Абсорбционная колонна


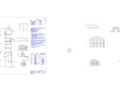
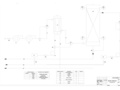
- Добавлен: 25.10.2022
- Размер: 2 MB
- Закачек: 0
Описание
Состав проекта
![]() |
![]() ![]() ![]() ![]() |
![]() ![]() ![]() ![]() |
![]() |
![]() ![]() ![]() |
![]() ![]() ![]() |
![]() ![]() ![]() |
![]() ![]() ![]() |
![]() ![]() ![]() |
Дополнительная информация
rrsrrrrrresrsryers-ssrr.dwg

Колонна абсорбционная
Вентиль регулирующий
Условные обозначения
Наименование среды в трубопроводе
Оборотная вода подающая
Оборотная вода (десорбция)
Установка абсорбционная
rrssrr-ryerrryirsryere.dwg

Технические требования
Аппарат предназначен для улавливания метанола из газовой
(воздушной)смеси водой
Емкость номинальная - 20.5 м.куб.
Объемный расход газовой смеси - 3.4 куб.м.с.
Давление в колонне - 0.1 МПа.
Температура абсорбции - 24 С.
Тип тарелок - колпачковые.
испытании и поставке аппарата должны
выполняться требования:
а) ГОСТ 12.2.003-74 "Оборудование производственное. Общие
требования безопасности" ;
б) ОСТ 26.291-79 "Сосуды и аппараты стальные сварные.
Технические требования.
Материал деталей колонны
соприкасающихся с разделяемыми
- сталь Х18Н10Т ГОСТ 5632-72
Аппарат испытать на прочность и плотность гидравлически в
горизонтальном положении давлением 0.2 МПа
положении - наливом.
Сварные соединения должны соответствовать требованиям
ОСТ 26-01-82-77 "Сварка в химическом машиностроении.
Сварочные швы в объеме 100
рентгенопросвечиванием.
Действительное расположение штуцеров
Не указанный вылет штуцеров - 120мм.
Размеры для справок.
Схема расположения штуцеров
Колонна абсорбционная
3 Расчет абсорбции(Исправленное)1.docx
1.1 Начальные и конечные концентрации жидкой и газовой фаз
Для начала найдем объемный расход инертного газа (воздуха):
где Vвоз – объемный расход воздуха м3с;
V0 – количество газовой смеси поступающей на установку (при нормальных условиях) м3с;
yн – начальная объемная концентрация метанола в газовой фазе доля.
Плотность воздуха в рабочих условиях выраженная в кгм3 равна:
гдеМвозд – молярная масса воздуха гмоль;
V0 – молярный объем воздуха при н.у лмоль;
T0 – нормальная температура К;
T – рабочая температура К;
P – рабочее давление Па;
P0 - нормальное давление Па.
Тогда массовый расход воздуха:
гдеGвоз - массовый расход инертного газа кгс;
Vвоз - объемный расход инертного газа м3с.
Относительные массовые концентрации газовой фазы:
где- соответственно начальная и конечная относительные массовые концентрации газовой фазы кг мет.кг возд.;
yн – начальная объемная концентрация метанола в газовой фазе доля;
Ммет Мвозд – соответственно мольные массы метанола и воздуха кгкмоль;
– степень извлечения доля.
.Количество поглощенного метанола определим из уравнения материального баланса:
гдеМ – количество поглощаемого метанола кгс;
Gвоз – массовый расход инертного газа кгс;
– соответственно начальная и конечная относительные массовые концентрации газовой фазы кг мет.кг возд.
Уравнение линии равновесия по закону Рауля выглядит так:
где - равновесная мольная доля метанола в газовой смеси
кмоль мет.кмоль смеси;
х - мольная доля метанола в поглотителе кмоль мет.кмоль воды;
Р – парциальное давление метанола в газовой смеси при рабочих условиях определяется на основе справочных данных МПа;
П – рабочее давление МПа;
Данные о парциальном давлении метанола над водным раствором возьмем из справочника. Ниже представлена таблица данных для построения линии равновесия.
Таблица 3.1 – Данные для построения линии равновесия
Где - равновесная мольная доля метанола в газовой смеси
кмоль ам.кмоль смеси;
x - массовая концентрация метанола в поглотителе кг мет.кг воды.
Перейдем от мольных долей к относительным массовым концентрациям:
где – равновесная массовая концентрация метанола в газовой смеси
- относительная массовая концентрация метанола в поглотителе кг мет.кг воды.;
Ммет Мвозд Мвода – соответственно мольные массы метанола воздуха и воды кгкмоль;
- равновесная мольная доля метанола в газовой смеси
х - мольная доля метанола в поглотителе кмоль мет.кмоль воды.
Найденные значения приведены в таблице 3.2.
Таблица 3.2 – Данные для построения линии равновесия
Найдем относительные массовые концентрации жидкой фазы.
По условию относительная массовая концентрация метанола в поглотителе составляет .
Из графика линии равновесия (рисунок 3.1) находим равновесную массовую концентрацию метанола в жидкой фазе кг меткг воды при .
Зная степень насыщения поглотителя определим конечную массовую концентрацию метанола в поглотителе по уравнению:
где – конечная массовая концентрация метанола в поглотителе
– степень насыщения поглотителя доля;
- равновесная массовая концентрация метанола в жидкой фазе кг меткг воды.
Зная по графику линии равновесия можно определить начальную равновесную концентрацию метанола в газовой фазе кг меткг возд:
а также верхнюю точку рабочей линии имеющую координаты
(;). Назовем эту точку В и ее координаты (00329; 0051). По условию начальная массовая концентрация метанола в поглотителе составляет а конечная массовая концентрация метанола в газовой фазе составляет.
Нижнюю точку рабочей линии назовем А и ее координаты (0; 00051). Точки А и В являются координатами рабочей линии изображенной на
Рисунок 3.1 – Рабочая и равновесная линии
Определим расход жидкого поглотителя по формуле:
где L – расход жидкого поглотителя кгс;
М – количество поглощаемого метанола кгс;
- соответственно конечная и начальная массовая концентрация метанола в газовой фазе кг мет.кг возд.
Определим большую и меньшую движущие силы:
где – соответственно большая и меньшая движущие силы на входе и выходе потоков из аппарата кг мет.кг возд.;
– соответственно начальная и конечная относительные массовые концентрации газовой фазы кг мет.кг возд.;
– соответственно равновесные массовые концентрации метанола в газовой смеси кг мет.кг возд.
Т.к. то движущая сила массопередачи в единицах концентрации газовой фазы определяется по формуле:
где – движущая сила массопередачи кг мет.кг возд.
1.2 Скорость газа и диаметр абсорбера
Предельную скорость газа (скорость захлебывания) для колпачковых тарелок определим из уравнения
где - скорость захлебывания мс;
- соответственно плотность жидкой и газовой фазы кгм³;
- диаметр колпачка равный 01 м;
- высота между тарелкой и колпачком равная 04 - 009 = 031 м.
Среднюю концентрацию метанола в смеси с водой и в смеси газовых компонентов определим из формул:
где – средняя относительная массовая концентрация метанола в поглотителе кг мет.кг воды;
– средняя относительная массовая концентрация метанола газовой фазе кг мет.кг возд.
Плотность жидкой фазы определим по уравнению:
где - соответственно плотность воды и метанола при 24 °С кгм³;
Перейдем от относительной массовой концентрации к мольным долям:
где yср – концентрация метанола в газовой фазе доли.
Мольная масса газовой смеси в кгкмоль равна:
Тогда плотность газовой фазы в кгм3 при температуре 24 °С давлении 01 МПа составляет:
Находим предельную скорость газа:
Диаметр абсорбера находим из уравнения расхода:
где d - диаметр абсорбера м;
V - объемный расход газа при условиях в абсорбере м³с;
- рабочая скорость газа мс;
Объемный расход газа в абсорбере рассчитываем по формуле:
где V0 - количество газовой смеси поступающей на установку при нормальных условиях м3с;
T0 - нормальная температура К;
T - температура газовой смеси поступающей в абсорбер K;
P - рабочее давление Па;
Рабочую скорость примем равной 08 от предельной т.е.
где – рабочая скорость газа мс;
з – скорость захлебывания (предельная скорость газа) мс.
Выбираем стандартный диаметр абсорбера .
При этом действительная скорость газа в колонне:
где - действительная скорость газа в колонне мс;
d - диаметр абсорбера м;
- стандартный диаметр абсорбера м.
Для колонны диаметром 2200 мм выбираем колпачковую тарелку ТСК-Р со следующими конструктивными размерами:
Свободное сечение колонны м2
Длина линии барботажа м
Свободное сечение тарелки м2
Относительная площадь для прохода паров %
Скорость пара в рабочем сечении тарелки определяется по формуле:
1.3 Высота светлого слоя жидкости и паросодержание
Высоту светлого слоя жидкости на тарелке находят по уравнению:
где - высота светлого слоя жидкости на тарелке м;
- высота переливной перегородки м;
- линейная плотность орошения м3(м.с).
Объемный расход жидкости равен:
Откуда линейная плотность орошения равна:
где - периметр слива равный 1606 м.
Высота переливной перегородки на колпачковой тарелке определяется по формуле:
где - высота прорезей колпачка м;
- зазор между колпачком и тарелкой м;
- расстояние от верхнего края прорезей до верха сливной планки м.
Для колпачка диаметром 100 мм величина зазора между колпачком и тарелкой составляет м а высота прорезей колпачка м. Расстояние от верхнего края прорезей до верха сливной планки примем равным м.
Высота переливной перегородки по формуле равна:
При условии что высота сливной планки должна быть кратна 5 то примем м.
Высота светлого слоя жидкости на тарелке равна:
Паросодержание барботажного слоя находим по формуле:
где - критерий Фруда.
Величина критерия Фруда рассчитывается по формуле:
где - ускорение свободного падения мс2.
Величина критерия Фруда равна:
Паросодержание барботажного слоя равно:
1.4 Коэффициенты массоотдачи и массопередачи
Коэффициенты массоотдачи определяем по уравнениям
где - коэффициенты массоотдачи соответственно в жидкой и газовой фазе м2с;
х y - динамические коэффициенты вязкости растворителя и газовой смеси при 24 0С мПас.
Примем динамический коэффициент вязкости газовой смеси равным коэффициенту вязкости воздуха: y = 0017 мПас.
Коэффициент молекулярной диффузии паров метанола в воздухе
где мет возд – соответственно мольные объемы метанола и воздуха (справочные данные) см3моль.
Для метанола мет = (С) + (О) + (Н)4 = 91+148+374 = 387.
Коэффициент молекулярной диффузии метанола в воде вычисляется по формуле:
где – параметр учитывающий ассоциацию молекул растворителя;
х – динамический коэффициент вязкости растворителя мПас;
– мольный объем диффундирующего вещества (метанола) см3моль.
Для воды: = 26; х = 092 мПас.
Теперь когда найдены все неизвестные величины найдем коэффициенты массоотдачи:
Переведем x y в выбранную для расчета размерность:
где - коэффициенты массоотдачи ;
- средние значения объемных массовых концентраций метанола в жидкой и газообразной фазах кгм3 .
Средние концентрации метанола в смеси с водой и в смеси газовых компонентов были определены по формулам (3.1.15) и (3.1.16):
Найдем средние значения объемных массовых концентрации метанола в жидкой и газообразной фазах по формулам кгм³:
Выразим коэффициенты массоотдачи в выбранной для расчета размерности :
Коэффициент массопередачи Кy находят по уравнению аддитивности фазовых диффузионных сопротивлений:
где Ку - коэффициент массопередачи для газовой фазы кг(м2с);
m - коэффициент распределения кг вод.кг см.
1.5 Число тарелок абсорбера
Тогда определим движущую силу массопередачи
Суммарная поверхность тарелок определяется по уравнению:
где F - суммарная поверхность тарелок м2.
Рабочую площадь тарелок с учетом площади занятой переливными устройствами определим по формуле:
Тогда требуемое число тарелок:
1.6 Выбор расстояния между тарелками и определение высоты
Расстояние между тарелками принимают несколько большим суммы высот барботажного слоя (пены) и сепарационного пространства :
Высоту сепарационного пространства вычисляют исходя из допустимого брызгоуноса с тарелки принимаемого равным 01 кг жидкости на 1 кг газа.
Эффективная высота сепарационного пространства равна:
где - высота сепарационного пространства м;
- межтарельчатое расстояние выбранное в зависимости от диаметра колонны и равное 04 м.
Величина брызгоуноса найдем из следующей зависимости кгкг:
где E – масса жидкости уносимая с 1 м2 рабочей площади сечения колонны кг(м2·с);
ρy – плотность газовой фазы кгм³;
т - скорость пара в рабочем сечении тарелки мс;
- поверхностное натяжения жидкости 007196 Нм.
Из графической зависимости и т находят значение := 15
Величину брызгоуноса найдем из формулы:
e 01 следовательно величина брызгоуноса верна.
Высота газожидкостного барботажного слоя равна м:
Межтарельчатое расстояние равно м:
Принятое значение межтарельчатого расстояния удовлетворяет условию неравенства.
Тогда высота тарельчатой части абсорбера м:
Примем расстояние между верхней тарелкой и крышкой абсорбера =22 м; расстояние между нижней тарелкой и днищем абсорбера м. Тогда общая высота абсорбера:
1.7 Гидравлическое сопротивление тарелок абсорбера
Гидравлическое сопротивление тарелок абсорбера определяют по формуле:
где n - число тарелок абсорбера;
- полное гидравлическое сопротивление одной тарелки Па.
Полное гидравлическое сопротивление одной тарелки складывается из трех слагаемых:
где - гидравлическое сопротивление сухой (неорошаемой) тарелки Па;
- гидравлическое сопротивление газожидкостного слоя (пены) на тарелке Па;
- гидравлическое сопротивление обусловленное силами поверхностного натяжения Па.
Вычислим гидравлическое сопротивление сухой (неорошаемой) тарелки по формуле
где - коэффициент сопротивления (для колпачковой тарелки примем равным 50).
Гидравлическое сопротивление газожидкостного слоя (пены) на тарелке определим по уравнению
Гидравлическое сопротивление обусловленное силами поверхностного натяжения найдем из уравнения
где - эквивалентный диаметр колпачка тарелки 01 м.
Определим полное гидравлическое сопротивление одной тарелки:
Тогда гидравлическое сопротивление всех тарелок абсорбера Па:
2 Расчет и подбор холодильника для охлаждения газа
2.1 Подбор теплообменника
Для данного расчета можно использовать кожухотрубчатые аппараты типов ХН или ХК.
Принимаем для газовой (воздушной) смеси индекс «1» для воды (в трубах) - индекс «2». В межтрубное пространство поступает воздушная смесь в трубное - вода.
Температурная схема теплообмена при противотоке:
Средняя разность температур:
где tср - средняя разность температур оС;
tб tм - соответственно большая и меньшая разность температур для жидкости и газа при противотоке оС.
Средняя температура воды t2 оС:
где t2н и t2к - начальная и конечная температуры воды оС.
Средняя температура газовой (воздушной) смеси:
где t1 t2 – соответственно средние температуры газовой смеси и воды оС;
tср - средняя разность температур оС.
Количество теплоты передаваемое от воздушной смеси к воде можно
вычислить по формуле:
где Q - количество теплоты Вт;
V1 - объемный расход газа м3с;
ρ1 - плотность газовой смеси кгм3;
с1 - средняя удельная теплоемкость газовой смеси Дж(кгК);
t1н t1к - начальная и конечная температуры газовой смеси 0С.
N - количество теплообменников (число на которое необходимо разбить поток для достижения оптимального соотношения всех параметров теполообмена). Примем N = 1.
Пересчитаем расход и плотность смеси с учетом новых условий:
где V1 и ρ1 - соответственно объемный расход и плотность газовой смеси при средней температуре газовой смеси 41 0С;
V0 - объемный расход смеси газов при нормальных условиях м3с;
Мсм - молекулярная масса смеси газов кгкмоль;
t1 - средняя температура смеси К;
При средней температуре теплоёмкость газовой смеси определим по формуле:
где с1 - удельная теплоёмкость газовой смеси при средней температуре Дж(кгК);
смет свозд - удельные теплоёмкости метанола и воздуха при средней температуре газовой смеси Дж(кгК);
смет = 2510 Дж(кгК); свозд = 1005 Дж(кгК);
- начальная относительная массовая концентрация газовой фазы кг.смкг.возд.
Согласно формуле (3.2.4) тепловая нагрузка равна:
Расход воды определяется из уравнения
где G2 - расход воды кгс;
с2 - средняя удельная теплоемкость воды равная 4190 Дж(кгК);
t2н t2к - начальная и конечная температуры воды оС.
Ориентировочно определим максимальную величину площади поверхности теплообмена:
Q - количество теплоты Вт;
tср - средняя разность температур оС;
Кmin - минимальное значение коэффициента теплопередачи Вт(м2К). Принимаем минимальны коэффициент теплопередачи Кmin = 70 Вт(м2К).
В многоходовых теплообменниках средняя движущая сила несколько меньше чем в одноходовых из-за возникновения смешанного взаимного направления движения теплоносителя. Определим поправку для среднелогарифмичекой разности температур по уравнению:
где Δ t — поправочный коэффициент для среднелогарифмичекой разности температур;
Р — тепловая эффективность
R — коэффициенты рассчитываемые по формулам (3.2.11) – (3.2.13).
Тепловую эффективность Р найдём по формуле:
Подставив найденные значения Р и R найдём коэффициенты
Тогда определим поправку для среднелогарифмичекой разности температур:
Таким образом среднелогарифмичекая разность температур с учётом поправки составит:
С учётом поправки максимальное значение площади поверхности теплообмена по формуле (3.2.9) составит:
Выбираем кожухотрубчатый шестиходовой холодильник со следующими характеристиками: диаметр кожуха D = 1000 мм число труб n = 642 диаметр труб d = 252 мм длина труб L = 3 м поверхность теплообмена F = 151 м2.
Площадь сечения потока между перегородками: Sм = 013 м2.
Проведем уточненный расчёт теплообменника.
) Межтрубное пространство.
Критерий Рейнольдса для межтрубного пространства найдем по формуле
где Re1 - критерий Рейнольдса для межтрубного пространства;
d - внешний диаметр труб теплообменника м;
G1 - массовый расход газовой смеси кгс;
Sм - площадь сечения потока между перегородками м2;
- динамический коэффициент вязкости газовой смеси при ее средней температуре мПас.
Массовый расход смеси газов равен:
где G1 - массовый расход газовой смеси при ее средней температуре кгс;
ρ1 - плотность газовой смеси кгм3.
N - число теплообменников (в данном случае N = 1).
Динамический коэффициен вязкости найдем по формуле
где 1 - динамический коэффициент вязкости газовой смеси мПас;
Мсм - молекулярная масса газовой смеси кгкмоль;
yн - начальная мольная доля метанола в воде кмоль сп.кмоль см.;
Ммет - молекулярная масса метанола кгкмоль;
Мвозд - молекулярная масса воздуха кгкмоль;
мет возд - соответственно динамический коэффициент вязкости метанола и воздуха мПас;
При средней температуре смеси мет = 04424 мПас возд = 00191 мПас.
Подставим полученное значение в формулу (3.2.16):
Коэффициент теплоотдачи для газовой смеси найдем по уравнению:
где α1 - коэффициент теплоотдачи для газовой смеси Вт(м2К);
λ1 - коэффициент теплопроводности газовой смеси при ее средней температуре Вт(мК);
Nu1 - критерий Нуссельта для смеси газов.
Так как при теплообмене не происходит изменение агрегатного состояния и Re >104 то критерий Нуссельта найдем по формуле:
где Re1 - критерий Рейнольдса для смеси газов;
Pr1 - критерий Прандтля для газовой смеси;
Prст1 - критерий Прандтля для стенки.
Критерий Прандтля для газовой смеси определим из уравнения:
где с1 - теплоемкость газовой смеси;
- динамический коэффициент вязкости газовой смеси при ее средней температуре мПас;
λ1 - коэффициент теплопроводности смеси при температуре 4065 0С Вт(мК).
Коэффициент теплопроводности смеси примем равным коэффициенту теплопроводности воздуха так как физические свойства смеси близки к свойствам воздуха тогда по таблице λ1 = 00272 Вт(мК).
Выразим из формулы (3.2.19) значение критерия Нуссельта поправкой можно пренебречь т.к. для газов =1.
Тогда критерий Нуссельта:
Определим коэффициент теплоотдачи к газовой смеси по формуле (3.2.18):
) Трубное пространство.
Критерий Рейнольдса для воды:
где Rе2 - критерий Рейнольдса;
G2 - массовый расход воды кгс;
dвн - внутренний диаметр труб м;
- динамический коэффициент вязкости воды при t2 = 21 0С мПас;
z - число ходов теплообменника (z = 6);
n - общее число труб теплообменника (n = 642).
Находим: 2 = 1 мПас.
Найдем внутренний диаметр труб теплообменника по формуле
где dвн - внутренний диаметр труб м;
d - внешний диаметр труб м;
- толщина стенок труб м.
Тогда критерий Рейнольдса равен:
Находим ориентировочное значение произведения (Gr2Pr2).
При расчете теплоотдачи в случае Re 10000 определяющая температура:
t = 05(tст.2 + t2) (3.2.23)
где tст.2 - температура стенки со стороны воды 0С;
t2 - средняя температура воды 0С.
Ввиду того что температура tст.2 будет определена только в конце расчета необходимо задаться величиной Δ t2.
В данном случае теплопередачи от газа к жидкости следует учесть что коэффициент теплоотдачи от газа к стенке обычно значительно меньше коэффициента теплоотдачи от стенки к жидкости поэтому примем:
Таким образом получаем:
Тогда определяющая температура:
t = 05(22966 + 21) = 2198.
При этих допущениях:
ρ2 - плотность воды кгм3;
- коэффициент объемного расширения воды К-1;
- динамический коэффициент вязкости воды мПас;
Pr2 - критерий Прандтля.
Для воды при температуре 2198 оС : ρ2 = 9973 кгм3; 2 = 21910-4 К-1; 2 = 0950 мПас; Pr2 = 665.
Произведение (Gr2Pr2) = 286500 8·105.
Найдем значение выражения ():
где Ре2 - критерий Пекле для воды;
L - длина труб теплообменника м.
Так как произведение (Gr2Pr2) 8105 10000 Re2 2300 и выражение
() > 20 то для расчета критерия Нуссельта для воды воспользуемся
графической зависимостью от Re·10-3. При Re·10-3 = 4954 . Отсюда Nu2 будет равен:
Следовательно коэффициент теплоотдачи к воде движущейся по трубам:
где α2 - коэффициент теплоотдачи Вт(м2К);
Nu2 - критерий Нуссельта;
λ2 - коэффициент теплопроводности воды при определяющей температуре принимаем λ2 = 0609 Вт(мК);
dвн - внутренний диаметр труб м.
Коэффициент теплопередачи определим по формуле:
где К - коэффициент теплопередачи Вт(м2К);
α1 α2 - соответственно коэффициенты теплоотдачи газа и воды Вт(м2К).
- сумма термических сопротивлений стенки и загрязнений Вт(м2К).
Для определения суммы термических сопротивлений стенки и загрязнений примем тепловую проводимость загрязнений стенки со стороны воздуха rзагр.1 = 2800 Вт(м2К) коэффициент теплопроводности стенки λ = 465 Вт(мК) (сталь) тепловую проводимость загрязнений стенки со стороны воды среднего качества rзагр.2 = 2380 Вт(м2К).
Подставим имеющиеся значения в формулу (3.2.30) и определим коэффициент теплопередачи:
Поверхностная плотность теплового потока:
где q - поверхностная плотность теплового потока Втм2;
К - коэффициент теплопередачи Вт(м2К);
tср - средняя разность температур 0С.
Проверим правильность расчета температуры стенки tст и уточним значения определяющей температуры t и отношения (Pr2Prст).
Расчетное значение tст 0С:
Уточненное значение произведения t и (Pr2Prст):
t = 05(22478 + 21) = 21739.
Допущения не превышают 5 % следовательно расчеты были произведены верно.
Расчетная площадь поверхности теплообмена:
где F - расчетная площадь поверхности теплообмена м2;
Q - кол-во теплоты передаваемое от воздушной смеси к воде Вт;
q - поверхностная плотность теплового потока Втм2.
Из принятого ряда теплообменников подходит теплообменник со стандартной площадью теплообмена Fст = 151 м2 при длине труб L = 3 м.
Запас площади поверхности теплообмена составит:
где Δ - запас поверхности теплообмена %;
- номинальная поверхность теплообмена м2.
Запас поверхности теплообмена (%) по формуле составит:
Запас площади поверхности теплообмена достаточен.
2.2 Расчет гидравлического сопротивления холодильника
Скорость жидкости в трубах определим по формуле
где - скорость воды в трубах мс;
- площадь сечения одного хода по трубам равная 0036 м2 ;
ρ2 - плотность воды.
В турбулентном потоке различают три зоны для которых коэффициент λ рассчитывают по разным формулам. Примем абсолютную шероховатость
= 02·10-3 м (трубы стальные бывшие в эксплуатации с незначительной коррозией).
Относительная шероховатость:
где e – относительная шероховатость;
– абсолютная шероховатость м;
d – внутренний диаметр трубопровода м.
е = 02·10-30021 = 9510-3.
Для выбора формулы определим значения следующих величин:
Т.к. Re то коэффициент трения рассчитываем для зоны смешанного трения по формуле:
Диаметр штуцеров в распределительной камере при диаметре кожуха
D = 1000 мм и числе ходов z = 6 равен: dтр.ш = 015 м.
Тогда скорость в штуцерах:
где тр.ш - скорость в штуцерах мс;
dтр.ш - диаметр штуцеров м.
Расчётная формула для определения гидравлического сопротивления в трубном пространстве:
где Ртр - гидравлическое сопротивление Па;
λтр - коэффициент трения;
тр - скорость воды мс;
ρтр - плотность воды;
тр.ш - скорость воды в штуцерах мс.
Число рядов труб омываемых потоком в межтрубном пространствегде n – число труб. Тогда округляем до m = 15.
При диаметре кожуха D = 1000 мм и длине труб L = 3 м число сегментных перегородок х = 4; диаметр штуцеров к кожуху dмтр.ш = 0300 м.
Тогда скорость потока в штуцерах:
где мтр.ш - скорость в штуцерах мс;
dмтр.ш - диаметр штуцеров м;
Скорость потока в наиболее узком сечении межтрубного пространства площадью Sмтр = 0102 м2 равна мтр мс:
По формуле (3.2.15) найдем значение критерия Рейнольдса для потока газа в наиболее узком сечении межтрубного пространства:
Гидравлическое сопротивление межтрубного пространства найдем по формуле:
где Рмтр - гидравлическое сопротивление Па;
m - число рядов омываемых потоком труб;
х - число сегментных перегородок;
мтр - скорость воздуха мс;
ρ1 - плотность воздуха при рабочих условиях кгм3;
мтр.ш - скорость воздуха в штуцерах мс.
1 Аналитическая часть.docx
Абсорбцией называется процесс избирательного поглощения газов или паров из газовой (парогазовой) смеси жидким поглотителем – абсорбентом. Этот процесс является избирательным и обратимым что даёт возможность применять его не только с целью получения растворов газов в жидкостях но также и для разделения газовых и паровых смесей. Если поглощаемый газ – абсорбтив – химически не взаимодействует с абсорбентом то такую абсорбцию называют физической (не поглощаемую составную часть газовой смеси называют инертом или инертным газом). Если же абсорбтив в жидкой фазе образует с абсорбентом химическое соединение то такой процесс называется хемосорбцией. В технике встречается сочетание обоих видов абсорбции.
Физическая абсорбция (или просто абсорбция) обычно обратима. На этом свойстве абсорбционных процессов основано выделение поглощаемого газа из раствора – десорбция. Десорбцию газа проводят отгонкой его в токе инертного газа или водяного пара в условиях подогрева адсорбента или снижения давления над адсорбентом. Отработанные после хемосорбции абсорбенты обычно регенерируют химическими методами или нагреванием. Регенерированный абсорбент вновь возвращается на абсорбцию (круговой процесс).
Сочетание абсорбции и десорбции позволяет многократно применять поглотитель и выделять поглощенный газ в чистом виде. Часто десорбцию проводить не обязательно так как полученный в результате абсорбции раствор является конечным продуктом пригодным для дальнейшего использования (соляная кислота полученная из хлороводорода водой).
Примерами использования процессов абсорбции в технике могут служить разделение углеводородных газов на нефтеперерабатывающих установках получение соляной кислоты и аммиачной воды очистка
отходящих газов с целью улавливания ценных продуктов или обезвреживания газосбросов. Остановимся на этом подробнее.
В промышленности абсорбцию применяют для решения следующих задач:
) для получения готового продукта (абсорбция SO3 в производстве серной кислоты; абсорбция HC абсорбция оксидов азота водой в производстве азотной кислоты и т.д.) при этом абсорбцию проводят без десорбции;
) для выделения ценных компонентов из газовой смеси (абсорбция бензола из коксового газа ацетилена из газов крекинга или пиролиза природного газа и т.д.); при этом абсорбцию проводят в сочетании с десорбцией;
) для очистки газовых выбросов от вредных примесей (очистка топочных газов от SO2 очистка от фтористых соединений газов выделяющихся при производстве минеральных удобрений и т.д.). Очистку газов от вредных примесей абсорбцией используют также применительно к технологическим газам когда присутствие примесей недопустимо для дальнейшей переработки газа (очистка нефтяного и коксового газов от H2S очистка азотоводородной смеси для синтеза аммиака от СО2 и СО и т.д.). В этом случае извлекаемые из газовых смесей компоненты обычно используют поэтому их выделяют десорбцией;
) для осушки газов когда в абсорбционных процессах (абсорбция десорбция) участвуют две фазы – жидкая и газовая и происходит переход вещества из газовой фазы в жидкую (при абсорбции) или наоборот (при десорбции) причём инертный газ и поглотитель являются только носителями компонента соответственно из газовой и жидкой фазах и в этом смысле в массопередаче не участвуют.
Аппараты в которых проводят процессы абсорбции называют абсорберами.
Абсорбция как и другие процессы массопередачи протекает на поверхности раздела фаз. Поэтому абсорбционные аппараты – абсорберы должны обеспечивать развитую поверхность контакта между жидкой и газовой фазами.
По способу образования этой поверхности что непосредственно связано с конструктивными особенностями абсорберов их можно подразделить на четыре основные группы: пленочные насадочные распыливающие (распылительные) тарельчатые.
2 Пленочные абсорберы
В плёночных абсорберах поверхностью контакта фаз является поверхность жидкости текущей по твердой обычно вертикальной стенке.
К этому виду аппаратов относятся:
- трубчатые абсорберы;
- абсорберы с плоскопараллельной или листовой насадкой;
- абсорберы с восходящим движением пленки жидкости.
Трубчатый абсорбер по устройству аналогичен кожухотрубчатому теплообменнику. В абсорберах с большим число труб для более равномерной подачи и распределения жидкости по трубам применяют специальные распределительные устройства. Газ движется по трубам снизу вверх навстречу стекающей жидкой пленке.
Абсорбер с плоскопараллельной насадкой. В такую колонну помещают пакет листовой насадки в виде вертикальных листов из различного материала (металл пластмассы натянутая на каркас ткань и др.). В верхней части абсорбера находятся распределительные устройства для обеспечения равномерного смачивания листовой насадки с обеих сторон.
Абсорберы с восходящим движением пленки. Такие аппараты состоят из пучка труб закрепленных в трубных решетках. Движущийся с достаточно большой скоростью газ увлекает пленку снизу вверх т.е. абсорбер работает в режиме восходящего прямотока. Для повышения эффективности процесса применяют многоступенчатые абсорберы подобного типа. В аппаратах с восходящим потоком жидкости можно создавать очень высокие скорости газа (порядка десятков метров в секунду) коэффициенты массопередачи при этом существенно возрастают но одновременно с этим сильно растет гидравлическое сопротивление. Эти аппараты не следует применять при высоких давлениях в системе.
Пленочные противоточные колонны работают при скоростях газа не превышающих скорости захлебывания. Начало захлебывания (подвисания) характеризуется резким возрастание гидравлического сопротивления а также количества находящейся в аппарате жидкости. Гидравлическое сопротивление этих абсорберов мало поскольку в них практически отсутствуют потери напора на преодоление местных сопротивлений. Поэтому пленочные противоточные абсорберы целесообразно применять при больших производительностях по газу.
3 Насадочные абсорберы
Насадочные абсорберы получили наибольшее применение в промышленности. Эти абсорберы представляют собой колонны заполненные насадкой – твердыми телами различной формы. Равномерного распределения жидкости по всей высоте насадки по сечению колонны обычно не достигается что объясняется пристеночным эффектом. Вследствие этого жидкость имеет тенденцию растекаться от центральной части колонны к её стенкам. Поэтому часто насадку в колонну загружают секциями высотой в четыре – пять диаметров (но не более трех – четырех метров в каждой
секции) а между секциями устанавливают перераспределители жидкости назначение которых состоит в направлении жидкости от периферии колонны к ее оси.
Жидкость в насадочной колонне течет по элементу насадки в виде тонкой пленки поэтому поверхностью контакта фаз является в основном смоченная поверхность насадки. Часть поверхности насадки в основном в местах соприкосновения насадочных элементов друг с другом бывает смочена неподвижной (застойной) жидкостью.
При противоточной схеме абсорбции газ движется снизу вверх а жидкость стекает вниз. При этом уходящий газ соприкасается со свежим абсорбентом над которым парциальное давление поглощаемого компонента очень мало или даже равно нулю. Поэтому при противотоке можно достичь более полного извлечения компонента из газовой смеси чем при прямоточной схеме.
Преимуществом насадочных колонн является простота устройства особенно при работе с агрессивными средами т.к. в этом случае требуется защита от коррозии только корпуса колонны и поддерживающих насадку решеток насадка же может быть выполнена из химически стойкого материала (керамика фарфор). Другое преимущество – более низкое чем в тарельчатых абсорберах гидравлическое сопротивление. Однако они мало пригодны при работе с загрязненными жидкостями. Кроме того в насадочных колоннах затруднен отвод тепла выделяющегося при поглощении газа.
4 Распыливающие абсорберы
В распыливающих абсорберах контакт между фазами достигается распыливанием или разбрызгиванием жидкости в газовом потоке. Такие абсорберы изготавливаются обычно в виде колонн в которых распыление
жидкости производится сверху а движение снизу вверх. Применяются они главным образом для поглощения хорошо растворимых газов. Общая поверхность капель возрастает с увеличением плотности орошения и с уменьшением их размера в скорости движения. Поэтому для эффективной работы абсорбера большая плотность орошения имеет решающее значение.
Эти абсорберы подразделяются на следующие группы:
- полевые (форсуночные) распыливающие абсорберы в которых жидкость распыливается на капли форсунками;
- скоростные прямоточные распыливающие абсорберы в которых жидкость распыливается за счет кинетической энергии газового потока;
- механические распыливающие абсорберы в которых жидкость распыливается вращающимися деталями. Они достаточно эффективны а недостатками являются сложность устройства и значительный расход энергии.
Преимуществами распыливающих абсорберов являются их простота и дешевизна низкое гидравлическое сопротивление и возможность использования при абсорбции газов сильно загрязненных механическими примесями. К их недостаткам относят трудность применения загрязненных жидкостей в качестве поглотителей необходимость затраты энергии на распыление жидкости и применения больших плотностей орошения а также трудность регулирования количества подаваемой жидкости.
5 Тарельчатые абсорберы
Тарельчатые абсорберы обычно представляют собой вертикальные цилиндры – колонны внутри которых на определенном расстоянии друг от друга по высоте колонны размещают горизонтальные перегородки – тарелки. Тарелки служат для развития поверхности контакта фаз при направленном движении этих фаз (жидкость течет сверху вниз а газ проходит снизу вверх) и многократном взаимодействии жидкости и газа.
Таким образом процесс массопереноса в тарельчатых колоннах осуществляется в основном в газожидкостных системах создаваемых на тарелках поэтому в таких аппаратах процесс происходит ступенчато и тарельчатые колонны в отличие от насадочных в которых массоперенос происходит непрерывно относят к группе ступенчатых аппаратов.
На каждой тарелке в зависимости от ее конструкции можно поддерживать тот или иной вид движения фаз обычно перекрестный ток или
полное перемешивание жидкости.
Преимуществами тарельчатых абсорберов являются хороший контакт между фазами и возможность работы при любом в том числе низком расходе жидкости. В этих абсорберах может быть осуществлен отвод тепла (змеевики выносные холодильники). Тарельчатые абсорберы по сравнению с насадочными более пригодны для работы с загрязненными средами.
Основные недостатки этих аппаратов – сложность конструкции и высокое гидравлическое сопротивление связанное при пропускании больших количеств газа со значительными затратами энергии на перемещение газа через аппарат. Поэтому тарельчатые абсорберы применяют преимущественно в тех случаях когда абсорбция ведется под повышенным давлением так как при этом высокое гидравлическое сопротивление не существенно.
К тарелкам предъявляют такие основные требования как наличие высокого К.П.Д.( т.е. обеспечение хорошего контакта между жидкостью и паром) малого гидравлического сопротивления устойчивой работы при значительном колебании расходов пара и жидкости. Так же они должны быть просты по конструкции удобны в эксплуатации и нечувствительны к различным осадкам и отложениям.
Из-за разнообразия массообменных процессов применяют тарелки различных типов: колпачковые ситчатые клапанные струйно-направленные с S-образными элементами.
– переливные патрубки; 2 – тарелки; 3 – корпус; 4 – кольцевая опора; 5 – выносной кипятильник; 6 – опорные кольца
Рисунок 1.1 - Общий вид тарельчатой колонны
Из-за разнообразия массообменных процессов применяют тарелки различных типов:колпачковые ситчатые клапанные струйно-направленные с S-образными элементами.
6 Конструкции тарелок.
Колпачковые тарелкисложны и металлоемки по сравнению с тарелками других типов.
– сливная труба; 2 – основание; 3 – паровой патрубок; 4 – колпачки; 5 – перегородка; 6 – прижимное кольцо; 7 – царга; 8 – опорная плита; 9 – регулировочная планка; 10 – сливная перегородка; 11 – шпильки; 12 – скоба; 13 – сальниковая набивка; 14 – регулировочный винт; 15 – кольцо.
Рисунок 1.2 – Схема колпачковой тарелки
Основной частью колпачковой тарелки является основание2– стальной отбортованный диск толщиной 4 мм с отверстиями для установки паровых патрубков3и сегментной сливной трубы1.Над паровыми патрубками установлены стандартные колпачки4.Для создания необходимого уровня жидкости тарелка снабжена сливной перегородкой10к которой винтами прикреплена регулировочная планка9.Перегородка5образует так называемый входной карман в который погружается сливная труба выше расположенной тарелки. Нижняя тарелка установлена на кольце15приваренном к царге. Точность горизонтальной установки обеспечивается регулировочными винтами14.
Для установки располагаемой выше тарелки служат стоики1 имеющие опорные плитки8.Таким образом заполняют всю царгу.
Зазор между бортом основания тарелки и царгой уплотняют установкой сальниковой набивки13и зажатием ее прижимным кольцом6с помощью шпилек11и скоб12.
Жидкость через сегментную сливную трубу заполняет тарелку на уровень определяемый положением регулировочной планки9. Колпачки своими прорезями погружены в жидкость. Пар проходит снизу через паровые патрубки щели колпачков и барботирует сквозь слой жидкости; при этом происходит массообмен. Жидкость переливается на ниже расположенную тарелку а пар идет вверх.
Колпачки (см. рисунок 1.3) для тарелок изготавливают двух исполнений (I – нерегулируемые по высоте и II – регулируемые по высоте).
Колпачки1прикреплены к паровым патрубкам2специальными болтами5 шайбами3и гайками4.По краю колпачок имеет прорези шириной 4 мм и высотой 15; 20 или 30 мм.
Колпачки располагают на тарелке по вершинам равносторонних треугольников или в шахматном порядке. Расстояние между краями колпачков 40÷ 60мм.
– колпачок; 2 – паровой патрубок; 3 – шайба; 4 – гайка; 5 – болт.
Рисунок 1.3 - Схема колпачка
Ситчатая тарелка– это лист с пробитыми в ней круглыми (рисунока) щелевидными (рисунокб) или просеченными треугольными (рисунокв) отверстиями размером 2÷ 15мм. Пар проходящий в отверстия барботирует через слой жидкости которая стекает через переливные патрубки.
Скорость пара в отверстиях 10÷ 12мс.
Рисунок 1.4 – Ситчатые тарелки: а) круглые; б) щедевидные; в) треугольные отверстия.
Ситчатые тарелки просты в конструкции и эффективны. Их недостаток – необходимость точного регулирования заданного режима (особенно по расходу газа) и чувствительность к осадкам и отложениям забивающим отверстия.
Ситчатые тарелки применяют в основном для колонн малого размера т.к. при диаметрах более 25 м распределения жидкости на тарелке становится неравномерным.
Рисунок 1.5 - Волнистая ситчатая тарелка
Клапанные тарелки.Основные элементы клапанной тарелки – подъемные клапаны круглой и прямоугольной формы закрывающие отверстия в тарелке. Конструктивно клапан выполнен так что подъем возможен только на определенную величину. При определенной скорости паров в отверстии клапаны уравновешиваются потоками пара и при дальнейшем увеличении нагрузки начинают подниматься таким образом что скорость пара в сечении между клапаном и полотном тарелки остается примерно постоянной. Следствием этого является равномерное распределение пара по площади тарелки уменьшение уноса жидкости и меньшее гидравлическое сопротивление.
Рисунок 1.6 – Подъемный клапан в клапанновой тарелке
Клапаны изготавливают штамповкой из листового металла толщиной 2÷ 3мм. Диаметр дисковых клапанов 50÷ 100мм полная высота подъема 8÷ 15мм. В крайнем нижнем положении между клапаном и плоскостью тарелки имеется зазор 1÷15мм.
Тарелки струйно-направленные.Применяют для колонных аппаратов диаметром 1000 3600 мм. На штампованных секциях просечены и отогнуты под углом 30 или 40° полукруглые «язычки» (радиусом 20; 25 или 30 мм). Расстояние между соседними рядами язычков 50 мм. При поступлении снизу пара (газа) создается его струйно-направленное движение через слой находящейся на тарелке жидкости и происходит интенсивный барботаж.
Рисунок 1.7 – Схема поступления пара (газа) через слой жидкости в тарелке
Тарелка с S-образными элементами. Их основное преимущество – простота конструкции и большая жесткость штампованных элементов. S-образные элементы представляют собой колпачки с односторонним выходом пара. Пар из них выходит в том же направлении что и движущаяся по тарелке жидкость.
Рисунок 1.8 – Схема тарелки с S-образными элементами.
0 Введение.docx
В промышленности абсорбция широко применяется для выделения из газовых смесей ценных компонентов для очистки технологических и горючих газов от вредных примесей для санитарной очистки газов и т.д.
При переходе из газовой фазы в жидкую энергия молекул распределяемого компонента уменьшается. Поэтому процесс абсорбции сопровождается выделением тепла и повышением температуры системы. Кроме того объем системы в процессе абсорбции уменьшается за счет уменьшения объема газовой фазы. Следовательно согласно принципу Ле-Шателье растворимость газа в жидкости увеличивается при повышении давления и уменьшении температуры процесса. Статика процесса абсорбции описывается уравнением Генри а кинетика – основными уравнениями массопередачи.
При абсорбции процесс массопередачи протекает на поверхности соприкосновения фаз. Поэтому в аппаратах для поглощения газов жидкостями (абсорберах) должна быть создана развитая поверхность соприкосновения между газом и жидкостью. По способу образования этой поверхности абсорбционные аппараты можно разделить на поверхностные барботажные и распыливающие.
Основная сложность при проектировании абсорберов заключается в правильном выборе расчётных закономерностей для определения кинетических коэффициентов из большого числа различных порой противоречивых
противоречивых зависимостей представленных в технической литературе.
В данном курсовом проекте производится расчёт и проектирование абсорбционной установки непрерывного действия для улавливания паров метанола из газовой (воздушной) смеси водой используя входные параметры и справочные (табличные) данные. Также в установке требуется предусмотреть (рассчитать и подобрать) насосы для подачи поглотителя (воды) в абсорбер воды в холодильник для охлаждения газа до требуемой температуры и газодувку для подачи газовой смеси в абсорбер.
3 Расчет газодувки, насосов и трубопровода.docx
Примем скорость воздуха в трубопроводе 20 мс. Тогда диаметр трубопровода находим из уравнения расхода:
гдеd – диаметр трубопровода м;
V – объемный расход воздушногазовой смеси при начальной температуре t = 70 °С м3с;
– скорость воздушногазовой смеси в трубопроводе мс.
Определим объемный расход воздушногазовой смеси при начальной температуре t = 70 °С по формуле (3.1.22):
Тогда диаметр трубопровода
На основе расчета выбираем стандартный трубопровод изготовленный из нержавеющей стали с наружным диаметром 560 мм и толщиной стенок 35 мм. Тогда внутренний диаметр трубопровода составит 553 мм.
Фактическая скорость газовой смеси в трубе равна
гдеV – объемный расход воздушногазовой смеси при начальной температуре t = 70 °С;
d – внутренний диаметр трубопровода м.
Определим потери на трение и местные сопротивления.
Критерий Рейнольдса для потока в трубопроводе:
гдеRe – критерий Рейнольдса для газа в трубопроводе;
– фактическая скорость потока в трубопроводе мс;
ρy – плотность газовой смеси при 70 °С кгм3;
y – динамический коэффициент вязкости газовой смеси при 70 °С Пас.
Плотность газовой смеси при 70 °С находим по формулам (3.1.20).
Динамический коэффициент газовой смеси определяем по формуле мПас:
где y – динамический коэффициент вязкости газовой смеси при рабочей температуре 24 °С мПас;
Мсм – мольная масса газовой смеси кгкмоль;
уср – концентрация метанола в газовой фазе доли;
Мвозд Ммет – мольные массы воздуха и метанола соответственно кгкмоль;
возд мет – динамический коэффициент вязкости воздуха и газообразного метанола при 70 °С мПас.
Динамический коэффициент вязкости воздуха при 70 °С
мПас; динамический коэффициент вязкости газообразного метанола при 70 °С мПас.
Примем абсолютную шероховатость = 01·10-3 м (стальные новые трубы).
Относительная шероховатость определяется по формуле (3.3.5):
гдее – относительная шероховатость;
– абсолютная шероховатость м;
е = 01 10-3 0553 = 181 10-4.
В турбулентном потоке различают три зоны для которых коэффициент λ рассчитывают по разным формулам.
Для выбора формулы определим значения следующих величин:
Т.к. Re то коэффициент трения рассчитываем для зоны смешанного трения по формуле (3.3.6):
Гидравлическое сопротивление трубопровода найдем по формуле:
гдеРтр1 – гидравлическое сопротивление трубопровода Па;
λ – коэффициент трения;
– сумма коэффициентов местных сопротивлений;
d – диаметр трубопровода м;
– фактическая скорость газа в трубе мс;
l – длина трубопровода м.
Определим коэффициенты местных сопротивлений:
)вход в трубу (с острыми краями): 1 = 05;
)задвижка (для d > 300 мм): 2 = 015;
)колено (угольник) под углом 90о: 3 = 11;
Сумма коэффициентов местных сопротивлений:
Длина трубопровода на этом участке: l = 65 м.
Избыточное давление которое должна обеспечивать газодувка для преодоления гидравлического сопротивления трубопровода теплообменника и абсорбера:
гдеPг – давление которое должна обеспечивать газодувка Па;
Ртр1 – гидравлическое сопротивление трубопровода Па;
Рмтр – межтрубное гидравлическое сопротивление холодильника Па;
Ркол – гидравлическое сопротивление колонны Па.
Примем что гидравлическое сопротивление вспомогательных устройств составляет 10% от сопротивления тарелок абсорбера тогда гидравлическое сопротивление абсорбционной колонны.
Ркол = 11Рa (3.3.10)
гдеРкол – гидравлическое сопротивление абсорбера Па;
Рa – гидравлическое сопротивление тарелок абсорбера Па.
Ркол = 114574144 = 503156.
Для преодоления такого гидравлического сопротивления понадобится 2 последовательно соединенных газодувки.
Полезная мощность одной газодувки:
гдеNп – полезная мощность одной газодувки Вт;
Vвозд – объемный расход воздушногазовой смеси одной газодувки м3с;
Pг – давление которое должна обеспечивать газодувка Па.
Принимая пер = 1 (при непосредственном соединении валов газодувки и двигателя) и н = 06 получим мощность на валу двигателя Nдв Вт:
гдеNдв – мощность двигателя на валу Вт;
пер – коэффициент полезного действия передачи от электродвигателя к насосу;
н – коэффициент полезного действия насоса;
Nп – полезная мощность одной газодувки Вт.
Анализ разнообразных источников показывает что лучше всего удовлетворяет газодувка марки ТГ-300-118 (V = 5 м3с ρ·g·H = 18 кПа n = 50 с-1); газодувка снабжена электродвигателем типа ВАО-315М-2 мощностью 160 кВт.
4 Расчет и подбор насосов
4.1 Расчет насоса для подачи поглотителя в абсорбер
Необходимо рассчитать и подобрать насос для подачи поглотителя (воды) в абсорбер из емкости при заданных для него условиях т.е. при температуре жидкости 24 °С насос должен преодолеть давление 01 МПа и гидравлическое сопротивление в трубах в размере 217468 Па.
Для всасывающего и нагнетательного трубопровода примем одинаковую скорость течения воды равную 2 мс. Тогда диаметр труб равен:
Vж – объемный расход поглотителя м3с;
– скорость воды в трубопроводе мс.
Объемный расход поглотителя определим по формуле:
гдеVж – объемный расход поглотителя м3с;
L – массовый расход поглотителя при температуре 24 °С кгс;
ρж – плотность поглотителя (воды) при температуре 24 °С кгм3.
На основе расчета выбираем нержавеющий стальной трубопровод наружным диаметром 18 мм и толщиной стенок 3 мм.
Внутренний диаметр трубопровода составит 12 мм.
Фактическая скорость воды в трубопроводе:
где – фактическая скорость в трубе мс;
гдеRe – критерий Рейнольдса для потока жидкости в трубопроводе;
– фактическая скорость в трубе мс;
d – внутренний диаметр трубопровода м;
ρж – плотность жидкого поглотителя при температуре 24 °С кгм3;
ж – динамический коэффициент вязкости жидкого поглотителя при температуре 24 °С Пас.
Температура воды поступающей в абсорбер 24 °С.
ж = 09142·10-3 Па·с;
Т.к. Re > 10000 то развивается турбулентный режим течения воды.
Примем абсолютную шероховатость равной Δ = 0210-3 (трубы стальные бывшие в эксплуатации с незначительной коррозией) тогда относительная шероховатость:
е = 0210-30012 = 0017.
В турбулентном потоке различают три зоны для которых коэффициент λ рассчитывают по разным формулам. Для выбора формулы определим значения следующих величин:
Т.к. Re то коэффициент трения рассчитываем для зоны смешанного трения по формуле (3.108):
Определим коэффициенты местных сопротивлений.
Для всасывающей линии:
)вентиль прямоточный: для d = 0012 м и Re 300000 2 = 123:
Длина трубопровода на этом участке 15 м.
Потерянный напор во всасывающей линии:
гдеhп.вс – потерянный напор во всасывающей линии м;
– сумма коэффициентов местных сопротивлений на линии всасывания;
– фактическая скорость воды в трубе мс;
g – ускорение свободного падения мс2.
Для нагнетательной линии:
)вентиль нормальный: при d =0012 м 1 = 104;
)колено под углом 90°: 2 = 2184;
Длина трубопровода на этом участке 12 м.
Потерянный напор на нагнетательной линии:
гдеhп.наг – потерянный напор на нагнетательной линии м;
– сумма коэффициентов местных сопротивлений на линии нагнетания;
– фактическая скорость воды в трубе мс.
Общие потери напора:
hп = hп.вс + hп.наг (3.4.1.10)
гдеhп – общие потери напора м;
hп.наг – потерянный напор на нагнетательной линии м;
hп.вс – потерянный напор во всасывающей линии м.
hп = 0996 + 7782 = 8778.
Находим потребный напор насоса по формуле:
гдеH – требуемый напор насоса м. вод. ст;
Р – давление в абсорбере Па;
Р0 – давление при нормальных условиях Па;
Hг – геометрическая высота подъема жидкости м;
hп – общие потери напора м.
Примем Hг = 1288 м (высота абсорбера).
Такой напор при заданной производительности обеспечивается одноступенчатым центробежным насосом. Учитывая широкое распространение этих насосов в промышленности ввиду их достаточно высокого к.п.д. компактности и удобства комбинирования с электродвигателем выбираем насос именно такого класса.
Полезную мощность насоса определим по формуле:
Nп = Vж ρж g Н (3.4.1.12)
гдеNп — полезная мощность насоса Вт;
Vж – объемный расход поглотителя при температуре 24 °С м3с;
H – требуемый напор насоса м. вод. ст;
Nп = 5334 10-4 9973 981 15745 = 82166.
Мощность двигателя на валу определяется по формуле:
гдеN – мощность на валу двигателя Вт;
Nп — полезная мощность насоса Вт.
Принимаем = 1 и = 06 (для центробежных насосов средней производительности) тогда мощность на валу двигателя:
Заданному напору более всего соответствует центробежный насос марки Х818 который при оптимальных условиях работы обеспечивает расход
10-3 м3с и напор 18 м ст. жидкости при = 040. Насос обеспечен электродвигателем ВАО-31-2 номинальной мощностью Nн = 3 кВт = 082. Частота вращения вала n = 483 с-1.
4.2 Расчет насоса для подачи воды в холодильник
Массовый расход жидкости для холодильника G2 = 4415 кгс. Плотность воды при температуре ее подачи в холодильник (t = 18 °C):
Объемный расход жидкости для холодильников Vводы м3с:
Для всасывающего и нагнетательного трубопровода примем одинаковую скорость течения воды равную 2 мс. Тогда диаметр труб равен
Vводы – объемный расход поглотителя м3с;
На основе расчета выбираем трубопровод из углеродистой стали наружным диаметром 0056 м и толщиной стенок 35 мм. Тогда внутренний диаметр d = 0049 м.
Фактическая скорость воды в трубе равна:
Vводы – объемный расход поглотителя м3с.
гдеRe – критерий Рейнольдса для потока в трубопроводе;
ρводы – плотность жидкого поглотителя при температуре 18 °C кгм3;
воды – динамический коэффициент вязкости жидкого поглотителя при температуре 18 °C Пас.
Температура воды поступающей в холодильник t = 18 °C
воды = 105410-3 Пас.
Примем абсолютную шероховатость равной Δ = 0210-3 (трубы стальные бывшие в эксплуатации с незначительной коррозией) тогда относительная шероховатость определяется по формуле (3.107):
е = 0210-30049 = 408210-3.
)вентиль прямоточный: для d = 0049 м и Re 300000 2 = 0735:
Потерянный напор на всасывающей линии:
Примем длину трубопровода на этом участке l = 2 м.
)вентиль нормальный: при d = 0049 м 1 = 4698;
Примем длину трубопровода на этом участке 4 м.
Общие потери напора по формуле (3.2.63):
hп = 0678 + 198 = 2658.
Потребный напор насоса определим по формуле (3.133) где геометрическую высоту подъема жидкости находим по следующей формуле:
где НГ – геометрическая высота подъема жидкости м;
Ртр – гидравлическое сопротивление трубного пространства Па;
ρ – плотность воды при температуре 18 °C кгм3;
g – ускорение свободного падения мс2
Потребный напор насоса:
Nп = Vводы ρводы g Н (3.4.2.9)
Nп = 442 10-3 9986 981 2747 = 118944.
Мощность на валу двигателя:
гдеNдв – мощность на валу двигателя Вт;
Принимаем =1 и =06 (для центробежных насосов средней производительности) тогда мощность на валу двигателя:
Заданному напору более всего соответствует центробежный насос марки Х2018 который при оптимальных условиях работы обеспечивает расход 5510-3 м3с и напор 105 м ст. жидкости при = 060. Насос обеспечен электродвигателем АО2-31-2 номинальной мощностью Nн = 3 кВт = 083. Частота вращения вала n = 483 с-1.
5 Выбор трубопровода
5.1 Оптимальный диаметр патрубка для входа исходной газовой
Определим оптимальный диаметр патрубка по формуле:
гдеV – объемный расход газовой смеси при 70 °C который определили ранее в пункте 3.3 м3с;
– скорость газовой смеси мс.
Таким образом согласно ГОСТу 8732-78 выбираем стандартный диаметр патрубка d = 530 х 9.
5.2 Оптимальный диаметр патрубка для выхода газовой смеси из холодильника
Определим оптимальный диаметр патрубка по формуле (3.147):
гдеV – объемный расход газовой смеси при 24 °C м3с;
Объемный расход газовой смеси находим по формуле (3.67):
гдеV1 – объемный расход газовой смеси при температуре 24 °С м3с;
V0 – объемный расход смеси газов при нормальных условиях м3с;
T0 – нормальная температура К;
t1 – средняя температура смеси °С;
P – рабочее давление Па;
P0 – нормальное давление Па;
Таким образом согласно ГОСТу 8732-78 выбираем стандартный диаметр патрубка d = 500 х 9.
5.3 Оптимальный диаметр патрубка для входа воды в теплообменник
гдеV – объемный расход воды при 18 °C который определили ранее в пункте 3.4.2 м3с;
Таким образом выбираем стандартный диаметр патрубка
5.4 Оптимальный диаметр патрубка для входа воды в колонну
гдеV – объемный расход воды при 24 °C который определили ранее в пункте 3.4.1 м3с;
5.5 Оптимальный диаметр патрубка для выхода жидкости из колонны
Стандартный диаметр патрубка будет такой же как и в пункте 3.5.4.
5.5 Оптимальный диаметр патрубка для выхода воздуха из колонны
Объемный расход воздуха находим по формуле (3.67):
гдеV1 – объемный расход воздуха при температуре 24 °С м3с;
V0 – объемный расход воздуха при нормальных условиях который определяли ранее по формуле (3.1) м3с;
t1 – температура воздуха °С;
2 Технологическая часть.docx
На рисунке дана схема абсорбционной установки. Газовая смесь на абсорбцию из общего трубопровода по линии С1 подается газодувками Г1 и Г2 в межтрубное пространство холодильника Х1 при температуре 70 °С где охлаждается водой до температуры 24 °С. Затем газ подается на абсорбцию в нижнюю часть колонны КА где равномерно распределяется по поперечному сечению абсорбера.
Охлаждающая вода для трубного пространства холодильников подается насосом Н1 из емкости Е1 по водопроводу В4 при температуре 18 °С где нагревается до 24 °С вследствие охлаждения газа. Из холодильника вода самотеком уходит в канализацию.
Поглотитель (вода) подается из водопроводной сети по водопроводу В4 через промежуточную емкость Е2 с помощью центробежного насоса Н2 при температуре абсорбции 24 °С в верхнюю часть колонны и равномерно распределяется по поперечному сечению абсорбера. Подача воды регулируется рядом вентилей.
В колонне осуществляется противоточное взаимодействие газа и жидкости. Газ после абсорбции выходит из колонны в общий газопровод по линии С2. Абсорбент на выходе из колонны направляется самотеком в канализацию. В технологической схеме предусмотрены контрольно-измерительные приборы для обеспечения устойчивой работы абсорбционной установки.
В данной установке используется противоточный барботажный абсорбер с колпачковыми тарелками. Абсорбер представляет собой колонный аппарат который состоит из цилиндрической обечайки и
приваренных к ней крышки и днища. Для подвода и отвода сред смонтированы штуцера. Внутри колонны размещены массообменные устройства в данном случае колпачковые тарелки.
Абсорбер работает по следующему принципу. Смесь газов подается в нижнюю часть абсорбера и поднимается вверх. Чистый поглотитель подается на верхнюю тарелку абсорбера и по тарелкам стекает вниз поглощая на каждой тарелке абсорбируемый компонент. Очищенный газ отводится через штуцер в верхней части колонны. Поглотитель насыщенный абсорбтивом отводится через штуцер в днище абсорбера.
В данном абсорбере используются колпачковые тарелки которые работают по следующему принципу (Рисунок 2.1). Газ поступает на тарелку 1 по патрубкам 2 разбиваясь затем прорезями колпачка 3 на большое число отдельных струй. Прорези колпачков наиболее часто выполняются в виде зубцов треугольной или прямоугольной формы. Далее газ проходит через слой жидкости перетекающей по тарелке от одного сливного устройства 4 к другому. При движении через слой значительная часть мелких струй распадается и газ распределяется в жидкости в виде пузырьков. Интенсивность образования пены и брызг на колпачковых тарелках зависит от скорости движения газа и глубины погружения колпачка в жидкость.
–тарелка 2–газовые патрубки 3–колпачки 4–сливные трубы
Рисунок 2.1 – Схема работы колпачковой тарелки
Процесс барботажа на тарелке весьма сложен. Проводившиеся до сих пор исследования дают возможность представить лишь качественную картину процесса. Движущиеся струйки газа (пара) обычно сливаются друг с другом при этом некоторая часть сечения прорезей обнажается и образуются каналы по которым газ (пар) проходит из-под колпачка сквозь жидкость. Поэтому поверхность взаимодействия газа (пара) с жидкостью непосредственно в зоне барботажа невелика. Основная зона фазового контакта находится в области пены и брызг над жидкостью которые образуются вследствие распыления газа (пара) в жидкости и уноса брызг при трении газа (пара) о жидкость.
Чтобы газ не попадал в переливные трубы и не препятствовал таким образом нормальному перетоку жидкости с тарелки на тарелку нижние концы переливных труб опущены под уровень жидкости. Благодаря этому создается гидрозатвор предотвращающий прохождение газа через переливные трубы.
Интенсивность образования пены и брызг зависит от скорости движения газа (пара) и глубины погружения колпачка в жидкость. Сечение и форма прорезей колпачка имеют второстепенное значение но желательно устройство узких прорезей так как при этом газ (пар) разбивается на более мелкие струйки что увеличивает поверхность соприкосновения фаз.
Колпачки (Рисунок 2.2) располагают на небольшом расстоянии друг от друга (шаг равен в среднем 15 диаметрам колпачка) с тем чтобы пузырьки газа (пара) выходящие из соседних колпачков прежде чем принять вертикальное направление движения не столкнулись друг с другом.
– тарелка; 2 – колпачок; 3 – патрубок
Рисунок 2.2 – Колпачок
Колпачковые тарелки менее чувствительны к загрязнениям чем колонны с ситчатыми тарелками и отличаются более высоким интервалом устойчивой работы колонны с колпачковыми тарелками.
Применение колпачковых тарелок позволяет уменьшить расстояние между тарелками (уменьшить высоту колонны) а также упрощает пуск и остановку абсорбционной установки. К недостаткам можно отнести высокое гидравлическое сопротивление относительную сложность изготовления монтажа и обслуживания.
Основными типами насосов применяемых в химической технологии являются центробежные поршневые и осевые насосы. Насосы отличаются между собой производительностью напором и принципом действия.
Центробежные насосы (Рисунок 2.3) имеют значительные преимущества по сравнению с поршневыми: равномерность подачи быстроходность компактность простоту устройства возможность перекачивания загрязненных жидкостей так как в центробежных насосах имеются большие зазоры между кожухом и колесом и отсутствуют клапаны. Для установки центробежных насосов не требуются массивные фундаменты.
– рабочее колесо; 2 – корпус; 3 – всасывающий трубопровод; 4 – напорный трубопровод; 5 – приемный клапан с всасывающей сеткой
Рисунок 2.3 – Схема центробежного одноступенчатого насоса
Центробежный одноступенчатый насос имеет рабочее колесо 1 с загнутыми назад лопатками которое с большой скоростью вращается в корпусе 2 спиралеобразной формы. Жидкость из всасывающего трубопровода 3 поступает по оси колеса и попадая на лопатки приобретает вращательное движение. Под действием центробежной силы давление жидкости увеличивается и она выбрасывается из колеса в неподвижный корпус 2 и напорный трубопровод 4.
При этом на входе в колесо создается пониженное давление и вследствие разности давлений жидкость из приемного резервуара поступает в насос.
Без заполнения корпуса жидкостью колесо насоса при вращении не может создать достаточной разности давлений необходимой для подъема жидкости по всасывающей трубе.
Поэтому перед пуском в ход центробежный насос должен быть залит жидкостью. Чтобы жидкость не выливалась из насоса и всасывающей трубы при заливке насоса или его остановке на конце всасывающей трубы устанавливают приемный (обратный) клапан 5 с всасывающей сеткой. Одноступенчатые центробежные насосы предназначены для создания небольших напоров – до 50 м.
В поршневом компрессоре (Рисунок 2.4) всасывание и нагнетание жидкости происходят при возвратно-поступательном движении поршня 1 в цилиндре 2 насоса. При движении поршня вправо в замкнутом пространстве между крышкой 3 цилиндра и поршнем создается разрежение.
Под действием разности давлений в приемной емкости и цилиндре газ поднимается по всасывающему трубопроводу и поступает в цилиндр через открывающийся при этом всасывающий клапан 4. Нагнетательный клапан 5 при ходе поршня вправо закрыт так как на него действует сила давления жидкости находящейся в нагнетательном трубопроводе. При ходе поршня влево в цилиндре возникает давление под действием которого закрывается клапан 4 и открывается клапан 5. Газ через нагнетательный клапан поступает в напорный трубопровод и далее в напорную емкость. Таким образом всасывание и нагнетание газа поршневым компрессором простого действия происходит неравномерно: всасывание – при движении поршня слева направо нагнетание – при обратном направлении движения поршня. В данном случае за два хода поршня газ один раз всасывается и один раз нагнетается. Поршень компрессора приводится в движение кривошипно-шатунным механизмом 6 преобразующим вращательное движение вала в возвратно-поступательное движение поршня.
- поршень; 2 - цилиндр; 3 - крышка цилиндра; 4 - всасывающий клапан; 5 - нагнета тельный клапан; 6 - кривошипно-шатунный механизм; 7 - уплотнительные кольца
Рисунок 2.4 – Схема горизонтального поршневого компрессора простого действия
По числу всасываний или нагнетаний осуществляемых за один оборот кривошипа или за два хода поршня поршневые насосы делятся на насосы простого и двойного действия. В зависимости от конструкции поршня различают собственно поршневые и плунжерные (скальчатые) насосы.
В поршневых компрессорах основным рабочим органом является поршень 1 снабженный уплотнительными кольцами 7 пришлифованными к внутренней зеркальной поверхности цилиндра. Плунжер не имеет уплотнительных колец и отличается от поршня значительно большим отношением длины к диаметру.
В зависимости от способа действия поршневые компрессоры бывают простого и двойного действия. По расположению цилиндров подразделяются на горизонтальные вертикальные и с наклонными цилиндрами; по числу ступеней сжатия подразделяются на одно- двух- и многоступенчатые а по способу охлаждения – с воздушным (небольшие компрессоры) и водяным охлаждением. По своему назначению различают компрессоры воздушные кислородные аммиачные углекислотные и др. В пищевых предприятиях применяются стационарные и передвижные компрессоры.
Расход сжатого газа обычно не вполне соответствует расчетному. Он может меняться в значительных пределах в зависимости от характера и условий работы потребителей. Поэтому давление в газосборнике меняется так как объем его рассчитывается главным образом из условий выравнивания неравномерностей подачи газа поршнем движущимся с переменной скоростью.
Только весьма кратковременное несоответствие между подачей компрессора и расходом может быть компенсировано воздухосборником (ресивером) который при возрастании давления принимает избыток газа а при снижении – его отдает. Обычно же с уменьшением расхода газа потребителями давление в газосборнике увеличивается и может превысить пределы допустимого. Как известно при подборе компрессора стремятся к тому чтобы его номинальная подача немного превышала расход потребителя. Поэтому практически регулирование подачи т. е. приведение подачи компрессора в соответствие с расходом газа потребителями сводится к снижению подачи компрессора ниже номинальной.
В качестве теплообменников как вспомогательного оборудования применяют кожухотрубчатые теплообменники. Они состоят из кожуха трубной решетки трубки сферического днища штуцера для подвода и отвода первого теплоносителя и штуцера для подвода и отвода второго теплоносителя. Схема теплообменника (одноходового) представлена на рисунке 2.5.
- корпус (обечайка); 2 – трубные решетки; 3 – трубы; 4 – крышки
Рисунок 2.5- Одноходовой кожухотрубчатый теплообменник
Трубы в решетках таких теплообменников размещают по периметрам правильных шестиугольников то есть по вершинам равносторонних треугольников. Трубы в трубных решетках закрепляют чаще всего развальцовкой.
Действие теплообменника основано на прохождении одного теплоносителя через трубное пространство и второго через межтрубное пространство а имеющаяся между ними разность температур позволяет передавать тепло через разделительные стенки труб.
В таких теплообменниках при небольших расходах теплоносителя достигаются высокие скорости движения жидкости и обеспечивается интенсивная теплоотдача и теплопередача; спиральные теплообменники которые компактны работают при высоких скоростях теплоносителей.
Для охлаждения поглотителя применяют поверхностные теплообменники в которых отсутствует непосредственный контакт теплоносителей. В качестве такого теплообменника используем кожухотрубчатый теплообменник принцип работы приведен выше.