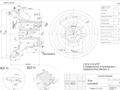
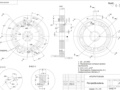
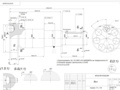
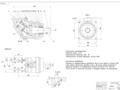
- Добавлен: 25.10.2022
- Размер: 9 MB
- Закачек: 0
Описание
Состав проекта
![]() |
![]() ![]() ![]() ![]() |
![]() ![]() ![]() |
![]() ![]() ![]() ![]() |
![]() ![]() ![]() ![]() |
![]() ![]() ![]() |
![]() ![]() ![]() |
![]() ![]() ![]() |
![]() ![]() ![]() ![]() |
![]() ![]() ![]() ![]() |
![]() ![]() ![]() |
Дополнительная информация
блок цилиндров.dwg

Нормальный исходный
Коэффициент смещения
Делительный диаметр
сопряженного червяка
Радиусы скруглений 6мм max
Штамповочные уклоны
Неуказанные пред. отклонения размеров: отверстий +t2
остальных +- t22 по ГОСТ 25670-83
h14 ± 2.Поверхность А притереть с поверхностью детали 4
Внешний окружной модуль
Внешнее конусное расстояние
Среднее конусное расстояние
Средний делительный диаметр
титульный лист.doc
Конструкторско-механический факультет
Кафедра гидропривода и гидропневмоавтоматики
ПОЯСНИТЕЛЬНАЯ ЗАПИСКА
к курсовому проекту
по дисциплине «Объемные гидромашины и гидропередачи»
на тему «Аксиально-поршневой насос F11»
Руководитель Леладзе.И.С.
распределитель.dwg

Нормальный исходный
Коэффициент смещения
Делительный диаметр
сопряженного червяка
Радиусы скруглений 6мм max
Штамповочные уклоны
Неуказанные пред. отклонения размеров: отверстий +t2
остальных +- t22 по ГОСТ 25670-83
20 23 HRC 2. Неуказанные острые кромки притупить 3. H12
± 4. Притереть поверхность А с поверхностью детали 2
сборочный чертеж.dwg

Техническая характеристика
Номинальное давление
Номинальная частота вращения
Технические требования
Момент на проворачивание приводного вала после сборки не более 14Нм
При сборке обеспечить боковой зазор и величину пятна контакта в
зубчатой передачи в соответствии степени точности ГОСТ 1643-81
Течь масла по плоскости разъема и контурам крышки не допускается
ПЗ.doc
Рис.1 Принципиальные схемы аксиально-поршневых насосов
Во время работы насоса при вращении вала приходит во вращение и блок цилиндров. При наклонном расположении блока цилиндров (см. рис.1 б г) поршни кроме вращательного совершают и возвратно-поступательные аксиальные движения (вдоль оси вращения блока цилиндров). Когда поршни выдвигаются из цилиндров происходит всасывание а когда вдвигаются - нагнетание. Через окна 1 и 3 в распределительном устройстве 2 цилиндры попеременно соединяются то с всасывающей то с напорной гидролиниями. Для исключения соединения всасывающей линии с напорной блок цилиндров плотно прижат к распределительному устройству а между окнами этого устройства есть уплотнительные перемычки ширина которых b больше диаметра dк отверстия соединительных каналов в блоке цилиндров. Для уменьшения гидравлического удара при переходе цилиндрами уплотнительных перемычек в последних сделаны дроссельные канавки в виде небольших усиков за счет которых давление жидкости в цилиндрах повышается равномерно.
В насосах с двойным несиловым карданом (см. рис.1 б) углы между осью промежуточного вала и осями ведущего и ведомого валов принимают одинаковыми и равными 1 = 2 = 2. При такой схеме вращение ведущего и ведомого валов будет практически синхронным а кардан полностью разгруженным так как крутящий момент от приводящего двигателя передается блоку цилиндров через диск 5 изготавливаемый заодно с валом 6.Аксиально-поршневые машины бескарданного типа (см. рис.1 г) блок цилиндров соединяется с ведущим валом через шайбу и шатуны поршней. По сравнению с гидромашинами с карданной связью машины бескарданного типа проще в изготовлении надежнее в эксплуатации имеют меньший габарит блока цилиндров. По данной схеме отечественной промышленностью выпускается большинство аксиально-поршневых машин серии 200 и 300 (рис.3.10).
Аксиально-поршневой гидромотор типа Г15-2:
Подача (расход) аксиально-поршневой гидромашины зависит от хода поршня который определяется углом γ наклона диска или блока цилиндров ( γ 25 ). Если конструкция гидромашины в процессе ее эксплуатации допускает изменение угла γ то такие машины регулируемые. При изменении угла наклона шайбы или блока цилиндров с + γ до - γ достигается реверсирование направления потока жидкости или вращения ротора гидромашины.Аксиально-поршневые насосы получили широкое распространение в коммерческой технике т.к. в составе гидравлических систем обеспечивают плавную бесступенчатую оптимальную передачу энергии к исполнительным механизмам. Современная коммерческая техникав своей конструкции содержит огромное количество разных элементов гидравлических систем.
Рис.3Различные конструкции аксиально-поршневых насосов с наклонным блоком цилиндров нашли широкое применение в машиностроение: больших средних и малых размеров с рабочими объемами начинающими свой отсчет от 5 см3 и достигающими 100 и более сантиметров кубических работающих на широких диапазонах давлениях с непривычно большими частотами вращения они завоевали доверие и стали практически не заменимыми элементами в гидросхемах самых разных строительных машин. Среди всех гидромашин данного типа инженеры-конструкторы отдают свое предпочтение тем у которых предусмотрено шестеренное ведение блока цилиндра так как они являются более надежными и долговечными. Все достоинства и недостатки относящиеся к конструкции различным характеристикам и показателям производству ремонту и обслуживанию насосов данного типа были детально рассмотрены в курсовом проекте на примере аналога насоса фирмы Parker - F11.
Патентно-технический обзор литературы
Прежде чем насос F11 приобрел свой нынешний вид огромное количество прототипных моделей подвергались доработкам и различным опытам. У конструкторов и изобретателей ушло практически 40 лет для того чтобы упростить зубчатое коническое зацепление создать сферический поршень и соединить это в единую гидромашину работающую на непривычно больших для нее оборотах.
Одним из прототипов насоса типа F11 является гидромашина спроектированная в 1988 году инженерами-конструкторами Ричардом Рейнольдсом и Марком Стронзе и представленная в патенте под номером 4.941.395 17 июля 1990 года.
Основной принцип действия конструкции данной гидромашины ничем не отличается от предыдущих ранее спроектированных моделей: вращение блоку цилиндров передается от вращающегося вала приводящегося в движение с помощью двигателя; как и прежде блок цилиндров и вал расположены под определенным углом по отношению друг к другу. Такой способ передачи движения от вращающегося вала к блоку всегда имел один существенный недостаток- асинхронное вращение гильзы цилиндра и вала т.е расхождение кинематических соотношений с чем пытались бороться всякий раз при проектировании новой гидромашины с наклонным блоком цилиндров. Наклонные гидравлические устройства широко используются в авиации где синхронизацию между блоком цилиндров и валом необходимо выполнить при высоких ускорениях работающего двигателя. Ранее известные два вида синхронизации подобных устройств двойной карданный шарнир и касание шатунами внутренних поверхностей гильз поршней недостаточно хорошо работали до требуемого стандарта которые имели не высокий уровень точности и не оправданную стоимость для удовлетворения необходимых уровней производительности. Третьим способом стало шестеренное ведение блока цилиндров описанное в данном патенте.
Изобретение относится к наклонным гидравлические устройства для передачи крутящего момента между вращающимся блоком цилиндров с множеством взаимных поршней и вращающимся валом связанным с блоком цилиндров определенным значением угла
обеспечивая синхронную работу блока цилиндров и валов. В данной конструкции зубчатая передача представляет собой совместное движение шестерни 64 посаженой на вращающийся вал 20 и колеса 60 которое крепится на блок цилиндров 62 каждое из которых обкатывается во внутреннему зубчатому венцу 70имеющее два набора зубьев один из которых связан с шестерней а другой с колесом.
Наличие зубчатой передачи обеспечивает синхронизацию движения вала и гильзы цилиндра что является наиболее эффективным способом для решения задачи о совместном вращении вала и блока.
Секрет дизайна и конструкции конического зубчатого зацепления раскрывает патент номер 3.013.411 автором которого является немецкий изобретатель Гуннер Вахлмарк.
Целью настоящего изобретения является улучшение и упрощение передачи совместной постоянной скорости которая может быть легко изготовлена на стандартных зуборезных машинах. В ранее представленных патентах зубчатое зацепление состоит из шестерни колеса и внутреннего зубчатого венца по одну сторону которого обкатываются зубья шестерни а по другую – зубья колеса что увеличивало размеры и себестоимость гидромашин подобного типа.
Важным объектом настоящего изобретения является не только упрощение самого зубчатого зацепления которое сводится к передачи движения между вращающимся валом и блоком цилиндром посредством только шестерни и колеса но еще и то что теперь подобная зубчатая передача может работать на больших оборотах. Другим достоинствам данного изобретения является еще и то что вал и блок цилиндров могут размещаться относительно друг друга под углом в 400 что раньше было не доступно так как предельным углом был угол в 250.
В целях для достижения постоянной скорости каждый из внешних зубьев диска 26 формируется с четырьмя в основном плоском диске 46 .Другими словами диск зубы 45 и 28 могут быть описаны как двойные спиральные зубы каждый из которых имеет противоположные пары правую руку и левую руку винтовой зубчатой передачи лица. Винтовой угол правой руки и левой стороны лица равны и противоположны. В результате передачи зубы представляют собой ромбовидную форму в плане как показано на рисунках.
Для более лучший работы аксиально-поршневой гидромашины с наклонным блоком цилиндров необходимы было изменить поршневую группу в которой были значительные утечки связанные с их конструкцией что приводило к общему снижению КПД.
Обыкновенные поршни и цилиндры предотвращают утечку за счет тесного сопряжения друг с другом. Такая конструкция подвержена чрезмерному износу что приводит к частым заменам без того дорогих деталей гидромашины подобного типа. Обычные поршни сравнительно тяжелы и тем самым усугубляют и без того существующую проблему износа подшипников вибрацию и тому подобное. Хотя есть различные устройства такие как обычные поршневые кольца предусматривающие усилия чтобы компенсировать износ отнюдь не решают полностью проблему которая оставалась открытой до 7 мая 1956 года. В этот день был издан патент номер 2.956.845 автором которого является Гуннер Валкхамер изобретатель улучшенного поршня со сферической головкой. Данный поршень имеет более легкий вес и меньшие габариты по сравнению со своими прототипами.
Часть головки поршня 56 предназначена для получения сферической поверхностью поршневых уплотнений. Для этого кольцевую канавку 70 формируют в части зажимного кольца 64 смежных направляющих кольцом 62. Поршневое уплотнительное кольцо 74
формируется из жесткого упругого материала таких как высококачественная сталь или другого подходящего материала. Располагается в паз 70 и имеет поверхности адаптированные для близких установок для взаимодействия с поверхности 71 72 и 73 из паза. Паз 70 немного шире чем уплотнительное кольцо 74 примерно на одну тысячную дюйма (.001 ") так что это общее оформление осуществляется между кольцом и противоположных поверхностях 72 и 73 от 30 паз.
В соответствии с настоящим изобретением направляющее кольцо 62 и уплотнительное кольцо 74 снабжены соответствующей сегментарной сферической наружной поверхностью из сплавов 75 и 76. В целях обеспечения свободного взаимодействия поршня 45 и цилиндра 41 был сделан небольшой зазор - половина одной тысячной дюйма (00005 "). В целях устранения небольшой утечки которые будут при эксплуатации в зазор между кольцом и цилиндром ставят уплотнительное кольцо 74. Сферическая поверхность 76 из кольца всегда находится в устойчивой линии соприкосновения с цилиндрической поверхности цилиндра. Таким образом теоретические утечки практически не существует а это было подтверждено в опытах.
Все доработки изменения в чертежах многочисленные опыты и эксперименты на протяжении 40 лет привели к тому что Parker- одна из ведущих в мире фирм по изготовлению объемных гидромашин не так давно с гордостью представила свою модель насоса и мотора данного типа марки F11.
Как видно из рисунка зубчатая передача представляет собой только совместное движение шестерни посаженой на вращающийся вал и колеса которое заодно сделано с блоком цилиндров. Отсутствует внутренний зубчатый венец что уменьшает габариты технологичность и себестоимость гидромашины. Распределительная шестерня уникальной конструкции обеспечивает синхронизацию вращения вала и гильзы цилиндра в результате чего устройства F11 и F12 устойчивы к высоким ускорениям и торсионным вибрациям. Угол 400 между валом и гильзой цилиндра обеспечивает очень компактную и легкую конструкцию.
Изобретение Гуннара Вахлмарка повышает долговечность эксплуатации гидромашины благодаря меньшему весу размерам и головки поршня представляющей собой сферическую поверхность
. Поршень меньше изнашивается практически не реагирует на повышение температур значительно предотвращаются утечки и трение поршневой пары.
Уникальная сферическая форма конструкции поршня позволяет гидромашинам типа F11 и F12 применяться при необычно высоких частотах вращения вала. Рабочие давление до 480 бар обеспечивает высокую выходную мощность. Многослойное поршневое кольцо дает важные преимущества как например малую внутреннею утечку и устойчивость к тепловым ударам.
Насосы и моторы типа F11 и F12 обеспечивают высокий крутящий момент при запуске а так же на низких частотах вращения. Прочные роликовые подшипники допускают значительные внешние осевые и радиальные нагрузки на валу. Простая и эффективная конструкция насосов или моторов данного типа с небольшим числом подвижных деталей повышает надежность и долговечность устройств.
Выбор рабочей жидкости
Основная функция рабочих жидкостей (жидких сред) для гидравлических систем — передача механической энергии от ее источника к месту использования с изменением значения или направления приложенной силы.
В постоянном совершенствовании конструкций гидроприводов отмечаются следующие тенденции:
повышение рабочих давлений и связанное с этим расширение верхних температурных пределов эксплуатации рабочих жидкостей;
уменьшение общей массы привода или увеличение отношения передаваемой мощности к массе что обусловливает более интенсивную эксплуатацию рабочей жидкости;
уменьшение рабочих зазоров между деталями рабочего органа (выходной и приемной полостей гидросистемы) что ужесточает требования к чистоте рабочей жидкости (или ее фильтруемости при наличии фильтров в гидросистемах).
С целью удовлетворения требований продиктованных указанными тенденциями развития гидроприводов современные рабочие жидкости (гидравлические масла) для них должны обладать определенными характеристиками:
иметь оптимальный уровень вязкости и хорошие вязкостно - температурные свойства в широком диапазоне температур т. е. высокий индекс вязкости;
отличаться высоким антиокислительным потенциалом а также термической и химической стабильностью обеспечивающими длительную бессменную работу жидкости в гидросистеме;
защищать детали гидропривода от коррозии; обладать хорошей фильтруемостью;
иметь необходимые деаэрирующие деэмульгирующие и антипенные свойства;
предохранять детали гидросистемы от износа; быть совместимыми с материалами гидросистемы.
Насосы серии F11 проверены во многих отраслях наиболее требовательной и самой распространенной в применении является гидравлическая система устройства цепной пилы. Для обеспечения работы насоса данного типа рекомендуется использовать масло HLP 32 которое можно заменить более дешевым отечественным маслом И20-Апрактически ничем не уступающее в физико-химических и эксплуатационных свойствах.
Класс вязкости по ISO
Индустриальное масло И-20А
Дистиллятное или смесь дистиллятного с остаточным из сернистых и малосернистых нефтей селективной очистки. Его употребляют в качестве рабочей жидкостей в гидравлических системах станочного оборудования автоматических линий прессов для смазывания легко- и средненагруженных зубчатых передач направляющих качения и скольжения станков где не требуются специальные масла и в других механизмах.
Наиболее широко применяют масло И-20А в гидравлических системах промышленного оборудования для строительных дорожных и других машин работающих на открытом воздухе. Применение указанных масел в тех или иных механизмах зависит от вязкости: по мере ее увеличения масла используют в более нагруженных и менее быстроходных механизмах. Помимо снижения трения и износа в трущихся частях деталей машин и механизмов они должны обеспечивать отвод тепла от узлов трения защищать детали от коррозии загрязнений быть уплотняющими средствами не допускать образования пены при контакте с воздухом предотвращать образование стойких эмульсий с водой и т.д. Нефтеперерабатывающая промышленность производит большой ассортимент современных нелегированных и легированных индустриальных масел с улучшенными эксплуатационными свойствами: антиокислительными смазывающими защитными деэмульгирующими и др.
Плотность жидкости - физическая величина характеризующая отношение массы жидкости к ее объему. Плотность зависит от температуры и давления.
Где -плотность вещества
Вязкость (внутреннее трение) характеризует сопротивляемость рабочей жидкости сдвигу ее слоев под действием приложенной силы. Сила трения между слоями определяется из закона Ньютона.
Для учета влияния сил инерции на вязкое трение используется соотношение между коэффициентами вязкого и кинематического трения.
Индекс вязкости (ИВ) Дина и Дэвиса. Этот индекс устанавливает характер изменения вязкости от температуры испытуемой жидкости по сравнению с двумя эталонными жидкостями при следующих условиях. Эталонные и испытуемая жидкости должны иметь одинаковую вязкость при температуре 98.9°С.
Смазывающие свойства рабочей жидкости связаны с прочностью масляной пленки и способностью ее противостоять разрыву. Чем больше вязкость тем выше прочность масляной пленки на сдвиг. Рабочая жидкость должна предотвращать контактирование и схватывание трущихся поверхностей при малых скоростях скольжения т.е. должна обладать противозадирными качествами и уменьшать износ поверхностей трения. Такие свойства достигаются за счет добавления к основе противозадирных противоизносных присадок. В качестве таких присадок применяют имеющие длинные молекулярные цепи органические соединения хлора фосфора серы свинца и олова. Влияние противоизносных присадок основано на химическом взаимодействии с металлом.
Для улучшения антикоррозионных свойств в рабочую жидкость вводятся ингибиторы ржавления.
Антипенные свойства характеризуют способность рабочей жидкости выделять воздух или другие газы без образования пены. Она оценивается по времени исчезновения пены после подачи в жидкость распыленного воздуха или прекращения перемешивания. Антипенную способность улучшают добавлением антипенной присадки ПМС-200А в количестве 0.003 0.005%.
Поверхностное натяжение характеризуется силой сопротивления жидкости изменению формы своей поверхности. Это свойство в значительной степени влияет на вспениваемость рабочей жидкости. Величина поверхностного натяжения определяется отношением свободной энергии граничного слоя к площади его поверхности и имеет размерность Джм2 или Нм.
Зольность характеризует количество остатка полученного от прокаливания и сжигания рабочей жидкости и оценивается в процентном отношении к весу сжигаемого продукта. При сжигании жидкости минеральные вещества переходят в золу в виде окислов и солей. Чем меньше зольность тем выше качество рабочей жидкости. У современных рабочих жидкостей зольность составляет 02 15%.
Коксуемость - свойство рабочей жидкости образовывать углистый осадок (кокс) под действием высоких температур (500 600°С) без доступа воздуха. Коксуемость выражается в процентах от веса нагреваемого масла и не должна превышать 1%.
Облитерация - свойство образовывать твердый осадок из молекул масла на поверхности гидрооборудования. При движении активно полярные молекулы оседают на стенках обладающих поверхностной энергией каналов. Каталитическое воздействие на облитерацию оказывают следующие факторы: скорость протекания масла величина щелевого зазора или капиллярного канала и перепад давления. Облитерация уменьшает проходное сечение и чувствительность следящих систем. Возможно "залипание" золотников и других подвижных элементов направляющей и регулирующей аппаратуры.
Расчетная часть АПГМ с наклонным блоком цилиндров
Рабочий объем – q = 10 cм3с
Давление в линии нагнетания - Рн
Давление в линии всасывания (насос) - Рвс = 0.05Рн
Номинальная частота вращения вала – n=3000 обмин
Количество плунжеров – z = 7
Угол наклона диска γ= 400
Коэффициент полезного действия =095
Объемный КПД принимаем об.= 096
Рабочая жидкость – И-20А по ГОСТ 20799-88
1. Расчет основных параметров
1.1 Угловая скорость
1.2 Определение теоретического расхода
1.3 Характерный рабочий объем
1.4 Расчет объема рабочих камер
2.Расчет размеров блока цилиндров
2.1. Диаметр отверстия d под поршень определяется в соответствии с расчетной схемой из уравнения
2.2 Диаметр Dц на котором расположены оси цилиндров блока находится из соотношения
2.3 Расстояние между отверстиями в блоке цилиндров
2.4 Наружный диаметр блока цилиндров
2.5 Диаметр внутренней расточки
2.6 Толщина дна блока цилиндров
2.7 Высота технологической расточки цилиндра
2.8 Диаметр технологической расточки цилиндра
2.9 Длина цилиндра в блоке цилиндров
2.10 Высота блока цилиндров
2.11Проверка блока цилиндров на прочность
Блок цилиндров выполнен из стали 45Х
Проверка на прочность осуществляется из условия
Условие прочности выполнено
2.13 Проверка блока на жесткость
Условия жесткости выполнены
3 Кинематические соотношения
3.1 Скорость поршня относительно цилиндра
3.2 Ускорение поршня и шатуна относительно цилиндра
3.3 Коэффициент неравномерности подачи
4. Расчет основных сил действующих в гидромашине
4.1 Сила давления действующая на поршни гидромашины
Sn=м2 площадь поршня
Pi=20МПа*11304*10-6м2=22608Н=226кН
4.2 Главная равнодействующая сила определяется как сумма от давления от давления нагнетания р2 и всасывания р1. Предположим что большая часть поршней находится в зоне нагнетания
Р=Σ Pi= 11304*10-6 (20*106=11304*10-6*83*106=938232Н=938кН
4.3 Главная осевая сила
Rb=cos40*11304*10-6 (20*106=938232*0766H=71868H=718кН
4.3 Главная поперечная (тангенциальная) сила
Tb= sin40*11304*10-6 (20*106=938232*0642H=60308H=603кН
4.5 Среднее значение крутящего момента
MT=( 20*106- 1*106) sin40*11304*10-6 =
20*214776*0642*10-3=595Нм
4.6 Моменты относительно осей ОХ и OY
My=20*106cos40=9767*0766=7481Нм
5 Проектирование зубчатого зацепления
В зависимости от вида изделия условий его эксплуатации и требованным габаритным размерам выбирают твердость колес и материалы для их изготовления. Для выбранной конической зубчатой передачи с прямыми зубьями которая является мало нагруженной всем предъявляемым требованиям подходит сталь 45X.
5.Расчет конической зубчатой передачи
5.1 Окружная скорость на среднем диаметре шестерни
n1=3000 обмин частота вращения шестерни
Сv=15 для конической зубчатой передачи с прямыми зубьями коэффициент учитывающий вид термической обработки зубчатых колес для данной передачи У+У
u=2 передаточное число
T2=595 Нм момент на колесе
5.2 Диаметр внешней делительной окружности колеса мм
KH=1 коэффициент неравномерности нагрузки
KHV=1 коэффициент внешней динамической нагрузки
h=085 для конической зубчатой передачи с прямыми зубьями
[h]= допустимые контактные напряжения при расчете зубчатых передач на контактную выносливость
Sh=1 коэффициент безопасности
KHL=1 коэффициент долговечности при переменных нагрузках
Базовый предел контактной выносливости
ho=2HB+70=2*100+70=270МПа2
по ГОСТ ближайшее значение de2=200мм
5.3 Конусное расстояние и ширина зубчатого венца
5.4 Предварительно подсчитаем углы делительных конусов
=arctgu=arctg2=6343498
5.5 Внешнее конусное расстояние
5.6 Ширина зубчатого венца
b=0285Re=11236*0285=3202 мм
5.7 Внешний торцевой модуль
[]F- допустимое напряжение на изгиб зубьев колеса
F0=324 базовый предел выносливости
KFC-коэффициент учитывающий влияние двустороннего приложения нагрузки
KFL-коэффициент долговечности равен 1
SF-коэффициент безопасности равен 1
[]F=(324*1*1)1=324 Нмм2
KFV= 1 коэффициент динамической нагрузки для прямозубых колес
F= коэффициент понижающей нагрузки принимаем 085 для прямозубых колес
Для колеса z2=de1mte=de22 mte=2002*1.5=6666
5.9 Фактическое передаточное число
5.10 Окончательные значения размеров колес
5.11.Углы делительных конусов шестерни и колеса
=arctguf=arctg2=63434980
=90-6343498=26565050
5.12.Делительные диаметры колес
De2=mez2=15*54=102мм
5.13 Внешние диаметры колес
dae1=De1+2(1+xe1)mecos 1=51+2(1+029)15cos26565050=5446мм
dae2=De2+2(1+xe2)mecos 2=102+2(1+029)15cos63434980=10373мм
5.14. Диаметры впадин зубьев
dfe1=De1-2(12-xe1)mecos 1=51-2(12-029)15cos26565050=4805мм
dfe2=De2-2(12+xe2)mecos 2=102+2(12+029)15cos63434980=9891мм
5.15. Средние диаметры
dm1=0857 De1=43707мм
dm2=0857 De2=87414мм
6. Расчет и конструирование поршневой группы
Dш=0.536d=12*0.536=6.4мм
6.2 Диаметр разноски центров сфер шатунов в ведущем диске
DР=Dц*КD=34*1.14=38.76мм
6.3. Диаметр головки поршня
Dшб=2+104d=12*1.04+2=14.48мм
6.4. Диаметр отверстия для смазки в поршне
6.5.Расстояние от середины головки поршня до канавки
Lk= Dшб *0.405=14.48*0.405=6.55мм
Lпор=Lш*0.78=37*0.78=47 мм
L1= Dшб*0.55=14.48*0.55=8.04мм
6.10Диаметр уплотнительных колец Рис.13
Dупл= Dшп*0.956=11.256*0.956=10.77мм
6.11.Диаметр основания юбки
Dосн= Dшп*0.892=11.256*0.892=10.05мм
6.12.Ширина расточки под уплотнение в поршне
b= L1*0.17=8.04*0.17=1.336мм
6.13 Ширина от основания юбки до расточки
b1= L1*0.9=0.804*0.9=0.7236мм
6.14 Ширина между расточками
b2= L1*0.25=0.804*0.25=2.01мм
h= Dцtgγ=34*tg40=28мм
6.16Напряжение сжатия в сферических шарирах
Кс=1-коэффициент использования площади опорной поверхности
dc- диаметр сферической головки
Действующие напряжения 20МПа меньше допустимых 100МПа условие выполнено.
6.17 Расчет шатунов на продольную устойчивость и прочность
fтр=0.06-коэффициент трения.
Напряжение сжатия и изгиба
6.18 Суммарное напряжение
6.19 Условие прочности
Условие прочности выполнено так как действующие напряжения 80.8Мпа меньше допустимых 197МПа.
6.20Расчет шатуна на продольную устойчивость проводят приближенно по формуле Эйлера
Fk-критическая сила продольного сжатия
J-момент инерции шатуна
Е=2*105Мпа модуль упругости для материала шатуна
Ку=3-коэффициент устойчивости
7.Расчет системы распределения.
7.1Расчет каналов для прохода рабочей жидкости и гидравлическое уравновешивание блока цилиндров.
Всасывающий канал-1-2 мс
Диаметры проходного клапана всасывающего и напорного патрубков насоса определяются по допускаемым скоростям на основании геометрической подачи насоса.
7.2Для всасывающего патрубка
7.3.Для напорного патрубка
7.4.Площадь овального окна
7.5.Радиус круговой выточки по формуле
7.6.Скорость течения жидкости
7.7.Расчет углов перекрытия
Угол охвата окна в блоке цилиндров [1]:
7.8.Угол охвата радиуса скругления окон[1]:
φи=φ0-2φр=41-29.6=11.4
7.9Размер разгрузочных канавок
где - коэффициент показывающий насколько сила прижимающая блок цилиндров к распределителю больше отжимающей сил
7.10. Определяем силы действующие в стыке блок цилиндров распределитель Прижимающая сила действующая от одного поршня
Pпр=(113.04*10-6-47.4*10-6)20*106=1.3кН
7.11.Отжимающая сила
7.12.Сила со стороны пружины
P=0.015*1.3=0.0195кН
7.13.Геометрические размеры распределителя (рис.5)[3]:
7.14Проверка на контактные нагрузки:
где Sу - площадь уплотняющих поясков приходящихся на один сектор:
Р - равнодействующая сила:
Рис.16 Взаимодействие сил между распределителем и блоком цилиндром
Так как для данного материала []=4МПаа y=3.3МПа то условие контактных нагрузок выполняется.
8.Момент центробежных сил поршней
8.1 При вращении блока цилиндров на каждый поршень действует центробежная сила
8.2Момент центробежных сил стремящих опрокинуть блок цилиндров около края распределителя.
Для уравновешивания момента центробежных сил применяется пружина помещенная в расточке блока цилиндров сила которой действует вдоль оси блока и создает относительно зоны опрокидывания момент
9.Момент ведения блока цилиндров
9.1Тем не менее для вращения блока приходится преодолевать некоторый момент величину которого необходимо знать для расчета на прочность деталей обеспечивающих синхронизацию вращения вала и блока.
Возникающий на блоке цилиндров момент складывается из двух составляющих инерционного момента Ми и момент трения блока о распределитель Мf. Инерционный момент возникает при переходных процессах(запуск и остановка) гидромашины и равен
Jб-момент инерции блока относительно оси вращения
Численное значение момента трения Мf можно оценить лишь приблеженно. Избыток прижимающих сил воспринимается контактными силами которые с учетом центрального прижима равны
9.2.Полагая с запасом что эти силы действуют по наибольшему диаметру распределителя Dм получим выражение для момента трения от действия контактных сил.
f- коэффициент трения 0.015-0.03
9.3 Момент трения Мfж определяется величиной касательных напряжений в жидкостной пленке
-вязкость жидкости в зазоре
Δ-средний зазор составляющий при номинальных частотах вращения величины порядка 10-15мкм
Dц аi-средний диаметр и ширина i-го пояска на котором возникает момент трения
1.1Предварительный расчет диаметра вала.
Можно назначить диаметр под подшипник 34 мм под сальник 30 мм под фланец муфты 28 мм и ориентировочно для посадки шестерни 40мм.
Ориентировочно радиальная нагрузка на свободном конце вала от муфты принимаем
1.2 Уточняем размеры
1.7Ma= Fa1*0.5*d=76*54*0.5=205.2Hм
A=76*3368.5+33=24.7H
B=76*68.5101.5=51.3H
Проверка суммы сил на ось у
Изгибающие моменты в вертикальной плоскости от силы Fr1
Mr1= Fr1abc=76*68.5*33154=1115Hм
MFa1= Fa1*0.5dac=27*54*68.50.5*154=328.5Hм
1.10Изгибающие моменты в вертикальной плоскости от силы Ft1
Mt1= Ft1abc=0.76*0.685*0.330.154=1115Hм
MF=Fm*c=0.152*1928=293.0Н
1.11.Для сечения под шестерней получаем
В сечении изгибающие моменты
В сечении под правой опорой
1.12.В том же сечении касательное напряжение от крутящего напряжения
Принимаем для полученных значений материал вала-Ст40Х
1.13.Ориентируясь на выбранный материал и термообработку имеем
Коэффициент под подшипники
под правый подшипник
И под левый 120>93 под шестерню.
1.16Поэтому сечение вала под подшипником целесообразно проверить на усталость по запасу прочности
Общий запас прочности в сечении под подшипником
Проверяем статическую прочность при пусковых режимах
1.19.Проверяем жесткость на вал
Средний диаметр между опорами 56мм
.Тогда прогиб в вертикальной плоскости от силы Fr
1.20. От момента силы Fа прогиба не будет
В горизонтальной плоскости прогиб дают силы Ft Fm
Этот прогиб обеспечивает надежную работу зацепления так как допустимым прогибом является значение [y]=0.06 что значительно больше полученной величины.
Угол закрутки вала в данном примере мал:
Таким образом условия прочности и жесткости выполняются. По этим условиям диаметр вала можно сохранить.
1.21.Зубчатая шестерня крепится на валу шпонкой.
Ширина шпонки 5 мм высота 8 мм
Для призматической шпонки необходимая рабочая длина
Так как ширина колеса 26мм можно назначить длину шпонки с учетом закругления по краям 20мм.
2.Расчет шпоночного соединения
2.1Расчет и проверка шпонки под шестерню.
Расчет длины шпонки lp несколько меньше ее длины l
2.2.Призматические шпонки рассчитываются на напряжение смятия по боковым поверхностям
Проверка шпонки на срез
Условие ни срез выполнено
2.3.Расчет шпоночного соединения
Призматические шпонки рассчитываются на напряжение смятия по боковым поверхностям
2.4.Проверка шпонки на срез
3. Подбор подшипников качения
3.1 Подбор подшипников качения для опоры А
Для подбора подшипников необходимо получить суммарные осевые и радиальные нагрузки на опорах в горизонтальных и вертикальных плоскостях
Для левой опоры Faг=980Н. И для правой Faв=410Н
Креж- коэффициент режима нагружения зависящий от графика нагрузки по времени.
Режим нагружения определяется
Так как осевая нагрузка сравнительно мала попробуем подобрать шарикоподшипники
К=1.4-коэффициент безопасности 1.2-1.4
КТ=1 температурный коэффициент равный 1
Y=0-коэффициент осевой нагрузки
X=1-коэффициент радиальной нагрузки
V=1-коэффициент вращения кольца равный 1
Откуда требуемая динамическая грузоподъемность
Подходит подшипник средней серии №308 имеющий С=15000Н и С0=6000Н.
d=40мм-посадочный диаметр внутреннего кольца на вал
D=90мм посадочный диаметр наружного кольца в расточку корпуса или другой детали
В=20мм-щирина подшипника
R=2- радиус закрепления обойм подшипника в местах посадок
3.4 Подбор подшипников качения для опоры В
3.6.Откуда требуемая динамическая грузоподъемность
Подходит подшипник средней серии №306 имеющий С=10000Н и С0=4150Н.
d=30мм-посадочный диаметр внутреннего кольца на вал
D=72мм посадочный диаметр наружного кольца в расточку корпуса или другой детали
В=18мм-щирина подшипника
Для обоих подшипников качения для нормальной эксплуатации должны надежно защищаться от попадания пыли грязи. Для этого они предохраняются с внешней стороны системой уплотнений или глухими крышками. Для выбранных подшипников предусмотрено манжетное уплотнение. При монтаже колец подшипников на валах и в гнездах корпуса они должны надежно фиксироваться. Некоторые из способов фиксации сочетают с уплотнительными устройствами как в данном примере.
4.Расчет круговой гайки.
Гайка круглая шлицевая ГОСТ 11871-88
Номинальный днаметр резьбы d мм
5.Расчет пружинного кольца
Кольца должны изготовляться из стальной углеродистой пружинной проволоки классов II IIА и III по ГОСТ 9389-75
Условный диаметр кольца
5.2Номинальный диаметр
5.3.Предельные отклонения
5.5.Предельные отклонения
5.5.Допускаемая осевая нагрузка 59.4 кН
Данная пружина проходит по всем требуемым параметрам
Расчет КПД спроектированной гидромашины
Общий кпд складывается из
- объемного КПД учитывающего объемные потери то есть утечки через зазоры между поршнями и стенками блока цилиндров Qут перетечки из линии высокого давления в линию низкого давления Qпер и условные утечки то есть утечки из-за деформации под давлением камеры и жидкости составляющих мертвый объем Qсж
-гидравлического КПД учитывающего потери на местных сопротивлениях и по длине
-механического КПД учитывающего потери на трение в подшипниках вала и ротора
С учетом всех этих потерь формула для общего КПД будет иметь вид
Расчет объемного КПД
Объемный КПД определяется как соотношение действительной подачи к теоретической
Qд-действительная подача
Qт-теоретическая подача
ΣQпот-объемные потери
1.1 Расчет объемных потерь
ΣQпот=ΣQут+ΣQпер+ΣQсж
ΣQут-расход утечек через зазоры между поршнями и стенками блока цилиндров
ΣQпер-расход перетечек из линии высокого давления в линию низкого давления
ΣQсж-потери на сжатие мертвого объема
1..2 Утечки в паре поршень цилиндр
р1-давление в линии нагнетания
р2-давление в линии слива
=0.015мм-радиальный зазор
=35700*10-5-динамическая вязкость рабочей жидкости
Lср-средняя длина щели поршень-цилиндр
L1 и L2 максимальная и минимальная длина щели утечки
m-число ходов поршня за один оборот
1..3Расход жидкости через щель между поршнем и цилиндров в связи с движением поршневой группы
1..4Суммарные утечки через поршневые группы
1..5 Перетечка рабочей жидкости в паре распределитель-блок цилиндров
lэ=12 мм ширина перетечки распределительных окон
Lп=0.03мм средняя длина щели по перемычкам
=0.02мм-радиальный зазор в распределителе
х=4 -количество перемычек
1..6 Утечки в дренаж по распределителю
Lут-длина окружности пояска распределителя
а-ширина уплотняющего пояска
1.7.Условные потери обусловленные сжатием жидкости в поршневом пространстве
Vпп-объем поршневого пространства
Модуль упругости жидкости
ΣQпот=0.045+0.2091+0.2453=0.4994
1.9.Расчет гидравлического КПД
Направление течение жидкости от распределителя
Где гидравлические потери равные сумме потерь по длине и местных потерь перепад давлений
Расчет гидравлических потерь по давлению
Где гидравлические потери равные сумме потерь по длине и местных потерь
Расчет гидравлических потерь по длине не учитываются.
1.11Расчет местных гидравлических потерь
коэффициент местного сопротивления при внезапном расширении или внезапном сужении
ρ=885 плотность рабочей жидкости
V=-скорость течения жидкости на участке
1.12.Расчет коэффициентов местного сопротивления
Расширение между сечениями 1-1 и 2-2
d1-1 и d2-2 диаметры в сечении 1-1 и 2-2
Сужение между сечениями 2-2 и 3-3
d3-3 диаметр в сечении 3-3
1.13.Расчет местного сопротивления
1.14.Тогда гидравлический КПД равен
Расчет механического КПД
Точный расчет механического КПД выполнить нельзя. Возможен лишь приближенный подсчет основанный на ряде допущений. При подсчете сил гидродинамического трения в подвижном контакте поршней с цилиндрами а также в распределительных устройствах условно принимается что в каждом случае зазор а следовательно толщина слоя жидкости между трущимися поверхностями остается постоянной. Тогда применяем формулу вытекающую из закона Ньютона по которой сила трения равна
п-радиальный зазор между поршнем и цилиндром в блоке цилиндров равный 0.04
Lп-длина поршня равная 48.28мм
Р-равнодействующая сила
=0.09-коэффициент трения
1.16.Механический КПД
Подбор конструктивных деталей
1. Подбор резиновой армированной манжеты для валов.
2Подбор стальной уплотнительной шайбы
Внешний диаметр шайбы
3 Подбор болтового соединения
Уплотнительное кольцо
В ходе курсовой работы были проведены расчёты основных параметров аксиально- поршневого насоса с шестерённым ведением наклонного блока цилиндров и по ним был спроектирован насос с рабочим объёмом Vo = 10 см3; давлением P = 20 МПа; частотой вращения вала n = 3000 мин-1. По полученным значениям был сформирован эскиз данного насоса опираясь на аналог машины. Основными отличиями разработанного насоса от оригинала является разница в полученном КПД: у спроектированной гидромашины общий КПД равен 95% а у оригинала – 96-97%. Расхождения в значениях имеют место по причине того что были применены иные материалы для блока цилиндров шестеренного зацепления поршней и прижимающей пружины. Роликовые подшипники так же были заменены шариковыми подшипниками качения. Выполненная курсовая работа позволила ознакомиться с методикой расчета аксиально- поршневых насосов с наклонным блоком цилиндров с шестерённым ведением блока цилиндра получить необходимый навык работы с технической литературой.
Список использованной литературы и программ
Патент № 3.013.411 от 9 дек. 1961 года «Коническая зубчатая передача для гидромашин с наклонным блоком цилиндров». Автор патента Г. Вахлмарк.
Патент №2.956.845 от 18 окт.1960 года «Сферические поршни». Автор патента Г. Вахлмарк.
Петент № 4.941.395 от 17 июл. 1990 года «Аксиально- поршневая гидромашина с шестеренным ведением наклонного блока цилиндров». Авторы патента Ричард Рейнольдс и Марк Строзе.
А.Ю.Домогаров А.И. Степаков И.С.Леладзе. Справочно-нормативные материалы на рабочие жидкости и смазки. М:2004 год-123с
А.Ю.Домогаров. Рабочие жидкости М:2004 год-115с
Дунаев П.Ф. Леликов О.П. Конструирование узлов и деталей машин. 5-е изд. М.: Высш. шк. 1998 – 447 с.
Балдин В.А Галевко В.В. Детали машин и основы конструирования
М.: Академкнига 2006 – 332 с.
А.В. Кулагин. Основы теории и конструирования объемных гидромашин Высш. шк. 1968 – 400с.
Ю.М. Исаев. Расчет и конструирование Аксиально-поршневых насосов. Ленинград:1979-97с
Леладзе И.С. Методические указания к курсовому проекту по дисциплине «Современные конструкции объемных гидромашин» М:2008-72с
Материалы и каталоги по насосу типа F11 предоставленные фирмой Parker
Autocad Microsoft Word ABBYY FineReader Foxit Reader.
содержание.doc
Выбор рабочей жидкости12
Расчетная часть АПГМ с наклонным блоком цилиндров15
1.Расчет основных параметров15
2.Расчет размеров блока цилиндров16
3.Кинематические соотношения18
4.Расчет основных сил действующих в гидромашине19
5.Проектирование зубчатого зацепления21
6.Расчет и конструирование поршневой группы24
7.Расчет системы распределения.27
8.Момент центробежных сил поршней 31
9.Момент ведения блока цилиндров32
Прочностной расчет33
2.Расчет шпоночного соединения38
3.Подбор подшипников качения39
4.Расчет круговой гайки.42
5. Расчет пружинного кольца 43
Расчет КПД спроектированной гидромашины45
Подбор конструктивных деталей49
Список использованной литературы и программ52
задание.doc
на курсовой проект по дисциплине «Объемные гидромашины и передачи» студенту группы 4ГП Вариант 9
Спроектировать объемную гидромашину типа:
АКСИАЛЬНО-ПОРШНЕВОЙ НАСОС тип F11
Исходные данные:Номинальное давление20 МПа
Частота вращения вала номинальная3000 мин -1
Рекомендуемая литература:
anguage=EN&PageID=m3517
Кулагин А.В. Основы теории и конструирования объемных гидропередач. М. Высшая школа 1968.
Бим-Бад Б.М. и др. Атлас конструкций гидромашин и гидропередач. М. ИНФР А-М 2004.
Исаев Ю.М. Расчет и конструирование аксиально-поршневых насосов Ленинград 1979.
Башта Т.М. Объемные насосы и гидравлические двигатели гидросистем. М. Машиностроение 1974.
Провести обзор технической и патентной литературы по теме проекта.
Провести предварительный расчет гидромашины.
Выполнить предварительную конструктивную разработку общего вида машины (без детальной проработки) и согласовать ее с преподавателем.
Провести проверочный расчет гидро- или пневмомашины:
а)уточнить основные конструктивные параметры
б)определить объемные гидравлические и механические потери
в)рассчитать узлы с гидростатической разгрузкой
г)провести необходимые прочностные расчеты
д)провести дополнительные расчеты по указанию преподавателя.
Пояснительная записка на 20 листов формата А4.
Графическая часть на 1-2 листах формата А1 содержащая общие виды и лист деталировки.
Графические материалы и пояснительная записка должны быть выполнены в соответствии с требованиями ЕСКД и "Методическими указаниями по курсовому и дипломному проектированию на кафедре ГП и ГПА".
Дата выдачи проекта:
поршень.dwg

Нормальный исходный
Коэффициент смещения
Делительный диаметр
сопряженного червяка
Радиусы скруглений 6мм max
Штамповочные уклоны
Неуказанные пред. отклонения размеров: отверстий +t2
остальных +- t22 по ГОСТ 25670-83
18 22HRC 2.Отклонение от соосности сфер не более
вал.dwg

Нормальный исходный
Коэффициент смещения
Делительный диаметр
сопряженного червяка
Радиусы скруглений 6мм max
Штамповочные уклоны
Неуказанные пред. отклонения размеров: отверстий +t2
остальных +- t22 по ГОСТ 25670-83
Азотировать 20..23 HRC.HV>6000МПа на поверхности Б. 2.Острые кромки притупить 0.2х45 3.H12
реферат.doc
Пояснительная записка 52
АПГМШЕСТЕРЕННОЕ ВЕДЕНИЕ НАКЛОННОГО БЛОКА ЦИЛИНДРОВСФЕРИЧЕСКИЙ ПОРШЕНЬ КОНИЧЕСКОЕ ЗАЦЕПЛЕНИЕ ТОРЦЕВОЙ РАСПРЕДЕЛИТЕЛЬ ПРУЖИННОЕ КОЛЬЦО НАПРАВЛЯЮЩАЯРАБОЧИЙ ОБЪЕМ ДАВЛЕНИЕ НАГНЕТАНИЯ ДАВЛЕНИЕ СЛИВА.
В курсовом проекте спроектирован нерегулируемый аксиально-поршневой насос с шестеренным ведением блока цилиндров типа F11 фирмы Parker.
Проведен патентно-технический обзор литературы в ходе которого рассмотрены конструкции машин сходныч данной а так же конструкция АПГМ аналогичной проектируемой.
Исходя из требований к насосу и условий его эксплуатации выбрана рабочая жидкость.
Произведен расчет размеров основных узлов(блока цилиндров конического зубчатого зацепления поршневой группыраспределителя пружинного кольца валаподшипников болтов) и выполнен прочностной расчет.
Произведен расчет КПД гидромашины.
Сделаны выводы относительноспроектированного насоса.
Рекомендуемые чертежи
- 21.04.2021